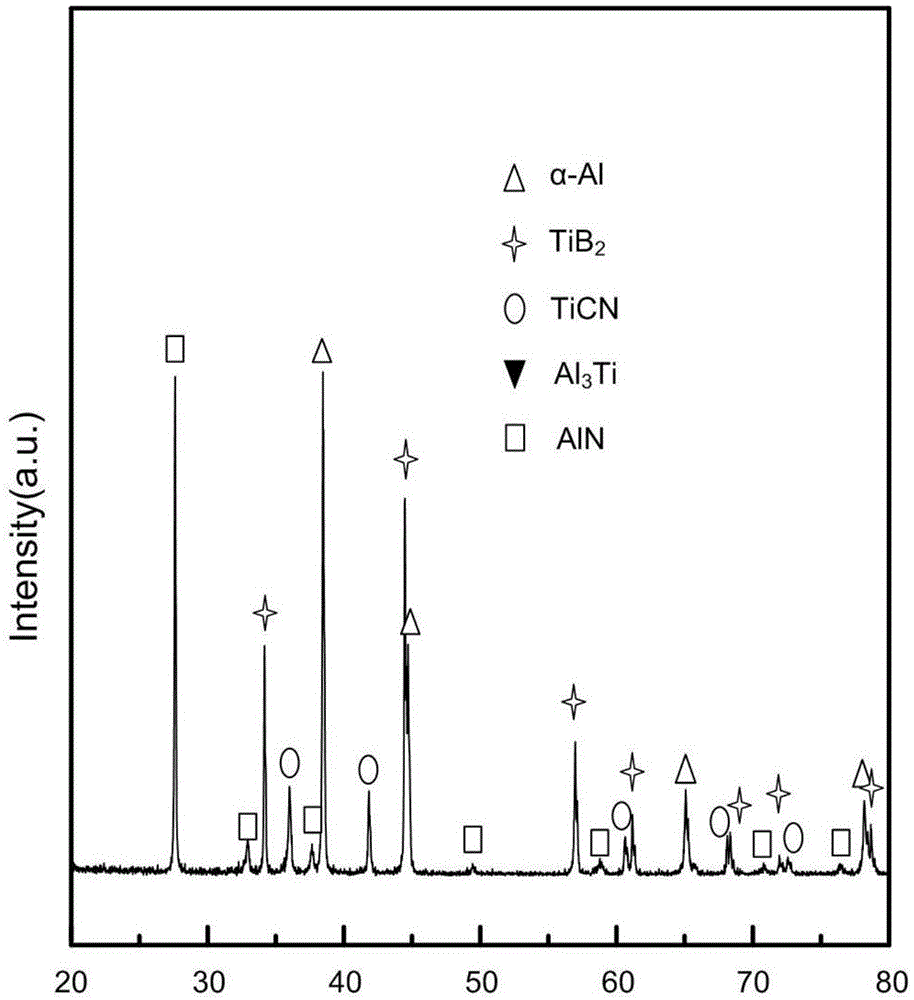
本发明涉及一种多相陶瓷颗粒混杂制备高弹性模量高强度铝合金的方法,属于铝合金制备
技术领域:
。
背景技术:
:随着汽车,军民用航空和电子领域的巨大发展,廉价轻质、高强塑性、高导热和尺寸稳定性好的陶瓷颗粒作为铝合金的强化剂得到了越来越多的关注。al-si-mg合金,作为一种可热处理强化合金,其具有自然时效能力,铸造性能优良,流动性好、气密性高、耐蚀性好。但其作为铝合金,相比于钢,其弹性模量和刚度仍较低,在某些高载荷的工况下仍无法很好的应用。但作为铝合金材料,其仍然具有一定的优势,即密度低,塑性较好。因此,考虑通过向熔体中加入陶瓷颗粒作为增强相来提高合金的强韧性。在目前的研究中,引入颗粒的方法主要分为外加法和内生法。外加法中陶瓷颗粒与基体之间的润湿性较差,颗粒与基体的界面之间容易产生化学反应而污染。本技术方案即在液相中引发自蔓延反应,该反应较为剧烈,瞬时在熔体内合成大量细小的陶瓷颗粒,并可以通过超声辅助分散等手段辅助颗粒分散均匀。基体与颗粒放热界面接触良好,界面无污染。且本方案中的内生ticn颗粒为纳米尺寸,具有高硬度、高模量以及热稳定性和化学稳定性好等特点,在加入铝合金熔体时不会与铝合金基体发生反应,且可以在一定程度上提高合金的塑性;同时内生的tib2、aln陶瓷颗粒也具有比强度高、熔点高、硬度高、耐腐蚀性较好以及电导率较高等特点。技术实现要素:本发明的目的在于提供一种多相陶瓷颗粒混杂制备高弹性模量高强度铝合金制备方法,通过向熔体内加入预先制备好的混合粉体压坯,其在熔体内发生高温自蔓延反应,分别可生成ticn颗粒、tib2、aln颗粒,再通过外加法加入微米尺寸sic颗粒,多相混杂的陶瓷颗粒可以通过晶粒细化强化、奥罗万强化、析出相强化等不同方式协同作用,显著增加铝合金的强韧性。并优化多相颗粒的百分含量,实现铝合金材料中各种颗粒的良好均匀分布。为了实现上述目的,本发明的技术方案如下。一种多相陶瓷颗粒混杂制备高弹性模量高强度铝合金的方法,具体包括以下步骤:(1)al-ti-b4c-bn体系原位内生陶瓷颗粒强化剂的制备,具体如下:(1a)al-ti-b4c-bn体系反应压坯的制备:称取所需的粒度13-48μm的al粉、粒度为13-45μm的ti粉、粒度为0.5-6.5μm的b4c粉、粒度为0.5~1.3μm的bn粉备用;首先按bn粉、b4c粉的摩尔比为1:1将称量好的bn粉、b4c粉放入球磨罐中,用行星式球磨机将上述粉体以200~300r/min的速度高速球磨活化处理1.5~3h。(1b)预计在al-ti-b4c-bn体系生成ticn、tib2、aln颗粒的总含量为20wt.%-40wt.%,按ti粉,b4c粉,bn粉摩尔比为9:2.8:2.8称量ti粉和混合好的bn粉及b4c粉,余量为al粉,配制成100g粉体,具体如下:①多相ticn-aln-tib2陶瓷的质量分数为20wt.%:其中al-ti-b4c-bn体系中,ti:b4c:bn的摩尔比为9:2.8:2.8;其中al粉:80g、ti粉:13.16g、b4c粉:4.72g、bn粉:2.12g。②多相ticn-aln-tib2陶瓷的质量分数为30wt.%,其中al-ti-b4c-bn体系中,ti:b4c:bn的摩尔比为9:2.8:2.8;其中al粉:70g、ti粉:19.73g、b4c粉:7.09g、bn粉:3.18g。③多相ticn-aln-tib2陶瓷的质量分数为40wt.%,其中al-ti-b4c-bn体系中,ti:b4c:bn的摩尔比为9:2.8:2.8;其中al粉:60g、ti粉:26.31g、b4c粉:9.45g、bn粉:4.24g。(1c)将配制好的粉料与氧化锆磨球放入混料机中,混料机以30-60r/min的速度混合8-32h;随后将混合均匀的粉料取出并用铝箔包好,在液压机上冷压制成φ30圆柱形压坯,压力60-100mpa;高35-45mm;致密度为60-75%。(2)sic陶瓷颗粒的预处理,具体如下:(2a)sicp表面氧化处理:将sicp粉末以为0.3-0.8mm的厚度平铺在高纯刚玉坩埚上,高纯刚玉坩埚直径为100mm、高度为20mm;随后将刚玉坩埚置于高温箱式电阻炉内锻烧。sicp高温氧化处理采用分段氧化方式,具体分段氧化工艺如下:①升温到573k,速率为20-100k/min,在573k下保温10min;②升温到973k,升温速率为20-100k/min,保温10min;③加热到预定温度保温973k-1373k,保温1-12h;(2b)球磨预分散处理:取粒度为15-40μm的al-si-mg(si:6.5%-10wt.%,mg:0.3-0.7wt.%,余量为al)合金粉末和粒度为5-20μm的sicp粉末,按照sicp与al-si-mg合金粉质量比1:20-1:1.5,配制成混合粉末;将配制好的混合粉料放入球磨罐中。球料总体积为球罐容积的2/3,转速为20-90rpm,正反转交替进行,间隔时间30min、球磨时间24-96h。(2c)含有sic颗粒压坯的制备:将球磨混料的粉料取出,用铝箔包好,在液压机上冷压制成直径为φ30-φ45的轴向压力致密化的圆柱形陶铝复合压坯,压力60-100mpa;致密度为60-75%。