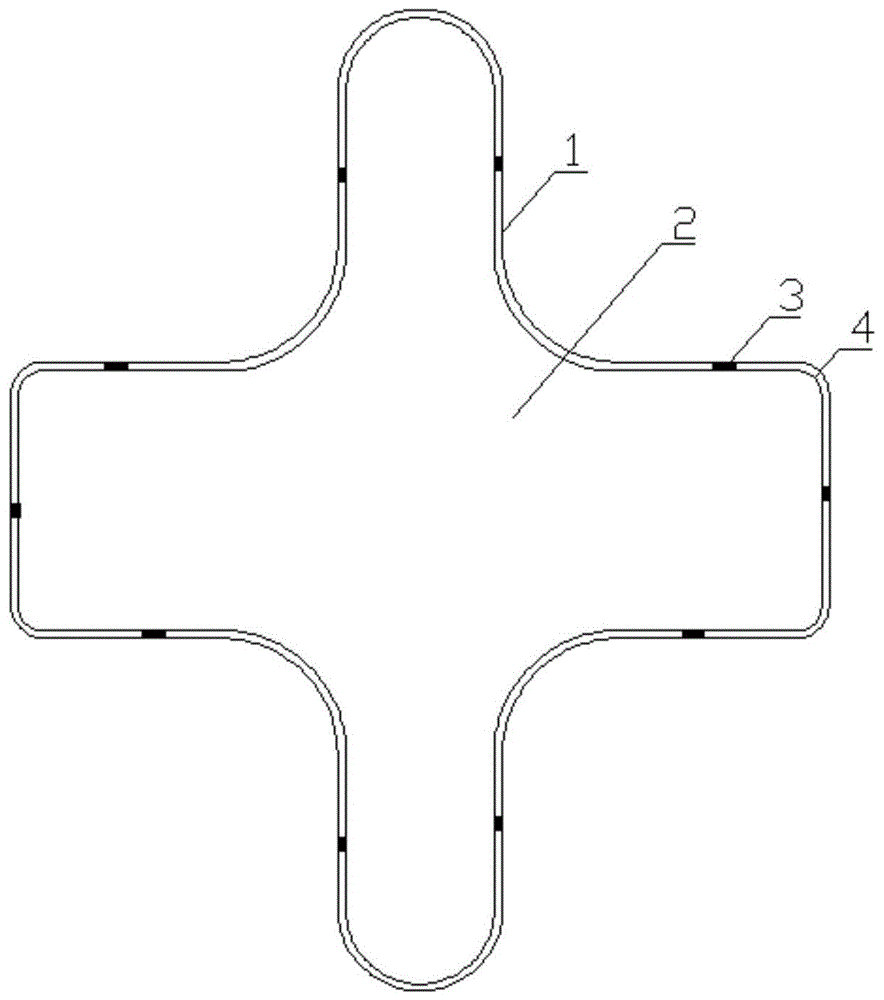
本发明属于铝合金铸造
技术领域:
,具体涉及一种铝合金铸件的多区合金化强化制备方法。
背景技术:
:随着以航空、航天等为代表的高
技术领域:
的快速发展,对铸造铝合金铸件提出了更高的要求。为满足这种高性能要求,一是采用设置粗大的加强筋来实现高性能,但这势必会增大铸件的重量;二是通过高合金化来实现高性能,但高合金化材料的铸造工艺性能低,出现充不满等铸造缺陷。因此,如何在不增加铸件重量且不降低铸造性能的基础上,实现铸件性能的大幅提升是急需解决的关键问题。此外,文献cn101130210a公开的强化铝合金表面的方法,包括下列步骤:a.将含有碳纤维粉和硬质材料的涂敷料涂敷在铸型的表面,使涂层干燥,保持铸型温度为室温到300℃;b.将液态铝合金注入铸型,在外加旋转磁场作用下进行冷却凝固,凝固结束后铝合金铸件的表面形成了一层含有碳纤维粉的铝合金基复合材料。然而,该方法本质上属于外置颗粒强化方式,并不能同时提升铝合金铸件的强度和断后伸长率。技术实现要素:本发明目的在于提供一种铝合金铸件的多区合金化强化制备方法,以实现在不增加铸件重量且不降低铸造性能的基础上,实现铸件性能的提升。本发明目的是采用如下技术方案实现的。一种铝合金铸件的多区合金化强化制备方法,其特征在于:它是将薄壁合金孔板熔铸在铝合金铸件表层,所述薄壁合金孔板的壁厚不大于0.5mm,所述薄壁合金孔板的孔径不大于8mm,所述薄壁合金孔板上相邻孔的孔边距介于5mm~10mm之间。作为优选方案,所述薄壁合金孔板的成分为al-20wt.%cu。作为优选方案,熔铸充型前,所述薄壁合金孔板与铸型内腔壁面的距离控制为1mm~3mm。作为优选方案,所述薄壁合金孔板上的孔为呈规则布置的矩形孔、圆形孔或三角孔。为进一步提升铝合金铸件本体性能,所述方法的步骤包括:步骤1,制备al-20wt.%cu铸锭;步骤2,将所得铸锭轧制成厚度为0.4mm~0.5mm的薄板;步骤3,将所得薄板进行冲孔,制得薄壁合金孔板;步骤4,对所得薄壁合金孔板进行表面预处理除油除污,然后将薄壁合金孔板嵌入铸型内腔,薄壁合金孔板通过导线外接低压电加热电源,再将整个铸型置于石棉橡胶板上后放置于真空罐内;步骤5,先对真空罐进行抽真空,真空度控制为-0.06mpa~-0.09mpa,然后开启低压电加热电源对薄壁合金孔板进行加热,加热温度控制为500℃~600℃;步骤6,待薄壁合金孔板温度稳定后,关闭低压电加热电源,并立即进行熔体充型;步骤7,充型完成后,对真空罐内进行加压凝固,压力控制为0.4mpa~0.6mpa,保压10min;充型完成后,在加压的同时再次开启低压电加热电源,控制加热温度为450℃~540℃,保温30min;步骤9,按照铸件基体合金要求进行后续热处理。