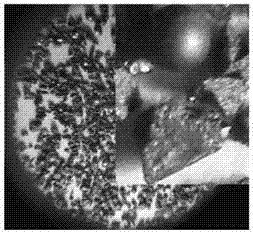
本发明属于不锈钢轧制
技术领域:
,尤其涉及一种降低热板抛丸处理后表面粗糙度的方法。
背景技术:
:随着不锈钢行业发展,客户需求多样化,为满足高档装饰材料的要求,带钢表面性能亟待于提高,特别是提高带钢表面质量,降低带钢表面粗糙度。现有技术中,不锈钢热轧退火后进行后续工序之前需要进行酸洗,即不锈钢热线酸洗,其目的是去掉热轧及退火过程中在钢带表面形成的铁鳞即氧化铁皮。由于不锈钢的铁鳞中含有与基体结合更为紧密的氧化铬,造成酸洗困难。因此,为提高酸洗效果,必须在酸洗之前进行酸洗前预处理。对于冷轧钢卷,酸洗前预处理通常采用化学除鳞法,而对于热轧不锈钢(即热板),酸洗前预处理一般采用机械破鳞法,例如抛丸处理、破鳞辊处理。抛丸处理是利用离心力使很小的钢丸以很高速度喷射在运行的带钢的表面,将钢丸的动能转化为对带钢的表面的冲击力,使得带钢的氧化皮从基体脱离,从而达到清除带钢表面铁鳞的效果。抛丸处理的质量取决于抛丸机料仓内钢丸的质量、数量、喷射速度、冲击方向、粒度混合比。在质量、喷射速度、冲击方向可以得到有效控制的情况下,钢丸的粒度混合比以及钢丸颗粒数量的控制在抛丸处理的过程中就显得尤为重要。现有技术中,由于缺乏有效的抛丸处理工艺,抛丸处理后的热板表面粗糙度较高,无法满足市场需求。因此如何改进抛丸处理工艺以降低热板抛丸处理后表面粗糙度成为本领域书人员亟待解决的技术问题。技术实现要素:本发明的目的在于提供一种降低热板抛丸处理后表面粗糙度的方法,利用本发明的方法,通过合理选择抛丸介质、优化钢丸粒度以及控制料仓粒度混合比,可以有效降低热板抛丸处理后表面粗糙度,使得热板抛丸处理后表面粗糙度保持在ra≤3.2μm的水平。为此,本发明的降低热板抛丸处理后表面粗糙度的方法包括:选择抛丸介质,所述抛丸介质选择为钢丸;优化钢丸粒度,0.5mm及以上粒度的钢丸总量<2%,0.3mm~0.425mm粒度的钢丸总量达到90%左右;控制料仓粒度混合比,钢丸在抛丸机料仓内的料仓粒度混合比控制为0.3mm~0.355mm粒度的钢丸占比50%以上,0.5mm及以上粒度的钢丸占比<5%。优选地,在本发明的降低热板抛丸处理后表面粗糙度的方法中,钢丸粒度分布为:粒度0.125mm0.18mm0.3mm0.355mm0.425mm0.5mm0.6mm0.71mm钢丸0.01%7.42%17.55%39.56%33.60%1.85%0.01%0.00%优选地,在本发明的降低热板抛丸处理后表面粗糙度的方法中,料仓粒度混合比控制为:粒度0.125mm0.18mm0.3mm0.355mm0.425mm0.5mm0.6mm0.71mm钢丸0.79%10.29%18.53%35.65%31.14%3.42%0.18%0.00%优选地,在本发明的降低热板抛丸处理后表面粗糙度的方法中,所述钢丸为高碳铸钢丸。优选地,在本发明的降低热板抛丸处理后表面粗糙度的方法中,控制料仓粒度混合比的方法为:a)固定添加模式,每台抛丸机24小时内均匀连续添加补充磨料1.5吨;b)控制抛丸幕帘分离器均匀分布,风选用风速达到正常范围6~10km/h;c)控制除尘灰中尺寸≥0.2mm的有效颗粒的比例≤10%。利用本发明的降低热板抛丸处理后表面粗糙度的方法,通过选择钢丸作为抛丸介质,避免使用含带棱角钢砂的混合磨料,可以有效解决现有技术中钢板表面抛打较深、表面形貌不理想、表面粗糙度较大等问题;通过优化钢丸粒度的分布,可以得到最高的清理效率,同时抛丸处理后的冷板表面粗糙度能够显著降低;通过优化钢丸的料仓粒度混合比,避免大颗粒对表面抛打残留深坑,又可以保证表面清理等级满足预期要求,此外还能够降低除尘灰有效颗粒含量,并可以节省抛丸介质。