(3)多种颗粒复合强化al-si-mg合金,具体如下:(3a)将预先称量好的铝合金放置于坩埚中并随坩埚一起放入坩埚式电阻熔炼炉内,升温至1073k;铝合金的成分为si:6.5%-10wt.%,mg:0.3-0.7wt.%,余量为al;(3b)待合金完全熔化后并保温30min,加入清渣剂对合金液进行精炼除渣,打渣处理后保温10min。得到未强化al-si-mg合金。(3c)将步骤(1)中制得的压坯在753-823k下预热0.5-2h;将坩埚式电阻熔炼炉内的温度升至1123-1203k,将预热后的压坯压入到所述坩埚中的合金液内;加入压坯的量占总合金液质量的0.33-1.67wt.%。(3d)熔体内产生有瞬间明亮的火光后保持压坯浸入合金熔体中不低于1分钟,随后进行机械搅拌,时间为1-5min;将坩埚的炉温降至1073-1123k;(3e)将含有微米sic陶瓷颗粒的强化剂加入到坩埚内,其中sic陶瓷颗粒的实际加入量为坩埚中金属液总量的2wt.%-8wt.%,采用机械搅拌处理熔体120-300s。随后保温3-5min;(4)强化后的al-si-mg合金的浇铸成型及热处理:(4a)保温超声波探头后对坩埚中的合金液采用超声处理,处理时间为10-15min。超声辅助分散结束后,移除超声设备,保温3-5min。(4b)超声处理后的混合铝液转至保温炉保温,然后进行炉内精炼。在温度为1003-1023k条件下,伸入旋转吹气探头至保温炉底部,由旋转吹气探头向铝合金液中通入cl2和ar进行精炼,向炉内吹气处理2-5min,扒渣,随后保温静置;(4c)将搅拌处理后的金属液浇铸到金属型模具内,得到复合陶瓷颗粒强化铝合金的板状试样。(4d)固溶处理:将强化后的铝合金在高温烘箱中进行固溶处理,固溶温度803-823k,固溶时间为6-15h,固溶处理后进行冷水淬火;(4e)自然时效处理:在空气中进行自然时效处理,时效时间为6-15h;(4f)人工时效处理:在电热鼓风干燥箱中进行人工时效处理,时效温度428-438k,时效时间为6-15h。进一步地,步骤(1)、(2)中球磨混料时,行星式球磨机中所装的球磨罐内预先盛有直径分别为5mm、7mm、11mm、15mm、20mm、22mm的zro2球,每种10个,zro2球质量共800g;控制zro2磨球和混合粉末的质量比是8:1-10:1;进一步地,步骤(3)中熔体内观察到明亮的火光说明al-ti-b4c-bn体系在铝合金熔体内生成了ticn、tib2、aln陶瓷颗粒。其中设计陶瓷颗粒的生成量依据加入的al-ti-b4c-bn粉体压坯的质量来控制。进一步地,步骤(3)中所用到清渣剂的成分为35wt.%kcl、30wt.%mgcl2、5wt.%alf3、15wt.%na3alf6、5wt.%mg3n2、5wt.%na2co3、5wt.%c2cl6。进一步地,步骤(4)中金属型模具的尺寸和材质分别为:200mm×150mm×20mm和45#钢。该发明的有益效果在于:本发明方法中,直接加入的微米尺寸sic陶瓷颗粒,具有密度低、高强度、高模量、来源丰富和价格低廉、化学稳定性好、抗热冲击性能良好以及抗蠕变良好等优点,可以显著增加铝合金的刚度与弹性模量。多相混杂的陶瓷颗粒可以通过晶粒细化强化、奥罗万强化、析出相强化等不同方式协同作用,进一步强化铝合金,且陶瓷颗粒的分散效果更好,强化过程简单方便,可操作性强,适合工业批量化生产,实用价值和潜力巨大。铝合金的强韧性同时提高,合金的应用领域进一步拓展,轻质铝合金的刚度与弹性模量提高,对于实现制备高性能轻量化材料具有重要的应用价值。本发明提供的是设计开发了一种利用多尺度陶瓷颗粒混杂制备高弹性模量高强度铝合金的方法,将al粉、ti粉以及bn和b4c粉混合制成粉体压坯加入熔体中,通过熔体内高温自蔓延反应引入纳米尺寸的ticn颗粒、亚微米尺寸的tib2和aln颗粒,并优化颗粒的百分含量,实现陶铝复合材料中微纳米颗粒的均匀分布,配合微米尺寸的sic颗粒,实现在铝基体中纳米尺寸陶瓷颗粒和微米尺寸陶瓷颗粒的叠加效应,多相陶瓷颗粒在铝基体内稳定存在,界面结合良好,分散均匀,实现陶铝复合材料中颗粒的多相多尺度分布,且多相多尺度颗粒稳定存在,内生陶瓷颗粒与铝合金基体不会发生界面反应,颗粒尺寸为纳米、微米混杂,不会降低复合材料的塑性,具有重要的应用价值。整体操作简单,节约成本,具有重要的经济效益。附图说明图1为实施例1和对比例2中制备的20wt.%内生多相ticn-aln-tib2熔体内反应后压坯的x射线衍射图。图2为实施例1和对比例2中使用的微米sic颗粒形貌图。图3为实施例3和对比例3中制备的40wt.%内生多相ticn-aln-tib2熔体内反应后压坯的x射线衍射图。图4为实施例3和对比例3中使用的微米sic颗粒形貌图。图5为实施例2中制备的30wt.%内生多相ticn-aln-tib2熔体内反应后压坯的x射线衍射图。图6为实施例2中使用的微米sic颗粒形貌图。具体实施方式下面结合对比例和实施例对本发明的具体实施方式进行描述,以便更好的理解本发明。对比例1:本对比例中未加入内生ticn颗粒、tib2和aln颗粒和微米sic陶瓷颗粒时,基体亚共晶al-si-mg合金的制备过程,具体如下:(1)将预先称量好的铝合金放置于坩埚中并随坩埚一起放入坩埚式电阻熔炼炉内,升温至1073k;铝合金的成分为si:8wt.