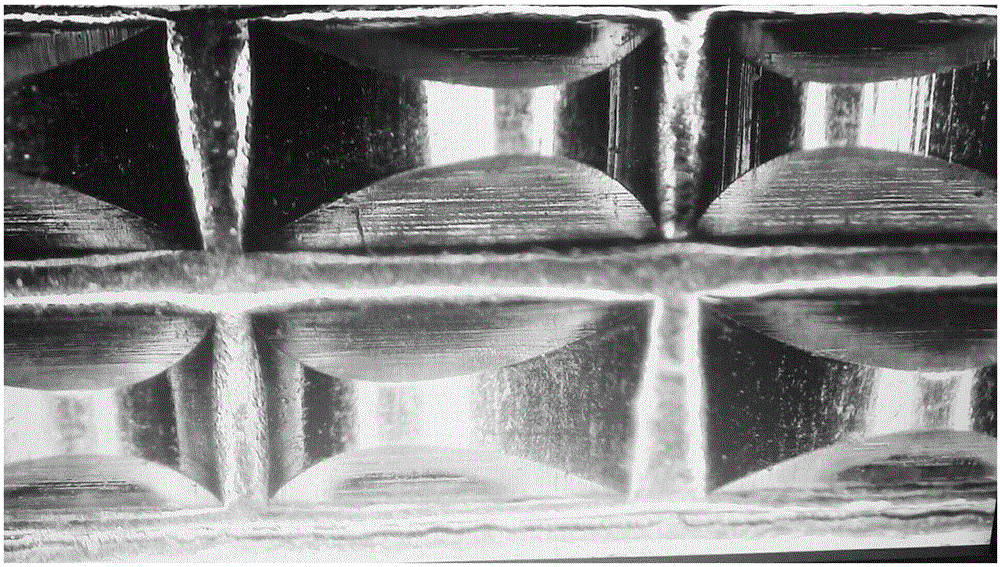
本发明涉及直线切割用底钉座表面加工
技术领域:
,具体的涉及直线切割用底钉座表面处理方法。
背景技术:
:直线切割用底钉座是直线形切割缝合器的重要部件,直线切割用底钉座通常采用模具压花形成底钉座花纹,然而在压制花纹的同时会造成底钉座毛刺增多的问题,并且底钉座本身表面较粗糙,亮度不够,不符合医用标准,因此需对底钉座进行表面处理,除去表面毛刺,提高底钉座表面的光亮程度。公开于该
背景技术:
部分的信息仅仅旨在增加对本发明的总体背景的理解,而不应当被视为承认或以任何形式暗示该信息构成已为本领域一般技术人员所公知的现有技术。技术实现要素:本发明的目的在于提供直线切割用底钉座表面处理方法,从而克服上述现有技术中的缺陷。为实现上述目的,本发明提供了直线切割用底钉座表面处理方法,包括以下步骤:(1)振动抛光,将直线切割用底钉座放入到装有抛光钢珠的振动抛光机中抛光处理1~2.5h,所述振动抛光机中按1:1比例添加有光亮剂和清洁剂,振动抛光去除底钉座表面的油脂和污渍;(2)磁力抛光,将经过步骤(1)振动抛光处理的底钉座转移到磁力抛光机中进行抛光处理20~40min,所述磁力抛光机中按1:1比例添加有光亮剂和清洁剂,磁力抛光去除底钉座死角处的油脂和污渍;(3)初步清洗,将经过步骤(2)处理的底钉座放置到循环水槽中进行初步清洗,清洗掉底钉座表面的光亮剂和清洁剂;(4)超声波清洗,将经过步骤(3)处理的底钉座放置到超声波清洗机中进行彻底清洗,彻底清洗掉底钉座死角处的油脂和污渍;(5)等离子处理,将经过步骤(4)处理的底钉座放置到装有抛光盐水溶液的等离子处理设备中进行表面等离子处理,所述等离子处理的条件为:温度90~100℃,电压305~400v,时间为0.5~30min;(6)后处理,对经过步骤(5)处理的底钉座进行清洗、风干获得处理后的成品。所述步骤(1)振动抛光所采用的抛光钢珠的直径为2~10mm。所述步骤(1)振动抛光所采用的光亮剂的组分为:苄叉丙酮5.5~10%,壬基酚聚氧乙烯醚8~15%,苯甲酸钠3~5%,烟酸0.3~0.8%,其余为水。所述步骤(5)抛光盐的组分为:硝酸盐65~80%、硫酸铵2.5~3.0%、一水柠檬酸0.5~1.0%、纳米二氧化硅粉末0.5~1.5%、纳米氧化锌粉末0.05~0.85%、其余为氯化钠。所述步骤(5)抛光盐的组分为:硝酸盐70~75%、硫酸铵2.8~3.0%、一水柠檬酸0.5~0.8%、纳米二氧化硅粉末0.5~1.0%、纳米氧化锌粉末0.06~0.5%、其余为氯化钠。所述步骤(5)抛光盐的组分为:硝酸盐73%、硫酸铵2.8%、一水柠檬酸0.6%、纳米二氧化硅粉末0.8%、纳米氧化锌粉末0.35%、其余为氯化钠。所述步骤(5)抛光盐水溶液的浓度为90g/l~150g/l。所述步骤(5)等离子处理是电流密度为120~200a/dm2。所述步骤(6)后处理时清洗采用超声波清洗的方式进行清洗,清洗3~5次,每次清洗60~1800s。所述步骤(6)后处理时风干采用风干机进行风干或者采用红外烘箱进行风干,所述风干机风干的速度为5m/min。