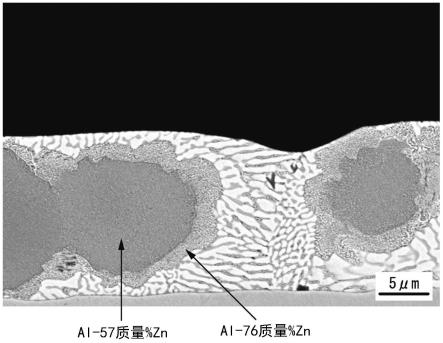
熔融zn-al-mg系镀覆钢材
技术领域
1.本发明涉及熔融zn-al-mg系镀覆钢材。
2.本技术基于2020年6月9日在日本技术的特愿2020-100073号而主张优先权,并将其内容援引于此。
背景技术:3.在建材、土木的领域中,熔融zn-al-mg系镀覆钢材大多以未涂装的状态被使用。因此,要求平面部的耐蚀性优异的熔融zn-al-mg系镀覆钢材。此外,最近,在家电、汽车的领域也正在使用熔融zn-al-mg系镀覆钢材。在家电、汽车的领域中,熔融zn-al-mg系镀覆钢材大多以涂装的状态被使用。此外,在建材领域中,进行涂装来使用的场景也在增加。因此,要求不易因腐蚀而引起涂膜膨起的熔融zn-al-mg系镀覆钢材。在专利文献1~6中记载了各种熔融zn-al-mg系镀覆钢材。
4.在专利文献1中记载了一种耐蚀性优异的镀覆钢板,其在钢板的表面具有zn合金镀层,所述zn合金镀层含有mg:1~10重量%、al:2~19重量%、si:0.01~2重量%、并且mg与al满足下式、mg(%)+al(%)≤20%、剩余部分包含zn及不可避免的杂质,其中,zn合金镀层具有在〔al/zn/mgzn2的三元共晶组织〕的基体中混合存在〔mg2si相〕和〔mgzn2相〕及〔zn相〕的金属组织。
5.在专利文献2中记载了一种耐蚀性及表面外观良好的熔融zn-al-mg镀覆钢板,其是在钢板表面形成有熔融zn-al-mg镀层的熔融zn基镀覆钢板,所述熔融zn-al-mg镀层为al:4.0~10重量%、mg:1.0~4.0重量%、剩余部分包含zn及不可避免的杂质,该镀层具有在〔al/zn/mgzn2的三元共晶组织〕的基体中混合存在〔al相〕的金属组织。
6.在专利文献3中记载了一种鲜映性优异的高耐蚀性涂装钢板,其在钢板的单面或两面具有锌系镀层,所述锌系镀层含有al:4~10质量%、mg:1~5质量%、ti:0.01质量%以下且剩余部分包含锌及不可避免的杂质,作为中间层,具有铬酸盐皮膜或磷酸盐被膜的化学转化被膜,作为上层,具有0.2~100μm厚的有机被膜层。
7.在专利文献4中记载了一种具有均匀外观的熔融zn-al-mg-si镀覆钢板,其具有zn合金镀层,所述zn合金镀层含有mg:2.8%以上、al:10.5%以上、si:0.01~0.5%、剩余包含zn及不可避免的杂质,在该zn合金镀层中mg2zn
11
/mgzn2的x射线强度比为0.5以下。
8.在专利文献5中记载了一种zn-ai-mg系熔融镀覆钢板(zn-ai-mg系热浸镀钢板),其具备钢板和热浸镀层,所述热浸镀层含有4质量%~22质量%的al和1质量%~5质量%的mg、且剩余部分包含zn及不可避免的杂质,其中,与热浸镀层的表面平行的上述热浸镀层的截面中的al相的(200)面的x射线衍射强度i(200)与al相的(111)面的x射线衍射强度i(111)之比即衍射强度比i(200)/1(111)为0.8以上。
9.在专利文献6中记载了一种表面性状优异的熔融zn-al-mg-si镀覆钢材,其在钢材表面具有镀层,所述镀层为al:5~18质量%、mg:1~10质量%、si:0.01~2质量%、剩余部分包含zn及不可避免的杂质,在该镀覆钢材表面,每1mm2存在200个以上的〔al相〕。
10.然而,最近,对于熔融zn-al-mg系镀覆钢材,要求平面部的耐蚀性的进一步提高,此外,更进一步强烈地要求防止涂膜膨起。
11.现有技术文献
12.专利文献
13.专利文献1:日本特开2000-104154号公报
14.专利文献2:日本特开平10-226865号公报
15.专利文献3:日本特开2004-225157号公报
16.专利文献4:日本特开2006-193791号公报
17.专利文献5:国际公开第2011/001662号
18.专利文献6:日本特开2001-355053号公报
技术实现要素:19.发明所要解决的课题
20.本发明是鉴于上述情况而进行的,课题是提供平坦部的耐蚀性优异、而且即使是在镀层表面形成了涂膜的情况下也能够防止涂膜膨起的熔融zn-al-mg系镀覆钢材。
21.用于解决课题的手段
22.为了解决上述课题,本发明采用以下的构成。
23.[1]一种熔融zn-al-mg系镀覆钢材,其特征在于,其具备:钢材;和形成于上述钢材表面的镀层,
[0024]
上述镀层以平均组成计含有mg:1~10质量%、al:4~22质量%,剩余部分包含zn及杂质,
[0025]
在上述镀层中,在〔al/zn/mgzn2的三元共晶组织〕的基体中,包含以上述镀层的截面中的面积率计为10~70%的〔al
·
zn混合组织〕,
[0026]
在上述〔al
·
zn混合组织〕中包含:zn浓度为75质量%以上且低于85质量%的范围的第1区域;和第2区域,所述第2区域位于上述第1区域的内侧、且zn浓度为67质量%以上且低于75质量%的范围,
[0027]
上述镀层的截面中的上述〔al
·
zn混合组织〕中的上述第2区域的面积率为超过0%且为40%以下。
[0028]
