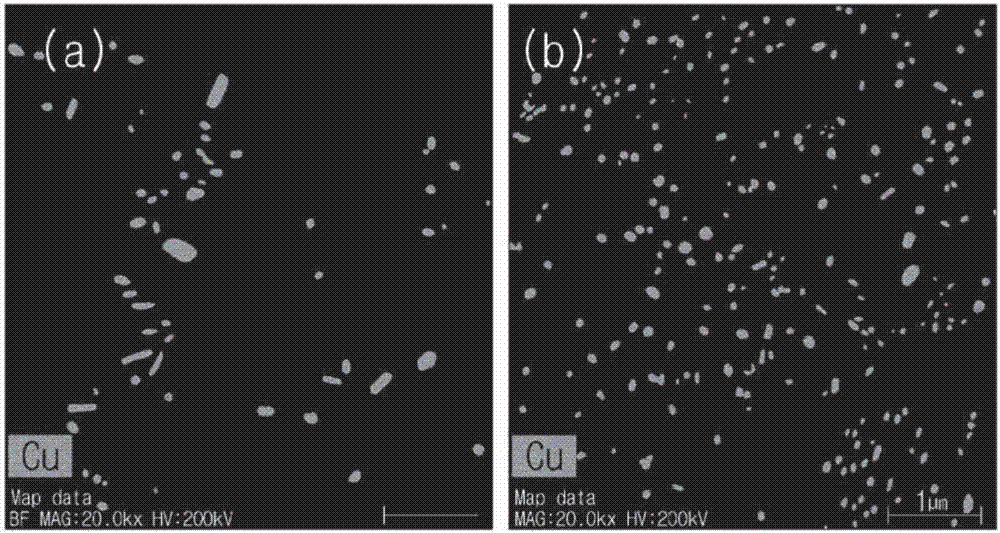
本发明涉及具有优异抗菌性的高硬度马氏体不锈钢及其制备方法。
背景技术:
:近年来,随着生活水平的提高,用户对于卫生和安全的关注持续增加。因此,需要开发不仅可以抑制生锈(不锈钢最重要的特征)还可以抑制细菌如大肠杆菌(escherichiacoli)和金黄色葡萄球菌(staphylococcusaureus)的生长的增强卫生特性的抑菌不锈钢。作为赋予不锈钢的抗菌性的方法,通过向不锈钢中添加金属元素如ag或cu的方法被广泛用于表达抗菌性。ag的情况,与cu相比其表现出更好的抗菌性,但是其材料非常昂贵,并且不仅会导致耐腐蚀性降低,而且由于具有较低的不锈钢基体固化量和较大比重的元素特征,使其难以均匀地分散/分布于不锈钢基体中。cu的情况,与ag相比其成本低,并作为抗菌成分展现出优异的抗菌性。已报道,将特定量以上的cu添加到不锈钢中时,其具有优异的抗菌性。含cu不锈钢的抑菌作用机理总结如下。在添加了一定量的cu的不锈钢的情况下,存在于表层中的cu元素被钢表面的水分离子化,少量成为活化的cu2+离子。活化的cu2+离子可降低细菌如大肠杆菌和金黄色葡萄球菌的正常反应所需的含sh-基团的酶的活性,从而最终杀死细菌并增强卫生特性。另一方面,在sts钢的情况下,由于在表面上形成具有高密度的钝化层,所以通过固化的cu原子与水接触可以以离子的形式洗脱的cu2+离子的量非常有限。因此,不仅降低了抗菌性,而且缩短了抑菌活性的持续时间。为了解决该问题,近年来,已经提出了通过将制造的钢板在适当的温度范围内在给定时间内进行预定的热处理而使微细的富cu析出物(e-cu)析出的方法。在这种情况下,由于预定的热处理而从表层部突出的e-cu析出相激活cu2+离子洗脱,并因此可以长时间稳定地保持改善的抗菌性。摇瓶法(shakingflask)和膜粘附法(filmadhesion)为广泛用于评估抗菌性的方法。摇瓶法主要用于防水/疏水材料、表面高度粗糙的材料和高吸收性材料,而膜粘附法主要用于光滑且无吸收的材料。在金属材料的情况下,抗菌性通常主要通过应用jisz2801标准以膜粘附法进行评估。若根据jisz2801标准评估抗菌性,将细菌使用含0.5-0.85%nacl的培菌液培养24小时。当在这些条件下测试时,在具有低耐腐蚀性的材料中出现腐蚀现象(如生锈)。当出现腐蚀现象时,会出现材料抗菌性的评估结果的可靠性降低的问题。因此,在评价抗菌性时,有必要确保在细菌培养之后观察不到腐蚀现象程度的耐腐蚀性。技术实现要素:发明要解决的技术问题本发明提供一种具有优异抗菌性的高硬度马氏体不锈钢及其制造方法,其中碳化铬在其微观结构中均匀分布并且不会在抗菌性能评价之后出现生锈或腐蚀。本发明的其他目的可通过下述实施例由本领域技术人员得出。解决技术问题的方法根据本发明的一优选实施方案,提供一种具有优异抗菌性的高硬度马氏体不锈钢,其包括:0.45至0.65重量%的碳(c);0.02至0.06重量%的氮(n);0.1至0.6重量%的硅(si);0.3至1.0重量%的锰(mn);0.1至0.4重量%的镍(ni);13至14.5重量%的铬(cr);0.4至0.6重量%的钼(mo);0.8至1.2重量%的钨(w);1.5至2.0重量%的铜(cu);以及余量的铁(fe)和不可避免的杂质。可将所述马氏体不锈钢进行分批退火处理,以使其具有18%以上的伸长率。可进行分批退火处理而将90个/100μm2以上的碳化铬分布于所述马氏体不锈钢的结构中。