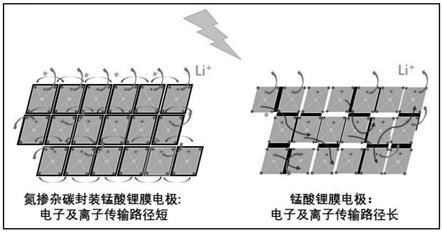
1.本发明属于电化学提锂技术领域,具体涉及一种用于溶存锂资源电化学提取的膜电极材料及其制备方法。
背景技术:2.金属锂具有高比热、电导率和化学活性的优点,历来在能源、材料、医疗、化工、航空航天以及国防等领域具有举足轻重的地位。随着信息时代和绿色经济时代的到来,质量轻、体积小和能量密度大的清洁锂离子电池得到了极为广泛的发展和应用。与此同时,高速发展的锂电产业也使得市场对锂资源的需求呈跳跃式的增长。目前,锂资源主要来源于陆地锂矿,尽管现如今的陆地锂矿仍能满足市场需求,但从长远来看单一的陆地锂资源将无法满足未来市场对锂资源的庞大需求。此外,陆地锂矿开采伴随的高能耗和环境污染,后期的环境治理难度大。因此发展多元化的锂资源开采方法将是未来锂资源开发的主流。其中,以海水和卤水为代表的溶存锂资源提取具有能耗低、无污染和储量巨大的优点,极具发展潜力。然而,溶存态的锂资源也存在着品味低、共存离子环境复杂的问题,因此发展高效的溶存锂资源提取方法对溶存锂资源的开发利用具有十分重要的意义。
3.目前,溶存锂资源开发方法主要有沉淀法、溶剂萃取法、吸附剂法、电渗析法和电化学法。其中,沉淀法虽然操作简单但无法用于高镁锂比溶液体系,溶剂萃取法虽然产品纯度高但成本较高,电渗析法则难以实现单价离子之间的有效分离。因此,针对低锂品位、复杂共存离子环境的海水和卤水体系,吸附剂法具有独特的优势,基于其独特的离子筛分性能,即使在海水和卤水体系中仍具有较高的锂离子选择性,但传统的吸附剂法也存在着吸附时间长、洗脱过程需要消耗大量酸的问题限制其进一步的工业化应用。
4.电化学法,是对传统吸附剂法的发展。基于外电场的驱动,强化了锂离子的嵌入和脱出速率,避免了酸性和氧化性洗脱剂的使用。目前,研究者们已经广泛研究了以锰酸锂、钛酸锂、磷酸铁锂以及三元锂电材料为代表的电极材料,但由于电极材料本身较差的导电性、氧化还原过程中的原子溶损以及jhan
‑
teller效应的固有缺陷使得其在电化学提锂领域的应用在一定程度上被限制。
技术实现要素:5.本发明的目的在于针对当前技术中存在的不足,提供一种用于溶存锂资源电化学提取的新型锂离子筛电极材料及其膜电极的制备方法。本发明采用含氮聚合物作为碳包覆的前驱体,制备中通过二段聚合的方式,即低温预聚合+室温聚合,并通过调节区间为1:0.1~1:10的不同投料比以及200~700℃的高温、n2环境煅烧,得到了具有均匀、完整的碳封装锂离子筛电极材料,并制备为碳封装锂离子筛膜电极用于溶存锂资源的富集。本发明得到的新型锂离子筛膜电极在复杂共存离子、低品位的锂原料液中具有较高的提锂速率、锂离子选择性和稳定的循环能力。
6.本发明的技术方案为:
7.一种用于溶存锂资源电化学提取的氮掺杂碳封装锂离子筛膜电极,该膜电极的电极材料包括主体材料和氮掺杂碳封装材料;其中,组成主体材料的锂离子筛与组成氮掺杂碳封装的含氮单体二者的质量配比为1:0.1~1:10;
8.所述的含氮聚合物所衍生的封装层包覆在正极材料的晶体表面,并与锂离子筛和含氮单体的质量配比呈正相关;
9.所述的含氮聚合物所衍生的封装层厚度为1~100nm。
10.所述的锂离子筛材料为锰酸锂锂离子筛、钛酸锂锂离子筛或三元锂离子筛;具体为 li2tio3、limn2o4、li(nicomn)o2或lifepo4;
11.所述氮掺杂碳封装为:基于原位聚合的含氮聚合物所衍生的三维原位氮掺杂碳封装层,所述的含氮聚合物单体包括五元环含氮单体、六元环含氮单体和非环状含氮单体中的任意一种或几种,
