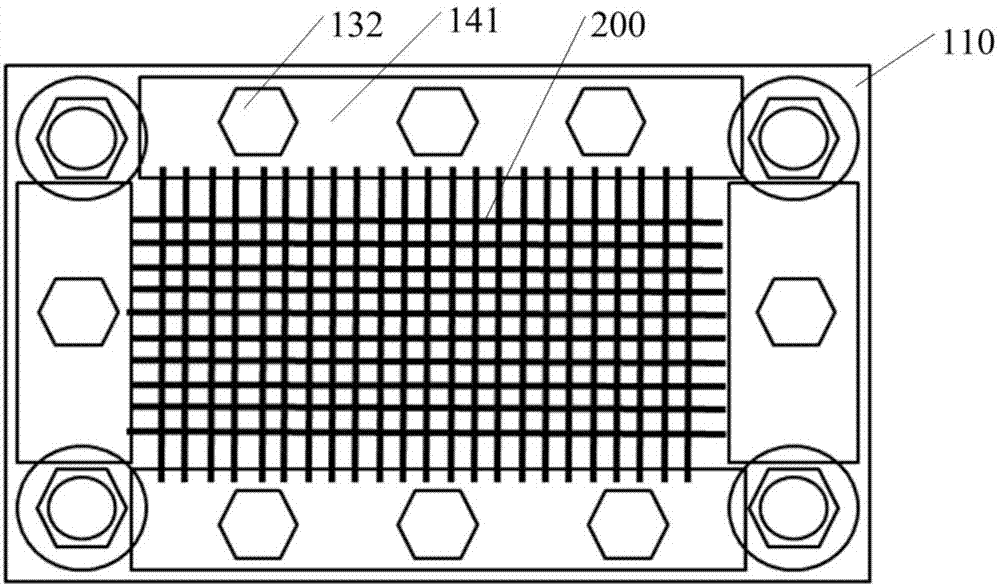
本实用新型涉及油水分离金刚石涂层金属网
技术领域:
,具体而言,涉及一种金属网沉积金刚石涂层装置和金属网沉积金刚石涂层系统。
背景技术:
:进入新世纪以来,油水分离技术已在石油化工、污水处理、食品工程等多个领域得到广泛应用。目前的含油废水主要采用重力沉降、粗粒化、离心分离等方法进行二级处理,这些方法虽然能够处理含油废水,但具有分离效率低、成本高、回收率低等缺点。油水分离是治理含油废水和含水油液的重要工业过程。油水分离是利用同一材料对油和水截然不同的浸润性而使油与水分离的,例如材料具有超疏水超亲油性质或者具有超亲水超疏油性质。随后超疏水性和超亲油性过滤材料的开发研发逐渐深入,这些过滤材料亲油疏水。一般方法是修饰材料的多孔结构为超疏水,而在各种多孔结构中,金属丝网由于其低成本、高机械强度和多孔结构成为理想材料。常规金属网可通过表面改性的方式在金属网状结构的表面进行改性,可以使用酸碱腐蚀的方法或者使用表面改性剂进行改性处理,典型通过腐蚀改变表面结构诱导超疏水超亲油性质,例如将金属铜网在硝酸溶液中腐蚀,增加铜丝表面的粗糙度,并通过修饰十六烷硫醇使其具备超疏水超亲油性质,该方法可以获得油水分离的效果。而由于油水混合状态、油水含量、油水混合液中所含的有机物种类、油水分离对象等多种因素的不同,导致油水分离难度变得越来越大。同时金属网进行表面改性使其具有疏水亲油的特性在实际应用中也遇到了诸多限制:首先,金属网本身耐腐性能有限,容易被环境所腐蚀,使用寿命较短;其次,金属网表面改性后应用于油水分离中特异性较强,针对的油的种类较少,特定的油水分离需要对应特定的腐蚀与改性剂处理;再次,通过酸碱腐蚀或者采用表面改性剂改性的方法进行油水分离时,时间不能很持久,酸碱腐蚀及添加表面改性剂的方法在金属表面添加的疏水官能团只在表面,容易失效。金刚石是世界上最硬的物质,拥有极为稳定的物理化学性质和较高的弹性模量。在金属网上沉积金刚石涂层可以使金属网获得疏水性和/或亲水性,由于金刚石具有极高的物理化学稳定性,不仅可以耐强酸强碱等的腐蚀,而且金刚石的高硬度及弹性模量都可以大大提高其使用寿命。专利CN103741116A提出了一种在金属网衬底上生长CVD金刚石涂层使金刚石网表面具有超疏水性和亲水性的方法,但是该方法过程复杂,所使用的沉积设备昂贵、成本高,只能在小尺寸工件上长金刚石薄膜,不利于工业化生产和工业用途。目前主要采用化学气相沉积(ChemicalVaporDeposition,CVD)方式沉积金刚石涂层,但是沉积时温度较高,由于金属网较薄,在沉积过程中容易变形,造成沉积不均匀,薄膜生长不均匀,降低了金刚石涂层金属网的油水分离效果。有鉴于此,特提出本实用新型。技术实现要素:本实用新型的目的之一在于提供一种金属网沉积金刚石涂层装置,装置结构简单,通过采用该装置可以将金属网固定住,沉积过程金属网不会变形,非常适用于三维方向上的化学气相沉积涂层的制备。本实用新型的目的之二在于提供一种包含所述的金属网沉积金刚石涂层装置的金属网沉积金刚石涂层系统,具有与上述金属网沉积金刚石涂层装置相同的优势。为了实现本实用新型的上述目的,特采用以下技术方案:第一方面,提供了一种金属网沉积金刚石涂层装置,所述金属网沉积金刚石涂层装置包括夹具本体;所述夹具本体包括平行设置的第一本体和第二本体,所述第一本体和所述第二本体的本体内部均独立地具有空洞,金属网置于所述第一本体与所述第二本体之间,且金属网边缘尺寸大于所述第一本体和所述第二本体的空洞尺寸,所述第一本体与所述第二本体通过垂直于所述第一本体的可拆卸夹紧机构固定,以夹紧所述第一本体与所述第二本体之间的金属网。