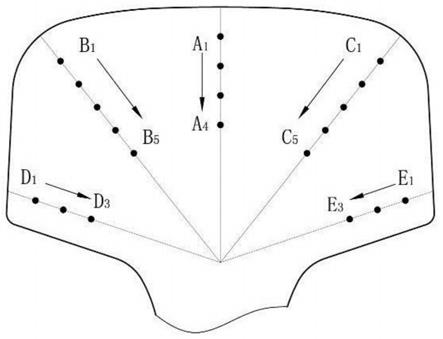
1.本发明涉及一种钢轨的生产方法,具体涉及一种提高热处理钢轨耐磨性能的生产方法,属于在线热处理钢轨生产技术领域。
背景技术:2.我国铁路建设正向着“客运高速化,货运重载化”方向快速发展,列车运行速度、载重量和运行密度显著增加,钢轨的使用环境也变得更为苛刻,钢轨磨耗和疲劳伤损等问题日益严重,严重影响了钢轨使用寿命和行车安全。
3.目前国内外钢轨厂家普遍采用了在线热处理工艺来提高钢轨强度和硬度,以提高其使用性能。钢轨在线热处理主要是利用轧制后钢轨的余温,对轨头进行加速冷却,获得更细化的珠光体组织,提高钢轨强度和硬度。横断面洛氏硬度是关系到热处理钢轨使用性能的一项关键指标,目前国内钢厂钢轨在线热处理工艺一般是对轨头表面采用基本恒定的冷却速度,热处理钢轨的横断面洛氏硬度从轨头表面到钢轨内部是逐渐下降的,表层材料具有良好的耐磨性,同时内部硬度降低,保证材料具有一定的韧性。但是在重载线路上,列车轴重大,表层材料磨损较快,钢轨的耐磨性明显下降,影响钢轨使用寿命;而如果将整个轨头材料全部硬化,钢轨的韧性又会显著下降,威胁到行车安全。
4.在钢轨在线热处理方法中,公开号为cn 1793403 a的中国发明专利公开了一种珠光体类热处理钢轨及其生产方法,其生产方法包括冶炼、轧制和热处理,从650
‑
880℃以1
‑
10℃/s的冷速将钢轨冷却到400
‑
500℃,再自然冷却至室温,生产出来的钢轨具有良好的耐磨性。
5.公开号为cn1178250a的中国发明专利提供了一种利用轧制余热生产高强度钢轨的热处理方法,其中钢轨包括0.65
‑
0.85质量%的c、0.21
‑
1.2质量%的si、0.50%
‑
1.5质量%的mn,以及v、cr、ti、mo、cu、ni和稀土元素中的至少一种。将热轧后保持在奥氏体区域的高温状态的钢轨连续送入装有热处理装置的机组中,通过喷嘴向钢轨喷射冷却介质,使钢轨得到均匀的加速冷却,获得硬度逐渐降低的微细珠光体组织。
6.公告号为cn106661651b的中国发明专利提供一种添加各种合金元素,头部表层的硬度以及韧性优秀的热处理钢轨的制造方法以及制造装置。所述钢轨包括0.75
‑
0.85质量%的c、0.5
‑
1.0质量%的si、0.5%
‑
1.0质量%的mn、0.5
‑
1.0质量%的cr、0
‑
0.01质量%的v,剩余部分为fe以及不可避免的杂质。所述钢轨表面温度500℃以上700℃以下前,以10℃/s以上的冷却速度进行强制冷却后,在珠氏体相变终止前,以
‑
5℃/s以上5℃/s以下的冷却速度对所述钢轨头部进行冷却。
7.公开号为cn 102220545 a的中国发明专利提供了一种耐磨性和塑性优良的高碳高强热处理钢轨及生产方法,轧制后热态钢轨余温为680
‑
900℃,以1.5
‑
10℃/s的冷速将钢轨冷却到400
‑
500℃,再自然冷却至室温,钢轨抗拉强度≥1330mpa,延伸率≥9%,轨头硬度≥380hb,组织为细珠光体,具有优良的耐磨性和塑性,能满足重载铁路的使用要求。
8.但上述专利只偏重于钢轨热处理方法和踏面硬度以及强度的提高,均未涉及通过
合理控制横断面洛式硬度来提高钢轨耐磨性的问题,针对目前重载铁路热处理钢轨耐磨性不好的问题,亟需一种能提高热处理钢轨耐磨性的生产方法。
技术实现要素:9.本发明所要解决的技术问题是针对目前重载铁路热处理钢轨横断面表面硬化层较浅,耐磨性不好的问题,提供一种提高热处理钢轨耐磨性的生产方法,通过合理控制横断面洛式硬度来提高钢轨耐磨性,同时保证钢轨轨头具有良好韧性。
10.本发明具体是这样实现的:
11.一种提高热处理钢轨耐磨性的生产方法,该方法主要包括对热轧后的钢轨轨头进行动态的加速冷却热处理,其中,开始冷却温度控制为720
‑
800℃,采用动态阶段性冷却工艺,即整个轨头冷却过程分为7个阶段,第1阶段冷却速度为5
‑
7℃/s,第2阶段冷速为7
‑
8℃/s,第3阶段冷速为8
‑
