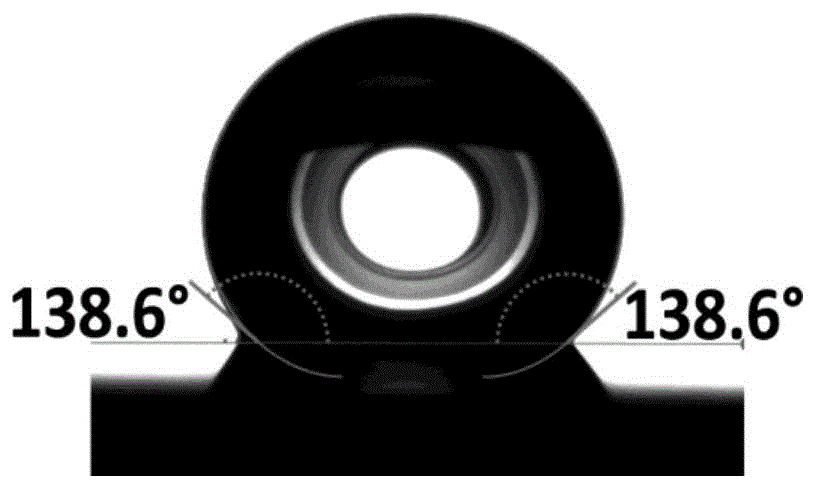
本发明涉及金属材料表面改性
技术领域:
,具体涉及一种镁合金微纳超疏水耐蚀性膜的制备方法。
背景技术:
:镁合金是比模量最高且比强度仅次于钛合金而位于第二位的金属结构材料;其密度约为铝的2/3、钛的2/5、钢的1/4,是工程应用中最轻的金属之一。它具有较高的比强度和比刚度,较压铸铝合金明显好的延伸率和冲击抗力,机械加工性能优良,尺寸稳定性好,阻尼减震和电磁屏蔽性能优良,回收性好,因此被专家誉为21世纪最具有开发与应用潜力和发展前景的绿色工程材料。广泛应用于航空航天、汽车、电子、生物医学、国防等领域。然而,镁合金存在着耐蚀性差、表面硬度低、不耐磨、易燃等缺点,特别是耐蚀性差这一缺点,严重限制了镁合金的应用范围。增强镁合金耐蚀性的途径有两种:一种是开发耐蚀性强的高纯合金或新合金;另一种是对现有镁合金进行表面处理。相比于第一种途径,表面处理可以更有效地提高镁合金耐蚀性而不改变镁合金的其他优异性能。常见的镁合金材料表面处理方法有化学氧化、阳极氧化、金属涂层、有机物涂层等。近些年来,研究者们通过探索自然界中动植物对水的排斥现象,将超疏水现象运用到金属的腐蚀防护中。超疏水表面是指液滴接触角大于150°,滚动角小于10°,具有特殊润湿性的材料表面。8-羟基喹啉常用作医药中间体,是合成克泻痢宁、氯碘喹啉、扑喘息敏的原料,也是染料、农药中间体,其硫酸盐和铜盐是优良的防腐剂、消毒剂和防霉剂;还可用作化学分析的络合滴定指示剂,能与cu2+、be2+、mg2+、ca2+等多种金属离子络合。由于其显著的螯合和络合能力,显现出对镁合金的缓蚀作用,与被腐蚀溶解的金属离子络合形成不溶性沉淀堵塞活性部位,防止被腐蚀的金属进一步溶解。目前有一些报道运用如化学刻蚀、激光刻蚀等方法在镁合金表面先损耗部分镁合金基体,然后利用这部分损耗的基体来形成一层耐蚀性膜,但是一旦遇到腐蚀介质,也会在一定程度上从耐蚀性膜的缝隙中进入并进而直接腐蚀镁合金基体。技术实现要素:为了解决现有技术中使用刻蚀的表面改性方法而先损耗部分镁合金基体以及在此基础上形成的膜层耐蚀性性差的技术问题,而提供一种镁合金微纳超疏水耐蚀性膜的制备方法。本发明的一种镁合金微纳超疏水耐蚀性膜的制备方法,通过在镁合金表面构建微纳结构,然后进行疏水处理,在镁合金表面制备出微纳超疏水耐蚀性膜,具体包括以下步骤:(1)将镁合金进行打磨处理,然后清洗去除表面杂质;(2)将步骤(1)处理得到的镁合金进行微纳结构的构建,所述微纳结构是通过浓度为0.3~0.6mol/l8-羟基喹啉的乙醇溶液浸泡8~10h在镁合金表面构建,构建完成后清洗并干燥;(3)将步骤(2)处理得到的镁合金进行疏水处理,然后进行干燥处理。优选的,所述微纳结构是通过浓度为0.5mol/l8-羟基喹啉的乙醇溶液浸泡8h在镁合金表面构建。进一步地,所述超疏水处理使用1h,1h,2h,2h-全氟辛基三乙氧基硅烷、乙醇和水的混合溶液进行修饰,所述1h,1h,2h,2h-全氟辛基三乙氧基硅烷、乙醇和水按体积比1:200:100。进一步地,所述打磨为依次经过400目、600目、800目、1000目碳化硅砂纸打磨。进一步地,步骤(1)中的清洗是依次放入无水乙醇和去离子水,分别超声清洗15~30min。进一步地,所述步骤(3)中的干燥处理是在80~120℃下干燥30min。