优选地,在本实用新型技术方案的基础上,所述第一本体和所述第二本体均为钼盘。优选地,在本实用新型技术方案的基础上,所述可拆卸夹紧机构包括螺栓和螺母。优选地,在本实用新型技术方案的基础上,所述夹具本体还包括第一弹簧片或第二弹簧片(142);第一弹簧片位于所述第一本体内侧;第二弹簧片位于所述第二本体内侧。优选地,在本实用新型技术方案的基础上,所述夹具本体还包括第一弹簧片和第二弹簧片;所述第一弹簧片位于所述第一本体内侧;所述第二弹簧片位于所述第二本体内侧。第二方面,提供了一种包含所述的金属网沉积金刚石涂层装置的金属网沉积金刚石涂层系统。优选地,在本实用新型技术方案的基础上,所述金属网沉积金刚石涂层系统包括真空系统和与所述真空系统相连通的反应室;所述反应室内设有热丝加热器;所述热丝加热器包括上下排热丝;所述金属网沉积金刚石涂层装置至于上下排热丝之间。优选地,在本实用新型技术方案的基础上,所述热丝加热器上方设有气体分配器;所述气体分配器包括氢气室、甲烷气室和水冷室;所述氢气室设有氢气通道,用于通入氢气;所述甲烷气室设有甲烷通道,用于通入甲烷气体;所述水冷室设有进水口和出水口,用于通入冷却水。优选地,在本实用新型技术方案的基础上,所述热丝加热器(300)的热丝为钨丝;所述钨丝直径为1-3mm。优选地,在本实用新型技术方案的基础上,所述上下排热丝之间的垂直距离为30-40mm;其中,上排热丝距离金属网的垂直距离为20-25mm。与已有技术相比,本实用新型具有如下有益效果:本实用新型设计的适合在金属网表面三维沉积纳米金刚石涂层的装置结构简单,可以将金属网固定住,有效防止沉积过程中金属网变形,非常适用于三维方向上的化学气相沉积涂层的制备。同时,通过采用本实用新型的金属网沉积金刚石涂层装置能够使沉积过程中的金属网的沉积温度更加均匀,从而使金刚石薄膜生长得更加均匀,得到的金刚石涂层金属网的油水分离效果好,分离效率高。附图说明图1为本实用新型一种实施方式的金属网沉积金刚石涂层装置的俯视图;图2为本实用新型一种实施方式的金属网沉积金刚石涂层装置的主视图;图3为本实用新型实施例1金属网表面形貌图;图4为本实用新型实施例1金属网上生长的金刚石薄膜表面形貌图。图标:100-夹具本体;110-第一本体;120-第二本体;130-可拆卸夹紧机构;131-螺栓;132-螺母;141-第一弹簧片;142-第二弹簧片;200-金属网;300-热丝加热器。具体实施方式下面将结合附图对本实用新型的技术方案进行清楚、完整地描述,显然,所描述的实施例是本实用新型一部分实施例,而不是全部的实施例。基于本实用新型中的实施例,本领域普通技术人员在没有做出创造性劳动前提下所获得的所有其他实施例,都属于本实用新型保护的范围。根据本实用新型的第一个方面,提供了一种金属网沉积金刚石涂层装置,图1为本实用新型一种实施方式的金属网沉积金刚石涂层装置的俯视图;图2为本实用新型一种实施方式的金属网沉积金刚石涂层装置的主视图。如图1和图2所示,金属网沉积金刚石涂层装置包括夹具本体100;夹具本体100包括平行设置的第一本体110和第二本体120,第一本体110和第二本体120的本体内部均独立地具有空洞,金属网200置于第一本体110与第二本体120之间,且金属网200边缘尺寸大于第一本体110和第二本体120的空洞尺寸;第一本体110与第二本体120通过垂直于第一本体110的可拆卸夹紧机构130固定,以夹紧第一本体110与第二本体120之间的金属网200。使用时将金属网200置于第一本体110和第二本体120之间,用可拆卸夹紧机构130将第一本体110与第二本体120夹紧,从而夹紧之间的金属网200,由于第一本体110和第二本体120中间是空的,金属网200边缘尺寸大于第一本体110和第二本体120的空洞尺寸,金属网200可以被架在第一本体110和第二本体120之间。