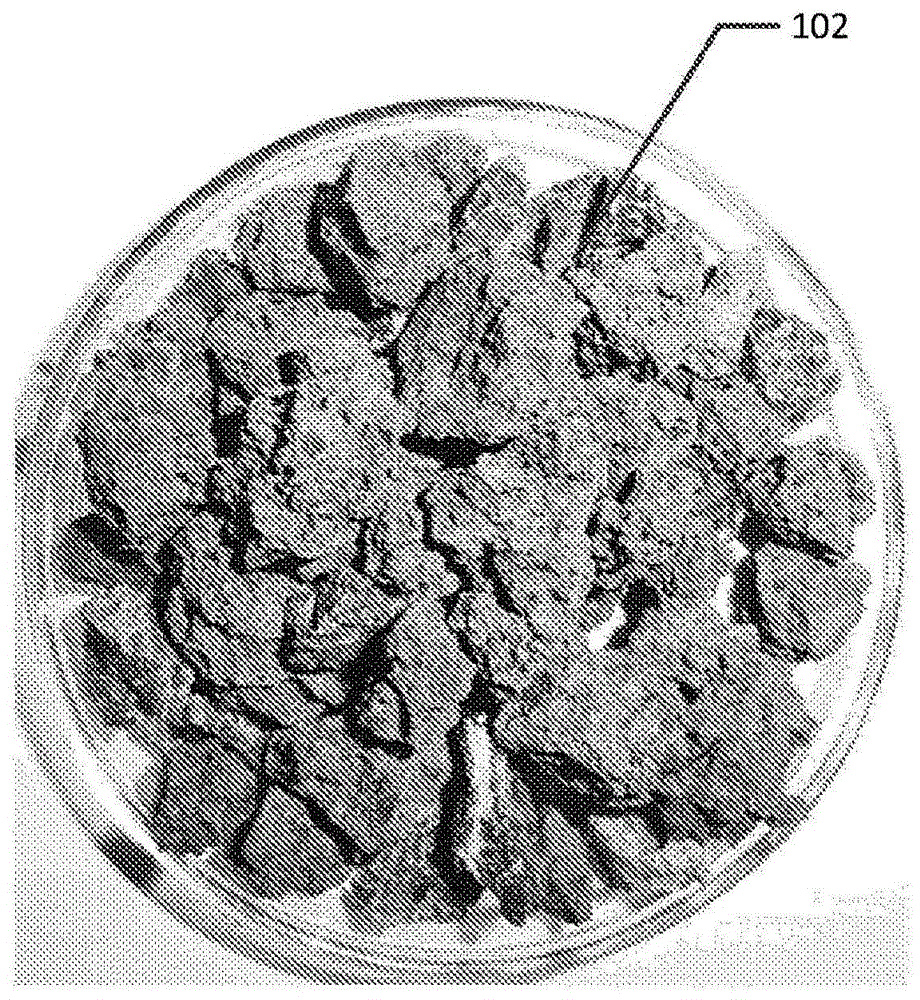
领域本公开内容涉及由回收的工业钢废物形成的陶瓷和形成这样的陶瓷的方法。发明
背景技术:
:全世界,由钢铁工业产生几百万吨废物(称为炉渣),从而导致废物管理担忧。炉渣全部是铸铁的非金属性部分,其在炉中的熔融物表面处由于较低的密度自然上升。在熔融钢流出之前,将炉渣从炉中倒出在地上。倒出的热炉渣由重载铲型装载机收集并移动至冷却室喷水,以便将其装在自卸卡车上并运输至金属回收的下一步骤。在阿拉伯联合酋长国(uae),emiratessteel是位于阿布扎比的大型钢厂,每年制造约350万吨钢产品。由这个产量,每年产生约700,000吨的钢炉渣。大约30%至40%的这些副产物作为集料被回收用于道路建设或铁路道渣,目前以约$3/吨的价格销售。然而,剩余的(表示大于400,000吨每年)目前没有可用的应用并且被储存在现场等待潜在的未来新应用。由于该国家禁止填埋工业废物,所以炉渣是废物管理问题,并且需要采取行动来确定新的市场以利用这些炉渣。已经努力将炉渣再使用于不同的目的。来自冶金工业的废物是在整个工业过程中直接产生的副产物,并且通常不需要补充处理以被安全地再使用。目前,在水泥生产工业中使用炉渣作为对熟料的补充,生产已知的波特兰高炉炉渣水泥(pbfs)。再使用钢炉渣的另一方式是作为陶瓷砖生产中的添加剂。另外,可使用钢炉渣作为用于道路和用于建设堤坝的沥青集料。它也可帮助稳定河底、河岸等。努力保护环境、人类健康,并在最小的环境影响下有效利用资源。这些应用目标是以相对低的附加值回收大量废物。发明概述本公开内容的一个方面涉及由钢炉渣形成陶瓷的方法。该方法包括:研磨表现出5mm或更小直径的钢炉渣以形成粉末,筛分该粉末以保留粒度在20μm至400μm范围内的粉末,用磁体从该粉末中去除游离铁,在700℃至1200℃范围内的温度下热处理该粉末1小时至10小时范围内的时间段,并氧化该粉末中的保留的铁,在20mpa至300mpa范围内的压缩压力下压实该粉末,并在700℃至1400℃范围内的温度下烧结该粉末0.5小时至4小时范围内的时间段以提供陶瓷。在另一方面,本公开内容涉及陶瓷。该陶瓷包括钢炉渣固结体,其中该钢炉渣包含:在2-12重量%范围内存在的氧化铝(al2o3),在24-60重量%范围内存在的氧化钙(cao),在20-33重量%范围内存在的氧化铁(fe2o3),在3-15重量%范围内存在的氧化镁(mgo),在9-20重量%范围内存在的二氧化硅(sio2),任选地,以下一种或多种:在0.01-8重量%范围内存在的mno、tio2和游离cao,和不可避免的杂质,其中重量%是相对于陶瓷总重量的重量百分比,以包括不可避免的杂质在内提供100重量%,其中陶瓷表现出2550kg/m3至2725kg/m3范围内的密度,并且陶瓷表现出在10-6mm/mm/min的应变速率下测量的40mpa至120mpa范围内的失效压缩强度。在又一方面,本公开内容涉及热能储存系统。该热能储存系统包括储存容器;放置在储存容器内的多个陶瓷模块;接触陶瓷模块的传热流体;与所述储存容器流体连通的入口扩散器;和与所述罐连通的出口扩散器,其中所述入口扩散器、所述储存容器、所述陶瓷模块和所述出口扩散器限定用于所述传热流体的流动路径。