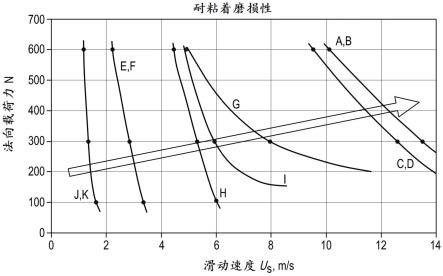
1.本发明总体上涉及轴承部件(/轴承组成部件)(bearing components)及其制造(尤其是热处理)方法。
背景技术:2.机床(machine tools)领域对超精密轴承的高性能钢(/钢材料)解决方案有很高的要求,所述超精密轴承,例如,用于在严酷条件下运行的加工和铣削主轴中。例如,在此类应用中,在转速为42,000rpm(2.5m ndm或者更高,其中“n”为每分钟转速,“dm”为跨滚动体间的节圆直径,单位为mm)时,接触压力可达2.7gpa。这类轴承通常为油气润滑或者脂润滑的角接触球轴承(acbb)。此外,预载荷值须被优化,用以获得主轴在整个速度区间内运行时所需的高刚性,并且防止打滑。这种状态造成轴承卡死失效(seizure falure)的高度风险。在加工和铣削的应用中改善主轴的润滑条件是复杂的。因此,人们一直致力于为此类轴承圈提供高性能的钢材料解决方案。
3.经常用于这种超精密轴承的一种钢料成分是n360 isoextra(由kapfenberg austria旗下的奥钢联集团edelstahl gmbh&co kg销售),具有以下质量百分含量(本发明中亦简写为“mass%”)的名义成分:0.30的c、0.60的si、0.40的mn、15.00的cr、1.00的mo和0.40的ni。然而,由于它是一种不锈钢,所以不是特别适合于应对粘着磨损(卡死失效)的风险。
技术实现要素:4.本教导的一个目的在于披露一种钢材料,例如,用于轴承外圈、轴承内圈或者滚动体之类的轴承部件。所述材料具有改进的组成成分(以下简称“组分”)和/或微观结构,能够降低,例如,在高速运转时,例如,由不良润滑状态所引发的一种或者一种以上的表面损伤(微点蚀)、粘着磨损和/或磨砺磨损(/磨粒磨损/磨料磨损)(abrasive wear),并且/或者能够提高对来自固体颗粒腐蚀(/污染)(contamination)的耐受能力。
5.本教导的一个方面是,所述轴承部件由一种钢合金形成,(例如意图用于冷成形操作的)优选为铬-钼-钒合金粉末冶金工具钢(形成)。
6.例如,根据本发明的教导制造的部件(零件),例如,轴承部件,优选由包括冷压(cold pressing)和烧结(sintering)/热等静压(hot-isostatic pressing,缩写hip)步骤的粉末冶金(p/m)工艺制造的条钢(steel bars)制成。在典型情况下,这种被hip或加固的条钢被热锻,然后被加工成不同的直径。随后,由p/m加工形成的条钢被锻造、轧制或者转化为轴承部件。所述轴承部件经过热处理工序,如后文进一步描述,形成,例如,用于超精密轴承套圈时具有优势的微观结构。
7.出于制造轴承部件之目的,这种形式的钢粉末也可被用于3d打印之类的增材制造工艺(additive manufacturing process)。在这一制造过程中,通常在真空或氩气氛围中,使用局部激光熔化技术。这种制造技术通常需要将基材(substrate)预热到高于室温的温
度,例如,300℃或者以上。预热步骤的目的是控制加工过程中产生的热应力——如果不加控制,所述热应力可能会导致破坏打印金属部件完整性的裂纹的形成。
8.上述过程也可被用于再造(修复)轴承滚道之目的——通过机加工移除滚道的受损层,然后在加工过的滚道上堆积新的金属层,随后通过研磨和/或硬车削等方法完成对新金属层的加工。
9.特别是,优选进行马氏体硬化热处理,该处理造成钢组织(/钢微观结构)(steel microstructure)具有相对较高的导热性和增强的热诱导软化耐受性(resistance to thermally induced softening,即较高的回火抗力)。此外,通过在保持混合物整体硬度足够高的情况下谋求(制造/产生)基体和第二相之间较大的硬度和强度差异,能够实现高应变硬化能力(high strain hardening capability)。在优选情况下,碳化物在钢组织中存在的宽度范围介于0.4~3.4μm之间。
10.本发明教导的一个非限制性方面是以轴承部件形式存在的,例如,适于在使用中降低粘着磨损的冷加工粉末冶金工具钢,该工具钢可以经受以下马氏体热处理:
11.(i)执行600~650℃温度范围内的第一次预热处理(/第一预热处理);
12.(ii)执行850~900℃温度范围内的第二次预热处理(/第二预热处理);
13.(iii)在真空1000~1180℃、优选1100~1150℃温度条件下进行奥氏体化15~30分钟(优选温度范围确保最大的耐磨性,但较低的奥氏体化温度范围(例如,低至1000℃)可在本教导的特定应用需要更高韧性的情况下被采用);
14.(iv)在至少(/最小)(minimum)4~5bar的超压(overpressure)下进行气体淬火;以及
15.(v)回火:在520~560℃温度条件下进行两次回火,例如,在540~560℃温度条件下每次回火1~3小时,优选每次回火1.5~2.5小时,或者,在520~560℃温度条件下进行三次回火,例如,在540~560℃温度条件下每次回火0.5~2.5小时,优选每次回火0.75~1.5小时。
16.以上方法中的每一个步骤都可以在不同的条件下实施,仍然可以得到与本教导一致的改进的微观结构。
17.可选的是,在回火步骤之间可以实施(/执行)深度冻结(deep freezing)。在这种情况下,优选在深度冻结之后对新形成的未回火马氏体进行回火。换言之,在回火步骤之间可以安插(accommodated)一个或者多个深度冻结步骤。例如,如果奥氏体化是在高于1150℃,例如,1180℃温度条件下进行的,那么,取决于被处理部件的壁厚,就可能需要,例如,在-70~-80℃范围内进行0.5~2小时的零下温度处理。
18.在回火以后,轴承部件优选展现出以下一项或者多项微观结构特征:
19.残余奥氏体:0~1.5vol%,优选0~1.0vol%,进一步优选连x射线衍射都检测不到含量;和/或
20.渗碳体:1.0~3.0vol%,优选1.8~2.5vol%;和/或
21.mo2c(富钼m2c型碳化物)正交晶系:0.5~2.5vol%,优选1.2~1.6vol%;和/或
22.铁-α(回火马氏体基体,典型情况下为体心四角体(bct)):80~95vol%,优选83~93vol%;和/或
23.vc(实质上是富钒碳化物):3~13vol%,优选3.5~12vol%。
