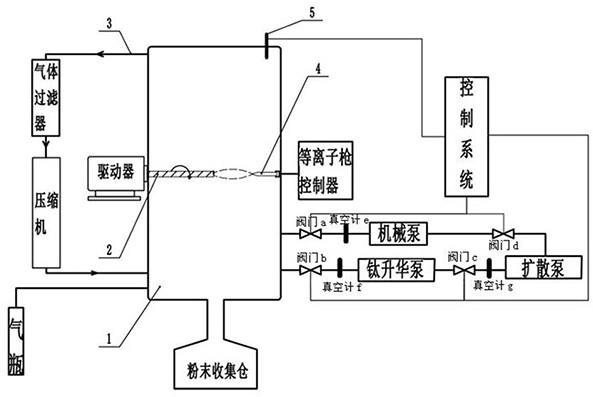
一种高球形度低氧含量tial合金粉末制备方法及其设备
技术领域
1.本发明属于粉末冶金技术领域,更具体地,涉及一种高球形度低氧含量tial合金粉末制备方法及其设备。
背景技术:[0002] tial合金以其优异的高温性能及低密度,已成为重要的高温结构材料,尤其是航空发动机低压涡轮叶片的主要材料。传统工艺通常采用铸造方式制备tial合金叶片,但由于tial合金本征脆性使得叶片毛坯加工难度大、导致叶片成品率低。热等静压技术或增材制造技术以tial合金粉末为原材料,实现低压涡轮叶片的近净成形。两种技术制造的叶片加工量小,成品率高。因此航空发动机低压涡轮叶片制备技术已由传统铸造逐步替换为热等静压或增材制造。
[0003]
热等静压或增材制造技术制备的低压涡轮叶片性能优劣的关键在于原材料粉末质量的好坏。高球形度粉末具有纯净度好、表面光洁度高以及粉末颗粒间不易桥接等优点,这是由于在热等静压或增材制造技术中粉末球形度越好,粉末振实密度越高、填充率也越高,零件成型过程中产生孔隙或裂纹越少,而孔隙和裂纹越少,零件的服役性能尤其是高温疲劳性能越优异。
[0004]
离心雾化技术相对其他制粉技术具有超洁净的加工环境、无非金属夹杂引入等优势,该技术制备的粉末较其他粉末制备技术具有球形度好、纯净度高等特点,因此离心雾化技术已成为热等静压和增材制造技术中首选的原材料制备方式。虽然离心雾化技术较其他制粉技术可以获得高球形度粉末,但tial合金与钛合金和铝合金材料类型不同,属于金属间化合物,合金的塑性较其他两种差(延伸率仅有1%),因此制粉过程中极易出现棒材开裂,易导致熔炼过程无法进行的风险;另外,该材料自身导热性差(热导率仅为22.5 wm
−
1 k
−1),造成金属熔滴凝固速度相对其他金属材料慢,凝固过程易异向变形,因此粉末的球形度往往劣于其他离心雾化粉末。这可以解释为:离心雾化技术中金属熔滴在飞行过程中,依靠克服表面张力自发凝固成球,金属熔滴尺寸越大必然导致飞行速度过快,熔滴凝固不充分而造成粉末球形度差。另外,相对于其他制粉技术,离心雾化技术采用预抽真空处理后再充入高纯惰性气体,粉末加工环境更纯净,因此粉末氧含量较其他制备技术低;但传统离心雾化技术中加工环境为非闭环惰性气体环境,气体在加工仓内处于持续进出流动状态,若要保证加工仓内压力恒定必然要不断对仓内气体进行补给,这样一则增加了气体使用成本,二则破坏了原始预抽真空的纯净度,增加了加工仓内氧含量。而对于tial合金而言,300~500℃时极易与氧、氮、氢反应,严重影响合金的塑性。因此如何提高tial合金粉末球形度、降低粉末中氧含量,是影响航空发动机低压涡轮叶片服役寿命的关键。
技术实现要素:[0005]
本发明的目的在于克服上述现有技术的缺点,提出一种高球形度低氧含量tial合金粉末制备方法及其设备,通过提高tial合金粉体综合性能、降低粉体中氧含量,改善热等
静压或增材制造零件性能,最终延长低压涡轮叶片服役寿命。
[0006]
为了实现上述目的,本发明采用了如下技术方案:一种高球形度低氧含量tial合金粉末制备方法,其特征在于,包括如下步骤:s1、通过至少两次真空感应熔炼、浇铸成tial合金棒材;s2、将步骤s1制备的棒材进行高温相变处理;s3、将步骤s2处理后的棒材进行机械加工得到精加工棒材;s4、以步骤s3制备的精加工棒材为自耗电极,将自耗电极放置于加工仓内;s5、开启真空系统泵组及真空阀门,使得加工仓内真空度低于10