%,mg:0.5wt.%,余量为al;(2)待合金完全熔化后并保温30min,加入清渣剂对合金液进行精炼除渣,打渣处理后保温10min。得到未强化al-si-mg合金。然后进行炉内精炼。在温度为1023k条件下,伸入旋转吹气探头至保温炉底部,由旋转吹气探头向铝合金液中通入cl2和ar进行精炼,向炉内吹气处理3min,扒渣,随后保温静置;(3)将金属液浇铸到金属型模具内,得到铝合金的板状试样。(4)固溶处理:将强化后的铝合金在高温烘箱中进行固溶处理,固溶温度813k,固溶时间为6h,固溶处理后进行冷水淬火;(5)自然时效处理:在空气中进行自然时效处理,时效时间为6h;(6)人工时效处理:在电热鼓风干燥箱中进行人工时效处理,时效温度438k,时效时间为10h。其中,步骤(2)中,所用到清渣剂的成分为35wt.%kcl、30wt.%mgcl2、5wt.%alf3、15wt.%na3alf6、5wt.%mg3n2、5wt.%na2co3、5wt.%c2cl6。其中,步骤(3)中的金属型模具的材质为:45#钢。金属型模具的尺寸为:200mm×150mm×20mm。本对比例中制备的未加入原位反应颗粒和微米sic陶瓷颗粒的基体亚共晶al-si-mg合金的弹性模量、拉伸强度和断裂应变分别为:70.5gpa、282mpa、7.6%。如表1所示。对比例2:本对比例中(对比少量添加内生ticn、tib2和aln颗粒和微米sic陶瓷颗粒的情况下铝合金的强化效果)的制备方法,具体如下:(1)al-ti-b4c-bn体系原位内生陶瓷颗粒强化剂的制备,具体如下:(1a)al-ti-b4c-bn体系反应压坯的制备:称取一定量所需的粒度约13μm的al粉、粒度约为13μm的ti粉、粒度为0.5μm的b4c粉、粒度为0.5μm的bn粉备用;首先按bn粉、b4c粉的摩尔比为1:1将称量好的bn粉、b4c粉放入球磨罐中。用行星式球磨机将上述粉体以200r/min的速度高速球磨活化处理1.5h。(1b)预计在al-ti-b4c-bn体系生成ticn、tib2、aln颗粒的总含量为20wt.%,按ti粉,b4c粉,bn粉摩尔比为9:2.8:2.8称量ti粉和混合好的bn粉及b4c粉,余量为al粉,配制成100g粉体。其中al-ti-b4c-bn体系中,ti:b4c:bn的摩尔比为9:2.8:2.8;其中al粉:80g、ti粉:13.16g、b4c粉:4.72g、bn粉:2.12g。(1c)将配制好的粉料与氧化锆磨球放入混料机中,混料机以60r/min的速度混合8h;随后将混合均匀的粉料取出并用铝箔包好,在液压机上冷压制成φ30圆柱形压坯,压力100mpa;高35mm;致密度为75%。(2)sic陶瓷颗粒的预处理,具体如下:(2a)sicp表面氧化处理:将sicp粉末以约为0.3mm的厚度平铺在高纯刚玉坩埚上,高纯刚玉坩埚直径为100mm、高度为20mm;随后将刚玉坩埚置于高温箱式电阻炉内锻烧。sicp高温氧化处理采用分段氧化方式,具体分段氧化工艺如下:①升温到573k,速率为20k/min,在573k下保温10min;②升温到973k,升温速率为30k/min,保温10min;③加热到预定温度保温1373k,保温12h;(2b)球磨预分散处理:取粒度为40μm的al-si-mg(si:7wt.%,mg:0.3wt.%,余量为al)合金粉末和粒度为6μm的sicp粉末,按照sicp与al-si-mg合金粉质量比1:2,配制成混合粉末;将配制好的混合粉料放入球磨罐中。球料总体积为球罐容积的2/3,转速为20rpm(正反转交替进行,间隔时间30min)、球磨时间24h。(2c)含有sic颗粒压坯的制备:将球磨混料的粉料取出,用铝箔包好,在液压机上冷压制成直径为φ30的轴向压力致密化的圆柱形陶铝复合压坯,压力60mpa;致密度为60%。(3)多尺度颗粒复合强化al-si-mg合金,具体如下:(3a)将预先称量好的铝合金放置于坩埚中并随坩埚一起放入坩埚式电阻熔炼炉内,升温至1073k;铝合金的成分为si:7wt.%,mg:0.3wt.%,余量为al;(3b)待合金完全熔化后并保温30min,加入清渣剂对合金液进行精炼除渣,打渣处理后保温10min。得到未强化al-si-mg合金。(3c)将步骤(1)中制得的压坯在773k下预热2h;将坩埚式电阻熔炼炉内的温度升至1123k,将预热后的压坯压入到所述坩埚中的合金液内;加入压坯的量占总合金液质量的0.25wt.%,生成的陶瓷颗粒实际量为al-si-mg合金液总量的0.05wt.%。(3d)熔体内产生有瞬间明亮的火光后保持压坯浸入合金熔体中不低于1分钟,随后进行机械搅拌,时间为3min;将坩埚的炉温降至1073k;(3e)将含有微米sic陶瓷颗粒的强化剂加入到坩埚内,其中sic陶瓷颗粒的实际加入量为坩埚中金属液总量的1.2wt.%,采用机械搅拌处理熔体120s。随后保温3min;(4)强化后的al-si-mg合金的浇铸成型及热处理:(4a)保温超声波探头后对坩埚中的合金液采用超声处理,处理时间为10min。超声辅助分散结束后,移除超声设备,保温5min。