有益技术效果:本发明提供的一种镁合金微纳超疏水耐蚀性膜的制备方法,通过在一定浓度的8-羟基喹啉的乙醇溶液中调控浸泡时间来构建出合适的微纳结构膜层,然后对具有微纳结构的镁合金进行疏水处理,进而制备出微纳超疏水耐蚀性膜;采用本发明方法制备的耐蚀性膜在镁合金表面不需要部分损耗镁合金基体就能生长出较为均匀、密集的微纳结构耐腐蚀膜层;本发明只有在构建出合适微纳结构的膜层后才能制备出具备超疏水性效果显著的微纳超疏水性膜层,且该膜层具备较好的耐腐蚀性能。本发明对镁合金的表面形状、尺寸要求低,所用设备简单、处理过程易实现。附图说明图1为是实施例1镁合金样品a的静态接触角。图2为实施例2中镁合金样品b在8-羟基喹啉的乙醇溶液浸泡8h后的10000倍扫描电镜图。图3为实施例2中镁合金样品b在8-羟基喹啉的乙醇溶液浸泡8h后的50000倍扫描电镜图。图4(a)为实施例3中镁合金样品c的静态接触角,图4(b)为实施例3中镁合金样品c的滚动角。具体实施方式以下结合附图及具体实施例进一步描述本发明,但不限制本发明范围。以下实施例均选用mg-al-zn系镁合金az91块状12×12×5(mm)作为实验样品,以下称镁合金样品。实施例1(1)分别用400目、600目、800目、1000目的碳化硅砂纸依次打磨镁合金样品以除去表层的氧化物和其他杂质,然后将其放入无水乙醇中超声清洗15min,再放入去离子水中超声清洗15min,以达到脱脂去污的效果;(2)疏水处理:蒸馏水10ml,无水乙醇20ml,1h,1h,2h,2h-全氟辛基三乙氧基硅烷溶液0.1ml,配制成混合溶液,将镁合金样品浸入混合液中浸泡2h后取出,蒸馏水冲洗;将其放入干燥箱内,120℃干燥30min,记为镁合金样品a。对本实施例所制备的镁合金样品a使用接触角测量仪进行接触角测试,镁合金基体经疏水修饰处理后的静态接触角如图1所示,从图1中可以得出,镁合金基体经1h,1h,2h,2h-全氟辛基三乙氧基硅烷溶液修饰后的表面静态接触角为138.6°,而所谓的超疏水是指表面与液滴间的接触角大于150°,本实施例中的接触角138.6°小于超疏水接触角150°,说明镁合金基体经过1h,1h,2h,2h-全氟辛基三乙氧基硅烷溶液处理后具备一定的疏水性能,但是未达到超疏水效果。对本实施例所制备的镁合金样品a的表面形貌使用扫描电子显微镜进行观察,表面均为经过打磨后的划痕,可见经1h,1h,2h,2h-全氟辛基三乙氧基硅烷溶液修饰后不影响表面形貌。实施例2(1)分别用400目、600目、800目、1000目的碳化硅砂纸依次打磨以除去表层的氧化物和其他杂质,然后将其放入无水乙醇中超声清洗15min,再放入去离子水中超声清洗15min,以达到脱脂去污的效果;(2)构建微纳结构:将试样放入0.5mol/l的8-羟基喹啉的乙醇溶液中室温浸泡8h,取出使用蒸馏水清洗;将其放入干燥箱内,120℃干燥30min,记为镁合金样品b。对本实施例所制备的镁合金样品b使用接触角测量仪进行接触角测试,测得表面静态接触角为62°,这说明镁合金基体经8-羟基喹啉的乙醇溶液浸泡后的表面显现出亲水性。对本实施例所制备的镁合金样品b的表面形貌使用扫描电子显微镜进行观察,结果如图2、图3所示。图2为b放大10000倍后的sem形貌图,从图2可看出,经8小时浸泡的b表面覆盖有一层粗糙的膜层,对其继续放大50000倍后sem形貌图如图3所示,从图3可以看出,所制备的膜层是较为均匀、密集的微孔状微纳结构。