附图说明为了更清楚地说明本发明实施例或现有技术中的技术方案,下面将对实施例或现有技术描述中所需要使用的附图作简单地介绍,显而易见地,下面描述中的附图仅仅是本发明的一些实施例,对于本领域普通技术人员来讲,在不付出创造性劳动的前提下,还可以根据这些附图获得其他的附图,附图中:图1a为现有技术中所用的抛丸混合磨料的放大图;图1b为本发明的降低热板抛丸处理后表面粗糙度的方法中所选用的钢丸的放大图;图2为本发明的降低热板抛丸处理后表面粗糙度的方法的示意图;图3为本发明的降低热板抛丸处理后表面粗糙度的方法中控制料仓粒度混合比所用装置的示意图。具体实施方式为使本发明的目的、技术方案和优点更加清楚,下面将结合本发明具体实施例及相应的附图对本发明技术方案进行清楚、完整地描述。显然,所描述的实施例仅是本发明的一部分实施例,而不是全部的实施例。基于本发明的实施例,本领域普通技术人员在没有做出创造性劳动前提下所获得的所有其他实施例,都属于本发明保护的范围。如图2所示,本发明的降低热板抛丸处理后表面粗糙度的方法包括:在抛丸介质方面进行了优化合理的选择,同时优化了钢丸粒度,此外还对料仓粒度混合比进行了优化控制。现有技术中,用于热板表面铁鳞处理的抛丸介质一般为高碳铸钢丸、高碳铸钢砂和混合磨料,其中混合磨料是指高碳铸钢丸与高碳铸钢砂以一定比例混合的抛丸介质。图1a示出了现有技术中所用的抛丸混合磨料的放大图,在放大15倍条件下,可以看出混合磨料中球形颗粒占比较少,而钢砂呈不规则形状,带有棱角。显然,现有技术中所用的混合磨料中钢砂占比较大,钢砂带有棱角,其抛打时棱角首先与带钢接触,由于接触面积小,棱角会对钢板接触面产生很强的力,在高效除鳞的效果下,势必会带来钢板表面抛打较深、表面形貌不理想、表面粗糙度较大等问题。通过对高碳铸钢丸与混合磨料的成分、硬度、外观对比,本发明的降低热板抛丸处理后表面粗糙度的方法中优选高碳铸钢丸作为抛丸介质。图1b示出了本发明的降低热板抛丸处理后表面粗糙度的方法中所选用的钢丸的放大图,在放大15倍条件下,可以看出钢丸则基本全为球形(少数异形<15%)。本发明的降低热板抛丸处理后表面粗糙度的方法中所选用的钢丸与现有技术中的混合磨料相比,其成份、密度、硬度相近,理论上对磨料消耗影响不大。钢丸因其球形外形而流动性较混合磨料好,使抛丸电流更稳定。此外,钢丸呈球形,抛打时与钢板接触表面积较大,受力相对均匀,不会产生局部受力较大,抛打深度相比较浅,在保证去除氧化铁皮的前提下,确保表面粗糙度不至过大。此外,抛丸的粒度大小对抛丸处理后产品表面的粗糙度影响较大,钢丸粒度越大,其冲击动能越大,冲击力也就越大。选择钢丸粒度时,在满足除鳞效率的前提下,若要降低表面粗糙度,尽可能选用较小的钢丸,最好使用级配钢丸。级配钢丸由50%以上名义尺寸的钢丸和逐渐变小的钢丸组成,兼顾了冲击力和覆盖率,可以得到最高的清理效率和较低的表面粗糙度。因此,在本发明的降低热板抛丸处理后表面粗糙度的方法中,进一步优化了钢丸粒度。表1示出了与现有技术所用的抛丸混合磨料中高碳铸钢丸相对照的本发明降低热板抛丸处理后表面粗糙度的方法中所用的钢丸粒度分布情况。表1混合磨料与钢丸粒度分布对照粒度0.125mm0.18mm0.3mm0.355mm0.425mm0.5mm0.6mm0.71mm混合磨料0.01%17.20%8.79%20.97%25.99%22.13%4.72%0.19%钢丸0.01%7.42%17.55%39.56%33.60%1.85%0.01%0.00%与现有技术所用的混合磨料相对比,可以看出本发明降低热板抛丸处理后表面粗糙度的方法中所用的钢丸的粒度整体偏小,0.5mm及以上粒度的钢丸占比减少25%左右,总量<2%,在具体实施例中0.5mm及以上粒度的钢丸总量可以仅为1.86%,因而更容易控制料仓粒度稳定;名义尺寸为0.3mm~0.425mm粒度的钢丸增加约35%,总量达到90%左右,在具体实施例中0.3mm~0.425mm粒度的钢丸总量可以达到90.71%,从而兼顾了冲击力和覆盖率,可以得到最高的清理效率,同时抛丸处理后的冷板表面粗糙度能够降低0.4%。