12.所述的含氮聚合物单体具体为吡咯、苯胺、丙烯腈、酰胺、乙烯亚胺、多巴胺以及氨脂,
13.所述的用于溶存锂资源电化学提取的氮掺杂碳封装锂离子筛膜电极的制备方法,该方法包括以下步骤:
14.(1)将锂离子筛材料分散于混合溶液a中,加入含氮单体,超声分散0.1h~5h后,
ꢀ‑
10℃~10℃、剧烈搅拌下滴加引发剂过硫酸铵溶液,反应温度为
‑
10℃~10℃,反应时间为 0.1h~5h;
15.其中,所述的锂离子筛材料为锰酸锂锂离子筛、钛酸锂锂离子筛或三元锂离子筛中的一种;所述混合溶液a由乙醇和水组成,体积比为乙醇:水=1:0.1~1:10;质量比为锂离子筛材料:水=1:50~1:200;质量比为,锂离子筛材料:含氮单体=1:0.1~1:10;引发剂过硫酸铵与含氮单体的摩尔量之比为1:0.5~1:2;
16.引发剂过硫酸铵溶液的溶剂与混合溶液a的成分相同,引发剂溶液浓度范围为 4.2775mg/ml~42.775mg/ml。
17.所述的含氮单体具体为吡咯、苯胺、丙烯腈、酰胺、乙烯亚胺、多巴胺或氨脂;
18.所述的剧烈搅拌的转速为500r/min~2000r/min;搅拌时间为0.1h~10h;
19.具体的,所述投料量的最优投料范围为质量比锂离子筛材料:含氮单体=1:0.130~0.140。
20.(2)随后,将反应器移至15~30℃下继续反应0.1~18h后,真空抽滤得到固体粉末,洗涤滤渣至滤液无色并在真空干燥箱中干燥过夜;所得固体粉末即为含氮聚合物封装的电极材料中间体;取所述中间体置于坩埚中,在管式炉中升温至200~700℃,进行煅烧0.1~10h;得到固体粉末,即为氮掺杂碳封装锂离子筛材料;
21.所述滤渣洗涤方式为无水乙醇与去离子水反复冲洗至滤液无色后继续洗涤1~10次。所述干燥方式为1℃~100℃真空干燥;
22.所述的升温速率为1~10℃/min。
23.(3)将氮掺杂碳封装锂离子筛材料、乙炔黑、粘结剂加入到混合溶液b中混合,所得的浆料均匀涂覆在碳布表面,干燥过夜,即得到氮掺杂碳封装锂离子筛膜电极;
24.浆料在碳布上的涂覆量为5~8mg/cm2;
25.具体的,所述步骤(3)中,锂离子筛材料为本发明所制备的氮掺杂碳封装锂离子筛,锂离子筛材料与乙炔黑、粘结剂的质量比为1:1:1~10:1:1混合。所述混合溶液b为体积比为 1:0.1~1:10的乙醇和去离子水,与固体总质量比为1:1~5:1。
26.所述混合方式为先磁力搅拌0.1~10h,然后超声分散0.1~1h。所述干燥方式为25~ 100℃下真空干燥。
27.所述的粘结剂具体为la132、pdfe或pvdf。
28.所述的氮掺杂碳封装锂离子筛膜电极的应用,用作溶存锂资源的电化学富集。
29.具体包括以下步骤:
30.(1)将所得氮掺杂碳封装锂离子筛膜电极接正极,agcl电极接负极,在0.01~1.00mol/l 的kcl溶液中,施加0.1~1.0v恒定电压,直至电流降至0.1ma停止,此时,所得电极为贫锂态的氮掺杂碳封装锂离子筛膜电极;然后将其接稳压电源的负极;
31.另外,将氮掺杂碳封装锰酸锂锂离子筛膜电极接稳压电源正极,构成“摇椅”式提锂体系;
32.(2)将所制备的富锂态氮掺杂碳封装锰酸锂膜电极接恒压电源正极置于回收液中,贫锂态氮掺杂碳封装锰酸锂膜电极接恒压电源负极置于原料液中;
33.其中,原料液为li
+
的单一溶液或与其他离子共存的混合溶液,其中,共存离子具体包括 ca
2+
、na
+
、k
+
、mg
2+
