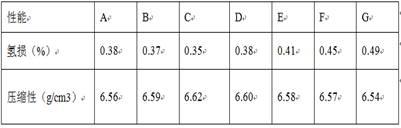
[0001]
本发明属于预合金钢粉领域,具体涉及一种高强度、高硬度水雾化预合金钢粉的制备方法。
背景技术:[0002]
我国铁基粉末冶金制品发展空间广阔,以汽车行业为例,我国年产汽车2000多万辆,但由于技术水平制约,我国每辆汽车上使用的铁基粉末冶金零件量不到5kg,而欧洲、美国等发达国家每辆汽车上使用的铁基粉末冶金零件量已达14-19.5kg。若我国每辆汽车增加9kg铁基粉末冶金零件,每年将至少增加18万吨钢铁粉末和铁基粉末冶金零部件的需求。因此,提高我国钢铁粉末和铁基粉末冶金零件的制备水平对于我国铁基粉末冶金及相关产业发展具有重要意义。
[0003]
粉末冶金技术能够以与制品形状极为相近的形状、高的尺寸精确度,来制造复杂形状的部件,因此,能够极大降低切削成本。因此,粉末冶金制品在多方面被用作各种机械、部件。并且近年来,为了实现部件的小型化、轻量化,提高粉末冶金制品强度的需求日益增加。特别是对铁基粉末制品的高强度化要求强烈。
[0004]
粉末冶金用铁基粉末成形体一般通过如下操作来制造:向铁基粉末中混入铜粉、石墨粉等合金用粉末、以及硬脂酸、硬脂酸锂等润滑剂而制成铁基粉末混合粉,然后将其填充到模具中进行加压成形。根据成分,可以将铁基粉末分类为铁粉(例如纯铁粉等)、合金钢粉等。高强度、高硬度水雾化预合金钢粉是使粉末冶金材料加工过程中的烧结和热处理(渗碳热处理、光亮热处理等)结合成一道工序制备的材料,其材料的生产过程更有效,产品经济效益更高。
[0005]
目前,一些欧美国家已经成功开发了专门为烧结硬化工艺而专门设计的预合金钢粉。瑞典hoganasab公司、美国hoeganaes公司和加拿大quebec metal powder金属粉末公司是国际上著名的粉末生产企业,他们已成功研发出多种烧结硬化用粉。烧结硬化正逐步成为一种低成本生产、高强度、高硬度粉末冶金铁基结构零件的工艺方法,其中加拿大quebec metal powder金属粉末有限公司设计开发了atomet4601、atomet4701、atomet4801等预合金水雾化钢粉,美国hoeganaes公司开发了flc-4608预合金钢粉产品,采用其烧结硬化工艺制备的产品已用于电动工具、家庭用具、机械及汽车制造等多个行业。
[0006]
目前国内在该方面的的研究和应用都比较少,更重要的是我国的预合金钢粉工艺技术和相关设备均起步较晚,在没有优良的基粉做支撑,没有完善配套的工艺及设备,极大地限制了对高强度、高硬度的预合金钢粉的技术发展。目前国内使用的烧结硬化预合金钢粉大多从国外进口,价格昂贵。
[0007]
申请人发现,目前的高强度、高硬度水雾化预合金钢粉在烧结硬化材料的应用中,均是通过添加合金元素来延迟奥氏体转变为铁素体与渗碳体,以利于形成马氏体,提高淬透性,但是在此过程中会添加过多的铬、锰元素;而该铬、锰元素易于氧化,烧结过程中难被还原,其氧化物分布在基体的晶界,会导致烧结硬化后基体材料的性能降低。
[0008]
进一步的,申请人还发现,在高强度、高硬度水雾化预合金钢粉的制备过程中,其预合金生粉在水雾化及脱水烘干过程中存在有氧化现象,且其氧化物在常规还原状态下易于被还原;再叠加前述的铬、锰元素易于氧化,且其氧化物在常规还原状态下难以被还原;两者共同影响,造成产品氢损较高,严重制约预合金钢粉的深度应用和推广。
技术实现要素:[0009]
为解决现有技术中存在的技术问题,本发明提供一种高强度、高硬度水雾化预合金钢粉的制备方法,以实现以下发明目的:(1)提供一种高强度、高硬度水雾化预合金钢粉的制备方法,能够有效克服预合金钢粉氢损较高的缺陷,促进预合金钢粉的深度应用和推广;(2)提供一种高强度、高硬度水雾化预合金钢粉的制备方法,克服为提高淬透性,添加过多铬、锰元素,导致粉末烧结硬化后基体材料性能下降的问题;(3)采用本发明的高强度、高硬度水雾化预合金钢粉的制备方法,提升制得的预合金钢粉经烧结硬化后的硬度、强度性能。
