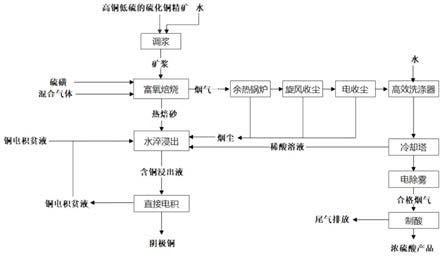
1.本发明涉及有色金属冶炼领域,特别地,涉及一种高铜低硫的硫化铜精矿的富氧焙烧方法。此外,本发明还涉及一种包括上述高铜低硫的硫化铜精矿的富氧焙烧方法获得的阴极铜。
背景技术:2.铜是人类最早发现和使用的金属之一,是国民经济发展中不可或缺的基础金属。铜具有许多可贵的物理、化学特性,是优良的导电和导热体,用于生活和生产中的方方面面。2002年,我国超越美国成为世界上最大的铜消费国,但是铜资源储量占有率低,资源禀赋差,对外依存度高。中南部非洲(赞比亚、刚果(金))有著名的卢富里安(lufilian)铜矿带,是世界上规模最大、铜品位最高的沉积层控铜矿带,已成为我国主要的铜资源海外供应基地之一。
3.中南部非洲成矿带中铜资源禀赋好,具有铜品位高、杂质元素含量低、开采条件好等优点,但是矿石中含硫量低且不稳定。当地基础设施落后,工业基础薄弱,劳动力专业素质整体较差,大部分工业产品和原材料需要进口,传统的火法冶炼处理高铜低硫的硫化铜精矿存在诸多的限制因素,因此,选用合适的工艺技术处理此部分资源至关重要。适合处理高铜低硫硫化铜精矿的冶金工艺主要为焙烧-浸出-(萃取)-电积工艺,该工艺具有投资省、建设周期短、见效果快、适应性强等优点,但是,此工艺能否顺利生产的关键点主要取决于富氧焙烧工序,如果富氧焙烧工序控制不当,将无法获得较高的铜浸出率和制酸转化率。。
技术实现要素:4.本发明提供了一种高铜低硫的硫化铜精矿的富氧焙烧方法,以解决针对处理高铜低硫的硫化铜精矿时,铜浸出率低,制酸转化率低的技术问题。
5.本发明采用的技术方案如下:
6.一种高铜低硫的硫化铜精矿的富氧焙烧方法,包括以下步骤:
7.s1、将高铜低硫的硫化铜精矿进行调浆,制成矿浆;
8.s2、将矿浆雾化,再喷入焙烧炉内,并向焙烧炉内加入硫磺和通入混合气体,进行富氧焙烧,获得烟气一和热焙砂;
9.s3、将步骤s2中获得烟气一依次经过余热锅炉、旋风收尘器、电收尘器进行烟气一降温和收尘,获得烟气二和烟尘;
10.s4、将步骤s3中的烟气二依次通过净化系统中的高效洗涤器、气体冷却塔和电除雾器进行除尘和降温,并利用净化系统补充的水吸收烟气二中的so3,产生稀酸溶液,将经过净化系统后的合格烟气进入制酸系统,制备浓硫酸产品;
11.s5、将步骤s2中获得热焙砂、步骤s3中的烟尘、步骤s4中的稀酸溶液与铜电积贫液进行水淬浸出,将水淬浸出后获得含铜浸出液进行直接电积,制备阴极铜。
12.进一步地,高铜低硫的硫化铜精矿包括cu 60%~68%,s 10%~18%,fe 0.8%
~5%。
13.进一步地,步骤s3中余热锅炉的出口温度为350℃~400℃;旋风收尘器的出口温度为330℃~380℃;电收尘器的出口温度为280℃~350℃,出口含尘量≤0.2g/nm3。
14.进一步地,步骤s4中的高效洗涤器的出口温度为60℃~80℃;气体冷却塔的出口温度20℃~40℃;电除雾器的出口酸雾量≤5mg/nm3;稀酸溶液中的硫酸含量为35g/l~55g/l。
15.进一步地,步骤s4中的制酸系统包括以下步骤:将合格烟气经过干燥塔后,通过鼓风机引流,依次经过ⅲ、ⅰ换热器,温度升至400℃~420℃,进入转化器,经过转化器的一、二、三段转化和换热后,温度降至240℃~260℃,合格烟气经过省煤器回收多余的热量后降至160℃~180℃,进入一吸塔,用98%的硫酸吸收合格烟气中的so3,再将合格烟气依次经过ⅳ、ⅱ换热器进行换热,升温至400℃后进入转化器的四段进行第二次转化,再经过ⅳ换热器降温至160℃~180℃,采用98%硫酸吸收合格烟气中的so3,经除雾器除沫、除雾后的尾气进入二吸塔,将达标后的尾气排放。