[2]根据[1]所述的熔融zn-al-mg系镀覆钢材,其特征在于,上述镀层的平均组成含有mg:1~10质量%、al:8~22质量%,剩余部分为zn及杂质,
[0029]
在上述〔al
·
zn混合组织〕中包含:上述第1区域、上述第2区域和第3区域,所述第3区域位于上述第2区域的内侧、且zn浓度为55质量%以上且低于67质量%的范围。
[0030]
[3]根据[1]或[2]所述的熔融zn-al-mg系镀覆钢材,其特征在于,上述〔al
·
zn混合组织〕中的上述第2区域的面积率为5~40%。
[0031]
[4]根据[1]至[3]中任一项所述的熔融zn-al-mg系镀覆钢材,其特征在于,在将上述镀层在镀层厚度方向的1/2位置处以2等分分割成上述钢材侧和镀层表面侧的情况下,上述〔al
·
zn混合组织〕的核生成点中的以个数比例计为60%以上的核生成点存在于上述镀层的钢材侧的区域中。
[0032]
[5]根据[1]至[4]中任一项所述的熔融zn-al-mg系镀覆钢材,其特征在于,在上述
镀层中进一步以平均组成计含有0.0001~2质量%的si。
[0033]
[6]根据[1]至[5]中任一项所述的熔融zn-al-mg系镀覆钢材,其特征在于,在上述镀层中进一步以平均组成计在合计为0.0001~2质量%的范围内含有ni、ti、zr、sr中的任1种或2种以上。
[0034]
[7]根据[1]至[6]中任一项所述的熔融zn-al-mg系镀覆钢材,其特征在于,在上述镀层中进一步以平均组成计在合计为0.0001~2质量%的范围内含有sb、pb、sn、ca、co、mn、p、b、bi、cr、sc、y、rem、hf中的任1种或2种以上。
[0035]
发明效果
[0036]
根据本发明,能够提供平坦部的耐蚀性优异、而且即使是在镀层表面形成了涂膜的情况下也能够防止涂膜膨起的熔融zn-al-mg系镀覆钢材。
附图说明
[0037]
图1是用扫描型电子显微镜拍摄试样no.1的镀层的截面而得到的表示镀层的反射电子图像的照片。
具体实施方式
[0038]
熔融zn-al-mg系镀覆钢材具有镀层,所述镀层具有下述成分:mg;al;和剩余部分包含zn及杂质,作为金属组织,在〔al/zn/mgzn2的三元共晶组织〕的基体中混合存在〔mgzn2相〕、〔zn相〕、〔al
·
zn混合组织〕中的至少1种。此外,当在热浸镀层中除了含有zn、al、mg以外还含有si的情况下,有可能不仅包含上述的相及组织,还包含〔mg2si相〕。在形成镀层时,通过使钢材浸渍于包含mg、al及zn的镀浴中后将钢材捞起,从而使附着于钢材表面的熔融金属凝固。在镀层凝固时,〔al
·
zn混合组织〕发生结晶,之后〔al/zn/mgzn2的三元共晶组织〕的基体发生结晶,由此在〔al/zn/mgzn2的三元共晶组织〕中形成〔al
·
zn混合组织〕。
[0039]
为了提高这样的熔融zn-al-mg系镀覆钢材的平坦部的耐蚀性,本发明的发明者们进行了深入研究,结果查明〔al
·
zn混合组织〕成为腐蚀初期的起点。〔al
·
zn混合组织〕是来源于al-zn-mg的三元系平衡状态图中的高温的al
″
相(为固溶有zn的al固溶体,大多包含少量的mg)的组织,根据状态图,在常温下处于包含微细的zn相和微细的al相的状态。对该〔al
·
zn混合组织〕的结构进行了详细研究,结果获知:能够分成zn浓度比较高的第1区域和zn浓度比较低的第2区域,第2区域的存在比例越大,则越存在平坦部的耐蚀性降低的倾向。而且判明了:以往的熔融zn-al-mg系镀覆钢材的第2区域的存在比例变得比较高。因此认知到:通过选择使第2区域的存在比例降低的制造条件,可得到平坦部的耐蚀性优异的熔融zn-al-mg系镀覆钢材。此外判明了:通过熔融zn-al-mg系镀覆钢材的平坦部的耐蚀性提高,从而即使是在熔融zn-al-mg系镀覆钢材的镀层表面形成了涂膜的情况下,也能够预防涂膜膨起。
[0040]
本实施方式的熔融zn-al-mg系镀覆钢材具备:钢材;和形成于钢材表面的镀层,镀层以平均组成计含有mg:1~10质量%、al:4~22质量%,剩余部分包含zn及杂质,在镀层中,在〔al/zn/mgzn2的三元共晶组织〕的基体中包含以镀层的截面中的面积率计为10~70%的〔al
·
zn混合组织〕,在〔al
·
zn混合组织〕中包含:zn浓度为75质量%以上且低于85质量%的范围的第1区域;和第2区域,所述第2区域位于第1区域的内侧、且zn浓度为67质
量%以上且低于75质量%的范围,镀层的截面中的〔al
·
zn混合组织〕中的第2区域的面积率为超过0%且为40%以下。
[0041]
此外,本实施方式的熔融zn-al-mg系镀覆钢材在镀层的平均组成含有mg:1~10质量%、al:8~22质量%、剩余部分为zn及杂质的情况下,也可以在〔al
·
zn混合组织〕中包含:第1区域、第2区域和第3区域,所述第3区域位于第2区域的内侧、且zn浓度为55质量%以上且低于67质量%的范围。
[0042]
此外,〔al
·
zn混合组织〕中的第2区域的面积率也可以为5~40%。
[0043]
进而,在将镀层在镀层厚度方向的1/2位置处以2等分分割成钢材侧和镀层表面侧的情况下,优选〔al