所述马氏体不锈钢可满足下述耐点蚀当量值(pren)且在使用含nacl的培菌液评估抗菌活性的过程中不会引起表面劣化,且可表现出99%以上的细菌减少率。耐点蚀当量值(pren)cr+3.0(mo+1/2w)+16n≥17所述分批退火处理可包括:第一次均热处理,将cu析出物均匀分布于所述马氏体不锈钢的结构中;第二次均热处理,将碳化铬均匀地分布于所述马氏体不锈钢的结构中;和第三次均热处理,将所述碳化铬的细颗粒进行球化。所述第一次均热处理可在500至600℃下进行,所述第二次均热处理可在800至900℃下进行,所述第三次均热处理可在600至750℃下进行。所述第一次均热处理可持续5至15小时,所述第二次均热处理可持续15至25小时,所述第三次均热处理可持续5至15小时。所述分批退火处理还可进一步包含:在所述第一次均热处理之后至所述第二次均热处理其间以40至200℃/h的速度升温的升温步骤,在所述第二次均热处理之后至所述第三次均热处理其间以10℃/h以上的速度冷却的冷却步骤,和在所述第三次均热处理之后的空气冷却处理步骤。并且,根据本发明的一优选实施方案,制备具有优异抗菌性的高硬度马氏体不锈钢的方法,其包括:通过热轧铸造钢带来生产热轧钢板的步骤,通过分批退火处理软化所述热轧钢板的步骤,以及通过冷轧所述软化完毕的钢板制造冷轧钢板的步骤,其中所述分批退火处理包含:第一次均热处理,将cu析出物均匀分布于所述马氏体不锈钢的结构中;第二次均热处理,将碳化铬均匀地分布于所述马氏体不锈钢的结构中;和第三次均热处理,将所述碳化铬的细颗粒进行球化。有益效果根据本发明,可通过将微细的碳化铬和e-cu析出物相均匀地分布在退火的添加有cu的高碳马氏体不锈钢的微观结构中而制备高硬度、高度耐腐蚀性和具备优异抗菌性的马氏体不锈钢材料。此外,根据本发明,在评估抗菌性之后的材料中不出现腐蚀现象。附图说明图1为表示根据本发明一实施方案的分批退火处理步骤的图。图2为表示根据本发明一实施方案的在第一均热处理中根据cu含量的结构中cu析出物的微观结构照片的图。图3为表示根据本发明一实施方案的在抗菌性测试之后材料表面的照片的图。具体实施方式根据本发明的一优选实施方案,提供一种具有优异抗菌性的高硬度马氏体不锈钢,其包括:0.45至0.65重量%的碳(c);0.02至0.06重量%的氮(n);0.1至0.6重量%的硅(si);0.3至1.0重量%的锰(mn);0.1至0.4重量%的镍(ni);13至14.5重量%的铬(cr);0.4至0.6重量%的钼(mo);0.8至1.2重量%的钨(w);1.5至2.0重量%的铜(cu);以及余量的铁(fe)和不可避免的杂质。本发明可进行各种修改并且包括各种实施方案,并且具体的实施方案在附图中示出并在详细描述中详细地进行描述。然而,应当理解,本发明并不旨在限于具体实施例,而是包括落入本发明的精神和范围内的所有改变,等同物和替代方案。在描述每个附图时,对相同元件使用了相同的附图标记。在下文中,将参考附图对本发明的实施方案进行详细描述。通常,在我们日常生活中广泛使用的有刃工具(例如菜刀、剪刀、剃须刀,以及作为医疗器械的解剖刀)用材料为了维持高耐磨性而需要高的硬度,并且由于容易与水分接触或储存在潮湿的环境中因此需要优异的耐腐蚀性。因此,作为有刃工具用材料主要使用已添加高碳的马氏体不锈钢。有刃工具用高碳马氏体钢的情况,包括0.45至0.70重量%的碳(c)、1.0重量%或更高的锰(mn)、1.0重量%或更高的硅(si),和12.0至15.0重量%的铬(cr)的钢被广泛使用为有刃工具用材料。