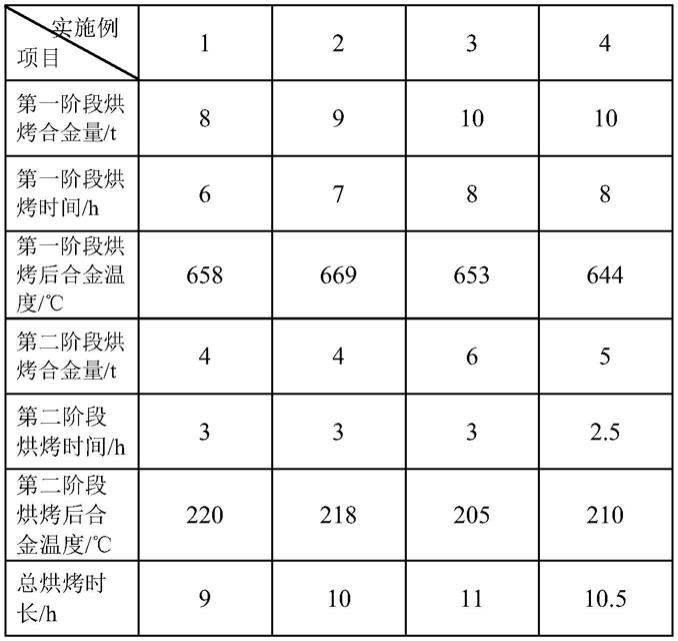
1.本发明属于冶金技术领域,尤其涉及一种钢包余热的利用方法。
背景技术:2.钢包是冶金工业中储存、转运钢水的重要容器件,其结构由钢壳和内衬构成,其中钢包内衬包含工作层、保温层和永久层。钢包的使用过程中循环经历空包接钢水、装钢水、浇铸钢水等流程,钢包内衬也在周期性地受到高温钢水的冲刷和侵蚀,当钢包内衬到达使用寿命时,必须及时更换,否则会造成钢水的渗透,严重的会导致穿包,造成重大的安全事故。
3.达到使用寿命的钢包在拆除内衬前,由于内部温度过高,需要静置24-36小时,待自然冷却后再进行拆除,该静置过程会延长钢包的修砌周期,钢包内衬所蕴含的热量资源也无法得到有效利用,白白浪费。
技术实现要素:4.针对现有技术中达到使用寿命的钢包更换内衬前静置冷却时间长且浪费热量资源的技术问题,本发明提供一种钢包余热的利用方法。
5.为达到上述发明目的,本发明实施例采用了如下的技术方案:
6.一种钢包余热的利用方法,利用钢包余热烘烤合金,该方法至少包括以下步骤:
7.a、将待烘烤的合金转移至钢包内,盖好钢包包盖进行第一阶段烘烤,待合金温度≥600℃后,将合金倒出钢包;
8.b、立即加入新的待烘烤的合金,盖好包盖进行第二阶段烘烤,待合金温度与炉内温度一致后结束。
9.相对于现有技术而言,本发明中的钢包可选用达到使用寿命的钢包,通过利用钢包余热分段烘烤合金,可实现钢包内热量的有效回收,提高了资源利用率,同时加速了钢包的冷却,缩短了钢包的修砌周期。
10.优选在烘烤前将钢包转移至合金料仓上料口附近,便于用天车向钢包内加入待烘烤的合金,提高烘烤效率,减少烘烤合金的运输流程及时间,提高热力资源的回收率,节省人力及设备费用。
11.优选地,步骤a烘烤前的钢包内部温度1300~1500℃。
12.优选地,步骤a中,所述待烘烤的合金质量≤钢包公称容量的10%,烘烤时间为6~8小时。
13.优选的初始温度,烘烤质量和烘烤时间可以保证第一阶段烘烤结束后合金温度达到600℃以上,有效去除烘烤合金中的游离水跟结晶水,又不至于过度烘烤浪费热量。
14.优选地,步骤a中,第一烘烤阶段烘烤结束后,倒出钢包的合金并在合金专用料斗中冷却。
15.优选地,步骤a中所述冷却的方式为:在相对湿度≤40%的环境中冷却3~4小时,
再将所述合金转移至地下料仓冷却至室温。
16.优选的冷却环境及冷却方式,可以保证合金在冷却过程中的稳定性,又不会损坏物料转运设备。
17.优选地,步骤b中,第一阶段的烘烤合金倒出后,倒入第二阶段待烘烤的合金,第二阶段烘烤的合金质量≤钢包公称容量的5%。
18.优选的第二段烘烤合金质量可以保证第二烘烤阶段结束后合金温度≥200℃,有效去除烘烤合金中的游离水,在有效回收热量的同时加速钢包降温。
19.第二段烘烤结束的合金可转移至烘烤炉内继续烘烤。
具体实施方式
20.为了使本发明的目的、技术方案及优点更加清楚明白,以下结合具体实施例,对本发明进行进一步详细说明。应当理解,此处所描述的具体实施例仅仅用以解释本发明,并不用于限定本发明。
21.实施例1
22.本实施例提供了一种利用钢包余热烘烤合金的方法,具体包括以下步骤:
23.将公称容量为120吨的达到使用寿命的钢包转移至合金料仓上料口附近,烘烤前测量钢包内部温度为1300℃。