空洞形状不限,只要金属网200边缘被架在第一本体110和第二本体120之间不会窜出即可,形成一个夹具。沉积涂层时,将此装置置于基板位置。典型但非限制性的沉积涂层的方法为化学气相沉积(ChemicalVaporDeposition,CVD)法,包括热丝CVD、微波等离子体CVD或火焰燃烧法等。典型但非限制性的金属网例如为铜网、钛网或不锈钢网。在金属网上进行金刚石涂层沉积时通过采用本实用新型的金属网沉积金刚石涂层装置可以将金属网固定住,有效防止沉积过程中金属网变形,同时使沉积过程中的金属网的沉积温度更加均匀,从而使金刚石薄膜生长得更加均匀。由于金属网表面直接沉积出具有疏水亲油的纳米金刚石涂层,使金属网具有超好的疏水亲油性质,得到的金刚石涂层金属网的油水分离效果好,分离效率高。本实用新型设计的适合在金属网表面三维沉积纳米金刚石涂层的装置结构简单,适用于三维方向上的化学气相沉积涂层的制备。不仅适合在小尺寸工件的沉积,也适合对大面积金属网进行批量沉积,适合工业化生产和工业化应用。在一种优选的实施方式中,第一本体和第二本体均为钼盘。钼熔点高,高温下可以保持高强度,同时具有高弹性模量和低重量,是夹具本体的理想载体材料。在一种优选的实施方式中,可拆卸夹紧机构130包括螺栓131和螺母132。可拆卸夹紧机构包括多套螺栓和螺母,多个螺栓穿过平行的第一本体和第二本体,并用螺母调节第一本体和第二本体之间的距离,将其拧紧,夹紧中间的金属网,将金属网固定住,从而防止金属网高温下变形,使沉积更加均匀。在一种优选的实施方式中,夹具本体100还包括第一弹簧片141或第二弹簧片142;第一弹簧片141位于第一本体110内侧;第二弹簧片142位于所述第二本体120内侧。在一种优选的实施方式中,夹具本体100还包括第一弹簧片141和第二弹簧片142;第一弹簧片141位于第一本体110内侧;第二弹簧片142位于第二本体120内侧。这里的内侧是指金属网与本体接触的一侧。通过设置第一弹簧片和/或第二弹簧片,能够避免金属网用螺栓螺母固定时出现缝隙,使金属网夹紧固定得更加牢固,进一步防止金属网变形。根据本实用新型的第二个方面,提供了一种包含所述的金属网沉积金刚石涂层装置的金属网沉积金刚石涂层系统。金属网沉积金刚石涂层系统具有与上述金属网沉积金刚石涂层装置相同的优势,再此不再赘述。在一种优选的实施方式中,金属网沉积金刚石涂层系统包括真空系统和与真空系统相连通的反应室;反应室内设有热丝加热器300;热丝加热器包括上下排热丝;金属网沉积金刚石涂层装置至于上下排热丝之间。采用热丝气相沉积方式在金属网上沉积金刚石涂层。热丝化学气相沉积法温度通常较其它方法(例如微波法、火焰燃烧法)低,是一种低温生长纳米金刚石的方法,可以有效避免金属网在沉积过程中的变形。与其他方法相比,该方法成膜速率快、沉积设备简单、适合大面积沉积,制备工艺简单、工艺稳定、成本低,适合工业化生产和大规模工业化使用。采用热丝化学气相沉积的作用,在金属网上三维(各个方向)生长金刚石涂层,该方法制备得到的金刚石涂层金属网疏水亲油,可应用于油水分离中,油水分离效率高;由于金刚石具有极高的物理化学稳定性,不仅可以耐强酸强碱等的腐蚀,而且金刚石的高硬度及弹性模量都可以大大提高金属网本身的使用寿命。在一种优选的实施方式中,热丝加热器300上方设有气体分配器;气体分配器包括氢气室、甲烷气室和水冷室;氢气室设有氢气通道,用于通入氢气;甲烷气室设有甲烷通道,用于通入甲烷气体;水冷室设有进水口和出水口,用于通入冷却水。