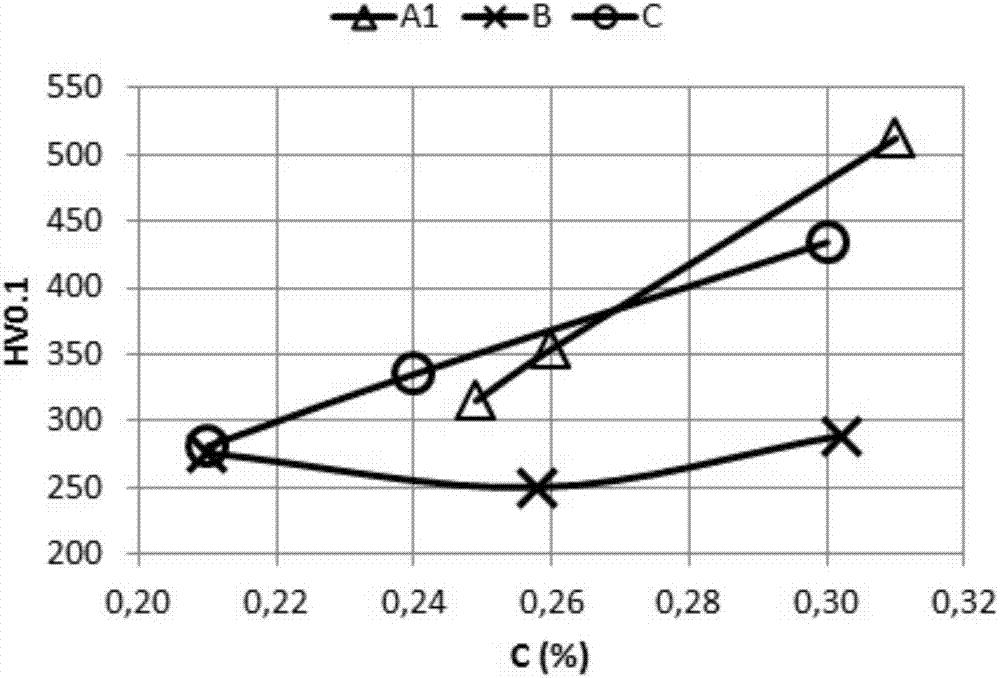
发明领域本发明涉及预合金化铁基粉末。本发明特别涉及包括少量合金元素的预合金化铁基粉末,以成本有效地制造烧结零件,特别是齿轮。背景在工业中,通过压实和烧结金属粉末组合物制成的金属产品的应用变得越来越广泛。生产具有各种形状和厚度的许多不同产品。质量要求不断提高,同时希望降低成本。使用单轴压制的粉末冶金(pm)技术能够成本有效地制造部件,尤其是在长序列中制造复杂部件时,因为不需要昂贵的机械加工就可制造净形状(netshape)或近净形状部件。但是,使用单轴压制的pm技术的一个缺点在于,烧结零件表现出一定孔隙度,这可能不利地影响该零件的机械性质。pm工业内的发展因此涉及基本沿两个不同的发展方向克服孔隙度的负面影响。一个方向是通过将粉末压实至较高生坯密度(gd)、促进烧结至高烧结密度(sd)和/或在生坯体(greenbody)收缩至高sd的条件下进行烧结来降低孔隙量。也可以通过不同种类的表面致密化操作除去部件表面区域(在此孔隙度对机械性质最有害)的孔隙以消除孔隙度的负面影响。另一发展路径集中于添加到铁基粉末中的合金元素。合金元素可作为混合粉末添加;完全预合金化到基础铁粉中;或通过所谓扩散结合法结合到基础铁粉的表面上。碳通常以石墨形式混入以避免粉末硬度的有害提高和可压缩性的降低(如果预合金化)。其它常用合金元素是铜、镍、钼和铬。但是,合金元素,尤其是镍、铜和钼的成本使得这些元素的添加不那么有吸引力。在废料再循环过程中铜也会累积,因此此类再循环材料不适用于不需要铜或需要最低限度铜的许多钢等级。由于低成本和优异的可硬化效应,铬更有吸引力。us4266974公开了仅含锰和铬作为有意加入的合金元素的在所要求保护的范围外的合金粉末的实例。这些实例含有2.92%的铬及0.24%的锰,4.79%的铬及0.21重量%的锰,或0.55%的铬及0.89重量%的锰。jp59173201公开了含有铬、锰和钼的低合金钢粉的还原退火方法。一个实例显示具有1.14重量%的铬含量和1.44重量%的锰含量作为仅有的有意加入的合金元素的粉末。在us6348080中公开了铬、锰和钼基预合金化钢粉。wo03/106079公开了具有比us6348080中描述的钢粉低的合金元素含量的铬、锰和钼合金化钢粉。该粉末适合在高于大约0.4重量%的碳含量下形成贝氏体结构。近年来,工业中对通过pm工艺制造用于汽车用途的部件,如齿轮和同步毂(synchronizationhub)表现出提高的兴趣,因为此类部件在长序列(longseries)中制造并通常具有适合这种制造法的尺寸和形状。但是,已经表明,难以获得对此类部件而言足够的强度和硬度以耐受此类部件经受的恶劣环境。为了克服这些问题,必须采用附加工艺步骤,如表面致密化,以获得足够的表面硬度和尺寸公差(dimensionaltolerance)。也遇到与烧结部件的硬化相关的问题,因为在采用通过在常压下气体渗碳接着在油中淬火的传统表面硬化工艺时,该部件中的孔隙率使得难以控制表面硬化层深度。此外,pm齿轮的传统表面硬化造成含有氧化敏感的合金元素,例如铬的粉末材料氧化的问题。因此,需要用于制造针对高负荷状况(stressfulconditions)的pm部件的改进的材料和方法。发明概述能够更好控制pm零件的表面硬化层深度以及将cr合金材料的氧化问题减至最低的一种备选的表面硬化法是低压渗碳(lpc)和随后高压气淬(hpgq)。结合高温真空烧结与通过lpc-hpgq法热处理的炉技术提供成本有效地制造优质pm部件,如齿轮和同步毂的优异可能性。这种技术也非常适用于加工成本有效的铬合金粉末钢材料。