[0010]
为解决以上技术问题,本发明采取的技术方案如下:一种高强度、高硬度水雾化预合金钢粉的制备方法,包括配料、冶炼工艺、雾化、还原、后处理。
[0011]
1、配料选取成分含量符合以下要求:mn<0.50%,p<0.04%,si<0.2%,s<0.04%,cr+ni+cu+mo≤0.20%的优质普碳废钢和生铁为原料,备用。
[0012]
所述优质普碳废钢:生铁的重量份比值为1-2:1-2。
[0013]
通过添加合金元素来延迟奥氏体转变为铁素体与渗碳体,以利于形成马氏体,即提高了淬透性;淬透性的提高意味着在较低的冷却速度下可以获得更多的马氏体。
[0014]
2、冶炼工艺所述冶炼工艺,包括ebt电炉冶炼、电炉出钢、lf精炼炉冶炼。
[0015]
所述ebt电炉冶炼,冶炼温度为1500-1600℃。
[0016]
所述ebt电炉冶炼,电炉出钢时,控制终点碳含量≥0.15%。
[0017]
所述ebt电炉冶炼,当电炉钢水成分符合以下要求:c≤0.28,p≤0.010%,s≤0.009%,mn≤0.13%,si≤0.03%,p≤0.010%,cr+ni+cu+mo≤0.07%,升温至1630-1660℃,进行电炉出钢。
[0018]
所述电炉出钢,通过控制电炉倾炉,使所述ebt电炉冶炼的钢水流入精炼钢包。
[0019]
所述电炉出钢,预留部分钢水,禁止氧化渣进入精炼钢包。
[0020]
所述lf精炼炉冶炼,所述精炼钢包进站精炼,在吹氩气搅拌保证钢水合金均匀的情况下,取样检测,根据检测数据,推算加入锰、镍、钼的添加量。
[0021]
所述吹氩气搅拌,氩气压力0.3-0.5mpa,氩气流量260-350nl/min。
[0022]
所述lf精炼炉冶炼,精炼初期加入锰铁(含锰73%),调整钢水中锰含量至0.35-0.55%。
[0023]
所述lf精炼炉冶炼,精炼末期加入镍板和钼铁(含钼65%),调整钢水中镍含量至1.30-1.55%、钼含量至1.15-1.40%。
[0024]
所述加入锰铁、镍板、钼铁,先加入80%重量份的锰铁、镍板、钼铁,取样检测后,根据钢水中mn、ni、mo含量,加入剩余量的锰铁、镍板、钼铁。
[0025]
所述lf精炼炉冶炼,强化脱氧时,使用无硅脱氧剂,保证快速变白渣;所述白渣精炼时间不低于15分钟。采用白渣精炼能降低钢水氧含量及最大限度保证气固夹杂物上浮,提高钢水的纯净度。
[0026]
所述lf精炼炉冶炼,精炼末期降低氩气压力,吹氩不低于10分钟,确保钢液的均匀性及部分夹杂物的上浮。
[0027]
所述lf精炼炉冶炼,精炼完成后,控制钢水成分:c含量≤0.28,p含量≤0.010%,s含量≤0.009%,si含量≤0.03%,p含量≤0.010%,mn含量0.35-0.55%,ni含量为1.30-1.55%,mo含量为1.15-1.40%,进入雾化步骤。
[0028]
所述冶炼工艺是本发明高强度、高硬度水雾化预合金钢制备的重要环节,一方面钢水的纯度影响着最终产品的综合性能;另一方面,决定着合金含量能否达到规定的要求。在超纯钢水冶炼的基础上,通过合理的配加合金工艺,以达到要求的合金含量。
[0029]
3、雾化所述雾化,为高压雾化,所述高压雾化喷嘴喷射夹角30-50
°
,水压力8-16mpa。
[0030]
雾化后制得的预合金钢粉,其成分含量为:c含量≤0.28%,s含量≤0.009%,si含量≤0.03%,p含量≤0.01,mn含量0.35-0.55%,ni含量为1.30-1.55%,mo含量为1.15-1.40%,氢损≤1.67%。
