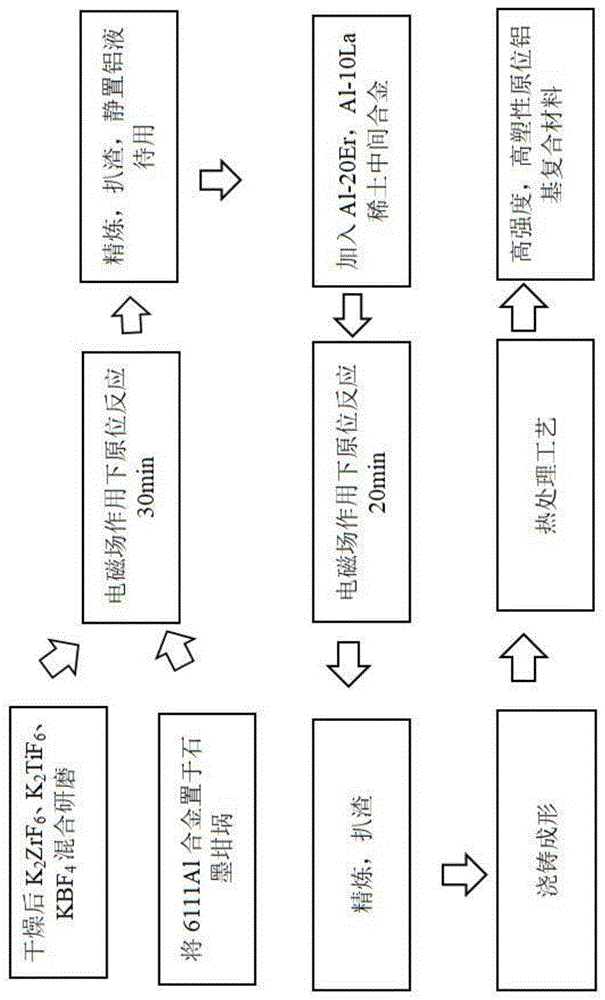
本发明涉及铝基复合材料,具体是一种高强度、高塑性原位铝基复合材料及其制备方法。
背景技术:
:颗粒增强铝基复合材料具有高比强度、高弹性模量、高耐磨性和低热膨胀系数等特点,相比单一铝合金或高分子材料有更加优异的性能,在航空航天、汽车工业、电子封装、体育器材等许多领域内有广阔的应用前景。颗粒作为增强相,在基体中均匀弥散分布,有细晶强化和第二相弥散强化的作用。基体与增强体结合良好,界面干净无污染,可以使铝基复合材料强度、硬度等各项力学性能提高。但是陶瓷颗粒增强铝基复合材料在制备过程中也会存在一些问题,陶瓷颗粒与铝基体润湿性是否良好,陶瓷颗粒与铝基体是否会发生过度的界面反应,陶瓷颗粒是否发生偏聚与团聚以及制备得到的铝基复合材料中是否存在疏松和气孔等等。这些问题的存在都严重影响着铝基复合材料的微观组织和各项力学性能,进一步制约铝基复合材料的应用。可以将稀土元素引入铝基复合材料中,改善陶瓷颗粒作为增强相存在的一些问题,发挥稀土与颗粒的协同强化作用,进一步提高铝基复合材料的各项力学性能。稀土元素化学性质活泼,在铝基体中主要表现在以下三个方面的积极作用:(1)变质细化作用。稀土元素作为形核核心,提高形核率,抑制晶粒长大,对晶粒起到细化的作用。(2)微合金化元素的强化作用。当稀土元素含量较低时,稀土固溶在铝基体中或者在晶界处聚集,起到固溶强化的作用。当稀土元素含量较高时,稀土形成稀土第二相化合物,在基体中弥散分布,可以起到第二相弥散强化作用。(3)净化基体作用。稀土元素化学性质活泼,在反应过程中一方面与杂质元素结合成稳定的化合物,消除杂质。另一方面,与h、o等元素反应生成稳定的化合物,使铝熔体的气体含量减少,减少铝锭凝固后的气孔,提高致密性。此外,稀土元素可以使陶瓷颗粒的分布更加弥散均匀以及提高颗粒与铝基体之间的润湿性。因此,研究稀土与颗粒协同增强的铝基复合材料有很广阔的应用前景。技术实现要素:本发明的目的在于针对存在的陶瓷颗粒增强铝基复合材料中存在的问题,提供一种稀土与二元陶瓷颗粒协同增强的铝基复合材料的制备方法,从而获得高强度,高塑性的原位铝基复合材料。本发明为实现其技术目的所采用的技术方案是通过熔体直接反应法制备颗粒与稀土协同强化的铝基复合材料。通过al-k2tif6-k2zrf6-kbf4反应体系,。制备zrb2和tib2陶瓷颗粒,并加入微合金化元素进一步提高材料的综合力学性能。稀土元素以中间合金al-20er和al-10la形式加入。最后对制备得到的材料进行固溶时效热处理,获得本发明的高强度、高塑性原位铝基复合材料。与现有制备技术相比,本技术方案的特征主要体现在:在电磁场作用下,通过原位反应制备出二元亚微米/纳米级增强颗粒,利用两种尺度增强颗粒间相互作用提高材料的强度与塑性。同时引入稀土er和la元素来协同提高复合材料的力学性能。sc是微合金化效果最好的一种稀土元素,但是它的昂贵价格限制了其在民用行业的大规模应用。稀土元素er的微合金化效果是最接近于sc的,而且价格也相对低廉,只有sc的1/40。