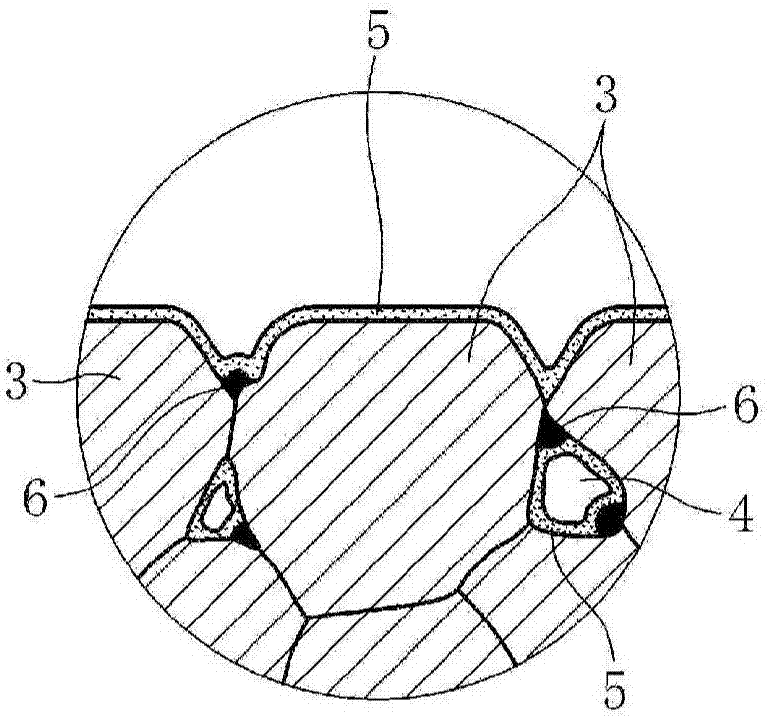
本发明涉及烧结轴承,特别是涉及al-cu合金(也被称为铝青铜)系烧结轴承。
背景技术:
:作为发动机的燃料使用的汽油、轻油等的品质在世界各地有所不同,有的地区也使用粗劣的燃料(汽油、轻油等)、生物燃料等。对于设置在可能与这样的燃料接触的位置(例如电动燃料泵、egr阀)的轴承来说,要求具有针对粗劣燃料、生物燃料中含有的硫化物、有机酸的耐腐蚀性。另一方面,随着发动机的小型化和轻量化,对于电动燃料泵等要求小型化和轻量化,对于其中所安装的轴承也要求小型化。例如在电动燃料泵中,为了在确保喷出性能的同时达成小型化,需要提高转速。对于支承这样高速旋转的轴的轴承来说,在要求小型化的同时,还要求耐腐蚀性、耐磨耗性(低摩擦特性)。例如,作为耐磨耗性优异的轴承,已知有铜系烧结轴承。但是,铜系烧结轴承与粗劣燃料、生物燃料中含有的硫化物、有机酸接触时,铜容易发生腐蚀。例如,在硫化物与铜系烧结轴承接触时,在表面(特别是轴承面)生成硫化铜,从而使轴承面与轴之间的间隙减少,可能招致旋转扭矩的上升。另外,在有机酸与铜系烧结轴承接触时,铜会发生溶出,因而可能使耐磨耗性降低、制品寿命缩短。根据以上所述,铜系烧结轴承的耐磨耗性优异,但耐腐蚀性差,因而不适于与粗劣燃料、生物燃料接触的用途。例如在专利文献1中示出了al-cu合金系烧结轴承。al-cu合金系烧结轴承的滑动性优异,同时由于在表面生成氧化铝膜,因而耐腐蚀性也优异。现有技术文献专利文献专利文献1:日本特开2009-7650号公报技术实现要素:发明所要解决的课题在上述专利文献1中揭示了调整al-cu合金系烧结轴承中的各成分的混配比的技术。但是,即使应用这样的技术,也不能说耐腐蚀性得到了充分提高,要求进行进一步的研究。鉴于以上的情况,本发明的目的在于提高al-cu合金系烧结轴承的耐腐蚀性。用于解决课题的手段为了达成上述目的,本发明提供一种烧结轴承,该烧结轴承含有al、cu以及ni,并且al-cu-ni合金组织彼此被烧结,上述al-cu-ni合金组织具有al-cu-ni母相和al-ni化合物相、不具有al-cu化合物相。如此,通过在al-cu合金系烧结轴承中混配ni并使al-cu-ni母相(固溶体合金相)在合金组织中析出,耐腐蚀性提高。此时,在al-cu-ni合金组织中,通常不仅母相析出,而且耐腐蚀性低于母相的化合物相也析出。具体地说,al-cu化合物相的耐腐蚀性特别低,al-ni化合物相的耐腐蚀性高于al-cu化合物相。因此,在al-cu-ni合金组织中,若调整原料粉末的成分、混配比以使得耐腐蚀性特别差的al-cu化合物相不发生析出、耐腐蚀性比较优异的al-ni化合物相析出,则能够得到具有非常优异的耐腐蚀性的烧结轴承。上述的烧结轴承的组成例如含有7质量%~11质量%的al、1质量%~6质量%的ni,余部的主成分为cu。另外,在上述的烧结轴承中,即使混配si来替代ni,也能够得到与上述同样的效果。即,上述目的可利用下述烧结轴承来达成:该烧结轴承含有al、cu以及si,并且al-cu-si合金组织彼此被烧结,上述al-cu-si合金组织具有al-cu-si母相和al-si化合物相、不具有al-cu化合物相。该烧结轴承的组成例如含有7质量%~11质量%的al、1质量%~6质量%的si,余部的主成分为cu。