沉积过程中需要通入CH4和H2,其中CH4为金刚石的生长提供碳源,H2产生活性氢基团-H去刻蚀非金刚石相的SP2键。优选地,控制氢气通道出口平面至热丝加热器上排热丝平面距离在3-5mm。通过控制氢气流出与热丝之间的距离,可以使H2产生活性氢基团-H更好地去刻蚀非金刚石相的SP2键,得到质量更好的金刚石薄膜。在一种优选的实施方式中,热丝加热器300的热丝为钨丝;钨丝直径为1-3mm,例如1mm、2mm或3mm。钨丝熔点高,电阻率和电阻温度系数度也较高,可用较少的能量将钨丝很快的加热到沉积温度,节约能量。在一种优选的实施方式中,上下排热丝之间的垂直距离为30-40mm,例如30mm、32mm、34mm、35mm、36mm、38mm或40mm;其中,上排热丝距离金属网200的垂直距离为20-25mm,例如为20mm、21mm、22mm、23mm、24mm或25mm。通过控制上、下排热丝的离样距离保证金属网的沉积温度,使沉积温度更适宜更均匀。优选地,一种金刚石涂层金属网的制备方法,包括以下步骤:采用上述的金属网沉积金刚石涂层系统通过热丝化学气相沉积方式在金属网表面沉积金刚石涂层。优选地,反应室温度为500-800℃,例如为500℃、550℃、600℃、650℃、700℃、750℃或800℃。优选地,反应室温度以15-25℃/min的升温速率从室温升至500-800℃,并保温10-20min。升温速率典型但非限制性的例如为15℃/min、20℃/min或25℃/min。保温时间典型但非限制性的例如为10min、15min或20min。热丝化学气相沉积时反应室温度较低,进一步缓解了金属网在沉积过程中容易变形导致不能有效沉积的缺陷。优选地,气体分配器还包括惰性气体;典型但非限制性的惰性气体为氩气。反应过程中控制氢气、甲烷气体和惰性气体的总流量为400-600mL/min,其中甲烷气体流量占总流量的1-5%,氢气流量占总流量的25-45%,惰性气体流量占总流量的50-70%。通过控制总流量以及氢气、甲烷气体和惰性气体的流量占比,以生长出质量好、附着力强的纳米金刚石薄膜。氢气过少不利于产生活性氢基团-H去刻蚀非金刚石相的SP2键,CH4气体过少不能为金刚石的生长提供充足的碳源。优选地,沉积时沉积压强为1500-2000Pa。通过控制沉积压强,有利于获得高质量的膜层,生长的金刚石薄膜结构致密。优选地,沉积时间控制在1.5-3h,例如为1.5h、2h、2.5h或3h。通过控制沉积时间生长出的金刚石薄膜厚度适宜,附着力较好。在一种优选的实施方式中,采用热丝化学气相沉积方式在金属网表面沉积金刚石涂层前对金属网进行纳米金刚石植晶处理。植晶处理是在基体表面预先植入一层微小的金刚石颗粒作为成核点,以提高金刚石沉积密度。典型但非限制性的植晶处理方式是用含金刚石微粉的悬浮液对基底表面进行超声处理。优选地,植晶处理为将金属网放入植晶溶液中超声20-60min后取出干燥,优选干燥为用氮气吹干。超声时间典型但非限制性的例如为20min、30min、40min、50min或60min。优选地,植晶溶液为纳米金刚石悬浮液;优选纳米金刚石悬浮液包括纳米金刚石粉、碳酸二甲酯和水,纳米金刚石粉质量占纳米金刚石悬浮液质量的0.005-0.01%,碳酸二甲酯在纳米金刚石悬浮液中的浓度为1×10-6-10×10-6mol/L;优选纳米金刚石悬浮液的pH为2-4。纳米金刚石悬浮液是纳米金刚石粉分散于碳酸二甲酯和水的溶剂中,纳米金刚石粉质量分数为0.005-0.01%,例如0.005%、0.006%、0.007%、0.008%、0.009%或0.01%。