用于例如齿轮和同步毂的此类粉末材料的关键特征是高可压缩性(能够压实至高部件密度)、高纯度(以避免夹杂物对机械性质的有害作用)和对lpc-hpgq法优化的可硬化性(以在气淬(gasquenching)后在齿轮中提供所需微结构)。本发明包括旨在具有所有上述关键特征的新型低成本低(lean)预合金化铁基粉末。因此,尽管该合金粉末中的合金元素含量低并且与传统油淬火相比hpgq的冷却速率相对较低,但该材料的可硬化性足以提供通过该新型方法制成的pm部件,如齿轮和同步毂的优异性质。术语低压渗碳在本文中也意在包括低压碳氮共渗(carbonitriding)。详述在本发明的第一方面中,提供一种预合金化铁基粉末,其由下列成分构成:-0.7-0.9重量%的铬(cr);-0.2-0.4重量%的钼(mo);-0.01-0.15重量%的锰(mn);-最多0.20重量%的氧(o);-最多0.05重量%的碳(c)-少于0.05重量%的氮(n)-最多0.3的其它不可避免的杂质;和-余量铁(fe)。在第一方面的一个实施方案中,提供一种预合金化铁基粉末,其中o量为最多0.15重量%。在第一方面的另一实施方案中,提供一种预合金化铁基粉末,其中mn的量为0.09-0.15重量%。在第一方面的另一实施方案中,提供一种预合金化铁基粉末,其中mn的量为0.01-0.09重量%。在第一方面的另一实施方案中,提供一种预合金化铁基粉末,其中如根据astmb796-02测得,其最长维度大于100微米的夹杂物的数量为最多1.0/cm2。在第一方面的另一实施方案中,提供一种预合金化铁基粉末,其中如根据astmb796-02测得,其最长维度大于150微米的夹杂物的数量为最多0.0/cm2。在本发明的第二方面中,提供一种铁基粉末混合物,其包含或含有:-根据第一方面或实施方案的预合金化铁基粉末;-所述铁基粉末混合物的0.2-0.7重量%的量的石墨;-任选地,所述铁基粉末混合物的最多1重量%的量的润滑剂;-任选地,所述铁基粉末混合物的最多1重量%的量的机械加工性增强剂;和-任选地,硬相材料。在本发明的第三方面中,提供一种制造烧结部件的方法,其包含步骤:-a)提供根据权利要求8的铁基粉末混合物;-b)将所述铁基粉末混合物转移到压实模具中;-c)在至少600mpa的压实压力下将所述铁基粉末混合物压实成生压坯(greencompact);-d)从模具中推出所述生压坯;-e)对所述生压坯施以烧结步骤;-f)任选进一步增密(densify)所述烧结部件;-g)在含碳气氛中在最多40毫巴,优选最多20毫巴的压力下对所述烧结部件施以低压渗碳(lpc);-h)在10至30巴的压力下和以至少5℃的冷却速率从大约850-1000℃的温度到至少低于大约300℃对所述渗碳部件施以高压气淬hpgq;和-i)任选在空气中在150-300℃的温度下对所述淬火部件施以回火。在本发明的第三方面的一个实施方案中,提供一种方法,其中推出后的生压坯(来自上述步骤d)具有至少7.10克/立方厘米,优选至少7.15克/立方厘米,最优选至少7.20克/立方厘米的生坯密度。在本发明的第三方面的一个实施方案中,提供一种方法,其中所述烧结步骤包括在还原气氛中或在在最多20毫巴压力下的真空中在1000℃至1350℃,优选1200℃至1350℃的温度下烧结。在本发明的第三方面的一个实施方案中,提供一种方法,其中烧结过程中的还原气氛含有氢气。在本发明的第三方面的一个实施方案中,步骤f)由表面致密化或热等静压(hotisostaticpressing,hip)构成。在本发明的第三方面的一个实施方案中,提供一种方法,其中低压渗碳步骤包括在含有c2h2、ch4和c3h8的至少一种的气氛中渗碳。