进一步地,经试验得出,将料仓粒度混合比控制在一定范围内,能够有效降低抛丸处理后的冷板表面粗糙度。需要说明的是,料仓粒度混合比是指以具有上表1所示的粒度分布比例制备的钢丸为基本原料向料仓补充磨料过程(即加砂)中,在抛丸幕帘分离器控制下,实际补充到料仓的钢丸在料仓中的总体含量比例,因受加砂量、加砂频次及分离器风速等影响,各种粒度的钢丸的料仓粒度混合比会不同于其钢丸粒度分布比例。因此,在本发明的降低热板抛丸处理后表面粗糙度的方法中,还对料仓粒度混合比进行了优化控制。表2示出了与现有技术所用的抛丸混合磨料料仓粒度混合比相对照的本发明降低热板抛丸处理后表面粗糙度的方法中所用的钢丸料仓粒度混合比对照情况。表2料仓粒度混合比的优化控制对照可以看到,在本发明的降低热板抛丸处理后表面粗糙度的方法中,钢丸在抛丸机料仓内的料仓粒度混合比控制为0.3mm~0.355mm粒度的钢丸占比50%以上,在具体实施例中0.3mm~0.355mm粒度的钢丸占比可以为54.18%;0.5mm及以上粒度的钢丸占比<5%,在具体实施例中0.5mm及以上粒度的钢丸占比可以仅为3.6%,由此能够将抛丸处理后的冷板表面粗糙度ra由3.5μm降低至3.1μm。在本发明的降低热板抛丸处理后表面粗糙度的方法中,对料仓粒度混合比进行优化控制的方法为:a)固定添加模式,即每台抛丸机24小时内均匀连续添加补充磨料1.5吨;b)控制抛丸幕帘分离器均匀分布,风选用风速达到正常范围6~10km/h;c)控制除尘灰中尺寸≥0.2mm的有效颗粒的比例≤10%。图3示出了本发明的降低热板抛丸处理后表面粗糙度的方法中控制料仓粒度混合比所用装置的示意图,其中,钢丸添加到新料储存箱1内,通过远程控制管道开口控制器3的开口度,使钢丸经由加料管道2均匀地添加到抛丸机料仓4,避免一次集中添加并可有效控制料仓粒度混合比。实施例在本发明实施例的降低热板抛丸处理后表面粗糙度的方法中,选用高碳铸钢丸作为抛丸介质,钢丸的粒度如上表1所示,同时将钢丸在抛丸机料仓内的料仓粒度混合比控制为名义尺寸0.3mm的颗粒占比为17%左右;0.5mm以上尺寸颗粒<5%。利用该实施例的降低热板抛丸处理后表面粗糙度的方法,可以将抛丸处理后的冷板表面粗糙度ra由3.5μm降低至3.1μm,同时吨钢抛丸介质消耗也由2.06kg/吨钢降至1.88kg/吨钢,降幅达8.7%。本发明的降低热板抛丸处理后表面粗糙度的方法的有益效果包括:通过选择钢丸作为抛丸介质,避免使用含带棱角钢砂的混合磨料,可以有效解决现有技术中钢板表面抛打较深、表面形貌不理想、表面粗糙度较大等问题;通过优化钢丸粒度的分布,可以得到最高的清理效率,同时抛丸处理后的冷板表面粗糙度能够显著降低;通过优化钢丸的料仓粒度混合比,使得名义尺寸0.3mm的颗粒占比为17%左右、0.5mm以上颗粒<5%,避免大颗粒对表面抛打残留深坑,又可以保证表面清理等级满足预期要求,此外还能够降低除尘灰有效颗粒含量,并可以节省抛丸介质,吨钢抛丸介质消耗降幅达8.7%。应说明的是,以上实施例仅用于说明本发明的技术方案,而非对其限制;尽管参照前述实施例对本发明进行了详细的说明,本领域的普通技术人员应当理解:其依然可以对前述实施例所记载的技术方案进行修改,或者对其中部分技术特征进行等同替换;而这些修改或者替换,并不使相应技术方案的本质脱离本发明的范围。当前第1页12