‑3pa,关闭真空系统泵组及真空阀门;s6、向加工仓内充入氩气和氦气的混合气体,直至加工仓内压力为2
×
101pa,氧含量低于50ppm,关闭装有混合气体的气瓶、开启惰性气体闭环系统;s7、开启驱动器从而使得驱动器带动自耗电极以30000~33000rpm的速度旋转,开启等离子枪控制器,产生功率为50~60kw的等离子电弧,等离子电弧加热高速旋转的自耗电极端面使其熔化形成液面并形成金属熔滴,金属熔滴快速凝固成tial合金球形金属粉末;s8、在高纯惰性气体环境下,对步骤s7制备的金属粉末进行筛分包装。
[0007]
进一步地,所述步骤s2中高温相变处理在真空环境下,真空度低于10
‑2pa,温度加热至1330~1350℃,保温1~4h,采用水淬冷却;然后在真空环境下回火处理即加热至1300~1320℃,保温1~4h,炉冷冷却。
[0008]
进一步地,所述步骤s7中tial合金球形金属粉末的球形度≥98%,tial合金球形金属粉末氧含量低于50ppm。
[0009]
一种实现高球形度低氧含量tial合金粉末制备方法的设备,其特征在于,所述设备包括加工仓,所述加工仓上设置有用于带动自耗电极旋转的驱动器,与驱动器相对应的位置设置有等离子枪,所述等离子枪由等离子枪控制器控制,所述加工仓上连接有真空系统泵组,所述真空系统泵组通过控制系统与设置于加工仓上的氧探头连接。
[0010]
进一步地,所述加工仓上还设置有惰性气体闭环系统,所述惰性气体闭环系统包括气体循环管路,所述气体循环管路的输入端和输出端分别与加工仓连接,所述气体循环管路上依次连接有气体过滤器和压缩机。
[0011]
进一步地,所述真空系统泵组包括与加工仓连接的机械泵与扩散泵,所述机械泵及扩散泵均与控制系统连接。
[0012]
进一步地,所述加工仓与扩散泵之间连接有钛升华泵,所述钛升华泵与控制系统连接。
[0013]
与现有技术相比,本发明具有以下有益效果:本发明将tial合金铸态棒材进行高温相变处理,为获得离心雾化细小熔滴提供了组织基础;通过本发明可有效提高粉末球形度,使得粉体综合性能指标提高;本发明真空系统泵组中设计了钛升华泵,用于进一步降低加工仓内氧含量,保证所制备tial合金粉末氧含量低于50ppm;本发明增设了惰性气体闭环系统,降低了制粉过程惰性气体使用成本、同时减小了合金粉末中氧含量;tial合金棒材经历至少两次熔炼,最大程度降低了tial合金中杂质元素含量,提高合金纯净度。
[0014]
本发明中,通过以下参照附图对本发明的示例性实施例的详细描述,本发明的其
它特征及其优点将会变得清楚。
附图说明
[0015]
此处的附图被并入说明书中并构成本说明书的一部分,与说明书一起用于解释本发明的原理。
[0016]
为了更清楚地说明本发明实施例或现有技术中的技术方案,下面将对实施例或现有技术描述中所需要使用的附图作简单地介绍,显而易见地,对于本领域普通技术人员而言,在不付出创造性劳动性的前提下,还可以根据这些附图获得其他的附图。
[0017]
图1为本发明一种高球形度低氧含量tial合金粉末制备设备结构图;图2为利用本发明技术制备的tial合金粉末的扫描电镜照片;图3为利用传统技术制备的tial合金粉末的扫描电镜照片;图4为采用本发明技术制备的tial合金粉末所生产的tial合金低压涡轮叶片的截面微观组织形貌;其中:1、加工仓;2、自耗电极;3、气体循环管路;4、等离子电弧;5、氧探头。
具体实施方式
[0018]