10℃/s,第4阶段冷速为1
‑
2℃/s,第5阶段冷速为4
‑
6℃/s,第6阶段冷速为3
‑
4℃/s,第7阶段冷速为2
‑
3℃/s,待轨头温度降至300℃以下时,停止加速冷却,最后自然冷却至室温。
12.更进一步的方案是:
13.开始冷却温度控制为740
‑
780℃,采用动态阶段性冷却工艺,即整个轨头冷却过程分为7个阶段,第1阶段冷却速度为5.5
‑
6.5℃/s,第2阶段冷速为7.2
‑
7.8℃/s,第3阶段冷速为8.5
‑
9.5℃/s,第4阶段冷速为1.2
‑
1.8℃/s,第5阶段冷速为4.5
‑
5.5℃/s,第6阶段冷速为3.5
‑
4℃/s,第7阶段冷速为2.2
‑
2.6℃/s,待轨头温度降至300℃以下时,停止加速冷却,最后自然冷却至室温;
14.更进一步的方案是:
15.第1阶段、第2阶段、第3阶段冷却时间均为7
‑
10s,第4阶段的冷却时间为5
‑
8s,第5阶段和第6阶段冷却时间分别为15
‑
20s,第7阶段冷却至轨头温度降至300℃以下时,停止加速冷却;
16.更进一步的方案是:
17.第1阶段与第2阶段、第2阶段与第3阶段之间的冷速差应控制在2℃/s以内;
18.更进一步的方案是:
19.在轨头加速冷却的同时,对轨底也施加一定的冷却速度,其冷却速度控制在轨头冷速的70
‑
80%,当轨头停止加速冷却时,轨底也相应停止冷却;
20.更进一步的方案是:
21.对钢轨通长进行加速冷却热处理,轨头温度是指钢轨轨头踏面中心部位表面的温度;
22.更进一步的方案是:
23.在上述生产方法中,以钢轨的总重量为基准,所述钢轨的化学成分包括0.78
‑
0.85重量%的c、0.60
‑
0.80重量%的si、0.75
‑
1.10重量%的mn、0.08
‑
0.15重量%的v、0.10
‑
0.15重量%的cr,≤0.025重量%的p、≤0.025重量%的s,其余为fe和不可避免的杂质;
24.更进一步的方案是:
25.冷却的介质为本领域常用的冷却介质,包括但是不限于水、聚合物溶液、油、压缩空气、水雾或者油雾混合气。
26.本发明还包括其他钢轨生产过程中的常规方法,比如铁水脱硫、转炉冶炼、lf精炼、真空处理、连铸、铸坯加热、轧制、矫直等工序,对上述工序没有特别的限定,按照常规的钢轨生产工艺方法进行即可。例如,浇铸过程应在全程保护下进行,防止与空气接触,浇铸成的钢坯应进行缓冷处理,采用步进梁加热炉进行铸坯加热,并进行保温处理,采用万能轧制生产线进行轧制,采用平立复合矫直工艺等;
27.本发明提供的一种能提高热处理钢轨耐磨性的生产方法,通过对轨头进行动态阶段性加速冷却,合理分配各阶段的冷却速度和冷却时间,实现外界冷却流场与高温金属热交换的动态平衡,通过合理控制横断面洛式硬度分布,提高钢轨耐磨性,同时保证钢轨轨头具有良好韧性,提高钢轨综合使用性能,该生产方法简单,可操作性强,易于推广应用。
附图说明
28.图1为钢轨轨头横断面洛氏硬度测量示意图;
29.图2为钢轨滚动接触磨损试验示意图。
具体实施方式
30.下面结合具体实施例对本发明作进一步的说明。
31.本发明提供一种提高热处理钢轨耐磨性的生产方法,该方法主要包括对热轧后的钢轨轨头进行动态的加速冷却热处理,其中,开始冷却温度控制为720
‑
800℃,采用动态阶段性冷却工艺,即整个轨头冷却过程分为7个阶段,第1阶段冷却速度为5
‑
7℃/s,第2阶段冷速为7
‑
8℃/s,第3阶段冷速为8
‑
10℃/s,第4阶段冷速为1
‑
2℃/s,第5阶段冷速为4
‑
6℃/s,第6阶段冷速为3
‑
4℃/s,第7阶段冷速为2
‑
3℃/s,待轨头温度降至300℃以下时,停止加速冷却,最后自然冷却至室温。
32.优选地,所述的开始冷却温度控制为740
‑
780℃,采用动态阶段性冷却工艺,即整个轨头冷却过程分为7个阶段,第1阶段冷却速度为5.5
‑
6.5℃/s,第2阶段冷速为7.2
‑
7.8℃/s,第3阶段冷速为8.5
‑
9.5℃/s,第4阶段冷速为1.2
‑
