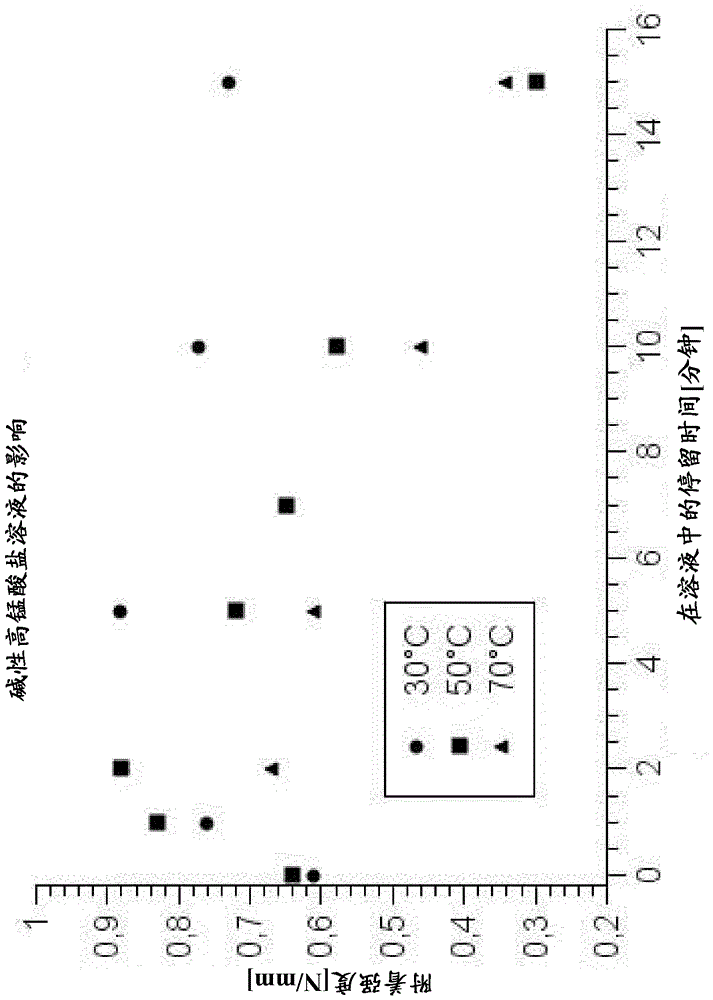
发明领域本发明涉及使用无六价铬的蚀刻溶液将制品的非电导塑料表面金属化的方法。蚀刻溶液基于高锰酸盐溶液。在用蚀刻溶液处理之后,可通过已知的方法将制品金属化。发明背景由非电导塑料制造的制品可通过无电镀金属化方法,或者通过直接电镀方法金属化。在两种方法中,所述制品首先经清洁和蚀刻,然后用贵金属处理并最终金属化。所述蚀刻通常通过铬硫酸进行。蚀刻用于使制品的表面易于接受后续的金属化,使得制品的表面被顺序处理步骤中相应的溶液良好地润湿,并且沉积金属最终在表面上具有足够牢固的附着。对于蚀刻,制品的表面,例如由丙烯腈-丁二烯-苯乙烯共聚物(abs共聚物)制造,使用铬硫酸蚀刻,以便形成微穴,金属沉积在其中并随后牢固地附着在那里。在蚀刻之后,将塑料通过包含贵金属的活化剂活化,用于无电镀金属化,然后经无电镀金属化。随后,还可以电解涂敷更厚的金属层。在直接电镀方法的情况下,其不需要无电镀金属化,经蚀刻的表面通常用钯胶体溶液处理。随后,将表面与包含与络合剂络合的铜离子的碱性溶液接触以增加电导率。该步骤导致铜层的形成,及因此导致在制品的表面上具有提高的电导率的金属层。此后,制品可直接经电金属化(ep1054081b1)。然而,基于铬硫酸的蚀刻溶液是有毒的且因此应尽可能被替代。文献描述了用包含高锰酸盐的那些溶液替换基于铬硫酸的蚀刻溶液的尝试。在碱性介质中使用高锰酸盐用于作为电子电路载体的电路板的金属化早已确定。因为在氧化中出现的六价态(锰酸盐)为水溶性的且在碱性条件下具有充足的稳定性,所以所述锰酸盐类似于三价铬,可电解氧化回初始氧化剂(在该情况下为高锰酸盐)。文献de19611137a1描述了高锰酸盐也用于作为电路板材料的其它塑料的金属化。对于abs塑料的金属化,碱性高锰酸盐的溶液已经被认为是不适合的,因为不能以这种方法在金属层和塑料基底之间获得可靠的、充足的附着强度。该附着强度在“剥离试验”中测定。其至少应为0.4n/mm的值。ep11001052公开了酸式高锰酸盐溶液,其据说适用于塑料电镀。在其中描述的溶液在几个方面不同于本发明,例如因为它们使用很高的酸浓度和很低的高锰酸盐浓度(例如15mh2so4和0.05mkmno4)。ep1001052未报导通过该处理可获得附着强度。室内实验已经表明附着强度在0.4n/mm的值以下。此外,在ep1001052中描述的溶液不稳定。因此,不能获得金属化的恒定品质。作为铬硫酸的替代物,wo2009/023628a2提出包含碱金属高锰酸盐的强酸性溶液。所述溶液在40-85重量%磷酸中包含约20g/l的碱金属高锰酸盐。这些溶液形成难以去除的胶态锰(iv)物类。根据wo2009/023628a2,甚至在短时间之后,所述胶体的效果是适当品质的涂覆已不再可能。为了解决所述问题,wo2009/023628a2提出使用锰(vii)源,其不包含任何碱金属或碱土金属离子。然而,这些锰(vii)源的制备为昂贵的和不方便的。因此,有毒的铬硫酸仍然用于塑料的蚀刻处理。在塑料基底的常规电镀中,其中第一金属层首先在无外电流下沉积,有时在塑料表面上小于1mg/m²的钯足以在无外电流下开始金属沉积。在不需要无电镀金属化的直接电镀中,在塑料表面上需要至少30mg/m²-50mg/m²的钯以允许电解金属化。40mg/m²的钯通常足以直接电镀。至今,仅当塑料表面在金属化之前已经用毒性铬硫酸蚀刻时,可获得在塑料表面上钯的这些最低量。附图说明图1:用不同的蚀刻处理处理塑料表面对塑料表面的钯覆盖度的影响。图2:用二醇化合物溶液对塑料表面的处理时间对于随后涂敷的金属层的附着强度、沉积的二氧化锰的量和结合的钯的量的影响。图3a:碱性蚀刻步骤的温度对附着强度的影响,如果其在本发明的金属化方法的酸性蚀刻步骤之后执行。图3b:碱性蚀刻步骤的处理时间对附着强度和结合的钯的量的影响,如果其在本发明的金属化方法的酸性蚀刻步骤之后执行。发明描述因此,本发明基于以下问题:至今尚不能以环境安全的方式获得由非电导塑料制造的制品的金属化,其具有足够的过程可靠性且随后涂敷的金属层有足够的附着强度。此外,如果所述塑料在金属化之前没有用铬硫酸蚀刻,至今尚不能通过直接电镀获得由非电导塑料制造的制品的强附着、大面积金属化。因此本发明的目标为发现用于制品的非电导塑料的蚀刻溶液,这些为非毒性但是为涂敷在塑料表面的金属层提供足够附着强度。本发明的另一目标为发现用于制品的非电导塑料表面的蚀刻溶液,其为非毒性的且其允许非电导塑料表面直接电镀。这些目标通过本发明的以下方法实现:将制品的非电导塑料表面金属化的方法,其包含以下工艺步骤:a)用蚀刻溶液处理所述塑料表面;b)用胶体溶液或金属化合物的溶液处理所述塑料表面;和c)用金属化溶液将所述塑料表面金属化;其特征在于所述蚀刻溶液包含至少一种酸性蚀刻溶液及至少一种碱性蚀刻溶液,且每种蚀刻溶液包含高锰酸盐离子源。在本发明的背景中,制品应理解为是指已经由至少一种非电导塑料制造或已经用至少一种非电导塑料的至少一层覆盖的制品。因此所述制品具有至少一个非电导塑料表面。在本发明的背景中塑料表面应理解为是指制品的这些所述表面。本发明的工艺步骤按特定的顺序实施,但不是必紧密连续。在所有情况下,有可能在所述步骤之间实施其它工艺步骤和另外的漂洗步骤,优选用水。用包含至少一种酸性蚀刻溶液和至少一种碱性蚀刻溶液的蚀刻溶液对塑料表面的发明性蚀刻(工艺步骤a)),比已知的处理(例如使用铬硫酸或单独用已知的酸性或碱性高锰酸盐溶液)获得涂敷在塑料表面的金属层的高得多的附着强度。此外,用包含至少一种酸性蚀刻溶液和至少一种碱性蚀刻溶液的蚀刻溶液对塑料表面的发明性蚀刻(工艺步骤a)),在用胶体溶液或金属化合物的溶液活化塑料表面期间,导致金属在塑料表面高得多的覆盖度。因此,不仅随后可以将塑料表面无无外电流地金属化,而且可以直接电镀塑料表面,这是指不在无外电流下将塑料表面金属化,而通过电解法直接金属化。这些作用未在已知的蚀刻处理中观察到,例如使用铬硫酸,或单独用已知的酸性或碱性高锰酸盐溶液。塑料表面已经由至少一种非电导塑料制造。在本发明的一个实施方案中,至少一种非电导塑料选自包含以下的组:丙烯腈-丁二烯-苯乙烯共聚物(abs共聚物)、聚酰胺(pa)、聚碳酸酯(pc),以及abs共聚物与至少一种其它聚合物的混合物。在本发明的优选实施方案中,非电导塑料为abs共聚物或abs共聚物与至少一种其它聚合物的混合物。至少一种其它聚合物更优选为聚碳酸酯(pc)、这是指特别优选abs/pc混合物。在本发明的一个实施方案中,可在工艺步骤a)前实施以下另外的工艺步骤:用包含碘酸盐离子源的溶液处理支架。用包含碘酸盐离子源的溶液处理支架还在下文中称作支架的保护。支架的保护可在本发明的方法期间的不同时间进行。在工艺步骤a)之前的时间,制品还没有固定在支架上。因此用包含碘酸盐离子源的溶液单独处理支架,不带有制品。在本发明的另一实施方案中,可在工艺步骤a)前实施以下另外的工艺步骤:将制品固定在支架上。该另外的工艺步骤在下文中称作固定步骤。制品固定到支架允许用单独工艺步骤的连续溶液同时处理大量制品,及在用于电解沉积一个或多个金属层的最后步骤期间建立电接触连接。通过本发明的方法处理制品优选在常规的浸渍过程中实施,通过将制品连续浸渍在容器内的溶液中,在其中进行相应的处理。在这种情况下,制品可固定在支架上或引入鼓内浸入溶液中。备选地,制品还可在所谓传送系统上处理,通过例如平放在托盘上并在水平方向上连续传送通过系统。优选固定在支架上。支架通常自身涂布有塑料。塑料通常为聚氯乙烯(pvc)。在本发明的另一个实施方案中,支架保护可在固定步骤之前实施。在本发明的另一个实施方案中,在工艺步骤a)前实施以下另外的工艺步骤:在包含至少一种二醇化合物的水溶液中处理塑料表面。该另外的工艺步骤在下文中称作预处理步骤。该预处理步骤提高了塑料和金属层之间的附着强度。如果另外在工艺步骤a)前实施固定步骤,预处理步骤在固定步骤和工艺步骤a)之间实施。二醇化合物应理解为是指以下通式(i)的化合物:(i)其中n为1-4的整数;和r1和r2各自独立地为-h、-ch3、-ch2-ch3、-ch2-ch2-ch3、-ch(ch3)-ch3、-ch2-ch2-ch2-ch3、-ch(ch3)-ch2-ch3、-ch2-ch(ch3)-ch3、-ch2-ch2-ch2-ch2-ch3、-ch(ch3)-ch2-ch2-ch3、-ch2-ch(ch3)-ch2-ch3、-ch2-ch2-ch(ch3)-ch3、-ch(ch2-ch3)-ch2-ch3、-ch2-ch(ch2-ch3)-ch3、-co-ch3、-co-ch2-ch3、-co-ch2-ch2-ch3、-co-ch(ch3)-ch3、-co-ch(ch3)-ch2-ch3、-co-ch2-ch(ch3)-ch3、-co-ch2-ch2-ch2-ch3。