这里将详细地对示例性实施例进行说明,其示例表示在附图中。下面的描述涉及附图时,除非另有表示,不同附图中的相同数字表示相同或相似的要素。以下示例性实施例中所描述的实施方式并不代表与本发明相一致的所有实施方式。相反,它们仅是与所附权利要求书中所详述的、本发明的一些方面相一致的设备的例子。
[0019]
为了使本领域的技术人员更好地理解本发明的技术方案,下面结合附图及实施例对本发明作进一步详细描述。
[0020]
一种高球形度低氧含量tial合金粉末制备方法,包括如下步骤:s1、通过至少两次真空感应熔炼、浇铸成tial合金棒材;tial合金棒材经历至少两次熔炼,最大程度降低了tial合金中杂质元素含量,提高合金纯净度;s2、将步骤s1制备的棒材进行高温相变处理;s3、将步骤s2处理后的棒材进行机械加工得到精加工棒材;s4、以步骤s3制备的精加工棒材为自耗电极2,将自耗电极2放置于加工仓1内;s5、开启真空系统泵组及真空阀门,使得加工仓1内真空度低于10
‑3pa,关闭真空系统泵组及真空阀门;s6、向加工仓1内充入氩气和氦气的混合气体,直至加工仓1内压力为2
×
101pa,氧含量低于50ppm,关闭装有混合气体的气瓶、开启惰性气体闭环系统;惰性气体闭环系统的开启为了保持加工仓1内压力恒定,降低了制粉过程惰性气体使用成本、同时降低了合金粉末中的氧含量;s7、开启驱动器从而使得驱动器带动自耗电极2以30000~33000rpm的速度旋转,开启等离子枪控制器,产生功率为50~60kw的等离子电弧4,等离子电弧4加热高速旋转的自耗电极2端面使其熔化形成液面并形成金属熔滴,金属熔滴快速凝固成tial合金球形金属粉末;粉末球形度得到了提高,粉末平均球形度由85%提高到99%,粉体综合性能指标提高;s8、在高纯惰性气体环境下,对步骤s7制备的金属粉末进行筛分包装。
[0021]
其中,tial合金成分以重量百分含量计如下:al:28~35wt.%、b:≤0.35wt.%、si:≤0.2wt.%、mn:≤4 wt.%、fe:≤0.1wt.%、c:≤0.05wt.%,余量为ti和不可避免的杂质元素。
[0022]
进一步地,步骤s2中高温相变处理在真空环境下,真空度低于10
‑2pa,温度加热至1330~1350℃,保温1~4h,采用水淬冷却;然后在真空环境下回火处理即加热至1300~1320℃,保温1~4h,炉冷冷却。水淬冷却的水冷却速度快,抑制了晶粒快速长大,水淬冷却的目的在于为下一步回火处理提供更多的形核质点,第一次高温加热过程中形成大量的γ相和γ/α相间的细小片层组织;回火处理的目的在于促进水淬产生的形核质点长大,形成细小的γ/α相相间的均匀全片层组织。高温相变处理目的在于细化tial合金组织,将粗大的铸态组织转变为细小的片层组织,片层晶团尺寸减小至100μm左右,为获得离心雾化细小熔滴提供组织基础,使得最终tial合金粉末的球形度高,提高粉体综合性能指标。
[0023]
进一步地,步骤s5中的真空系统泵组包括与加工仓1连接的机械泵与扩散泵,所述机械泵及扩散泵均与控制系统连接。
[0024]
机械泵为预抽泵,用于初步降低加工仓1内真空度至10
‑1pa,扩散泵为真空系统泵组的主泵,用于保证加工仓1真空度低于10
‑3pa。
[0025]
进一步地,加工仓1与扩散泵之间连接有钛升华泵,所述钛升华泵与控制系统连接。
[0026]
钛升华泵用于吸收加工仓1中的氧,从而使加工仓1中氧含量进一步降低,保证制备tial合金金属粉末氧含量低于50ppm。
[0027]
进一步地,步骤s6中惰性气体闭环系统用于干燥净化循环使用的惰性气体,包括输入端和输出端分别与加工仓1连接的气体循环管路3,所述气体循环管路3上依次连接有气体过滤器和压缩机。