·
zn混合组织〕的核生成点中的以个数比例计为60%以上的核生成点存在于镀层的钢材侧的区域中。
[0044]
以下,对本实施方式的熔融zn-al-mg系镀覆钢材进行说明。
[0045]
成为镀层的基底的钢材对材质没有特别限制。作为材质,可以适用于普通钢、al镇静钢、一部分高合金钢,对形状也没有特别限制。此外,也可以对钢材实施ni预镀。通过对钢材适用后述的热浸镀法,从而形成本实施方式的镀层。
[0046]
接下来,对镀层的化学成分进行说明。
[0047]
本实施方式的镀层以平均组成计含有mg:1~10质量%、al:4~22质量%,作为剩余部分包含zn及杂质。此外,镀层也可以以平均组成计含有si:0.0001~2质量%。进而,镀层也可以以平均组成计含有合计为0.0001~2质量%的ni、ti、zr、sr中的任1种或2种以上。进而,镀层还可以以平均组成计含有合计为0.0001~2质量%的sb、pb、sn、ca、co、mn、p、b、bi、cr、sc、y、rem、hf中的任1种或2种以上。
[0048]
mg的含量以平均组成计为1~10质量%的范围。mg是为了提高镀层的耐蚀性所需的元素。镀层中的mg的含量低于1质量%时,提高耐蚀性的效果变得不充分。如果mg的含量超过10质量%,则镀浴中的渣滓(dross)产生变得显著,因镀层上的渣滓附着而产生未正常形成镀层的部位,因此有可能耐蚀性降低。因此,mg的含量设定为10质量%以下。从因渣滓的产生而引起耐蚀性降低的观点出发,优选设定为1.5~6质量%。更优选设定为2~5质量%的范围。
[0049]
al的含量以平均组成计为4~22质量%的范围。al是为了确保耐蚀性所需的元素。镀层中的al的含量低于4质量%时,提高耐蚀性的效果变得不充分,如果超过22质量%,则虽然原因不明,但耐蚀性降低。从耐蚀性的观点出发,优选设定为8~22质量%。更优选设定为9~13质量%。
[0050]
此外,镀层也可以在0.0001~2质量%的范围内含有si。si是对于提高镀层的密合性而言有效的元素。通过含有0.0001质量%以上的si从而表现出提高密合性的效果,因此优选含有0.0001质量%以上的si。另一方面,即使含有si超过2质量%,提高镀层密合性的效果也饱和,因此si的含量设定为2质量%以下。从镀层密合性的观点出发,也可以设定为0.02~1质量%的范围,也可以设定为0.03~0.8质量%的范围。
[0051]
此外,在镀层中,也可以以平均组成计含有合计为0.0001~2质量%的ni、ti、zr、sr中的任1种或2种以上。包含上述这些元素的金属间化合物作为〔al
·
zn混合组织〕的结晶核(晶核)起作用,使〔al/mgzn2/zn的三元共晶组织〕变得更微细、均匀,提高镀层的外观、平滑性。将上述这些元素中的1种或2种以上设定为合计为0.0001~2质量%的理由是由于低
于0.0001质量%时,使凝固组织变得微细均匀的效果变得不充分,如果超过2质量%,则不仅使〔al/zn/mgzn2的三元共晶组织〕变得微细化的效果饱和,而且反而增大镀层的表面粗糙度从而外观变差,因此将上限设定为2质量%。特别是在以提高外观作为目的来添加的情况下,优选含有0.001~0.5质量%。更优选为0.001~0.05质量%的范围,进一步优选为0.002~0.01质量%的范围。
[0052]
在镀层中,也可以以平均组成计含有合计为0.0001~2质量%的sb、pb、sn、ca、co、mn、p、b、bi、cr、sc、y、rem、hf中的1种或2种以上。通过含有上述这些元素,能够进一步改善耐蚀性。rem是周期表中的原子序号为57~71的稀土类元素中的1种或2种以上。
[0053]
镀层的化学成分的剩余部分为锌及杂质。
[0054]
接下来,对镀层的组织进行说明。本实施方式的镀层在〔al/zn/mgzn2的三元共晶组织〕的基体中包含以相对于构成镀层的全部组织的总面积而言的面积率计为10~70%的〔al
·
zn混合组织〕。此外,在〔al/zn/mgzn2的三元共晶组织〕的基体中,除了包含〔al
·
zn混合组织〕以外,还可以包含〔mgzn2相〕、〔zn相〕、〔mg2si相〕。
[0055]
〔al/zn/mgzn2的三元共晶组织〕是指al相、zn相和金属间化合物即mgzn2相的三元共晶组织,形成有〔al/zn/mgzn2的三元共晶组织〕的al相例如相当于al-zn-mg的三元系平衡状态图中的高温下的“al
″
相”(为固溶有zn相的al固溶体,大多包含少量的mg)。该高温下的al
″
相在常温下通常分离成微细的al主体相和微细的zn主体相而出现。此外,〔al/zn/mgzn2的三元共晶组织〕中的zn相是固溶有少量的al、根据情况进一步固溶有少量的mg的zn固溶体。〔al/zn/mgzn2的三元共晶组织〕中的mgzn2相是在zn-mg的二元系平衡状态图的zn为约84质量%的附近处存在的金属间化合物相。仅由状态图观察可认为即使在各个相中固溶有si、其他的元素,也为少量,其量通过通常的分析无法明确地进行区别,因此将由该3个相形成的三元共晶组织在本说明书中表示为〔al/zn/mgzn2的三元共晶组织〕。
