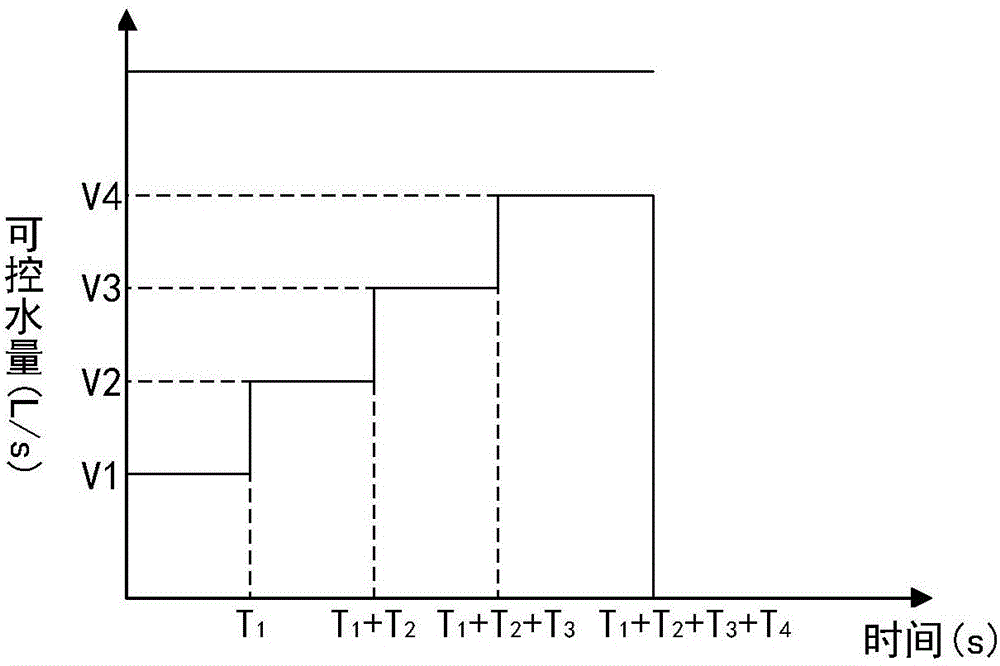
本发明总体来说涉及铁路车辆车轮,具体而言,涉及一种铁路车辆车轮的热处理方法。
背景技术:
:铁路车辆车轮一般采用铸造或锻造,然后进行热处理的方法生产,车轮1型式通常如图1所示,车轮1的重量一般在500KG左右,材质为碳素钢,车轮1与轨道接触的部位为轮辋11,接触面即为踏面12。一直以来,铁路车轮1的主要热处理方式为车轮1整体加热奥氏体化,然后踏面12进行喷水冷却淬火,该热处理方法要求在车轮轮辋11区域实现淬火,获得优异的细珠光体组织和非常重要的压应力,而在辐板和轮毂上实现正火处理,获得较好的韧性。但是近年来,随着铁路重载运输的需要,车轮1的强硬度、耐磨性、承载量要求越来越高,车轮1的含碳量越来越高,采用传统的低压力、恒定大水量的淬火难以避免在车轮表层产生贝氏体,使车轮组织变脆,服役性能下降。在碳含量接近0.77%的情况下,采用水冷的同时不允许出现贝氏体,逐渐成为车轮设计的基本技术要求,这逐渐成为车轮制造技术的难题之一。因此,需要提供一种铁路车辆车轮热处理方法,以解决上述技术问题,制造符合技术要求的铁路车辆车轮。技术实现要素:本发明的一个主要目的在于克服上述现有技术的至少一种缺陷,提供一种可以获得较细珠光体组织、同时有效避免激冷淬火时在车轮踏面表层产生贝氏体等硬脆组织的铁路车辆车轮热处理方法。本发明的另一个主要目的在于克服上述现有技术的至少一种缺陷,提供一种通过可以获得较细珠光体组织、同时有效避免激冷淬火时在车轮踏面表层产生贝氏体等硬脆组织的热处理方法所获得的铁路车辆车轮。为实现上述发明目的,本发明采用如下技术方案:根据本发明的一个方面,提供了一种铁路车辆车轮热处理方法,包括以下步骤:(1)车轮经整体加热完全奥氏体化;(2)采用恒定压力小流量喷水对所述车轮的踏面进行短时间冷却;(3)采用连续可控水量阶梯式喷水对所述车轮的踏面进行淬火,对所述车轮踏面以下形成均衡冷速,使整个车轮的轮辋区域获得均衡的细珠光体组织。根据本发明的一实施方式,所述步骤(2)和所述步骤(3)的总和时间为3-5分钟。根据本发明的一实施方式,所述步骤(2)的时间为30-50秒。根据本发明的一实施方式,所述步骤(2)中的所述恒定压力为0.8-0.9MPa。根据本发明的一实施方式,所述步骤(3)包括依次连续的第一阶段、第二阶段、第三阶段和第四阶段,其中,所述第一阶段的可控水量为V1,所述第二阶段的可控水量为V2,所述第三阶段的可控水量为V3,所述第四阶段的可控水量为V4,且V1<V2<V3<V4。根据本发明的一实施方式,所述第一阶段的时间为T1,所述第二阶段的时间为T2,所述第三阶段的时间为T3,所述第四阶段的时间为T4,T1<T2<T3<T4。根据本发明的一实施方式,V2-V1=A1,V3-V2=A2,V4-V3=A3,且A1<A2<A3。根据本发明的一实施方式,所述步骤(2)和所述步骤(3)中,所述车轮处于转动状态。根据本发明的一实施方式,所述车轮水平转动,喷水方向为水平朝向所述车轮的踏面。为实现上述发明目的,本发明还采用如下技术方案:根据本发明的一个方面,提供了一种铁路车辆车轮,所述车轮采用如上所述的热处理方法形成。