因此,选用er元素来提高材料的强度与塑性。而稀土元素la是一种有效的的细化变质剂。因此,选用la元素能显著细化晶粒,改善材料的微观组织。充分发挥两种尺度的增强颗粒和两种稀土元素的强化特点及其协同强化作用,做到提升复合材料的强度与塑性。发明采用的技术方案具体步骤如下:1.本发明选择6111为基体,陶瓷zrb2和tib2增强颗粒通过氟盐原位反应获得,稀土以中间合金的形式加入。将6111铝合金基体放于坩埚中加热至熔融状态,6111铝合金化学成分及质量百分比:si:1.15%;mg:0.72%;cu0.70%;mn0.27%;fe0.26%;zn0.16%;cr0.11%;ti0.15%;余量为al。加入混合均匀的氟盐,同时施加电磁场反应,得到tib2颗粒和zrb2颗粒。再加入稀土中间合金,同时施加电磁场反应。反应结束后对熔体进行精炼除气、扒渣,去除复合熔体中残留的熔渣,杂质和气体。最后,将铝熔体浇铸铜模中,获得陶瓷颗粒zrb2、tib2和稀土er、la协同强化的铝基复合材料。将获得的铝基复合材料进行热处理,进一步提升其强度。其具体步骤如下:1)氟盐的准备:将纯度为99wt%,200目的氟钛酸钾,纯度99wt%,200目的氟锆酸钾和纯度为99wt%,200目的氟硼酸钾在烘箱中烘干,烘箱温度为200-300℃,时间为90-180min。去除氟盐中的结晶水。取所需质量比例混合均匀得到反应盐,包覆铝箔待用。其中k2tif6、k2zrf6和kbf4质量比为48:33:78,k2zrf6、k2tif6和kbf4的加入量总和为铝合金质量的16%。2)原位颗粒的生成:将6111铝合金基体放于坩埚中加热至熔融状态,当温度在850-900℃时,加入均匀混合好的氟盐,同时施加电磁场反应30min,得到微米级的tib2颗粒和纳米级的zrb2颗粒。反应结束后对熔体进行精炼除气、扒渣,去除复合熔体中残留的熔渣,杂质和气体,静置铝熔体待用。3)稀土的引入:当温度降至750-800℃时,加入稀土中间合金al-20er和al-10la,同时施加电磁场反应20min。反应结束后再一次对熔体进行精炼除气、扒渣,去除复合熔体中残留的熔渣,杂质和气体。4)制备颗粒与稀土协同强化的铝基复合材料:随后当温度降至720-750℃时,将铝熔体浇铸到预热150-200℃的铜模中,将浇铸得到的铝基复合材料进行热处理,获得陶瓷颗粒zrb2、tib2和稀土er、la协同强化的铝基复合材料。3.所述的生成zrb2和tib2的反应方程式分别为:3k2zrf6+6kbf4+10al=3zrb2+9kalf4+k3alf63k2tif6+6kbf4+10al=3tib2+9kalf4+k3alf64.所述的通过熔体直接反应法制备得到的zrb2颗粒呈近六边形,尺寸为80-100nm,zrb2颗粒为复合材料质量的1%;tib2颗粒呈近六边形或四边形,尺寸为0.5-1μm,tib2颗粒同样为复合材料质量的1%。引入的稀土er质量分数为复合材料的0.1%,稀土la质量分数为复合材料的0.5%。