此外,在上述的烧结轴承中,即使混配zn来替代ni,也能够得到与上述同样的效果。即,上述目的可利用下述烧结轴承来达成:该烧结轴承含有al、cu以及zn,并且al-cu-zn合金组织彼此被烧结,上述al-cu-zn合金组织具有al-cu-zn母相和al-zn化合物相、不具有al-cu化合物相。该烧结轴承的组成例如含有7质量%~11质量%的al、1质量%~5质量%的zn,余部的主成分为cu。另外,由于纯铜容易附着硫化物,因而在烧结轴承中若存在纯铜组织(cu相),则由于硫化物附着至cu相而容易发生硫化腐蚀。因此,在烧结轴承的原料中含有纯铜粉末的情况下,需要使al在cu相中扩散而进行合金化,烧结工序的成本增高。因此,上述烧结轴承的原料粉末优选不含有纯铜粉末。在使游离石墨在上述那样的烧结轴承的轴承面露出时,能够通过游离石墨自身的润滑性而使润滑性和耐磨耗性提高。对于设置在燃料泵的用于支承轴的旋转的轴承、或者设置在egr阀的用于支承阀在轴向的往复移动的轴承来说,它们与燃料等中含有的硫化物、有机酸接触,要求优异的耐腐蚀性。作为在这样的用途中所使用的轴承,能够适当地使用上述的烧结轴承。发明效果如上所述,根据本发明,能够提高al-cu合金系烧结轴承的耐腐蚀性。附图说明图1是本发明的实施方式的烧结轴承的截面图。图2是上述烧结轴承的放大截面图。图3是上述烧结轴承的al-cu-ni合金组织的放大图。图4是其他实施方式的烧结轴承的al-cu-si合金组织的放大图。图5是其他实施方式的烧结轴承的al-cu-zn合金组织的放大图。图6是燃料泵的截面图。图7是egr阀的截面图。图8是比较例的试验片的al-cu合金组织的放大图。图9是表示腐蚀试验的结果的曲线图。具体实施方式如图1所示,本发明的一个实施方式的烧结轴承1形成圆筒状,在内周插入轴2。烧结轴承1的内周面1a为圆筒面,作为滑动支承轴2的外周面的轴承面发挥功能。烧结轴承1的外周面1b为圆筒面,作为安装于其他部件的安装面发挥功能。烧结轴承1由烧结金属、特别是al-cu合金系烧结金属形成,在本实施方式中,由包含al、cu和ni的烧结金属形成。具体地说,烧结轴承1例如含有7质量%~11质量%的al、1质量%~6质量%的ni,余部的主成分为cu。在本实施方式中,除了上述成分以外,相对于al、cu、ni的总量100质量%,还含有3质量%~6质量%的石墨(游离石墨)、以及0.1质量%~0.4质量%的p。在本实施方式中,烧结轴承1含有8.5质量%的al、5质量%的ni,余部的主成分为cu。如图2中放大所示,烧结轴承1具有al-cu-ni合金组织3,相邻的al-cu-ni合金组织3彼此烧结结合。在al-cu-ni合金组织3之间设有无数个内部空孔4。内部空孔4与烧结轴承1的表面连通。在al-cu-ni合金组织3的表面也即包含内周面1a(轴承面)的烧结轴承1的表面和烧结轴承1的内部空孔4的周围形成有氧化铝覆膜5。利用该氧化铝覆膜5保护al-cu-ni合金组织3,因而耐腐蚀性和耐磨耗性提高。游离石墨6分布在烧结轴承1的表面和内部。该游离石墨6的一部分在烧结轴承1的轴承面(内周面1a)露出。在al-cu-ni合金组织3的晶界部存在p(磷)(省略图示)。图3中进一步放大示出al-cu-ni合金组织3。如该图所示,al-cu-ni合金组织3具有al-cu-ni母相(α相)、以及al-ni化合物相(κ相),另一方面,其不具有al-cu化合物相(γ相)。