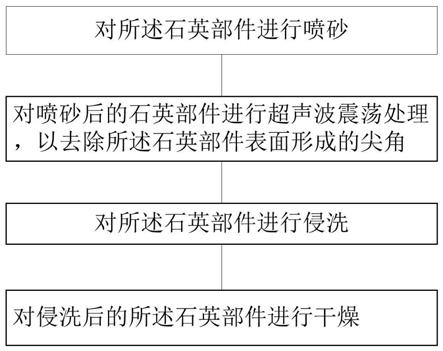
1.本发明涉及半导体技术领域,具体涉及一种用于石英部件的表面处理方法。
背景技术:2.现有半导体制备设备例如tf cvd机台tel hp
–
ti反应室,在制成中钛薄膜因制程会持续累积在反应室内,导致机台内放置晶圆的石英部件表面累计的膜会越来越厚,在晶圆制备过程中,累积在晶圆表面的膜容易掉落在晶圆表面,造成晶圆表面薄膜生长异常,目前针对石英部件表面附着力不好的问题,没办法提前预防,只能在测机以及后站晶圆电性异常时才能发现。
技术实现要素:3.本发明的目的在于提供一种用于石英部件的表面处理方法,能够增加石英部件表面粗糙度,增强石英部件的附着力,还能够去除石英部件喷砂后形成尖角,以避免石英部件在制成过程中表面形成线状膜,提高晶圆的良率。
4.根据本发明实施例的用于石英部件的表面处理方法,包括:对所述石英部件进行喷砂;对喷砂后的石英部件进行超声波震荡处理,以去除所述石英部件表面形成的尖角;对所述石英部件进行侵洗;对侵洗后的所述石英部件进行干燥。
5.根据本发明的一些实施例,在对所述石英部件进行喷砂之前还包括以下步骤:对所述石英部件进行药剂清洗;对清洗后的所述石英部件进行水洗震荡;对所述水洗震荡后的石英部件进行干燥。
6.根据本发明的一些实施例,在对喷砂后的石英部件进行超声波震荡处理,以去除所述石英部件表面形成的尖角的步骤中,超声波震荡处理后的所述石英部件的粗糙度ra2与喷砂后所述石英部件的粗糙度ra1满足:95%ra1≤ra2≤105%ra1。
7.可选地,在对所述喷砂后的石英部件进行超声波震荡处理步骤中,所述超声波震荡的频率为100khz~150khz。
8.可选地,在对所述喷砂后的石英部件进行超声波震荡处理的步骤中,采用超声波震荡的时间为10min~20min。
9.根据本发明的一些实施例,在对侵洗后的所述石英部件进行干燥后还包括以下步骤:对所述石英部件的表面粗糙度进行检测,以判断所述石英部件的表面粗糙度是否满足预设粗糙度标准。
10.可选地,在对所述石英部件的表面粗糙度进行检测的步骤中,包括以下步骤:选取所述石英部件的多个检测点;对所述多个检测点进行测量以获取多个粗糙度;在判断所述石英部件的表面粗糙度是否满足预设粗糙度标准中,判断多个所述粗糙度是否满足所述预设粗糙度标准。
11.可选地,所述预设粗糙度标准为每个所述检测点的粗糙度为4.5um-7.5um,且多个所述检测点的粗糙度的最大差值小于2um。
12.可选地,在判断多个所述粗糙度是否满足所述预设粗糙度标准的步骤后,还包括以下步骤:在所述检测点的粗糙度不满足预设粗糙度标准时,对粗糙度高的检测点区域进行打磨,对粗糙度低的检测点区域进行喷砂,直至多个所述检测点的粗糙度满足预设粗糙度标准。
13.根据本发明的一些实施例,在对喷砂后的石英部件进行超声波震荡处理;对所述石英部件进行侵洗步骤中,所述超声波震荡处理和对石英部件进行侵洗循环执行多次。
附图说明
14.图1是根据本发明一个实施例的用于石英部件的表面处理方法;
15.图2是根据本发明另一个实施例的用于石英部件的表面处理方法;
16.图3是喷砂后的石英部件薄膜附着后的结构示意图;
17.图4是喷砂后石英部件表面的图像采集图片;
18.图5是经过超声波震荡处理后石英部件的表面结构示意图;
19.图6是经过超声波震荡后石英部件表面的图像采集图片。
20.附图标记:
21.1:石英部件;2:喷砂后石英部件表面形成的喷砂层;3:尖角;4:线状膜。
具体实施方式
22.以下结合附图和具体实施方式对本发明提出的一种石英部件的表面处理方法作进一步详细说明。