等阳离子中一种或几种;原料也中锂离子的浓度为20~500mg/l;
34.回收液为阳离子溶液,所述的阳离子为li
+
、ca
2+
、k
+
、na
+
、mg
2+
中一种或多种;阳离子溶液中阳离子的浓度范围为20~2000mg/l;
35.(3)施加0.1~1.0v恒定电压,至电极容量吸附饱和时(电流降至0.1ma)停止;
36.还包括如下步骤:将完成步骤(3)的电极取出后清洗,随后,将两电极位置对换并继续施加相同的恒定电压,重复步骤步骤(2)
‑
(3),即可实现li
+
从原料液向回收液中的富集。
37.本发明的实质性特点为:
38.本发明基于简单的吡咯单体原位聚合和高温煅烧获得三维原位包覆的氮掺杂碳封装电极材料其主体晶体的特定晶体结构在包覆、高温煅烧过程中不发生改变,且对锂离子具有高选择性,并在本发明所提供的反应过程中进行了晶体尺寸减小、晶胞参数增加以及结晶度增大。此外,均匀、完整的氮掺杂碳封装层来自于含氮单体的原位聚合,不同于普通的无机碳,其具有规整、刚性的结构以及高的机械强度和导电性能,可以有效改善锰酸锂电极导电性、循环性较差的问题,进而改善锰酸锂电极材料在。同时,结合“摇椅”式电极体系,有望进一步提高锰酸锂电极材料的提锂性能,提高溶存锂资源电化学提的效率。
39.材料碳封装的前驱体为具有共轭条件的含氮导电聚合物。基体材料为任意锂离子电池电极材料(如钛系正极材料、锰系正极材料和三元锂电正极材料中的任意一种),具有简单制备,无需其他特殊处理的特点;得到的材料为不同晶体形貌的同种晶体物质,(如limn2o4,有尖晶石型和层状结构的两种,任一种用于本发明所述相关膜电极材料的制备,其他电极主体材料亦然),具有“特定晶体结构”,即在本发明所述的电极体系下不发生任何变化,反之若发生晶体改变就很难保证达到本发明的效果。
40.本发明的有益效果为:
41.本发明所述由氮掺杂碳封装锂离子筛电极材料所组成的膜电极,在外电场的作用
下可以实现溶存锂资源从原料液到回收液中的高效富集,富集性能在原始锂离子筛的基础上有较大的提高。所述氮掺杂碳封装锂离子筛的主体材料,其晶型在包覆、高温煅烧过程中不发生改变,且对锂离子具有高选择性,并在本发明所提供的包覆、高温反应过程中的晶体尺寸减小、晶胞参数增加以及结晶度增大。同时,含氮聚合物衍生的碳封装层在包覆、高温过程中,在锂离子筛的表面形成均匀、完整的氮掺杂碳封装层,该封装层来自于含氮聚合物而非无机碳,与普通的无机碳相比其具有规整、刚性的结构以及高的机械强度和导电性能。
42.与现有技术相比,本发明所述的氮掺杂碳封装锂离子筛,通过碳封装层作为缓冲层有效抑制了过渡金属元素(mn、ti)的溶损和jhan
‑
teller效应所引起的容量快速下降,并减小了膜电极的极化现象,提高了电极的倍率性能,拥有更高的初始充放电容量,约119.22mah/g (最多可达119.22mah/g)。同时,通过碳封装作为导电层,有效提高了电子和离子的传输速率,强化了锂离子筛基体的电子和离子电导率,进一步提高了约49%的膜电极的提锂速率。另外,基于高温煅烧过程中的晶体细化,有效的优化了提锂性能。此外,晶胞参数的增加,扩大了锂离子筛晶体的晶面间距,适当的拓宽了锂离子通道,增强了锂离子的竞争力,提高了膜电极对锂离子的选择性。综上所述,本发明所提供的氮掺杂碳封装锂离子筛膜电极可以在复杂共存离子和低品位锂浓度的工作环境下,实现锂资源的高效提取。
附图说明
43.为了使本发明的内容更容易被清楚的理解,以基于聚吡咯以及锰酸锂所制备的氮掺杂碳封装锂离子筛膜电极材料为例并结合附图,对本发明作进一步详细的说明,其中,