(4b)超声处理后的混合铝液转至保温炉保温,然后进行炉内精炼。在温度为1023k条件下,伸入旋转吹气探头至保温炉底部,由旋转吹气探头向铝合金液中通入cl2和ar进行精炼,向炉内吹气处理3min,扒渣,随后保温静置;(4c)将搅拌处理后的金属液浇铸到金属型模具内,得到复合陶瓷颗粒强化铝合金的板状试样。(4d)固溶处理:将强化后的铝合金在高温烘箱中进行固溶处理,固溶温度803k,固溶时间为15h,固溶处理后进行冷水淬火;(4e)自然时效处理:在空气中进行自然时效处理,时效时间为15h;(4f)人工时效处理:在电热鼓风干燥箱中进行人工时效处理,时效温度438k,时效时间为6h。其中,步骤(1)、(2)中球磨混料时,行星式球磨机中所装的球磨罐内预先盛有直径分别为5mm、7mm、11mm、15mm、20mm、22mm的zro2球,每种10个,zro2球质量共800g。另外,控制zro2磨球和混合粉末的质量比是8:1-10:1;其中,步骤(3)中熔体内观察到明亮的火光说明al-ti-b4c-bn体系在铝合金熔体内生成了ticn、tib2、aln陶瓷颗粒。其中设计陶瓷颗粒的生成量依据加入的al-ti-b4c-bn粉体压坯的质量来控制。其中,步骤(3)中,所用到清渣剂的成分为35wt.%kcl、30wt.%mgcl2、5wt.%alf3、15wt.%na3alf6、5wt.%mg3n2、5wt.%na2co3、5wt.%c2cl6。其中,步骤(4)中金属型模具的尺寸和材质分别为:200mm×150mm×20mm和45#钢。0.05wt.%内生颗粒(ticn颗粒、tib2和aln颗粒混合体)(如图1和图2所示)和1.2wt.%sic陶瓷颗粒(如图3)的复合强化处理al-si-mg合金的弹性模量、拉伸强度和断裂应变分别为:73.6gpa、298mpa、7.8%,比未强化的al-si-mg合金(弹性模量:70.5gpa、拉伸强度:282mpa、断裂应变分别为:7.6%)的性能分别提高了4.3%、5.6%、2.6%。弹性模量、强度、断裂应变都没有显著提高,如表1所示,显然,少量的陶瓷颗粒的添加不足以显著的提高铝合金的性能。对比例3:本对比例中(对比大量添加内生ticn颗粒、tib2和aln颗粒混合体和微米sic陶瓷颗粒的情况下铝合金的强化效果)的制备方法,具体如下:(1)al-ti-b4c-bn体系原位内生陶瓷颗粒强化剂的制备,具体如下:(1a)al-ti-b4c-bn体系反应压坯的制备:称取一定量所需的粒度约25μm的al粉、粒度约为25μm的ti粉、粒度为3μm的b4c粉、粒度为1μm的bn粉备用;首先按bn粉、b4c粉的摩尔比为1:1将称量好的bn粉、b4c粉放入球磨罐中。用行星式球磨机将上述粉体以300r/min的速度高速球磨活化处理3h。(1b)预计在al-ti-b4c-bn体系生成ticn、tib2、aln颗粒的总含量为40wt.%,按ti粉,b4c粉,bn粉摩尔比为9:2.8:2.8称量ti粉和混合好的bn粉及b4c粉,余量为al粉,配制成100g粉体。其中al-ti-b4c-bn体系中,ti:b4c:bn的摩尔比为9:2.8:2.8;其中al粉:60g、ti粉:26.31g、b4c粉:9.45g、bn粉:4.24g。(1c)将配制好的粉料与氧化锆磨球放入混料机中,混料机以40r/min的速度混合20h;随后将混合均匀的粉料取出并用铝箔包好,在液压机上冷压制成φ30圆柱形压坯,压力80mpa;高40mm;致密度为68%。(2)sic陶瓷颗粒的预处理,具体如下:(2a)sicp表面氧化处理:将sicp粉末以约为0.8mm的厚度平铺在高纯刚玉坩埚上,高纯刚玉坩埚直径为100mm、高度为20mm;随后将刚玉坩埚置于高温箱式电阻炉内锻烧。sicp高温氧化处理采用分段氧化方式,具体分段氧化工艺如下:①升温到573k,速率为90k/min,在573k下保温15min;②升温到973k,升温速率为70k/min,保温10min;③加热到预定温度保温1273k,保温5h;(2b)球磨预分散处理:取粒度为25μm的al-si-mg(si:9.5wt.%,mg:0.7wt.%,余量为al)合金粉末和粒度为10μm的sicp粉末,按照sicp与al-si-mg合金粉质量比1:4,配制成混合粉末;将配制好的混合粉料放入球磨罐中。球料总体积为球罐容积的2/3,转速为80rpm(正反转交替进行,间隔时间30min)、球磨时间96h。(2c)含有sic颗粒压坯的制备:将球磨混料的粉料取出,用铝箔包好,在液压机上冷压制成直径为φ38的轴向压力致密化的圆柱形陶铝复合压坯,压力80mpa;致密度为68%。(3)多尺度颗粒复合强化al-si-mg合金,具体如下:(3a)将预先称量好的铝合金放置于坩埚中并随坩埚一起放入坩埚式电阻熔炼炉内,升温至1073k;铝合金的成分为si:9.5wt.%,mg:0.7wt.%,余量为al;(3b)待合金完全熔化后并保温30min,加入清渣剂对合金液进行精炼除渣,打渣处理后保温10min。得到未强化al-si-mg合金。(3c)将步骤(1)中制得的压坯在773k下预热2h;将坩埚式电阻熔炼炉内的温度升至1123k,将预热后的压坯压入到所述坩埚中的合金液内;加入压坯的量占总合金液质量的1.8wt.