由上述技术方案可知,本发明的铁路车辆车轮热处理方法的优点和积极效果在于:本发明中通过较高水压下小流量用于消除薄膜沸腾或缩短薄膜沸腾阶段,同时避免较高冷速形成贝氏体,此后采用连续可控水量阶梯式喷水淬火,对车轮踏面以下形成均衡冷速,使整个轮辋区域获得均衡的细珠光体组织,从而获得均衡的力学性能,即较高的强硬度和塑韧性,减小在车轮磨耗方向上的硬度梯度。附图说明通过结合附图考虑以下对本发明的优选实施例的详细说明,本发明的各种目标、特征和优点将变得更加显而易见。附图仅为本发明的示范性图解,并非一定是按比例绘制。在附图中,同样的附图标记始终表示相同或类似的部件。其中:图1是铁路车辆车轮的结构示意图。图2是根据一示例性实施方式示出的本发明铁路车辆车轮热处理方法中步骤(3)示意图。图3是根据一示例性实施方式示出的本发明铁路车辆车轮热处理方法中对车轮进行淬火的状态示意图。图4是本发明铁路车辆车轮轮辋截面硬度及梯度图。图5是本发明铁路车辆车轮踏面以下的微观组织测试图。图6是图5中1#样微观组织的金相照片。图7是图5中2#样微观组织的金相照片。图8是图5中3#样微观组织的金相照片。其中,附图标记说明如下:1、车轮;11、轮辋;12、踏面;2、喷头;R、车轮转动方向;V1、V2、V3、V4、可控水量;T1、T2、T3、T4、时间。具体实施方式现在将参考附图更全面地描述示例实施方式。然而,示例实施方式能够以多种形式实施,且不应被理解为限于在此阐述的实施方式;相反,提供这些实施方式使得本发明将全面和完整,并将示例实施方式的构思全面地传达给本领域的技术人员。图中相同的附图标记表示相同或类似的结构,因而将省略它们的详细描述。在对本发明的不同示例的下面描述中,参照附图进行,所述附图形成本发明的一部分,并且其中以示例方式显示了可实现本发明的多个方面的不同示例性结构、系统和步骤。应理解,可以使用部件、结构、示例性装置、系统和步骤的其他特定方案,并且可在不偏离本发明范围的情况下进行结构和功能性修改。而且,虽然本说明书中可使用术语“顶部”、“底部”、“前部”、“后部”、“侧部”等来描述本发明的不同示例性特征和元件,但是这些术语用于本文中仅出于方便,例如根据附图中所述的示例的方向。本说明书中的任何内容都不应理解为需要结构的特定三维方向才落入本发明的范围内。本发明提供了一种铁路车辆车轮,该车轮通过本发明的热处理方法形成。本发明的铁路车辆车轮热处理方法,包括以下步骤:(1)车轮经整体加热完全奥氏体化;(2)采用恒定压力小流量喷水对所述车轮的踏面进行短时间冷却;(3)采用连续可控水量阶梯式喷水对所述车轮的踏面进行淬火,对所述车轮踏面以下形成均衡冷速,使整个车轮的轮辋区域获得均衡的细珠光体组织。其中,所述步骤(2)和所述步骤(3)的总和时间为3-5分钟,所述步骤(2)的时间为30-50秒,但本发明并不以此为限,能够实现本发明目的时间取值,均属于本发明的上述时间的取值范围。所述步骤(2)中的所述恒定压力为0.8-0.9MPa,但本发明并不以此为限,能够实现本发明目的的恒定压力值,均属于本发明的恒定压力取值范围。而且本发明中,如图2所示,图2是根据一示例性实施方式示出的本发明铁路车辆车轮热处理方法中步骤(3)示意图。