24.如果钢合金中v的含量小于或等于4mass%,那么铁-α(基体)的含量优选为89~94vol%,进一步优选为90~93vol%,vc的含量优选为3~5vol%,进一步优选为3.5~4.5vol%。另一方面,如果钢合金中v的含量大于4mass%,那么铁-α(基体)的含量优选为81~86vol%,进一步优选为83~85vol%,vc的含量优选为9~14vol%,进一步优选为10~12.5vol%。
25.本教导的一个方面是,所述钢合金具有以下含量(按质量百分比计)的组分:1.25~1.55c(碳)、0.28~0.90si(硅)、0.22~0.54mn(锰)、4.0~5.10cr(铬)、2.80~3.65mo(钼)和3.45~4.0v(钒),钢组分的大部分是铁。在优选情况下,所述钢合金具有以下含量(按质量百分比计)的组分:1.32~1.45c、0.32~0.48si、0.26~0.48mn、4.3~4.85cr、3.35~3.55mo和3.55~3.85v,可选包含0~0.13w、0~0.20ni、0~0.15cu、0~0.8co、0~0.03p和0~0.03s,余量为铁和不可避免的杂质。在另外一种选择中,所述钢合金具有以下含量(按质量百分比计)的组分:1.3~1.45c、0.7~0.9si、0.3~0.5mn、4.85~5.2cr、2.8~3.2mo和3.7~4.0v,可选包含0~0.1w、0~0.18ni、0~0.12cu、0~0.8co、0~0.025p和0~0.028s,余量为铁和不可避免的杂质。
26.所述钢合金可具有以下含量(按质量百分比计)的组分:1.4c、0.4si、0.4mn、4.6cr、3.5mo和3.7v,可选包含0~0.1w、0~0.18ni、0~0.12cu、0~0.025p和0~0.028s,余量为铁和不可避免的杂质。在进一步优选的情况下,所述钢合金具有以下含量(按质量百分比计)的组分:1.40c、0.40si、0.40mn、4.70cr、3.50mo和3.70v,可选包含0~0.1w、0~0.18ni、0~0.12cu、0~0.025p和0~0.028s,余量为铁和不可避免的杂质。在另外一种选择中,所述钢合金可具有以下含量(按质量百分比计)的组分:1.35c、0.8si、0.40mn、5.0cr、2.95mo和3.85v,可选包含0~0.1w、0~0.18ni、0~0.12cu、0~0.025p和0~0.028s,余量为铁和不可避免的杂质。
27.本教导的另外一个方面是,所述钢合金具有以下含量(按质量百分比计)的组分:2.1~2.5c、0.3~0.5si、0.3~0.4mn、4.55~5.10cr、3.35~3.85mo和7.6~8.2v,可选包含0~0.1w、0~0.2ni、0~0.12cu、0~0.8co、0~0.025p和0~0.028s,余量为铁和不可避免的杂质。在优选情况下,所述钢合金具有以下含量(按质量百分比计)的组分:2.2~2.4c、0.3~0.5si、0.3~0.4mn、4.65~4.95cr、3.45~3.75mo和7.6~8.1v,可选包含0~0.1w、0~0.2ni、0~0.12cu、0~0.8co、0~0.025p和0~0.028s,余量为铁和不可避免的杂质。
28.所述钢合金可具有以下含量(按质量百分比计)的组分:2.3c、0.4si、0.4mn、4.8cr、3.6mo和8.0v,可选包含0~0.1w、0~0.12cu、0~0.025p和0~0.028s,余量为铁和不可避免的杂质。作为一种选择,所述钢合金可具有以下含量(按质量百分比计)的组分:2.30c、0.40si、0.40mn、4.80cr、3.60mo和8.00v,可选包含0~0.1w、0~0.12cu、0~0.025p和0~0.028s,余量为铁和不可避免的杂质。
29.在以上或者以下描述的任何一种钢合金中,钨可以至少大体上(/基本上/大量地)(substantially)或者全部由钼代替,并且/或者钼也可以至少大体上(substantially)或者全部由钨代替。例如,在以上或者以下描述的任何一种钢合金中,mo/w的替代率可以为1:2。即是说,例如,1wt%(重量百分比)的mo可以由2wt%的w代替,反之亦然。
30.通过结合随附的权利要求书和附图阅读以下详细说明,本发明的额外目的、方面、实施方式和优势将显而易见。
附图说明
31.图1显示本教导及其对照例(/比较例)材料进行粘着磨损试验的结果。
32.图2显示合金i(对照例)的纳米压痕硬度h
it
测量结果的反卷积结果(deconvolution result)。
33.图3显示合金i的纳米压痕弹性模量测量结果的反卷积结果。
34.图4显示合金c(本教导的实施例)的纳米压痕硬度h
it
测量结果的反卷积结果。
35.图5显示合金c的纳米压痕弹性模量的测量结果的反卷积结果。
具体实施方式
36.以下说明根据本教导的钢合金的合金元素的优选范围。
37.在本教导的一种实施方式中,碳(c)在钢合金中的含量优选具有大于等于1.25、大于等于1.3或者大于等于1.32的质量百分比下限,具有小于等于1.55、小于等于1.45或者小于等于1.42的质量百分比上限,或者处于由以上上限和下限不受限制地任意组合所获得的任何范围内。
38.在本教导的另外一种实施方式中,碳在钢合金中的含量优选具有大于等于2.1、大于等于2.2或者大于等于2.25的质量百分比下限,具有小于等于2.5、小于等于2.4或者小于等于2.35的质量百分比上限,或者处于由以上上限和下限不受限制地任意组合所获得的任何范围内。
39.硅(si)在钢合金中的含量优选具有大于等于0.28、大于等于0.3或者大于等于0.32的质量百分比下限,具有小于等于0.9、小于等于0.6、小于等于0.5、小于等于0.48或者小于等于0.43的质量百分比上限,或者处于由以上上限和下限不受限制地任意组合所获得的任何范围内。在本发明教导的一种备选实施方式中,硅在钢合金中的含量优选具有大于等于0.7、大于等于0.74或者大于等于0.78的质量百分比下限,具有小于等于0.9、小于等于0.86或者小于等于0.82的质量百分比上限,或者处于由以上上限和下限不受限制地任意组合所获得的任何范围内。
40.锰(mn)在钢合金中的含量优选具有大于等于0.22、大于等于0.26或者大于等于0.3的质量百分比下限,具有小于等于0.54、小于等于0.5或者小于等于0.48的质量百分比上限,或者处于由以上上限和下限不受限制地任意组合所获得的任何范围内。