根据通式(i),二醇化合物包括二醇自身和二醇衍生物。二醇衍生物包括二醇醚、二醇酯和二醇醚酯。二醇化合物为溶剂。优选的二醇化合物为乙二醇、二甘醇、乙二醇单甲醚乙酸酯、乙二醇单乙醚乙酸酯、乙二醇单丙醚乙酸酯、乙二醇乙酸酯、二甘醇单乙醚乙酸酯、二甘醇单甲醚乙酸酯、二甘醇单丙醚乙酸酯、丁基乙二醇、乙二醇单丁醚、乙二醇二乙酸酯和它们的混合物。特别优选二甘醇单乙醚乙酸酯、乙二醇乙酸酯、乙二醇二乙酸酯、丁基乙二醇和它们的混合物。在使用乙二醇酯和乙二醇醚酯的情况下,最好通过适合的措施保持二醇化合物水溶液的ph在中性范围之内,以便尽可能抑制水解以产生醇和羧酸。一个实例是二甘醇单乙醚乙酸酯的水解:ch3-co-o-ch2ch2-o-ch2ch2-o-ch2ch3+h2o→ch3-cooh+ho-ch2ch2-o-ch2ch2-o-ch2ch3包含二醇化合物的溶液的水浓度同样地对二醇酯和二醇醚酯有影响。然而,由于两个原因溶液必须包含水:首先为了获得不可燃的处理溶液,其次为了能调节对塑料表面的攻击。纯溶剂,即100%二醇化合物,将溶解大多数的未交联聚合物或至少留下不可接受的表面。因此已发现缓冲二醇酯或二醇醚酯的溶液是非常有利的,从而保持其在中性ph范围内,这意味着清除通过溶剂水解获得的质子。已经发现磷酸盐缓冲液混合物足以适用于该目的。易溶的磷酸钾允许足够高的浓度,在溶剂浓度达40体积%时具有良好的缓冲能力。对塑料表面的最佳处理时间取决于使用的塑料、温度和二醇化合物的特性和浓度。处理参数对经处理的塑料表面和在随后工艺步骤中涂敷的金属层之间的附着有影响。二醇化合物的更高的温度或浓度也影响塑料表面的质地。在任何情况下,对于随后的蚀刻步骤a),应能从塑料基质中再次去除溶剂,因为所述方法中的后续步骤(更特别是在工艺步骤b)中的活化)否则会受干扰。该预处理步骤中的处理时间为1-30分钟,优选5-20分钟,和更优选7-15分钟。在实施例8中,对于abs/pc混合物,检验用二醇溶液对塑料表面的处理时间(停留时间)对于随后涂敷的金属层的附着强度的影响。结果显示在图2的图中。图2中的术语“归一化值”表示:对于附着强度,标绘初始测量结果。对于锰值,标绘已经归一化为最高锰测量结果的值。对于钯值,标绘已经相应地归一化为最高的钯测量结果的值。所有初始测量结果概括在表10.2中。未用二醇化合物处理(图2中停留时间0分钟),不能通过直接电镀将任何金属沉积在塑料表面上。在用二醇化合物处理仅4分钟后,相反地,已经获得0.8n/mm的良好附着强度,且这随着更长的处理时间提升直到达到最优值。处理温度为20℃-70℃,取决于使用的溶剂或溶剂混合物的特性。优选20℃-50℃的处理温度,特别优选为20℃-45℃的处理温度。在预处理步骤中的塑料表面的处理可在包含一种二醇化合物的水溶液或包含两种或更多种不同二醇化合物的水溶液中实施。二醇化合物在水溶液中的总浓度为5体积%-50体积%,优选10体积%-40体积%和更优选20体积%-40体积%。如果所述溶液包含一种二醇化合物,则总浓度对应于这一种二醇化合物的浓度。如果所述溶液包含两种或更多种不同二醇化合物,则总浓度对应于存在的所有二醇化合物的浓度总和。在包含至少一种二醇化合物的溶液的情况下,二醇化合物/二醇化合物的%浓度数值总是理解为指体积浓度%。例如,对于abs塑料表面的预处理,15体积%的二甘醇单乙醚乙酸酯与10体积%的丁基乙二醇的混合物的溶液在45℃下被认为是有利的。在其中的第一溶剂用于产生附着强度,而第二溶剂(作为非离子型表面活性剂)提高润湿性并帮助从塑料表面去除存在的任何污物。对于abs/pc混合物的处理,认为例如bayblendt45或bayblendt65pg,二甘醇单乙醚乙酸酯的40体积%的水溶液在室温下是更有利地,因为其允许在这些塑料的情况下涂敷的金属层的更高附着强度(见实施例8)。在本发明的另一个实施方案中,支架保护可在固定步骤和预处理步骤之间实施。在本发明的另一个实施方案中,支架保护可在预处理步骤和工艺步骤a)之间实施。在这些时候,制品已经固定在支架上。因此支架连同制品一起用包含碘酸盐离子源的溶液处理。不论支架的保护单独地或连同制品一起进行,其导致对支架的塑料罩壳的保护,避免金属沉积,而固定在支架上的制品在固定步骤期间则被金属化。支架的保护保证了支架的塑料罩壳在随后的工艺步骤b)至c)中不被金属化,意味着支架保持无金属。该作用在支架的pvc罩壳上特别显著。在工艺步骤a)中的发明性蚀刻处理用包含至少一种酸性蚀刻溶液和至少一种碱性蚀刻溶液的蚀刻溶液实施。酸性蚀刻溶液包含:1.高锰酸盐离子源和2.酸。碱性蚀刻溶液包含:1.高锰酸盐离子源和2.氢氧根离子源。酸性和碱性蚀刻溶液因此包含高锰酸盐离子源。高锰酸盐离子源选自碱金属高锰酸盐。碱金属高锰酸盐选自包含高锰酸钾和高锰酸钠的组。高锰酸盐离子源独立选择用于酸性和碱性蚀刻溶液,意味着两种蚀刻溶液可包含相同的高锰酸盐离子源或两种蚀刻溶液可包含不同的高锰酸盐离子源。存在于酸性和碱性蚀刻溶液中的高锰酸盐离子源的浓度为30g/l-250g/l,优选30g/l-180g/l,还优选90g/l-180g/l,更优选90g/l-110g/l,甚至更优选70g/l-100g/l。由于它的溶解度,高锰酸钾可以最多70g/l的浓度存在于蚀刻溶液中。高锰酸钠可以最多250g/l的浓度存在于蚀刻溶液中。这两种盐各自的浓度下限通常为30g/l。在酸性蚀刻溶液中,高锰酸盐离子源的含量优选90g/l-180g/l。在碱性蚀刻溶液中,高锰酸盐离子源的含量优选30g/l-100g/l。用于酸性和碱性蚀刻溶液的高锰酸盐离子源的浓度独立选择,意味着两种蚀刻溶液可包含相同浓度的高锰酸盐离子源或两种蚀刻溶液可包含不同浓度的高锰酸盐离子源。用于酸性蚀刻溶液的酸优选无机酸。在工艺步骤a)中的酸性蚀刻溶液中的无机酸选自包含硫酸、硝酸和磷酸的组。酸浓度必须不过高,因为酸性蚀刻溶液否则不稳定。酸浓度为0.02-0.6摩尔/l,基于一元酸。优选0.06-0.45摩尔/l,更优选0.07-0.30摩尔/l,在所有情况下基于一元酸。优选使用0.035-0.15摩尔/l浓度的硫酸,对应于基于一元酸的0.07-0.30摩尔/l的酸浓度。在另一个实施方案中,蚀刻溶液仅包含如上所述的高锰酸盐离子源和如上所述的酸。在这个实施方案中,蚀刻溶液不包含任何其它成分。酸性蚀刻溶液可在30℃-90℃的温度下使用,优选55℃-75℃。已经发现在金属层和塑料表面之间的足够高的附着强度还可以在30℃-55℃的低温下获得。然而,在那种情况下,不能保证在预处理步骤中来自用二醇化合物处理的全部溶剂从塑料表面去除。这对纯abs特别成立。因此,如果在本发明的方法中执行预处理步骤,在随后的工艺步骤a)中选择的温度应选择为更高水平,即55℃-90℃,优选55℃-75℃。用酸性蚀刻溶液的最佳处理时间取决于要处理的塑料表面和蚀刻溶液的选定温度。对于abs和abs/pc塑料表面,塑料表面和随后涂敷的金属层之间的最佳附着强度及用活化剂金属对塑料表面的最佳覆盖度在5-30分钟的处理时间下获得,优选10-25分钟和更优选10-15分钟。比30分钟更长的处理时间通常导致附着强度或金属覆盖度没有进一步的提高。酸性高锰酸盐溶液在升高的温度下,例如在70℃,非常有反应性。塑料表面的氧化反应然后形成许多会沉淀析出的锰(iv)物类。这些锰(iv)物类主要为锰(iv)氧化物或氧化物水合物,且在下文中简单称作二氧化锰。二氧化锰沉淀,如果其保留在塑料表面上,对后续的金属化具有干扰作用。在工艺步骤b)的活化期间,其保证塑料表面的区域不被金属胶体覆盖或引起在随后工艺步骤中要涂敷的金属层的不可接受的粗糙度。二氧化锰还催化高锰酸盐与水的反应且可因此导致蚀刻溶液的不稳定性。蚀刻溶液因此应有利地保持无二氧化锰。意外地,已发现当在酸性蚀刻溶液中所选的酸浓度低且所选的高锰酸盐浓度高时,难以去除的二氧化锰物类的形成显著地减少。在工艺步骤a)中的碱性蚀刻溶液中的氢氧根离子源选自碱金属氢氧化物,其包含氢氧化钠、氢氧化钾和氢氧化锂。氢氧根离子源优选氢氧化钠。在碱性蚀刻溶液中的氢氧根离子源独立于高锰酸盐离子源而选择,意味着碱性蚀刻溶液可包含氢氧根离子源和具有相同碱金属离子的高锰酸盐离子源,或碱性蚀刻溶液可包含氢氧根离子源和具有不同的碱金属离子的高锰酸盐离子源。