换言之,以下述范围来设定al-cu-ni合金组织3的组成(al、cu、ni的混配比),该范围为在al-cu-ni三元相图中α相和κ相析出、且γ相不析出的范围。如此,通过使耐腐蚀性非常高的al-cu-ni母相析出,能够赋予烧结轴承1优异的耐腐蚀性。另外,在烧结轴承1中生成al-cu-ni合金组织3时,实际上无法避免耐腐蚀性差的化合物相的析出,但如上所述通过使耐腐蚀性比较高的al-ni化合物相析出、不使耐腐蚀性特别低的al-cu化合物相析出,烧结轴承1的耐腐蚀性进一步提高。此时,优选al-cu-ni合金组织3中的al-cu-ni母相的比例高,例如以面积比计为50%以上、优选为70%以上,在图示例中大约为85%左右。烧结轴承1的密度比为80%~95%的范围。烧结轴承1的密度比小于80%时强度不充分,密度比大于95%时含油量不足,因而不优选。烧结轴承1的表层的密度比高于内部的密度比。即,烧结轴承1的表面的空孔率(表面开孔率)小于烧结轴承1的内部的空孔率。另外,烧结轴承1的外周面1b侧的表层的密度比高于内周面1a侧的表层的密度比。即,烧结轴承1的外周面1b的表面开孔率小于烧结轴承1的内周面1a的表面开孔率。需要说明的是,密度比α由下式来表示。α(%)=(ρ1/ρ0)×100其中,ρ1:多孔质体的密度、ρ0:假定该多孔质体中不存在空孔时的密度另外,烧结轴承1的表层是指从烧结轴承1的表面到规定深度(例如,烧结轴承1的内径的1/100~1/15左右的深度)的区域。在烧结轴承1的内部空孔浸渗有润滑油。作为润滑油,可以使用矿物油、聚α烯烃(pao)、酯、液态油脂等。其中,对于轴承的用途来说,不一定必须要浸渗润滑油,也可以在干燥状态下使用。在插入到烧结轴承1的内周的轴2进行旋转或轴向移动或者进行这两种运动而使烧结轴承1的内周面1a与轴2的外周面发生滑动时,保持在烧结轴承1的内部空孔中的润滑油随着温度上升渗出到内周面1a。利用该渗出到内周面1a的润滑油,在烧结轴承1的内周面1a与轴2的外周面之间的轴承间隙内形成油膜,轴2被烧结轴承1支承。接下来,对上述烧结轴承1的制造方法进行说明。烧结轴承1经下述工序形成:混合工序,将各种粉末混合得到原料粉末;压粉工序,将原料粉末利用模具压缩得到粉体压坯(压粉体);烧结工序,将粉体压坯烧结得到烧结体;以及精整工序,将烧结体利用模具压缩进行成型修整。下面对各工序进行详细说明。[混合工序]在混合工序中,通过利用混合机将各种粉末混合,生成原料粉末。原料粉末包含作为al源、cu源、ni源、p源以及固体润滑剂的粉末。在原料粉末中不包含纯cu粉末和纯al粉末。在原料粉末中根据需要进一步混合烧结助剂(例如氟化铝粉末或氟化钙粉末)、脱模用润滑剂(例如硬脂酸锌粉末或硬脂酸钙粉末)。下面对各粉末进行详细说明。作为al和cu源,可以使用例如al-cu-ni合金粉末、al-cu合金粉末。作为ni源,可以使用例如al-cu-ni合金粉末、cu-ni合金粉末。在本实施方式中,使用al-cu-ni合金粉末(预合金粉末)作为al、cu、ni源。al-cu-ni合金粉末包含7质量%~11质量%的al。al-cu-ni合金粉末可以使用例如通过雾化法制造的粉末。al-cu-ni合金粉末的粒径为106μm以下、平均粒径为20μm~50μm。