所述步骤(3)包括依次连续的第一阶段、第二阶段、第三阶段和第四阶段,其中,所述第一阶段的可控水量为V1,所述第二阶段的可控水量为V2,所述第三阶段的可控水量为V3,所述第四阶段的可控水量为V4,且V1<V2<V3<V4,也即在这四个阶段中,可控水量是在不断上升的。另外,所述第一阶段的时间为T1,所述第二阶段的时间为T2,所述第三阶段的时间为T3,所述第四阶段的时间为T4,且T1<T2<T3<T4),也就是说这四个阶段的用时是不断增加的。而对于相邻两阶段间的可控水量增量而言,其中,V2-V1=A1,V3-V2=A2,V4-V3=A3,且A1<A2<A3,也就是说水量的增量仍然是递增的。本发明的一实施例如图3所示,图3是根据一示例性实施方式示出的本发明铁路车辆车轮热处理方法中对车轮进行淬火的状态示意图。所述步骤(2)和所述步骤(3)中,所述车轮处于转动状态。该实施例中,所述车轮1水平转动,如箭头R所示,喷头2的喷水方向为水平朝向所述车轮1的踏面12。本发明中通过较高水压下小流量用于消除薄膜沸腾或缩短薄膜沸腾阶段,同时避免较高冷速形成贝氏体,此后采用连续可控水量阶梯式喷水淬火,对车轮踏面以下形成均衡冷速,使整个轮辋区域获得均衡的细珠光体组织,从而获得均衡的力学性能,即较高的强硬度和塑韧性,减小在车轮磨耗方向上的硬度梯度。本发明的方法最显著的优点是避免恒定水量淬火时表层冷速过高形成贝氏体组织(一种硬脆相,为车轮制造标准中明确杜绝的组织),内部冷速过缓导致硬度及淬硬深度不够。而且,根据车轮钢的CCT曲线,确定材料的临界冷却速度,通过设置几个淬火步骤,控制每一步淬火的喷水流量与喷水时间,可在轮辋区域获得一个恒定的冷却速度。这种连续、阶梯式递增、可控水量的淬火方式可保证车轮轮辋冷速的一致,使车轮轮辋区域的硬度梯度极大的减小,在整个车轮的磨耗区组织及性能状态趋于一致,可明显改善车轮的使用性能。采用上述热处理方法,对一种碳含量在0.67-0.77%、锰含量在0.60-0.90%、硅含量在0.15-1.0%的高碳钢重载铁路车轮进行热处理,热处理后车轮磨耗部位的硬度及其梯度如下图4所示,从图4中可以看出,车轮硬度较高,梯度合理,符合该类型车轮的设计原理。并对车轮踏面以下的微观组织进行测试(如图5所示),1#、2#、3#样的测试结果如下表1所示,金相照片分别见图6,图7,图8。从测试结果看,车轮微观组织均满足车轮使用要求,即车轮整体组织为有较好耐磨性,同时不存在贝氏体等硬脆相,保证车轮的使用安全。车轮踏面由表及里铁素体含量增加,硬度降低,符合车轮制造原理。由于高碳钢极易发生相变,一般淬火方法难免在车轮表层生成贝氏体等有害组织,采用本发明的热处理方法,有效避免了该问题。表1试样编号微观组织铁素体含量(%)1#细珠光体+少量铁素体0.102#细珠光体+少量铁素体0.243#细珠光体+少量铁素体0.42以上结合附图示例说明了本发明的一些优选实施例式。本发明所属
技术领域:
的普通技术人员应当理解,上述具体实施方式部分中所示出的具体结构和工艺过程仅仅为示例性的,而非限制性的。而且,本发明所属
技术领域:
的普通技术人员可对以上所述所示的各种技术特征按照各种可能的方式进行组合以构成新的技术方案,或者进行其它改动,而都属于本发明的范围之内。当前第1页1 2 3