氢氧根离子源的浓度为1g/l-100g/l,优选5g/l-50g/l,和更优选10g/l-30g/l。碱性蚀刻溶液可在20℃-90℃的温度下使用,优选30℃-75℃,和更优选30℃-60℃。碱性蚀刻溶液的温度对活化剂的金属在塑料表面的覆盖度实际上并无影响。相反地,在30℃-60℃的温度范围内用碱性蚀刻溶液对塑料表面的处理导致更高的附着强度。碱性高锰酸盐溶液的稳定性在升高的温度下稍微下降。然而,通常,碱性高锰酸盐溶液比酸性高锰酸盐溶液稳定得多。碱性高锰酸盐溶液的稳定性在40℃-60℃范围内并无区别。用碱性蚀刻溶液的最佳处理时间同样地取决于被处理的塑料表面和蚀刻溶液的选定温度。对于abs和abs/pc塑料表面,塑料表面和随后涂敷的金属层之间的最佳附着强度和来自活化剂的金属对塑料表面的最佳覆盖度在用碱性蚀刻溶液处理时间为1-20分钟时获得,优选1-15分钟,和更优选1-5分钟。比20分钟更长的处理时间通常不会导致用来自活化剂的金属对塑料表面的覆盖度或附着强度的任何进一步提高。在实施例9中,在碱性高锰酸盐溶液中温度和处理时间(停留时间)对塑料和通过电镀(通过直接电镀)涂敷的金属之间的附着强度及在活化步骤期间结合的钯的量的影响,已经通过例如由abs/pc混合物形成的塑料表面检验。在不同温度下在碱性高锰酸盐溶液蚀刻步骤后获得的附着强度显示在图3a中。据此,通过电镀涂敷的金属层对abs/pc混合物的最佳附着强度在碱性高锰酸盐溶液中2-5分钟停留时间后获得。考虑碱性高锰酸盐溶液的温度,在30℃-50℃获得最佳附着强度。对于由abs/pc混合物形成的塑料表面,发现用碱性高锰酸盐溶液在约50℃下用1-5分钟的处理时间处理是特别有利的。图3b显示了在实施例9中在用碱性高锰酸盐溶液在50℃下处理之后获得的附着强度和结合至表面的钯的量。为了更好清楚,发现的钯的量除以50的系数用于图示。由在碱性高锰酸盐溶液中约1分钟的停留时间,已经达到结合的钯的最大量;在碱性高锰酸盐溶液中更长的停留时间不会导致结合在塑料表面上的钯的量的任何显著变化。对于结合至由abs/pc混合物形成的塑料表面的钯的量,用碱性高锰酸盐溶液在约50℃下处理1-5分钟因此也非常适合。在工艺步骤a)中,蚀刻溶液可按不同的顺序使用。在本发明特别优选的实施方案中,在工艺步骤a)中首先使用酸性蚀刻溶液然后用碱性蚀刻溶液,使得工艺步骤a)包含以下步骤:ai)用酸性蚀刻溶液处理所述塑料表面,和aii)用碱性蚀刻溶液处理所述塑料表面。在本发明的另一优选实施方案中,在工艺步骤a)中,首先使用碱性蚀刻溶液然后使用酸性蚀刻溶液,使得工艺步骤a)包含以下步骤:ai)用碱性蚀刻溶液处理所述塑料表面,和aii)用酸性蚀刻溶液处理塑料表面。实施例1和2描述了两个实施方案的效果。在实施例1中,塑料面板首先用酸性蚀刻溶液(酸性高锰酸盐溶液)然后用碱性蚀刻溶液(碱性高锰酸盐溶液)处理,然后用钯胶体活化并通过直接电镀提供铜层。将塑料面板通过直接电镀用铜层完全且均匀地覆盖。在实施例2中,用酸性和碱性蚀刻溶液按上述两种顺序处理塑料面板。随后,用钯胶体、非电镀镀镍和电解镀铜活化面板。已经用酸性和碱性蚀刻溶液以上述两种顺序蚀刻的塑料面板提供有铜层。已经首先用碱性和随后用酸性蚀刻溶液蚀刻的面板同样地覆盖有铜层,但它不完全完整。在塑料面板上得到的金属层的附着强度根据标准astmb5331985(2009年再通过),通过实施例2描述的剥离试验测定。沉积金属层中获得的附着强度比用单一酸性蚀刻溶液或单一碱性蚀刻溶液或现有技术的铬硫酸溶液(见对比实施例3)处理后可获得的那些高得多。首先用酸性随后用碱性蚀刻溶液蚀刻的塑料面板显示了比首先用碱性随后用酸性蚀刻溶液蚀刻的塑料面板更高的附着强度。备选地,在工艺步骤a)中,可实施超过两步的用蚀刻溶液处理塑料表面。例如,在工艺步骤a)中的前两步可各自包含用酸性蚀刻溶液处理塑料表面,而第三步包含用碱性蚀刻溶液处理塑料表面。或者,在工艺步骤a)中的前两步各自包含用碱性蚀刻溶液处理塑料表面,而第三步包含用酸性蚀刻溶液处理塑料表面。或工艺步骤a)包含三步的用蚀刻溶液处理塑料表面,在所有情况下交替使用酸性与碱性蚀刻溶液。工艺步骤a)还可包含超过三步的用蚀刻溶液处理塑料表面。不论在工艺步骤a)中实施的步骤数与它们的顺序,重要的是工艺步骤a)总是包含至少一个步骤用酸性蚀刻溶液处理塑料表面和至少一个步骤用碱性蚀刻溶液处理塑料表面。特别优选实施方案中,其中在工艺步骤a)中,在所有情况下第一步由用酸性蚀刻溶液处理塑料表面组成,且在所有情况下最后一步由用碱性蚀刻溶液处理塑料表面组成。定期(通常每日)分析蚀刻溶液的成分对优化过程可靠性是有利的。这包括酸或碱的滴定,以获得初始酸浓度或氢氧根离子浓度,以及高锰酸盐浓度的光度测定。后者可用简单的光度计实现。来自绿光发射二极管的光(波长λ=520nm)相当精确地对应于高锰酸盐的吸收最大值。然后必须根据分析数据加入消耗量。实验已表明,在工艺步骤a)中在推荐的工作温度下在10分钟的反应时间内用酸性蚀刻溶液处理塑料表面的步骤中,约0.7g/m²-1.2g/m²的二氧化锰在abs塑料表面上形成。与从高锰酸盐溶液中由制品带出的损失相比,在表面反应中的该消耗量是可忽略的。发明性蚀刻溶液不包含任何铬或铬化合物;蚀刻溶液既不包含铬(iii)离子也不包含铬(vi)离子。因此发明性蚀刻溶液无铬或铬化合物;蚀刻溶液无铬(iii)离子和铬(vi)离子。用包含至少一种酸性蚀刻溶液和至少一种碱性蚀刻溶液的蚀刻溶液对塑料表面的发明性蚀刻(工艺步骤a))比已知的处理(例如使用铬硫酸,或单独用已知的酸性或碱性高锰酸盐溶液)获得涂敷在塑料表面的金属层的高得多的附着强度。用酸性蚀刻溶液处理塑料表面,使用酸浓度低且高锰酸盐浓度高的蚀刻溶液。由此,可调节二氧化锰物类的形成,使得蚀刻溶液的稳定性得到保证,且仍然获得对更高的附着强度的显著贡献。用碱性高锰酸盐溶液对塑料表面的单独或唯一的处理,如作为蚀刻溶液在电路板工业中通常所用,不适合于本发明目标,因为其不会得到塑料表面和金属层之间的足够的附着强度。本发明的工艺步骤a)包含用包含至少一种酸性蚀刻溶液和至少一种碱性蚀刻溶液的蚀刻溶液处理塑料表面,且因此构成用不同的蚀刻溶液处理塑料表面的步骤组合。用至少一种酸性蚀刻溶液和至少一种碱性蚀刻溶液对塑料表面处理的发明性步骤组合比已知的处理(例如使用铬硫酸,或单独用已知的酸性或碱性高锰酸盐溶液)获得涂敷在塑料表面的金属层的高得多的附着强度。如已经在实施例2中所描述,已经测定在塑料表面上的金属层的附着强度,这些已经通过本发明的金属化方法的两个优选实施方案产生。在实施例3中,abs/pc塑料面板以不同的方法蚀刻:一组塑料面板用本发明的酸性蚀刻溶液,一组用本发明的碱性蚀刻溶液,且一组用铬硫酸酸(由现有技术已知)。随后,所有面板用钯胶体活化,然后无电镀镀镍,然后电解镀铜,且如实施例2所描写,测定金属层在塑料面板上的附着强度。实施例2和3中对于无外电流金属化的塑料面板所获得的附着强度值概括在表1。对于已经首先用酸性蚀刻溶液然后用碱性蚀刻溶液(蚀刻处理i,表1中)蚀刻过的塑料面板,获得得最佳的附着强度。按反顺序(首先碱性蚀刻溶液,然后酸性蚀刻溶液,蚀刻处理ii,表1中)蚀刻面板之后,获得的附着强度低于在单独酸性蚀刻步骤(酸性蚀刻溶液,蚀刻处理iii,表1)之后获得的那些。然而,在蚀刻处理ii之后的附着强度远超过用单独碱性蚀刻步骤(蚀刻处理iv,表1)或用铬硫酸(蚀刻处理v,表1)蚀刻之后的那些。蚀刻处理i、iii和iv的对比显示在发明性蚀刻处理i中的第一酸性蚀刻步骤已经贡献了附着强度的大部分。然而,随后执行的碱性蚀刻步骤,导致附着强度的显著的额外提高。该效果是出乎意料的,因为单独执行的碱性蚀刻步骤(蚀刻处理iv)未导致任何显著的附着强度(见表1)。虽然用蚀刻处理ii(首先碱性蚀刻溶液,然后酸性蚀刻溶液)蚀刻之后比用发明性蚀刻处理i(首先酸性,然后碱性)蚀刻之后获得较低的附着强度,但发明性蚀刻处理ii未达到比已知的蚀刻处理iv(仅碱性蚀刻溶液)或已知的蚀刻处理v(铬硫酸)好得多的附着强度,这同样出乎意料。表1:在不同的蚀刻处理之后,无外电流下,在塑料表面上涂敷的金属层的附着强度。*金属层和塑料表面之间有气泡。在实施例5中,由abs/pc混合物制造的塑料面板用蚀刻处理i.、iii.、iv.和v.处理,用钯胶体活化,然后通过直接电镀提供铜层,然后如实施例2描述测定涂敷的铜层的附着强度。