碳酸二甲酯(DMC)浓度为1×10-6mol/L、2×10-6mol/L、3×10-6mol/L、4×10-6mol/L、5×10-6mol/L、6×10-6mol/L、7×10-6mol/L、8×10-6mol/L、9×10-6mol/L或10×10-6mol/L。纳米金刚石悬浮液的pH为2-4,例如pH2、pH3或pH4。通过采用该纳米金刚石悬浮液(植晶溶液)对金属网进行植晶处理后残留在金属网表面缺陷内的金刚石微粉的碎屑可以为热丝化学气相沉积法沉积金刚石提供成核核心,提高形核密度,显著提高金刚石薄膜与基底的附着力。在一种优选的实施方式中,金刚石涂层金属网的制备方法,包括以下步骤:(a)对金属网表面进行清洗;(b)对清洗好的金属网进行腐蚀处理;(c)对金属网进行再清洗;(d)对金属网进行纳米金刚石植晶处理;(e)植晶处理后采用上述的金属网沉积金刚石涂层系统通过热丝化学气相沉积方式在金属网表面沉积金刚石涂层,得到金刚石涂层金属网;优选地,步骤(a)包括先用水超声清洗2-3次,每次5-10min,再用酒精超声清洗1-2次,每次5-10min。先对金属网表面进行清洗,清除金属网表面的杂质,保持试样表面清洁干净。优选地,步骤(b)包括先在碱溶液中超声5-10min,然后在酸溶液中超声30-60s;优选碱溶液为0.5-1mol/L的NaOH溶液;优选酸溶液为0.5-1mol/L的HCl溶液。先在碱溶液中超声5-10min,例如5min、6min、7min、8min、9min或10min,然后在酸溶液中超声30-60s,例如30s、40s、50s或60s。碱溶液浓度例如为0.5mol/L、0.6mol/L、0.7mol/L、0.8mol/L、0.9mol/L或1mol/L;酸溶液浓度例如为0.5mol/L、0.6mol/L、0.7mol/L、0.8mol/L、0.9mol/L或1mol/L。对清洗好的金属网进行腐蚀处理,增加表面粗糙度,提高金刚石颗粒的吸附密度。优选地,步骤(c)包括先用水超声清洗2-3次,每次5-10min,再用酒精超声清洗1-2次,每次5-10min。对腐蚀处理后的金属网进行清洗,将残留在金属网中的腐蚀溶液清洗干净。优选地,步骤(d)包括将金属网放入植晶溶液中超声20-60min后取出干燥,优选干燥为用氮气吹干;优选植晶溶液为纳米金刚石悬浮液;优选包括纳米金刚石粉、碳酸二甲酯和水,纳米金刚石粉质量占纳米金刚石悬浮液质量的0.005-0.01%,碳酸二甲酯在纳米金刚石悬浮液中的浓度为1×10-6-10×10-6mol/L;优选纳米金刚石悬浮液的pH为2-4。对金属网进行金刚石的植晶处理。典型的植晶溶液为爆轰纳米金刚石悬浮液,成分为金刚石粉质量分数0.005%,DMC浓度为5×10-6M,其余为去离子水,pH为3。植晶方式为将试样放入植晶溶液中超声30分钟,取出,用氮气吹干。步骤(e)采用上述的金属网沉积金刚石涂层系统通过热丝化学气相沉积方式在金属网表面沉积金刚石涂层,沉积参数与上文的描述内容相同。该方法通过腐蚀处理和植晶处理的表面预处理方法增加了生长的成核密度和二次形核率,得到具有纳米尺寸晶粒度的薄膜,并通过采用本实用新型的金属网沉积金刚石涂层系统对金属网进行金刚石涂层沉积,金属网上生长出的金刚石薄膜均匀,质量好,将得到的金刚石涂层金属网用于油水分离中分离效率高、使用寿命长。优选地,可用于包含常见有机溶剂、动植物油、石油、汽、柴油及原油等含油污水的分离。优选地,将金刚石涂层金属网置于油水混合物中,油能够通过金刚石涂层金属网而水不能通过金刚石涂层金属网,达到油水分离的目的。下面通过具体的实施例和对比例进一步说明本实用新型,但是,应当理解为,这些实施例仅是用于更详细地说明之用,而不应理解为用于以任何形式限制本实用新型。本实用新型涉及的各原料均可通过商购获取。实施例和对比例的金属网为铜网。