在制备有刃工具用高碳马氏体不锈钢时,包括分批退火处理步骤而进行制备。在进行分批退火处理的过程中,由于碳和铬之间的反应,微细颗粒的碳化铬析出并分布于铁素体基体中。随着基体中固体碳含量的下降,所得材料可以容易地应用于不锈钢制造过程如轧制和酸洗。此外,均匀分布在铁素体基体微观结构中的微细碳化铬颗粒能够在由有刃工具类制造商进行的硬化热处理过程中快速再固化铬和碳,使其成为高温奥氏体相,并且在淬火之后提高了马氏体不锈钢微观结构的硬度和耐腐蚀性。因此,为了获得具有优异硬度和耐腐蚀性的有刃工具用高碳马氏体钢,必须将微细碳化铬颗粒均匀地分布于微观结构中。同时,如上所述,在评价抗菌性时,由于金属材料可能出现生锈或腐蚀现象,因此有刃工具用高碳马氏体钢也有可能出现抗菌性的评价结果的可靠性下降的问题。作为与抗菌马氏体不锈钢相关的专利文献,虽然日本专利公开号h9-195016和h9-256116等公开了一种具有优异抗菌性的马氏体不锈钢及其制备方法,其中e-cu析出相均匀分布,然而,已证实没有对抗菌性(如材料的生锈)以及细菌减少率有很大影响的因素的相关信息进行公开。因此,为了开发具有优异抗菌性的高硬度马氏体不锈钢,有必要在将碳化铬均匀地分布于其微观结构中的同时,确保在抗菌评价之后不出现材料腐蚀现象的耐腐蚀性。本发明涉及具有优异抗菌性的高硬度马氏体不锈钢及其制备方法,其特征在于:马氏体不锈钢包括:0.45至0.65重量%的碳(c);0.02至0.06重量%的氮(n);0.1至0.6重量%的硅(si);0.3至1.0重量%的锰(mn);0.1至0.4重量%的镍(ni);13至14.5重量%的铬(cr);0.4至0.6重量%的钼(mo);0.8至1.2重量%的钨(w);1.5至2.0重量%的铜(cu);以及余量的铁(fe)以及不可避免的杂质,并且根据日本工业标准(jis)z2801抗菌评价方法测定,其具有99.9%以上的细菌减少率。下文中将对构成本发明有刃工具用高碳马氏体不锈钢的合金元素的含量进行描述。如果c的含量低,会降低马氏体不锈钢的硬化热处理之后的硬度,从而可能无法确保机械加工性和耐磨性,因此,添加0.45%以上的c。另一方面,如果c的含量过高,由于过量形成的碳化铬不仅会劣化材料的耐腐蚀性而且由于碳偏析,在退火结构中有可能形成粗碳化物,因此,将上限限定为0.65%。n作为为了提高耐腐蚀性并同时提高硬度所添加的元素,由于不会发生局部微偏析,因此具有替代c添加也不会在产品中形成粗的析出物的优点。为了展现这种效果而添加0.02%以上的n。然而,过量的n在铸造的过程中可能会导致孔的生成,因此n的上限限定为0.06%。si作为为了脱氧而必须添加的元素,所以添加0.1%以上的si。然而,过量的si会降低酸洗性能并增加材料的脆性,所以si的上限限制在0.6%。mn作为为了脱氧而必须添加的元素,因此添加0.3%以上的mn。然而,如添加过量的mn会劣化钢表面质量,并由于其中残留的奥氏体降低最终热处理材料的的硬度,因此,mn的上限限制在1.0%。ni作为在制钢过程中不可避免地从铁屑中带入的元素,添加0.1%以上的镍。然而,如果含有高含量的ni会形成最终热处理材料中的残留奥氏体而很难确保高的硬度。因此,ni的上限限制在0.4%。由于cr是用于确保耐腐蚀性的基本元素,所以添加13%以上。然而,过量的cr会增加制造成本并增加结构中铬成分的微偏析,导致碳化铬的局部粗化,由此降低硬化热处理材料的耐腐蚀性和硬度。