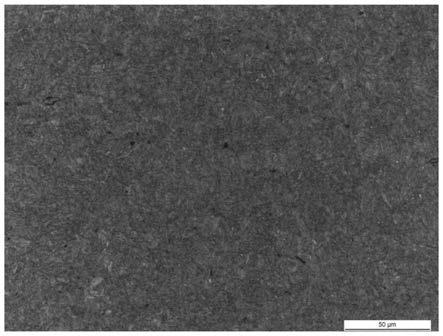
[0001]
本发明属于钢铁冶炼技术领域,具体涉及一种非焊接耐磨构件用钢及其制备方法。
背景技术:[0002]
传统工艺制备的耐磨钢广泛应用于工程机械、矿山煤矿等领域,其布氏硬度等级覆盖300~600。这类耐磨钢通常采用中低碳成分体系,碳含量一般小于0.5%,同时添加一定量的cr、mo等元素来提高材料的淬透性,并通过淬火+低温回火的工艺获得回火马氏体,以提高材料的硬度和耐磨性能。目前,耐磨钢的生产主要技术是将热轧钢板进行淬火+低温回火的工艺来获得回火马氏体组织,提高了材料的耐磨性能。
[0003]
中国专利201810675587.4公开了一种耐磨钢板及其制造方法,其中化学成分百分比为:c0.29~0.35%、si0.21~0.27%、mn0.82~0.88%、p0.005~0.010%、 s0.001~0.0015%、cr0.95~1.05%、mo0.12~0.18%、ni0.50%、al0.05%、 cu≤0.05%、nb≤0.005%、ti≤0.005%、v≤0.02%、b0.0015%,余量为fe和其他不可避免的杂质;该耐磨钢板中添加了大量的cr、ni、mo元素,其合金成本偏高。
[0004]
中国专利201911086164.x公开了一种耐磨钢板及其制备方法,其中化学成分百分比为:c0.05~0.12%、si0.10~0.50%、mn1.00~1.50%、p≤0.020%, s≤0.005%、nb0.015~0.025%、cr0.50~0.90%、ni0.08~0.25%,ti0.008~0.035%、 als0.015~0.040%、as≤0.04%、sn≤0.03%、n≤0.005%、o≤0.003%、h≤0.0002%,余量为fe和不可避免的杂质。该专利申请采用低c成分体系以及nb-cr-ni 复合添加,其在保证钢板具有足够的韧性的条件下提高了钢板的耐磨性能,但仍存在合金成本偏高的问题。
[0005]
中国专利201910124582.7公开了一种高强度耐磨钢,其中化学成分百分比为:c0.41~0.59%、si0.31~0.58%、mn7.1~8.9%、p≤0.018%、s≤0.01%、 ti0.25~0.35%,cr3.60~5.60%、zr0.10~0.30%,余量为fe和不可避免的杂质;该专利申请在高锰钢的基础上添加了3.6~5.6%的cr元素,进一步提高材料的耐磨性能,但同样存在合金成本偏高的问题。
[0006]
在耐磨钢生产的现有技术中,存在的主要问题为:由于成本偏高而影响了推广应用;在传统耐磨钢中,为了保证材料的可焊性,需要控制材料的c 含量和碳当量,同时通过加入大量合金元素来提高材料的耐磨性,因此成本过高。但是,在耐磨钢的实际使用过程中,有大量构件是不需要进行焊接的。
[0007]
因此,亟需一种具有良好耐磨性以及较低成本的非焊接用途的耐磨构件用钢的研究开发。
技术实现要素:[0008]
鉴于上述问题,本发明提供一种非焊接耐磨构件用钢及其制备方法。本发明提供的非焊接耐磨构件用钢在具有良好耐磨性能的同时,还具有成本得以显著降低的优势;所
述非焊接耐磨构件用钢可用于非焊接用途,可替代传统的普碳钢、低合金钢以及传统耐磨钢,能够延长非焊接用途耐磨构件的使用寿命。
[0009]
用于实现上述目的的技术方案如下:
[0010]
本发明提供一种非焊接耐磨构件用钢,其特征在于,按质量百分比计,所述非焊接耐磨构件用钢包含:c 0.95~1.25%,si 0.60~1.0%,mn 0.3~0.5%,p≤ 0.015%,s≤0.005%,al 0.015~0.06%,b 0.003~0.005%,ti 0.025~0.045%,v0.05~0.10%,nb 0.03~0.06%,余量为铁和不可避免的杂质。