16.进一步地,步骤s2中富氧焙烧的包括:将硫磺向焙烧炉中喷入,硫磺采用粒度为2mm~8mm的硫磺粉,硫磺的喷入量为硫化铜精矿干重的0~10%;向沸腾的焙烧炉的风室内通入氧气和空气的混合气体,混合气体的含氧量浓度为25%~35%,混合气体的流量为16000m3/h~21000m3/h;富氧焙烧的温度为740℃~780℃,炉底压力为16kpa~22kpa。
17.进一步地,步骤s1中调浆采用浮选后的硫化铜精矿矿浆或硫化铜干精矿与水混合,搅拌3h~6h;矿浆的质量浓度为74%~78%。
18.进一步地,步骤s5中水淬浸出的反应温度为40℃~60℃,反应时间为5h~9h;铜电积贫液的含铜量为35g/l~45g/l,硫酸浓度为120g/l~180g/l。
19.进一步地,还包括将步骤中s5直接电积后得到的铜电积贫液回流进行水淬浸出。
20.根据本发明的另一方面,还提供了一种上述高铜低硫的硫化铜精矿的富氧焙烧方法获得的阴极铜。
21.本发明具有以下有益效果:
22.本发明的高铜低硫的硫化铜精矿的富氧焙烧方法,将硫化铜精矿进行调浆,调制成矿浆,将雾化后的矿浆喷入焙烧炉内,焙烧炉通过控制风量、硫磺添加量和炉温实现富氧焙烧。焙烧炉产生的烟气一依次通过余热锅炉、旋风收尘器、电收尘器进行收尘和降温,将获得的烟气二继续依次通过高效洗涤器、气体冷却塔和电除雾器进一步除尘和降温,获得合格烟气。合格烟气通过制酸获得浓硫酸产品。焙烧产生的热焙砂、收尘设备收集的烟尘、净化系统获得的稀酸溶液、铜电积贫液进入水淬浸出系统用于浸出铜,再将含铜浸出液进行直接电积,制备阴极铜。另外,上述高铜低硫的硫化铜精矿的富氧焙烧方法中,烟尘参与水淬浸出,由于烟尘中的含铜高,最高可占高铜低硫的硫化铜精矿含铜的50%,从而有效保证铜的回收率。上述高铜低硫的硫化铜精矿的富氧焙烧方法,解决了高铜低硫硫化铜精矿焙烧过程中,因矿石性质变化导致的富氧焙烧无法正常生产的问题。实现了硫化铜精矿中铜的高回收率,并能充分利用硫化铜精矿中的硫制备合格的浓硫酸产品。该方法具有成本低、综合回收率高、操作简单的特点。
23.除了上面所描述的目的、特征和优点之外,本发明还有其它的目的、特征和优点。下面将参照附图,对本发明作进一步详细的说明。
附图说明
24.构成本技术的一部分的附图用来提供对本发明的进一步理解,本发明的示意性实施例及其说明用于解释本发明,并不构成对本发明的不当限定。在附图中:
25.图1是本发明优选实施例的高铜低硫的硫化铜精矿的富氧焙烧方法工艺流程图。
具体实施方式
26.需要说明的是,在不冲突的情况下,本技术中的实施例及实施例中的特征可以相互组合。下面将参考附图并结合实施例来详细说明本发明。
27.图1是本发明优选实施例的高铜低硫的硫化铜精矿的富氧焙烧方法工艺流程图。
28.如图1所示,本实施例的高铜低硫的硫化铜精矿的富氧焙烧方法,包括以下步骤:
29.s1、将高铜低硫的硫化铜精矿进行调浆,制成矿浆;
30.s2、将矿浆雾化,再喷入焙烧炉内,并向焙烧炉内加入硫磺和通入混合气体,进行富氧焙烧,获得烟气一和热焙砂;
31.s3、将步骤s2中获得烟气一依次经过余热锅炉、旋风收尘器、电收尘器进行烟气一降温和收尘,获得烟气二和烟尘;