[0031]
4、还原所述还原,包括一次精还原和二次精还原。
[0032]
所述还原,采用纯氢还原。
[0033]
所述一次精还原,还原温度为925-980℃,气流量为70 nm3/h,料层厚度23-29mm,带速145-185mm/min。
[0034]
所述一次精还原,还原后产品氢损0.31%左右,压缩性为6.64(g/cm3)左右。
[0035]
所述二次精还原,还原温度为925-980℃,气流量为70 nm3/h,料层厚度23-29mm,带速145-185mm/min。
[0036]
所述二次精还原,还原后产品氢损0.14%左右,压缩性为6.69(g/cm3)左右。
[0037]
预合金钢生粉在高温、还原气氛下脱去铁粉中的氧之后,还原气氛成为含有一定水蒸气的湿气氛,此时还原气氛的露点升高,再进入脱碳区脱去铁粉中的碳,这就是所谓的“干脱氧、湿脱碳”。由于预合金生粉一方面在水雾化及脱水烘干过程中被氧化(氢损1.6%左右),该氧化物易于在常规还原状态下被还原,另一方面因含有mn元素,该元素易于氧化而很难在常规状态下被还原,所以为了达到要求的氢损含量,在本发明的还原工艺中,采用二次精还原工艺,通过还原温度、气流量、带速和料厚等工艺参数的设置,提升产品性能。
[0038]
5、后处理所述后处理,经破碎、磁选、动力或无动力合批后,即可制得本发明的高强度、高硬度水雾化预合金钢粉。
[0039]
所述制得的高强度、高硬度水雾化预合金钢粉性能指标为:c含量≤0.003%,s含量≤0.011%,si含量≤0.03%,p含量≤0.012%,mn含量0.35-0.55%,ni含量为1.30-1.55%,mo含量为1.15-1.40%,氢损≤0.14%。
[0040]
与现有技术相比,本发明的有益效果为:(1)本发明所述的高强度、高硬度水雾化预合金钢粉的制备方法,有效克服原料成分中铬、锰元素过多导致烧结硬化后基体材料性能下降的问题,烧结硬化后,烧结硬度平均达35.0-37.5hrc,横向断裂强度平均达1042.6-1109.1 mpa;(2)本发明所述的高强度、高硬度水雾化预合金钢粉的制备方法,有效克服预合金钢粉氢损较高的缺陷,其预合金钢粉的压缩性达6.69g/cm3,氢损值达0.14%;(3)本发明所述的高强度、高硬度水雾化预合金钢粉的制备方法,其预合金钢粉的松装密度达3.01 g/cm3;(4)本发明所述的高强度、高硬度水雾化预合金钢粉的制备方法,其预合金钢粉的粒度组成:+100目为0.6%;+140目为20.4%;+200目为29.6%;+325目为27.9%;-325目为21.5%,后期应用性能好;(5)本发明所述的高强度、高硬度水雾化预合金钢粉的制备方法,采用两次还原工艺,有益于氧的脱除,还原效果好,有效提升预合金钢粉性能。
具体实施方式
[0041]
为了对本发明的技术特征、目的和效果有更加清楚的理解,现说明本发明的具体实施方式。
[0042]
实施例1一种高强度、高硬度水雾化预合金钢粉的制备方法,包括配料、冶炼工艺、雾化、还原、后处理。
[0043]
1、配料选取成分含量符合以下要求:mn<0.50%,p<0.04%,si<0.2%,s<0.04%,cr+ni+cu+mo≤0.20%的优质普碳废钢和生铁为原料,备用。
[0044]
所述优质普碳废钢:生铁的重量份比值为1:2。
[0045]
2、冶炼工艺所述冶炼工艺,包括ebt电炉冶炼、电炉出钢、lf精炼炉冶炼。
[0046]
所述ebt电炉冶炼,冶炼温度为1550℃。
[0047]
所述ebt电炉冶炼,电炉出钢时,控制终点碳含量≥0.15%。
[0048]
所述ebt电炉冶炼,当电炉钢水成分符合以下要求:c≤0.28%,p≤0.010%,s≤0.009%,mn≤0.13%,si≤0.03%,p≤0.010%,cr+ni+cu+mo≤0.07%,升温至1630℃,进行电炉出钢。