[0011]
在一些优选实施方式中,本发明所述的非焊接耐磨构件用钢中,按质量百分比计,所述非焊接耐磨构件用钢包含:c 1.25%,si 0.60%,mn 0.3%,p0.009%,s 0.004%,al 0.052%,b 0.005%,ti 0.042%,v 0.09%,nb 0.052%,余量为铁和不可避免的杂质。
[0012]
在一些实施方式中,本发明所述的非焊接耐磨构件用钢中,所述非焊接耐磨构件用钢的微观组织包括回火后的马氏体和颗粒状渗碳体。通过控制马氏体形貌和颗粒状渗碳体的尺寸和分布,能够提高材料的耐磨性和韧性的良好匹配。
[0013]
在一些实施方式中,本发明所述的非焊接耐磨构件用钢中,所述非焊接耐磨构件用钢的厚度为1.5~12mm。
[0014]
本发明还提供本发明所述的非焊接耐磨构件用钢的制备方法,所述制备方法包括以下步骤:
[0015]
冶炼并连铸得到钢板坯,将所述钢板坯依次进行加热和热轧,得到热轧板;
[0016]
将所述热轧板依次进行空冷、卷取,得到钢卷;
[0017]
将所述钢卷依次进行开平矫直、横切、切割下料,得到钢板;
[0018]
将所述钢板依次进行淬火加热、油淬冷却、回火加热和冷却,得到所述非焊接耐磨构件用钢;
[0019]
其中,按质量百分比计,所述钢板坯包含:c 0.95~1.25%,si 0.60~1.0%, mn 0.3~0.5%,p≤0.015%,s≤0.005%,al 0.015~0.06%,b 0.003~0.005%, ti 0.025~0.045%,v 0.05~0.10%,nb 0.03~0.06%,余量为铁和不可避免的杂质。
[0020]
在一些优选实施方式中,本发明所述的非焊接耐磨构件用钢的制备方法中,按质量百分比计,所述钢板坯包含:c 1.25%,si 0.60%,mn 0.3%,p 0.009%, s 0.004%,al 0.052%,b 0.005%,ti 0.042%,v 0.09%,nb 0.052%,余量为铁和不可避免的杂质。
[0021]
在一些实施方式中,本发明所述的非焊接耐磨构件用钢的制备方法中,所述将所述钢板坯进行加热的过程中,所述加热温度为1240~1280℃,优选 1250℃。
[0022]
在一些实施方式中,本发明所述的非焊接耐磨构件用钢的制备方法中,所述热轧的过程中,精轧的开轧温度为1020~1080℃,精轧的终轧温度为 850~890℃;
[0023]
在一些优选实施方式中,本发明所述的非焊接耐磨构件用钢的制备方法中,所述热轧的过程中,所述精轧的开轧温度为1060℃,所述精轧的终轧温度为870℃。
[0024]
在一些实施方式中,本发明所述的非焊接耐磨构件用钢的制备方法中,粗轧的开轧温度为1100~1150℃,粗轧的终轧温度为1000~1100℃。
[0025]
在一些实施方式中,本发明所述的非焊接耐磨构件用钢的制备方法中,所述卷取的过程中,所述卷取温度为680~720℃,优选700℃。
[0026]
在一些实施方式中,本发明所述的非焊接耐磨构件用钢的制备方法中,所述将所
述钢板进行淬火加热的过程中,淬火加热温度为850~890℃,淬火保温时间为30~40min。
[0027]
在一些优选实施方式中,本发明所述的非焊接耐磨构件用钢的制备方法中,所述将所述钢板进行淬火加热的过程中,所述淬火加热温度为870℃,所述淬火保温时间为36min。
[0028]