实施例5中对于通过直接电镀金属化的塑料面板获得的附着强度值概括在表8.2中。对于所有蚀刻处理,在实施例5中直接电镀之后获得的附着强度低于实施例2和3中通过无外电流金属化涂敷的金属层的附着强度。已知效果为直接金属化之后在塑料表面上金属层的附着强度通常低于无外电流的金属化。该效果也在这里观察到。实施例5中的附着强度,在定性的方面,显示了与实施例2和3中相同的性能。对于已经用发明性蚀刻处理i.(首先酸性蚀刻溶液,然后碱性蚀刻溶液)(表8.2)蚀刻的塑料面板,获得最佳的附着强度。对比蚀刻处理i.、iii.和iv.,甚至在直接电镀的情况下,显示首先的酸性蚀刻步骤和后续的碱性蚀刻步骤的相互作用,其已经在发明性蚀刻处理i.中对实施例2和3概述,这导致涂敷的金属层的特别良好的附着强度。酸性蚀刻步骤与碱性蚀刻步骤的组合(发明性蚀刻处理i.)导致比单独执行的酸性蚀刻处理iii.更高的附着强度。酸性蚀刻步骤与碱性蚀刻步骤的组合(发明性蚀刻处理i.)还导致比用已知的蚀刻处理iv.(仅碱性蚀刻溶液)或已知的蚀刻处理v.(铬硫酸)好得多的附着强度。当借助无外电流金属化将金属层涂敷在塑料表面上时,本发明的方法产生至少0.8n/mm的附着强度。如果通过直接电镀将金属层涂敷在塑料表面上,本发明的方法产生至少0.6n/mm的附着强度。因此,通过本发明的方法获得的附着强度远超过所需的0.4n/mm的最小值。此外,用包含至少一种酸性蚀刻溶液和至少一种碱性蚀刻溶液的蚀刻溶液对塑料表面的发明性蚀刻(工艺步骤a)),在用胶体溶液或金属化合物的溶液活化塑料表面期间,导致金属在塑料表面高得多的覆盖度。当用金属胶体实施活化时,该效果特别显著。因此,首先,不仅可随后将塑料表面无外电流金属化,而且可直接电镀塑料表面,这是指塑料表面不经无外电流金属化,而是通过电解法直接金属化。其次,这使得可降低在金属胶体或金属化合物溶液中的金属浓度。不管在胶体溶液或金属化合物的溶液中的低金属浓度,随后可将塑料表面无外电流金属化或直接电镀塑料表面。这些效果在已知的蚀刻处理的情况中未观察到,例如使用铬硫酸,或单独用已知的酸性或碱性高锰酸盐溶液。在实施例4中,由abs和abs/pc混合物制造的塑料面板通过蚀刻处理i.(首先酸性蚀刻溶液,然后碱性蚀刻溶液)、iii.(仅酸性蚀刻溶液)和v.(铬硫酸)蚀刻,且用具有不同钯浓度的胶态活化剂溶液活化。在活化之后,结合在面板表面上的钯溶于限定体积的王水中,且通过具有电感耦合等离子体的光学发射谱仪(icp-oes)测定在其中的钯浓度。icp-oes的测量原理包括将存在于溶液中的样品雾化且通过电感耦合等离子体将存在的离子诱导发光。发射的光被分成它的波长且随后通过光谱仪测量它们的强度。存在的离子可在它们的发射谱线的基础上确定且量化。icp-oes为本领域技术人员已知,用于测定溶液中的金属离子。icp-oes测量的实施在实施例4中描述。对于不同的塑料面板和不同的蚀刻处理,表面结合的钯的值在表7中概括,且以图的形式显示在图1中。在图1中,以下术语具有以下含义:abs:abs共聚物bb:bayblendt45,abs/pc混合物高锰酸盐,1个步骤:用酸性高锰酸盐溶液处理,对应于蚀刻处理iii.高锰酸盐,2个步骤:首先用酸性高锰酸盐溶液,然后用碱性高锰酸盐溶液处理,对应于蚀刻处理i.。对于活化剂中的所有钯浓度,已经用酸性蚀刻溶液初步处理和随后用碱性蚀刻溶液处理(发明性蚀刻处理i.,见表7和图1)的组合蚀刻的由abs/pc混合物制造的塑料面板与已经通过单独酸性蚀刻步骤(蚀刻处理iii.,酸性蚀刻溶液)或铬硫酸(蚀刻处理v.)蚀刻的abs/pc面板相比,获得高得多的塑料表面的钯载量。在活化剂中100ppm-200ppm的钯浓度下,已经用酸性蚀刻溶液初步处理和随后用碱性蚀刻溶液处理(发明性蚀刻处理i.,见表7和图1)的组合蚀刻的由abs制造的塑料面板与已经通过单一酸性蚀刻步骤(蚀刻处理iii.,酸性蚀刻溶液)或铬硫酸(蚀刻处理v.)蚀刻的abs面板相比,获得高得多的塑料表面的钯载量。用酸性和碱性蚀刻溶液组合蚀刻,因此意外地导致以下效果:来自活化剂的多很多的钯沉积在塑料表面上。因此,用酸性和碱性蚀刻溶液的组合蚀刻允许塑料表面首先活化,后续无外电流金属化。其次,通过用酸性和碱性蚀刻溶液组合蚀刻,也可直接后续电解金属化(直接电镀)。如开始所述,直接电镀比无外电流的塑料表面金属化通常需要金属(即,例如,钯)对塑料表面更高的覆盖度。因此,通过发明性蚀刻处理的效果,即来自活化剂的更高金属覆盖度,开启了以下可能性:用酸性和碱性高锰酸盐溶液发明性蚀刻处理之后,能通过直接电镀使塑料表面成功经历金属化。在用酸性和碱性高锰酸盐溶液组合蚀刻之后,用具有不同的钯浓度的活化剂处理不同的塑料表面。在塑料表面的更高钯覆盖度下观察到的有利效果经测试,且在活化剂中50ppm或50ppm以上至200ppm的钯浓度范围内观察到。在活化剂中钯的浓度因此可降低至50ppm-100ppm。不论在活化剂中这种低钯浓度,无外电流的塑料表面金属化或甚至塑料表面的直接电镀随后为可能的。在实施例6中,abs/pc混合物面板的表面上的钯吸收在不同的蚀刻处理之后另外测量。通过蚀刻处理i.(首先酸性蚀刻溶液然后碱性蚀刻溶液)和蚀刻处理iv.(仅碱性蚀刻溶液)蚀刻abs/pc面板,然后用胶态的钯活化剂处理,然后将结合在经不同蚀刻的塑料面板表面上的钯再一次通过王水去除,且如实施例4所述测定在得到的溶液中的钯浓度。获得的结果在实施例6中报导。在已经通过发明性蚀刻处理i.蚀刻的面板上,比已经通过蚀刻处理iv.处理的面板上,发现显著更多表面结合的钯。这些结果可与来自实施例4的对于发明性蚀刻处理i.和蚀刻处理iii.(仅酸性蚀刻溶液)蚀刻之后的abs/pc面板的钯覆盖度的那些结果比较。在实施例4中,当面板已经通过发明性蚀刻处理i.处理时,与面板通过蚀刻处理iii.的单独酸性蚀刻步骤处理时相比,对于活化剂中的所有钯浓度,在abs/pc面板上发现高得多的每单位面积的钯量。这对获得的附着强度引起类似的效果,这已经讨论过。单独酸性蚀刻步骤和单独碱性蚀刻步骤两者都不可带来来自活化剂的提高的塑料表面金属覆盖度。仅酸性蚀刻步骤与碱性蚀刻步骤的组合带来活化之后塑料表面高得多的覆盖度的有利效果。已发现在发明性蚀刻处理i.中的首先酸性蚀刻步骤对钯覆盖度作出大的贡献。然而,随后执行的碱性蚀刻步骤带来钯覆盖度的显著额外增加。该效果是出乎意料的,因为单独执行碱性蚀刻步骤(蚀刻处理iv.)不会带来塑料表面的任何显著的钯覆盖度(见实施例6中的值)。在另一个实施方案中,在工艺步骤a)中高锰酸盐处理之后,通过漂洗掉过量的高锰酸盐溶液来清洁制品。漂洗以一个或多个(优选三个)用水漂洗的步骤实现。在本发明的另一个优选实施方案中,在工艺步骤a)和b)之间实施以下另外的工艺步骤:aiii)在包含用于二氧化锰的还原剂的溶液中处理所述塑料表面。另外的工艺步骤aiii)也称为还原处理。该还原处理将附着在塑料表面的二氧化锰还原为水溶性锰(ii)离子。还原处理在工艺步骤a)的高锰酸盐处理之后且任选在漂洗之后进行。出于该目的,使用还原剂的酸性溶液。还原剂选自包含羟基硫酸铵、羟基氯化铵和过氧化氢的组。优选过氧化氢的酸性溶液,因为过氧化氢既无毒性也不形成复合物。在还原处理的溶液(还原溶液)中过氧化氢的含量为25ml/l-35ml/l的30%过氧化氢溶液(重量%),优选30ml/l的30%过氧化氢溶液(重量%)。用于还原溶液的酸为无机酸,优选硫酸。酸浓度为0.4摩尔/l-5.0摩尔/l,优选1.0摩尔/l-3.0摩尔/l,更优选1.0摩尔/l-2.0摩尔/l,在所有情况下基于一元酸。在使用硫酸的情况下,特别优选50g/l96%硫酸-100g/l96%硫酸的浓度,对应于基于一元酸的1.0摩尔/l-2.0摩尔/l的酸浓度。还原处理去除会干扰制品金属化的二氧化锰沉淀。因此,工艺步骤aiii)的还原处理促进了用期望的金属层对制品的均匀和连续覆盖,并促进了涂敷在制品的金属层的附着强度和光滑度。工艺步骤aiii)的还原处理同样地对支架的塑料罩壳的金属化有有利影响。在工艺步骤b)期间钯对塑料罩壳的不期望的覆盖被抑制。当还原溶液包含强无机酸,优选硫酸时,该效果特别显著。在还原溶液中,比起羟基硫酸铵或羟基氯化铵,优选过氧化氢,也因为其更好地抑制支架金属化。在工艺步骤aiii)中的还原处理在30℃-50℃实施,优选40℃-45℃。还原处理实施1-10分钟,优选3-6分钟的时间。为了在活化之前获得支架的充分保护,将在还原溶液中的处理时间提高至3-10分钟是有利的,优选3-6分钟。