该陶瓷模块包含钢炉渣固结体,其中该钢炉渣包含:在2-12重量%范围内存在的氧化铝(al2o3),在24-60重量%范围内存在的氧化钙(cao),在20-33重量%范围内存在的氧化铁(fe2o3),在3-15重量%范围内存在的氧化镁(mgo),在9-20重量%范围内存在的二氧化硅(sio2),任选地,以下一种或多种:在0.01-8重量%范围内存在的mno、tio2和游离cao,和不可避免的杂质,其中重量%是相对于陶瓷总重量的重量百分比,以包括不可避免的杂质在内提供100重量%,其中陶瓷表现出2550kg/m3至2725kg/m3范围内的密度,并且陶瓷表现出在10-6mm/mm/min的应变速率下测量的40mpa至120mpa范围内的失效压缩强度。附图简要描述结合附图参考以下对本文实施方案的描述,本公开内容的上述和其它特征以及获得它们的方式将变得更明显,其中:图1是接收状态的炉渣的图像。图2是来自emiratessteel的接收状态的四种炉渣(0-5mm;5-10mm;10-20mm;>20mm)的图像。图3是通过干粉压实使接收状态的炉渣形成陶瓷的5步法的示意。图4说明研磨后的炉渣粉末的图像。图5a是生坯压实体实例的图像。图5b是陶瓷实例的图像。图6a是在400倍放大倍率下拍摄的接收状态的炉渣的环境扫描电子显微镜(esem)图像。图6b是在400倍放大倍率下拍摄的陶瓷的环境扫描电子显微镜(esem)图像。图7a说明陶瓷几何构造的实例。图7b说明陶瓷几何构造的实例。图7c说明陶瓷几何构造的实例。图7d说明陶瓷几何构造的实例。图7e说明陶瓷几何构造的实例。图7f说明陶瓷几何构造的实例。图8a说明用于压实炉渣粉末的示例性模具的示意分解图。图9是研磨和筛分颗粒的累积粒度(最大线性尺寸)的图。图10是烧结密度相对于压实压力的图。图11是陶瓷(烧结样品)的质量百分比改变相对于温度的图。图12是陶瓷(烧结样品)的比热容相对于温度的图。图13是压缩强度相对于压实压力的图。图14是热能储存系统的示意。本发明详细描述如上所述,本公开内容涉及陶瓷和由回收的工业钢废物并且特别是钢炉渣形成这样的陶瓷的方法。在优选实施方案中,先进陶瓷是使用干粉压实工艺形成的,并且如下所示,可取决于应用来调节密度和压缩强度以及热性质。表现出比石墨和由氧化铝粉末形成的其它压缩固体的更大的压缩强度的陶瓷可用于例如储热系统,因为陶瓷可在最高至1000℃的固体材料中储存热。从炼钢过程中可回收多种类型的钢炉渣。应理解钢炉渣是从炼钢过程中回收的炉渣,与从熔炼和形成铜、铅、镍或其它金属产生的炉渣相反。如上所述,炉渣是矿石的非金属性部分,其在矿石(例如在铁矿石中)的熔炼和精炼中自然上升。也可将炉渣引入至炉中以保护熔融钢免于空气和氧化。以粗集料的形式生产原始电弧炉(eaf)炉渣(也称为黑炉渣)。将eaf炉渣引入炉中,以保护熔融钢浴免于空气和氧化,因为eaf炉渣的密度比钢低,所以eaf炉渣位于混合物的上部。一旦从eaf中提取,将炉渣冷却并固化,然后破碎以便使用磁体回收有价值的铁内容物。图1是在钢生产过程中产生的原始eaf炉渣102的照片。图2说明可获得的四种不同尺寸的eaf炉渣:在照片中从左至右为[0-5mm]202、[5-10mm]204、[10-20mm]204和>20mm208。eaf炉渣包含,并且优选基本上由以下构成:氧化铝(al2o3):2-12重量%,氧化钙(cao):24-60重量%,氧化铁(fe2o3):20-33重量%,氧化镁(mgo):3-15重量%,二氧化硅(sio2):9-20重量%,任选地,以下一种或多种:0.01-8重量%。