与现有技术相比,本发明具有如下有益效果:本发明采用抛光清洗结合等离子处理,以及对等离子处理的工艺进行了优化,在等离子处理时抛光盐中加入纳米二氧化硅粉末以及纳米氧化锌粉末,能够获得表面细腻光亮的直线切割用底钉座,本发明的表面处理工艺简单,操作方便。附图说明:图1为本发明的实施例1的底钉座显微镜放大图;图2为本发明的实施例2的底钉座显微镜放大图;图3为本发明的实施例3的底钉座显微镜放大图;图4为未经过本发明处理的底钉座显微镜放大图。具体实施方式:下面对本发明的具体实施方式进行详细描述,但应当理解本发明的保护范围并不受具体实施方式的限制。除非另有其它明确表示,否则在整个说明书和权利要求书中,术语“包括”或其变换如“包含”或“包括有”等等将被理解为包括所陈述的元件或组成部分,而并未排除其它元件或其它组成部分。实施例1:直线切割用底钉座表面处理方法,包括以下步骤:(1)振动抛光,将直线切割用底钉座放入到装有抛光钢珠的振动抛光机中抛光处理2h,所述振动抛光机中按1:1比例添加有光亮剂和清洁剂,振动抛光去除底钉座表面的油脂和污渍,所述抛光钢珠的直径为5mm,所述光亮剂的组分为:苄叉丙酮8%,壬基酚聚氧乙烯醚10%,苯甲酸钠4%,烟酸0.5%,其余为水;(2)磁力抛光,将经过步骤(1)振动抛光处理的底钉座转移到磁力抛光机中进行抛光处理35min,所述磁力抛光机中按1:1比例添加有光亮剂和清洁剂,磁力抛光去除底钉座死角处的油脂和污渍;(3)初步清洗,将经过步骤(2)处理的底钉座放置到循环水槽中进行初步清洗,清洗掉底钉座表面的光亮剂和清洁剂;(4)超声波清洗,将经过步骤(3)处理的底钉座放置到超声波清洗机中进行彻底清洗,彻底清洗掉底钉座死角处的油脂和污渍;(5)等离子处理,将经过步骤(4)处理的底钉座放置到装有抛光盐水溶液的等离子处理设备中进行表面等离子处理,所述等离子处理的条件为:温度95℃,电压350v,时间为15min,电流密度为150a/dm2,所述步骤抛光盐的组分为:硝酸盐73%、硫酸铵2.8%、一水柠檬酸0.6%、纳米二氧化硅粉末0.8%、纳米氧化锌粉末0.35%、其余为氯化钠,抛光盐水溶液的浓度为120g/l;(6)后处理,对经过步骤(5)处理的底钉座进行清洗、风干获得处理后的成品,所述清洗采用超声波清洗的方式进行清洗,清洗4次,每次清洗1500s,所述风干采用风干机进行风干,风干的速度为5m/min。实施例2:直线切割用底钉座表面处理方法,包括以下步骤:(1)振动抛光,将直线切割用底钉座放入到装有抛光钢珠的振动抛光机中抛光处理2.5h,所述振动抛光机中按1:1比例添加有光亮剂和清洁剂,振动抛光去除底钉座表面的油脂和污渍,所述抛光钢珠的直径为8mm,所述光亮剂的组分为:苄叉丙酮10%,壬基酚聚氧乙烯醚15%,苯甲酸钠5%,烟酸0.8%,其余为水;(2)磁力抛光,将经过步骤(1)振动抛光处理的底钉座转移到磁力抛光机中进行抛光处理40min,所述磁力抛光机中按1:1比例添加有光亮剂和清洁剂,磁力抛光去除底钉座死角处的油脂和污渍;(3)初步清洗,将经过步骤(2)处理的底钉座放置到循环水槽中进行初步清洗,清洗掉底钉座表面的光亮剂和清