为更进一步提升铝合金铸件本体性能,步骤4中,采用2-3层薄壁合金孔板嵌入铸型内腔,相邻薄壁合金孔板的间距为3mm,相邻薄壁合金孔板采用铝合金支点固结在一起;首层薄壁合金孔板与铸型内腔壁面的距离控制为2mm。有益效果:采用本发明提供的方法,在不增加铸件重量且不降低铸造性能的基础上能够实现铸件性能的大幅提升,不仅具有优异的铸造工艺性能,而且能够增强基体与增强体之间的结合力,使合金化元素可充分扩散,增大了合金化元素的固溶度,还能够防止氧化物被引入铸件中;采用本发明提供的方法,不仅能够在浇注熔体时使镁合金丝材快速熔化,确保合金元素均匀分布在铸件表层,而且能够使合金元素充分扩散,充分融入基体中;本发明提供的方法实施过程简单,成本低,适用于大规模工业生产;采用本发明制备的铝合金铸件本体性能优异,相比于涂层强化、加强筋强化方式得到的铝合金铸件本体性能更优。附图说明图1是实施例1中熔体充型前的薄壁合金孔板在铸型内的布局示意图;图2是实施例1中薄壁合金孔板的局部示意图;图3是实施例2中熔体充型前的薄壁合金孔板在铸型内的布局示意图;图4是实施例2中两张薄壁合金孔板叠拼固定状态局部示意图;图5是实施例2中薄壁合金孔板的局部示意图。图中,1-铸型内壁、2-铸型内腔、3-铸型内壁与薄壁合金孔板的固定点、4-薄壁合金孔板、41-首层薄壁合金孔板、42-内层薄壁合金孔板、43-首层薄壁合金孔板与内层薄壁合金孔板之间的固结点、5-薄壁合金孔板上的孔。具体实施方式下面结合附图和实施例对本发明作进一步说明,但以下实施例的说明只是用于帮助理解本发明的原理及其核心思想,并非对本发明保护范围的限定。应当指出,对于本
技术领域:
普通技术人员来说,在不脱离本发明原理的前提下,针对方案进行的改进也落入本发明权利要求的保护范围内。实施例1铸件材料为zl205,铸件高度为485mm,铸件最大轮廓直径567mm,铸件转角部位呈弧形,薄壁合金孔板材为al-20wt.%cu,该铸件的制备方法如下:步骤1,制备al-20wt.%cu铸锭;步骤2,将所得铸锭轧制成厚度为0.5mm的薄板;步骤3,将所得薄板进行冲圆孔,制得薄壁合金孔板,其中,薄壁合金孔板的孔径为8mm,相邻孔的孔边距为10mm(指的是相邻孔之间的最短孔边距),如图2所示;步骤4,对所得薄壁合金孔板进行表面预处理除油除污,然后将薄壁合金孔板嵌入铸型内腔并固定,如图1所示,固定好的薄壁合金孔板与铸型内腔形状基本一致,薄壁合金孔板与铸型内腔壁面的距离控制为2mm,薄壁合金孔板通过导线外接低压电加热电源,再将整个铸型置于石棉橡胶板上后放置于真空罐内;步骤5,先对真空罐进行抽真空,真空度控制为-0.06mpa,然后开启低压电加热电源对薄壁合金孔板进行加热,加热温度控制为580℃;步骤6,待薄壁合金孔板温度稳定后,关闭低压电加热电源,并立即进行熔体充型;步骤7,充型完成后,对真空罐内进行加压凝固,压力控制为0.4mpa,保压10min;充型完成后,在加压的同时再次开启低压电加热电源,控制加热温度为540℃,保温30min;步骤9,按照铸件基体合金要求进行后续固溶处理和时效处理,固溶参数为535℃/18h,时效参数为172℃/8h。