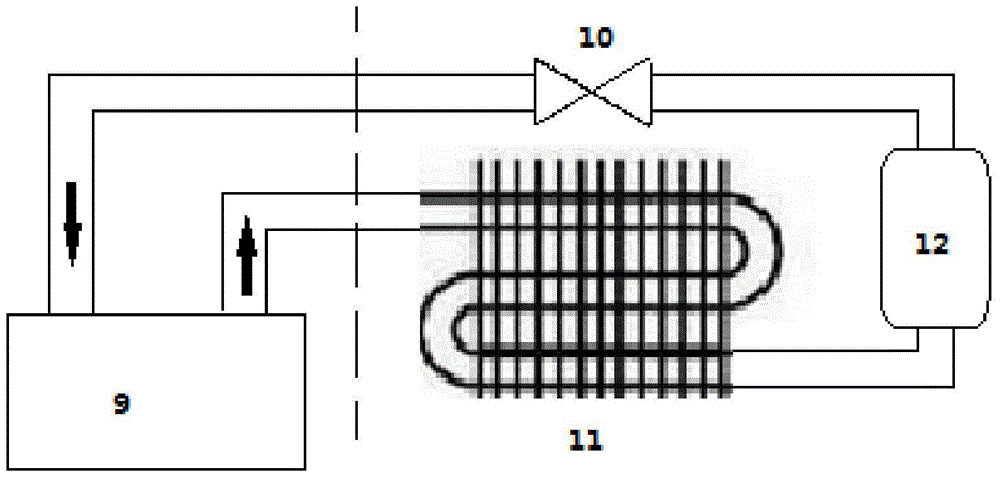
本发明涉及金属成形件的3D打印领域,具体涉及局部打印部位的温度控制。
背景技术:近年,3D打印在世界范围内兴起,正在快速改变传统的生产方式和生活方式,作为战略性新兴产业,美国、德国等发达国家高度重视并积极推广该技术。随着3D打印技术发展及推广应用的需求,利用3D直接制造金属零件成为了制造业发展的新方向。目前用于金属零件的3D打印的方法很多,基本的原理在于逐点添加熔融的金属到基体上,加工出当前层的轮廓,然后垂直移动至下一个打印层,设备调入下一图层进行加工,如此层层加工,直到整个零件加工完毕。现有的3D打印机成型的金属零件存在一个问题,即缺少对金属结晶过程的控制,因而不易获得需要的金相组织,机械性能和热学性能还不能很好满足直接使用的要求,必须经后处理方可得到改善。在3D打印中,由于其处于打印点的熔融金属的体积微小,传热效率高,说明对打印点局部的熔融金属的冷却速度的控制具有可行性。
技术实现要素:为了当前3D打印所存在的力学性能方面的问题,本发明提出了一种对金属材料3D打印局部冷却速度进行实时控制的方法以改善。为实现以上技术目的,本发明采用的方案是:一种用于金属材料3D打印局部温度控制系统,其特征是,利用流动的冷却气体与金属基体接触降温,通过调节气体流量与温度控制冷却过程,所述的流动的冷却气体是惰性气体;结构表征为:包括局部冷却装置,该局部冷却装置又包括冷却室5、气体入口3、气体出口4,利用冷却室将冷却气体与外部隔离开来,气体入口是冷却气体进入冷却室的入口,气体出口是冷却气体流出冷却室的出口,包括水冷装置11,使热的冷却气体冷却到需要温度供再利用,并防止过热气体对气体循环装置其他部件的损害;包括抽气泵,使得在冷却室的气体出口处形成负压,将冷却室内冷却气体抽出冷却室,包括气体流量调节阀10,用于控制气体流量;以上局部冷却装置、水冷装置、抽气泵、气体流量调节阀通过管路依次串接形成气体的循环系统;包括红外温度传感器,安装于冷却室的出口侧,用于检测金属冷却后金属的温度T3;包括两个气体温度传感器,分别检测气体入口、出口的温度T1、T2,包括上位机,设置了以下参数:熔融点的温度T4、打印台移动过一个冷却室长度的时间t、冷却气体比热容c气、金属的比热容c金、气体密度ρ气、处于冷却室中的待冷却金属的质量m、冷却室和金属与外部的热量交换后得到的热传导效率η;包括主控制器,其输入端分别与外温度传感器、气体温度传感连接,其输出端连接水冷装置中的控制器、抽气泵、气体流量调节阀,主控制器通过通信电缆与上位机相连,获取计算所需的数据;主控制器根据采集到的温度数据以及上位机提供的数据,按照以下公式算法确定气体的流量值q气:其中:c气、c金分别为冷却气体和金属的比热容,ρ气为考虑温度的气体的密度,t为打印台移动过一个冷却室长度的时间,m为处于冷却室中的待冷却金属的质量,η为考虑到装置和金属与外部的热量交换后得到的热传导效率,(T4-T3)/t表征了所需要的冷却速度,T4、t恒定,T3是控制的对象;以上通过求解q气得到气体流量大小;随着q气的变化,T2会随之变化,在控制算法中加入了T2的反馈;所述主控制器根据金属需要的冷却速度控制流量大小。所述的冷却室,是由隔离板6形成的通道,整个冷却室壳体采用耐热材料。在冷却室的气体出口旁的挡板下端增加一段防漏圆弧,以防止冷却室内的气体泄漏到冷却室外。有益效果本发明在现有3D打印技术上,通过对打印点附近刚形成的金属组织的冷却速度进行控制,可以获得所需要的金相组织,以获得所需要的力学性能,并且可在整个打印过程中动态改变气体流量,使整个金属零件的力学性能分布得到优化,采用本方法获得的3D打印金属件将具有更优异的力学性能。此外,采用了本发明的3D打印机集成了热处理功能,也可提高成形件的生产效率。打印过程中在线调节气体流量,使不同部位具有不同金相组织。附图说明附图1是局部冷却装置结构原理图。附图2是冷却循环系统原理图。附图3控制系统硬件图。附图4是控制系统原理图。数字标记:1为打印头,2为打印层,3为冷却气体进口,4为冷却气体出口,5为冷却室,6为冷却室隔离板,7为防漏圆弧,8为红外温度传感器,9为局部冷却装置,10为流量调节阀,11为水冷装置,12为抽气泵。