mno、tio2和游离cao和不可避免的杂质,其中重量%是相对于炉渣组成总重量的重量百分比,以包括不可避免的杂质在内提供100重量%。不可避免的杂质通常是不能避免的,并且通常是工艺环境、原料或工艺设备产生的。不可避免的杂质可占组成的0.01至10.0重量%。24-60重量%存在的cao优选与其它组分反应形成各种cao晶相(这是24-60%cao),其可包括例如以下一种或多种:ca2sio4、4cao·al2o3·fe2o3、ca2al(alsio7)、ca3sio5、2cao·al2o3·sio2、feo、fe3o4、mgo和sio2。未反应的量(游离cao)可表现出与反应的cao不同的晶相(以痕量%包括)。供选择地,或者除了使用eaf炉渣之外,在所述方法中可使用其它炉渣类型。例如,在bof工艺中产生碱性氧气转炉(bof)炉渣,其中将加压氧吹入炉中以氧化进料并去除不需要的元素。与eaf炉渣类似,bof炉渣从炉流出并被水淬火以形成粗集料。来自初级钢制造工艺的熔融钢在钢包炉(lf)中经历还原过程以获得高品质钢。这个工艺的副产物是白色粉末lf炉渣,其对最终钢脱硫、脱气、杂质去除和脱碳起重要作用。高炉(bf)炉渣是炼铁工业的副产物。在熔炼过程中,熔剂中的石灰与铁矿石和焦炭反应形成浮渣层。可以以冷却方法为基础获得从细粉末至粗集料的不同类型的bf炉渣。bf炉渣一般用于水泥工业。优选地,使用图3的流程图中说明的多步骤方法300以形成本文所述eaf炉渣陶瓷,该方法体现:(1)研磨、优选球磨接收状态的炉渣302,以获得具有期望粒度/粒度分布的粉末,然后(2)筛分研磨的粉末以获得均匀混合物304,(3)任选地,使用磁体306去除游离铁内容物,(4)然后在炉中氧化粉末以获得非铁炉渣粉末308,(5)在高压下压缩以获得固体(称为生坯压实体310),和最后(6)在高温下烧结以将所有颗粒结合在一起并获得陶瓷312。如上详述,使表现出5mm或更小粒度(最长线性尺寸)的接收状态的炉渣经受研磨或粉碎处理,优选球磨。优选将颗粒减小至400μm或更小的粉末尺寸,其中该尺寸是粉末的最长线性尺寸。当使用商购球磨机时,优选将颗粒粉碎0.5小时至2小时范围内的时间段,包括其中所有值和范围。球提供研磨介质并且可选自例如2mm至40mm范围内的多种尺寸,包括其中所有值和增量。可领会可使用变化的其它范围。然后筛分经研磨的粉末以获得粒度在20至400μm之间(包括其中所有值和范围)的均匀粉末混合物。均匀混合物可理解为混合物的构成颗粒的形状、尺寸和表面积的均匀分布。在特别优选的实施方案中,将粉末筛分至20μm和200μm范围内的尺寸。另外,颗粒的平均粒度优选在50μm至70μm的范围内,包括其中所有值和范围。然后可处理粉末以去除炉渣粉末中存在的铁。在第一步骤中,优选使用磁体去除游离铁,即未夹带在粉末颗粒内的铁。然后优选通过热处理工艺氧化粉末中保留的铁,所述热处理工艺的等温温度在800℃至1100℃之间(包括其中所有值和范围)和优选1000℃持续1至10小时(包括其中所有值和范围)。在将铁去除或氧化之后,任选地但优选在压实过程之前加入添加剂。添加剂可提高颗粒之间的结合。特别地,将包括聚合物和水的粘合剂与粉末混合,以将粉末保持生坯(即未烧结)状态。粘合剂配制剂的非限制性实例包括聚乙烯醇(pva)和水。除了聚乙烯醇之外或代替聚乙烯醇可使用的聚合物包括聚(碳酸亚烷基酯)、淀粉、羧甲基纤维素、糊精和蜡。