[0056]
接下来,对〔al
·
zn混合组织〕进行说明。在本实施方式中,将高温相的al
″
相在冷却时分离成微细的zn主体相和微细的al主体相而形成的组织称为〔al
·
zn混合组织〕。需要说明的是,zn主体相有可能固溶有al和mg。al主体相有可能固溶有zn和mg。
[0057]
〔al
·
zn混合组织〕是在扫描型电子显微镜的反射电子图像中在〔al/zn/mgzn2的三元共晶组织〕的基体中具有清晰的边界且看起来为岛状的相,它例如相当于al-zn-mg的三元系平衡状态图中的高温下的“al
″
相”(为固溶有zn相的al固溶体,包含少量的mg)。关于该高温下的al
″
相,固溶的zn量、mg量根据镀浴的al、mg浓度不同而异。该高温下的al
″
相在常温下通常分离成微细的al主体相和微细的zn主体相,但在常温下所见到的岛状的形状可以视为保留了高温下的al
″
相的形骸。仅由状态图观察可认为在该相中未固溶有si、其他的添加元素,或者即使固溶有si、其他的添加元素,也为极微量,但通过通常的分析无法明确地进行区别,因此将该来源于高温下的al
″
相并且在形状上保留了al
″
相的形骸的组织在本说明书中称为〔al
·
zn混合组织〕。该〔al
·
zn混合组织〕与形成了〔al/zn/mgzn2的三元共晶组织〕的al相在扫描型电子显微镜的反射电子图像中能够清晰地进行区别。
[0058]
镀层的截面中的〔al
·
zn混合组织〕的面积率优选为10~70%的范围。如果〔al
·
zn混合组织〕的面积率为该范围,则能够提高平面部的耐蚀性。
[0059]
面积率的测定方法是对镀层的截面通过扫描型电子显微镜的反射电子图像进行观察。以将倍率放大至1000倍的状态拍摄5个部位的照片。照片按照使镀层的厚度整体进入
视场中的方式进行拍摄。照片拍摄位置是随机地进行选择的。必须接受面积率的计算结果并任意地再选择拍摄位置。进而,使用扫描型电子显微镜中附属的能量色散型x射线元素分析装置,取得与所拍摄的照片相对应的元素测绘数据,确定〔al
·
zn混合组织〕。然后,测定全部的截面照片中出现的〔al
·
zn混合组织〕的全部截面积,通过将其除以全部的截面照片中出现的镀层的截面积,从而测定〔al
·
zn混合组织〕的面积率。
[0060]
此外,〔zn相〕是指在〔al/zn/mgzn2的三元共晶组织〕的基体中具有清晰的边界且看起来为岛状的相,实际上有时还会固溶有少量的al进而少量的mg。仅由状态图观察可认为在该相中未固溶有si、其他的添加元素,或者即使固溶有si、其他的添加元素,也为极微量。该〔zn相〕与形成了〔al/zn/mgzn2的三元共晶组织〕的zn相在扫描型电子显微镜的反射电子图像中能够清晰地进行区别。在本实施方式的镀层中,根据制造条件的不同也有可能包含〔zn相〕,但在实验中基本未见到对平面部耐蚀性提高造成的影响,因此即使在镀层中包含〔zn相〕,也没有特别问题。
[0061]
此外,〔mgzn2相〕是指在〔al/zn/mgzn2的三元共晶组织〕的基体中具有清晰的边界且看起来为岛状的相,实际上有时还会分散、固溶有少量的al。仅由状态图观察可认为在该相中未固溶有si、其他的添加元素,或者即使固溶有si、其他的添加元素,也为极微量。该〔mgzn2相〕与形成了〔al/zn/mgzn2的三元共晶组织〕的mgzn2相在扫描型电子显微镜的反射电子图像中能够清晰地进行区别。在本实施方式的镀层中,根据制造条件的不同也有可能不含〔mgzn2相〕,但在大部分的制造条件下是被包含于镀层中的。
[0062]
此外,〔mg2si相〕是指在含有si的镀层的凝固组织中具有清晰的边界且看起来为岛状的相。仅由状态图观察可认为未固溶有zn、al、其他的添加元素,或者即使固溶有zn、al、其他的添加元素,也为极微量。该〔mg2si相〕在镀层中在扫描型电子显微镜的反射电子图像中能够清晰地进行区别。
[0063]
接下来,对〔al
·
zn混合组织〕的微细结构进行说明。〔al
·
zn混合组织〕如上所述显示出保留了高温下的al
″
相的形骸的岛状的形状。此外,〔al
·
zn混合组织〕的内部结构根据状态图可推测在常温下显示出分离成微细的al相和微细的zn相的形态。
[0064]
另一方面,如果观察〔al
·
zn混合组织〕的zn浓度的分布,则〔al
·
zn混合组织〕至少能够区分为第1区域和第2区域,所述第2区域位于第1区域的内侧且平均zn浓度比第1区域低。此外,在镀层的平均al浓度为8~22质量%的情况下,在第2区域的内侧包含平均zn浓度比第2区域更低的第3区域。第1区域是在对镀层进行截面观察的情况下位于〔al
·
zn混合组织〕的最外侧,构成了与〔al/zn/mgzn2的三元共晶组织〕的边界。第2区域位于第1区域的内侧,第3区域位于第2区域的更内侧。
[0065]
第1区域是zn浓度为75质量%以上且低于85质量%的区域,第2区域是zn浓度为67质量%以上且低于75质量%的区域,第3区域是zn浓度为55质量%以上且低于67质量%的区域。zn以外的剩余部分为al及杂质。此外,在镀层含有si的情况下,有可能在第1区域、第2区域及第3区域中的任一者或全部的区域中包含si。