具体实施方式下面结合附图和实施例对本发明进一步说明。如附图1是局部冷却装置原理图,在打印头1旁附加一个局部冷却装置9,打印点的金属熔融后,随着打印台的移动进入到该装置的冷却室5中,利用冷却气体带走冷却室内的热量,冷却气体从3进入从4排出,通过调节气体流量来控制局部的冷却速度以获得需要的金相组织。为了防止冷却气体四处游散,冷却室四周设有了隔离板6,尽量减少隔离板底部与打印金属层的垂直距离,同时通过在冷却气体出口4施加负压吸气的办法使气体产生流动,在出气口旁的挡板下端增加一段防漏过渡圆弧7,采用这种方法,可使冷却室的密封效果符合要求。为了更好实现控制,局部冷却装置进出气口设置气体温度传感器分别得到温度T1、T2,在装置出口侧设置红外温度传感器检测金属冷却后的温度T3,连同熔融点的温度T4一并传入主控制器,主控制器能根据这几个温度以及金属、气体的热力学参数,依照金属需要的冷却速度控制流量大小。利用气体与金属之间热交换的平衡,冷却气体流量简便的计算方法为:其中c气、c金分别为冷却气体和金属的比热容,ρ气为考虑温度的气体的密度,t为打印台移动过一个冷却室长度的时间,m为处于冷却室中的待冷却金属的质量,η为考虑到装置和金属与外部的热量交换后得到的热传导效率,通过实验测得。(T4-T3)/t表征了所需要的冷却速度,由于T4、t恒定,T3是控制的对象。通过求解q气得到气体流量大小。随着q气的变化,T2会随之变化,因此在控制算法中加入了T2的反馈,如附图4所示。冷却气体通过循环装置循环,采用了抽气泵以形成负压,采用气体流量调节阀以控制气体流量。从出气口抽出的热气进入到抽气泵以前经过水冷降温,以防止对泵造成危害。通过控制水冷可以控制新鲜冷却气体的温度。通过在打印过程中根据需要动态调节气体流量,可在金属零件的不同部位实现不同的金相组织,从而使金属零件各个部位具有不同的力学性能。附图1表述了局部冷却装置的大致结构,局部冷却装置可按照附图1所示的结构进行设计制造,需要采用耐热材料,如陶瓷等。装置的进、出气口与图2中的冷却循环系统出、进气口相连接。为保证良好隔离效果,隔离板7底部与打印金属层的垂直距离应当最多不超过冷却室高度的1/20,隔离板厚度不小于冷却室宽度的1/4。附图2表示了整个冷却循环系统的组成。冷却系统管道采用金属或其他耐热材料以保证不因气体的高温而破坏。抽气泵12根据需要选用,它可在在气流进口形成负压,在气流出口形成微小正压,如果需要的气体流量较小,也可采用微型抽气泵。流量阀10推荐采用性能比较高的数字型气体流量控制器,可以由主控制器向其输入数字量信号以精确控制流量。对更新后冷却气体的温度控制通过水冷装置11来完成,水冷装置中的控制器通过调整流量调节冷却气体的温度。冷却装置出进口温度T2、T1的采集可以采用管道温度传感器,测量温度范围至少应满足0-200℃,图1中的传感器8采用红外温度传感器,用以测量冷却后金属温度T4,应当注意为其增加隔热装置,并且同打印金属层保持一定安全距离。整个系统的控制系统如图3所示,具体的控制过程为:主控制器首先根据采集到的温度数据以及上位机提供的必要数据,按照设计方案中得到的下式粗略估计气体理想的流量值q气:然后,根据红外传感器的反馈T3,按照图4所示的方法,利用T3与T’3的误差,采用一定的控制算法如模糊算法、PID算法等,对q气的值进行精确修正,并将相应的控制指令传入气体流量控制阀,由其完成对气体流量的控制。随着打印过程的进行,可以根据上位机发出的信息动态调整理想冷却速度,从而调整q气使金属不同的部位具有不同的金相组织,用以改善力学性能。图3中,主控制器通过总线与上位机通信,获取气体、金属属性信息,获取熔融点的温度以及需要的冷却速度;通过传感器获得实时检测温度信息,经过数据处理后得到气体流量,再驱动气体流量控制阀。主控制器还有一个功能是控制水冷装置以控制冷却气体温度。图4中T1、T2为冷却装置进出气口气体温度,T3为金属冷却后的温度,T4为打印熔融点的温度。T’3为根据T4和给定冷却速度所得到的金属冷却后的理想温度。算法采用了带T3反馈的闭环控制算法。