44.图1为本发明所述的电极材料制备过程示意图及膜电极工作示意图,其中,图1a为氮掺杂碳封装锰酸锂电极材料的制备过程示意图,图1b为氮掺杂碳封装锰酸锂膜电极的电化学提锂过程示意图;
45.图2为本发明所述氮掺杂碳封装锰酸锂膜电极的强机理化示意图;
46.图3为本发明所述实施例1与对比例1中,氮掺杂碳封装锰酸锂电极材料的电镜图像,其中,图3a为煅烧后的产品即氮掺杂碳封装锰酸锂电极材料,图3b为未煅烧的中间体即含氮聚合物封装锰酸锂电极材料;
47.图4为本发明所述实施例1与对比例1中,氮掺杂碳封装锂离子筛电极材料的x射线衍射图谱。
48.图5为本发明所述实施例1与对比例1中,氮掺杂碳封装锂离子筛电极材料的元素分布图,其中图5a为元素分布扫描部位电镜图,图5b为各元素分布综合图,图5c为c元素分布图,图5d为n元素分布图,图5e为o元素分布图,图5f为mn元素分布图;
49.图6为本发明所述实施例1与对比例1中,氮掺杂碳封装锂离子筛电极材料的红外光谱图,其中图6a为锰酸锂、聚吡咯、聚吡咯封装锰酸锂以及氮掺杂碳封装锰酸锂电极材料的红外光谱图,图6b为聚吡咯封装锰酸锂和氮掺杂碳封装锰酸锂电极材料的红外光谱局部放大图;
50.图7为本发明所述实施例1中,氮掺杂碳封装锰酸锂膜电极在单一licl(0.05mol/l) 溶液中的锂离子电吸附容量随时间变化图;
51.图8为本发明所述实施例1与对比例1中,锰酸锂膜电极和氮掺杂碳封装锰酸锂膜电极在不同共存混合溶液中的离子迁移量随时间变化图,其中图8a为li、mg混合溶液中的
离子电吸附容量随时间变化图,图8b为li、na混合溶液中的离子电吸附容量随时间变化图,图 8c为li、k混合溶液中的离子电吸附容量随时间变化图,图8d为li、ca混合溶液中的离子电吸附容量随时间变化图;
52.图9为本发明实所述实施例1与对比例1中,锰酸锂膜电极和氮掺杂碳封装锰酸锂膜电极的循环伏安曲线图,和电流随v
1/2
/s
1/2
的变化图,其中图9a和9b分别为氮掺杂碳封装锰酸锂膜电极在扫速为0.1
‑
0.5mv/s下的循环伏安曲线图及电流随v
1/2
/s
1/2
的变化图,图9c和9d 分别为锰酸锂膜电极在扫速为0.1
‑
0.5mv/s下的循环伏安曲线图及电流随v
1/2
/s
1/2
的变化图;图9e和图9f分别为锰酸锂膜电极和氮掺杂碳封装锰酸锂膜电极在30个循环伏安过程后的电流随电压变化图;
53.图10为本发明所述实施例1与对比例1中,锰酸锂膜电极和氮掺杂碳封装锰酸锂膜电极的充放电容量随循环次数的变化图;
54.图11为本发明所述实施例1中,氮掺杂碳封装锂锰酸锂膜电极在提锂过程中电吸附容量虽循环次数的变化图
55.图12为本发明所述实施例1中,氮掺杂碳封装锂锰酸锂膜电极在模拟浓海水中各离子电吸附容量随时间的变化图。
具体实施方式
56.本发明下述实施例与对比例,均通过tas
‑
990f原子吸收分光光度计测定回收液中各阳离子的浓度随时间的变化并通过电化学工作站、环境扫描电镜、x射线衍射仪以及红外光谱仪对电极材料及膜电极性能进行分析比较。
57.本发明下述实施例与对比例,所述电化学提锂过程基于图1(b)所示的装置进行。左侧为回收液室,右侧为原料液室,两室以单价选择性阴离子交换膜(acs)隔离,左侧电极为富锂态电极,右侧电极为贫锂态电极,两电极分解接恒压电源的正极和负极。
58.实施例1
59.选用主体材料为锰酸锂,碳封装材料为吡咯,在最优投料质量比锰酸锂:吡咯=1:0.135 的条件下为实例,本发明所述的氮掺杂碳封装锰酸锂电极材料的制备及性能测试,包括如下步骤