使用的过氧化氢还原剂必须不时地补充。过氧化氢的消耗可由结合至塑料表面的二氧化锰的量计算。实际上,观察在工艺步骤aiii)期间的还原反应过程中气体的释放和当气体释放停止时计量过氧化氢的初始量(例如30ml/l的30%溶液)就足够。在还原溶液的升高的操作温度下,例如40℃,反应迅速且在最多一分钟之后完成。此外,意外地,已经发现在工艺步骤a)(蚀刻)中塑料表面上的二氧化锰增加量的沉积的情况下,在随后的活化(工艺步骤b))中金属胶体对塑料表面的覆盖度提高,当在它们之间,在工艺步骤aiii)(还原处理)中从塑料表面去除沉积的二氧化锰时。如关于工艺步骤a)(蚀刻)的部分所述,在酸性蚀刻溶液中更高浓度的硫酸导致二氧化锰在塑料表面上有利的增加量的沉积。然而,同时,在酸性蚀刻溶液中更高浓度的硫酸也具有不利作用,即二氧化锰的增加量显著削弱了酸性蚀刻溶液的稳定性,且必须再一次从在蚀刻(工艺步骤a)之后在增加的程度上从塑料表面去除二氧化锰的沉积物。在酸性蚀刻溶液中硫酸浓度的水平因此导致相反的效果,其对最终涂敷到塑料表面的金属层的品质兼具正反两种效果。因此,在关于工艺步骤a)(蚀刻)的部分中,指定的无机酸的浓度范围,特别是对于酸性蚀刻溶液中的硫酸,为其中非常显著地抑制不利效果同时在最大可能程度上支持有利效果的浓度窗口。在酸性蚀刻溶液和碱性蚀刻溶液中塑料表面的蚀刻组合导致沉积在塑料表面上的二氧化锰的量进一步增加。对于由abs和abs/pc混合物制造的塑料面板,这显示在实施例7中。沉积在塑料面板上的二氧化锰的量借助于icp-oes再一次测定,如实施例4和7所述。在发明性蚀刻处理i.(首先酸性蚀刻溶液,然后碱性蚀刻溶液)之后沉积的二氧化锰的量比单独酸性蚀刻步骤(蚀刻处理iii.)之后高得多。在工艺步骤a)(蚀刻)中塑料表面上的二氧化锰增加量的沉积的情况下,在随后的活化(工艺步骤b))中,当在工艺步骤aiii)(还原处理)中同时从塑料表面去除沉积的二氧化锰时,来自活化剂的金属对塑料表面的覆盖度提高由实施例8显示。在实施例8中,检验塑料表面在二醇化合物中的停留时间对附着强度和对沉积的二氧化锰及结合的钯的量的影响。实施例8的结果以图的形式显示在图2中。图2中的术语“归一化值”在以上已经解释。所有初始测量概括在表10.2中。在塑料表面上发现的锰的量为在蚀刻期间结合的二氧化锰的量的度量。由图2可推出,随着在二醇溶液中塑料表面的停留时间提高,沉积在塑料表面上的二氧化锰的量也提高。沉积在塑料表面上的镁的相应量也归为来自钯活化剂在塑料表面结合的钯的量。图2清楚显示了随着沉积的二氧化锰的增加量,结合至塑料表面的钯的量也增加。对于塑料表面的金属化的工业规模应用,所述制品通常固定在支架上。这些是金属运载系统,其允许用单独工艺步骤的连续溶液同时处理大量制品,并允许最后的步骤电解沉积一个或多个金属层。支架通常自身涂覆有塑料。因此,支架大体上类似构成基底,用于塑料表面的金属化过程。然而,不期望所述支架的额外金属化,因为在制品的涂覆之后,必须再次从支架去除金属层。这意味着用于去除的额外费用和不便,以及额外的化学品消耗。此外,在这种情况下金属化设备的生产率更低,因为所述支架在再装载制品之前首先必须去金属化。在使用包含铬酸的蚀刻剂的情况下,该问题减少许多。在蚀刻期间,铬酸也穿透入支架的塑料罩壳中并在后续的工艺步骤期间从这些塑料罩壳中扩散出来,因此防止支架的金属化。如果期望用更加环境安全的工艺步骤替代用于塑料蚀刻处理的毒性铬硫酸,防止不需要的支架金属化也是有利的。在本发明的另一个实施方案中,支架的保护可在工艺步骤a)和工艺步骤b)之间实施,优选在工艺步骤aiii)和aiv)之间。不论支架的保护时间是否在本发明的方法描述的时间之中,其导致对支架的塑料罩壳的保护,避免金属沉积,而固定在支架上的制品在固定步骤期间被金属化。在本发明的一个实施方案中,当工艺步骤bii)由制品在金属化溶液中的无电镀金属化组成时,用碘酸盐离子的处理是特别有利的。用包含碘酸盐离子源的溶液对支架的保护在20℃-70℃的温度下执行,更优选45℃-55℃。优选支架保护的工艺步骤通过用包含碘酸盐离子的溶液处理支架来实施。适合的碘酸盐离子源为金属碘酸盐。金属碘酸盐选自包含碘酸钠、碘酸钾、碘酸镁、碘酸钙和它们的水合物的组。金属碘酸盐的浓度为5g/l-50g/l,优选15g/l-25g/l。用碘酸盐离子对支架处理的持续时间为1-20分钟,优选2-15分钟和更优选5-10分钟。包含碘酸盐离子源的溶液可还包含酸。优选选自包含硫酸和磷酸的组的无机酸,优选硫酸。酸浓度为0.02摩尔/l-2.0摩尔/l,优选0.06摩尔/l-1.5摩尔/l,更优选0.1摩尔/l-1.0摩尔/l,在所有情况下基于一元酸。在使用硫酸的情况下,特别优选5g/l96%硫酸-50g/l96%硫酸的浓度,对应于基于一元酸的0.1摩尔/l-1.0摩尔/l的酸浓度。本发明的方法还包含工艺步骤b),其中塑料表面用金属胶体溶液或金属化合物的溶液处理。金属胶体或金属化合物的金属选自包含元素周期表(pte)过渡i族和pte过渡viii族的金属的组。pte的过渡viii族金属选自包含以下的组:钯、铂、铱、铑和两种或更多这些金属的混合物。pte的过渡i族金属选自包含金、银和这些金属的混合物的组。在金属胶体中优选的金属为钯。金属胶体用保护性胶体稳定。保护性胶体选自包含金属保护性胶体、有机保护性胶体和其它保护性胶体的组。作为金属保护性胶体,优选锡离子。有机保护性胶体选自包含聚乙烯醇、聚乙烯基吡咯烷酮和明胶的组,优选聚乙烯醇。在本发明的优选实施方案中,在工艺步骤b)中的金属胶体溶液为具有钯/锡胶体的活化剂溶液。该胶体溶液由钯盐、锡(ii)盐和无机酸获得。优选的钯盐为氯化钯。优选的锡(ii)盐为氯化锡(ii)。无机酸可由盐酸或硫酸组成,优选盐酸。胶体溶液通过在氯化锡(ii)的帮助下将氯化钯还原为钯而形成。氯化钯向胶体的转化完成;因此,胶体溶液不再包含任何氯化钯。如果,在随后的工艺步骤中,塑料表面经无电镀金属化,在胶体溶液中钯的浓度为5mg/l-100mg/l,优选20mg/l-50mg/l和更优选30mg/l-45mg/l,基于pd2+。如果,在随后的工艺步骤中,塑料表面通过直接电镀金属化,在胶体溶液中钯的浓度为50mg/l-200mg/l,优选75mg/l-150mg/l,更优选100mg/l-150mg/l和更优选80mg/l-120mg/l,基于pd2+。氯化锡(ii)的浓度为0.5g/l-10g/l,优选1g/l-5g/l和更优选2g/l-4g/l,基于sn2+。盐酸的浓度为100ml/l-300ml/l(37重量%的hcl)。此外,钯/锡胶体溶液另外包含锡(iv)离子,其通过锡(ii)离子的氧化形成。在工艺步骤b)期间,胶体溶液的温度为20℃-50℃和优选35℃-45℃。活化剂溶液的处理时间为0.5分钟-10分钟,优选2分钟-5分钟和更优选3分钟-5分钟。在本发明的另一实施方案中,在工艺步骤b)中,金属化合物溶液用于代替金属胶体。使用的金属化合物的溶液为包含酸和金属盐的溶液。金属盐中的金属由一种或更多种以上列出的pte的过渡i族和viii族金属组成。金属盐可为钯盐,优选氯化钯、硫酸钯或乙酸钯,或银盐,优选乙酸银。酸优选为盐酸。备选地,也可使用金属络合物,例如钯络合盐,例如钯-氨基吡啶络合物的盐。工艺步骤b)中存在的金属化合物为40mg/l-80mg/l的浓度,基于金属。金属化合物的溶液可在25℃-70℃,优选25℃的温度下使用。用金属化合物溶液的处理时间为0.5分钟-10分钟,优选2分钟-6分钟和更优选3分钟-5分钟。在工艺步骤a)和b)之间,可实施以下另外的工艺步骤:aiv)在含水酸性溶液中处理塑料表面。在工艺步骤aiii)和b)之间优选实施工艺步骤aiv)。如果,在本发明的方法中,在工艺步骤aiii)后进行支架保护,则工艺步骤aiv)更优选在支架保护和工艺步骤b)之间实施。在工艺步骤aiv)中塑料表面的处理也称为初步浸渍,且含水酸性溶液用作初步浸渍溶液。初步浸渍溶液具有与工艺步骤b)中的胶体溶液相同的组成,在胶体和它们的保护性胶体中无金属存在。初步浸渍溶液,在工艺步骤b)中使用钯/锡胶体溶液的情况下,排他地包含盐酸,如果胶体溶液同样地包含盐酸。对于初步浸渍,在环境温度下简短的浸入初步浸渍溶液就足够。不漂洗塑料表面,在初步浸渍溶液中处理之后,还直接用工艺步骤b)的胶体溶液处理它们。当工艺步骤b)包括用金属胶体溶液处理塑料表面时,优选实施工艺步骤aiv)。当工艺步骤b)包括用金属化合物溶液处理塑料表面时,也可实施工艺步骤aiv)。