可在总粉末配制剂的0.01重量%至10重量%的范围内,并优选在总配制剂的0.01重量%至5重量%的范围内添加聚合物。可根据需要将其它任选的添加剂与粉末混合。这样的额外添加剂包括但不限于润滑剂、表面活性剂、分散剂、絮凝剂和增塑剂。特别地,添加干润滑剂以减小压缩过程中的摩擦。干润滑剂包括但不限于,硬脂酸铝、硬脂酸锌、滑石、石墨等。可在总粉末配制剂的30重量%至50重量%的范围内添加粘土以提高弹性。可使用水不仅作为粘合剂的载体,而且作为其它添加剂的载体。除了水之外,或供选择地,可使用其它载体。其它载体可包括有机液体例如有机溶剂。优选的有机溶剂包括具有20个或更少碳数的短链醇类例如乙醇、丙酮、丁醇、甘油等。载体可在总粉末配制剂的2%至20%范围内存在,包括其中所有值和范围例如2%至10%。可在粉末配制剂(炉渣粉末和添加剂)总重量的0重量%至60重量%范围内的量提供添加剂(包括粘合剂和载体),包括其中所有范围和值,并且炉渣优选以粉末配制剂的40重量%至100重量%范围内的量存在,包括其中所有值和范围。由于炉渣的属性和最终陶瓷产物的所需形状,使用粘合剂可使颗粒之间的粘合容易。然后,优选使用冷或热的干法压实工艺将粉末组合物形成为陶瓷。在冷的干法压实工艺中,通过两个连续步骤制备陶瓷:压实工艺以获得生坯体,随后烧结工艺。在将炉渣粉末与(一种或多种)添加剂(如果存在的话)混合之后,然后压缩粉末。在优选实施方案中,将粉末置于模具中,然后将模具置于压机中。在实施方案中,可加热模具。在以下实施例中进一步讨论模具的实例。在实施方案中,可将炉渣粉末压实成各种形状。粉末的压缩压力部分地取决于粉末的属性而变化。例如,二氧化锆的压实压力在170kpa和400kpa之间。对于其它粉末,压缩压力在100mpa和165mpa之间。然而,对于本文的钢炉渣粉末而言,压力落在30mpa至300mpa的范围内,包括其中所有值和范围,并且优选120至180mpa,和更优选160mpa至180mpa,以获得压实的生坯固体(称作生坯压实体)。图5a是生坯压实体502的实例的图像。在压实之后,在相对高的温度下烧结生坯压实体以改进强度。可在烧结室例如炉或烘箱中进行烧结,并且优选在周围环境下发生烧结;然而,也可考虑在真空中或在低氧环境下进行烧结。优选使用包括预加热阶段和烧结阶段的温度程序。在烧结室中的温度从室温(20-25℃)转变至烧结温度的预加热阶段过程中,使用相对慢的加热速率,加热速率在1k/min至10k/min的范围内,并优选为5k/min,包括其中所有值和范围。预加热阶段的时间优选在0.5至2小时之间,包括其中所有值和范围。当温度从约200℃转变至800℃时,水分蒸发并且添加剂(如果有的话)烧尽。选择烧结温度在材料熔点的50%和90%之间。因此,在本文的钢炉渣的情况下,烧结温度在800℃和1400℃的范围内,并且优选在1000℃至1400℃的范围内选择。烧结时间(或保持时间)在0.5小时至4小时的范围内,包括其中所有值和范围例如1100℃。在烧结过程中,材料经历水释放(如果有的话);粘合剂(如果有的话)燃烧;以及在陶瓷显微组织中形成晶界。虽然该工艺在压制和烧结方面消耗能量,但是干法粉末压实的优点是可实现不是通过铸造以其他方式实现的许多形状。在热的干法压缩工艺中,在一个步骤内制成陶瓷;其中,热处理与压缩同时发生。在混合炉渣粉末和添加剂(如果有的话)之后,将粉末放入压实模具中,并在加热的同时压缩。