32.s4、将步骤s3中的烟气二依次通过净化系统中的高效洗涤器、气体冷却塔和电除雾器进行除尘和降温,并利用净化系统补充的水吸收烟气二中的so3,产生稀酸溶液,将经过净化系统后的合格烟气进入制酸系统,制备浓硫酸产品;
33.s5、将步骤s2中获得热焙砂、步骤s3中的烟尘、步骤s4中的稀酸溶液与铜电积贫液进行水淬浸出,将水淬浸出后获得含铜浸出液进行直接电积,制备阴极铜。
34.本发明的高铜低硫的硫化铜精矿的富氧焙烧方法,将硫化铜精矿进行调浆,调制成矿浆,将雾化后的矿浆喷入焙烧炉内,焙烧炉通过控制风量、硫磺添加量和炉温实现富氧焙烧。焙烧炉产生的烟气一依次通过余热锅炉、旋风收尘器、电收尘器进行收尘和降温,将获得的烟气二继续依次通过高效洗涤器、气体冷却塔和电除雾器进一步除尘和降温,获得合格烟气。合格烟气通过制酸获得浓硫酸产品。焙烧产生的热焙砂、收尘设备收集的烟尘、净化系统获得的稀酸溶液、铜电积贫液进入水淬浸出系统用于浸出铜,再将含铜浸出液进行直接电积,制备阴极铜。另外,上述高铜低硫的硫化铜精矿的富氧焙烧方法中,烟尘参与水淬浸出,由于烟尘中的含铜高,最高可占高铜低硫的硫化铜精矿含铜的50%,从而有效保证铜的回收率。上述高铜低硫的硫化铜精矿的富氧焙烧方法,解决了高铜低硫硫化铜精矿焙烧过程中,因矿石性质变化导致的富氧焙烧无法正常生产的问题。实现了硫化铜精矿中铜的高回收率,并能充分利用硫化铜精矿中的硫制备合格的浓硫酸产品。该方法具有成本低、综合回收率高、操作简单的特点。
35.针对高铜低硫的硫化铜精矿在焙烧时,存在铜浸出率和烟气制酸相互制约的难题。因此,可以利用浮选硫化铜精矿粒度较细的特点,将高铜低硫的硫化铜精矿调制成适宜浓度的矿浆,通过雾化喷入焙烧炉中,实现物料的均匀分散,高效的完成焙烧过程。另外,通过控制焙烧炉风量、硫磺添加量和焙烧温度等参数,实现硫化铜精矿铜矿物相高效转化,将硫化铜精矿铜矿物转化为硫酸铜和氧化铜,转化后的铜矿物极易被硫酸浸出,从而获得较高的回收率,具体反应过程如下:2cu2s+5o2=2cuso4+2cuo、cu2s+2o2=2cuo+so2。焙烧炉产生的烟气依次通过余热锅炉、旋风收尘器和电收尘器设备,实现烟气一降温和烟尘回收,回
收的烟尘通过收集进入水淬浸出系统。收尘之后的烟气二进入净化系统,进一步的收尘和降温,净化系统中吸收了烟气二中的so3产生稀酸溶液,并捕集烟气二中的烟尘,稀酸溶液进入水淬浸出系统,通过收尘系统和净化系统能够有效回收烟气中的烟尘和so3,有效确保了烟气中硫和铜的回收利用。净化之后的合格烟气进入制酸系统,制备出合格的硫酸产品。
36.上述步骤s3中将余热锅炉、旋风收尘器和电收尘器采用串联工艺,即烟气一依次通过这三个设备,经过余热锅炉以充分利用该设备的换热和收尘能力,将入口大于700℃的烟气一降至350℃~400℃,在余热锅炉中通过热交换,余热锅炉可以产生蒸汽供用气部门使用。同时烟气一经过余热锅炉时,烟气一由于流速下降,粗颗粒烟尘会因重力下降,掉入灰斗中,灰斗中的烟尘进入水淬中回收。经过余热锅炉降温和除尘后烟气温度仍然较高,可以达到350℃~400℃,且仍然含有部分较粗的颗粒,这些都不利于电收尘设备运行。因此,在余热锅炉和电收尘器之间增加了旋风收尘器。旋风收尘器主要是利用烟气一以一定的速度切向给入,通过离心力的作用,较粗的烟尘通过底部排出,收集的烟尘进入水淬系统回收,较细的颗粒和烟气一从上部排出,同时烟气通过该设备可以降温20℃~40℃。经过旋风收尘器之后的烟气一再进入电收尘器,电收尘器是在两个曲率半径相差较大的金属阳极和阴极上,通过高压直流电,维持一个足以使气体电离的静电场,气体电离后所产生的电子:阴离子和阳离子,吸附在通过电场的粉尘上,使粉尘获得电荷,从而达到收尘的目的。通过电收尘的灰斗收集掉落下来的烟尘,烟尘进入水淬系统。同时烟气一在电收尘器设备中进一步降温,需要控制电收尘器的出口温度不能超过350℃。