在一些实施方式中,本发明所述的非焊接耐磨构件用钢的制备方法中,所述回火加热的过程中,回火加热温度为250~300℃,回火保温时间为60~90 min;
[0029]
在一些优选实施方式中,本发明所述的非焊接耐磨构件用钢的制备方法中,所述回火加热的过程中,回火加热温度为270℃,回火保温时间为90min。
[0030]
在一些实施方式中,本发明所述的非焊接耐磨构件用钢的制备方法中,所述非焊接耐磨构件用钢的厚度为1.5~12mm。
[0031]
在一些实施方式中,本发明所述的非焊接耐磨构件用钢的制备方法中,将所述热轧板进行空冷的过程中,采用后段冷却的方式。
[0032]
在一些实施方式中,本发明所述的非焊接耐磨构件用钢的制备方法中,将所述热轧板进行空冷的过程中,所述后段冷却包括:将所述热轧板出精轧轧机后首先进行空冷,然后将层流冷却水从最后一组向前开启。
[0033]
在一些实施方式中,本发明所述的非焊接耐磨构件用钢的制备方法中,所述切割下料的过程中,采用等离子切割或者激光切割(获得目标钢板形状)。
[0034]
在一些实施方式中,本发明所述的非焊接耐磨构件用钢的制备方法中,所述将所述钢卷依次进行开平矫直、横切、切割下料,得到钢板,包括:将所述钢卷进行开平矫直和横切,得到开平钢板;将所述开平钢板采用等离子切割或者激光切割进行下料(获得目标钢板形状),得到所述钢板。
[0035]
在一些实施方式中,本发明所述的非焊接耐磨构件用钢的制备方法中,所述淬火加热采用感应加热的方式。
[0036]
在一些实施方式中,本发明所述的非焊接耐磨构件用钢的制备方法中,所述油淬冷却包括:冷却至18~31℃。
[0037]
在一些优选实施方式中,本发明所述的非焊接耐磨构件用钢的制备方法中,淬火介质为油。
[0038]
在一些实施方式中,本发明所述的非焊接耐磨构件用钢的制备方法中,所述冷却包括:空冷或随炉冷却。
[0039]
本发明另外提供本发明所述的非焊接耐磨构件用钢的制备方法制备得到的非焊接耐磨构件用钢。
[0040]
本发明提供的非焊接耐磨构件用钢的成分体系设计思路主要体现在:
[0041]
c:相比于现有技术中耐磨钢的中低碳成分体系,本发明采用了较高含量的c含量,通过c元素在热处理过程中的作用来提高材料的耐磨性能。由于本发明提供的钢适用于非焊接耐磨构件,因此对c含量和碳当量无特定要求,可以通过提高c元素含量来大幅度降低合金成本。本发明配合其他合金元素添加量及热处理工艺的技术特点,基于上述。设计思路和大量优化选择试验,将c元素含量限定为0.95~1.25%,优选c1.25%。
[0042]
si:本发明采用较高含量的si,一方面通过添加si元素来提高材料的整体强度水平,同时有利于在热处理后使得材料获得一定比例的软相组织,提高材料的塑韧性。基于上
述设计思路和大量优化选择试验,将si元素含量限定为0.60~1.0%,优选si 0.60%。
[0043]
mn:锰为固溶强化元素,本发明为控制合金成本,采用较低的mn含量。由于已经采用了较高的c含量,而c和mn均为易于中心偏析元素,不易同时添加过高的c和mn。因此,基于上述设计思路和大量优化选择试验,将mn元素含量限定为0.3~0.5%,优选mn 0.3%。
[0044]
p:p为有害元素,在钢热处理中易于引发脆性,应尽量降低。本发明严格控制钢中p元素的含量,并将它与其他合金元素以及c元素进行合理配比,从而提高钢材料的综合性能。基于上述设计思路和大量优化选择试验,将p 元素含量限定为p≤0.015%,优选p 0.009%。
[0045]
s:s元素对钢材料性能易产生不利影响,本发明严格控制钢中s≤0.005%,优选s 0.004%,避免s出现回火脆性及形成mn的夹杂物造成韧性下降。