引入稀土后,zrb2颗粒尺寸细化至50-80nm,tib2颗粒尺寸细化至0.1-0.25μm。6.所述的电磁场励磁电流为170-200a,频率为5-10hz。7.所述的热处理工艺包括固溶处理和时效处理。固溶处理为从室温升温到550℃,保温3h。随后进行淬火处理,淬火介质为20℃的水。时效处理为从室温升温到175℃,保温6h。8.本发明具有以下优点和效果:(1)通过原位反应制备复合材料,由于增强体材料在基体中反应生成,基体与增强体之间亲和力较高,界面干净。增强颗粒尺寸细小,在基体中弥散分布。(2)反应过程中施加电磁场,对熔体起到搅拌作用,加速颗粒之间的碰撞,优化增强颗粒的尺寸、形貌和分布。(3)加入稀土可以使颗粒分布更加均匀,细化晶粒,避免了颗粒尺寸跨度过大,团聚等问题带来的负面影响。还提高增强颗粒与基体润湿性,改善界面结合性,减少铝熔体凝固过程的铸造缺陷。附图说明附图用来对本发明做简单地介绍,对于本领域普通技术人员来讲,在不付出创造性劳动的前提下,还可以根据这些附图获得其他的附图。图1为本发明实施例的制备工艺流程图。图2为实施例2所述工艺条件下制备的颗粒与稀土协同强化的铝基复合材料sem图,(a)500倍sem图;(b)2000倍sem图。图3为实施例2所述工艺条件下制备的颗粒与稀土协同强化的铝基复合材料sem图及eds能谱图。图4为复合材料的颗粒图和析出相图,(a)颗粒图(b)析出相图。具体实施方式本发明可以通过以下实例实施,结合附图对实例作详细说明。但本发明的保护范围不限于下述的实施例。实施例1制备出zrb2质量分数占复合材料1%,tib2质量分数占复合材料1%和er质量分数占复合材料0.1%,la质量分数占复合材料0.3%的一种高强度、高塑性铝基复复合材料。以氟钛酸钾k2tif6,氟锆酸钾k2zrf6和氟硼酸钾kbf4为反应物,将其放于200℃干燥箱中烘3h,去除氟盐中的结晶水。按照质量比k2tif6:k2zrf6:kbf4=48:33:78称取氟盐,将其搅拌混合均匀后,用铝箔包覆待用。将1234g6111铝合金放在坩埚式感应炉中熔炼。当温度在850-900℃,加入均匀混合的氟盐,同时施加励磁电流为200a,频率为10hz的电磁场搅拌30min。反应结束后对熔体进行精炼除气、扒渣,去除复合熔体中残留的熔渣,杂质和气体,静置铝熔体待用。当温度降至750-800℃,加入6.17gal-20er和30.02gal-10la,同时施加励磁电流为200a,频率为10hz的电磁场搅拌20min。反应结束后再一次对熔体进行精炼除气、扒渣,去除复合熔体中残留的熔渣,杂质和气体。随后当温度降至720-750℃时,将铝熔体浇铸到预热150-200℃的铜模中。最后将浇铸得到的铝基复合材料进行550℃×3h的固溶处理和175℃×6h的时效处理。实施例2制备出zrb2质量分数占复合材料1%,tib2质量分数占复合材料1%和er质量分数占复合材料0.1%,la质量分数占复合材料0.5%的一种高强度、高塑性铝基复复合材料。以氟钛酸钾k2tif6,氟锆酸钾k2zrf6和氟硼酸钾kbf4为反应物,将其放于200℃干燥箱中烘3h,去除氟盐中的结晶水。