41.铬(cr)在钢合金中的含量优选具有大于等于4.0、大于等于4.3、大于等于4.55、大于等于4.6、大于等于4.65或者大于等于4.85的质量百分比下限,具有小于等于5.20、小于等于5.10或者小于等于4.95的质量百分比上限,或者处于由以上上限和下限不受限制地任意组合所获得的任何范围内。
42.钼(mo)在钢合金中的含量优选具有大于等于2.80、大于等于3.35或者大于等于3.45的质量百分比下限,具有小于等于3.85、小于等于3.75、小于等于3.65或者小于等于3.2的质量百分比上限,或者处于由以上上限和下限不受限制地任意组合所获得的任何范围内。如上所述,钼(mo)可以至少大体上或全部由钨(w)代替。例如,在以上或以下描述的任何钢合金中,mo/w替代比可以为1:2。
43.在本发明教导的另外一种实施方式中,钒(v)在钢合金中的含量优选具有大于等于3.45、大于等于3.55或者大于等于3.7的质量百分比下限,具有小于等于4.0、小于等于
3.95或者小于等于3.9的质量百分比上限,或者处于由以上上限和下限不受限制地任意组合所获得的任何范围内。
44.在本发明教导的一种备选实施方式中,钒在钢合金中的含量优选具有大于等于4.6、大于等于7.8、大于等于7.85或者大于等于7.9的质量百分比下限,具有小于等于8.2、小于等于8.15或者小于等于8.1的质量百分比上限,或者处于由以上上限和下限不受限制地任意组合所获得的任何范围内。
45.在本发明教导的一些具体实施方式中,钨的含量可以介于,例如,0~0.13mass%范围内。然而,在其他具体实施方式中,钨的添加量可以介于1.5~3.5mass%范围内。如上所述,钨可以至少大体上或全部由钼代替,抑或相反。例如,在以上或者以下描述的任何钢合金中,mo/w替代比可以为1:2。
46.镍(ni)的含量可以介于,例如,0~0.20mass%范围内。
47.铜(cu)的含量可以介于,例如,0~0.14mass%范围内。
48.磷(p)的含量可以介于,例如,0~0.03mass%范围内。
49.硫(s)的含量可以介于,例如,0~0.03mass%范围内。
50.钴(co)的含量可以介于,例如,0~0.8mass%范围内,更优选介于0~0.2mass%范围内。
51.不可避免的杂质的含量可以介于,例如,0~0.5mass%范围内,优选介于0~0.3mass%范围内,更优选介于0~0.2mass%范围内,更进一步优选介于0~0.1mass%范围内。
52.实验结果
53.以下结合对照例(/比较例)说明本发明教导的钢合金工作示例及其具有代表性的制造方法。有必要指出,本发明的钢合金、轴承部件和制造方法不限于工作示例的具体细节,其组分和步骤可以在不偏离本发明主旨的范围内进行适当地修改。
54.1.材料和方法
55.具有以下表1描述的钢合金组分的棒在以下过程中被予以使用。钢合金a ~d和g~h是根据粉末冶金(p/m)工艺(/过程)(process)制备的。
[0056][0057]
所有上述钢合金都是在球化退火的状态被提供的。这些不同的钢合金被实施了以下硬化热处理。然而,概括而言,所有的钢合金都经过了淬火和回火,因此其微观结构以回火马氏体基体为特征,所述回火马氏体基体具有一些残余奥氏体和主要取决于合金化学成分的各种类型的碳化物、碳氮化物和氮化物。
[0058]
更具体而言,这些钢合金被实施了以下表2所描述的热处理:
[0059]
表2
[0060][0061]
bruker d8 discover衍射仪被用于对淬火和回火样品进行x射线衍射分析,在50kv和50ma条件下,使用锆滤波的钼k
α1,2
辐射进行操作。针对15
°
~63
°
的2θ扫描范围实施步进扫描(/阶梯扫描/阶跃扫描)(step-scan)模式θ:θ扫描。角步长(/角步宽/角度步长宽度)(angular step width)为0.02
°
,每步收集时间10s。使用topas(第5版)软件根据里特维德精化方法(rietveld refinement method)对结果进行分析,所述软件从马萨诸塞州比勒利卡的布鲁克公司(bruker corporation of billerica,massachusetts)处获得,得到的微观结构信息如以下表3所示。所有数值均为平均体积百分比,其中,每组合金中至少有两件样品被分析。
[0062][0063]
三种类型的筛选试验被设计和实施在经过淬火和回火的合金上,用以评估这些热处理钢合金对超精密轴承应用中常见的不同表面破坏模式的耐受程度,即:表面损伤(微点蚀)、粘着磨损和磨料磨损。这些试验将在后续部分中分步描述。
[0064]
a.表面损伤(surface distress)
[0065]
表面损伤也被称为微点蚀(micropitting)(源于观察到的表面微裂隙或者微凹坑),是一种在润滑条件不佳的情况下与滚/滑动的粗糙接触(对应于高强度表面拖曳)有关的粗糙环境下的表面起始疲劳(surface-initiated fatigue)。在显微镜下,受影响的表面区域显现出微剥落、微凹坑或者微裂隙的存在(垂直于滚动和滑动方向),具有在深度上几十和几微米的典型尺寸。表面损伤对轴承功能尤其具有伤害性。尽管它并非是滚动轴承的主要失效模式,但它可以促成或者加速其他更为严重的失效模式的出现,比如,表面起始剥落(surface-initiated spalling)。
[0066]
为了评估微点蚀,微点蚀试验仪被予以使用。在所述试验仪中,三个相同直径的垫圈(由合金i制成)被设置为各自的旋转轴分别位于等边三角形的三个顶点上。其中,两个垫圈被局部浸没在油(润滑剂)中,第三个垫圈对被设置在三个垫圈之间从而能够接触到全部三个垫圈的滚子样本(由上述经过淬火和回火的钢合金制成)施加载荷。每个滚子样本均具有12毫米的直径。所述滚子和垫圈由两台独立电机驱动,用以确保滑滚比(slide-to-roll ratio)被控制在(从纯滚动至纯滑动的)全范围内。
[0067]
微点蚀试验仪是根据以下表4所示条件被操作的。
[0068]
表4
[0069][0070][0071]
在每次试验以后,滚子样本都被拆下,正确清洁以便去除润滑剂残留,然后测量其最终重量,以获得其表面损伤和(不可避免的)轻微磨损共同作用下所导致的重量损失。然后,采集滚子表面的5~10幅光学图像,用以捕捉其在不同圆周位置之处的全部接触轨迹。通过将表面外观与表面损伤标准等级进行比对,这些图像被进行视觉分析。最终的试验结果包含表面损伤平均耐受等级(从1(即不可接受)到5(即优秀),四舍五入到0.5)和重量损失(以毫克计)。
[0072]
b.粘着磨损(adhesive wear)