[0046]
al:al为脱氧元素,基于大量优化选择试验,将al元素含量限定为 0.015~0.06%,优选al 0.052%。
[0047]
b:添加b元素可以提高钢材料的淬透性,通过添加b来实现无须添加cr、mo等贵合金的目的,但过高含量的b会降低钢材料的塑韧性。基于大量优化选择试验,将b元素含量限定为0.003~0.005%,优选b 0.005%。
[0048]
ti:本发明通过添加少量的ti来形成tin或tic,起到在细化奥氏体晶粒的作用的同时还提高钢材料的强度。基于大量优化选择试验,将ti元素含量限定为0.025~0.045%,优选ti 0.042%。
[0049]
nb:本发明通过添加少量的nb元素,并依靠nb的c化物、n化物析出,钉扎晶界,从而提高材料的强度和硬度。基于大量优化选择试验,将 nb元素含量限定为0.03~0.06%,优选nb 0.052%。
[0050]
v:v元素为析出强化元素,同时还可以提高钢材料的强度和硬度。本发明通过添加较高含量的v元素,可以在钢的热轧状态下获得大量的v析出物,而部分v析出物可细化热处理组织,并保留至最终产品中,从而提高钢材料的强度和硬度水平。基于大量优化选择试验,将v元素含量限定为 0.05~0.10%,优选v 0.09%。
[0051]
本发明所述的一个或多个技术实施方案,至少具有如下技术效果或优点:
[0052]
(1)本发明提供的非焊接耐磨构件用钢,采用高c含量、高si含量和低mn含量的成分体系,同时添加b元素来提高钢的淬透性;此外,通过添加一定量的nb、v和ti元素,来提高钢的综合力学性能。
[0053]
(2)本发明提供的非焊接耐磨构件用钢的厚度为1.5~12mm,抗拉强度大于1610mpa,布氏硬度大于471,-20℃冲击功大于54j。
[0054]
(3)本发明提供的非焊接耐磨构件用钢的耐磨性能达到编号为345b钢的2.84倍以上,可用于非焊接用途,可替代传统的普碳钢、低合金钢以及传统耐磨钢,能够延长非焊接用途耐磨构件的使用寿命。
[0055]
(4)本发明提供的非焊接耐磨构件用钢的制备方法中,采用了全流程组织控制技术,在轧制阶段通过控制加热、粗轧、精轧和卷取的温度,控制钢的晶粒尺寸,从而获得了细小均匀、高耐磨性的非焊接耐磨构件用钢,同时具备成本较低的优势。
[0056]
(5)本发明提供的非焊接耐磨构件用钢的制备方法中,控制热轧阶段的的温度区间,获得良好板形质量和细小均匀的热轧板;此外采用适当的回火加热工艺,以保证得到耐
磨性和韧性匹配的耐磨构件用钢。
[0057]
(6)本发明提供的非焊接耐磨构件用钢的组织由回火后的马氏体及颗粒状渗碳体组成。本发明采用了较低的回火温度250~300℃,故保留了大部分马氏体板条的形貌,从而使得钢材料的耐磨性大幅提升。此外,本发明通过添加nb、v和ti元素并匹配最佳生产工艺,从而控制了渗碳体组织的形貌,使得最终产品具有良好的韧性。
附图说明
[0058]
为了更清楚地说明本发明实施例中的技术方案,下面将对实施例描述中所需要使用的附图作一简单地介绍,显而易见地,下面描述中的附图是本发明的一些实施例,对于本领域普通技术人员来讲,在不付出创造性劳动的前提下,还可以根据这些附图获得其它的附图。
[0059]
图1示出了本发明实施例4制备的非焊接耐磨构件用钢的金相照片。
具体实施方式
[0060]
下文将结合具体实施方式和实施例,具体阐述本发明,本发明的优点和各种效果将由此更加清楚地呈现。本领域技术人员应理解,这些具体实施方式和实施例是用于说明本发明,而非限制本发明。
[0061]