实施例和对比例使用的爆轰纳米金刚石悬浮液成分为金刚石粉质量分数0.005%,DMC浓度为5×10-6M,其余为去离子水,pH为3。实施例采用的金属网沉积金刚石涂层系统包括金属网沉积金刚石涂层装置、真空系统和与真空系统相连通的反应室;反应室内设有热丝加热器;热丝加热器包括上下排热丝;热丝为钨丝;上下排热丝之间的垂直距离为30-40mm。金属网沉积金刚石涂层装置至于上下排热丝之间。热丝加热器上方设有气体分配器;气体分配器包括氢气室、甲烷气室和氩气室;氢气室用于通入氢气;甲烷气室用于通入甲烷气体;氩气室用于通入氩气。金属网沉积金刚石涂层装置包括位于上下排热丝之间的夹具本体;夹具本体包括平行设置的上下钼盘,上下钼盘中间均有空洞,呈口字形,上下钼盘内侧均设有形状对应的弹簧片,金属网置于钼盘内侧的弹簧片之间,金属网边缘尺寸大于上下钼盘的空洞尺寸,将螺栓垂直穿入夹具本体并贯穿上下钼盘,用螺母拧紧,使金属网被夹紧。实施例1一种金刚石涂层金属网的制备方法,包括以下步骤:(1)对金属网表面进行清洗,首先使用去离子水超声清洗2次,每次5分钟,最后用酒精超声清洗5分钟,用氮气吹干;(2)对清洗好的金属网进行腐蚀处理,增加表面粗糙度,并提高金刚石纳米颗粒的吸附密度。腐蚀处理为在碱溶液中超声清洗5分钟,然后在酸溶液中清洗30秒。其中碱溶液为1M的NaOH,酸溶液为1M的HCl;(3)对金属网进行清洗,将残留在金属网中的腐蚀溶液清洗干净。使用去离子水超声清洗2次,每次5分钟,最后用酒精超声清洗5分钟,用氮气吹干;(4)对金属网进行纳米金刚石的植晶处理,植晶溶液为爆轰纳米金刚石悬浮液,植晶方式为将试样放入植晶溶液中超声30分钟,取出,用氮气吹干;(5)采用金属网沉积金刚石涂层系统对植晶之后的金属网进行三维纳米金刚石薄膜的制备,以20℃/min的升温速度从室温升至600℃,并保温15min;反应过程中控制气体总流量为500mL/min,甲烷+氩气+氢气的总流量为500mL/min,其中甲烷10mL/min,氩气282mL/min,氢气为208mL/min。压强为1500Pa。上排热丝离金属网沉积金刚石涂层装置中金属网距离25mm,下排热丝离金属网沉积金刚石涂层装置中金属网距离15mm,沉积时间为2小时。图3为实施例1金属网表面形貌图;图4为实施例1金属网上生长的金刚石薄膜表面形貌图。实施例2一种金刚石涂层金属网的制备方法,包括以下步骤:(1)对金属网表面进行清洗,首先使用去离子水超声清洗3次,每次5分钟,最后用酒精超声清洗5分钟,用氮气吹干。(2)对清洗好的金属网进行腐蚀处理,增加表面粗糙度,并提高金刚石纳米颗粒的吸附密度。腐蚀处理为在碱溶液中超声清洗10分钟,然后在酸溶液中清洗60秒。其中碱溶液为:0.5M的NaOH,酸溶液为0.5M的HCl。(3)对金属网进行清洗,将残留在金属网中的腐蚀溶液清洗干净。使用去离子水超声清洗3次,每次5分钟,最后用酒精超声清洗5分钟,用氮气吹干。(4)对金属网进行纳米金刚石的植晶处理,植晶溶液为爆轰纳米金刚石悬浮液。植晶方式为将试样放入植晶溶液中超声30分钟,取出,用氮气吹干。(5)采用金属网沉积金刚石涂层系统对植晶之后的金属网进行三维纳米金刚石薄膜的制备,以20℃/min的升温速度从室温升至600℃,并保温15min;反应过程中控制气体总流量为400mL/min,甲烷+氩气+氢气的总流量为400mL/min,其中甲烷5mL/min,氩气255mL/min,氢气为140mL/min。压强为1500Pa。上排热丝离金属网沉积金刚石涂层装置中金属网距离25mm,下排热丝离金属网沉积金刚石涂层装置中金属网距离15mm,沉积时间为3小时。