23.下面参考附图描述根据本发明实施例的石英部件的表面处理方法。
24.根据本发明实施例的石英部件的表面处理方法包括以下步骤:对石英部件1进行喷砂;对喷砂后的石英部件1进行超声波震荡处理,以去除石英部件1表面形成的尖角3;对石英部件1进行侵洗;对侵洗后的石英部件1进行干燥。
25.具体地,在半导体制备设备中,石英部件1可位于沉积腔室内,如位于等离子体喷淋头周围,用于聚集等离子气体到腔室载台上方,在对晶圆进行沉积制备过程中,石英部件1表面不可避免附着形成一定厚度的薄膜,薄膜在石英部件1表面的附着力较低,容易掉落在晶圆表面造成晶圆异常,通过对石英部件1的表面进行喷砂以形成喷砂层2,能够增强石英部件1表面的粗糙度,使得薄膜在石英部件1表面的附着力会大大增加,以避免薄膜掉落在晶圆表面造成晶圆良率异常。
26.喷砂过程是利用高速砂流的冲击作用清理和粗化基体表面的过程。采用压缩空气为动力,以形成高速喷射束将喷料(铜矿砂、石英砂、金刚砂、铁砂、海南砂)高速喷射到需要处理的工件表面,使工件表面的外表面的外表或形状发生变化,由于磨料对工件表面的冲击和切削作用,使工件的表面获得一定的清洁度和不同的粗糙度,使工件表面的机械性能得到改善,因此提高了工件的抗疲劳性,增加了它和涂层之间的附着力,延长了涂膜的耐久性。
27.在对石英部件1进行喷砂时,可使用石英砂进行喷砂,从而能够增加石英部件1表面的粗糙度,增强薄膜的附着力,使得薄膜不易脱落。喷砂时可对石英部件1容纳晶圆的内壁面和部分外壁面进行喷砂,可采用遮护部件遮住部分石英部件1,暴露需要石英部件1需
要喷砂的部分,减少喷砂材料的浪费。在其他实施例中,也可采用石英砂进行喷砂。
28.在一些具体示例中,在喷砂过程中,可采用180目的小颗粒石英砂进行固定角度喷砂,以提高喷砂后石英部件的表面粗糙度的均匀性,本实施例中,可以采用与石英表面成70-90度的角度进行喷砂,具体的为70度、75度、80度、85度或90度;喷砂压力为3-5公斤压力,具体的可以为3公斤、3.5公斤、4公斤、4.5公斤或5公斤;喷砂机的喷头距离待喷砂的石英部件1的表面距离为8cm-10cm,具体可以为8cm、9cm或10nm,从而能够使得喷砂更加均匀,且达到符合要求的石英部件的粗糙度。
29.对石英部件1表面喷砂后,石英部件1的表面会形成一些尖角3,在后续晶圆长膜工艺中,石英部件1的尖角3处长的膜会呈线状垂下以形成线状膜4,线状膜4容易脱落掉晶圆上。为了降低线状膜4掉落在晶圆表面造成的良率异常,可对喷砂后的石英部件1进行超声波震荡处理,以去除石英部件1表面形成的尖角3,由此使得石英部件1表面粗糙度更加均匀,避免后续工艺中在尖角3处长出线状膜4,以进一步地提高晶圆良率。
30.其中,超声波震荡处理后的所述石英部件1的粗糙度ra2与喷砂后所述石英部件1的粗糙度ra1满足:95%ra1≤ra2≤105%ra1,这样通过超声波震荡处理后的石英部件1的粗糙度与喷砂后的石英部件1的粗糙度的误差为
±
5%,由此,能够保证石英部件1表面对薄膜的附着性,同时在此范围内也能够避免喷砂后形成的尖角3对产品造成缺陷。需要说明的是,当超声波震荡处理和清洗分为多次循环进行时,此处超声波震荡处理后的石英部件1的粗糙度ra2指的是多次超声波震荡处理后的石英部件1的粗糙度。
31.图3为喷砂后石英部件1薄膜附着后的结构示意图,图4是喷砂后石英部件1表面的图像采集图片,如图3和图4所示,喷砂后的石英部件1表面锐角明显且突出点比较锋利,线状膜4附着在喷砂后形成的尖角3上;图5是经过超声波震荡处理后石英部件1的表面结构示意图,图6是经过超声波震荡后石英部件1表面的图像采集图片,如图6所示,石英部件1表面锐角较为平缓,无特别突出的点,如图5所示,超声波震荡处理后的石英部件1表面无尖角3,线状膜4无法附着。