在用金属胶体或金属化合物在工艺步骤b)中处理塑料表面之后,可漂洗这些塑料表面。在本发明的另一个实施方案中,塑料表面在后续工艺步骤中经无电镀金属化。在该实施方案中,在工艺步骤b)和c)之间实施以下另外的工艺步骤:bi)在含水酸性溶液中处理塑料表面,和bii)在金属化溶液中将塑料表面无电镀金属化。实施方案示意性地显示在表2中。表2:塑料金属化的实施方案当要通过无电镀金属化方法金属化所述制品时,即通过无电镀方法将第一金属层涂敷在塑料表面时,使用这些另外的工艺步骤bi)和bii)。如果在工艺步骤b)中已经用金属胶体实施活化,在工艺步骤bi)中用加速剂溶液处理塑料表面以从塑料表面去除胶体溶液中的胶体成分,例如保护性胶体。如果在在步骤b)中的胶体溶液中胶体为钯/锡胶体,则使用的加速剂溶液优选为酸的水溶液。所述酸选自,例如,包含硫酸、盐酸、柠檬酸和四氟硼酸的组。在钯/锡胶体的情况下,加速剂溶液帮助去除锡化合物,其用作保护性胶体。备选地,在工艺步骤bi)中,当在工艺步骤b)中金属化合物的溶液已经用于代替金属胶体用于活化时,实施还原剂处理。如果金属化合物的溶液为氯化钯的盐酸溶液或银盐的酸性溶液时,用于该目的的还原剂溶液则包含盐酸和氯化锡(ii)。还原剂溶液还可包含另一种还原剂,例如nah2po2或硼烷或氢硼化物,例如碱金属硼烷或碱土金属硼烷或二甲基氨基硼烷。在还原剂溶液中优选使用nah2po2。在工艺步骤bi)中,在加速或用还原剂溶液处理之后,可首先漂洗塑料表面。工艺步骤bi)和任选一个或多个漂洗步骤后进行工艺步骤bii),在其中无电镀金属化塑料表面。例如,使用常规的镍浴完成无电镀镍,镍浴尤其包含硫酸镍、次磷酸盐例如次磷酸钠作为还原剂、以及有机络合剂和ph调节剂(例如缓冲剂)。使用的还原剂可同样地为二甲基氨基硼烷或次磷酸盐和二甲基氨基硼烷的混合物。作为镀镍的备选方案,塑料表面的无电镀镀铜是可能的。对于镀铜,可使用无电镀铜浴,通常包含铜盐例如硫酸铜、氯化铜、铜-edta或次磷酸铜,以及还原剂例如甲醛或次磷酸盐,例如碱金属或铵盐,或次磷酸和另外的一种或多种络合剂例如酒石酸,以及ph调节剂例如氢氧化钠。由此致使导电的表面可随后经电解进一步金属化以获得功能化或装饰性表面。在本发明的另一个实施方案中,通过直接电镀金属化塑料表面,表示不通过无电镀而是直接通过电解金属化方法将塑料表面金属化。在这个实施方案中,以下另外的工艺步骤在工艺步骤b)和c)之间实施:bi)在转化溶液中处理所述塑料表面。该实施方案示意性地显示在表3。表3:塑料金属化的另外的实施方案在转化溶液中塑料表面处理的作用为足以用于直接电解金属化的电导层在没有之前的非电镀金属化时在塑料表面上形成。如果在工艺步骤b)中的胶体溶液中的胶体为钯/锡胶体,使用的转化溶液优选为通过络合剂络合的铜离子的碱性溶液。例如,转化溶液可包含有机络合剂,例如酒石酸、乙二胺四乙酸(edta)或乙醇胺和/或它们的盐,和铜盐,例如硫酸铜。在用转化溶液在工艺步骤bi)中处理之后,塑料表面可首先经漂洗。因此已经使之导电的塑料表面可随后经进一步的电解金属化,以便获得功能性或装饰性的表面。本发明方法的步骤c)为用金属化溶液将塑料表面金属化。工艺步骤c)中的金属化可电解实现。对于电解金属化,可使用任何期望的金属沉积浴,例如用于镍、铜、银、金、锡、锌、铁、铅或它们的合金的沉积。这种沉积浴为本领域技术人员所熟悉的。watts镍浴通常用作亮镍浴,这包含硫酸镍、氯化镍和硼酸。以及作为添加剂的糖精。用作亮铜浴的组合物的实例为包含以下的一种组合物:硫酸铜、硫酸、氯化钠和作为添加剂的有机硫化合物(其中硫为低氧化态,例如有机硫化物或二硫化物)。在工艺步骤c)中塑料表面的金属化作用为用金属涂覆塑料表面,金属选自以上列出用于沉积浴的金属。在本发明的另一个实施方案中,工艺步骤c)之后,实施以下另外的工艺步骤:ci)经金属化的塑料表面在升高的温度下的存储。如在通过湿化学方法用金属涂覆非导体的所有电镀方法中,金属和塑料基底之间的附着强度在金属层涂敷之后的第一周期内提高。在室温下,该过程在约三天后完成。这可通过在升高的温度下储存显著地加速。该过程在80℃下约一小时后完成。假定初始低附着强度由位于金属和非电导基底之间的边界并阻碍静电力形成的薄的水层引起。已经发现用酸性和碱性高锰酸盐溶液的发明性蚀刻(工艺步骤a))产生塑料表面的结构,与例如用铬硫酸的常规预处理相比,其允许塑料与金属层的更大的接触面积。这也是为什么获得比用铬硫酸处理(见实施例2、3和5)更高的附着强度的原因。然而,比起使用铬硫酸的情况,更光滑的表面有时在金属化之后直接产生甚至更低的初始附着强度。特别是在电镀镍的情况下,且很特别地当沉积的金属层具有高的内应力时,或当金属和塑料的热膨胀系数差距很大且复合物暴露于快速变化的温度时,初始附着强度可能不足。在该情况下,在升高的温度下处理经金属化的塑料表面为有利的。该步骤可包括将由abs塑料制造的金属化制品在50℃-80℃的升高的温度下处理5分钟-60分钟的时间,优选在70℃下,在水浴中,使得水可分布在塑料基质内的金属-塑料界面上。在升高的温度下,经金属化的塑料表面的处理或储存的效果在于进一步提高初始的、相对低的附着强度,使得在工艺步骤ci)之后,获得涂敷在塑料表面上的金属层的附着强度在至少或大于0.6n/mm的期望范围内。本发明的方法因此使得能实现制品的非电导塑料表面的金属化,具有良好的方法可靠性且随后涂敷的金属层有优良的附着强度。在本文中,不仅平面的塑料表面通过本发明的方法以高附着强度金属化;此外,不均匀形状的塑料表面也提供有均匀和强附着的金属涂层。此外,用包含至少一种酸性蚀刻溶液和至少一种碱性蚀刻溶液的蚀刻溶液对塑料表面的发明性蚀刻(过程工艺步骤a)),在用胶体溶液或金属化合物溶液活化塑料表面期间,导致金属对塑料表面高得多的覆盖度。有效实施例在下文中描述的有效实施例旨在详细地说明本发明。实施例1:发明性实施例bayblendt45pg的面板(10cm×5cm,abs/pc混合物)在已经用磷酸钾缓冲剂调节至ph=7的2-(2-乙氧基乙氧基)乙酸乙酯的40%溶液中在25℃下处理7分钟(预处理步骤)。随后,在流水下漂洗面板约1分钟。在已经加热到70℃的酸性高锰酸盐溶液(100g/lnamno4,10g/l96%h2so4)中处理面板10分钟。此后,在碱性高锰酸盐溶液中(30g/lnamno4和20g/lnaoh)处理面板10分钟(蚀刻处理i.,工艺步骤a))。此后,面板具有均匀的褐色表面。用25ml/l96%硫酸和30ml/l30%的过氧化氢组成的还原溶液在40℃下还原,从面板去除二氧化锰(工艺步骤aiii))。在后续的漂洗和简短的初步浸渍入300ml/l36%盐酸溶液(工艺步骤aiv))之后,将面板在基于钯胶体(得自atotech的adhemaxaktivatorpl,125mg/l钯)的胶态活化剂中在40℃下活化5分钟(工艺步骤b))。此后,漂洗面板然后在60℃下浸入基于铜离子的转化溶液中(来自atotech的futuronultraculink,工艺步骤bi))1分钟。漂洗之后,通过在室温下将其引入铜电镀浴中(得自atotech,cupracidht,工艺步骤c))中且施加约2.5a的电流,将面板镀铜。2分钟之后,面板完全且均匀地镀铜。在实施例1中的工艺步骤概括在表4中。实施例2:发明性实施例将两个bayblendt45pg面板(10cm×5cm,abs/pc混合物)在2-(2-乙氧基乙氧基)乙酸乙酯的溶液中预处理,如实施例1所述,然后在流水下漂洗约1分钟。将两个面板标明p1和p2。面板p1在已经加热到70℃的酸性高锰酸盐溶液中(100g/lnamno4,10g/l96%h2so4)处理10分钟。面板p2在已经保持在50℃的碱性高锰酸盐溶液中(30g/lnamno4和20g/lnaoh)处理10分钟。此后,将面板p1在所述碱性高锰酸盐溶液中处理10分钟(蚀刻处理i.,工艺步骤a)),且将面板p2在所述的酸性高锰酸盐溶液中处理10分钟(蚀刻处理ii.,工艺步骤a))。随后,如实施例1所述将两个面板用还原溶液处理且经初步浸渍。随后,将面板在基于钯胶体的胶态活化剂中(得自atotech的adhemaxaktivatorpl,23ppm的钯)在40℃活化5分钟(工艺步骤b))。其后,面板经漂洗,然后在40℃下去除钯颗粒的保护壳5分钟(得自atotech的adhemaxacc1加速剂,工艺步骤bi))。