对于本文的炉渣粉末,压缩压力优选在20-300mpa的范围内,包括其中所有值和范围。烧结温度在700℃和1200℃的范围内,包括其中所有值和范围,保持时间在0.5至4小时之间,包括其中所有值和范围。使用1-10k/min的范围内、优选1k/min的缓慢加热速率将烘箱/炉室的温度升高至烧结温度。将陶瓷保持在模具中,同时维持烧结温度。因此,可理解产生的陶瓷作为钢炉渣粉末的固结块或固结体,其中将炉渣粉末熔合在一起。图5b中显示了在烧结之后陶瓷502'的图像。在冷或热的干法压实工艺中烧结之后,然后将陶瓷冷却至室温。在实施方案中,可控制冷却以影响冷却速率。优选的冷却速率在1k/min至50k/min的范围内,包括其中所有范围和值。在非限制性实施方案中,可通过关闭烘箱或在给定的时间段内递进减小烘箱的温度,将陶瓷冷却至室温。在另外的实施方案中,可通过在烧结之后将陶瓷体浸入水中来冷却陶瓷。各种工艺参数可影响陶瓷所得的性质,这样的参数可包括压缩压力、预加热持续时间、加热速率、烧结温度、保持时间(在烘箱达到烧结温度之后烘箱/炉维持的持续时间)和几何形状。例如,压缩压力对生坯压实体和陶瓷的密度具有所说明的影响。另外,冷却速率影响陶瓷所得的显微组织。考虑到上述情况,上述方法提供在2500kg/m3至2850kg/m3范围内的生坯压实体密度,包括其中所有值和范围,和更优选在2700kg/m3至2850kg/m3的范围内。例如,如果目标是实现高压缩强度,则在制造过程中可选择160mpa的压实压力以减小能量消耗,同时仍实现大约2725kg/m3的生坯密度。烧结密度优选在2550kg/m3至2725kg/m3的范围内,包括其中所有值和范围,并且更优选2700kg/m3至2725kg/m3。除了压缩压力和烧结参数的影响之外,陶瓷性质并且特别是显微组织也受到陶瓷从烧结冷却的影响,并且在下面进一步讨论。现在参考图6a和6b,图6a是接收状态的eaf炉渣的环境扫描电子显微镜图像(esem)且图6b是压实之后陶瓷的esem图像。可以看出,在烧结之后在陶瓷中存在数量增加的具有较大尺寸的晶粒。如上所述,陶瓷的显微组织受烧结之后陶瓷的冷却速率影响。如图6b所示,与通过淬火形成的晶体尺寸相比,相对更低的冷却速率导致形成更大的晶体。更大的晶体提供不同的陶瓷机械性质(例如硬度、韧性)和相对更耐用的最终材料。因此,与相对更高的冷却速率相比,可在1k/min至10k/min范围内的冷却速率(包括其中所有值和范围)下实现更大的晶体。另外,陶瓷优选表现出以10k/min的加热速率在40℃至1100℃的温度范围内小于1%室温(20℃至25℃)下质量的热稳定性(即相对于温度改变的质量改变)。陶瓷还优选表现出100℃下0.66jg-1k-1至1000℃下1.19jg-1k-1范围内的比热容cp。此外,当使用astm标准astmc1424-15测量时,陶瓷表现出在10-6mm/mm/min的应变速率下测量的在40mpa至120mpa范围内(包括其中所有值和范围)的失效压缩强度。陶瓷可形成为多种形状,包括但不限于:球、柱体、拉西(raschig)环、蜂窝结构、波状板、槽砖等,如图7a至7f所示。