60.(1)聚吡咯衍生氮掺杂碳封装锰酸锂粉体的制备
61.以高温固相法制备锰酸锂锂离子筛粉体。通过前文所述方法,将吡咯单体在limn2o4锂离子筛表面进行三维包覆得到含氮聚合物封装锰酸锂中间体。所得中间体置于坩埚中,在高温条件下,于管式炉中进行高温煅烧。所得粉末即为所述实例:基于聚吡咯所衍生的氮掺杂碳封装锰酸锂锂离子筛。
62.a)取1g limn2o4均匀分散于乙醇和去离子水的的混合溶液100ml中。其中,乙醇与水的体积比为1:1、limn2o4与混合溶液的质量比为1:100。随后,加入质量比为limn2o4:含氮单体=1:0.135的吡咯单体135μl,超声分散后30min后,在
‑
1℃下以1500r/min的转速剧烈搅拌5h,将单体与离子筛充分混合均匀;
63.b)取摩尔比为(nh4)2s2o8:含氮单体=1:1的过硫酸铵0.4277g溶于体积比为乙醇:水=1:1 的混合溶液40ml中作为引发剂溶液。随后,逐滴全部滴加至剧烈搅拌(转速为1500r/min) 的混合溶液中,并在
‑
1℃下反应5h(滴加和反应时间合计5小时);随后,将反应
(0.05mol/l)中的平衡时间约40min,电吸附容量为34.57mg/g。
75.在li
+
:mg
2+
=0.05mol/l:1.00mol/l的锂镁混合溶液80ml中进行提锂实验后,通过 tas
‑
990f原子吸收分光光度计对回收液中离子含量进行检测,如附图8所示,在相同的混合离子溶液中实施例1的平衡时间约40min,均短于对比例2(大于40min)。实施例1在相同时间下的锂离子迁移量均大于对比例2。其中,实施例1在5min时的锂迁移量约是对比例2 的两倍。同时,如表2所示,实施例1中氮掺杂碳封装锰酸锂离子筛膜电极材料对ca
2+
、na
+
、 k
+
、mg
2+
四种共存离子的选择系数也得到了进一步的提升。
76.表2
[0077][0078]
另外,如附图9a~d所示,由不同扫速下的cv曲线分析可知,锂离子在电极上的嵌入和脱出受扩散过程控制。如表3所示,氮掺杂碳封装锰酸锂离子筛膜电极的锂离子扩散系数均得到了较大的提升。同时,如图9e~9f所示,氮掺杂碳封装锰酸锂离子筛膜电极在30个cv 循环后不发生氧化还原峰的位移,说明氮掺杂碳封装锰酸锂离子筛膜电极的极化现象得到了改善。
[0079]
表3
[0080][0081]
此外,氮掺杂碳封装锰酸锂离子筛膜电极材料的初始充放电容量比锰酸锂膜电极高 23.56%、24.77%(附图10)。50个充放电循环后,氮掺杂碳封装锰酸锂离子筛膜电极的充放电容量比锰酸锂离子筛膜电极分别高28.5%和25.6%(附图10)。在十个实际循环操作过程后电吸附锂容量衰减约8%(附图11)。在模拟浓海水中,氮掺杂碳封装锰酸锂离子筛膜电极的锂容量仍可以达到37.14mg/g(附图12),对ca、na、mg离子的分离系数分别为1381.89、 2110.64、228.25。综上,基于附图2所示强化机理的氮掺杂碳封装锰酸锂膜电极被成功制备并具有理想的电化学提锂性能。
[0082]
对比例2
[0083]
本对比例所述的电化学提锂过程与实施例1相比,提锂过程的操作条件和电极体系结构均相同,其区别仅在于,对比例2中所使用的的氮掺杂碳封装膜电极非同一配比。具体的,本对比例中:吡咯单体的投料量为540μl;过硫酸铵引发剂的投料量为1.71g。
[0084]
在li
+
:mg
2+