[0073]
粘着磨损是一种发生在彼此相对滑动的两个配合面之间的与润滑剂有关的损伤。它以物质从一个表面向另外一个表面的转移(涂抹(smearing)或者刮擦(scuffing))为特征,在典型情况下伴以摩擦生热。所述摩擦生热有时会造成配合面的回火或者再硬化。相对滑动的速度须高于轴承在滚动接触区域的几何形状所引起的打滑。
[0074]
在轴承中,粘着磨损可能发生在滚动轴承中相对高速运转的滚动体与滚道之间的表面上。在承载区(loaded zone)以外,滚动体由于不受驱动,其旋转受到阻滞。当滚动体进入承载区时,它们受到迅疾加速。这会引起滑动(抑或甚至打滑,即滚动体在滚道上严重滑行),滑动会产生足够的热量,将金属与金属接触点处的两个表面融合在一起。这种“焊接”过程引起材料从一个表面向另外一个表面转移,同时还导致更高的摩擦。在超精密轴承中,这种情况通常不会发生,因为轴承主要承受轴向载荷。因此,超精密轴承中的主要滑动机制在典型情况下是球转动(ball spinning)和微滑动(micro-sliding),通常在普遍施加在这类轴承上的非常高的转速下才变得重要。
[0075]
wam(wedeven associates machine)的球盘(球对垫圈)机被用于确定粘着磨损,因为它是一种能够在广泛测试条件下使用的多功能试验仪。由于球和盘(垫圈)可以以完全独立的方式被控制,并且可以被施以高载荷(造成上至2.8gpa的接触压力),所以它是一种能够满足粘着磨损试验所需高载荷和高滑动速度的适宜机器。
[0076]
为拥有恒定的(油)膜厚度,润滑剂的卷携速度(决定接触位置处润滑剂油膜厚度的速度,等于两个接触面的平均线速度)保持不变,而滑动速度(即两个接触面速度之差)不断增加,直至出现表面粘着磨损。这以牵引系数(traction coefficient)的突然增加为特征,通常伴有独特的(/有区别的)(distinct)噪音。所述卷携速度被选择为使试验在边界润滑条件(boundary lubrication conditions)下(λ=0.2)进行。这在试验开始时是有效的;由于摩擦生热,被测部件的温度会上升,这会导致润滑剂粘度下降,而润滑剂粘度下降会继而降低接触位置处的油膜厚度。
[0077]
为测试以上描述的淬火和回火材料,由上述钢合金制成的垫圈被按照以下规格参数制备:厚度4.75mm,外径85mm,内(孔)径60mm。
[0078]
垫圈被固定在装配于wam盘轴上的支撑盘上。各垫圈表面被沿环形轨迹研磨至粗糙度值rq=0.5μm。球为陶瓷球(rb-20,638 h13/g10 si3n4 tsn-03nh)。每次测试都使用一条新的垫圈(轨迹)路径;每个球被使用两次。润滑油为shell turbo t32,一种没有极端压力添加剂(/极压添加剂)或抗磨添加剂的矿物涡轮润滑油。试验条件如下表5所述。
[0079]
表5
[0080]
[0081][0082]
试验采用三种不同的载荷(100n、300n、600n)进行,相应导致1.5、2.2和2.8gpa的接触压力。由于不同的钢合金具有不同的弹性模量,这些接触压力可能会在试验过程中发生些许改变。
[0083]
第一次试验是在300n的载荷下进行的,如果粘着磨损(在低滑动速度下)快速出现,那么下一次试验则施加100n,之后两种载荷均被重复施加。最后,有一次试验是在600n的条件下进行的。假如粘着磨损是在300n的载荷下在高滑动速度情况下出现的,那么下一次试验就在600n的载荷下进行,仅最后一次试验是在100n的载荷下进行。按照这种方式,垫圈上可用的测试路径均已被最为有效地利用过了。
[0084]
在被正确清洁以后,球和垫圈被实施光学观察,用以确认粘着磨损已实际发生。试验结果然后被绘制在图纸上,显示载荷或其对应的接触压力与粘着磨损发生时的滑动速度之间的关系。磨损图(scuffing map)中各点可以用线条连接起来。线条的左侧区域为无粘着磨损发生的安全区域,线条的右侧区域为粘着磨损被期待发生的非安全区域。
[0085]
c.磨料磨损(abrasive wear)
[0086]
磨料磨损试验被实施用来确定材料在滑动过程中的耐磨性。尤其是,销钉对垫圈(pin-on-washer)的磨料磨损试验被实施,该试验需要一个销钉试样和一个垫圈试样。被坚实固定(/保持)的球被作为销钉试样,所述球被以恒定的载荷压抵在垫圈上。测试机器使垫圈以特定的滑动速度在控制良好的润滑条件下围绕垫圈中心旋转。滑动路径为垫圈表面上的一个圆。经过特定的滑动距离以后,磨损量通过测量垫圈的重量损失(以毫克计)予以确定。
[0087]
销钉对垫圈的试验仪器是根据astm g99标准构建的。两种类型的球,即钢球和氧化铝球,被用于磨损由上述淬火和回火钢合金制成的垫圈。
[0088]
氧化铝(al2o3)球的直径为9.5mm,由上海泛联科技股份有限公司(shanghai unite technology co.,ltd)提供。该陶瓷球仅经过烧结,未被进一步粗研磨、半抛光研磨和抛光研磨,因此粗糙度ra(平均值)≈2μm。该陶瓷球试样的显微结构包含具有少量二次相的等晶α氧化铝,硬度大于等于1600hv3,杨氏模量为350gpa,泊松比为0.29,粗糙度如下:ra平均值为2721.3nm,rz平均值为26.46μm。所述球在100n载荷下被静止压抵在垫圈上,产生最大约为2.6gpa的陶瓷—钢(ceramic-steel)接触压力。
[0089]
在硬化和回火处理以前,上述钢合金被形成为具有上述规格的垫圈试样,即:厚度4.75mm,外径85mm,内(孔)径60mm。然后,垫圈试样被按照以上描述的热处理方式进行热处理(硬化和回火)。之后,垫圈试样被打磨成具有高光洁度。在研磨以后,垫圈试样展现出以下表6所示的特征。
[0090]
表6
[0091]
合金硬度hv10粗糙度ra平均值(nm)粗糙度rz平均值(μm)
a、b767
±
17.50.198c、d756
±2‑‑
e、f704
±
28.40.298g816
±1‑‑
h923
±
812.60.167i728
±3‑‑
j、k685
±
27.40.195
[0092]
在磨损试验的过程中,每一个垫圈试样都在室温下被浸入shell turbine t32油中。为使碎屑在接触位置处的影响最小化,在每次试验之后,所述油均被更换。垫圈以0.19m/s的速度旋转,该速度低至足以避免滑动引发的温升。在滑动3千米路程(/距离)之前和之后,垫圈的重量被测量。
[0093]
2.结果与讨论
[0094]
a.表面损伤
[0095]