24.步骤a、将8吨待烘烤的合金转移至钢包中,盖好包盖烘烤6小时后倒出钢包;
25.烘烤结束后的合金从钢包倒出后转移至合金专用料斗中,测量温度后在相对湿度为35%的常温环境中冷却4小时,再将合金转移至地下料仓中冷却至室温。
26.步骤b、步骤a中烘烤后的合金倒出后,立即加入新的待烘烤的硅锰合金,盖好包盖烘烤至合金温度与炉内温度一致后结束。烘烤结束后将合金转移至烘烤炉内继续烘烤,钢包进一步冷却后拆除并更换内衬。
27.实施例2
28.本实施例提供了一种利用钢包余热烘烤合金的方法,具体包括以下步骤:
29.将公称容量为120吨的达到使用寿命的钢包转移至合金料仓上料口附近,烘烤前测量钢包内部温度为1450℃。
30.步骤a、将9吨待烘烤的硅锰合金转移至钢包中,盖好包盖烘烤7小时后倒出钢包;
31.烘烤结束后的合金从用钢包倒出后转移至合金专用料斗,测量温度后在相对湿度为35%的常温环境中冷却4小时,再将合金转移至地下料仓中冷却至室温。
32.步骤b、步骤a中烘烤后的合金倒出后,立即向钢包内加入4吨待烘烤的硅锰合金,盖好包盖烘烤至合金温度与炉内温度一致后结束。烘烤结束后将合金转移至烘烤炉内继续烘烤,钢包进一步冷却后拆除并更换内衬。
33.实施例3
34.本实施例提供了一种利用钢包余热烘烤合金的方法,具体包括以下步骤:
35.将公称容量为120吨的达到使用寿命的钢包转移至合金料仓上料口附近,烘烤前测量钢包内部温度为1500℃。
36.步骤a、将10吨待烘烤的硅锰合金转移至钢包中,盖好包盖烘烤8小时后倒出钢包;
37.烘烤结束后的合金从用钢包倒出后转移至合金专用料斗,测量温度后在相对湿度
为40%的常温环境中冷却3小时,再将合金转移至地下料仓中冷却至室温。
38.步骤b、步骤a中烘烤后的合金倒出后,立即向钢包内加入6吨待烘烤的硅锰合金,盖好包盖烘烤至合金温度与炉内温度一致后结束。烘烤结束后将合金转移至烘烤炉内继续烘烤,钢包进一步冷却后拆除并更换内衬。
39.实施例4
40.本实施例提供了一种利用钢包余热烘烤合金的方法,具体包括以下步骤:
41.将公称容量为120吨的钢包转移至合金料仓上料口附近,烘烤前测量钢包内部温度为1500℃。
42.步骤a、将9吨待烘烤的硅锰合金转移至钢包中,盖好包盖烘烤8小时后倒出钢包;
43.烘烤结束后的合金从用钢包倒出后转移至合金专用料斗,测量温度后在相对湿度为35%的常温环境中冷却3小时,再将合金转移至地下料仓中冷却至室温。
44.步骤b、步骤a中烘烤后的合金倒出后,立即向钢包内加入5吨待烘烤的硅锰合金,盖好包盖烘烤至合金温度与炉内温度一致后结束。烘烤结束后将合金转移至烘烤炉内继续烘烤,钢包进一步冷却后拆除并更换内衬。
45.效果例
46.各实施例所达到的烘烤后温度如表1所示。
47.表1实施效果
[0048][0049]
由表1中的实施效果可见,本发明实施例得到的经第一阶段烘烤后的合金温度大于600℃,有效地去除了合金中的游离水和结合水,达到了合金烘烤标准,第二阶段烘烤后的合金温度大于200℃,有效地去除了合金中的游离水,钢包的余热得到了有效地回收,并且在12小时内将钢包降温至200℃左右,缩短了钢包的修砌周期。
[0050]
以上所述仅为本发明的较佳实施例而已,并不用以限制本发明,凡在本发明的精神和原则之内所作的任何修改、等同替换或改进等,均应包含在本发明的保护范围之内。