=0.05mol/l:1.00mol/l的锂镁混合溶液80ml中进行提锂实验后,通过 tas
‑
990f原子吸收分光光度计对回收液中离子含量进行检测。结果表明,在相同的混合离子溶液中对比例2的平衡时间约20min,锂容量为4.56mg/g,锂镁分离系数为42.64。
[0085]
对比例3
[0086]
本对比例所述的电化学提锂过程与实施例1相比,提锂过程的操作条件和电极体系结构均相同,其区别仅在于,对比例2中所使用的的氮掺杂碳封装膜电极非同一配比。具
体的,本对比例中:吡咯单体的投料量为270μl;过硫酸铵引发剂的投料量为0.85g。
[0087]
在li
+
:mg
2+
=0.05mol/l:1.00mol/l的锂镁混合溶液80ml中进行提锂实验后,通过 tas
‑
990f原子吸收分光光度计对回收液中离子含量进行检测。结果表明,在相同的混合离子溶液中对比例2的平衡时间约20min,锂容量为9.39mg/g。
[0088]
对比例4
[0089]
本对比例所述的电化学提锂过程与实施例1相比,提锂过程的操作条件和电极体系结构均相同,其区别仅在于,对比例2中所使用的的氮掺杂碳封装膜电极非同一配比。具体的,本对比例中:吡咯单体的投料量为180μl;过硫酸铵引发剂的投料量为0.57g。
[0090]
在li
+
:mg
2+
=0.05mol/l:1.00mol/l的锂镁混合溶液80ml中进行提锂实验后,通过 tas
‑
990f原子吸收分光光度计对回收液中离子含量进行检测。结果表明,在相同的混合离子溶液中对比例2的平衡时间约35min,锂容量为20.74mg/g,锂镁分离系数为180.55。
[0091]
对比例5
[0092]
本对比例所述的电化学提锂过程与实施例1相比,提锂过程的操作条件和电极体系结构均相同,其区别仅在于,对比例2中所使用的的氮掺杂碳封装膜电极非同一配比。具体的,本对比例中:吡咯单体的投料量为105μl;过硫酸铵引发剂的投料量为0.342g。
[0093]
在li
+
:mg
2+
=0.05mol/l:1.00mol/l的锂镁混合溶液80ml中进行提锂实验后,通过 tas
‑
990f原子吸收分光光度计对回收液中离子含量进行检测。结果表明,在相同的混合离子溶液中对比例2的平衡时间约35min,锂容量为25.89mg/g,锂镁分离系数为234.32。
[0094]
通过上述对比例1,可以清楚的发现,本发明所提供的新型膜电极材料与传统膜电极材料相比,在吸附速率、平衡时间、锂镁分离系数方面均得到了较大的提升。进一步地,基于对比例2
‑
5,可以清楚的发现,基于平衡时间、锂容量以及锂镁分离系数三个核心参数,不同的投料量所对应的膜电极核心参数不尽相同,并在本发明所提供的最优的投料配比(实施例1)下,新型膜电极材料的性能达到最优。
[0095]
显然,基于平衡时间、锂容量以及锂镁分离系数三个核心参数,上述实施例仅清楚地说明本发明中氮掺杂碳封装锂离子筛材料及其相关膜电极材料的关键制备方法和使用方法,而未对实施方式进行严格的限定。对于所属领域的普通技术人员来说,在上述说明的基础上还可以做出其它不同形式的变化或变动。这里无需也无法对所有的实施方式予以穷举。而由此所引伸出的显而易见的变化或变动仍处于本发明创造的保护范围之中。
[0096]
本发明所提供的新型氮掺杂碳封装膜电极,在电化学提锂领域,其提锂速度具有较大的提升,且循环稳定性能亦有所提升。以实施例为例,与本课题组前期工作相比,在相同的工作条件下,提锂速率提升约49.19%,单次提锂耗时由2h缩短至约40min;锂镁分离系数提升约40%;循环性能提升约20%。与国内外其他类似的提锂电极体系相比,在低品位的模拟海水 (c