需要说明的是,平均粒径是指通过激光衍射测定的粒径的平均值。具体地说,是利用(株)岛津制作所制造的sald-3100通过激光衍射对5000个粉末进行测定时的粒径的平均值(以下相同)。作为p源,可以使用p合金粉末。p合金粉末可以使用例如p-cu合金粉末,在本实施方式中使用7质量%~10质量%p-cu合金粉末。p具有提高烧结时的固液相间的润湿性的效果。p成分过少时,固液相间的烧结促进效果较差。另一方面,p成分过多时,烧结过度进行,al容易偏析。因此,p合金粉末的混合量例如如下进行设定:相对于al、cu以及ni的总量100质量%,使原料粉末中的p成分为0.1质量%~0.6质量%、优选为0.1质量%~0.4质量%。作为固体润滑剂,可以使用例如石墨粉末。石墨粉末主要以游离石墨的形式存在于烧结轴承1的空孔内和表面。特别是在轴承面(内周面1a)露出的石墨粉末赋予烧结轴承1优异的润滑性,有助于耐磨耗性的提高。相对于原料粉末中的al、cu、ni的总量100质量%,石墨粉末的混合量例如为3质量%~6质量%。石墨的混合量小于3质量%时,得不到添加石墨所带来的润滑性、耐磨耗性的提高效果。另一方面,石墨的混合量大于6质量%时,担心会开始阻碍例如al向cu中的扩散。石墨的混合量大于10质量%时,材料强度降低,会阻碍al向cu中的扩散,因而不优选。需要说明的是,通常若相对于原料粉末的主成分添加4质量%以上的石墨,则成型变得困难,但通过使用造粒石墨作为石墨粉末则能够进行成型。在本实施方式中,石墨粉末使用将天然石墨或人造石墨的微粉利用树脂粘结剂造粒后进行粉碎得到的粒径为145目以下的石墨粉末。氟化铝和氟化钙作为烧结助剂发挥功能。具体地说,氟化铝和氟化钙在850℃~900℃(该温度为al-cu-ni合金粉末的烧结温度)发生熔融同时缓慢地蒸发,保护al-cu-ni合金粉末的表面,抑制氧化铝的生成,从而促进烧结、增进铝的扩散。氟化铝和氟化钙在烧结时发生蒸发、挥散,因而在烧结轴承1的完成品中几乎无残留。相对于原料粉末中的al、cu、ni的总量100质量%,氟化铝和氟化钙优选共添加0.05质量%~0.2质量%的程度。氟化铝和氟化钙小于0.05质量%时,作为烧结助剂的效果不充分,得不到致密且具有高强度的烧结体。另一方面,氟化铝和氟化钙大于0.2质量%时,即使添加更多量,作为烧结助剂的效果也达到极限,因此从成本的方面考虑,优选限制在0.2质量%以下。需要说明的是,若无特别需要,则也可以不在原料粉末中混配p合金粉末、氟化铝和氟化钙等烧结助剂、石墨粉末等固体润滑剂以及硬脂酸锌等脱模用润滑剂中的一种或两种以上。[压粉工序]在压粉工序中,将上述的原料粉末填充到压粉模具中进行压缩,从而形成与烧结轴承1大致相同形状的粉体压坯。在本实施方式中,通过在200mpa~700mpa的压力下对填充在压粉模具中的原料粉末进行压缩来进行粉体压坯的成型。需要说明的是,也可以在将压粉模具加热到70℃以上的状态下进行粉体压坯的成型。在本实施方式的烧结轴承1中,al源仅由al-cu-ni合金粉末构成,原料粉末中不包含纯al粉末。由此可解决由于相对密度小的纯al粉末所引起的原料粉末流动性的劣化以及与纯al颗粒的飞散相伴的处理上的问题。据此,原料粉末在压粉模具中的填充性增高,因而能够避免成型性的降低或粉体压坯的强度不足。[烧结工序]在烧结工序中,在规定的烧结温度下对粉体压坯进行加热,使相邻的原料粉末彼此烧结结合,从而形成烧结体。