[0049]
所述电炉出钢,通过控制电炉倾炉,使所述ebt电炉冶炼的钢水流入精炼钢包。
[0050]
所述电炉出钢,预留部分钢水,禁止氧化渣进入精炼钢包。
[0051]
所述lf精炼炉冶炼,所述精炼钢包进站精炼,在吹氩气搅拌保证钢水合金均匀的情况下,取样检测,根据检测数据,推算加入锰、镍、钼的添加量。
[0052]
所述吹氩气搅拌,氩气压力0.3mpa,氩气流量260nl/min。
[0053]
所述lf精炼炉冶炼,精炼初期加入锰铁(含锰73%),调整钢水中锰含量至0.45%。
[0054]
所述lf精炼炉冶炼,精炼末期加入镍板和钼铁(含钼65%),调整钢水中镍含量至1.43%、钼含量至1.28%。
[0055]
所述加入锰铁、镍板、钼铁,先加入80%重量份的锰铁、镍板、钼铁,取样检测后,根据钢水中mn、ni、mo含量,加入剩余量的锰铁、镍板、钼铁。
[0056]
所述lf精炼炉冶炼,强化脱氧时,使用无硅脱氧剂,保证快速变白渣;所述白渣精炼时间不低于15分钟。采用白渣精炼能降低钢水氧含量及最大限度保证气固夹杂物上浮,提高钢水的纯净度。
[0057]
所述lf精炼炉冶炼,精炼末期降低氩气压力,吹氩不低于10分钟,确保钢液的均匀性及部分夹杂物的上浮。
[0058]
所述lf精炼炉冶炼,精炼完成后,控制钢水成分:c含量≤0.28,p含量≤0.010%,s含量≤0.009%,si含量≤0.03%,p含量≤0.010%,mn含量0.35-0.55%,ni含量为1.30-1.55%,mo含量为1.15-1.40%。
[0059]
3、雾化所述雾化,为高压雾化,所述高压雾化喷嘴喷射夹角30
°
,水压力8mpa。
[0060]
雾化后制得的预合金钢粉,其成分含量为:c=0.27%,s=0.008%,si=0.03%,p=0.01%,mn=0.45 %,ni=1.43%,mo=1.30%,氢损为1.69%。
[0061]
4、还原所述还原,包括一次精还原和二次精还原。
[0062]
所述还原,采用纯氢还原。
[0063]
所述一次精还原,还原温度为945℃,气流量为70 nm3/h,料层厚度27mm,带速180mm/min。
[0064]
所述一次精还原,还原后产品氢损0.33%,压缩性为6.57(g/cm3)。
[0065]
所述二次精还原,还原温度为955℃,气流量为70 nm3/h,料层厚度23mm,带速180mm/min。
[0066]
所述二次精还原,还原后产品氢损0.17%,压缩性为6.61(g/cm3)。
[0067]
5、后处理所述后处理,经破碎、磁选、动力或无动力合批后,即可制得高强度、高硬度水雾化预合金钢粉。
[0068]
所述制得的高强度、高硬度水雾化预合金钢粉性能指标为:c=0.003%,s=0.013%,si=0.04%,mn=0.45%,p=0.011%,ni=1.44%,mo=1.30%,氢损=0.16%,常温500mpa下压缩性为6.62g/cm3,松装密度3.08g/cm3。
[0069]
粒度组成:+100目为0.8%;+140目为20.2%;+200目为29.3%;+325目为28.4%;-325目为21.3%。
[0070]
烧结性能试验:选取本实施例1制得的高强度、高硬度水雾化预合金钢粉作为样品1,加入2%wt的铜、0.9%wt的石墨、0.6%wt的润滑剂,在600mpa压力下压制烧结坯件,在氨分解气氛下,1120℃温度下烧结30分钟。具体试验结果见下表:
实施例2一种高强度、高硬度水雾化预合金钢粉的制备方法,包括配料、冶炼工艺、雾化、还原、后处理。
[0071]