%,生成的陶瓷颗粒实际量为al-si-mg合金液总量的0.72wt.%。(3d)熔体内产生有瞬间明亮的火光后保持压坯浸入合金熔体中不低于1分钟,随后进行机械搅拌,时间为3min;将坩埚的炉温降至1073k;(3e)将含有微米sic陶瓷颗粒的强化剂加入到坩埚内,其中sic陶瓷颗粒的实际加入量为坩埚中金属液总量的8.0wt.%,采用机械搅拌处理熔体300s。随后保温5min;(4)强化后的al-si-mg合金的浇铸成型及热处理:(4a)保温超声波探头后对坩埚中的合金液采用超声处理,处理时间为10min。超声辅助分散结束后,移除超声设备,保温5min。(4b)超声处理后的混合铝液转至保温炉保温,然后进行炉内精炼。在温度为1003k条件下,伸入旋转吹气探头至保温炉底部,由旋转吹气探头向铝合金液中通入cl2和ar进行精炼,向炉内吹气处理5min,扒渣,随后保温静置;(4c)将搅拌处理后的金属液浇铸到金属型模具内,得到复合陶瓷颗粒强化铝合金的板状试样。(4d)固溶处理:将强化后的铝合金在高温烘箱中进行固溶处理,固溶温度813k,固溶时间为10h,固溶处理后进行冷水淬火;(4e)自然时效处理:在空气中进行自然时效处理,时效时间为12h;(4f)人工时效处理:在电热鼓风干燥箱中进行人工时效处理,时效温度433k,时效时间为11h。其中,步骤(1)、(2)中球磨混料时,行星式球磨机中所装的球磨罐内预先盛有直径分别为5mm、7mm、11mm、15mm、20mm、22mm的zro2球,每种10个,zro2球质量共800g。另外,控制zro2磨球和混合粉末的质量比是8:1-10:1;其中,步骤(3)中熔体内观察到明亮的火光说明al-ti-b4c-bn体系在铝合金熔体内生成了ticn、tib2、aln陶瓷颗粒。其中设计陶瓷颗粒的生成量依据加入的al-ti-b4c-bn粉体压坯的质量来控制。其中,步骤(3)中,所用到清渣剂的成分为35wt.%kcl、30wt.%mgcl2、5wt.%alf3、15wt.%na3alf6、5wt.%mg3n2、5wt.%na2co3、5wt.%c2cl6。其中,步骤(4)中金属型模具的尺寸和材质分别为:200mm×150mm×20mm和45#钢。1.8wt.%内生颗粒(ticn颗粒、tib2和aln颗粒混合体)(如图1和图2所示)和8.0wt.%sic陶瓷颗粒(如图3)的复合强化处理al-si-mg合金的弹性模量、拉伸强度和断裂应变分别为:92.5gpa、381mpa、3.5%,比未强化的al-si-mg合金(弹性模量:70.5gpa、拉伸强度:282mpa、断裂应变分别为:7.6%)的性能分别提高了31.2%、35.1%、53.9%。虽然弹性模量和强度提高,但是强度不如0.50wt.%内生混杂尺度颗粒(ticn颗粒、tib2和aln颗粒混合体)和7wt.%sic陶瓷颗粒的复合强化处理al-si-mg合金的强度,并且断裂应变大幅降低,如表1所示实施例1:本实施例中多相陶瓷颗粒混杂制备高弹性模量高强度铝合金的方法,具体如下:(1)al-ti-b4c-bn体系原位内生陶瓷颗粒强化剂的制备,具体如下:(1a)al-ti-b4c-bn体系反应压坯的制备:称取一定量所需的粒度约13μm的al粉、粒度约为13μm的ti粉、粒度为0.5μm的b4c粉、粒度为0.5μm的bn粉备用;首先按bn粉、b4c粉的摩尔比为1:1将称量好的bn粉、b4c粉放入球磨罐中。用行星式球磨机将上述粉体以200r/min的速度高速球磨活化处理1.5h。(1b)预计在al-ti-b4c-bn体系生成ticn、tib2、aln颗粒的总含量为20wt.%,按ti粉,b4c粉,bn粉摩尔比为9:2.8:2.8称量ti粉和混合好的bn粉及b4c粉,余量为al粉,配制成100g粉体。其中al-ti-b4c-bn体系中,ti:b4c:bn的摩尔比为9:2.8:2.8;其中al粉:80g、ti粉:13.16g、b4c粉:4.72g、bn粉:2.12g。(1c)将配制好的粉料与氧化锆磨球放入混料机中,混料机以60r/min的速度混合8h;随后将混合均匀的粉料取出并用铝箔包好,在液压机上冷压制成φ30圆柱形压坯,压力100mpa;高35mm;致密度为75%。(2)sic陶瓷颗粒的预处理,具体如下:(2a)sicp表面氧化处理:将sicp粉末以约为0.3mm的厚度平铺在高纯刚玉坩埚上,高纯刚玉坩埚直径为100mm、高度为20mm;随后将刚玉坩埚置于高温箱式电阻炉内锻烧。sicp高温氧化处理采用分段氧化方式,具体分段氧化工艺如下:①升温到573k,速率为20k/min,在573k下保温10min;②升温到973k,升温速率为30k/min,保温10min;③加热到预定温度保温1373k,保温12h;(2b)球磨预分散处理:取粒度为40μm的al-si-mg(si:7wt.%,mg:0.3wt.%,余量为al)合金粉末和粒度为6μm的sicp粉末,按照sicp与al-si-mg合金粉质量比1:2,配制成混合粉末;将配制好的混合粉料放入球磨罐中。球料总体积为球罐容积的2/3,转速为20rpm(正反转交替进行,间隔时间30min)、球磨时间24h。