在本发明的第三方面的一个实施方案中,提供一种方法,其中所述低压渗碳步骤进一步包括在含氨气氛中渗碳。在本发明的第四方面中,提供通过第三方面或实施方案获得的部件。在本发明的第五方面中,提供一种烧结部件,其由下列成分构成:-0.7-0.9重量%的铬(cr),-0.2-0.4重量%的钼(mo),-0.01-0.15重量%的锰(mn),-0.2-1.0重量%的碳(c)-最多0.15重量%的氧(o),-最多1.0%,优选低于0.5重量%,最优选低于0.3重量%的非o的不可避免的杂质-余量铁(fe)在本发明的第五方面的一个实施方案中,提供一种烧结部件,其特征在于所述部件是齿轮。在本发明的第五或第四方面的一个实施方案中,提供一种烧结部件,其特征在于齿轮齿表面微硬度为至少700hv0.1,且齿轮齿芯(gearteethcore)硬度为300-550hv0.1。铁基预合金化钢粉的制备可通过含有指定量合金元素的钢熔体在保护性或非保护性气氛中的水雾化制造钢粉。可进一步对该雾化粉末施以如经此引用并入本文的us6,027,544中所述的还原退火法。该钢粉的粒度可以为任何尺寸,只要其与压制和烧结或粉末锻造法相容。在优选的粒度分布中,如根据ss-en24-497测得,20重量%或更少的粉末高于150微米,且最多30重量%或更少的粉末低于45微米。在另一优选粒度分布中,10重量%或更少的粉末高于75微米且至少30重量%或更多的粉末低于45微米。钢粉的含量铬cr用于通过固溶体硬化(solidsolutionhardening)增强该基质。cr还提高烧结体的可硬化性和耐磨性。但是,高于铁基粉末的0.9重量%的cr含量会降低该钢粉的可压缩性。低于0.7重量%的cr含量对所需性质,如可硬化性和耐磨性的作用不足。低于0.7重量%cr时,获得仅微不足道的可压缩性提高。钼mo,如同cr,通过固溶体硬化增强该基质并提高可硬化性。但是,与cr相比,mo对钢粉的可压缩性具有较低负面影响并对烧结部件具有较高可硬化性作用。但是,mo相对昂贵。因此mo含量为该铁基粉末的0.2-0.4重量%。锰mn,如同cr,提高钢粉的强度、硬度和可硬化性。但是,低mn含量通常合意,且高于0.15重量%的含量会不利地增加钢粉中的含锰夹杂物的形成,也会由于固溶体硬化和提高的铁素体硬度而对可压缩性具有负面影响。如果mn含量低于0.01重量%,获得如此低含量的成本不合理地高。对于mn的正面作用比负面作用占优势的一些用途,0.09-0.15重量%的较高mn区间是合意的。对于另一些用途,例如承受高负荷的部件,较低mn含量是合意的,如在0.01-0.09重量%区间内的mn含量。氧o优选为最多0.20重量%,以防止与铬和锰形成氧化物,因为这些氧化物损害该粉末的强度和可压缩性。由于这些原因,o优选为最多0.15重量%。该钢粉中的碳c应该为最多0.05重量%,更高含量会不可接受地降低该粉末的可压缩性。由于相同原因,氮n应保持少于0.05重量%。包括o、c和n的不可避免的杂质的总量应小于1.0重量%,优选地,除o、c和n外的不可避免的杂质的总量应该最多0.3重量%以不损害钢粉的可压缩性或充当有害夹杂物的前体(former)。部件如齿轮或同步毂用于例如汽车用途的前提条件是高的防故障可靠性,这尤其与高和受控疲劳强度相关联。为了获得所需性质,不仅合金元素cr和mo的精确和谨慎的组合是重要的,该钢粉中的夹杂物的低数量和受控最大尺寸也是重要的。该新型预合金化铁基粉末的特征在于最长维度大于100微米的夹杂物的数量为最多1.0/cm2。最长维度大于150微米的夹杂物的数量为最多0.0/cm2,如根据astmb796-02测得。铁基粉末混合物组合物在压实之前,将该铁基钢粉与石墨和润滑剂混合。