微点蚀试验仪表面损伤试验的结果如以下表7所示:
[0096]
表7
[0097] a、bc、de、fghij、k平均表面损伤耐受能力55144.533平均滚子重量损失(mg)0.270.070.800.180.200.290.72
[0098]
表7展示每种钢品变体3~4次试验的表面损伤耐受能力和滚子重量损失的平均值,除了e、f仅做过一次mpr试验。
[0099]
钢合金a、b、c和d表现出优越的表面损伤耐受能力。合金c和d还同时表现出优越的平均滚子重量损失。
[0100]
b.粘着磨损
[0101]
如图1所示,不同的钢合金被观测到在粘着磨损耐受能力方面具有很大的差异。尽管所有的材料在被施加300n或600n载荷时都达到了粘着磨损极限,但有一些材料(尤其是钢合金a~d)在100n载荷的情况下并未展现出粘着磨损。
[0102]
从图1中可以看出,钢合金a~d展现出显著优于其他钢合金的粘着磨损耐受能力。
[0103]
c.磨料磨损
[0104]
垫圈试样在被执行以上描述的磨料磨损试验以后的重量损失被列入以下表8中。对于陶瓷与钢之间的接触,陶瓷球比垫圈表面更硬,比垫圈表面粗糙100倍以上,从而表明主要的磨损机制为磨料磨损。
[0105]
表8
[0106][0107]
钢合金a、b和i展现出具有优势的低磨料磨损结果(/低磨粒磨损结果)(low abrasive wear results)。
[0108]
为证实(demonstrate)微观结构上的差异,合金c和i试样的纳米力学性能被在纳米尺度上进行了测量。硬度和弹性模量的分布由多处纳米压痕测量结果确定,然后被反卷积,从而获得微观结构成分和相应的塑性和弹性性能在纳米尺度上的估计值。合金c被按照以上表2的描述进行热处理。合金i被按照以下方式进行热处理:在850~860℃温度条件下进行奥氏体化15~25min,然后在大约50℃温度条件下油淬(oil-quenched),最后在200℃温度条件下回火4小时。
[0109]
具体而言,纳米压痕测量结果(nanoindentation measurements)是通过使用尖端半径约为150nm的金刚石三面别科维奇压痕仪(diamond three-sided berkovich indenter)进行纳米压痕试验获得的。测量采用的是csm instruments(现为anton paar)公司的超级纳米压痕测试仪(ultra nanoindentation tester,缩写unht),该测试仪具有0.1nm的垂直位移分辨率和0.1μn的力分辨率。多处压痕试验是在最大压痕载荷l
max
为7mn的条件下进行的。每件试样分别在其三处不同位置的三个网格内被制造出总共1500个压痕,所述三个网格中的每一个网格都具有间隔距离为7μm的20
×
25处压痕。
[0110]
纳米压痕硬度(h
it
)和弹性模量(e
it
)是根据oliver和pharr的方法(参见e.broitman,“宏、微观和纳米尺度压痕硬度测量:关键概述”,《摩擦学快报》(tribology letters),第65卷,第23页,2017;w.oliver和g.pharr,“利用载荷和位移传感压痕试验测定硬度和弹性模量的改进技术”,《材料研究杂志》(journal of materials research),第7卷,no.6,第1564~1583页,1992),遵循iso 14577第4部分标准(具体为iso 14577:“金属材料—针对硬度和材料参数的仪器压痕试验”,国际标准化组织,日内瓦,2015)被计算出来的。
[0111]
通过以高斯曲线拟合数据来进行反卷积(deconvolution)。所述数据被认为属于一种具有非相互作用n相(non-interacting n phases)的材料。假设每一相均具有高斯分布的力学特性(/机械特性)(mechanical property)x(x=h或e),那么相数n及其高斯曲线参数被选择为能使统计判定系数(statistical coefficient of determination)r2最小
化。
[0112]
钢合金i
[0113]
图2显示在r2=0.935的情况下获得的合金i纳米压痕硬度h
it
测量结果的反卷积结果,被观察到其中有四处峰存在。各峰的顶点位置、偏移量σ以及四峰中的每一峰面积(area)分别如以下表9所示。
[0114]
表9
[0115][0116]
图3显示在r2=0.963的情况下获得的合金i纳米压痕弹性模量测量结果的反卷积结果,被观察到其中仅有一处峰存在。各峰的顶点位置、偏移量σ和面积分别如以下表10所示。
[0117]
表10
[0118][0119]
图4显示在r2=0.909的情况下获得的合金c纳米压痕硬度h
it
测量结果的反卷积结果,被观察到其中有五处峰存在。各峰的顶点位置、偏移量σ以及五峰中的每一峰面积分别如以下表11所示。
[0120]
表11
[0121][0122]
图5显示在r2=0.924的情况下获得的合金c纳米压痕弹性模量测量结果的反卷积结果,被观察到其中有四处峰存在。各峰的顶点位置、偏移量σ以及四峰的面积分别如以下表12所示。
[0123]
表12
[0124][0125]
该纳米压痕数据也被用于获得各合金c和i的硬度和弹性模量的平均纳米尺寸值。下表13对比宏观尺度和纳米尺度上的测量值,其中纳米尺度的测量值是通过计算1500个测量结果的平均值和离散度获得的。有必要指出,用维氏压痕法(hv)和仪器纳米压痕法(h
it
)测量的硬度没有直接的关系。根据上文提及的iso 14577,hv=0.9244h
it
的相互关系应当仅作参考。
[0126]
表13
[0127]
[0128]
在硬度方面,合金c与i的宏观硬度相同(61.0
±
0.1hrc vs.61.4
±
0.1hrc),测量值的微小差异处于测试仪在被用于测量硬度时在设置和配置上的试验误差(0.4)范围内。然而,对比图2和4可以看出,合金c和i包含显著不同的硬度成分(hardness components)。尤其是,与合金i相比,合金c(如图4所示)在硬度值较低和较高的地方都有峰值,而合金i的峰值(如图2所示)则更为紧密地聚集在一起。
[0129]
通常而言,轴承部件的疲劳寿命与显微硬度成正比。然而,合金c的硬度成分范围更广(即最低和最高硬度峰值之间的差异更大)。这意味着合金c具有更强的应变硬化能力(strain hardening capability),使它能够更好地耐受基体内的损伤,更能抵御表面起始疲劳。
[0130]