(2c)含有sic颗粒压坯的制备:将球磨混料的粉料取出,用铝箔包好,在液压机上冷压制成直径为φ30的轴向压力致密化的圆柱形陶铝复合压坯,压力60mpa;致密度为60%。(3)多尺度颗粒复合强化al-si-mg合金,具体如下:(3a)将预先称量好的铝合金放置于坩埚中并随坩埚一起放入坩埚式电阻熔炼炉内,升温至1073k;铝合金的成分为si:7wt.%,mg:0.3wt.%,余量为al;(3b)待合金完全熔化后并保温30min,加入清渣剂对合金液进行精炼除渣,打渣处理后保温10min。得到未强化al-si-mg合金。(3c)将步骤(1)中制得的压坯在773k下预热2h;将坩埚式电阻熔炼炉内的温度升至1123k,将预热后的压坯压入到所述坩埚中的合金液内;加入压坯的量占总合金液质量的0.5wt.%,生成的陶瓷颗粒实际量为al-si-mg合金液总量的0.1wt.%。(3d)熔体内产生有瞬间明亮的火光后保持压坯浸入合金熔体中不低于1分钟,随后进行机械搅拌,时间为3min;将坩埚的炉温降至1073k;(3e)将含有微米sic陶瓷颗粒的强化剂加入到坩埚内,其中sic陶瓷颗粒的实际加入量为坩埚中金属液总量的2wt.%,采用机械搅拌处理熔体120s。随后保温3min;(4)强化后的al-si-mg合金的浇铸成型及热处理:(4a)保温超声波探头后对坩埚中的合金液采用超声处理,处理时间为10min。超声辅助分散结束后,移除超声设备,保温5min。(4b)超声处理后的混合铝液转至保温炉保温,然后进行炉内精炼。在温度为1023k条件下,伸入旋转吹气探头至保温炉底部,由旋转吹气探头向铝合金液中通入cl2和ar进行精炼,向炉内吹气处理3min,扒渣,随后保温静置;(4c)将搅拌处理后的金属液浇铸到金属型模具内,得到复合陶瓷颗粒强化铝合金的板状试样。(4d)固溶处理:将强化后的铝合金在高温烘箱中进行固溶处理,固溶温度803k,固溶时间为15h,固溶处理后进行冷水淬火;(4e)自然时效处理:在空气中进行自然时效处理,时效时间为15h;(4f)人工时效处理:在电热鼓风干燥箱中进行人工时效处理,时效温度438k,时效时间为6h。其中,步骤(1)、(2)中球磨混料时,行星式球磨机中所装的球磨罐内预先盛有直径分别为5mm、7mm、11mm、15mm、20mm、22mm的zro2球,每种10个,zro2球质量共800g。另外,控制zro2磨球和混合粉末的质量比是8:1-10:1;其中,步骤(3)中熔体内观察到明亮的火光说明al-ti-b4c-bn体系在铝合金熔体内生成了ticn、tib2、aln陶瓷颗粒。其中设计陶瓷颗粒的生成量依据加入的al-ti-b4c-bn粉体压坯的质量来控制。其中,步骤(3)中,所用到清渣剂的成分为35wt.%kcl、30wt.%mgcl2、5wt.%alf3、15wt.%na3alf6、5wt.%mg3n2、5wt.%na2co3、5wt.%c2cl6。其中,步骤(4)中金属型模具的尺寸和材质分别为:200mm×150mm×20mm和45#钢。0.1wt.%内生颗粒(纳米尺寸的ticn颗粒、亚微米尺寸的tib2和aln颗粒混合体)(如图1和图2所示)和2wt.%sic陶瓷颗粒(如图3所示)的复合强化处理al-si-mg合金的弹性模量、拉伸强度和断裂应变分别为:75.9gpa、328mpa、8.1%,比未强化的al-si-mg合金(弹性模量:70.5gpa、拉伸强度:282mpa、断裂应变分别为:7.6%)的性能分别提高了7.6%、16.3%、6.5%。弹性模量和强度提高显著,并且提高了材料的塑性。如表1所示。实施例2:本实施例中的多相陶瓷颗粒混杂制备高弹性模量高强度铝合金的方法,具体如下:(1)al-ti-b4c-bn体系原位内生陶瓷颗粒强化剂的制备,具体如下:(1a)al-ti-b4c-bn体系反应压坯的制备:称取一定量所需的粒度约48μm的al粉、粒度约为45μm的ti粉、粒度为6.5μm的b4c粉、粒度为1.3μm的bn粉备用;首先按bn粉、b4c粉的摩尔比为1:1将称量好的bn粉、b4c粉放入球磨罐中。用行星式球磨机将上述粉体以260r/min的速度高速球磨活化处理2h。(1b)预计在al-ti-b4c-bn体系生成ticn、tib2、aln颗粒的总含量为30wt.%,按ti粉,b4c粉,bn粉摩尔比为9:2.8:2.8称量ti粉和混合好的bn粉及b4c粉,余量为al粉,配制成100g粉体。其中al-ti-b4c-bn体系中,ti:b4c:bn的摩尔比为9:2.8:2.8;其中al粉:70g、ti粉:19.73g、b4c粉:7.09g、bn粉:3.18g。(1c)将配制好的粉料与氧化锆磨球放入混料机中,混料机以30r/min的速度混合32h;随后将混合均匀的粉料取出并用铝箔包好,在液压机上冷压制成φ30圆柱形压坯,压力60mpa;高45mm;致密度为60%。(2)sic陶瓷颗粒的预处理,具体如下:(2a)sicp表面氧化处理:将sicp粉末以约为0.6mm的厚度平铺在高纯刚玉坩埚上,高纯刚玉坩埚直径为100mm、高度为20mm;随后将刚玉坩埚置于高温箱式电阻炉内锻烧。