实施例3(1)分别用400目、600目、800目、1000目的碳化硅砂纸依次打磨以除去表层的氧化物和其他杂质,然后将其放入无水乙醇中超声清洗15min,再放入去离子水中超声清洗15min,以达到脱脂去污的效果;(2)构建微纳结构:将试样放入0.5mol/l的8-羟基喹啉的乙醇溶液中浸泡,室温下反应时间为8h,取出使用蒸馏水清洗并干燥;(3)疏水处理:蒸馏水10ml,无水乙醇20ml,1h,1h,2h,2h-全氟辛基三乙氧基硅烷溶液0.1ml配制成混合溶液,将步骤(2)中的镁合金样品浸入混合液中浸泡2h后取出,蒸馏水冲洗;将其放入干燥箱内,120℃干燥30min,记为镁合金样品c。对本实施例所制备的镁合金样品c使用接触角测量仪进行接触角测试,镁合金基体经构建微纳结构后进行超疏水修饰处理,测得静态接触角及滚动角如图4(a)、(b)所示,从图4(a)可以看出,镁合金基体经构建微纳结构后进行超疏水修饰处理其静态接触角值达到了163.1°大于超疏水表面接触角150°,从图4(b)可以测得其滚动角为8°小于超疏水表面滚动角10°,根据超疏水表面的定义,说明样品的疏水性效果显著。腐蚀性能测试使用电化学工作站对实施例1、实施例2和实施例3的镁合金样品进行耐腐蚀性能测试。将样品置于3.5wt%nacl溶液中进行电化学测试,根据动电位极化曲线拟合得到样品的自腐蚀电位及腐蚀电流密度数据,数据见表1。表1实施例1~3及裸镁合金的动电位极化曲线拟合结果镁合金样品自腐蚀电位ecorr(v)腐蚀电流密度icorr(a·cm-2)az91镁合金基体-1.466.32×10-5实施例1:a-1.364.25×10-6实施例2:b-1.333.99×10-6实施例3:c-1.274.81×10-8由表1中的数据可知,实施例1,经1h,1h,2h,2h-全氟辛基三乙氧基硅烷修饰的镁合金基体与裸镁合金相比,腐蚀电流密度降低了1个数量级,说明疏水表面可以在很小程度上提高耐蚀性。实施例2中经8-羟基喹啉的乙醇溶液浸泡后的样品b相对于az91镁合金基体,腐蚀电流密度降低了1个数量级,这说明该膜层对镁合金起着一定的耐腐蚀保护作用。实施例3中经8-羟基喹啉的乙醇溶液浸泡后再进行疏水修饰得到的样品c相对于az91镁合金基体,腐蚀电流密度降低了3个数量级,这说明实施例3中在镁合金基体表面形成的一层微纳超疏水膜层对镁合金起着较好的耐腐蚀保护作用。比较实施例1、实施例2和实施例3可知,镁合金基体单独经疏水处理(实施例1)后表面具备一定的疏水性但耐腐蚀性不佳;单独经微纳结构构建(实施例2)的膜层为亲水膜层且具备一定的耐腐蚀性,但耐腐蚀效果也不佳;然而在疏水处理前构建出合适的微纳结构(实施例3)膜层即微纳超疏水膜层,能够显现出超疏水性效果及较好的耐腐蚀性,这是因为合适的微纳结构有助于超疏水性效果的显现,而较好的耐腐蚀性又得益于超疏水性的贡献,这两者形成了有效的协同作用,相辅相成。实施例4(1)分别用400目、600目、800目、1000目的碳化硅砂纸依次打磨以除去表层的氧化物和其他杂质,然后将其放入无水乙醇中超声清洗30min,再放入去离子水中超声清洗15min,以达到脱脂去污的效果;(2)构建微纳结构:将试样放入0.3mol/l的8-羟基喹啉的乙醇溶液中浸泡,室温下反应时间为10h,取出使用蒸馏水清洗并干燥;(3)疏水处理:蒸馏水10ml,无水乙醇20ml,1h,1h,2h,2h-全氟辛基三乙氧基硅烷溶液0.1ml配制成混合溶液,将步骤(2)中的镁合金样品浸入混合液中浸泡3h后取出,蒸馏水冲洗;将其放入干燥箱内,120℃干燥30min,得到表面具有微纳超疏水结构膜层的镁合金样品。