[0028]
进一步地,所述步骤s7中tial合金球形金属粉末的球形度≥98%,tial合金球形金属粉末氧含量低于50ppm。
[0029]
一种实现高球形度低氧含量tial合金粉末制备方法的设备,所述设备包括加工仓1,所述加工仓1上设置有用于带动自耗电极2旋转的驱动器,与驱动器相对应的位置设置有等离子枪,所述等离子枪由等离子枪控制器控制,所述加工仓1上连接有真空系统泵组,所述真空系统泵组通过控制系统与设置于加工仓1上的氧探头5连接。
[0030]
进一步地,所述加工仓1上还设置有惰性气体闭环系统,所述惰性气体闭环系统包括气体循环管路3,所述气体循环管路3的输入端和输出端分别与加工仓1连接,所述气体循环管路3上依次连接有气体过滤器和压缩机。
[0031]
惰性气体闭环系统用于干燥净化循环使用的惰性气体,降低了制粉过程惰性气体使用成本、同时减小了合金粉末中氧含量。
[0032]
进一步地,所述真空系统泵组包括与加工仓1连接的机械泵与扩散泵,所述机械泵及扩散泵均与控制系统连接。
[0033]
机械泵为预抽泵,用于初步降低加工仓1内真空度至10
‑1pa,扩散泵为真空系统主泵,用于保证加工仓1真空度低于10
‑3pa。
[0034]
进一步地,所述加工仓1与扩散泵之间连接有钛升华泵,所述钛升华泵与控制系统
连接。
[0035]
钛升华泵用于吸收加工仓1中的氧,从而使加工仓1中氧含量进一步降低,保证制备tial合金金属粉末氧含量低于50ppm。
[0036]
下面结合具体的工艺处理过程进行说明:实施例1:本发明提供了一种高球形度低氧含量tial合金粉末制备方法,具体按照如下步骤实施:步骤1:通过两次真空感应熔炼、浇铸成tial4522xd合金棒材;其中,tial4522xd合金成分以重量百分含量计如下:al: 30wt.%、b:0.2 wt.%、si:0.1 wt.%、mn:3wt.%、fe:0.07wt.%、c:0.02wt.%、o:40ppm,余量为ti和不可避免的杂质元素。
[0037]
步骤2:将步骤1制备的棒材进行高温相变处理,即将步骤1制备的棒材在真空度为9
×
10
‑3pa的真空环境下加热至1350℃,保温2h,水淬冷却;真空环境下回火处理即加热至1310℃,保温2h,炉冷冷却高温相变处理。
[0038]
步骤3:将步骤2高温相变处理后棒材精车加工。
[0039]
步骤4:以步骤3制备的精加工棒材为自耗电极2置于制粉设备加工仓1内。
[0040]
步骤5:开启真空系统中阀门a、阀门d和机械泵至真空计e显示真空度为10
‑1pa;开启扩散泵和阀门c、阀门b,至真空计g显示真空度达10
‑2pa;开启钛升华泵,至真空计f显示真空度低于10
‑3pa;关闭阀门a、阀门b、阀门c、阀门d。
[0041]
步骤6:通过气体组件向加工仓1内充入体积比例为1:9的氩气和氦气混合气体,至加工仓1内压力为2
×
101pa;关闭装有混合气体的气瓶,开启惰性气体闭环系统中的压缩机及气体过滤器,保证加工仓1内的压力恒定为2
×
101pa,氧探头5显示氧含量低于50ppm。
[0042]
步骤7:开启驱动器带动自耗电极2以33000rpm超高速旋转,开启等离子枪控制器,产生功率58kw的等离子电弧4,等离子电弧4加热自耗电极2端面使其熔化形成液面,液面在离心力作用下从自耗电极2端面甩出,被甩出的熔滴运动过程中快速凝固成球形金属粉末,粉末收集仓用于收集金属粉末。
[0043]