[0066]
〔al
·
zn混合组织〕中的第2区域的比例以对镀层进行截面观察的情况下的面积率计相对于〔al
·
zn混合组织〕需要为超过0%且为40%以下的范围。第2区域的比例可以为5~40%的范围,也可以为5%以上且低于40%,还可以为5~35%的范围。〔al
·
zn混合组织〕中的第2区域的存在比例越少,则平坦部的耐蚀性越提高。然而,将第2区域的面积率设定为
0%在制造上伴有困难,因此将下限设定为超过0%。此外,如果第2区域超过40%,则平坦部的耐蚀性降低,因此将上限设定为40%以下。确认了:如果开始腐蚀,则镀层的〔al
·
zn混合组织〕中的特别是zn浓度为67质量%以上且低于75质量%的第2区域优先被腐蚀。因此,据推测:通过减少成为腐蚀的起点的第2区域,从而平坦部的耐蚀性提高。
[0067]
此外,没有必要对第1区域及第3区域的面积率进行特别限定。
[0068]
对〔al
·
zn混合组织〕的微细结构的确定方法进行说明。〔al
·
zn混合组织〕的微细结构的确定方法是利用〔al
·
zn混合组织〕的面积率的测定中使用的照片的元素测绘数据。首先,对〔al
·
zn混合组织〕内部的zn浓度的分布进行分析。在分析时,使用扫描型电子显微镜(sem)中附属的能量色散型x射线元素分析装置,将sem的加速电压设定为15kv。该情况下,根据特性x射线的逸出深度的关系,实质上zn浓度是对每个约1μm2的区域进行测定。通过将其进行绘图化,能够以约1μm的网格进行成分分析。基于由该成分分析结果得到的zn浓度(质量%)来决定第1区域、第2区域及第3区域的范围。
[0069]
具体而言,根据成分分析结果,将zn浓度为75质量%以上且低于85质量%的范围的区域确定为第1区域,将zn浓度为67质量%以上且低于75质量%的范围的区域确定为第2区域,将zn浓度为55质量%以上且低于67质量%的范围的区域确定为第3区域。然后,测定各个区域的截面积。对全部照片中出现的全部的〔al
·
zn混合组织〕实施以上的测定,测定全部的〔al
·
zn混合组织〕中的第2区域的总面积。然后,通过将第2区域的总面积除以作为测定对象的〔al
·
zn混合组织的全部截面积〕,从而测定第2区域的面积率。
[0070]
本实施方式的熔融zn-al-mg系镀覆钢材如下文所述的那样通过下述方式来形成:通过使钢材浸渍于镀浴中后将钢材捞起,从而使附着于钢材表面的熔融金属凝固。如上所述,在镀层凝固时,首先〔al
·
zn混合组织〕发生结晶,之后,〔al/zn/mgzn2的三元共晶组织〕的基体发生结晶。最初结晶的〔al
·
zn混合组织〕来源于al-zn-mg的三元系平衡状态图中的高温的al
″
相,该高温的al
″
相最终成为本实施方式中的〔al
·
zn混合组织〕。在〔al
·
zn混合组织〕中,首先,在熔融金属中产生的核生成点成为起点,一次臂从核生成点进行生长,进而由一次臂生成二次臂。因此,〔al
·
zn混合组织〕成为以核生成点作为起点的枝晶状的组织。
[0071]
而且,就本实施方式的熔融zn-al-mg系镀覆钢材而言,在将镀层在镀层厚度方向的1/2位置处以2等分分割成钢材侧和镀层表面侧的情况下,优选〔al
·
zn混合组织〕的核生成点中的以个数比例计为60%以上的核生成点存在于镀层的钢材侧的区域中。由此,在镀层的构成组织之中,成为腐蚀初期的起点的〔al
·
zn混合组织〕变得在钢材侧的区域中大量存在,镀层的表面侧的区域中的〔al
·
zn混合组织〕的存在比例变少。由此,镀层的平坦部的耐蚀性更加提高。
[0072]
此外,在镀层上形成涂膜的情况下,〔al
·
zn混合组织〕可成为镀层与涂膜的密合性的阻碍要因。通过在镀层的钢板侧的区域中大量存在〔al
·
zn混合组织〕,使得在表面露出的〔al
·
zn混合组织〕的比例相对地降低,因此下述效果进一步被提高:防止在镀层表面形成了涂膜的情况下的涂膜膨起。
[0073]
〔al
·
zn混合组织〕的核生成点的分布的测定方法设定为如下所述。首先,通过进行镀层的截面观察来测定镀层的厚度。接着,在镀层的表面,将一边为1mm的正方形的区域设定为测定区域。接着,将测定区域中的镀层从表面慢慢地进行磨削,对新出现的磨削面通过电子显微镜进行观察。具体而言,在将镀层的总厚度设定为t时,通过磨削使距离镀层表
面在深度方向上为t/4位置、t/2位置及3t/4位置依次露出,在各磨削面中,随时通过电子显微镜来确认〔al
·
zn混合组织〕的形态。磨削的深度通过对事先赋予的压痕的形状变化进行观察来控制。
[0074]
〔al
·
zn混合组织〕中的核生成点是〔al
·
zn混合组织〕的一次臂彼此的结合点。在距离〔al
·
zn混合组织的核生成点〕比较远的磨削面,看起来一次臂是离散地被配置的,但在距离核生成点比较近的磨削面,看起来4个或6个一次臂是靠近的。因此,在对各磨削面进行观察时,由各磨削面中的一次臂的形状的变化来推测核生成点是位于观察中的磨削面的钢材侧、还是位于镀层的表面侧。像这样操作,在距离镀层表面在深度方向上为t/4位置、t/2位置及3t/4位置处的磨削面中,通过随时确认〔al