在弹性模量方面,合金i仅展现出一个峰,在207.40gpa位置处具有最大值(如图3所示),而合金c则展现出三个显著的峰,如图5所示。尤其是,合金c的其中一个峰(207.2gpa)具有与合金i的唯一峰近似的弹性模量,但合金c的这个峰仅覆盖了33%的数据。合金c的另外两个显著峰分别处于254gpa(覆盖46%的数据)和148gpa(覆盖21%的数据)的弹性模量位置处,证明合金c与i具有显著不同的微观结构。
[0131]
本发明教导的其他方面包括但不限于:
[0132]
1.一种轴承部件,由铬-钼-钒合金工具钢构成,其制造工艺(/过程)包括以下步骤:
[0133]
(i)执行600~650℃温度范围内的第一次预热处理;
[0134]
(ii)执行850~900℃温度范围内的第二次预热处理;
[0135]
(iii)在真空1000~1180℃温度条件下进行奥氏体化5~60分钟,优选在1080~1150℃温度条件下进行奥氏体化20~40分钟或者在1100~1150℃温度条件下进行奥氏体化15~40分钟;
[0136]
(iv)在至少(/最小)(minimum)4~5bar的超压(overpressure)下进行气体淬火;以及
[0137]
(v)回火:在530~560℃温度条件下进行两次回火,每次回火1.5~2.5小时,优选在545~560℃温度条件下每次回火1.5~2.5小时;或者,在530~560℃温度条件下进行三次回火,每次回火0.5~1.5小时,优选在545~560℃温度条件下每次回火0.75~1.25小时。
[0138]
2.根据以上方面1的轴承部件,其中,在所述回火步骤以后,所述轴承部件具有包含以下成分的微观结构:
[0139]
残余奥氏体:0~1.5vol%,优选0~1vol%;和/或
[0140]
渗碳体:1.0~3.0vol%,优选1.8~2.5vol%;和/或
[0141]
mo2c正交晶系:0.5~2.5vol%,优选1.2~1.6vol%;和/或
[0142]
铁-α(基体(matrix)):80~95vol%,优选83~94vol%;和/或
[0143]
vc:3~13vol%,优选3.5~12vol%。
[0144]
3.一种轴承部件,由铬-钼-钒合金工具钢构成,并且具有以下成分的微观结构:
[0145]
残余奥氏体:0~1.5vol%,优选0.4~1vol%:和/或
[0146]
渗碳体:1.0~3.0vol%,优选1.8~2.5vol%;和/或
[0147]
mo2c正交晶系:0.5~2.5vol%,优选1.2~1.6vol%;和/或
[0148]
铁-α(基体):80~95vol%,优选83~94vol%;和/或
[0149]
vc:3~13vol%,优选3.5~12vol%。
[0150]
4.一种用于制备由铬-钼-钒合金工具钢构成的轴承部件的方法,包含以下步骤:
[0151]
(i)执行600~650℃温度范围内的第一次预热处理;
[0152]
(ii)执行850~900℃温度范围内的第二次预热处理;
[0153]
(iii)在真空1080~1185℃温度条件下进行奥氏体化5~60分钟,优选在1080~1120℃温度条件下进行奥氏体化20~40分钟或者在1120~1170℃温度条件下进行奥氏体化15~40分钟;
[0154]
(iv)在至少(/最小)(minimum)4~5bar的超压下进行气体淬火;以及
[0155]
(v)回火:在530~560℃温度条件下进行两次回火,每次回火1.5~2.5小时,优选在545~560℃温度条件下每次回火1.5~2.5小时;或者,在550~570℃温度条件下进行三次回火,每次回火0.5~1.5小时,优选在545~560℃温度条件下每次回火0.75~1.25小时。
[0156]
5.根据以上方面1~4中任意一个方面所述的轴承部件或者方法,其中,所述轴承部件由粉末冶金工艺(powder metallurgy process)制成。
[0157]
6.根据以上方面1~4中任意一个方面所述的轴承部件或者方法,其中,所述轴承部件由喷射成型工艺制成。
[0158]
在方面6中,喷射成型(spray forming)(亦称“喷射铸造(spray casting)”、“喷射沉积(spray deposition)”、“原位压实(in-situ compaction)”或者“奥斯普瑞工艺(ospray process)”)可被用于形成所述的轴承部件,类似于钢液(liquid steel)雾化的气体雾化过程。然而,与允许雾化液滴在自由下落过程中凝固不同的是(instead of),一个旋转收集器被插入到腔内距离雾化喷嘴一定距离的位置处。喷射的液滴聚集并冻结(凝固)在旋转的收集器上。如果收集器的回收频率与喷雾沉积的速度相匹配,那么喷雾形成的产品,例如,可用于制作轴承圈的管,就可以被制作成型。从本质上讲,钢液滴在产品构建阶段就已经凝固,因此无需cip或者hip(热等静压)之类的额外处理。
[0159]
6.1根据以上方面1~4中任意一个方面所述的轴承部件或者方法,其中,所述轴承部件由3d打印工艺制成。
[0160]
7.根据任何一个前述方面所述的轴承部件或者方法,其中,所述钢合金包含质量百分含量为1.25~1.55或2.1~2.5的c(碳),可选1.32~1.45的c,可选1.3~1.45的c,可选2.2~2.4的c。
[0161]
8.根据任何一个前述方面所述的轴承部件或者方法,其中,所述钢合金包含质量百分含量为0.28~0.90的si(硅),可选0.32~0.5的si,可选0.32~0.48的si,可选0.3~0.43的si,可选0.7~0.9的si。
[0162]
9.根据任何一个前述方面所述的轴承部件或者方法,其中,所述钢合金包含质量百分含量为0.22~0.54的mn(锰),可选0.26~0.48的mn,可选0.3~0.5的mn。
[0163]
10.根据任何一个前述方面所述的轴承部件或者方法,其中,所述钢合金包含质量百分含量为4.0~5.1的cr(铬),可选4.30~5.10的cr,可选4.60~5.10的cr,可选4.65~4.95的cr,可选4.65~4.85的cr,可选4.85~5.2的cr。
[0164]
11.根据任何一个前述方面所述的轴承部件或者方法,其中,所述钢合金包含质量百分含量为2.80~3.65或3.35~3.85的mo(钼),可选3.35~3.55的mo,可选2.8~3.2的mo,可选3.45~3.75的mo。
[0165]