实施例3一种金刚石涂层金属网的制备方法,包括以下步骤:(1)对金属网表面进行清洗,首先使用去离子水超声清洗2次,每次10分钟,最后用酒精超声清洗5分钟,用氮气吹干。(2)对清洗好的金属网进行腐蚀处理,增加表面粗糙度,并提高金刚石纳米颗粒的吸附密度。腐蚀处理为在碱溶液中超声清洗8分钟,然后在酸溶液中清洗40秒。其中碱溶液为:0.6M的NaOH,酸溶液为0.6M的HCl。(3)对金属网进行清洗,将残留在金属网中的腐蚀溶液清洗干净。使用去离子水超声清洗2次,每次10分钟,最后用酒精超声清洗5分钟,用氮气吹干。(4)对金属网进行纳米金刚石的植晶处理,植晶溶液为爆轰纳米金刚石悬浮液。植晶方式为将试样放入植晶溶液中超声30分钟,取出,用氮气吹干。(5)采用金属网沉积金刚石涂层系统对植晶之后的金属网进行三维纳米金刚石薄膜的制备,以20℃/min的升温速度从室温升至600℃,并保温15min;反应过程中控制气体总流量为420mL/min,甲烷+氩气+氢气的总流量为420mL/min,其中甲烷15mL/min,氩气255mL/min,氢气为150mL/min。压强为1500Pa。上排热丝离金属网沉积金刚石涂层装置中金属网距离25mm,下排热丝离金属网沉积金刚石涂层装置中金属网距离15mm,沉积时间为1.5小时。实施例4一种金刚石涂层金属网的制备方法,包括以下步骤:(1)对金属网表面进行清洗,首先使用去离子水超声清洗2次,每次5分钟,最后用酒精超声清洗10分钟,用氮气吹干。(2)对清洗好的金属网进行腐蚀处理,增加表面粗糙度,并提高金刚石纳米颗粒的吸附密度。腐蚀处理为在碱溶液中超声清洗5分钟,然后在酸溶液中清洗30秒。其中碱溶液为:1M的NaOH,酸溶液为1M的HCl。(3)对金属网进行清洗,将残留在金属网中的腐蚀溶液清洗干净。使用去离子水超声清洗2次,每次5分钟,最后用酒精超声清洗10分钟,用氮气吹干。(4)对金属网进行纳米金刚石的植晶处理,植晶溶液为爆轰纳米金刚石悬浮液。植晶方式为将试样放入植晶溶液中超声20分钟,取出,用氮气吹干。(5)采用金属网沉积金刚石涂层系统对植晶之后的金属网进行三维纳米金刚石薄膜的制备,以15℃/min的升温速度从室温升至500℃,并保温20min;反应过程中控制气体总流量为500mL/min,甲烷+氩气+氢气的总流量为500mL/min,其中甲烷5mL/min,氩气255mL/min,氢气为140mL/min。压强为2000Pa。上排热丝离金属网沉积金刚石涂层装置中金属网距离25mm,下排热丝离金属网沉积金刚石涂层装置中金属网距离15mm,沉积时间为4小时。实施例5一种金刚石涂层金属网的制备方法,包括以下步骤:(1)对金属网表面进行清洗,首先使用去离子水超声清洗2次,每次5分钟,最后用酒精超声清洗5分钟,用氮气吹干。(2)对清洗好的金属网进行腐蚀处理,增加表面粗糙度,并提高金刚石纳米颗粒的吸附密度。腐蚀处理为在碱溶液中超声清洗5分钟,然后在酸溶液中清洗30秒。其中碱溶液为:1M的NaOH,酸溶液为1M的HCl。(3)对金属网进行清洗,将残留在金属网中的腐蚀溶液清洗干净。使用去离子水超声清洗2次,每次5分钟,最后用酒精超声清洗5分钟,用氮气吹干。(4)对金属网进行纳米金刚石的植晶处理,植晶溶液为爆轰纳米金刚石悬浮液。植晶方式为将试样放入植晶溶液中超声60分钟,取出,用氮气吹干。(5)采用金属网沉积金刚石涂层系统对植晶之后的金属网进行三维纳米金刚石薄膜的制备,以25℃/min的升温速度从室温升至800℃,并保温10min;反应过程中控制气体总流量为500mL/min,甲烷+氩气+氢气的总流量为500mL/min,其中甲烷5mL/min,氩气255mL/min,氢气为140mL/min。