对本实例镁合金样品使用接触角测量仪进行接触角测试,测得其表面静态接触角为158°,滚动角为9°,这说明所制备的膜层超疏水性效果显著;对本实例镁合金样品的表面形貌使用扫描电子显微镜进行观察,观察到表面膜的结构较为均匀、密集呈微孔状。以上说明所制备的膜为微纳超疏水膜层。将样品置于3.5wt%nacl溶液中进行电化学测试,根据动电位极化曲线拟合得到样品的腐蚀电流密度5.33×10-8a·cm-2,相对于az91镁合金基体,腐蚀电流密度降低了3个数量级,这说明实施例4中在镁合金基体表面形成的一层微纳超疏水膜层对镁合金起着较好的耐腐蚀保护作用。对比例1本对比例制备方法与实施例3相同,不同点在于:步骤(2)中使用0.2mol/l的8-羟基喹啉的乙醇溶液。对本对比例所制备的镁合金样品使用接触角测量仪进行接触角测试,测得表面静态接触角为93°小于150°,不具有超疏水特性。对本对比例镁合金样品的表面形貌使用扫描电子显微镜进行观察,观察到表面膜的结构不均匀、疏松,未见均匀、密集的微孔结构,这说明使用0.2mol/l的8-羟基喹啉的乙醇溶液浸泡10h后的微纳结构生长状况极差,即本对比例中可视为未成功构建合适的微纳结构,这也就导致后续疏水处理未表现出超疏水性特性。将样品置于3.5wt%nacl溶液中进行电化学测试,根据动电位极化曲线拟合得到样品的自腐蚀电位为-1.36v、腐蚀电流密度为1.07×10-5a·cm-2,相对于az91镁合金基体,本对比例中在镁合金基体表面制备的膜层耐腐蚀性保护作用较差。对比例2本对比例制备方法与对比例1相同,不同点在于:步骤(2)中在8-羟基喹啉的乙醇溶液中浸泡时间>10h,选取浸泡时间20h、48h、72h。对本对比例一系列实验中所制备的样品表面形貌使用扫描电子显微镜进行观察,观察到表面膜的结构状况与对比例1中基本相似;结合对比例1,可见在0.2mol/l的8-羟基喹啉的乙醇溶液浸泡10h甚至更久也不会构建出本发明实施例1和4中的合适的微纳结构。对比例3本对比例制备方法与实施例3相同,不同点在于:步骤(2)中使用0.7mol/l的8-羟基喹啉的乙醇溶液。对本对比例所制备的镁合金样品使用接触角测量仪进行接触角测试,测得表面静态接触角为125.3°小于150°,不具有超疏水特性。对本对比例镁合金样品的表面形貌使用扫描电子显微镜进行观察,观察到镁合金表面呈现不均匀的坑状,未见均匀、密集的微孔结构,这说明使用0.7mol/l的8-羟基喹啉的乙醇溶液浸泡10h后的微纳结构生长状况极差,即本对比例中可视为未成功构建合适的微纳结构,这也就导致后续疏水处理未表现出超疏水性特性。这可能是因为较高浓度的8-羟基喹啉的乙醇溶液对镁合金基体产生了一定的腐蚀作用,影响到构建微纳结构。对比例4本对比例制备方法与对比例3相同,不同点在于:步骤(2)中在8-羟基喹啉的乙醇溶液中的浸泡时间<8h,选取浸泡1h、4h、7h。对本对比例中的一系列实验所制备的样品通过扫描电子显微镜进行观察,表面结构与对比例3中基本相似;结合对比例3,可见在0.7mol/l的8-羟基喹啉的乙醇溶液浸泡8h甚至更少时间也不会构建出本发明实施例1和4中的合适的微纳结构。通过以上实验,可以发现微纳结构需在一定浓度(0.3~.6mol/l)的8-羟基喹啉的乙醇溶液中浸泡一定时间(8~10h)才能在镁合金基体表面构建出合适微观结构的微纳结构膜层,而只有在构建出合适微纳结构的膜层后才能制备出具备超疏水性效果显著的膜层,同时制备的微纳超疏水性膜层具备较好的耐腐蚀性能。当前第1页12