32.超声波震荡处理后石英部件1表面具有震荡掉落的颗粒,通过对石英部件1进行侵洗,可将石英部件1表面掉落的颗粒冲洗掉。其中,超声波震荡处理和石英部件1的侵洗可循环多次进行,也就是说,可对石英部件1进行多次超声波震荡处理和多次清洗,具体地,对石英部件1进行一次超声波震荡处理后,对石英部件1进行一次侵洗,以冲掉石英部件1表面的颗粒,然后再次对石英部件1进行超声波震荡处理,并再次进行侵洗,由此循环进行多次,以去掉石英部件1表面的尖角3。在多次进行超声波震荡处理和侵洗后,可对石英部件1进行干燥。
33.在对石英部件1进行超声波震荡处理过程中,超声波震荡的频率可以为100khz~150khz,进一步可以为120khz~140khz,超声波震荡的功率为130hz~170hz,进一步可以为145hz~160hz,采用超声波震荡处理的时间可以为10min~20min,进一步可以为13min~18min,在对石英部件1进行侵洗时可采用超纯水进行侵洗,侵洗的时间可以为15min~25min。在一些具体示例中,可对石英部件1进行超声波震荡处理的频率可以为130khz,功率为155hz,震荡处理时间持续为15min,去除尖角3后用超纯水冲洗20min,超纯水可以为常温。在此条件下进行超声波震荡处理,可以去除喷砂后石英部件表面形成的尖角,且超声波震荡处理后石英部件表面的粗糙度可以维持和喷砂后石英部件表面粗糙度在
±
5%的范围
内,从而在去除尖角的情况下,保持石英部件表面粗糙度,从而提高薄膜在石英部件表面的附着力,避免薄膜掉落在晶圆表面造成晶圆良率异常。
34.需要说明的是,这里的超声波震荡处理的时间指的是在本发明实施例的用于石英部件1表面处理方法中的超声波震荡处理的总时间,例如在进行超声波震荡处理和侵洗的过程只进行一次时,则石英部件1经过一次超声波震荡处理时间为10min~20min,进一步可以为13min~18min,然后进行侵洗的时间为15min~25min。再例如,超声波震荡处理和侵洗可分为多次循环进行,则石英部件1多次超声波震荡处理的总时间为10min~20min,进一步可以为13min~18min,多次侵洗的时间为15min~25min,其中超声波震荡处理和侵洗可循环进行3-4次,每次超声波震荡处理时间可以为3min-5min,每次侵洗的时间为4min-7min。
35.如图2所示,在对石英部件1进行喷砂之前,还包括以下步骤:对石英部件1表面进行药剂清洗,对清洗后的石英部件1进行水洗震荡,并对水洗震荡后的石英部件1进行干燥,这样,在对石英部件1进行喷砂前,能够有效去除石英部件1的表面形成的薄膜,也能够使得石英部件1表面粗糙度更加均匀,从而有利于对石英部件1进行均匀喷砂,使得喷砂后的石英部件1表面粗糙度更加均匀一致,减小尖角3和尖角3处线状膜4的产生。
36.在一些示例中,石英部件1表面沉积形成的薄膜为钛,对石英部件1进行药剂清洗时,采用的药剂可为双氧水和氢氧化钾的混合溶液,其中双氧水的浓度可以为40%,氢氧化钾的浓度可以为20%,由此,可有效去除石英表面形成的薄膜。需要说明的是,药剂清洗时的药剂溶液的成分不限于此,可根据不同材料的薄膜选择不同的药剂清洗。