另外,产生的陶瓷包含:钢炉渣固结体,其中钢炉渣包含并优选基本上由以下构成:在2至12重量%的范围内存在的氧化铝(al2o3),在24至60重量%的范围内存在的氧化钙(cao),在20至33重量%的范围内存在的氧化铁(fe2o3),在3至15重量%的范围内存在的氧化镁(mgo),在9至20重量%的范围内存在的二氧化硅(sio2),任选地,以下一种或多种:在0.01至8重量%的范围内存在的mno、tio2和游离cao,和不可避免的杂质,其中重量%是相对于陶瓷总重量的重量百分比,以包括不可避免的杂质在内提供100重量%。各组分可在上述范围内或以其增量(选择为0.1重量%)存在。从24至60重量%存在的cao优选与其它组分反应形成各种cao晶相(这是24-60%cao),其可包括例如以下一种或多种:ca2sio4、4cao·al2o3·fe2o3、ca2al(alsio7)、ca3sio5、2cao·al2o3·sio2、feo、fe3o4、mgo和sio2。未反应的量(游离cao)可表现出与反应的cao不同的晶相(以痕量%包括)。此外,优选从合金组成排除铁。实验实验例使用由emiratessteel提供的eaf炉渣,即黑色炉渣(见图2)来获得陶瓷。炉渣具有小于5mm的不同尺寸的直径(最大线性尺寸)。使用retschpm100球磨机和直径为2mm(20个球)、5mm(10个球)和15mm(2个球)的32个球将接收状态的炉渣球磨0.75小时。然后筛分粉末以获得粒度小于200μm尺寸的均匀混合物(见图4)。筛分后,使粉末经受1000℃下热处理过程6小时,以氧化炉渣粉末中的铁。然后将热处理的粉末与粘合剂、以粘合剂的4重量%存在的聚乙烯醇(pva)和以粘合剂的96重量%存在的水的混合物混合,其中粘合剂以总粉末配制剂的5重量%存在。然后使用模具和压缩压机,使用冷的干法粉末压实来压实经热处理的粉末。在图8a至8d中说明模具系统。模具800包括由工具钢制成的三个零件:基座802、柱状模子804和冲头806。该系统形成直径为20mm和高度为45mm的模具腔808。使用乙醇和滑石的混合物作为模具腔表面上的干润滑剂以减小模具壁上的摩擦。乙醇以乙醇/滑石配制剂的60重量%的水平存在并且滑石以乙醇/滑石配制剂的40重量%的水平存在。将模具置于单轴压机carverautoch3889中,并且通过使模具经受1000kgf(9kn)至7000kgf(70kn)范围内的力从而提供约30mpa至216mpa的压实压力来形成样品。总共选择五个压实力。图5a中示出了产生的生坯压实体的实例。然后烧结生坯压实体。温度程序来升高温度并烧结生坯压实体,其包括预加热阶段和烧结阶段。在预加热阶段过程中,使用5k/min的加热速率直至温度从室温(20℃至25℃)升高至烧结温度。在预加热过程中,水分蒸发并且粘合剂燃烧。选择1200℃的烧结温度,保持时间为1小时。应理解粉末压实和烧结是为了提高强度。在烧结步骤之后,使陶瓷冷却。如图5b所示,获得没有任何明显裂纹的陶瓷产物。从中间切开样品以检查内部的开裂,并且对于人类观察者没有检测到裂纹。表征炉渣粉末、生坯压实体和陶瓷的许多物理和机械性质,包括粒度、密度、热稳定性、比热容、压缩强度和热膨胀系数。对不同样品重复所有实验3次以验证实验结果的可重复性。从炉渣粉末的表征开始,在研磨之后,根据astm标准(astmb925-15)筛分该粉末以获得直径小于0.2mm的颗粒。为了测定研磨的eaf炉渣粉末的粒度分布,采用激光衍射(ld)法,使用horibala-950v2激光颗粒分析仪。不受任何特定理论的约束,ld的测量涉及给定尺寸的颗粒将散射激光的方式;即光散射的角度受粒度影响。