li+
=170mg/l)中,具有更短的提锂时间和更高的锂容量(90min,37.14mg/g),且更适应未来市场对低品位原料液提锂的需求。相关参数比较如下表所示。
[0097]
本发明所述电极与其他类似电极体系的提锂条件和性能比较
[0098][0099]
[1]c.p.lawagon,g.m.nisola,r.a.i.cuevas,h.kim,s.
‑
p.lee,w.
‑
j.chung,li1
‑
xni0.33co1/3mn1/3o2/agforelectrochemicallithiumrecoveryfrombrine,chemicalengineeringjournal348(2018)1000
‑
1011.
[0100]
[2]x.zhao,g.li,m.feng,y.wang,semi
‑
continuouselectrochemicalextractionoflithiumfrombrineusingcf
‑
nmmo/acasymmetrichybridcapacitors,electrochimicaacta331(2020)135285.
[0101]
[3]z.zhao,x.si,x.liu,l.he,x.liang,liextractionfromhighmg/liratiobrinewithlifepo4/fepo4aselectrodematerials,hydrometallurgy133(2013)75
‑
83.
[0102]
[4]m.
‑
y.zhao,z.
‑
y.ji,y.
‑
g.zhang,z.
‑
y.guo,y.
‑
y.zhao,j.liu,j.
‑
s.yuan,studyonlithiumextractionfrombrinesbasedonlimn2o4/li1
‑
xmn2o4byelectrochemicalmethod,electrochimicaacta252(2017)350
‑
361.
[0103]
[5]x.zhao,y.jiao,p.xue,m.feng,y.wang,z.sha,efficientlithiumextractionfrombrineusingathree
‑
dimensionalnanostructuredhybridinorganic
‑
gelframeworkelectrode,acssustainablechemistry&engineering8(2020)4827
‑
4837.
[0104]
实施例2,
[0105]
其他步骤同实施例1,不同之处为,聚吡咯替换为聚2,5
‑
二甲氧基苯胺,煅烧温度由500℃替换为600℃;
[0106]
基于聚苯胺所得到的氮掺杂碳封装锰酸锂膜电极表现出于实施例1相似的性能,吸附性能得到提升,平衡时间约1h。
[0107]
实施例3
[0108]
其他步骤同实施例1,不同之处为,聚吡咯替换为聚2,5
‑
二甲氧基苯胺,煅烧温度由500℃替换为600℃;
[0109]
基于聚2,5
‑
二甲氧基苯胺所得到的氮掺杂碳封装锰酸锂膜电极表现出于实施例1和2相似的性能,吸附速率得到提升,平衡时间约1h。
[0110]
实施例4
[0111]
其他步骤同实施例1,不同之处为,锰酸锂替换为钛酸锂;
[0112]
得到的材料的性能接近实施例1。
[0113]
本发明未尽事宜为公知技术。