37.上述步骤s4中的高效洗涤器、气体冷却塔和电除雾器三个设备也是依次串联的,烟气二从电收尘出来后,依次通过高效洗涤器、气体冷却塔和电除雾器。烟气二通过高效洗涤器,通过利用该设备的核心装置逆喷管(一根内部衬有石墨的玻璃钢管,给入烟气二温度太高容易融化)实现功能,主要是将电收尘出口280℃~350℃的烟气二降至60℃~80℃。逆喷管主要是溶液从底部喷入产生一定的液柱,烟气二从顶部给入,形成逆向流动,形成烟气二和液体充分的接触,从而降温、除尘和吸收so3,除尘功能主要利用液体对烟气二颗粒可以进行捕收实现的。烟气二主要含有so2少量的so3,so2难以被水直接吸收产生硫酸,而so3容易被水吸收产生硫酸,所以在高效洗涤器中会产生稀酸溶液。气体冷却塔是进一步降低流经高效洗涤器烟气二的温度,控制不高于40℃。该设备中烟气二从下部给入,液体从顶部喷入,也是烟气二和液体实现逆向流动和充分接触,实现降温。除尘和吸收so3的目的,原理和高效洗涤器一样。电除雾器将流经气体冷却塔的烟气二中的酸雾去除,使烟气二净化后出口的酸雾量≤5mg/nm3。因此,将高效洗涤器、气体冷却塔和电除雾器依次串联排布,利用了高效洗涤器能够快速的降低烟气二的温度,气体冷却塔进一步的降低烟气二的温度,电除雾器能够去除高效洗涤器和气体冷却塔产生的酸雾。稀酸溶液在高效洗涤器、冷却塔和电除雾器中都有产生,而且三个设备产生的稀酸溶液在净化系统中循环,并仅有一个出口去往水淬系统进行水淬浸出。通过向净化系统补充水以吸收烟气二中的so3。由于净化系统主要是用于吸收烟气二中的so3,而烟气二中的so2则基本不会被吸收,所以经过净化系统净化后的合格烟气含有so2,将合格烟气进入制酸系统,制备浓硫酸产品。
38.本实施例中,高铜低硫的硫化铜精矿包括cu 60%~68%,s 10%~18%,fe 0.8%~5%。
39.高铜低硫的硫化铜精矿来自高铜低硫的矿石。高铜低硫的矿石经过选矿后铜精矿
可以达到60%以上,主要是因为其铜矿以辉铜矿为主。另外因为该类型的矿是沉积型矿床,硫化铁类矿物含量低,加上浮选过程也只能捕收硫化类矿物,因此形成了高铜低硫的特点。常规的铜矿类型主要以斑岩型和矽卡岩型为主,属于硫化矿型,其主要的铜矿物是黄铜矿,选矿得到的铜精矿其铜品位一般在20~32%,硫品位15~30%,其铜硫比较低,属于常规性的铜精矿。针对硫化铜浮选精矿目前冶炼主要有火法工艺,火法工艺包括熔池熔炼技术和闪速熔炼,熔池熔炼技术主要以艾萨炉、奥斯迈特炉、侧吹炉和底吹炉等为主,闪速熔炼主要以山东阳谷祥光为主要代表,但是在两种方式处理高铜低硫的硫化铜精矿过程中,需要补充添加硫化铁矿和石英渣等辅助材料,用于造渣。另外,上述高铜低硫的硫化铜精矿的硫的含量也偏低,无法实现火法运行所需的热平衡。焙烧-湿法工艺也可用于冶炼硫化铜精矿,其中的富氧焙烧常常用来处理常规的硫化铜精矿,但是针对高铜低硫的硫化铜精矿采用富氧焙烧存在以下方面的技术难题:(1)热量无法平衡,热量不足;(2)烟气制酸不同,常规的硫化铜精矿采用富氧焙烧,烟气中的二氧化硫浓度高,制酸相对容易,然而高铜低硫的硫化铜精矿的硫含量较低,制酸较难;(3)高铜低硫的硫化铜精矿在炉温控制方面,要求更为严格。