烧结工序例如使用网带式连续炉来进行。通过对粉体压坯进行加热,相邻的al-ni-cu合金粉末(al-cu-ni合金组织)彼此烧结结合(扩散接合),形成烧结体。此时,利用原料粉末中含有的p成分促进al-cu-ni合金组织彼此的烧结、提高烧结体的强度。另外,原料粉末中的石墨粉末以游离石墨的形式残留在烧结体的内部和表面。在像这样得到的烧结体的al-cu-ni合金组织中,析出有al-cu-ni母相(α相)与al-ni化合粒相(κ相)析出,另一方面,未析出al-cu化合物相(γ相)(参照图2)。通过以得到这样的合金组织的方式来设定原料粉末的成分、混配比,可得到非常优异的耐腐蚀性。具体地说,例如,预先获取该烧结温度下的al-cu-ni的三元相图,根据该三元相图设定得到上述那样的组织的成分及其混配比,从而能够得到上述那样的烧结体。烧结温度优选为900℃~950℃、更优选为900℃~920℃。另外,气氛气体可以使用氢气、氮气或者它们的混合气体。烧结时间增长则耐腐蚀性提高,例如对于燃料泵中使用的烧结轴承1来说,烧结时间优选为20分钟~60分钟(例如30分钟)。若al-cu-ni合金粉末的共晶温度达到548℃以上,则产生各种液相。在产生液相时,粉体压坯发生膨胀,利用所产生的液相形成烧结颈后,收缩达到致密化,从而得到烧结体。此时,在烧结体的表层,al-cu-ni合金组织被氧化而阻碍烧结,达不到致密化,尺寸处于膨胀状态,因而担心烧结体的强度不足。但是,在烧结体的内部,al-cu-ni合金组织不容易被氧化,可充分进行烧结,因而能够充分确保烧结体的强度。[精整工序]在精整工序中,对于通过烧结而发生了膨胀的烧结体进行压缩来进行尺寸成型修整。具体地说,将芯棒插入到烧结体的内周,同时利用上下冲头将烧结体的轴向宽度限定在规定尺寸,在该状态下将它们一体地压入到模头的内周。由此,烧结体的外周面被模头压迫而进行成型,同时烧结体的内周面被芯棒的外周面挤压而进行成型。利用该精整工序,发生了膨胀的烧结体的表层被压缩,表层的密度大于内部的密度。另外,烧结体的外周面侧的表层的压缩量大于内周面侧的表层的压缩量,因而外周面侧的表层的密度大于内周面侧的密度。需要说明的是,在精整工序后,通过进一步对烧结体的内周面1a旋转精整,可以使在内周面1a(轴承面)开孔的空孔进一步减小。[含油工序]在含油工序中,润滑油浸渗到上述烧结体的内部空孔中。具体地说,在减压环境下将烧结体浸渍在润滑油中后,恢复常压,从而使润滑油浸渗到烧结体的内部空孔中。通过以上操作完成烧结轴承1。本发明并不限于上述的实施方式。例如,烧结轴承1的组成并不限于上述组成,也可以混配si来替代上述实施方式中的ni。具体地说,例如烧结轴承的组成可以为含有7质量%~11质量%的al、1质量%~6质量%的si,余部的主成分为cu。图4中示出了含有8.5质量%的al、2质量%的si、余部的主成分为cu的烧结轴承的al-cu-si合金组织。在该al-cu-si合金组织中,析出有al-cu-si母相(α相)和al-si化合物相(κ相),未析出al-cu化合物相(γ相)。al-cu-si合金组织中的al-cu-si母相的比例例如以面积比计为50%以上、优选为70%以上,在图示例中大约为75%左右。其他成分、制法等与上述的实施方式相同,因而省略说明。