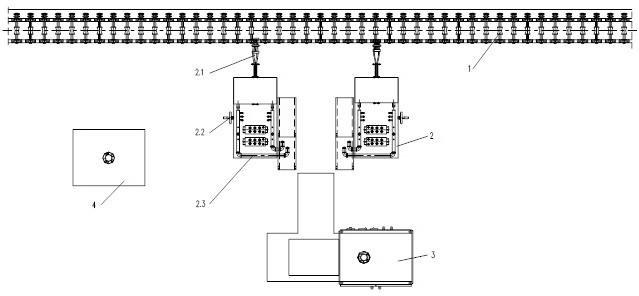
1.本发明涉及材料领域紫铜直管的硬度调整、塑性优化及内应力消除,特别是涉及一种紫铜直管退火的装置及方法。
背景技术:2.退火是一种金属热处理工艺,指的是将金属缓慢加热到一定温度,保持足够时间,然后以适宜速度冷却。目的是降低硬度,改善切削加工性;消除残余应力,稳定尺寸,减少变形与裂纹倾向;细化晶粒,调整组织,消除组织缺陷。
3.紫铜(即纯铜)具有优良的导电、导热性和塑性及良好的耐腐蚀性,在电子工业、仪器仪表和高压开关等工业中有广泛的应用,工业生产中对紫铜制件的表面硬度和内部晶粒度要求比较苛刻,通常的退火处理工艺及装置难以满足要求。
技术实现要素:4.为了能够实现紫铜直管降低硬度、提高塑性、消除内应力及细化结晶组织问题,本发明提供了一种紫铜直管退火的装置及方法。该方法通过上料缓存、辊轮传输、退火工艺、下料缓存四道工序,采用电感线圈金属加热方式进行紫铜直管退火,解决紫铜直管退火的技术问题。
5.本发明解决技术问题所采用的技术方案是:一种紫铜直管退火的装置主要由辊轮、感应线圈及台架、电源及控制柜和除尘净化装置组成,在辊轮输送线侧部设有一组感应线圈及台架以及电源及控制柜,感应线圈及台架一侧设置有除尘净化装置;其中,辊轮用于管件的转运,感应线圈及台架为退火工艺的主要执行装置,电源及控制柜作为退火装置的主控装置,并为退火工艺提供输出电源,除尘净化装置用于装置运行过程中烟尘的净化处理。
6.为了进一步解决本发明所要解决的技术问题,本发明提供的感应线圈及台架中,所述感应线圈及台架包括感应线圈和台架,在台架下部设有位置调节旋轮和伸缩气缸,台架上部设有感应线圈和加热感应器,所述加热感应器采用快速替换工位,满足不同规格的管件变化,感应线圈采用预制件装配式结构,便于维修及更换;所述感应线圈由大截面矩型铜管整体绕制而成,管内通冷却水;为保护其绝缘强度,在感应线圈表面涂防潮绝缘磁漆;所述台架上设有位置调节旋轮为手动升降装置,并安装有刻度尺和上下限位保护机构,在手动模式下,调整感应线圈位置,使待加热管件处于感应线圈中心位置,同时,可根据管件直径参数,通过伸缩气缸切换感应线圈及台架。
7.进一步地,一种紫铜直管退火的方法主要包括上料缓存、辊轮传输、退火工艺、下料缓存四道工序,具体流程为:管件首先进入上料缓存工位,再通过上料机构进入辊轮输送,由辊轮输送线转运到退火工位,执行退火工艺,退火结束后的管件由辊轮输送线转运到下料工位处,并通过下料机构进入下料缓存架。
8.积极效果:由于一种紫铜直管退火的装置主要由辊轮、感应线圈及台架、电源及控
制柜、除尘净化装置组成,采用电感线圈金属加热方式进行紫铜直管退火,加热感应器采用快速替换工位,满足不同规格的管件变化;一种紫铜直管退火的方法主要包括上料缓存、辊轮传输、退火工艺、下料缓存四道工序,具体分为自动模式与手动模式;采用连续加热的方式,并设有温控系统,可实现对加热温度的闭环控制,确保加热温度符合工艺要求。适宜作为一种紫铜直管退火的装置及方法应用。
附图说明
9.附图1是一种紫铜直管退火的装置结构示意图;附图2是一种紫铜直管退火方法工艺流程框图。
10.图中,1.辊轮,2.感应线圈及台架,2.1.感应线圈,2.2.位置调节旋轮,2.3.伸缩气缸,3.电源及控制柜,4.除尘净化装置。
具体实施方式
11.为使本发明实施例的目的、技术方案和优点更加清楚,下面将结合本发明实施例中的附图,对本发明实施例中的技术方案进行清楚、完整地描述,显然,所描述的实施例是本发明一部分实施例,而不是全部的实施例。通常在此处附图中描述和示出的本发明实施例的组件可以以各种不同的配置来布置和设计。因此,以下对在附图中提供的本发明的实施例的详细描述并非旨在限制要求保护的本发明的范围,而是仅仅表示本发明的选定实施例。基于本发明中的实施例,本领域普通技术人员在没有作出创造性劳动前提下所获得的所有其他实施例,都属于本发明保护的范围。
12.据图所示,一种紫铜直管退火的装置主要由辊轮1、感应线圈及台架2、电源及控制柜3和除尘净化装置4组成,在辊轮1输送线侧部设有一组感应线圈及台架2以及电源及控制柜3,感应线圈及台架2一侧设置有除尘净化装置4;其中,辊轮1用于管件的转运,感应线圈及台架2为退火工艺的主要执行装置,电源及控制柜3作为退火装置的主控装置,并为退火工艺提供输出电源,除尘净化装置4用于装置运行过程中烟尘的净化处理。