1、配料选取成分含量符合以下要求:mn<0.50%,p<0.04%,si<0.2%,s<0.04%,cr+ni+cu+mo≤0.20%的优质普碳废钢和生铁为原料,备用。
[0072]
所述优质普碳废钢:生铁的重量份比值为1:1。
[0073]
2、冶炼工艺所述冶炼工艺,包括ebt电炉冶炼、电炉出钢、lf精炼炉冶炼。
[0074]
所述ebt电炉冶炼,冶炼温度为1550℃。
[0075]
所述ebt电炉冶炼,电炉出钢时,控制终点碳含量≥0.15%。
[0076]
所述ebt电炉冶炼,当电炉钢水成分符合以下要求:c≤0.28%,p≤0.010%,s≤0.009%,mn≤0.13%,si≤0.03%,p≤0.010%,cr+ni+cu+mo≤0.07%,升温至1650℃,进行电炉出钢。
[0077]
所述电炉出钢,通过控制电炉倾炉,使所述ebt电炉冶炼的钢水流入精炼钢包。
[0078]
所述电炉出钢,预留部分钢水,禁止氧化渣进入精炼钢包。
[0079]
所述lf精炼炉冶炼,所述精炼钢包进站精炼,在吹氩气搅拌保证钢水合金均匀的情况下,取样检测,根据检测数据,推算加入锰、镍、钼的添加量。
[0080]
所述吹氩气搅拌,氩气压力0.35mpa,氩气流量300nl/min。
[0081]
所述lf精炼炉冶炼,精炼初期加入锰铁(含锰73%),调整钢水中锰含量至0.45%。
[0082]
所述lf精炼炉冶炼,精炼末期加入镍板和钼铁(含钼65%),调整钢水中镍含量至1.43%、钼含量至1.28%。
[0083]
所述加入锰铁、镍板、钼铁,先加入80%重量份的锰铁、镍板、钼铁,取样检测后,根据钢水中mn、ni、mo含量,加入剩余量的锰铁、镍板、钼铁。
[0084]
所述lf精炼炉冶炼,强化脱氧时,使用无硅脱氧剂,保证快速变白渣;所述白渣精炼时间不低于15分钟。采用白渣精炼能降低钢水氧含量及最大限度保证气固夹杂物上浮,提高钢水的纯净度。
[0085]
所述lf精炼炉冶炼,精炼末期降低氩气压力,吹氩不低于10分钟,确保钢液的均匀性及部分夹杂物的上浮。
[0086]
所述lf精炼炉冶炼,精炼完成后,控制钢水成分:c含量≤0.28,p含量≤0.010%,s含量≤0.009%,si含量≤0.03%,p含量≤0.010%,mn含量0.35-0.55%,ni含量为1.30-1.55%,mo含量为1.15-1.40%。
[0087]
3、雾化所述雾化,为高压雾化,所述高压雾化喷嘴喷射夹角47
°
,水压力12mpa。
[0088]
雾化后制得的预合金钢粉,其成分含量为:c=0.28%,s=0.009%,si=0.03%,p=0.01%,mn=0.47 %,ni=1.44%,mo=1.31,氢损为1.67%。
[0089]
4、还原所述还原,包括一次精还原和二次精还原。
[0090]
所述还原,采用纯氢还原。
[0091]
所述一次精还原,还原温度为965℃,气流量为70 nm3/h,料层厚度25mm,带速170mm/min。
[0092]
所述一次精还原,还原后产品氢损为0.31%,压缩性为6.64(g/cm3)。
[0093]
所述二次精还原,还原温度为965℃,气流量为70 nm3/h,料层厚度25mm,带速170mm/min。
[0094]
所述二次精还原,还原后产品氢损0.14%,压缩性为6.69(g/cm3)。
[0095]
5、后处理所述后处理,经破碎、磁选、动力或无动力合批后,即可制得本发明的高强度、高硬度水雾化预合金钢粉。
[0096]
所述制得的高强度、高硬度水雾化预合金钢粉性能指标为:c=0.003%,s=0.011%,si=0.03%,mn=0.48%,p=0.012%,ni=1.45%,mo=1.34%,氢损为0.14%,常温500mpa下压缩性为6.69g/cm3,松装密度为3.01g/cm3。