另外,也可以混配zn来替代上述实施方式中的ni。具体地说,例如烧结轴承1的组成可以为含有7质量%~11质量%的al、1质量%~5质量%(优选为1质量%~4质量%)的zn,余部的主成分为cu。图5中示出了含有8.5质量%的al、3质量%的zn,余部的主成分为cu的烧结轴承的al-cu-zn合金组织。在该al-cu-zn合金组织中,析出有al-cu-zn母相(α相)和al-zn化合物相(δ相),未析出al-cu化合物相(γ相)。al-cu-zn合金组织中的al-cu-zn母相的比例例如以面积比计为50%以上、优选为70%以上,在图示例中大约为80%左右。其他成分、制法等与上述的实施方式相同,因而省略说明。另外,除了上述实施方式的ni以外,还可以混配si或zn、或者这两者。另外,也可以混配si和zn来代替上述实施方式中的ni。上述的烧结轴承1例如被组装到图6所示的燃料泵(电动燃料泵10)中。电动燃料泵10具有大致圆筒状的金属制外壳11、固定在外壳11的上端部的合成树脂制马达罩12、固定在外壳11的下端部的金属制泵罩13和泵主体14。在外壳11的内部配置有马达的电枢15。设置于电枢15的轴2的轴向两端部被安装于马达罩12和泵罩13的烧结轴承1旋转自由地支承。在烧结轴承1的内部空孔中预先浸渗有润滑油。磁体16被固定在外壳11的内周面,该磁体16和电枢15以规定间隔在半径方向对置。在马达罩12设置有与通到燃料喷射阀的燃料供给管(省略图示)连接的喷出口17。在该喷出口17设置阻止燃料倒流的止回阀18。止回阀18利用弹簧19向关闭方向施力。在轴2的端部(图中下端)固定泵轮20。在图示例中,2个泵轮20设置在在轴向隔离开的2个位置。在泵主体14设置有吸入口21。在使电枢15和泵轮20一体旋转时,燃料箱内的燃料由吸入口21汲上来,通过外壳11的内部,由喷出口17喷出。旋转自由地支承电枢15的轴2的烧结轴承1处于经常与燃料(例如汽油)接触的环境下。另外,上述的烧结轴承1也可以安装在图7所示的egr阀30中。egr阀30具备:外壳31、配置在外壳31的内部的阀32、向关闭阀32的方向施力的弹簧33、以及向将阀32打开的方向进行驱动的驱动部34(例如步进马达)。在外壳31的内部形成气体流路35,在气体流路35的中途设置阀座36。阀32的轴32a在轴向滑动自由地被固定于外壳31的烧结轴承1支承。对于该烧结轴承1,在内部空孔中未浸渗润滑油,以干燥状态进行使用。在驱动部34停止的状态下,阀32通过弹簧33的施加力而被挤压到阀座36,由此构成气体流路35关闭的状态。另一方面,在对驱动部34进行驱动而使阀32向下方移动时,阀32从阀座36脱离,构成气体流路35打开的状态,由发动机喷出的尾气返回到发动机的吸气侧。接下来制作由组成不同的烧结金属构成的多个试验片(实施例1~4、比较例1~4),对它们实施腐蚀试验。各试验片具有下述表1所示的组成,利用上述所示的制法进行制作。下面对各试验片进行详细说明。【表1】alnisiznsncu实施例18.53.0---bal.实施例28.55.0---bal.实施例38.5-2.0--bal.实施例48.5--3.0-bal.比较例18.5--5.0-bal.比较例2-30~35---bal.比较例38.5----bal.