·
zn混合组织〕的形态,能够确认核生成点是位于比t/2位置更靠钢材侧、还是位于镀层表面侧。然后,求出在测定区域内观察到的〔al
·
zn混合组织〕的核生成点的全部个数中的位于比t/2位置更靠钢材侧的核生成点的个数的比例。对合计5处测定区域实施以上的方法,将所得到的值的平均作为位于比该镀层的t/2位置更靠钢材侧的核生成点的个数的比例。
[0075]
镀层的附着量优选为10~300g/m2的范围,也可以为20~250g/m2的范围。如果镀层的附着量少,则无法充分确保耐蚀性。此外,如果镀层的附着量过厚,则有可能在加工成部件形状等时在镀层中产生开裂。
[0076]
接下来,对本实施方式的熔融zn-al-mg系镀覆钢材的制造方法进行说明。本实施方式的熔融zn-al-mg系镀覆钢材通过下述的所谓热浸镀法来形成:使钢材表面附着镀浴,接着将钢材从镀浴中捞起而使附着于钢材表面的熔融金属凝固。
[0077]
镀浴的组成含有mg:1~10质量%、al:4~22质量%、作为剩余部分包含zn及杂质为宜。此外,在镀浴中,也可以含有si:0.0001~2质量%。进而,在镀浴中,也可以含有合计为0.0001~2质量%的ni、ti、zr、sr中的任1种或2种以上。更进一步地,在镀浴中,也可以含有合计为0.0001~2质量%的sb、pb、sn、ca、co、mn、p、b、bi、cr、sc、y、rem、hf中的任1种或2种以上。
[0078]
镀浴的温度优选为超过380℃且为600℃以下的范围,也可以为400~600℃的范围。
[0079]
浸渍于镀浴中之前的钢材优选通过在还原性气氛中进行加热来对表面进行还原处理。例如,在氮与氢的混合气氛中在600℃以上、优选在750℃以上进行30秒以上热处理。将还原处理结束后的钢材冷却至镀浴的温度之后,浸渍于镀浴中。浸渍时间例如可以为1秒以上。在将浸渍于镀浴中的钢材捞起时,通过气体擦拭来调整镀层的附着量。附着量如上所述优选为10~300g/m2的范围,也可以为20~250g/m2的范围。
[0080]
在本实施方式的熔融zn-al-mg系镀覆钢材的制造方法中,从镀浴中捞起后的冷却条件是重要的。冷却条件有下述2种,可以采用任一种条件。
[0081]
需要说明的是,从镀浴中捞起后直至达到365~380℃的温度为止的冷却条件没有特别限定,只要为通常的冷却条件即5~10℃/秒左右即可。
[0082]
第1冷却条件设定为下述条件:在将钢材从镀浴中捞起后,在到达顶辊之前的镀层未完全凝固的365~380℃的温度范围内以恒定的温度进行保持,之后从365℃进行骤冷。这里的温度是熔融金属(镀层)的表面温度。在365~380℃的温度范围内以恒定的温度进行保持的情况下的保持时间优选为10~300秒的范围。此外,在365~380℃内恒定保持后进行骤
冷的情况下的平均冷却速度优选为50~100℃/秒的范围。关于骤冷,在温度保持时间的结束后立即进行骤冷为宜。此外,骤冷进行至镀层的温度达到100℃以下为止为宜。通过进行上述这些保持、骤冷,可得到目标组织。在365~380℃的温度区域中进行保持的理由是由于:由在镀覆中以未凝固的状态残留的液相促进通过固液界面反应而在该温度下形成的高温下的al
″
相的生长。在完全凝固的状态下,不会促进组织间的元素移动,高温下的al
″
相不生长,因此得不到目标组织。从365℃进行骤冷的理由是由于:抑制成为〔al
·
zn混合组织〕的第2区域的高温下的al
″
相的形成。需要说明的是,当在镀层完全凝固之后进行再加热而在365~380℃的温度区域中进行保持的情况下,有可能形成使耐蚀性劣化的mg2zn11相,这是不优选的。此外,镀层中的mg的含量低于1质量%时,在365~380℃的温度区域中,在镀覆中以未凝固的状态残留的液相的比率小,因此无法促进高温下的al
″
相的生长,得不到目标组织。从促进高温下的al
″
相的生长的观点出发,镀层中的mg的含量优选为1.5质量%以上。
[0083]
第2冷却条件设定为下述条件:在将钢材从镀浴中捞起后,在到达顶辊之前的镀层未完全凝固的380℃~365℃之间进行慢冷却,之后进行骤冷。这里的温度是熔融金属(镀层)的表面温度。在从380℃至365℃为止的温度范围内进行慢冷却的情况下的平均冷却速度优选为0.1~0.4℃/秒的范围。此外,在慢冷却后进行骤冷的情况下的平均冷却速度优选为50~100℃/秒的范围。关于骤冷,在慢冷却的结束后立即进行骤冷为宜。此外,骤冷进行至镀层的温度达到100℃以下为止为宜。
[0084]
如果脱离上述的冷却条件,则导致无法将第2区域的面积率设定为超过0%且为40%以下的范围。
[0085]
通过以上所述,能够制造本实施方式的熔融zn-al-mg系镀覆钢材。
[0086]
本实施方式的熔融zn-al-mg系镀覆钢材的平坦部的耐蚀性优异,而且即使是在镀层表面形成了涂膜的情况下也能够防止涂膜膨起。
[0087]
实施例
[0088]
将板厚为0.8mm的spcc(jis g3141)进行脱脂后,用东荣公司制的热浸镀模拟器在n