40.本实施例中,步骤s3中余热锅炉的出口温度为350℃~400℃。旋风收尘器的出口温度为330℃~380℃。电收尘器的出口温度为280℃~350℃,出口含尘量≤0.2g/nm3。由于前期的焙烧炉温需要控制在740℃~780℃范围内,因此,进入余热锅炉的温度通常在700℃~740℃,余热锅炉的换热一方面可以通过调节锅炉汽包的压力来实现,但是出口温度不能控制过低,如果控制太低,导致电收尘器温度低于250℃,低于烟气的露点,将造成电收尘设备淌水,淌水主要为稀酸,造成设备腐蚀无法正常生产,在正常生产中需要保持余热锅炉、旋风收尘器和电收尘器所收集的烟尘是干燥的。另一方面,实际生产中电收尘器的出口温度控制不超出350℃,如果高于此温度,烟气进入高效洗涤器中将造成逆喷管融化,高效洗涤器的逆喷管是生产中重要关键设备。控制烟尘含量过高说明前期收尘设备效果差,另外也将影响净化系统的正常生产。
41.本实施例中,步骤s4中的高效洗涤器的出口温度为60℃~80℃。气体冷却塔的出口温度20℃~40℃。电除雾器的出口酸雾量≤5mg/nm3。稀酸溶液中的硫酸含量为35g/l~55g/l。最终要实现烟气二从气体冷却塔出来后接近常温,即范围在20℃~40℃,才能确保电除雾器进行高效工作,控制酸雾量≤5mg/nm3,避免发生腐蚀。
42.本实施例中,步骤s4中的制酸系统包括以下步骤:将合格烟气经过干燥塔后,通过鼓风机引流,依次经过ⅲ、ⅰ换热器,温度升至400℃~420℃,进入转化器,经过转化器的一、二、三段转化和换热后,温度降至240℃~260℃,合格烟气经过省煤器回收多余的热量后降至160℃~180℃,进入一吸塔,用98%的硫酸吸收合格烟气中的so3,再将合格烟气依次经过ⅳ、ⅱ换热器进行换热,升温至400℃后进入转化器的四段进行第二次转化,再经过ⅳ换热器降温至160℃~180℃,采用98%硫酸吸收合格烟气中的so3,经除雾器除沫、除雾后的尾气进入二吸塔,将达标后的尾气排放。净化之后的合格烟气制酸主要是利用其中的so2,净化后的合格烟气进入制酸系统,制酸系统主要采用“3+1”的两转两吸工艺,其中在转化器中利用触媒五氧化二钒作为催化剂,可以实现烟气中的so2转化为so3。合格烟气
→
干燥塔
→
鼓风机引流
→ⅲ
换热器
→ⅰ
换热器
→
一段转化
→ⅰ
换热器
→
二段转化
→ⅱ
换热器
→
三段转化
→ⅲ
换热器
→
一吸塔
→ⅳ
换热器
→ⅱ
换热器
→
四段转化
→ⅳ
换热器
→
二吸塔
→
尾气处
理合格排放。通过以上的烟气流程,可以看出烟气在进入一吸塔之前经过了三次转化,在进入二吸塔之前经过一次转化,即3+1的两转两吸工艺。转化器是一个圆柱形的设备,分为四层即对应的ⅰ到ⅳ层转化,每层都装有五氧化二钒作为触媒,起到催化的作用,能够将合格烟气中的so2转化为so3。合格烟气的吸收是在吸收塔(一吸塔和二吸塔)中实现的,转化出来的合格烟气是从底部进入,吸收塔顶部喷入98%的浓硫酸,通过硫酸和合格烟气的交换,能够充分吸收合格烟气中的so3制备成合格的硫酸产品,经过两次吸收塔的吸收之后,能够实现合格烟气中的so3的充分利用,经过简易处理后就能达标排放。至于转化系统中的温度控制,主要控制两个方面的温度,一是要控制进入转化层的温度,二是要控制进入吸收塔的温度。制酸系统制备获得的浓硫酸产品含硫酸质量分数为92.5~98.5%。