以该组合物的0.2-0.7重量%的量加入石墨,并以该组合物的0.05-1.0重量%的量加入润滑剂。在某些实施方案中,可以各自以最多2重量%的量加入粉末形式的铜和/或镍。石墨为了提高该烧结部件的强度和硬度,在基质中引入碳。碳以石墨形式以该组合物的0.2-0.7重量%的量添加。少于0.2重量%的量会导致太低的强度,高于0.7%的量会导致太高的硬度、不足的伸长和损害最终部件的可机械加工性。获得300-550hv0.1的芯硬度所需的在铁基粉末混合物的0.2-0.7重量%区间内的确切石墨量取决于部件尺寸和冷却速率并可由本领域技术人员确定。铜和/或镍铜cu和镍ni是粉末冶金技术中常用的合金元素。cu和ni会通过固溶体硬化提高强度和硬度。cu也促进烧结过程中烧结颈的形成,因为cu在达到烧结温度之前熔融,以提供比固态烧结快得多的所谓的液相烧结。在某些实施方案中,cu和/或ni可以各自以最多2重量%的量添加到该铁基粉末混合物中。润滑剂将润滑剂添加到该组合物中以促进压实和压实部件的推出。少于该组合物的0.05重量%的润滑剂的添加具有微不足道的作用,高于该铁基粉末混合物的1重量%的添加会造成压实体的低密度。润滑剂可选自金属硬脂酸盐、蜡、脂肪酸及其衍生物、具有润滑作用的低聚物、聚合物和其它有机物。其它物质可以加入其它物质,如硬相材料和机械加工性增强剂,如mns、mos2、caf2、不同种类的矿物等。制造烧结部件的方法固结将该铁基粉末混合物转移到模具中并通过例如至少600mpa的单轴压实压力施以固结至至少7.10克/立方厘米,优选至少7.15克/立方厘米,最优选至少7.20克/立方厘米的生坯密度。烧结所得压实生坯部件进一步在还原气氛,如90体积%氮气和10体积%氢气中在大气压下或在减压下(在例如最多20毫巴压力下的所谓真空烧结)在1000-1350℃,优选1200-1350℃的温度下烧结15分钟至120分钟。在真空烧结的一个优选实施方案中,使用氢气或氢气和氮气的混合物作为低压还原气氛以确保部件中的氧化物的有效还原。任选进一步致密化在烧结步骤后,可以对该烧结部件施以任选的进一步致密化,如hip或通过例如表面辊轧的表面致密化。硬化在烧结后,在含有含碳物质,如ch4、c2h2和c3h8或其混合物的低压气氛(即最多40毫巴,优选最多20毫巴)中对该部件施以表面硬化工艺(即低压渗碳,lpc)。在温度已从烧结温度降至比奥氏体化温度高最多大约100℃的温度(即850-1000℃的温度)时,在炉中引入该含碳物质。或者,如果该部件在烧结后冷却至比850-1000℃低的温度,在lpc炉中引入含碳物质前将该部件加热到比奥氏体化温度高最多大约100℃的温度。在渗碳温度下的总停留时间为大约15-120分钟。通过在奥氏体化温度以上的低和受控温度下进行渗碳,可以将该部件的晶粒生长和变形减至最低。在短时期内将含碳物质引入炉中,有时被称作增进周期(boostcycle)。该增进周期可重复多次。在各增进周期后接着可被称作扩散周期的时期。当作为低压渗碳进行lpc工艺时,也将含氮物质(优选为氨形式)引入炉中。淬火在渗碳步骤后,该部件在惰性气氛中在高压下淬火,即高压气淬hpgq。淬火气体的实例是氮气、n2和氦气he。在10至30巴的压力下进行淬火,以使从大约850-1000℃的温度到至少低于大约300℃的冷却速率为至少5℃/s。回火为了消除应力,可以在空气中在150-300℃的温度下对该最部件施以回火15-120分钟。最终部件的性质根据本发明的预合金化铁基粉末和指定制造法的组合能够制造例如齿轮,其中轮齿具有硬马氏体表面层和主要由贝氏体和/或珠光体构成的较软芯。