压强为1500Pa。上排热丝离金属网沉积金刚石涂层装置中金属网距离20mm,下排热丝离金属网沉积金刚石涂层装置中金属网距离18mm,沉积时间为2小时。对比例1一种金刚石涂层金属网的制备方法,与实施例1不同的是,步骤(5)金属网沉积金刚石涂层系统中不含金属网沉积金刚石涂层装置,直接将金属网放置于基底位置,使上排热丝离金属网距离25mm,下排热丝离金属网距离15mm。对比例2一种金刚石涂层金属网的制备方法,与实施例1不同的是,步骤(5)利用微波等离子体CVD方法对植晶之后的金属网进行三维纳米金刚石薄膜的制备,实验条件:反应气体总流量为300sccm,比例为H2:CH4=292:8(sccm),压强为130Torr,微波功率1.7kw,沉积衬底温度约为800℃,沉积时间为7h,得到金刚石膜厚约为2μm。对比例3一种金刚石涂层金属网的制备方法,与实施例1不同的是,步骤(5)利用火焰燃烧法对植晶之后的金属网进行三维纳米金刚石薄膜的制备,实验条件:反应气体总流量为500sccm,比例为H2:C2H2:O2=5:245:250(sccm),压强为1000Pa,沉积衬底温度约为1000℃,沉积时间为5h,得到金刚石膜厚约为2μm。试验例用接触角测量仪测量实施例1得到的金刚石涂层金属网,该金刚石涂层金属网表面在空气环境中对3微升的正己烷的接触角小于120,为超疏水材料;再将金刚石涂层金属网浸没在正己烷中,测量金属网表面对3微升的水的接触角大于1400,为亲油材料。为了考察实施例和对比例得到的金刚石涂层金属网的油水分离性能,进行油水分离效率和使用寿命,测试方法如下:(1)油水分离效率:将得到的金属网放置于垂直放置的过滤器中间并用夹子固定,将正己烷和水按比例1:2在磁力搅拌条件下获得油水混合物,倒入上部分的进口倒入过滤器中,混合物中的正己烷快速通过金属网,而水被阻挡在金属网的上方不能通过,实现油水分离,通过计算保留在金属网上方的水的重量与原始倒入油水混合物中水的重量的比值,得到分离效率。(2)使用寿命:将得到的金属网按照上述油水分离试验重复进行使用,每次使用后用水清洗干净,使用50次后计算分离效率。测试结果如表1所示。表1实施例或对比例油水分离效率%重复使用50次后分离效率%实施例199.499.2实施例299.699.3实施例399.799.2实施例499.399.0实施例599.899.4对比例195.891.4对比例297.592.8对比例386.675.4从表1的结果可以看出,实施例1-5通过采用本实用新型的金属网沉积金刚石涂层系统和装置得到的金属网油水分离效率高,达99%以上,且重复利用50次后,分离效率几乎保持不变,这表明制备的金属网具有优异的可回收性,使用寿命长。对比例1没有采用金属网沉积金刚石涂层装置的夹具对金属网进行固定,得到的金属网油水分离性能有所下降,这是由于在高温下金属网在沉积过程中有轻微变形,导致金属网上各点的沉积温度不同,薄膜生长不均匀,影响其油水分离性能。对比例2采用微波等离子体CVD方法进行金刚石涂层沉积,沉积温度高,沉积设备昂贵,成本高,而且只能在小尺寸工件上长金刚石薄膜,而油水分离的金属网都是大面积的,故该方法在金属网表面沉积金刚石薄膜只适合实验室研究,不适合工业化生产和大量的工业用途。对比例3采用火焰燃烧法进行金刚石涂层沉积,得到的金属网的油水分离效果不好,这是由于火焰燃烧法沉积温度高,金属网上生长的金刚石薄膜不均匀,影响其油水分离性能。尽管已用具体实施例来说明和描述了本实用新型,然而应意识到,在不背离本实用新型的精神和范围的情况下可作出许多其它的更改和修改。因此,这意味着在所附权利要求中包括属于本实用新型范围内的所有这些变化和修改。当前第1页1 2 3