2-h2气氛中进行800℃、60秒加热还原处理,冷却至镀浴温度后,在与表1中所示的镀层的平均组成相同组成的450℃的镀浴中浸渍3秒,之后通过n2擦拭将镀层附着量以单面计设定为135g/m2。
[0089]
〔al
·
zn混合组织〕的控制通过镀覆后的冷却控制来进行,通过下述方式来制成作为目标的构成组织:在到达顶辊之前的镀层未完全凝固的380~365℃之间保持或滞留10~300秒钟,之后以50~100℃/秒的平均冷却速度骤冷至100℃以下。发明例47~52是在380~365℃之间进行40~150秒钟慢冷却(慢冷却时的平均冷却速度为0.1~0.4℃/秒的范围内)之后骤冷至100℃以下,其他的发明例是在375℃下仅保持表1中所示的保持时间后骤冷至100℃以下。比较例5未进行380~365℃之间的保持或慢冷却。作为制作试样的截面sem图像的一个例子,将no.1的镀层的截面照片示于图1中。将结果示于表1a、表1b、表2a及表2b中。
[0090]
在表1a、表1b中示出了镀覆后的冷却条件和镀层的平均组成。在表2a、表2b中示出了镀层截面中的〔al
·
zn混合组织〕的面积率、〔al
·
zn混合组织〕中的第2区域的面积率、第1区域、第2区域及第3区域的平均zn浓度、〔al
·
zn混合组织〕的核生成点的位置。此外,示出了平面耐蚀性及涂装后耐蚀性的评价结果。
[0091]
镀层的平均组成通过下述方式来测定:将镀层剥离并溶解后,通过电感耦合等离
子体发光分析法对镀层中所含的元素的含量进行分析。
[0092]
镀层中的〔al
·
zn混合组织〕的面积率是对镀层的截面用扫描型电子显微镜以放大至1000倍的状态拍摄5个部位的反射电子图像。照片按照使镀层的厚度整体进入视场中的方式进行拍摄。照片拍摄位置是随机地进行选择的。进而,使用扫描型电子显微镜中附属的能量色散型x射线元素分析装置,取得与所拍摄的照片相对应的元素测绘数据,确定〔al
·
zn混合组织〕。然后,测定全部的截面照片中出现的〔al
·
zn混合组织〕的全部截面积,通过将其除以全部的截面照片中出现的镀层的截面积,从而测定〔al
·
zn混合组织〕的面积率。
[0093]
〔al
·
zn混合组织〕中的第2区域的面积率、第1区域、第2区域及第3区域的平均zn浓度如下那样操作来进行测定。
[0094]
对镀层的截面用扫描型电子显微镜以放大至1000倍的状态拍摄5个部位的反射电子图像。照片按照使镀层的厚度整体进入视场中的方式进行拍摄。照片拍摄位置是随机地进行选择的。进而,使用扫描型电子显微镜中附属的能量色散型x射线元素分析装置,取得与所拍摄的照片相对应的元素测绘数据,确定〔al
·
zn混合组织〕。取得元素测绘数据时的sem的加速电压设定为15kv。该情况下,变成对每个约1μm2的区域测定zn浓度,能够以约1μm的网格进行成分分析。基于由元素测绘数据的成分分析结果得到的zn浓度(质量%)来决定第1区域、第2区域及第3区域的范围。
[0095]
具体而言,将zn浓度为75质量%以上且低于85质量%的范围的区域确定为第1区域,将zn浓度为67质量%以上且低于75质量%的范围的区域确定为第2区域,将zn浓度为55质量%以上且低于67质量%的范围的区域确定为第3区域。然后,测定各个区域的截面积。对全部照片中出现的全部的〔al
·
zn混合组织〕实施以上的测定,测定全部的〔al
·
zn混合组织〕中的第2区域的总面积。然后,通过将第2区域的总面积除以作为测定对象的〔al
·
zn混合组织〕的全部截面积,从而测定第2区域的面积率。
[0096]
此外,由第1区域、第2区域及第3区域的zn浓度的测定结果求出各区域中的zn的平均浓度。
[0097]
〔al
·
zn混合组织〕的核生成点的分布的测定方法设定为如下所述。首先,通过进行镀层的截面观察来测定镀层的厚度。接着,在镀层的表面,将一边为1mm的正方形的区域设定为测定区域。接着,将测定区域中的镀层从表面慢慢地进行磨削,对新出现的磨削面通过电子显微镜进行观察。具体而言,在将镀层的总厚度设定为t时,在距离镀层表面在深度方向上为t/4位置、t/2位置及3t/4位置处使磨削面依次露出,在各磨削面中,随时通过电子显微镜来确认al
·
zn混合组织的形态。磨削的深度通过对事先赋予的压痕的形状变化进行观察来控制。
[0098]
〔al
·
zn混合组织〕中的核生成点是〔al
·
zn混合组织〕的一次臂彼此的结合点。在距离〔al
·
zn混合组织〕的核生成点比较远的磨削面,看起来一次臂是离散地被配置的,但在距离核生成点比较近的磨削面,看起来4个或6个一次臂是靠近的。因此,在对各磨削面进行观察时,由各磨削面中的一次臂的形状的变化来推测核生成点是位于观察中的磨削面的钢材侧、还是位于镀层的表面侧。像这样操作,在距离镀层表面在深度方向上为t/4位置、t/2位置及3t/4位置处的磨削面中,通过随时确认〔al
·
zn混合组织〕的形态,从而确认核生成点是位于比t/2位置更靠钢材侧、还是位于镀层表面侧。然后,求出在测定区域内观察到的
〔al
·
zn混合组织〕的核生成点的全部个数中的位于比t/2位置更靠钢材侧的核生成点的个数的比例。对合计5处测定区域实施以上的方法,将所得到的值的平均作为位于比该镀层的t/2位置更靠钢材侧的核生成点的个数的比例。