因此,cr的上限限制在14.5%。mo对提高耐腐蚀性具有优异的效果,因此添加0.4%以上的mo。然而,过量的mo会增加制造成本。因此,mo的上限限制在0.6%。w由于具备提高耐腐蚀性和热处理硬度的效果,因此添加0.8%以上的w。然而,过量的w会增加制造成本并降低可加工性,因此,w的上限限制在1.2%。cu作为本发明不锈钢中最重要的合金元素,通过分批退火处理形成e-cu使抗菌性的确保成为可能。并且,其含量越高,则e-cu析出物的量越高,由此增加可提高抗菌性的cu2+的洗脱量。然而,过量的cu可劣化可处理性、可加工性和耐腐蚀性。因此,cu的上限限制在2.0%。根据本发明的一实施方案,具有上述成分的马氏体不锈钢通过连续铸造或钢锭铸造来制备铸造钢带之后,经过热轧处理来制备成可加工的热轧钢板。然后,制备的热轧钢板通过分批退火处理进行软化处理,以确保在进行适合用于有刃工具用的厚度的加工(例如精轧)之前的可加工性。如图1所示,根据本发明的一实施方案,分批退火处理包括第一均热处理,其中优先将球形cu析出物均匀地分布于马氏体不锈钢的结构中;第二次均热处理,其中将碳化铬均匀地分布于热轧钢板的结构中;和第三次均热处理,将碳化铬的微细颗粒球化。此外,进一步进行在所述第一次均热处理之后至所述第二次均热处理其间提高热轧钢板温度的升温步骤,在第二次均热处理之后至第三次均热处理其间降低热轧钢板温度的冷却步骤,和第三次均热处理后冷却热轧钢板的空气冷却处理步骤。首先,根据本发明的一实施方案,第一次均热处理为这样的处理:通过将热轧钢板在500至600℃的恒温气氛中均匀加热5至15个小时而使cu析出物均匀地分布于热轧钢板结构中。在该过程中,如图2(b)所示,微细cu析出物均匀地分布于结构中且具有几十nm的尺寸。该cu析出物通常充当碳化铬(其在晶界优先析出是众所周知的)的沉积点(depositionpoint),并在第二次均热处理中诱导碳化铬的均匀析出。在第一次均热处理中,当温度小于500℃时,不形成cu析出物。当温度超过600℃时,碳化铬与cu析出物同时析出,因此,不管cu析出物如何,碳化铬优先在晶界析出,使得可能无法确保微细碳化物的均匀分布。并且,当第一次均热处理小于5小时时,因为没有cu析出,因此无法确保碳化铬的均匀分布。当第一次均热处理持续超过15小时时,cu析出物的尺寸增加,但cu析出物的数量降低。因此,cu析出物为局部分布,使得其难于获得均匀分布的碳化铬。因此,优选第一次均热处理在500至600℃的恒温气氛中进行5至15小时。其次,根据本发明的一实施方案的升温步骤为这样的步骤:在第一次均热处理之后至第二次均热处理其间以40至200℃/h的速率将热轧钢板升温的步骤。如果在升温步骤中的加热速率为40℃/h以下,经过碳化铬变粗过程中的温度范围的时间,例如经过700至750℃所需的时间,会增加。因此,分布于微观结构中的碳化铬的密度可能会随着碳化铬尺寸的增加而降低。另一方面,如果加热速率为200℃/h以上,虽然由于经过碳化铬粗化的温度段的时间的减少而可获得微细碳化铬,然而,会减少碳化物扩散时间而使得碳化铬非均匀分散。因此,优选将在加热过程中的加热速率控制在大于40℃/h并且小于200℃/h的范围。接下来,在升温步骤之后进行本发明的一实施方案的第二次均热处理,其作为将碳化铬均匀分布在热轧钢板的结构中的步骤,为在800至900℃的恒温气氛中将热轧钢板均匀加热15至25小时的步骤。在该过程中,碳化铬均匀地分布于结构中。