洁剂;(4)超声波清洗,将经过步骤(3)处理的底钉座放置到超声波清洗机中进行彻底清洗,彻底清洗掉底钉座死角处的油脂和污渍;(5)等离子处理,将经过步骤(4)处理的底钉座放置到装有抛光盐水溶液的等离子处理设备中进行表面等离子处理,所述等离子处理的条件为:温度100℃,电压350v,时间为20min,电流密度为180a/dm2,所述步骤抛光盐的组分为:硝酸盐70%、硫酸铵2.9%、纳米氧化锌粉末0.5%、其余为氯化钠,抛光盐水溶液的浓度为150g/l;(6)后处理,对经过步骤(5)处理的底钉座进行清洗、风干获得处理后的成品,所述清洗采用超声波清洗的方式进行清洗,清洗5次,每次清洗1000s,所述风干采用风干机进行风干,风干的速度为5m/min。实施例3直线切割用底钉座表面处理方法,包括以下步骤:(1)振动抛光,将直线切割用底钉座放入到装有抛光钢珠的振动抛光机中抛光处理2h,所述振动抛光机中按1:1比例添加有光亮剂和清洁剂,振动抛光去除底钉座表面的油脂和污渍,所述抛光钢珠的直径为5mm,所述光亮剂的组分为:苄叉丙酮10%,壬基酚聚氧乙烯醚10%,烟酸0.5%,其余为水;(2)磁力抛光,将经过步骤(1)振动抛光处理的底钉座转移到磁力抛光机中进行抛光处理36min,所述磁力抛光机中按1:1比例添加有光亮剂和清洁剂,磁力抛光去除底钉座死角处的油脂和污渍;(3)初步清洗,将经过步骤(2)处理的底钉座放置到循环水槽中进行初步清洗,清洗掉底钉座表面的光亮剂和清洁剂;(4)超声波清洗,将经过步骤(3)处理的底钉座放置到超声波清洗机中进行彻底清洗,彻底清洗掉底钉座死角处的油脂和污渍;(5)等离子处理,将经过步骤(4)处理的底钉座放置到装有抛光盐水溶液的等离子处理设备中进行表面等离子处理,所述等离子处理的条件为:温度95℃,电压400v,时间为25min,电流密度为185a/dm2,所述步骤抛光盐的组分为:硝酸盐75%、硫酸铵3.0%、一水柠檬酸0.8%、其余为氯化钠,抛光盐水溶液的浓度为130g/l;(6)后处理,对经过步骤(5)处理的底钉座进行清洗、风干获得处理后的成品,所述清洗采用超声波清洗的方式进行清洗,清洗5次,每次清洗1600s,所述风干采用风干机进行风干,风干的速度为5m/min。采用显微镜对实施例1、实施例2及实施例3处理后的直线切割用底钉座的表面检测,放大倍数为80倍,显微镜照片如图1、图2和图3。对实施例1、实施例2、实施例3处理后的直线切割用底钉座的表面进行粗糙度的测试,实验结果如下:实施例1实施例2实施例3粗糙度(μm)0.050.080.15从实验结果看,采用本发明对直线切割用底钉座表面进行处理,能够获得表面较光洁细腻的底钉座,本发明工艺简单,操作便捷,能够保证底钉座的死角处表面处理均匀。前述对本发明的具体示例性实施方案的描述是为了说明和例证的目的,这些描述并非想将本发明限定为所公开的精确形式,并且很显然,根据上述教导,可以进行很多改变和变化。对示例性实施例进行选择和描述的目的在于解释本发明的特定原理及其实际应用,从而使得本领域的技术人员能够实现并利用本发明的各种不同的示例性实施方案以及各种不同的选择和改变。当前第1页12