比较例48.5---3.0bal.al-cu-ni系烧结体(实施例1、实施例2)其由使用含有al-cu-ni合金粉(其含有7质量%~11质量%al)的原料粉末制作的烧结体构成,含有8.5质量%的al、3.0质量%(实施例1)或者5.0质量%(实施例2)的ni,余部的主成分为cu。在该烧结体中生成的al-cu-ni合金组织中,确认到了al-cu-ni母相(α相)和al-ni化合物相(κ相)的析出(参照图3)。另外,未确认到al-cu化合物相(γ相)的析出。al-cu-si系烧结体(实施例3)其由使用含有al-cu-si合金粉(其含有7质量%~11质量%al)的原料粉末制作的烧结体构成,含有8.5质量%的al、2.0质量%的si,余部的主成分为cu。在该烧结体中生成的al-cu-si合金组织中,确认到了al-cu-si母相(α相)和al-si化合物相(δ相、κ相)的析出(参照图4)。另外,未确认到al-cu化合物相(γ相)的析出。al-cu-zn系烧结体(实施例4、比较例1)其由使用含有al-cu-zn合金粉(其含有7质量%~11质量%al)的原料粉末制作的烧结体构成,含有8.5质量%的al、3.0质量%(实施例4)或者5.0质量%(比较例1)的zn,余部的主成分为cu。在该烧结体中生成的al-cu-ni合金组织中,确认到了al-cu-zn母相(α相)和al-zn化合物相(δ相)的析出(参照图5)。另外,未确认到al-cu化合物相(γ相)的析出。铜镍合金系烧结体(比较例2)其由使用主要含有cu粉末和ni粉末的原料粉末制作的烧结体构成,含有30质量%~35质量%的ni。al-cu系烧结体(比较例3)其由使用含有al-cu合金粉(其含有7质量%~11质量%al)的原料粉末制作的烧结体构成,含有8.5质量%的al、余部的主成分为cu。在该烧结体中生成的al-cu合金组织中,确认到了al-cu母相(α相)和al-cu化合物相(γ相)的析出(参照图8)。al-cu-sn系烧结体(比较例4)其由使用含有al-cu合金粉(其含有7质量%~11质量%al)和sn粉末的原料粉末制作的烧结体构成,含有8.5质量%的al、3.0质量%的sn,余部的主成分为cu。在该烧结体中生成的al-cu-sn合金组织中,确认到了al-cu-zn母相(α相)和al-cu化合物相(γ相)的析出。将上述各试验片在含有硫化物和有机酸的溶液中浸渍规定时间,测定浸渍前后的重量变化率。其结果,如图9所示,实施例1~4在浸渍前后的重量几乎没有变化,与之相对,比较例1~4在浸渍前后的重量变化很大。具体地说,在比较例1、2、4中,通过上述浸渍处理,重量大幅减少(比较例1:-45.13%、比较例2:-8.25%、比较例4:-28.49%)。据认为,这是因为溶液中的有机酸使得烧结体中的al成分发生溶出。另外,在比较例3中,通过上述浸渍处理,重量大幅增加(+10.21%)。据认为,这是因为在烧结体上附着了硫化物。与之相对,在实施例1~4中,由于上述浸渍处理所致的重量变化率均被抑制得极小(大约小于0.5%)。由这些结果确认到,在实施例1~4中,在cu-al系烧结体中添加了适量的ni、si、zn中的任一种,该实施例1~4具有优异的耐腐蚀性,特别是具有al-cu-ni合金组织的实施例1和2具有非常优异的耐腐蚀性。符号说明1烧结轴承2轴3al-cu-ni合金组织4内部空孔5氧化铝覆膜6游离石墨10电动燃料泵30egr阀当前第1页12