如果均热温度小于800℃,由于在均热过程中在晶界局部析出的碳化铬可能形成团粒。如果均热温度大于900℃,碳化铬在晶界附近粗化。这种碳化铬团粒和粗碳化铬使得材料局部失衡,使其难以确保延展性并在最后的热处理过程中导致材料品质劣化。另外,如果第二次均热处理的均热时间为15小时以下,则可有效地形成微细颗粒的碳化铬,但碳化铬颗粒可能会团聚而使得分布不均匀。如果均热时间超过25小时,相邻的碳化铬颗粒因为过度退火而结合,不仅使碳化铬局部粗化,而且使处理效率因为热处理时间的增加而降低,并且因此增加制造成本。因此,优选第二次均热处理在800至900℃的恒温气氛下进行15至25小时。接下来,根据本发明的一实施方案的冷却步骤为这样的步骤:在第二均热处理之后至第三均热处理其间将热轧钢板冷却至600至750℃的步骤。冷却处理优选以超过10℃/h的速度将热轧钢板进行冷却。如果冷却速度低于10℃/h,经过碳化铬变粗过程的温度范围的所需时间会增加,因此,微细颗粒碳化铬在微观结构中变粗,使得难以在硬化热处理过程中确保耐腐蚀性和硬度。根据本发明的一实施方案的第三次均热处理为这样的步骤:在冷却步骤之后进行,将热轧钢板结构中的微细颗粒碳化铬以低温进行球化的步骤,并在600至750℃的恒温范围内保持并均匀地加热热轧带卷5至15小时的步骤。用于碳化铬球化的最小温度条件为600℃。如果温度超过750℃,球化的碳化铬过度生长,使得碳化铬的数量降低且延展性下降。此外,当第三次均热过程的恒温保持时间小于5小时时,碳化铬的球化不充分。当恒温处理时间超过15小时时,球化的碳化物由于过度生长会形成粗的微观结构。因此,优选第三次均热处理在600至750℃的恒温气氛下进行5至15小时。在第三次均热处理后,通过空气冷却热轧钢板而完成分批退火处理步骤。在经过上述分批退火处理完成软化后,进行冷轧退火的钢板的制备冷轧钢板的步骤,且对被加工成所期望的厚度和形状的所述冷轧钢板进行硬化热处理的步骤。硬化热处理分三阶段进行,第一阶段为将通过分批退火处理而均匀分布的碳化物再固化的奥氏体化→淬火热处理阶段。在该热处理阶段,在1000至1150℃下进行持续10秒至5分钟的热处理。此时,当热处理温度低于1000℃时,无法获得用于剃须刀片的钢材料所需的硬度。当热处理温度高于1150℃时,由于再固化碳化物的量的增加而导致残留奥氏体过量形成,由此有可能引发硬度降低的问题。并且,当热处理温度小于10秒时,也无法获得用于剃须刀片的钢材料所需的硬度,当热处理温度超过5分钟时,也会使颗粒生长而出现残留奥氏体。在淬火热处理完成后,在约-70℃的温度下进行10秒至5分钟的零下热处理,以将部分残留的奥氏体转化成马氏体。为了确保马氏体钢的延展性,在400至600℃下进行30分钟至2小时的回火处理,然后空气冷却,从而完成硬化热处理步骤。在下文中,将使用本发明的实施例对本发明进行说明。然而,下述实施例仅为本发明的优选实施例,本发明的权利保护范围并不限于下述实施例。首先,制备含有下表1所示的成分和余量的铁(fe)和不可避免的杂质(重量%)的根据实施例和对比实施例的热轧钢板。作为参考,将不锈钢的耐腐蚀性通过使用耐点蚀当量值(pren,等式1)进行量化,其是一种用于评价不锈钢产品耐腐蚀性的方法。