1.8℃/s,第5阶段冷速为4.5
‑
5.5℃/s,第6阶段冷速为3.5
‑
4℃/s,第7阶段冷速为2.2
‑
2.6℃/s,待轨头温度降至300℃以下时,停止加速冷却,最后自然冷却至室温。
33.本发明中,第1阶段、第2阶段、第3阶段冷却时间均为7
‑
10s,第4阶段的冷却时间为5
‑
8s,第5阶段和第6阶段冷却时间为15
‑
20s,第7阶段冷却至轨头温度降至300℃以下时,停止加速冷却。
34.本发明中,第1阶段与第2阶段、第2阶段与第3阶段之间的冷速差应控制在2℃/s以内。
35.选取上述工艺参数的原因如下:(1)对钢轨热处理强化原理是:轧后钢轨依然在奥氏体温度范围,进行加速冷却,降低珠光体转变温度,获得细化的珠光体组织,提高钢轨强度和硬度和耐磨性。将开始冷却温度控制为720
‑
800℃,是因为轨头金属量比较大,如果轧制后直接冷却,开冷温度过高,表层开始降温,但是心部温度很高,会向外进行热传导,导致珠光体相变的过冷度不足,影响最终性能,同时开始冷却温度过高,意味着钢轨奥氏体化温度和终轧温度就要提高,直接造成奥氏体晶粒粗大以及表面缺陷增多等问题,而开始冷却温度过低,与珠光体相变点距离较近,过冷度较低,相变驱动力不足,同时也会带来产生异
常组织的风险。本发明人通过研究发现,720
‑
800℃的开冷温度较为合适。(2)采用动态阶段性冷却工艺,即整个轨头冷却过程分为7个阶段,第1阶段冷速为5
‑
7℃/s,第2阶段冷速为7
‑
8℃/s,第3阶段冷速为8
‑
10℃/s,冷却时间均为7
‑
10s,第1阶段目的是为了快速带走轨头表层的热量,迅速形成稳定细化珠光体层,保证表面踏面硬度,同时为后续的热处理打下基础,表面珠光体相变完成后,珠光体相变向钢轨轨头次表面和内部发展,高温金属传热效率下降,此时第2阶段和第3阶段的冷速依次提高,是为了保证在表层一定深度内,冷却速度基本一致,珠光体相变驱动力应趋于一致,最终得到与表面硬度一致的硬化层,提高耐磨性。(3)第4阶段冷速为1
‑
2℃/s,主要是为了均匀前3阶段加速冷却产生的温度应力和相变应力,为下一阶段的冷却做准备。(4)第5阶段冷速为4
‑
6℃/s,第6阶段冷速为3
‑
4℃/s,第7阶段冷速为2
‑
3℃/s,此时轨头已经有足够深度的金属量发生了珠光体相变,心部蓄热区会进一步缩小,内部热量先传导给冷却珠光体层,然后再通过对流向外界散热,这3阶段采用依次降低冷却速度的工艺,保证转变界面的实际冷速是均匀下降的,以保证硬度不出现跳跃性下降。待轨头温度降至300℃以下时,整个轨头的珠光体转变均已完成,无需继续进行加速冷却。
36.本发明中,在轨头加速冷却的同时,对轨底也施加一定的冷却速度,其冷却速度控制在轨头冷速的70
‑
80%,这是因为轨头冷却速度较快,如果轨底自然冷却,轨头轨底温度差过大会造成钢轨大幅度弯曲,为了保证热处理过程中钢轨平直度,一般对轨底也要施加一定的冷却速度,而轨底金属量小于轨头,冷速一般控制在轨头冷速的70
‑
80%左右,尽量保持轨头轨底的温度一致性。
37.本发明的生产方法可以用于任何常规成分的在线热处理钢轨,能有效提高热处理钢轨耐磨性能,同时本发明人发现,特定化学成分的钢轨能够具有相对于其他化学成分的钢轨更好的效果,并且能够更适于本生产方法。这种特定化学成分的钢轨,以钢轨的总重量为基准,所述钢轨的化学成分包括0.78
‑
0.85重量%的c、0.60
‑
0.80重量%的si、0.75
‑
1.10重量%的mn、0.08
‑
0.15重量%的v、0.10
‑
0.15重量%的cr,≤0.025重量%的p、≤0.025重量%的s,其余为fe和不可避免的杂质;
38.所述生产方法还包括:铁水脱硫、转炉冶炼、lf精炼、真空处理、连铸、铸坯加热、轧制、矫直等工序,对上述工序没有特别的限定,按照常规的钢轨生产工艺方法进行即可。例如,浇铸过程应在全程保护下进行,防止与空气接触;浇铸成的钢坯应进行缓冷处理;采用步进梁加热炉进行铸坯加热,并进行保温处理;采用万能轧制生产线进行轧制;采用平立复合矫直工艺等。