sicp高温氧化处理采用分段氧化方式,具体分段氧化工艺如下:①升温到573k,速率为50k/min,在573k下保温15min;②升温到973k,升温速率为80k/min,保温8min;③加热到预定温度保温1373k,保温2h;(2b)球磨预分散处理:取粒度为15μm的al-si-mg(si:7wt.%,mg:0.3wt.%,余量为al)合金粉末和粒度为10μm的sicp粉末,按照sicp与al-si-mg合金粉质量比1:3,配制成混合粉末;将配制好的混合粉料放入球磨罐中。球料总体积为球罐容积的2/3,转速为50rpm(正反转交替进行,间隔时间30min)、球磨时间36h。(2c)含有sic颗粒压坯的制备:将球磨混料的粉料取出,用铝箔包好,在液压机上冷压制成直径为φ45的轴向压力致密化的圆柱形陶铝复合压坯,压力100mpa;致密度为75%。(3)多尺度颗粒复合强化al-si-mg合金,具体如下:(3a)将预先称量好的铝合金放置于坩埚中并随坩埚一起放入坩埚式电阻熔炼炉内,升温至1073k;铝合金的成分为si:8wt.%,mg:0.5wt.%,余量为al;(3b)待合金完全熔化后并保温30min,加入清渣剂对合金液进行精炼除渣,打渣处理后保温10min。得到未强化al-si-mg合金。(3c)将步骤(1)中制得的压坯在773k下预热2h;将坩埚式电阻熔炼炉内的温度升至1123k,将预热后的压坯压入到所述坩埚中的合金液内;加入压坯的量占总合金液质量的1.0wt.%,生成的陶瓷颗粒实际量为al-si-mg合金液总量的0.3wt.%。(3d)熔体内产生有瞬间明亮的火光后保持压坯浸入合金熔体中不低于1分钟,随后进行机械搅拌,时间为3min;将坩埚的炉温降至1073k;(3e)将含有微米sic陶瓷颗粒的强化剂加入到坩埚内,其中sic陶瓷颗粒的实际加入量为坩埚中金属液总量的5wt.%,采用机械搅拌处理熔体120s。随后保温3min;(4)强化后的al-si-mg合金的浇铸成型及热处理:(4a)保温超声波探头后对坩埚中的合金液采用超声处理,处理时间为10min。超声辅助分散结束后,移除超声设备,保温5min。(4b)超声处理后的混合铝液转至保温炉保温,然后进行炉内精炼。在温度为1023k条件下,伸入旋转吹气探头至保温炉底部,由旋转吹气探头向铝合金液中通入cl2和ar进行精炼,向炉内吹气处理3min,扒渣,随后保温静置;(4c)将搅拌处理后的金属液浇铸到金属型模具内,得到复合陶瓷颗粒强化铝合金的板状试样。(4d)固溶处理:将强化后的铝合金在高温烘箱中进行固溶处理,固溶温度823k,固溶时间为6h,固溶处理后进行冷水淬火;(4e)自然时效处理:在空气中进行自然时效处理,时效时间为15h;(4f)人工时效处理:在电热鼓风干燥箱中进行人工时效处理,时效温度428k,时效时间为15h。其中,步骤(1)、(2)中球磨混料时,行星式球磨机中所装的球磨罐内预先盛有直径分别为5mm、7mm、11mm、15mm、20mm、22mm的zro2球,每种10个,zro2球质量共800g。另外,控制zro2磨球和混合粉末的质量比是8:1-10:1;其中,步骤(3)中熔体内观察到明亮的火光说明al-ti-b4c-bn体系在铝合金熔体内生成了ticn、tib2、aln陶瓷颗粒。其中设计陶瓷颗粒的生成量依据加入的al-ti-b4c-bn粉体压坯的质量来控制。其中,步骤(3)中,所用到清渣剂的成分为35wt.%kcl、30wt.%mgcl2、5wt.%alf3、15wt.%na3alf6、5wt.%mg3n2、5wt.%na2co3、5wt.%c2cl6。其中,步骤(4)中金属型模具的尺寸和材质分别为:200mm×150mm×20mm和45#钢。0.3wt.%内生混杂尺度颗粒(纳米尺寸的ticn颗粒、亚微米尺寸的tib2和aln颗粒混合体)(如图4和图5)和5wt.%sic陶瓷颗粒(如图6)的复合强化处理al-si-mg合金的弹性模量、拉伸强度和断裂应变分别为:84.8gpa、369mpa、8.0%,比未强化的al-si-mg合金(弹性模量:70.5gpa、拉伸强度:282mpa、断裂应变分别为:7.6%)的性能分别提高了20.2%、30.9%、5.2%。弹性模量和强度提高显著。如表1所示。实施例3:本实施例中的多相陶瓷颗粒混杂制备高弹性模量高强度铝合金的方法,具体如下:(1)al-ti-b4c-bn体系原位内生陶瓷颗粒强化剂的制备,具体如下:(1a)al-ti-b4c-bn体系反应压坯的制备:称取一定量所需的粒度约25μm的al粉、粒度约为25μm的ti粉、粒度为3μm的b4c粉、粒度为1μm的bn粉备用;首先按bn粉、b4c粉的摩尔比为1:1将称量好的bn粉、b4c粉放入球磨罐中。用行星式球磨机将上述粉体以300r/min的速度高速球磨活化处理3h。(1b)预计在al-ti-b4c-bn体系生成ticn、tib2、aln颗粒的总含量为40wt.%,按ti粉,b4c粉,bn粉摩尔比为9:2.8:2.8称量ti粉和混合好的bn粉及b4c粉,余量为al粉,配制成100g粉体。其中al-ti-b4c-bn体系中,ti:b4c:bn的摩尔比为9:2.8:2.8;其中al粉:60g、ti粉:26.31g、b4c粉:9.45g、bn粉:4.24g。