该马氏体表面层应具有最低700hv0.1的微硬度并且芯微硬度应优选为300-550hv0.1。这样的齿轮具有有利的应力分布,即在表面层中有利的压缩应力。此外,最终pm齿轮部件具有大约0.3-1.5mm的严格控制的表面硬化层深度,即其中硬度为550hv0.1。图例图1显示实施例1中研究的材料的极限抗拉强度(uts)vs碳含量。图2显示实施例1中研究的材料的微硬度(hv0.1)vs碳含量。图3显示实施例2中所用的pm齿轮样品(以毫米测量)。图4显示实施例2中的热处理试样的齿轮齿横截面的金相图。图5显示在实施例2中的热处理试样的齿轮齿上测得的微硬度(hv0.1)分布图。图6显示试样(在用700mpa压实压力单轴压实后)的生坯密度(gd)(可压缩性)vs实施例3中的试验混合物中所用的预合金化钢粉的cr含量。实施例实施例1根据本发明的预合金化钢粉a1通过水雾化、接着还原退火工艺制造。在小型(15千克熔体量)水雾化装置中在保护性n2气氛中进行雾化。在实验室规模的带式炉中在h2气氛中在1000-1100℃的温度下进行退火。在退火后进行粉末的研磨和筛分(-212m)。该粉末的化学组成与其它两种商业级预合金化钢粉(b=85mo,c=可获自ab,sweden,并用作参考材料)的组成一起列在表1中。所有三种粉末具有用于pm的标准粒度分布并用-212μm筛网尺寸筛分。表1.化学组成(重量%)粉末fe(%)cr(%)mo(%)mn(%)o(%)c(%)a1基础0.900.340.030.03<0.01b基础0.030.850.090.07<0.01c基础1.800.040.090.14<0.01通过圆柱形试样(直径25毫米,高度20毫米)在润滑模头中在600mpa压实压力下的单轴压实评估钢粉的可压缩性。通过根据阿基米德原理在空气和水中称重试样,测量各试样的生坯密度(gd)。结果列在表2中并且表明粉末a1具有明显优于粉末c的可压缩性和与粉末b相当的可压缩性。表2.可压缩性(600mpa压实压力,润滑模头)粉末gd(g/cm3)a17.13b7.15c7.05将钢粉与0.25-0.35重量%石墨(kropfmühluf4)和0.60重量%润滑剂(lubee,可获自ab,sweden)混合。由该粉末混合物通过在700mpa的压实压力下单轴压实制造根据iso2740的标准拉伸试验棒。该试验棒的生坯密度为大约7.25克/立方厘米。该试验棒在n2/h2(95/5)气氛中在1120℃下烧结30分钟。烧结试样的热处理在真空(10毫巴)中在920℃下进行60分钟,接着用20巴n2高压气淬。在这种热处理操作中不进行渗碳,因为该实验的目的是评估该合金在通过将石墨添加到该粉末混合物中得出的碳含量下的可硬化性。随后在空气中在200℃下进行回火60分钟。对热处理的试样进行拉伸试验。试验结果表明a1和c在研究的碳含量范围内具有大约750-1130mpa的类似极限抗拉强度(uts)值;见图1。材料b在所有碳含量下具有低于600mpa的明显更低uts值。也在热处理的试样的抛光横截面上进行微硬度测量(根据vickers方法的hv0.1);见图2中的结果。材料a1在0.25-0.31%c范围内的碳含量下具有310-510hv0.1的微硬度值。材料b甚至在最高评估碳含量(0.30%c)下也具有低于300hv0.1的相对较低微硬度。材料c的微硬度值与材料a1比较相当。这一实施例证实粉末a1具有pm齿轮材料的性质的有吸引力的组合。高可压缩性允许压实到高密度,且可硬化性足以提供300-550hv0.1的微硬度值。这是在用于高负荷传动用途的齿轮制造中在表面硬化后齿轮齿芯硬度的所需硬度范围。评估的碳含量相当于在齿轮齿的芯区域中的典型碳含量。