较大的颗粒以较小的角度散射光,而小颗粒将以较宽的角度散射光。然后将由强度和角度限定的检测到的散射光的图案与粒度分布相关联。散射的总光与颗粒的总数成比例。表观密度、压缩性、孔隙率、粗糙度、生坯强度和其它性质可部分地取决于粒度。例如,粉末尺寸(即直径或最大线性尺寸)影响粉末压实。更细的颗粒可更难以压实,因为可需要更大的压力来获得期望的密度。在图9中说明研磨和筛分之后提供的测量的粒度分布,并且在表1中提供实验结果。表1粉末尺寸分布测量值中值尺寸(μm)38.7平均尺寸(μm)58.5标准偏差(μ)56.5模式尺寸(μm)123.7粉末的平均粒度测定为58.5μm和在5μm和200μm的范围之间。为了计算生坯压实体和烧结陶瓷的密度,用数字游标卡尺测量样品的尺寸(在我们的实施例中为直径和高度)并且用天平kernacs220-4称重样品。在烧结之前和之后进行测量。实验结果示于图10中。从实验结果来看,在220mpa的压实压力下获得了烧结产物的最大密度。然而,从160mpa至220mpa的压实压力,似乎密度改变相对小。为了测定陶瓷的热稳定性,使用来自netzsch的同时热分析仪sta449-f3。在测试过程中,相对于样品暴露的温度测量质量的减小或增加。在3.4ml氧化铝坩埚中测量73mg的样品,同时以10k/min的加热速率将仪器室的温度从40℃升高到1100℃。图11提供说明质量随时间改变与温度随时间改变的图。可以看出,热稳定性(即质量增加/损失)小于陶瓷初始重量的1%。为了测定粉末的比热容,使用来自netzsch的差示扫描量热计dsc404。使用比值法测定比热容。通过在相同条件下比较测量样品的热流量(heatflowrate)与标准材料的热流率,能够确定作为温度函数的比热容。在铂坩埚上使用10k/min的加热速率从40℃至1100℃测量样品。图12说明比热容与温度的关系。可以看出,在100℃下比热容是0.66j.g-1.k-1并且在1000℃下热容是1.19j.g-1.k-1。根据astmc1424-15在室温(20℃至25℃)下使用instron5982测试机对烧结陶瓷进行压缩测试,以便测定陶瓷的压缩强度。测试机测量施加至样品的力和位移(或样品在施加载荷的方向上的变形)。通过预先测量样品的尺寸,计算应变和应力。为了在测试中获得准静态条件,所用的应变速率为10-6mm/mm/min。柱状样品具有直径19.7mm和高度12.2mm的平均尺寸。施加压缩力并进行测试,直至样品失效,根据应力-应变曲线,以测定样品在失效前可保持的最大应力。压缩强度结果见图13。数据表明相对较高的压缩压力产生相对较高的密度,其表现出120mpa相对较高的压缩强度并且大于石墨和大多数压缩氧化铝粉末的压缩强度。相对较高的密度有助于颗粒具有限制裂纹发展的较多的相互作用,这使其更坚固。表2中提供在180mpa压力下压实的陶瓷样品的炉渣陶瓷的实验结果的简要总结。表2:eaf炉渣陶瓷的实验值。*在180mpa压力下压实的陶瓷样品上测量。这个工作证明由钢炉渣生产陶瓷的能力,其中可通过改变例如压实压力或冷却速率,将陶瓷设置具有不同的密度和压缩强度以满足广泛的应用。本文所述的陶瓷可用于许多应用中。这样的应用可包括能量储存应用,因为基于以上数据,陶瓷可在最高至1000℃的固体材料中储存热。例如,陶瓷可用作高温热能储存(tes)系统中的固体储存介质。图14中说明系统1400实例的示意,其中该系统包括储存罐1402。