12.根据任何一个前述方面所述的轴承部件或者方法,其中,所述钢合金包含质量百分含量为3.45~4.0或7.8~8.2的v(钒),可选3.55~3.85的v,可选3.7~4.0的v,可选7.6~8.1的v。
[0166]
13.根据任何一个前述方面所述的轴承部件或者方法,其中,所述钢合金可以选择性地包含一种或一种以上以下质量百分含量的成分:0~0.13的w、0~0.20的ni、0~0.15的cu、0~0.8的co、0~0.03的p和/或0~0.03的s;优选一种或一种以上以下质量百分含量的成分:0~0.1的w、0~0.18的ni、0~0.12的cu、0~0.2的co、0~0.025的p和0~0.028的s。
[0167]
14.根据任何一个前述方面所述的轴承部件或者方法,其中,所述钢合金包含至少50vol%的马氏体,优选至少60vol%的马氏体,进一步优选至少70vol%的马氏体。
[0168]
15.根据任何一个前述方面所述的轴承部件或者方法,其中,所述轴承部件是滚动轴承的内圈或者外圈。
[0169]
16.根据任何一个前述方面所述的轴承部件或者方法,其中,所述钢合金包含质量百分含量为1.25~1.55的c(碳)、0.28~0.90的si(硅)、0.22~0.54的mn(锰)、4.0~5.10的cr(铬)、2.80~3.65的mo(钼)和3.45~4.0的v(钒),基体的大部分为铁。
[0170]
17.根据以上方面1~15中任意一个方面所述的轴承部件或者方法,其中,所述钢合金包含质量百分含量为1.32~1.45的c、0.32~0.50的si、0.26~0.48的mn、4.30~4.85的cr、3.35~3.55的mo和3.55~3.85的v,可选包含0~0.13的w、0~0.20的ni、0~0.15的cu、0~0.2的co、0~0.03的p、以及0~0.03的s,余量为铁和不可避免的杂质。
[0171]
18.根据以上方面1~15中任意一个方面所述的轴承部件或者方法,其中,所述钢合金包含质量百分含量为1.3~1.45的c、0.7~0.9的si、0.3~0.5的mn、4.60~5.2的cr、2.8~3.2的mo和3.7~4.0的v,可选包含0~0.1的w、0~0.18的ni、0~0.12的cu、0~0.2的co、0~0.025的p和0~0.028的s,余量为铁和不可避免的杂质。
[0172]
19.根据以上方面1~15中任意一个方面所述的轴承部件或者方法,其中,所述钢合金包含质量百分含量为1.25~1.55的c、0.28~0.90的si、0.22~0.54的mn、4.0~5.10的cr、2.80~3.65的mo和3.45~4.0的v,可选包含0~0.1的w、0~0.18的ni、0~0.12的cu、0~0.2的co、0~0.025的p,余量为铁和不可避免的杂质。
[0173]
20.根据以上方面1~15中任意一个方面所述的轴承部件或者方法,其中,所述钢合金包含质量百分含量为1.32~1.45的c、0.32~0.50的si、0.26~0.48的mn、4.30~4.85的cr、3.35~3.55的mo和3.55~3.85的v,可选包含0~0.1的w、0~0.18的ni、0~0.12的cu、0~0.2的co、0~0.025的p,余量为铁和不可避免的杂质。
[0174]
21.根据以上方面1~15中任意一个方面所述的轴承部件或者方法,其中,所述钢合金包含质量百分含量为1.3~1.45的c、0.7~0.9的si、0.3~0.5的mn、4.60~5.2的cr、2.8~3.2的mo和3.7~4.0的v,可选包含0~0.1的w、0~0.18的ni、0~0.12的cu、0~0.2的co、0~0.025的p,余量为铁和不可避免的杂质。
[0175]
22.根据以上方面1~15中任意一个方面所述的轴承部件或者方法,其中,所述钢合金包含质量百分含量为2.1~2.5的c、0.3~0.4的si、0.3~0.4的mn、4.30~5.10的cr、3.35~3.85的mo和7.6~8.2的v,可选包含0~0.1的w、0~0.12的cu、0~0.2的co、0~0.025的p和0~0.028的s,余量为铁和不可避免的杂质。
[0176]
23.根据以上方面1~15中任意一个方面所述的轴承部件或者方法,其中,所述钢
合金包含质量百分含量为2.2~2.4的c、0.3~0.4的si、0.3~0.4的mn、4.60~4.95的cr、3.45~3.75的mo和7.6~8.1的v,可选包含0~0.1的w、0~0.12的cu、0~0.2的co、0~0.025的p和0~0.028的s,余量为铁和不可避免的杂质。
[0177]
24.根据任何一个前述方面所述的轴承部件或者方法,其中,当使用美国国立卫生研究院(the united states national institute of health)公开提供的imagej软件计算时,轴承部件微观结构的横截面上的碳化物晶粒的数字加权平均面积在0.1~0.5μm2范围之间,优选在0.15~0.4μm2范围之间。
[0178]
25.根据任何一个前述方面的所述轴承部件或者方法,其中,当使用美国国立卫生研究院公开提供的imagej软件计算时,轴承部件微观结构的横截面上99%的碳化物晶粒面积在0.0005~2.7μm2范围之间,优选在0.0007~2.7μm2范围之间。
[0179]
26.根据任何一个前述方面的所述轴承部件或者方法,其中,当使用美国国立卫生研究院公开提供的imagej软件计算时,所述碳化物晶粒占所述微观结构的横截面总面积的10~20%,优选12~17%。
[0180]
27.一种轴承部件,由铬-钼-钒合金工具钢构成,其制造构成包括以下步骤:
[0181]
(i)执行600~650℃温度范围内的第一次预热处理;
[0182]
(ii)执行850~900℃温度范围内的第二次预热处理;
[0183]
(iii)在真空1000~1180℃温度条件下进行奥氏体化5~60分钟;
[0184]
(iv)在至少4~5bar的超压下进行气体淬火;以及
[0185]
(v)回火:在520~560℃温度条件下进行两次回火,每次回火1.5~2.5小时,或者,在520~560℃温度条件下进行三次回火,每次回火0.5~1.5小时。
[0186]
28.根据以上方面27所述的轴承部件,其中,在所述回火步骤以后,所述轴承部件的微观结构包含:
[0187]
0~1.5vol%的残余奥氏体;
[0188]
1.0~3.0vol%的渗碳体;
[0189]
0.5~2.5vol%的mo2c正交晶系;
[0190]
80~95vol%的铁-α(基体);和
[0191]