[0099]
在表2a、表2b中设置〔al
·
zn混合组织〕的核生成点的位置的栏,在将镀层在镀层厚度方向的1/2位置处以2等分分割成钢材侧和镀层表面侧的情况下,将〔al
·
zn混合组织〕的核生成点中的以个数比例计为60%以上的核生成点存在于镀层的钢材侧的区域中的情况设定为
○
,将不是这样的情况设定为
×
。
[0100]
将所得到的合金镀覆钢板切断成100mm
×
50mm,供于平面耐蚀性评价试验。平面耐蚀性的评价通过jaso-cct-m609中规定的腐蚀促进试验来进行,在120个循环后通过比较腐蚀减量来进行。评价基准设定为如下所述,将
◎
、
○
、
△
作为合格。
[0101]
◎
:腐蚀减量低于40g/m2[0102]
○
:腐蚀减量为40g/m2以上且低于60g/m2[0103]
△
:腐蚀减量为60g/m2以上且低于80g/m2[0104]
×
:腐蚀减量为80g/m2以上
[0105]
涂装后耐蚀性(涂装后的涂膜膨起)通过下述方式进行评价:对于平板的试验片,形成膜厚为1.2μm的化学转化处理层,在形成了膜厚为20μm的涂膜层之后,对于正面用切割刀赋予到达至基底金属的割伤,进行120个循环的将sst4小时
→
干燥2小时
→
湿润2小时作为1个循环的cct。以试验结束后的割伤的单侧的最大膨起宽度进行判定。
[0106]
《化学转化处理层》
[0107]
通过下述方式来形成化学转化处理膜:将使硅烷偶联剂、丹宁酸、二氧化硅及聚酯树脂混合而成的无铬酸盐化学转化处理液涂布于镀层上并进行干燥。
[0108]
《涂膜层》
[0109]
通过在化学转化处理膜上涂布下述记载的底漆涂料树脂及外涂层涂料树脂来形成涂膜层。由底漆涂料树脂形成的层的厚度设定为5μm,由外涂层涂料树脂形成的层的厚度设定为15μm,合计设定为20μm。
[0110]
《涂膜层的造膜成分》
[0111]
(1)正面和背面的底漆涂料树脂
[0112]
聚酯/三聚氰胺+异氰酸酯并用固化型(nippon fine coatings公司制flc687涂料树脂)
[0113]
(2)正面的外涂层涂料树脂
[0114]
高分子聚酯/三聚氰胺固化型(nippon fine coatings公司制flc7000涂料树脂)
[0115]
(3)背面的外涂层涂料树脂
[0116]
聚酯/三聚氰胺固化型(nippon fine coatings公司制flc100hq涂料树脂)
[0117]
以下示出涂装后耐蚀性的评价基准。通过以下所示的评分来进行判定。将
◎
、
○
、
△
作为合格。
[0118]
◎
:最大膨起宽度低于5mm
[0119]
○
:最大膨起宽度为5mm以上且低于8mm
[0120]
△
:最大膨起宽度为8mm以上且低于10mm
[0121]
×
:最大膨起宽度为10mm以上
[0122]
[表1a]
[0123][0124]
下划线表示为本发明的范围外。
[0125]
[表1b]
[0126][0127]
下划线表示为本发明的范围外。
[0128]
[表2a]
[0129][0130]
下划线表示为本发明的范围外。
[0131]
[表2b]
[0132][0133]
下划线表示为本发明的范围外。
[0134]
如图1中所示的那样,发明例no.1的镀层在〔al/zn/mgzn2的三元共晶组织〕的基体中包含了〔al
·
zn混合组织〕。
[0135]
同样地,发明例的no.2~52、比较例no.1~5的镀层在〔al/zn/mgzn2的三元共晶组织〕的基体中包含了〔al
·
zn混合组织〕。
[0136]
如表1a、表1b、表2a及表2b中所示的那样,发明例的no.1~52的熔融zn-al-mg系镀覆钢材都满足本发明的范围,平面耐蚀性及涂装后耐蚀性良好。此外,如表2中所示的那样,〔al
·
zn混合组织〕的核生成点的位置被评价为
“○”
的熔融zn-al-mg系镀覆钢材的平面耐蚀性及涂装耐蚀性更优异。
[0137]
另一方面,比较例no.1的熔融zn-al-mg系镀覆钢材的镀层的al含量低,镀层中的〔al
·
zn混合组织〕的面积率低,此外,在〔al
·
zn混合组织〕中不含第2区域。因此,平面耐蚀性及涂装后耐蚀性变得低劣。
[0138]
比较例no.2的熔融zn-al-mg系镀覆钢材的镀层的al含量过量,镀层中的〔al
·
zn混合组织〕的面积率高,此外,〔al
·
zn混合组织〕中的第2区域的面积率也变高,平面耐蚀性及涂装后耐蚀性变得低劣。
[0139]
比较例no.3的熔融zn-al-mg系镀覆钢材在镀层中不含mg,此外,〔al
·
zn混合组织〕中的第2区域的面积率也变高,平面耐蚀性及涂装后耐蚀性变得低劣。
[0140]
比较例no.4的熔融zn-al-mg系镀覆钢材的镀层中的mg含量过量,此外,〔al
·
zn混合组织〕中的第2区域的面积率也变高,平面耐蚀性及涂装后耐蚀性变得低劣。
[0141]
比较例no.5的熔融zn-al-mg系镀覆钢材由于未进行380~365℃之间的保持或慢冷却,因此〔al
·
zn混合组织〕中的第2区域的面积率变高,平面耐蚀性及涂装后耐蚀性变得低劣。