[0097]
粒度组成:+100目为0.6%;+140目为20.4%;+200目为29.6%;+325目为27.9%;-325目为21.5%。
[0098]
烧结性能试验:选取本实施例2制得的高强度、高硬度水雾化预合金钢粉作为样品2,加入2%wt的铜、0.9%wt的石墨、0.6%wt的润滑剂,在600mpa压力下压制烧结坯件,在氨分解气氛下,1120℃温度下烧结30分钟。具体试验结果见下表:实施例3一种高强度、高硬度水雾化预合金钢粉的制备方法,包括配料、冶炼工艺、雾化、还原、后处理。
[0099]
1、配料选取成分含量符合以下要求:mn<0.50%,p<0.04%,si<0.2%,s<0.04%,cr+ni+cu+mo≤0.20%的优质普碳废钢和生铁为原料,备用。
[0100]
所述优质普碳废钢:生铁的重量份比值为1:2。
[0101]
2、冶炼工艺所述冶炼工艺,包括ebt电炉冶炼、电炉出钢、lf精炼炉冶炼。
[0102]
所述ebt电炉冶炼,冶炼温度为1550℃。
[0103]
所述ebt电炉冶炼,电炉出钢时,控制终点碳含量≥0.15%。
[0104]
所述ebt电炉冶炼,当电炉钢水成分符合以下要求:c≤0.28%,p≤0.010%,s≤0.009%,mn≤0.13%,si≤0.03%,p≤0.010%,cr+ni+cu+mo≤0.07%,升温至1630℃,进行电炉出钢。
[0105]
所述电炉出钢,通过控制电炉倾炉,使所述ebt电炉冶炼的钢水流入精炼钢包。
[0106]
所述电炉出钢,预留部分钢水,禁止氧化渣进入精炼钢包。
[0107]
所述lf精炼炉冶炼,所述精炼钢包进站精炼,在吹氩气搅拌保证钢水合金均匀的
情况下,取样检测,根据检测数据,推算加入锰、镍、钼的添加量。
[0108]
所述吹氩气搅拌,氩气压力0.3mpa,氩气流量260nl/min。
[0109]
所述lf精炼炉冶炼,精炼初期加入锰铁(含锰73%),调整钢水中锰含量至0.45%。
[0110]
所述lf精炼炉冶炼,精炼末期加入镍板和钼铁(含钼65%),调整钢水中镍含量至1.43%、钼含量至1.28%。
[0111]
所述加入锰铁、镍板、钼铁,先加入80%重量份的锰铁、镍板、钼铁,取样检测后,根据钢水中mn、ni、mo含量,加入剩余量的锰铁、镍板、钼铁。
[0112]
所述lf精炼炉冶炼,强化脱氧时,使用无硅脱氧剂,保证快速变白渣;所述白渣精炼时间不低于15分钟。采用白渣精炼能降低钢水氧含量及最大限度保证气固夹杂物上浮,提高钢水的纯净度。
[0113]
所述lf精炼炉冶炼,精炼末期降低氩气压力,吹氩不低于10分钟,确保钢液的均匀性及部分夹杂物的上浮。
[0114]
所述lf精炼炉冶炼,精炼完成后,控制钢水成分:c含量≤0.28,p含量≤0.010%,s含量≤0.009%,si含量≤0.03%,p含量≤0.010%,mn含量0.35-0.55%,ni含量为1.30-1.55%,mo含量为1.15-1.40%。
[0115]
3、雾化所述雾化,经高压雾化、混料、浸润、脱水、烘干、筛分处理后,制得雾化生粉。
[0116]
所述高压雾化,采用铁标准溶液作为雾化液;所述铁标准溶液为1毫克/毫升铁溶于2%的硝酸。
[0117]
所述高压雾化,喷嘴喷射夹角45
°
,雾化液压力18mpa,雾化液流量为275nm3/h,雾化液进液温度25℃。
[0118]
所述混料,向高压雾化后的物料中投入纳米碳化硅、膨润土粉,混合均匀。
[0119]
所述高压雾化后物料:纳米碳化硅:膨润土粉的重量份比值为22:1:1。
[0120]
所述膨润土粉,粒径为20μm。
[0121]
所述纳米碳化硅,粒径为50nm。
[0122]
所述浸润,将混料后的物料置于2倍体积的5%碳酸锌溶液中,静置30min。