等式1:pren=cr+3.0(mo+1/2w)+16n[表1]不锈钢种类csimncrnimowcunpren对比实施例10.6830.4080.69313.210.3080000.0313.69对比实施例20.6870.4020.73013.240.296000.510.0413.88对比实施例30.6510.40.68813.30.299001.020.0614.26对比实施例40.7000.3800.63812.760.310001.460.0313.24对比实施例50.6920.4240.72213.550.302001.980.0514.35对比实施例60.6950.3910.70113.160.3002.520.0413.8对比实施例70.490.3050.51713.980.3070.511.0500.03117.69对比实施例80.560.3130.47213.810.2950.491.0100.02917.36对比实施例90.620.2980.50514.010.3080.511.0300.0317.67对比实施例100.660.3120.52813.920.3100.481.021.500.02817.44实施例10.450.2970.48913.910.2870.480.991.520.02917.40实施例20.50.2990.50614.140.3020.490.951.50.0317.61实施例30.560.2980.509140.3010.511.520.0317.58实施例40.60.2910.50313.950.3050.490.981.50.0317.47在制备具有表1所示成分的用于有刃工具用高碳马氏体不锈钢的铸造钢带之后,通过热轧制备热轧钢板(厚度:3mm),并确认热轧钢材的边缘质量。然后,将制备的热轧钢板在以下分批退火条件下进行热处理之后,观察其微观结构并进行伸长率评价。[分批退火处理条件]-第一次均热处理:在500℃下持续10小时-升温步骤:升温速度为100℃/小时-第二次均热处理:在850℃下持续20小时-冷却处理步骤:温度下降速度为10℃/小时-第三次均热处理:在650℃下持续7小时接下来,通过冷轧制备冷轧钢板(厚度:1.5mm)并确认冷轧材料的边缘质量。此外,在如下条件下进行硬化热处理后,根据jisz2801,使用一种菌株(大肠杆菌)评价抗菌性。[硬化热处理条件]-奥氏体化:在1100℃下持续5分钟-淬火:在室温下油淬火-低温冻结:在-70℃持续5分钟-回火/烧结:在500℃下持续30分钟并且,进行表面观察以分析对评价材料是否存在腐蚀。将其结果示于表2。[表2]当热轧钢板中的cu含量为0至2.0%时,热轧后材料的表面和边缘的质量是令人满意的,而当cu含量为2.5%以上时(对比实施例6),已经证实产生了大量的裂纹。其被认为这是由于加入大量cu而导致热加工性劣化引起的。另外,即使在分批退火处理之后,伸长率也小于18%。基于上述结果,可以看出,为确保良好的热加工性,cu含量应被限制在2%以下。另一方面,在添加用于提高耐腐蚀性的mo、w等的情况下(对比实施例7至10和实施例1至4),无论c的添加量为0.45至0.70%,都表现出良好的热轧性。相反,已经证实在分批退火处理后的冷轧的过程中,当c含量超过0.65%时,在冷轧钢板的边缘产生大量的裂纹并且在冷轧后的伸长率低至小于18%。其被认为这不仅是由于过量的c形成的粗的碳化物引起的,而且还由于添加的元素如w和cu的析出引起的。基于上述结果,可以看出,为确保良好的冷加工性,c的含量应被限制在0.65%以下。并且,通过观察退火材料的微结构,观察到碳化铬和cu析出相。