在整个说明书中,除非另有特别说明,本文使用的术语应理解为如本领域中通常所使用的含义。因此,除非另有定义,本文使用的所有技术和科学术语具有与本发明所属领域技术人员的一般理解相同的含义。若存在矛盾,本说明书优先。
[0062]
除非另有特别说明,本发明中用到的各种原材料、试剂、仪器和设备等,均可通过市场购买得到或者可通过现有方法制备得到。
[0063]
本发明实施例提供的技术方案为解决上述技术问题,总体思路如下:
[0064]
本发明提供一种非焊接耐磨构件用钢,其特征在于,按质量百分比计,所述非焊接耐磨构件用钢包含:c 0.95~1.25%,si 0.60~1.0%,mn0.3~0.5%,p ≤0.015%,s≤0.005%,al 0.015~0.06%,b 0.003~0.005%,ti0.025~0.045%,v0.05~0.10%,nb0.03~0.06%,余量为铁和不可避免的杂质。
[0065]
本发明提供的非焊接耐磨构件用钢中,采用高c含量、高si含量和低 mn含量的成分体系,同时添加b元素来提高钢的淬透性;此外,通过添加一定量的nb、v和ti元素,来提高钢的综合力学性能。
[0066]
在一些优选实施方式中,本发明所述的非焊接耐磨构件用钢中,按质量百分比计,所述非焊接耐磨构件用钢包含:c 1.25%,si 0.60%,mn0.3%,p 0.009%,s 0.004%,al 0.052%,b 0.005%,ti 0.042%,v 0.09%,nb 0.052%,余量为铁和不可避免的杂质。
[0067]
本发明对上述合金元素的添加用量进行了进一步的筛选和优化,使得本发明获得的高密度钢的综合性能得到显著改善并达到最佳匹配,明显降低了合金成本。
[0068]
为了获得提高钢的强度、淬透性和耐磨性,本发明采用高c含量、高 si含量和低mn含量的成分体系,并对各个元素的添加用量进行了进一步筛选和优化,获得了具有最佳晶粒尺寸的非焊接耐磨构件用钢,使得组织均匀性和力学性能显著提高。
[0069]
在一些实施方式中,本发明所述的非焊接耐磨构件用钢中,所述非焊接耐磨构件
用钢的厚度为1.5~12mm。
[0070]
本发明还提供本发明所述的非焊接耐磨构件用钢的制备方法,所述制备方法包括以下步骤:
[0071]
冶炼并连铸得到钢板坯,将所述钢板坯依次进行加热和热轧,得到热轧板;
[0072]
将所述热轧板依次进行空冷、卷取,得到钢卷;
[0073]
将所述钢卷依次进行开平矫直、横切、切割下料,得到钢板;
[0074]
将所述钢板依次进行淬火加热、油淬冷却、回火加热和冷却,得到所述非焊接耐磨构件用钢;
[0075]
其中,按质量百分比计,所述钢板坯包含:c 0.95~1.25%,si 0.60~1.0%, mn 0.3~0.5%,p≤0.015%,s≤0.005%,al 0.015~0.06%,b 0.003~0.005%,ti 0.025~0.045%,v 0.05~0.10%,nb 0.03~0.06%,余量为铁和不可避免的杂质;
[0076]
在一些优选实施方式中,本发明所述的非焊接耐磨构件用钢的制备方法中,按质量百分比计,所述钢板坯包含:c 1.25%,si 0.60%,mn 0.3%,p 0.009%, s 0.004%,al 0.052%,b 0.005%,ti 0.042%,v 0.09%,nb 0.052%,余量为铁和不可避免的杂质。
[0077]
在一些实施方式中,本发明所述的非焊接耐磨构件用钢的制备方法中,所述将所述钢板坯进行加热的过程中,所述加热温度为1240~1280℃,优选 1250℃。
[0078]