陶瓷1404可特别地用作填充床热能储存系统中的填料材料,该系统使用气体(空气、加压空气、超临界co2、烟道气等)作为传热流体1406。入口扩散器1408、储存容器、陶瓷体和出口扩散器1410提供用于传热流体的流动路径,以与陶瓷模块直接接触地循环来装入和排出热能储存系统。当在热能储存中使用时,优选将炉渣粉末压实成为称作tes模块的形状,然后将其烧结。如图7a至7f所示,这些模块可采取上述形式,包括:球、柱体、rashid环、蜂窝结构、波状板、槽砖等。优选地,形状在模块和传热流体之间提供合适的交换表面(即,表面区域)。气体(例如干燥空气或co2)表现出相对低的传热系数;因此,提供相对大的热交换表面可为关键的。因为以随机填充床构造使用在热能储存罐中,例如,作为填料的陶瓷必须抵抗装入和排出温度之间的热循环和热应力。但同时它还必须抵抗填充在其顶部的其它陶瓷填料的物理重量。对于避免系统中陶瓷的劣化并且确保在tes系统的所有预期寿命(例如对于csp设备为25年)过程中不必更换材料而言机械性质则是非常重要的。控制填料布置对于管理传热流体压降和罐中的均匀流动而言也是重要的。通过冷却和成形陶瓷来控制显微组织有助于均匀地组织罐中的填料并减小压降。出于多种目的回收钢炉渣有助于减小来自工业的废物和环境影响。从实验室测试来看,钢炉渣显示在高温下有前景的稳定性和比用于tes的其它材料更高的热容。显示能够制造以eaf钢炉渣粉末为基础的固体。这种新的固体材料由于其可持续属性而具有固有的益处。在粉末的氧化过程、压实和烧结之后,已经显示tes模块是热稳定的,并且具有合适的比热容和压缩强度。其还可在较高温度下使用,从而给出最高至1100℃用作tes储存介质的可能性。在采用热能储存系统的可再生能源当中,集中太阳能(csp)是近年来已被迅速商业开发的有前景的技术。在2014年中,其全世界的总安装容量提高27%至总值为4.4gw。从那时起它已经加倍,接近可操作的约10.1gw。进行了巨大的努力来降低成本并且同时提高csp系统的性能,以使这种技术更有竞争力。csp与例如太阳能光伏或风力相比的主要优点是可调度性(dispatchability),其由热能储存(tes)系统的可能的集成所致。tes赋予功率输送灵活性,以便管理电力需求和供应之间的延迟。此外,如果储存容量足够,tes也可产生基本负载功率。一天24小时或者用于覆盖高峰需求的宝贵可调度电力,tes系统然后在白天中当可大量得到太阳能时充电,以在日落之后再使用,并且在夜间以这种方式继续以产生清洁电力。商购csp设备目前在290℃和565℃之间的温度范围内工作。下一代csp设备意图在从600℃直至1000℃和更大的更高温度下工作,并且通过使用例如组合的brayton-rankine循环来提高能量单元(powerblock)的效率,并且提高从太阳能到电的转化。因此,需要可达到高温的新的tes材料。目标储存介质必须直至1000℃是热稳定的、在高温下是耐腐蚀的、可大量获得的、廉价的、以及表现出大的储存密度。另一预期应用是在高温下需要并产生热并且将热的烟道气消散在大气中的工业应用中的废热回收。可将这种废热回收并储存在陶瓷中,以重新注入工业过程中并节省能量。出于说明的目的,已经给出了若干方法和实施方案的前述描述。其不意图为穷举的或将权利要求限制为所公开的精确步骤和/或形式,并且显然地根据以上教导,许多修改和变化是可能的。意图是本发明的范围由所附权利要求书限定。当前第1页12