39.本发明中,所述加速冷却和缓冷的冷却介质为本领域常用的冷却介质,包括但是不限于水、聚合物溶液、油、压缩空气、水雾或者油雾混合气,能够提供均匀冷却流场的物质均可。
40.通过本发明方法得到的热处理钢轨,钢轨全断面的室温金相组织为细片状珠光体和少量铁素体,未出现贝氏体和马氏体等异常组织,钢轨力学性能均满足相关标准要求。
41.为了更好地理解本发明,下面结合实施例进一步阐明本发明的内容,但应当理解,此处所描述的具体实施例仅仅用以解释本发明,并不限定本发明。
42.本发明实施例1
‑
4的冶炼化学成分分别按照表1所示。
43.表1实施例钢轨的化学成分
[0044][0045]
实施例1至3
[0046]
(1)按照常规的钢轨冶炼和浇铸方法进行,工序包括铁水脱硫、转炉冶炼、lf精炼、真空处理、连铸。其中,转炉炉渣碱度控制在2.5
‑
3.8;出钢水1/4左右时,随钢流加入硅、锰、钒等合金和增碳剂,钢水出至3/4时,合金、增碳剂全部加入;lf炉处理时间应大于40min;rh真空度≤90pa,纯真空处理时间应不低于20min,浇铸过程应在全程保护下进行,防止与空气接触,同时浇铸成的钢坯应进行缓冷处理。
[0047]
(2)按照常规的钢轨轧制方法进行,钢坯送入步进梁加热炉中加热并保温,加热温度1210
‑
1320℃,保温时间160
‑
240min,用万能轧机轧制成钢轨,开轧温度1080
‑
1150℃,终轧温度880
‑
930℃。
[0048]
(3)对钢轨进行动态阶段性在线热处理,轧后加速冷却的具体工艺参数按照表2所示。
[0049]
表2实施例加速冷却工艺参数
[0050][0051]
以目前国铁重载线路上使用范围最广泛的u75v热处理钢轨作为对比例,按照tb/t2344
‑
2012标准规定的方法测定实施例和对比例钢轨的抗拉强度、踏面硬度、金相组织、断裂韧性和洛氏硬度等性能指标,结果见表3和表4。其中,钢轨轨头横断面洛氏硬度测量见附图1。第1点距表面5mm,其余点间距均为5mm;d、e线与下颚距离为5mm;b、c线为a、d和a、e线的角平分线。
[0052]
表3实施例和对比例的力学性能对比
[0053][0054]
表4实施例和对比例的横断面洛氏硬度对比
[0055][0056]
续表4实施例和对比例的横断面洛氏硬度对比
[0057][0058]
为了验证本发明所得钢轨耐磨损性能,采用m
‑
2000型滚动接触磨损试验机,在相同试验条件下对实施例和对比例钢轨进行接触疲劳磨损试验。试验通过圆柱试样相对滚动,测量磨损失重量,试验示意图如图2所示。上试样分别取自实施例和对比例钢轨的5mm深度和15mm深度区域,下试样为布氏硬度380hb的车轮钢。
[0059]
试验条件如下:
[0060]
试样尺寸:厚度8mm,内径10mm,外径20mm;
[0061]
试验载荷:750n;
[0062]
试验环境:室温环境;
[0063]
转速:上试样180r/min,下试样200r/min;
[0064]
滑差率:10%;
[0065]
对磨总转数:3
×
105次。
[0066]
接触疲劳磨损试验结果见表5。
[0067]
表5实施例和对比例的接触疲劳磨损试验结果
[0068][0069]
可以看出,实施例1
‑
3中钢轨各项力学性能和金相组织良好,均满足相关标准要求,而且在表层至15mm深度范围内,横断面洛氏硬度基本保持一致,而对比例u75v热处理钢轨的横断面洛氏硬度随深度增加逐步下降。从接触磨损试验结果来看,在15mm深度位置,实施例钢轨的磨损失重量远低于u75v热处理钢轨。对比来看,本发明方法在保证热处理钢轨组织和力学性能的前提下,能有效提高耐磨性能。
[0070]
尽管这里参照本发明的解释性实施例对本发明进行了描述,上述实施例仅为本发明较佳的实施方式,本发明的实施方式并不受上述实施例的限制,应该理解,本领域技术人员可以设计出很多其他的修改和实施方式,这些修改和实施方式将落在本技术公开的原则范围和精神之内。