本发明所述的非焊接耐磨构件用钢的制备方法中,选择了加热温度为1240~1280℃,优选1250℃;其中,如果加热温度低于1240℃,则合金元素的析出物将无法充分回溶,会降低最终产品的强度和耐磨性;如果加热温度高于1280℃,则晶粒过于粗大,将遗传至后续工序,最终会降低钢材料的性能,并且还不利于降低最终产品的强度和耐磨性。
[0079]
在一些实施方式中,本发明所述的非焊接耐磨构件用钢的制备方法中,所述热轧的过程中,精轧的开轧温度为1020~1080℃,精轧的终轧温度为 850~890℃。
[0080]
发明人经过大量实验发现,如果精轧开轧温度低于1020℃,则会增加轧制力,不利于热连轧的顺利进行和带钢尺寸、板形的控制;如果精轧的开轧温度高于1080℃,则会造成晶粒粗大,不利于最终产品的组织细化;此外,如果终轧温度低于850℃,则会增加轧制力,并不利于进行板形控制;如果如果终轧温度高于890℃,则会造成组织粗大,从而降低最终产品的强韧性。
[0081]
本发明所述的非焊接耐磨构件用钢的制备方法中,优化选择了精轧的开轧温度和精轧的终轧温度,以保证轧制的连贯性,提高生产效率,同时降低轧制负荷,节约能源。
[0082]
在一些优选实施方式中,本发明所述的非焊接耐磨构件用钢的制备方法中,所述热轧的过程中,所述精轧的开轧温度为1060℃,所述精轧的终轧温度为870℃。
[0083]
在一些实施方式中,本发明所述的非焊接耐磨构件用钢的制备方法中,粗轧的开轧温度为1100~1150℃,粗轧的终轧温度为1000~1100℃;
[0084]
本发明所述钢板坯在热轧过程中,对于粗轧温度和精轧温度的控制精度,将直接影响最终产品的组织性能和综合性能。发明人针对发明目的,在各个合金元素及其含量的设计构思的基础之上,进一步优化选择最适用的制备工艺参数,特别是限定了粗轧的终轧温度和精轧的终轧温度的优化范围,显著提高了所述非焊接耐磨构件用钢的组织均匀性,有效降低了钢板坯的氧化程度以及细化了奥氏体晶粒。
[0085]
在一些实施方式中,本发明所述的非焊接耐磨构件用钢的制备方法中,所述卷取
的过程中,所述卷取温度为680~720℃,优选700℃。
[0086]
在所述卷取的过程中,如果卷曲温度低于680℃,会造成基料的强度提高,不利于后续工序的加工;如果卷曲温度高于720℃,则会造成扁卷现象,并使得最终产品的性能偏低。
[0087]
本发明采用卷取温度为680~720℃并优选700℃的目的为保证热轧钢的板形以及降低残余应力。
[0088]
在一些实施方式中,本发明所述的非焊接耐磨构件用钢的制备方法中,所述将所述钢板进行淬火加热的过程中,淬火加热温度为850~890℃,淬火保温时间为30~40min。
[0089]
本发明采用淬火加热温度为850~890℃,可以保证钢材料充分奥氏体化,能够提高材料性能指标;同时,还可以避免部分奥氏体晶粒的异常长大,避免强度指标的下降,有助于改善钢经过热处理后性能降低的缺陷。采用淬火保温时间为30~40min的目的是使得奥氏体化过程充分进行,并形成大小较为均匀的奥氏体晶粒。
[0090]
在一些优选实施方式中,本发明所述的非焊接耐磨构件用钢的制备方法中,所述将所述钢板进行淬火加热的过程中,所述淬火加热温度为870℃,所述淬火保温时间为36min。
[0091]
在一些实施方式中,本发明所述的非焊接耐磨构件用钢的制备方法中,所述回火加热的过程中,回火加热温度为250~300℃,回火保温时间为60~90 min。
[0092]
在一些优选实施方式中,本发明所述的非焊接耐磨构件用钢的制备方法中,所述回火加热的过程中,回火加热温度为270℃,回火保温时间为90min。
[0093]