随后面板在无外电流下在45℃镀镍10分钟(adhemaxlfs,来自atotech,工艺步骤bii))。虽然面板p1此后具有均匀、无光泽、淡灰的镍层,但在面板p2上有一些在其上没有镍沉积的未覆盖部位。此后,两个面板经漂洗且在3.5a/dm2下在室温下镀铜1小时(cupracidht,来自atotech,工艺步骤c))。漂洗之后,面板储存在80℃下1小时(工艺步骤ci))。随后,通过使用小刀切掉镀金属化塑料面板的宽1cm的条并测量它们的精确宽度来测定涂敷的金属层的附着强度。随后,拉伸测试机(得自instron)用于将金属层拉离塑料,且对准需要的力(根据astmb5331985,2009年再通过)。面板p1具有1.41n/mm和1.24n/mm(平均值:1.32n/mm)的铜层附着强度,且面板p2为1.01n/mm和0.95n/mm(平均值:0.98n/mm)。实施例2中的工艺步骤顺序概括在表5中。表4:实施例1中的工艺步骤顺序表5:实施例2中的工艺步骤顺序实施例3:对比实验将bayblendt45的四个面板(5.2×14.9×0.3cm,abs/pc混合物)在2-(2-乙氧基乙氧基)乙酸乙酯溶液中预处理10分钟且如实施例1所述漂洗。蚀刻处理iii.:两个经预处理的面板然后用温的(70℃)酸性高锰酸盐溶液处理,溶液包含100g/l的高锰酸钠和10g/l96%硫酸(最终浓度:0.1摩尔/l硫酸)。蚀刻处理iv.:另外两个经预处理的面板用碱性高锰酸盐溶液处理,溶液由30g/l的高锰酸钠和20g/l的氢氧化钠组成。蚀刻处理在70℃下实施10分钟。蚀刻处理v.:两个另外的未预处理的面板用铬硫酸溶液处理,溶液由380g/l氧化铬(vi)和380g/l96%硫酸组成。蚀刻处理在70℃下实施10分钟。此后,所有面板在水中漂洗1分钟,且来自蚀刻处理iii.和iv.的面板在50g/l的96%硫酸和30ml/l30%过氧化氢的溶液中清洁,使其无沉积的二氧化锰(工艺步骤aiii))。随后,所有面板如实施例2中说明的处理,即漂洗,简短的初步浸渍(工艺步骤aiv)),在钯胶体中(25ppm的钯)在45℃下活化3分钟(工艺步骤b)),并再次漂洗,在50℃下去除钯颗粒的保护壳(工艺步骤bi)),在无外电流下实现镀镍(工艺步骤bii)),然后漂洗,镀铜70分钟(工艺步骤c))并存储在80℃下30分钟(工艺步骤ci))。随后,如实施例2所述测定金属层在塑料面板上的附着强度。对于已经通过蚀刻处理iii.(仅酸性高锰酸盐溶液)蚀刻的面板,发现附着强度为1.09n/mm-1.32n/mm,对于已经通过蚀刻处理iv.(仅碱性高锰酸盐溶液)蚀刻的面板,发现附着强度为0n/mm(金属层和塑料表面之间有气泡)-0.25n/mm,而且,对于已经通过蚀刻处理v.(铬硫酸)蚀刻的面板,附着强度为0.45n/mm-0.70n/mm。对比而言,对于已经通过发明性蚀刻处理i.(首先酸性高锰酸盐溶液,然后碱性高锰酸盐溶液)蚀刻的面板,发现1.41n/mm-1.24n/mm的更佳附着强度(见实施例2)。实施例3中的工艺步骤顺序概括在表6。表6:实施例3中的工艺步骤顺序实施例4:对比实验将10.4cm×14.9cm×3mm大小的两组塑料面板novodurp2mc(abs)和bayblendt45(abs/pc混合物)在15%的2-(2-乙氧基乙氧基)乙酸乙酯和10%丁氧基乙醇的溶液中处理10分钟,所述溶液已经用磷酸钾缓冲剂调节到ph=7且保持在45℃的恒温箱中。蚀刻处理iii.:在仔细漂洗之后,如实施例3所述将面板仅酸蚀刻10分钟。蚀刻处理i.:两组面板之一随后在第二蚀刻步骤中在由30g/l高锰酸钠和20g/l氢氧化钠组成的碱性高锰酸盐溶液中在50℃进一步处理10分钟。蚀刻处理v.:由塑料制造的并且具有开始所述尺寸的第三组面板在铬硫酸酸性溶液中处理,然后如实施例3所述漂洗。通过蚀刻处理i.和iii.处理过的面板然后在过氧化氢和硫酸的还原溶液中清洁,然后如实施例2所述漂洗。来自所有蚀刻处理的所有面板随后初步浸渍在300ml/l36%盐酸溶液中,并用不同钯浓度(得自atotech的adhemaxaktivatorpl,钯浓度见表7)的胶态活化剂溶液在40℃下处理5分钟。在该过程中,不移动在活化剂溶液中的板以便获得可比较的值。在钯溶液和塑料基底之间的移动对获得的表面结合的钯的量有重大影响。良好的移动将导致几乎加倍的吸收的钯量,但是将难以再现。然后将面板漂洗和干燥。将干燥的面板水平放置在适合的结晶皿中并用精确的25ml/l与水1:1稀释的王水覆盖。在1分钟的反应时间之后,从每个面板收集液体并通过icp-oes测定其中的钯浓度。icp-oes测量用varianvistampx原子发射光谱仪进行。为了该目的,用0.10mg/l、0.25mg/l、0.50mg/l、2.0mg/l和5.0mg/l钯在1%hno3中的的标准溶液校准原子发射光谱仪。将样品溶解在1%hno3中并直接分析。仪器设置如下:钯的波长:340.458nm和360.955nm测量重复:3次喷雾器气体压力:200kpa辅助气体流速:1.5l/分钟等离子体气体流速:16.5l/分钟高频发生器的rf功率:1250瓦该测量结果用带有icp专家软件的仪器评价,且直接输出为以mg/l表示的浓度值。发现的钯浓度然后转化为每单位面积的钯量。对于结合至塑料表面的钯获得的值概括在表7中,并以图的形式显示在图1中。结果在说明书中讨论。表7:在不同的蚀刻处理及用不同钯浓度的胶体活化之后钯对塑料面板表面的覆盖度实施例5:对比实验在不同的蚀刻处理之后已经通过直接电镀涂敷的abs/pc面板上金属层的附着强度的对比。预期用于蚀刻处理i.、iii.和iv.的bayblendt45pg(5.2cm×14.9cm×0.3cm;abs/pc混合物)的面板,在2-(2-乙氧基乙氧基)乙酸乙酯的溶液中处理(预处理步骤)并如实施例1所述漂洗。蚀刻处理iii.:四个面板然后如实施例3所述仅酸蚀刻10分钟。蚀刻处理i.(发明性蚀刻处理):已经经历蚀刻处理iii.(酸性高锰酸盐溶液)的两个面板随后进一步用碱性高锰酸盐溶液如实施例4所述处理2分钟。蚀刻处理iv.:已经用二醇溶液预处理的最后二个面板用碱性高锰酸盐溶液如实施例3所述在50℃下处理。蚀刻处理v.:没有经二醇溶液预处理的两个面板用铬硫酸溶液如实施例3所述蚀刻。此后,所有面板在水中漂洗1分钟,且来自蚀刻处理i.、iii.和iv.的面板在还原溶液中经清洁以去除沉积的二氧化锰(工艺步骤aiii)),如实施例3说明。随后,所有面板如实施例1说明处理,即漂洗和简短的初步浸渍(工艺步骤aiv)),并在钯胶体(140mg/l钯)中在45℃下活化(工艺步骤b)),如实施例1所述。为了获得沉积的钯胶体的电导层,将面板浸渍在基于铜离子的转化溶液(futuronplusculink,得自atotech,工艺步骤bi))中3分钟。漂洗之后,所有面板通过将它们在25℃下引入铜电镀浴(cupracidht,得自atotech,工艺步骤c))中70分钟并施加3a/dm²的电流来镀铜。在板已经储存在70℃下60分钟并冷却之后,如实施例2所述测定铜层在塑料面板上的附着强度。表8.2显示了得到的附着强度的值。用不同的蚀刻处理的工艺步骤顺序概括在表8.1中。在每个工艺步骤之后使用的漂洗步骤未列出。工艺步骤停留时间温度40体积%的2-(2-乙氧基乙氧基)乙酸乙酯7分钟25℃蚀刻处理之一:i.:酸性高锰酸盐溶液和10分钟70℃碱性高锰酸盐溶液,或2分钟50℃iii.:酸性高锰酸盐溶液,或10分钟70℃iv.:碱性高锰酸盐溶液,或10分钟50℃v.:380g/lcro3,380g/l96%硫酸*10分钟70℃二氧化锰的去除1分钟40℃活化5分钟45℃转化(futuronplusculink)3分钟60℃镀铜(cupracidht,3a/dm²)70分钟25℃储存60分钟70℃表8.1:在不同的蚀刻处理之后abs/pc面板的直接电镀。*如果在铬硫酸中实施蚀刻处理,省略在2-(2-乙氧基乙氧基)乙酸乙酯中的预处理。表8.2:在不同的蚀刻处理之后在abs/pc面板的直接电镀之后金属层的附着强度对于已经用酸性和随后碱性高锰酸盐蚀刻步骤的组合处理的abs/pc面板,获得最高附着强度。实施例6:对比实验在不同的蚀刻处理之后abs/pc的钯吸收对比使用abs/pc混合物(bayblendt45pg)的面板实施该研究。面板为10cm×7.5cm×3mm的尺寸。将面板在2-(2-乙氧基乙氧基)乙酸乙酯的溶液中预处理(预处理步骤)10分钟并漂洗约1分钟,如实施例1所述。