步骤8:在高纯惰性气体环境下,对步骤7制备的金属粉末进行筛分包装:筛分为粉末粒度15~53μm,动态图像分析法检测粉末平均球形度为99%,氧氮氢分析仪测试tial4522xd合金粉末氧含量为40ppm。
[0044]
由图2~3可以看出,未采用本发明制备的tial合金粉末球形度差;采用本发明制备的tial合金粉末球形度高,平均值为99%;由图4可以看出,采用本发明技术制备的tial合金粉末所生产的tial合金低压涡轮叶片的截面微观组织无孔隙等缺陷。
[0045]
对比本发明制备tial合金粉末与传统离心雾化技术制备相同粒径粉末的粉体综合性能,如表1所示;不同工艺制备粉末中氧含量对比见表2所示。
[0046]
表1 tial合金粉末综合性能对比表
表2
ꢀꢀ
tial合金粉末氧含量对比表由表1可以看出,采用本发明一种高球形度低氧含量tial合金粉末制备方法得到的tial合金粉末,其球形度、松装密度及振实密度均比传统技术制备的tial合金粉末高,而霍尔流速比传统技术低。
[0047]
由表2可以看出,采用本发明一种高球形度低氧含量tial合金粉末制备方法得到的tial合金粉,其氧含量比传统技术制备的tial合金粉末低。
[0048]
可见,本发明采用的方法得到的tial合金粉末的粉体综合性能指标得到了显著提升,粉末球形度提高,粉末含氧量降低。
[0049]
实施例2:本发明提供了一种高球形度低氧含量tial合金粉末制备方法,具体按照如下步骤实施:步骤1:通过三次真空感应熔炼、浇铸成tial4822合金棒材;其中,tial4822合金成分以重量百分含量计如下:al:35wt.%、si:0.01wt.%、 fe:0.1wt.%、c:0.025wt.%、o:40ppm,余量为ti和不可避免的杂质元素。
[0050]
步骤2:将步骤1制备的棒材进行高温相变处理,即将步骤1制备的棒材在真空度为8.8
×
10
‑3pa的真空环境下加热至1340℃,保温1.5h,水淬冷却;真空环境下回火处理即加热至1300℃,保温1.5h,炉冷冷却高温相变处理。
[0051]
步骤3:将步骤2高温相变处理后棒材精车加工。
[0052]
步骤4:以步骤3制备的精加工棒材为自耗电极2置于制粉设备加工仓1内。
[0053]
步骤5:开启真空系统中阀门a、阀门d和机械泵至真空计e显示真空度达10
‑1pa;开启扩散泵和阀门c、阀门b,至真空计g显示真空度达10
‑2pa;开启钛升华泵,至真空计f显示真空度低于10
‑3pa;关闭阀门a、阀门b、阀门c、阀门d。
[0054]
步骤6:通过气体组件向加工仓1内充入体积比例为1:9的氩气和氦气混合气体,至加工仓1内压力为2
×
101pa;关闭装有混合气体的气瓶、开启惰性气体闭环系统中的压缩机及气体过滤器,保证加工仓1内的压力恒定为2
×
101pa,氧探头5显示氧含量低于50ppm。
[0055]
步骤7:开启驱动器带动自耗电极2以32000rpm超高速旋转,开启等离子枪控制器,产生功率55kw的等离子电弧4,等离子电弧4加热自耗电极2端面使其熔化形成液面,液面在离心力作用下从自耗电极2端面甩出,被甩出的熔滴运动过程中快速凝固成球形金属粉末。
[0056]
步骤8:在高纯惰性气体环境下,对步骤7制备的金属粉末进行筛分包装:筛分为粉末粒度45~75μm,动态图像分析法检测粉末平均球形度为98.5%,氧氮氢分析仪测试tial4822合金粉末氧含量为40ppm。
[0057]
实施例3:本发明提供了一种高球形度低氧含量tial合金粉末制备方法,具体按照如下步骤实施:步骤1:通过四次真空感应熔炼、浇铸成tial4722合金棒材;其中,tial4722合金成分以重量百分含量计如下:al:28wt.%、o:45ppm,余量为ti和不可避免的杂质元素。