实施例2根据本发明的预合金化钢粉a2通过水雾化、接着还原退火工艺制造。在小型(15千克熔体量)水雾化装置中在保护性n2气氛中进行雾化。在实验室规模的带式炉中在h2气氛中在1000-1100℃的温度下进行退火。在退火后进行粉末的研磨和筛分(-212m)。该粉末的化学组成列在表2中。该粉末具有用于pm的标准粒度分布并用-212μm筛网尺寸筛分。表2.化学组成(重量%)粉末fe(%)cr(%)mo(%)mn(%)o(%)c(%)a2基质0.850.300.040.06<0.01将粉末a2与0.40重量%石墨(c-uf)和0.60重量%润滑剂(lubee)混合。由该粉末混合物通过在700mpa的压实压力下单轴压实,压实大齿轮试样(参见图3中的尺寸)。该齿轮试样的生坯密度为7.20克/立方厘米。该齿轮试样在n2/h2(95/5)气氛中在1250℃下烧结30分钟。通过在965℃下低压渗碳(lpc)接着用20巴n2高压气淬进行烧结齿轮的表面硬化。lpc工艺中的基础气氛是n2(8毫巴压力)且渗碳气体是c2h2/n2(50/50)。施加四个渗碳增进周期,各增进周期的长度为37-65秒。各增进周期后的扩散时间在312-3550秒之间不等。在965℃下的总时间为96分钟。在气淬后随后在空气中在200℃下进行回火60分钟。对热处理的齿轮试样的抛光和蚀刻横截面进行的金相检查表明,该齿轮齿具有马氏体表面层和贝氏体芯结构;见图4。也在抛光横截面上进行微硬度测量(根据vickers方法的hv0.1)以研究齿轮齿的硬度分布图,见图5中的结果。这些测量表明表面硬度高于800hv0.1且芯硬度为320-340hv0.1,齿根处的硬度水平略低于侧面。表面硬化层深度(其中硬度为550hv0.1)在侧面为0.8毫米且在根部为0.6毫米。这一实施例证实粉末a2适用于在通过lpc-hpgq法进行表面硬化的方法中制造高强度pm齿轮。在该粉末混合物中使用该铁基粉末混合物的0.40重量%的石墨含量以在施加hpgq时在大齿轮部件内获得的冷却速率下为该合金提供足够的可硬化性。该粉末的高可压缩性允许压实到齿轮的高密度,并在热处理后在齿轮齿的表面处和在芯区域中都获得所需水平的硬度值。也实现界限分明的表面硬化层深度。实施例3通过水雾化、接着还原退火工艺制造具有不同cr含量(0.5-1.0%)和相同mo含量(0.3%)的预合金化钢粉。在小型(15千克熔体量)水雾化装置中在保护性n2气氛中进行雾化。在实验室规模的带式炉中在h2气氛中在1000-1100℃的温度下进行退火。对所有粉末使用相同退火参数。在退火后进行粉末的研磨和筛分(-212m)。粉末的化学组成列在表3中。表3.化学组成(重量%)粉末fecr(%)mo(%)mn(%)o(%)c(%)x1基础0.570.300.040.11<0.01x2基础0.760.320.030.13<0.01x3基础0.830.320.040.13<0.01x4基础0.920.330.030.12<0.01x5基础1.000.320.030.11<0.01将钢粉与0.25/0.35重量%石墨(kropfmühluf4)和0.60重量%润滑剂(lubee,可获自ab,sweden)混合。通过圆柱形试样(直径25毫米,高度20毫米)在700mpa压实压力下的单轴压实评估粉末混合物的可压缩性。通过根据阿基米德原理在空气和水中称重试样,测量各试样的生坯密度(gd)。结果列在图6中并且证实具有0.7-0.9重量%cr和0.3重量%mo的合金化含量(符合本发明)的预合金化铁基粉末产生高可压缩性且cr含量应该为最多0.9重量%。低于0.7重量%的cr含量不会显著提高可压缩性,即产生更高生坯密度(gd)。当前第1页12