对比实施例1铸件材料为zl205,铸件高度为485mm,铸件最大轮廓直径567mm,铸件转角部位呈弧形,该铸件的制备方法如下:步骤1,先对真空罐进行抽真空,真空度控制为-0.06mpa;步骤2,进行熔体充型;步骤3,充型完成后,对真空罐内进行加压凝固,压力控制为0.4mpa,保压10min;步骤4,按照铸件基体合金要求进行后续固溶处理和时效处理,固溶参数为535℃/18h,时效参数为172℃/8h。实施例2铸件材料为zl114,铸件高度为670mm,铸件最大轮廓直径427mm,铸件转角部位呈弧形,该铸件的制备方法如下:步骤1,制备al-20wt.%cu铸锭;步骤2,将所得铸锭轧制成厚度为0.4mm的薄板;步骤3,先将所得薄板进行冲矩形孔,制得薄壁合金孔板,其中,如图5所示,薄壁合金孔板的孔规格为5mm*5mm,相邻孔的孔边距为5mm;然后将两张薄壁合金孔板叠拼固定,两张薄壁合金孔板的间距控制为3mm,具体可以在薄壁合金孔板孔中插入铝合金柱节,然后加热熔化后冷却固定;步骤4,对所得薄壁合金孔板进行表面预处理除油除污,然后将薄壁合金孔板嵌入铸型内腔并固定,如图3和图4所示,固定好的薄壁合金孔板与铸型内腔形状基本一致,首层薄壁合金孔板与铸型内腔壁面的距离控制为2mm,薄壁合金孔板通过导线外接低压电加热电源,再将整个铸型置于石棉橡胶板上后放置于真空罐内;步骤5,先对真空罐进行抽真空,真空度控制为-0.09mpa,然后开启低压电加热电源对薄壁合金孔板进行加热,加热温度控制为500℃;步骤6,待薄壁合金孔板温度稳定后,关闭低压电加热电源,并立即进行熔体充型;步骤7,充型完成后,对真空罐内进行加压凝固,压力控制为0.6mpa,保压10min;充型完成后,在加压的同时再次开启低压电加热电源,控制加热温度为530℃,保温30min;步骤9,按照铸件基体合金要求进行后续固溶处理和时效处理,固溶参数为535℃/14h,时效参数为160℃/8h。对比实施例2铸件材料为zl114,铸件高度为670mm,铸件最大轮廓直径427mm,铸件转角部位呈弧形,该铸件的制备方法如下:步骤5,对真空罐进行抽真空,真空度控制为-0.09mpa;步骤6,进行熔体充型;步骤7,充型完成后,对真空罐内进行加压凝固,压力控制为0.6mpa,保压10min;步骤9,按照铸件基体合金要求进行后续固溶处理和时效处理,固溶参数为535℃/14h,时效参数为160℃/8h。性能检测:根据(gb/t228.1-2010)标准对前述实施例中制得的铸件进行性能检测,结果见表1。抗拉强度(mpa)断后伸长率(%)实施例150311.0%对比实施例14738.0%实施例23515.0%对比实施例23253.0%当前第1页12