按照质量比k2tif6:k2zrf6:kbf4=48:33:78称取氟盐,将其搅拌混合均匀后,用铝箔包覆待用。将1228g6111铝合金放在坩埚式感应炉中熔炼。当温度在850-900℃,加入均匀混合的氟盐,同时施加励磁电流为200a,频率为10hz的电磁场搅拌30min。反应结束后对熔体进行精炼除气、扒渣,去除复合熔体中残留的熔渣,杂质和气体,静置铝熔体待用。当温度降至750-800℃,加入6.14gal-20er和61.4gal-10la,同时施加励磁电流为200a,频率为10hz的电磁场搅拌20min。反应结束后再一次对熔体进行精炼除气、扒渣,去除复合熔体中残留的熔渣,杂质和气体。随后当温度降至720-750℃时,将铝熔体浇铸到预热150-200℃的铜模中。最后将浇铸得到的铝基复合材料进行550℃×3h的固溶处理和175℃×6h的时效处理。实施例3制备出zrb2质量分数占复合材料1%,tib2质量分数占复合材料1%和er质量分数占复合材料0.1%,la质量分数占复合材料0.7%的一种高强度、高塑性铝基复合材料以氟钛酸钾k2tif6,氟锆酸钾k2zrf6和氟硼酸钾kbf4为反应物,将其放于200℃干燥箱中烘3h,去除氟盐中的结晶水。按照质量比k2tif6:k2zrf6:kbf4=48:33:78称取氟盐,将其搅拌混合均匀后,用铝箔包覆待用。将1236g6111铝合金放在坩埚式感应炉中熔炼。当温度在850-900℃,加入均匀混合的氟盐,同时施加励磁电流为200a,频率为10hz的电磁场搅拌30min。反应结束后对熔体进行精炼除气、扒渣,去除复合熔体中残留的熔渣,杂质和气体,静置铝熔体待用。当温度降至750-800℃,加入6.18gal-20er和86.52gal-10la,同时施加励磁电流为200a,频率为10hz的电磁场搅拌20min。反应结束后再一次对熔体进行精炼除气、扒渣,去除复合熔体中残留的熔渣,杂质和气体。随后当温度降至720-750℃时,将铝熔体浇铸到预热150-200℃的铜模中。最后将浇铸得到的铝基复合材料进行550℃×3h的固溶处理和175℃×6h的时效处理。将上述三个实验获得的不同质量分数的铸锭按gb228-2002金属材料室温拉伸试验方法加工成拉伸试样,在ags-x万能材料试验机上测试材料的拉伸力学性能。表1铸锭热处理后力学性能指标实验编号抗拉强度(mpa)延伸率(%)基体铝合金267.86.5实施例1298.48.2实施例2326.114.8实施例3293.39.7力学性能测试表明,经过颗粒与稀土的协同强化后铝基复合材料的最佳抗拉强度为326.1mpa,延伸率为14.8%。与基体铝合金相比,抗拉强度提高了21.7%,延伸率提高了127%。通过熔体直接反应法制备的原位铝基复合材料,与未加稀土的铝基复合材料相比,强度提高,塑性提高。由于稀土的引入,改善了陶瓷颗粒易于团聚,分布不均匀等负面影响,成功提高铝基复合材料的力学性能,使铝基复合材料在航天航空、汽车工业、体育器材等领域有更广阔的实际应用前景。当前第1页1 2 3