本发明的核心技术方案除了钢的成分设计外,还设定了准确的回火温度范围区间,采用回火加热温度为250~300℃并优选270℃,使得钢材料的韧性进一步提高,并且有效控制了渗碳体形貌,从而保证钢材料具有高的耐磨性;其中,如果回火加热温度低于250℃,则钢材料的韧性大幅下降,并在后续使用过程中易于出现脆裂现象;如果回火加热温度高于300℃,则钢材料的强度和硬度大幅下降,耐磨性降低。此外通过采用回火保温时间为60~90min并优选 90min,从而使得钢的塑韧性和综合性能得到显著改善。
[0094]
在一些实施方式中,本发明所述的非焊接耐磨构件用钢的制备方法中,所述非焊接耐磨构件用钢的厚度为1.5~12mm。
[0095]
在一些实施方式中,本发明所述的非焊接耐磨构件用钢的制备方法中,将所述热轧板进行空冷的过程中,采用后段冷却的方式。该技术方案中,将所述热轧板进行空冷的过程中,采用后段冷却的方式,一方面有利于控制带钢板形和残余应力,同时还可以精准地控制卷取的温度,并避免通卷性能波动过大。
[0096]
在一些实施方式中,本发明所述的非焊接耐磨构件用钢的制备方法中,将所述热轧板进行空冷的过程中,所述后段冷却包括:将所述热轧板出精轧轧机后首先进行空冷,然后将层流冷却水从最后一组向前开启。
[0097]
在一些实施方式中,本发明所述的非焊接耐磨构件用钢的制备方法中,所述切割下料的过程中,采用等离子切割或者激光切割,能够避免由于切割热量所导致的变形和附加残余应力(获得目标形状)。
[0098]
在一些实施方式中,本发明所述的非焊接耐磨构件用钢的制备方法中,所述将所述钢卷依次进行开平矫直、横切、切割下料,得到钢板,包括:将所述钢卷进行开平矫直和横
实施例51.180.860.450.0100.0030.0390.0580.100.0400.0050 实施例60.951.00.500.0110.0020.0400.0330.0760.0250.0045 实施例71.080.930.330.0090.0030.0490.0370.0660.0280.0039 实施例81.100.770.320.0120.0020.0520.0460.0530.0330.0046 对比例10.170.211.120.0140.0090.025
ꢀꢀꢀ-ꢀ
对比例20.200.301.150.0100.0020.038
ꢀꢀ
0.0250.00200.60
[0118]
表2:本发明实施例1~8以及对比例1~2的制备工艺参数
[0119][0120]
表3:本发明实施例1~8以及对比例1~2的制备工艺参数
[0121][0122]
针对上述本发明实施例1~8以及对比例1~2制备得到的非焊接耐磨构件用钢分别进行力学性能测试,其比较结果见表4:
[0123]
表4:力学性能测试结果
[0124][0125]
对上述本发明实施例1~8以及对比例1~2制备得到的非焊接耐磨构件用钢进行耐磨性能测试试验。试验方法为:冲击载荷10kg,磨料材质为石英砂,砂流量为30kg/h,冲击时间为90分钟;测量本发明实施例1~8以及对比例 1~2制备得到的非焊接耐磨构件用钢的试样重量,得到失重量表征材料的耐磨性能。试验结果见表5:
[0126]
表5:本发明实施例1~8以及对比例1~2所得产品的耐磨性试验结果
[0127]
序号90min失重/gq355b1.211实施例10.412实施例20.404实施例30.425实施例40.387实施例50.394实施例60.411实施例70.409实施例80.399对比例11.228对比例20.743
[0128]