43.本实施例中,步骤s2中富氧焙烧的包括:将硫磺向焙烧炉中喷入,硫磺采用粒度为2mm~8mm的硫磺粉,硫磺的喷入量为硫化铜精矿干重的0~10%。向沸腾的焙烧炉的风室内通入氧气和空气的混合气体,混合气体的含氧量浓度为25%~35%,混合气体的流量为16000m3/h~21000m3/h。富氧焙烧的温度为740℃~780℃,炉底压力为16kpa~22kpa。上述高铜低硫的硫化铜精矿含硫较低,而硫的燃烧是热量的主要来源,因此,加入硫磺一方面是为了解决热量不足的问题,另一方面是为了解决烟气中硫含量不够,影响制酸的问题。但是,此处不能添加煤粒,虽然煤粒可以作为补充燃料增加热量,解决热量不足的问题,但是无法解决烟气中硫含量的问题。硫磺粉的粒度控制在2mm~8mm,当硫磺粉过细,在加入沸腾焙烧炉中,会被炉底鼓入的混合空气吹到炉顶,并在炉顶燃烧,造成焙烧炉温度难以控制,甚至会造成无法正常生产。硫磺颗粒过粗将造成加入焙烧炉困难,造成硫磺粉加入管堵塞。混合气体的含氧量浓度为25%~35%,当焙烧炉的氧气浓度低于25%,将造成焙烧炉内缺氧,原料无法充分焙烧,转化不够,形成的焙砂在水淬和浸出的过程中,浸出率下降,铜的回收率也下降。氧气浓度超过35%,一方面,氧气浓度较高,需要制氧站制备更多的氧气(浓度70%~80%左右)以和空气混合,造成电力浪费;另一方面,混合气体的氧气浓度过高,将造成燃烧后剩余大量的氧气,降低烟气一中so2浓度,不利后续制酸。硫磺加入量位0~10%,硫磺粉的加入量主要依据炉温进行调整,如果炉温过高则少加或者停止硫磺加入,如果炉温过低则需多加硫磺,以控制炉温在740℃~780℃的范围。混合气体的流量为16000m3/h~21000m3/h,在此流量下的混合气体使得所处理的物料能够在炉内形成沸腾,当混合气体的流量过低,物料无法沸腾,会压在炉底导致压炉,形成生产事故;当混合气体的流量过高,会将加入的物料从炉顶吹出,无法在炉内实现焙烧。富氧焙烧的温度为740℃~780℃,焙烧炉温控制在740℃~780℃,使得所处理的物料进行充分焙烧,所获得的热焙砂具有较高的铜浸出率,实现更好的经济效益。炉温过低可能无法实现有效的焙烧,热焙砂的铜浸出率会出现明显的下降,炉温过高,将会使物料中的低熔点矿物熔融,造成热焙烧炉结疤和过烧的现象,一方面影响焙烧炉的正常生产,另一方面也将造成铜的浸出率下降。上述炉底压力为16kpa~22kpa,与混合气体配合,共同促使所处理的物料在炉内沸腾。
44.本实施例中,步骤s1中调浆采用浮选后的硫化铜精矿矿浆或硫化铜干精矿与水混合,搅拌3h~6h。矿浆的质量浓度为74%~78%。
45.本实施例中,步骤s5中水淬浸出的反应温度为40℃~60℃,反应时间为5h~9h。铜电积贫液的含铜量为35g/l~45g/l,硫酸浓度为120g/l~180g/l。将上述获得的热焙砂、烟尘稀酸溶液、铜电积贫液进入水淬槽水淬浸出,再输送到浸出槽继续浸出,利用获得的稀酸
溶液把热焙砂中的铜浸出到溶液中,最后通过浓密机将不能浸出的尾渣和含铜的浸出液分离,得到含铜浸出液。含铜浸出液通过过滤处理后进入电积系统,电积系统可以将含铜浸出液中的铜电积得到合格的阴极铜。
46.本实施例中,还包括将步骤中s5直接电积后得到的铜电积贫液回流进行水淬浸出。经过直接电积后得到一个电积后的铜电积贫液,因为直接电积处理后,铜电积贫液中的铜浓度下降,因此,需要将铜电积贫再次返回到水淬槽,与烟尘、热焙烧、稀酸溶液在水淬槽中停留一定时间后(30分钟左右)打入浸出槽。铜电积贫液用来浸出焙砂,以提高铜浓度,从而又可以用于直接电积,实现不断的循环。
47.根据本发明的另一方面,还提供了一种上述高铜低硫的硫化铜精矿的富氧焙烧方法获得的阴极铜。
48.实施例
49.实施例1