[0123]
所述脱水,采用过滤机对所述浸润后物料进行脱水处理。
[0124]
所述烘干,采用95℃对脱水后物料进行烘干,烘干至含水率<1.5%。
[0125]
雾化后制得的预合金钢粉,其成分含量为:c=0.26%,s=0.010%,si=0.03%,p=0.011%,mn=0.48 %,ni=1.47%,mo=1.31,氢损为1.54%。
[0126]
4、还原所述还原,包括一次精还原和二次精还原。
[0127]
所述还原,采用纯氢还原。
[0128]
所述一次精还原,还原温度为965℃,气流量为70 nm3/h,料层厚度27mm,带速180mm/min。
[0129]
所述一次精还原,还原后产品氢损0.30%,压缩性为6.60(g/cm3)。
[0130]
所述二次精还原,还原温度为970℃,气流量为70 nm3/h,料层厚度23mm,带速185mm/min。
[0131]
所述二次精还原,还原后产品氢损0.15%,压缩性为6.65(g/cm3)。
[0132]
5、后处理所述后处理,经破碎、磁选、动力或无动力合批后,即可制得高强度、高硬度水雾化预合金钢粉。
[0133]
所述制得的高强度、高硬度水雾化预合金钢粉性能指标为:c=0.003%,s=0.008%,si=0.02%,mn=0.48%,p=0.010%,ni=1.47%,mo=1.31%,氢损=0.15%,常温500mpa下压缩性为6.65g/cm3,松装密度=3.02g/cm3。
[0134]
粒度组成: +140目为21.3%;+200目为30.5%;+325目为29.8%;-325目为18.4%。
[0135]
烧结性能试验:选取本实施例3制得的高强度、高硬度水雾化预合金钢粉作为样品3,加入2%wt的铜、0.9%wt的石墨、0.6%wt的润滑剂,在600mpa压力下压制烧结坯件,在氨分解气氛下,1120℃温度下烧结30分钟。具体试验结果见下表:实施例4一次精还原温度的选取与优化试验:基于目前一次精还原工艺的特点,首先固定氢气流量为70nm3/h,带速170mm/min,厚度27mm, 设置一次精还原温度为980℃、970℃、965℃、955℃、945℃、935℃、925℃七组数据测试,试验结果见下表:由表可知,在965℃下高温还原效果最好,氢损含量最低,压缩性可达到最高值6.62g/cm3。
[0136]
同时,在980℃、965 ℃、945 ℃温度下的粉饼块分别检测上中下位置的氢损含量,结果见下表;由上表可知,还原温度在965 ℃时,上下部位氢损值差别最小。因为在高温还原过程中,既有复杂的固、气多相化学反应,又有氢还原氧化铁的动力学问题。还原温度在800℃以上,反应产物层不是疏松的,气体需要通过扩散到铁氧体内部才能参与反应,所以高温还原过程,温度高对反应速度有利,但高温团聚阻碍了还原气氛的扩散,对反应起到了抑制作
用。随着温度从945℃提高到965℃的过程,化学反应速度增快,粉饼的团聚逐步增强,在965℃时,反应达到最佳的效果。随着温度的继续提高,粉饼的团聚致密度越来越高,该过程扩散起到决定性作用。因此随着温度的提高,反应越来越不彻底,导致了氢损含量逐步提高,从而使压缩性逐步降低;同时,因过高的温度使粉饼团聚加剧,增加了粉饼的破碎难度,提高了加工硬化程度,降低产品压缩性。
[0137]
除非另有说明,本发明中所采用的百分数均为质量百分数。
[0138]
最后应说明的是:以上所述仅为本发明的优选实施例而已,并不用于限制本发明,尽管参照前述实施例对本发明进行了详细的说明,对于本领域的技术人员来说,其依然可以对前述各实施例所记载的技术方案进行修改,或者对其中部分技术特征进行等同替换。凡在本发明的精神和原则之内,所作的任何修改、等同替换、改进等,均应包含在本发明的保护范围之内。