蚀刻处理i.(发明性蚀刻处理):在预处理之后,两个面板首先用包含100g/l高锰酸钠和10g/l96%硫酸(最终浓度:0.1摩尔/l硫酸)的温的(70℃)酸性高锰酸盐溶液处理10分钟。此后,将面板用由30g/l高锰酸钠和20g/l氢氧化钠组成的碱性高锰酸盐溶液在50℃下处理2分钟。蚀刻处理iv.:将另外两个经预处理的面板在50℃下用碱性高锰酸盐溶液如实施例3所述处理。此后,所有面板在水中漂洗1分钟并如实施例3说明在45℃下在还原溶液中处理(工艺步骤aiii))。随后,所有面板经漂洗和简短的初步浸渍,如实施例4所述。随后,将面板在基于钯胶体的胶态活化剂中(得自atotech的adhemaxaktivatorpl,140mg/l钯)在45℃下活化5分钟(工艺步骤b))。测定表面结合的钯的程序如实施例4所述。对于蚀刻处理i.(首先酸性高锰酸盐溶液,然后碱性高锰酸盐溶液),在abs/pc面板的表面上发现42.5mg/m²的钯量,而对于蚀刻处理iv.(仅碱性高锰酸盐溶液),发现8.2mg/m²的钯。发明性蚀刻处理的作用在于,与当表面仅用碱性蚀刻溶液处理时相比,显著地更多的钯结合在塑料表面上。实施例7分别为塑料novodurp2mc(abs)和bayblendt45(abs/pc混合物)的尺寸为10cm×7.5cm×3mm的两个面板在2-(2-乙氧基乙氧基)乙酸乙酯的溶液中处理10分钟,如实施例1所述。蚀刻处理iii.:在仔细漂洗之后,将所有面板在实施例3所述的酸性高锰酸盐溶液中如处理10分钟。蚀刻处理i.:已经通过蚀刻处理iii.处理的abs面板及abs/pc面板的每一个随后在碱性高锰酸盐溶液中如实施例4所述经进一步处理。此后,所有面板经干燥,且每个面板用25ml的50g/l96%硫酸和30ml/l30%过氧化氢的溶液从其上去除附着在面板表面上的二氧化锰。得到的溶液中,锰浓度通过icp-oes如实施例4所述测定并转化到相应的面板区域。用于icp-oes的锰的波长为:257.610nm和259.372nm。附着在塑料表面上的锰的获得值概括在表9中。表9:不同的蚀刻处理之后塑料表面上锰的量在塑料表面上发现的锰的量为在蚀刻期间结合的二氧化锰的量的度量。塑料表面在酸性高锰酸盐溶液和碱性高锰酸盐溶液中的蚀刻组合,与已经通过单一酸性蚀刻步骤(蚀刻处理iii.)蚀刻的塑料表面相比,导致沉积在塑料表面上的二氧化锰的量进一步提高。实施例8:在二醇化合物的溶液中的停留时间对附着强度和沉积的二氧化锰和钯的量的影响在25℃下,将bayblendt45pg(abs/pc混合物)的面板在2-(2-乙氧基乙氧基)乙酸乙酯的40%溶液中处理不同的持续时间(停留时间见表10.2)。蚀刻处理i.:随后,在第一个步骤中用酸性高锰酸盐溶液然后用碱性高锰酸盐溶液蚀刻板,如实施例6所述。用30ml/l的30%过氧化氢在5%硫酸中的溶液去除沉积的二氧化锰。对于在二醇溶液中具有不同的停留时间的一组面板,如实施例4和7所述,通过icp-oes测定沉积的锰的量。附着在塑料表面的锰的获得值概括在表10.2中并显示在图2中。在塑料表面发现的锰的量为在蚀刻期间结合的二氧化锰的量的度量。在后续的漂洗和短暂浸渍入300ml/l36%盐酸溶液(工艺步骤aiv))之后,将余下的面板在基于钯胶体的胶态活化剂中(得自atotech的adhemaxaktivatorpl,140mg/l钯)在45℃下活化5分钟(工艺步骤b))。对于在二醇溶液中具有不同停留时间的另一组的面板,将结合至塑料表面的钯再次去除并如实施例4所述通过icp-oes测定钯的量。获得的值概括在表10.2中并显示在图2中的图形中。此后,将余下的面板漂洗然后在60℃下浸渍在转化溶液中(工艺步骤bi)),经漂洗然后如实施例5所述镀铜。在70℃下存储1小时之后,如实施例2所述在剥离测试中测定附着强度。金属层的附着强度概括在表10.2中并显示在图2中。实施例8中的工艺步骤的顺序概括在表10.1中。工艺步骤停留时间温度40体积%的2-(2-乙氧基乙氧基)乙酸乙酯2-10分钟25℃酸性高锰酸盐溶液10分钟70℃碱性高锰酸盐溶液2分钟50℃二氧化锰的去除1分钟40℃活化5分钟45℃转化(futuronplusculink)3分钟60℃镀铜(cupracidht,3a/dm²)70分钟25℃储存60分钟70℃表10.1:实施例8中的工艺步骤顺序表10.2:附着强度,作为预处理中塑料表面在二醇溶液中的停留时间的函数沉积的mn和pd的量,*:不可能铜的沉积塑料表面在二醇化合物的溶液中的停留时间(预处理步骤)对涂敷的金属层的附着强度有影响。未用二醇化合物处理(图2中停留时间0分钟),不能通过直接电镀沉积任何金属在塑料表面上。在用二醇化合物处理仅4分钟后,相反地,已经获得0.8n/mm的良好的附着强度,且这随着更长的处理时间进一步提升。实施例9:在碱性高锰酸盐溶液中的处理时间和温度对塑料表面的影响如实施例1所述,将bayblendt45pg面板(14.9cm×5.1cm×3mm,表面积:1.64dm²,abs/pc混合物)在2-(2-乙氧基乙氧基)乙酸乙酯的溶液中处理(预处理步骤)并漂洗。蚀刻处理i.:将面板首先在已经加热到70℃的酸性高锰酸盐溶液(100g/lnamno4,10g/l96%h2so4)中处理10分钟。随后,将面板引入到30g/l高锰酸钠和20g/l氢氧化钠的碱性溶液中,在各种情况下,在30℃、50℃和70℃下使用溶液经不同的持续时间(停留时间见表11)。通过用还原溶液在45℃下还原,在30秒内从面板中去除二氧化锰(工艺步骤aiii)),如实施例3所述。随后,将所有面板如实施例1说明的处理,即漂洗、短暂的初步浸渍、在钯胶体中(140mg/l钯)在45℃下活化、再次漂洗、浸渍在基于铜离子的转化溶液中(得自atotech的futuronplusculink,工艺步骤bi))3分钟、并通过在铜电镀浴中施加3.5a/dm2的电流镀铜70分钟。在所有工艺步骤之间,塑料基底在流水下漂洗。随后,将镀铜面板储存在70℃下1小时然后如实施例2所述用instron拉伸试验机测定铜层与塑料基底的附着强度。对于这些面板的每一个,平行处理另一面板,但是在活化之后从过程移除,且通过icp-oes如实施例4所述测定表面上结合的钯的量。表11和图3a和3b显示附着强度和钯量的获得的结果。获得的结果在本说明书中讨论。表11:根据在碱性高锰酸盐溶液中不同长度的停留时间和温度,塑料面板上结合至表面的钯的量及附着强度。*:括号中的值为重复测量结果。实施例10:对比实施例在不同的蚀刻处理之后金属层的附着强度的对比将四个bayblendt45pg(10cm×5cm,abs/pc混合物)的面板在2-(2-乙氧基乙氧基)乙酸乙酯的溶液中预处理,如实施例1所述,然后在流水下漂洗约1分钟。蚀刻处理i:将一个预处理面板根据蚀刻处理i蚀刻(首先酸性高锰酸盐蚀刻溶液,之后碱性高锰酸盐蚀刻溶液,发明性蚀刻),如实施例2所述。蚀刻处理vi:将另一个经预处理的面板首先用已经加热到70℃的不包含高锰酸盐的10g/l96%h2so4的溶液蚀刻10分钟。之后将面板用已经保持在50℃的碱性高锰酸盐溶液(30g/lnamno4和20g/lnaoh)蚀刻10分钟。蚀刻处理ii:将另一个经预处理的面板根据蚀刻处理ii蚀刻(首先碱性高锰酸盐蚀刻溶液,之后酸性高锰酸盐蚀刻溶液,发明性蚀刻),如实施例2所述。蚀刻处理vii:将最后一个经预处理的面板首先用已经保持在50℃的碱性高锰酸盐溶液(30g/lnamno4和20g/lnaoh)蚀刻10分钟。之后将面板用已经加热到70℃的不包含高锰酸盐的10g/l96%h2so4的溶液蚀刻10分钟。随后,如实施例2所述,将四个面板用还原溶液处理且经初步浸渍。随后,将面板在基于钯胶体的胶体活化剂中(得自atotech的adhemaxaktivatorpl,50ppm的钯)在35℃活化5分钟(工艺步骤b))。其后,面板经漂洗,然后在50℃下去除钯颗粒的保护壳5分钟(得自atotech的adhemaxacc1加速剂,工艺步骤bi))。面板随后经无电镀镀镍、漂洗、电镀铜、再次漂洗、储存在80℃下,且如实施例2所述测定沉积金属层的附着强度。表12概括了附着强度的获得的结果。实施例10中的工艺步骤顺序概括在表13中。表12:在不同的蚀刻处理之后金属层的附着强度表13:实施例10中的工艺步骤顺序结果表明为了获得沉积在塑料基底上的金属层的高附着强度,所有的蚀刻溶液(碱性和酸性蚀刻溶液)需要包含高锰酸盐离子。当前第1页12