[0058]
步骤2:将步骤1制备的棒材进行高温相变处理,即将步骤1制备的棒材在真空度为8.5
×
10
‑3pa的真空环境下加热至1330℃,保温3h,水淬冷却;真空环境下回火处理即加热至1320℃,保温3h,炉冷冷却高温相变处理。
[0059]
步骤3:将步骤2高温相变处理后棒材精车加工。
[0060]
步骤4:以步骤3制备的精加工棒材为自耗电极2置于制粉设备加工仓1内。
[0061]
步骤5:开启真空系统中阀门a、阀门d和机械泵至真空计e显示真空度达10
‑1pa;开启扩散泵和阀门c、阀门b,至真空计g显示真空度达10
‑2pa;开启钛升华泵,至真空计f显示真空度低于10
‑3pa;关闭阀门a、阀门b、阀门c、阀门d。
[0062]
步骤6:通过气体组件向加工仓1内充入体积比例为1:9的氩气和氦气混合气体,至加工仓1内压力为2
×
101pa;关闭装有混合气体的气瓶、开启惰性气体闭环系统中的压缩机及气体过滤器,保证加工仓1内的压力恒定为2
×
101pa,氧探头5显示氧含量低于50ppm。
[0063]
步骤7:开启驱动器带动自耗电极2以31000rpm超高速旋转,开启等离子枪控制器,产生功率56kw的等离子电弧4,等离子电弧4加热自耗电极2端面使其熔化形成液面,液面在离心力作用下从自耗电极2端面甩出,被甩出的熔滴运动过程中快速凝固成球形金属粉末。
[0064]
步骤8:在高纯惰性气体环境下,对步骤7制备的金属粉末进行筛分包装:筛分为粉末粒度25~90μm,动态图像分析法检测粉末平均球形度为99%,氧氮氢分析仪测试ti2alnb合金粉末氧含量为45ppm。
[0065]
tial合金由于本征脆性差,锻造或拉拔过程均易出现裂纹,传统棒材制造方式均仅为熔炼后浇铸成型,铸造过程受冷却速率等多重因素影响,合金内部组织粗大且存在强烈的枝晶,而晶界处由于缺陷和杂质元素聚集程度高,熔点相对晶内低,离心雾化过程中优先从晶界熔融,粗大晶粒和强烈枝晶必然会导致大尺寸熔滴的形成,大尺寸熔滴易变形凝固成非球形粉末,组织细化后晶粒越小产生的熔滴越小,而熔滴越小,则其冷却速度越快,对应球化速率越高,由此形成粉末球形度越好。
[0066]
本发明所用工艺中自耗电极以30000~33000rpm速度超高速旋转,根据以下公式可知在自耗电极材料和直径都确定的情况下,自耗电极转速越大,获得熔滴尺寸越小,对应细小熔滴快速凝固过程中变形越小,粉末球形度越好。
[0067]
其中:ω为自耗电极转速,d为自耗电极直径,ρ为自耗电极密度,γ为熔滴表面张
力,d为粉末颗粒直径。
[0068]
本发明超高真空系统设计的钛升华泵以钛为吸气材料,吸附加工仓1内氧,同时结合大抽速的扩散泵,保证加工仓1内真空度极低(低于10
‑3pa),这是由于加工仓1内氧含量的高低主要是由真空系统决定的,所述的惰性气体闭环系统在保证加工过程中加工仓1内处于正压力环境,导致外界空气无法吸入加工仓1内,这样就保证了加工仓1内氧含量低于50ppm。
[0069]
以上所述仅是本发明的具体实施方式,使本领域技术人员能够理解或实现本发明。对这些实施例的多种修改对本领域的技术人员来说将是显而易见的,本文中所定义的一般原理可以在不脱离本发明的精神或范围的情况下,在其它实施例中实现。
[0070]
应当理解的是,本发明并不局限于上述已经描述的内容,并且可以在不脱离其范围进行各种修改和改变。本发明的范围仅由所附的权利要求来限制。