50.s1、将含铜61.88%、铁0.85%、硫14.73%的硫化铜干精矿(含水率<10%)与一定量的水在调浆槽中调制,并搅拌6h,制成矿浆,矿浆的质量浓度为76%;
51.s2、将矿浆通过雾化器雾化,再喷入焙烧炉内,干重投量为11.5t/h,将硫磺向焙烧炉中喷入,硫磺采用粒度为3mm~5mm的硫磺粉,硫磺的喷入量为1022.3kg/h,向沸腾的焙烧炉的风室内通入氧气和空气的混合气体,混合气体的含氧量浓度为32%,混合气体的流量为18400m3/h,富氧焙烧的温度为754℃~758℃,炉底压力为18.4kpa,进行富氧焙烧,获得烟气一和热焙砂;
52.s3、将步骤s2中获得烟气一依次经过余热锅炉(出口温度为390℃)、旋风收尘器(出口温度为355℃)、电收尘器(出口温度为331℃,出口含尘量≤0.15g/nm3)进行烟气一降温和收尘,获得烟气二和烟尘;
53.s4、将步骤s3中的烟气二依次通过净化系统中的高效洗涤器(出口温度为68.6℃)、气体冷却塔(出口温度为34.2℃)和电除雾器(出口酸雾量4.5g/nm3)进行除尘和降温,并利用净化系统补充的水吸收烟气二中的so3,产生稀酸溶液,稀酸溶液含硫酸量为48.62g/l,流量为10.2m3/h,将经过净化系统后的合格烟气进入制酸系统,将合格烟气经过干燥塔后,通过鼓风机引流,依次经过ⅲ、ⅰ换热器,温度升至420℃,进入转化器,经过转化器的一、二、三段转化和换热后,温度降至245℃,合格烟气经过省煤器回收多余的热量后降至168℃,进入一吸塔,用98%的硫酸吸收合格烟气中的so3,再将合格烟气依次经过ⅳ、ⅱ换热器进行换热,升温至400℃后进入转化器的四段进行第二次转化,再经过ⅳ换热器降温至170℃,采用98%硫酸吸收合格烟气中的so3,经除雾器除沫、除雾后的尾气进入二吸塔,酸转化率>99.99%,生产93.5%的浓硫酸产品7.5t/h,将达标后的尾气排放;
54.s5、将步骤s2中获得热焙砂、步骤s3中的烟尘、步骤s4中的稀酸溶液和直接电积后得到的铜电积贫液回流至进入水淬槽中,其中铜电积贫液的萃余液量为200m3/h、萃余液含铜43.4g/l、含硫酸为131.2g/l,反应温度为55.6℃,反应时间为0.5h,再输送到浸出槽继续浸出,反应温度为50.5℃,反应时间为6h,浸出矿浆浓度18.3%,铜的浸出率98.4%,利用获得的稀酸溶液把热焙砂中的铜浸出到溶液中,最后通过浓密机将不能浸出的尾渣和含铜的浸出液分离,得到含铜浸出液将含铜浸出液进行直接电积,制备阴极铜。
55.对比例1
56.与实施例1的区别为,调整矿浆浓度为68.5%,使得气体冷却塔出口温度超过40℃,电除雾器的出口酸雾量>5mg/nm3,铜浸出率为95.4%,制酸转化率97.2%,铜浸出率和制酸转化率均不理想。
57.对比例2
58.与实施例1的区别为,硫磺添加量为1500kg/h,使得焙烧炉的炉温超过800℃,导致炉壁挂料严重,热焙砂烧结严重,气体冷却塔的出口温度超过40℃,电除雾器的出口酸雾量>5mg/nm3,铜浸出率83.7%,制酸转化率94.2%,铜浸出率和制酸转化率均不理想。
59.对比例3
60.与实施例1的区别为,混合气体的含氧量浓度为50%,铜浸出率96.7%,制酸转化率90.1%,铜浸出率和制酸转化率均不理想。
61.以上所述仅为本发明的优选实施例而已,并不用于限制本发明,对于本领域的技术人员来说,本发明可以有各种更改和变化。凡在本发明的精神和原则之内,所作的任何修改、等同替换、改进等,均应包含在本发明的保护范围之内。