3~13vol%的vc。
[0192]
29.根据以上方面27或28所述的轴承部件,其中:
[0193]
所述奥氏体化步骤在1080~1150℃温度条件下被执行20~40分钟;并且
[0194]
所述两次回火在540~560℃温度条件下被执行,每次回火1.5~2.5小时,或者,所述三次回火在540~560℃温度条件下被执行,每次回火0.75~1.25小时。
[0195]
30.根据以上方面27~29中任意一个方面所述的轴承部件,其中,在所述回火步骤以后,所述轴承部件的微观结构包含:
[0196]
0~1vol%的残余奥氏体;
[0197]
1.8~2.5vol%的渗碳体;
[0198]
1.2~1.6vol%的mo2c正交晶系;
[0199]
83~94vol%的铁-α(基体);和
[0200]
3.5~12vol%的vc。
[0201]
31.根据以上方面27~30中任意一个方面所述的轴承部件,其中,所述钢合金包含
至少60vol%的马氏体。
[0202]
32.根据以上方面27~31中任意一个方面所述的轴承部件,其中,所述轴承部件由粉末冶金工艺形成。
[0203]
33.根据以上方面27~32中任意一个方面所述的轴承部件,其中,所述钢合金包含质量百分比含量为1.5~2.5的w。
[0204]
34.根据以上方面27~33中任意一个方面所述的轴承部件,其中,所述钢合金包含质量百分含量为1.25~1.55的c。
[0205]
35.根据以上方面27~34中任意一个方面所述的轴承部件,其中,所述钢合金包含质量百分含量为0.28~0.90的si。
[0206]
36.根据以上方面27~35中任意一个方面所述的轴承部件,其中,所述钢合金包含质量百分含量为0.22~0.54的mn。
[0207]
37.根据以上方面27~36中任意一个方面所述的轴承部件,其中,所述钢合金包含质量百分含量为4.0~5.10的cr。
[0208]
38.根据以上方面27~37中任意一个方面所述的轴承部件,其中,所述钢合金包含质量百分含量为2.80~3.65的mo。
[0209]
39.根据以上方面27~38中任意一个方面所述的轴承部件,其中,所述钢合金包含质量百分含量为3.45~4.0的v。
[0210]
40.根据以上方面27~39中任意一个方面所述的轴承部件,其中,所述轴承部件是滚动轴承的内圈或者外圈。
[0211]
41.根据以上方面40所述的轴承部件,其中,所述钢合金包含质量百分含量为1.25~1.55的c、0.28~0.90的si、0.22~0.54的mn、4.0~5.10的cr、2.80~3.65的mo和3.45~4.0的v,基体的大部分是铁。
[0212]
42.根据以上方面40所述的轴承部件,其中,在所述回火步骤以后,所述轴承部件的微观结构包含:
[0213]
0~1vol%的残余奥氏体;
[0214]
1.8~2.5vol%的渗碳体;
[0215]
1.2~1.6vol%的mo2c正交晶系;
[0216]
83~94vol%的铁-α(基体);和
[0217]
3.5~12vol%的vc;
[0218]
其中,所述钢合金包含至少60vol%的马氏体。
[0219]
43.根据以上方面42所述的轴承部件,其中,所述钢合金包含质量百分含量为1.32~1.45的c、0.32~0.50的si、0.26~0.48的mn、4.30~4.85的cr、3.35~3.55的mo、3.55~3.85的v、0~0.13的w、0~0.20的ni、0~0.15的cu、0~0.8的co、0~0.03的p和0~0.03的s,余量为铁和不可避免的杂质。
[0220]
44.根据以上方面43所述的轴承部件,其中,所述钢合金包含质量百分含量为1.4的c、0.4的si、0.4的mn、4.7的cr、3.5的mo、3.7的v、0~0.1的w、0~0.18的ni、0~0.12的cu、0~0.2的co、0~0.025的p和0~0.028的s,余量为铁和不可避免的杂质。
[0221]
45.一种轴承部件,由铬-钼-钒合金工具钢构成,其微观结构包含:
[0222]
0~1.5vol%的残余奥氏体;
[0223]
1.0~3.0vol%的渗碳体;
[0224]
0.5~2.5vol%的mo2c正交晶系;
[0225]
80~95vol%的铁-α(基体);和
[0226]
3~13vol%、优选3.5~12vol%的vc。
[0227]
46.一种制备由铬-钼-钒合金工具钢构成的轴承部件的方法,包含以下步骤:
[0228]
(i)执行600~650℃温度范围内的第一次预热处理;
[0229]
(ii)执行850~900℃温度范围内的第二次预热处理;
[0230]
(iii)在真空1000~1180℃温度条件下进行5~60分钟的奥氏体化;
[0231]
(iv)在至少4~5bar的超压下进行气体淬火;以及
[0232]
(v)回火:在520~560℃温度条件下进行两次回火,每次回火1.5~2.5小时,或者,在520~560℃温度条件下进行三次回火,每次回火0.5~1.5小时。
[0233]
47.根据以上方面46所述的方法,其中:
[0234]
所述奥氏体化步骤在1100~1150℃温度条件下进行20~40分钟;并且
[0235]
所述两次回火在540~560℃温度条件下进行,每次回火1.5~2.5小时,或者,所述三次回火在540~560℃温度条件下进行,每次回火0.75~1.25小时。
[0236]
以上结合附图详细描述了本发明具有代表性的非限制性实施例。这种详细描述仅意图教导本领域的技术人员实施当下教导优选层面的进一步细节,并非旨在限制本发明的保护范围。此外,以上披露的每一项额外特征和教导可以单独使用,也可以与其他特征和教导进行组合,用以提供改进的热处理钢合金,例如,用于超级精密轴承之类(但不限于此)的轴承应用。
[0237]
不仅如此,以上详尽描述中披露的特征和步骤的组合可能并非是在最广泛意义上实施本发明所必需的,其教导仅被用于特别描述本发明具有代表性的实施例。不仅如此,上述具有代表性的实施例的各种特征以及随附的各种独立和从属权利要求可以以未被具体明确枚举的方式加以组合,用于提供当下教导以外的有用的实施方式。
[0238]
说明书和/或权利要求中披露的全部特征均系出于原始书面公开之目的和限制要求保护的主题之目的而被彼此分开和独立地公开的,不依赖于实施例、方面和/或权利要求中特征的组成。此外,实体组的全部数值范围或表征均系出于原始书面公开之目的和限制要求保护的主题之目的而意图披露每个可能的中间值或中间实体的。