(1c)将配制好的粉料与氧化锆磨球放入混料机中,混料机以40r/min的速度混合20h;随后将混合均匀的粉料取出并用铝箔包好,在液压机上冷压制成φ30圆柱形压坯,压力80mpa;高40mm;致密度为68%。(2)sic陶瓷颗粒的预处理,具体如下:(2a)sicp表面氧化处理:将sicp粉末以约为0.8mm的厚度平铺在高纯刚玉坩埚上,高纯刚玉坩埚直径为100mm、高度为20mm;随后将刚玉坩埚置于高温箱式电阻炉内锻烧。sicp高温氧化处理采用分段氧化方式,具体分段氧化工艺如下:①升温到573k,速率为90k/min,在573k下保温15min;②升温到973k,升温速率为70k/min,保温10min;③加热到预定温度保温1273k,保温5h;(2b)球磨预分散处理:取粒度为25μm的al-si-mg(si:9.5wt.%,mg:0.7wt.%,余量为al)合金粉末和粒度为10μm的sicp粉末,按照sicp与al-si-mg合金粉质量比1:4,配制成混合粉末;将配制好的混合粉料放入球磨罐中。球料总体积为球罐容积的2/3,转速为80rpm(正反转交替进行,间隔时间30min)、球磨时间96h。(2c)含有sic颗粒压坯的制备:将球磨混料的粉料取出,用铝箔包好,在液压机上冷压制成直径为φ38的轴向压力致密化的圆柱形陶铝复合压坯,压力80mpa;致密度为68%。(3)多尺度颗粒复合强化al-si-mg合金,具体如下:(3a)将预先称量好的铝合金放置于坩埚中并随坩埚一起放入坩埚式电阻熔炼炉内,升温至1073k;铝合金的成分为si:9.5wt.%,mg:0.7wt.%,余量为al;(3b)待合金完全熔化后并保温30min,加入清渣剂对合金液进行精炼除渣,打渣处理后保温10min。得到未强化al-si-mg合金。(3c)将步骤(1)中制得的压坯在773k下预热2h;将坩埚式电阻熔炼炉内的温度升至1123k,将预热后的压坯压入到所述坩埚中的合金液内;加入压坯的量占总合金液质量的1.25wt.%,生成的陶瓷颗粒实际量为al-si-mg合金液总量的0.5wt.%。(3d)熔体内产生有瞬间明亮的火光后保持压坯浸入合金熔体中不低于1分钟,随后进行机械搅拌,时间为3min;将坩埚的炉温降至1073k;(3e)将含有微米sic陶瓷颗粒的强化剂加入到坩埚内,其中sic陶瓷颗粒的实际加入量为坩埚中金属液总量的6.0wt.%,采用机械搅拌处理熔体300s。随后保温5min;(4)强化后的al-si-mg合金的浇铸成型及热处理:(4a)保温超声波探头后对坩埚中的合金液采用超声处理,处理时间为10min。超声辅助分散结束后,移除超声设备,保温5min。(4b)超声处理后的混合铝液转至保温炉保温,然后进行炉内精炼。在温度为1003k条件下,伸入旋转吹气探头至保温炉底部,由旋转吹气探头向铝合金液中通入cl2和ar进行精炼,向炉内吹气处理5min,扒渣,随后保温静置;(4c)将搅拌处理后的金属液浇铸到金属型模具内,得到复合陶瓷颗粒强化铝合金的板状试样。(4d)固溶处理:将强化后的铝合金在高温烘箱中进行固溶处理,固溶温度813k,固溶时间为10h,固溶处理后进行冷水淬火;(4e)自然时效处理:在空气中进行自然时效处理,时效时间为12h;(4f)人工时效处理:在电热鼓风干燥箱中进行人工时效处理,时效温度433k,时效时间为11h。其中,步骤(1)、(2)中球磨混料时,行星式球磨机中所装的球磨罐内预先盛有直径分别为5mm、7mm、11mm、15mm、20mm、22mm的zro2球,每种10个,zro2球质量共800g。另外,控制zro2磨球和混合粉末的质量比是8:1-10:1;其中,步骤(3)中熔体内观察到明亮的火光说明al-ti-b4c-bn体系在铝合金熔体内生成了ticn、tib2、aln陶瓷颗粒。其中设计陶瓷颗粒的生成量依据加入的al-ti-b4c-bn粉体压坯的质量来控制。其中,步骤(3)中,所用到清渣剂的成分为35wt.%kcl、30wt.%mgcl2、5wt.%alf3、15wt.%na3alf6、5wt.%mg3n2、5wt.%na2co3、5wt.%c2cl6。其中,步骤(4)中金属型模具的尺寸和材质分别为:200mm×150mm×20mm和45#钢。0.5wt.%内生混杂尺度颗粒(纳米尺寸的ticn颗粒、亚微米尺寸的tib2和aln颗粒混合体)和6.0wt.%sic陶瓷颗粒的复合强化处理al-si-mg合金的弹性模量、拉伸强度和断裂应变分别为:89.1gpa、387mpa、7.7%,比未强化的al-si-mg合金(弹性模量:70.5gpa、拉伸强度:282mpa、断裂应变分别为:7.6%)的性能分别提高了26.3%、37.2%、1.3%。弹性模量和强度提高显著。如表1所示。表1对比例和实施例制备的强化亚共晶al-si-mg铝合金的性能样品弹性模量(gpa)抗拉强度(mpa)断裂应变(%)对比例170.52827.6对比例273.62987.8对比例392.53813.5实施例175.93288.1实施例284.83698.0实施例389.13877.7以上所述是本发明的优选实施方式,应当指出,对于本
技术领域:
的普通技术人员来说,在不脱离本发明原理的前提下,还可以做出若干改进和润饰,这些改进和润饰也视为本发明的保护范围。当前第1页12