从表1~5可以看出:本发明实施例1~8通过特定的化学成分设计和合理的生产工艺设计,得到具有低成本高耐磨性的非焊接用途构件用钢。本发明所述制备方法制备得到的非焊接耐磨构件用钢的厚度为1.5~12mm,抗拉强度大于1610mpa,布氏硬度大于471,-20℃冲击功大于54j,耐磨性能达到编号为345b钢的2.84倍以上。
[0129]
而对比例1~2钢材试验结果显示,q355b的耐磨性与本发明实施例1~8 有较大差距;对比例1~2显示,普通耐磨钢的耐磨性与本发明实施例1~8 也有明显差距。
[0130]
实施例9:本发明所述制备方法中的回火加热温度工艺优化实验
[0131]
考察本发明非焊接耐磨构件用钢的回火加热温度对钢材料的耐磨性和韧性的影响:
[0132]
方法1:按照本发明实施例4所示步骤进行操作,不同之处在于,其中回火加热温度为150℃,回火保温时间为60min。
[0133]
方法2:按照本发明实施例4所示步骤进行操作,不同之处在于,其中回火加热温度为320℃,回火保温时间为120min。
[0134]
方法3:按照本发明实施例4所示步骤进行操作,不同之处在于,其中回火加热温度为230℃,回火保温时间为30min。
[0135]
方法4:按照本发明实施例4所示步骤进行操作,不同之处在于,其中回火加热温度为350℃,回火保温时间为100min。
[0136]
方法5:本发明实施例4;
[0137]
方法6:本发明实施例6;
[0138]
方法7:本发明实施例8;
[0139]
考察结果见表6。
[0140]
表6:本发明中回火加热温度对钢材料的耐磨性和韧性的影响
[0141]
考察项目方法1方法2方法3方法4方法5方法6方法790min失重/g0.3970.9070.4010.98670.4120.4040.387布氏硬度471307479256506471497韧性(-20℃冲击功)17423468766361
[0142]
比较方法1-7可以看出:通过以上7种回火加热温度和保温时间的筛选,发现方法1至4所得到的钢材料耐磨性和韧性均不理想。而方法5至7得到的非焊接耐磨构件用钢的耐磨性和韧性得到显著提升。
[0143]
经过上述筛选试验,本发明最终确定了回火加热温度为250~300℃,回火保温时间为60~90min;并优选回火加热温度为270℃,回火保温时间为90min;从而得到了耐磨性和韧性得到显著提升的非焊接耐磨构件用钢,实现了良好的技术效果。
[0144]
图1为本发明实施例4制备得到的非焊接耐磨构件用钢的金相照片。所得非焊接耐磨构件用钢的组织由回火后的马氏体及颗粒状渗碳体组成。本发明采用了较低的回火温度250~300℃,故保留了大部分马氏体板条的形貌,从而使得钢材料的耐磨性大幅提升。此外,本发明通过添加nb、v和 ti元素并匹配最佳生产工艺,从而控制了渗碳体组织的形貌,使得最终产品具有良好的韧性。
[0145]
最后,还需要说明的是,术语“包括”、“包含”或者其任何其他变体意在涵盖非排他性的包含,从而使得包括一系列要素的过程、方法、物品或者设备不仅包括那些要素,而且还包括没有明确列出的其他要素,或者是还包括为这种过程、方法、物品或者设备所固有的要素。
[0146]
尽管已描述了本发明的优选实施例,但本领域内的技术人员一旦得知了基本创造性概念,则可对这些实施例作出另外的变更和修改。所以,所附权利要求意欲解释为包括优选实施例以及落入本发明范围的所有变更和修改。
[0147]
显然,本领域的技术人员可以对本发明进行各种改动和变型而不脱离本发明的精神和范围。这样,倘若本发明的这些修改和变型属于本发明权利要求及其等同技术的范围
之内,则本发明也意图包含这些改动和变型在内。