37.在对侵洗后的石英部件1进行干燥后,还包括以下步骤:对所述石英部件1的表面粗糙度进行检测,以判断所述石英部件1的表面粗糙度是否满足预设粗糙度标准。若石英部件1表面粗糙度不均匀,在后续工艺中长膜时造成石英部件1表面形成的薄膜厚度和阻值分布会发生偏移,在后续工艺薄膜沉积过程中,由于石英部件表面粗糙度不均匀,导致其表面沉积薄膜的厚度不一致,从而影响腔室中各区域的等离子气体浓度不一致,最终导致晶圆薄膜沉积出现厚度不一致的情况,通过对石英部件1表面粗糙度的检测,能够判断石英部件1表面粗糙度的均匀性。当石英部件1表面粗糙度不符合预设粗糙度标准时,可对石英部件1进行进一步处理,以使得石英部件1表面粗糙度更加均匀,符合预设粗糙度标准。
38.具体地,在对石英部件1表面粗糙度进行检测的步骤中,可以包括以下步骤:选取所述石英部件1的多个检测点,具体地,可选取石英部件1内侧壁的多个检测点和石英部件1外侧壁的多个检测点进行检测;对所述多个检测点进行测量以获取多个粗糙度;在判断所述石英部件1的表面粗糙度是否满足预设粗糙度标准中,判断多个所述粗糙度是否满足所述预设粗糙度标准。在检测点的粗糙度不满足预设粗糙度标准时,对粗糙度高的检测点区域进行打磨,对粗糙度低的检测点区域进行喷砂,直至多个检测点的粗糙度满足预设粗糙度标准。
39.例如,对于粗糙度值高的区域可采用百洁布对其进行打磨以降低粗糙度,对粗糙度值低的区域可进行再次喷砂,以增加粗糙度,从而使得处理后的石英部件1表面粗糙度更加均匀,有利于薄膜的附着,减少线状膜4的产生。
40.其中,预设粗糙度标准为每个检测点的粗糙度为4.5um-7.5um,且多个检测点的粗糙度的最大差值小于2um,由此可将石英部件1表面多个检测点的粗糙度控制4.5um-7.5um之间,且检测点中最大粗糙度值和最小粗糙度需控制在2um以内,以使得处理后的石英部件
1表面粗糙度更加均匀。
41.在本发明的一个具体示例中,可选取石英部件1内侧壁的8个检测点和石英部件1外侧壁的8个检测点进行检测,其中,内侧壁为石英部件1最近接近等离子气体喷淋头最接近的部分,下面表格为石英部件1喷砂前、喷砂后以及经过超声波震荡处理的16个检测点的粗糙度值。且喷砂过程采用了180目的小颗粒石英砂进行90固定角度喷砂,超声波震荡频率为130khz,功率为155hz,震荡时间为15min。
42.表1为石英部件1-8号检测点喷砂前、喷砂后以及经过超声波震荡处理后分别进行测量的粗糙度值
43.检测点12345678喷砂前0.951.070.991.001.030.961.010.97喷砂后5.335.745.364.795.475.554.965.36超声波震荡处理后5.335.755.254.795.475.514.975.38
44.表2为石英部件9-16号检测点喷砂前、喷砂后以及经过超声波震荡处理后分别进行测量的粗糙度值
45.检测点910111213141516喷砂前1.051.221.161.261.211.291.331.29喷砂后4.165.494.725.755.774.695.765.25超声波震荡处理后4.165.554.755.795.724.755.765.25
46.通过表格对比可看出,喷砂后大大增强了石英部件1的粗糙度,通过对喷砂后的石英部件1进行超声波震荡后,能够减小石英部件1表面形成的尖角3,且超声波震荡处理后石英部件表面的粗糙度可以维持和喷砂后石英部件表面粗糙度在
±
5%的范围内,从而在去除尖角的情况下,保持石英部件表面粗糙度,从而提高薄膜在石英部件表面的附着力,同时避免线状膜4的产生,进一步降低石英部件1表面薄膜掉落至晶圆表面的风险。
47.以上所述仅是本发明的优选实施方式,应当指出,对于本技术领域的普通技术人员,在不脱离本发明原理的前提下,还可以做出若干改进和润饰,这些改进和润饰也应视为本发明的保护范围。