首先,在对比实施例1至6中,可以看出,在恒定的c含量下,随着cu含量由0增加至2.5%,碳化铬的均匀性也随之增加。特别地,当cu含量大于1.5%时,由于可确保基体中碳化物的密度为90/100μm2以上,因此在客户自行进行的硬化热处理之后能够确保高硬度和优异的耐腐蚀性。另一方面,可以看出,当加入的cu含量增加1.5%以上时,分布于退火结构中的cu析出物为均匀分布,如图2(b)所示。更具体而言,当cu含量小于1.5%时,如图2(a)所示,非均匀cu析出相的形成可劣化抗菌性。相反,在图2(b)的情况下,其中添加1.5%以上的cu,cu析出相均匀地分布于基体中,因此其可表现出优异的抗菌性。基于上述结构,为确保高硬度、优异的耐腐蚀性和优异的抗菌性,cu的含量应为1.5%以上,不过,对于材料的高度可加工性而言,cu含量应被限制在1.5%至2.0%。此后,在使用热轧钢板完成硬化热处理之后,评价抗菌性,然后确认材料的表面是否存在生锈和腐蚀。首先,评价用于对比实施例1至6的材料(其不添加mo和w)的cu含量的抗菌性并观察所评价材料的表面腐蚀现象。其结果可以确定不管cu的添加量如何,抗菌性都高达99.9%然而,作为观察已被评价材料的表层的结果,可以确定的是,由于耐腐蚀性的劣化而加剧了表面腐蚀现象,如图3(a)所示。因此,尚不清楚表达抗菌活性是由材料本身含有的cu影响还是由铁锈或腐蚀溶出的fe离子影响。因此,为了获得可靠的定量评价结果,需要提高材料的耐腐蚀性,其不产生表层劣化,例如在评价抗菌性的过程中抑制材料的腐蚀现象。另一方面,在钢板添加了一定量的mo和w以提高耐腐蚀性的情况下(对比实施例7至10和实施例1至4),可以确定的是,在抗菌评价后,材料中没有形成表层分解(例如腐蚀现象),如图3(b)所示。即,设定cr、mo、w、n等的成分以使在上述等式1中表示的耐点蚀当量值(pren)的值为17以上,因此,可以确定的是,在评价抗菌性中没有观察到腐蚀现象。可以看出,在钢板不含cu的情况下(对比实施例7至9),显示抑菌率降至小于95%,而当钢板添加1.5%以上含量的cu的情况下(对比实施例10和实施例1至4),显示出99.9%的优异抗菌性,作为评估具有改善的耐腐蚀性的材料的抗菌性能的结果。基于上述结果,可以看出,当通过添加用于提高材料耐腐蚀性的元素如mo、w而将pren值设定为17以上时,当添加1.5%以上的cu时,不仅可确保优异的抗菌性,还可在评估抗菌性后抑制腐蚀现象,从而获得可靠地抗菌性以确保优异的抗菌性。根据上述结果,当将在根据本发明描述的条件下的分批退火处理和硬化热处理应用于马氏体不锈钢时,在根据jisz2801进行抗菌性评价后,没有观察到腐蚀现象并且获得了具有抑菌率为99.9%以上的优异抗菌性,其中所述马氏体不锈钢包括:0.45至0.65重量%的碳(c);0.02至0.06重量%的氮(n);0.1至0.6重量%的硅(si);0.3至1.0重量%的锰(mn);0.1至0.4重量%的镍(ni);13至14.5重量%的铬(cr);0.4至0.6重量%的钼(mo);0.8至1.2重量%的钨(w);1.5至2.0重量%的铜(cu);以及余量的铁(fe)和不可避免的杂质。如上所述,已经参考具体实施方案(例如特定构成要素,有限的实施例和附图)描述了本发明,但是应当理解,本发明不限于上述实施方案,并且本领域技术人员可在本发明的领域中对其进行各种修改和变化。因此,本发明的精神不应被解释为限于所描述的实施方案,并且所有等同物或权利要求的等同物以及所附权利要求均落入本发明的范围。当前第1页12