13.为了保证本发明结构的稳定性,所述感应线圈及台架2包括感应线圈2.1和台架,在台架下部设有位置调节旋轮2.2和伸缩气缸2.3,台架上部设有感应线圈2.1和加热感应器;所述加热感应器采用快速替换工位,满足不同规格的管件变化,感应线圈2.1采用预制件装配式结构,便于维修及更换;所述感应线圈2.1由大截面矩型铜管整体绕制而成,管内通冷却水;为保护其绝缘强度,在感应线圈2.1表面涂防潮绝缘磁漆;所述台架上设有位置调节旋轮2.2为手动升降装置,并安装有刻度尺和上下限位保护机构,在手动模式下,调整感应线圈2.1位置,使待加热管件处于感应线圈2.1中心位置,同时,可根据管件直径参数,通过伸缩气缸2.3切换感应线圈及台架2。
14.为了进一步保证本发明结构的稳定性,所述加热感应器的感应加热电源功率一般按下面公式计算:其中,p表示电源功率(单位:kw),g表示待加热管件重量(单位:kg),t2表示管件目标加热温度(单位:℃),t1表示管件初始温度(单位:℃),t表示加热节拍(单位:秒),c表示
被加热金属平均比热(单位:kj/(kg*℃)),对于紫铜,c=0.394 kj/(kg*℃),加热效率η取0.6。
15.为了优化本发明的结构,一种紫铜直管退火的装置还包括温度控制系统,所述温度控制系统主要由红外测温仪、plc可编程控制器和数字化采样模块组成,并与加热电源数据通信,以完成加热温度闭环控制;即,当检测到管件实际温度高于设定值时,加热电源将会自动降低输出功率;反之,当检测到管件实际温度低于设定值时,加热电源将自动提高输出功率,通过这一机制,确保待加热管件温度符合工艺要求。
16.为了优化本发明的结构,一种紫铜直管退火的方法主要包括上料缓存、辊轮传输、退火工艺、下料缓存四道工序,具体流程为:管件首先进入上料工位缓存,再通过上料机构进入辊轮转运输送,由辊轮转运输送线转运到退火工位,执行退火工艺,退火结束后的管件由辊轮转运输送线转运到下料工位处,并通过下料工位机构进入下料缓存架。
17.为了更加优化本发明结构的稳定性,一种紫铜直管退火的方法退火工艺采用连续加热的方式,即管件在辊轮上转运与加热同时进行,设计有温控系统,可实现对加热温度的闭环控制,确保加热温度符合工艺要求;管件加热温度通过控制辊轮运行速度和电源输出功率调节,当管件加热区间结束后,停止电源输出功率,并恢复辊轮正常运行速度,尽快将加热结束后的管件转运至下料工位。
18.为了再进一步优化本发明的结构,一种紫铜直管退火的方法的运行模式分为自动模式与手动模式,具体流程为:在自动模式下,本系统根据信息化系统下发的任务信息,如管径、厚度、长度、应力消除位置及温度要求等,自主适配退火工艺参数,如电源输出功率、辊轮运行速度,并调用规格参数相匹配的感应线圈,完成应力消除工艺,自动模式主要用于管件规格大批量、标准作业等情况,可显著提高产能及改善工作环境;在手动模式下,根据管件管径、厚度、温度要求等,手动设定电源输出功率,并选择规格参数相匹配的感应线圈,控制辊轮运行将管件由上料工位转送至应力消除工位,执行退火工艺,退火结束后,再控制辊轮运行将管件转送至下料工位,手动模式主要用于管件规格小批量及临时任务等情况,相比自动模式,灵活性及效率更高。
19.实施例:紫铜直管的几何数据:a.外径:φ20 mm~φ114mm;b.壁厚:2 mm~7mm;c.长度:0.5m~6m;d.直线度:≤1 mm/m。
20.采用电感线圈金属加热方式进行紫铜直管退火,对于适用范围内的管件,电感线圈加热速度可达0.8m/min,加热温度可达400℃~750℃,温度控制精度为
±
15℃,加热位置控制精度为
±
10mm,管件通过辊轮输送线进行转运。
21.最后应说明的是:以上所述仅为本发明的优选实施例而已,并不用于限制本发明,尽管参照前述实施例对本发明进行了详细的说明,对于本领域的技术人员来说,其依然可以对前述各实施例所记载的技术方案进行修改,或者对其中部分技术特征进行等同替换,凡在本发明的精神和原则之内,所作的任何修改、等同替换、改进等,均应包含在本发明的保护范围之内。