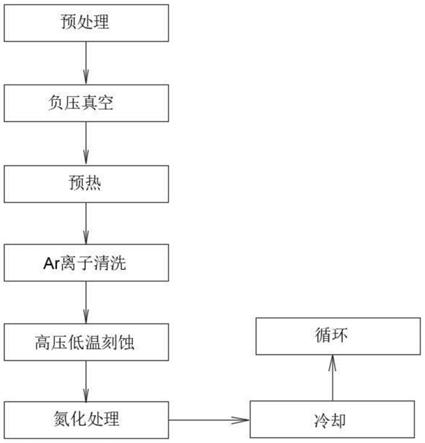
1.本发明涉及表面氮化处理技术领域,涉及一种金属材料表面高压低温氮化工艺。
背景技术:2.离子氮化法是在几十帕至几千帕的含氮气氛中,以炉体为阳极,被处理工件为阴极,在阴阳极间加上数百伏的直流电压,由于辉光放电现象便会产生象霓红灯一样的柔光覆盖在被处理工件的表面。此时,已离子化了的气体成分被电场加速,撞击被处理工件表面而使其加热。同时依靠溅射及离子化作用等对工件表面进行离子氮化处理。
3.现有技术中的离子氮化法主要为分解氨气或使用氰化物来进行氮化,此技术被广泛应用于汽车、机械、精密仪器、挤压成型机、模具等许多领域,而且主要应用在温度较高的金属表面,其中金属表面温度一般不低于250℃,但是在表面温度低于250℃后,现有技术无法进行处理,因其应用范围存在局限性。
技术实现要素:4.本发明的目的在于提供一种金属材料表面高压低温氮化工艺,解决现有技术无法针对250℃以下的金属表面进行氮化处理的问题。
5.本发明的目的通过以下述技术方案来实现,一种金属材料表面高压低温氮化工艺,其特征在于,包括以下步骤:
6.s1.预处理,将待加工金属工件表面进行抛光,随后加入到含有85%的酒精溶液中进行清洗,其中清洗过程采用超声清洗,得到清洗中间件;
7.s2.负压真空,将中间件表面进行丙酮擦拭处理,随即进行加热烘干处理,烘干后,进行负压抽真空处理;
8.s3.预热,将负压真空后的工件进行230℃-250℃的高温加热处理,加热处理后进行恒温静置;
9.s4.ar离子清洗,恒温静置后,在金属工件表面通入氩气处理,通入气压为1pa-1.5pa,随即接入脉冲偏压,进行辉光清洗;
10.s5.高压低温刻蚀,辉光清洗后加入再次加入氩气并同时开启离子源进行刻蚀,刻蚀持续时间10min-15min;
11.s6.氮化处理,再次进行刻蚀后,开启氮气持续氮化处理60min;
12.s7.冷却,静置冷却,直至工件表面温度降至140℃-160℃以下,停止静置;
13.s8.循环上述步骤。
14.需要说明的是,申请人经过长时间的研究,结合现有技术的简单化学反应等进行氮化处理的缺陷以及使用范围,得出上述的实验处理过程,其中实验的处理过程中,通入氩气、偏压处理以及负压真空等均区别于现有技术的简单的化学反应,同时现有技术因为是针对金属表面为250℃以上的金属表面进行加工,因此无法合理进行此温度下的加工,申请人突破了上述技术难题,将250℃以下的金属也进行了同等效果的处理。
15.所述s1具体为:超声清洗持续时长为8min-10min,其中超声清洗过程中采用交变频率波进行持续清洗。
16.需要说明的是,超声的持续时间与预处理中的酒精预先处理和抛光工序有关,后两者的处理时间越长则前者的超声处理时间越短,本技术将超声处理放在预处理之后,区别现有技术将此工序放置在最后的原因是,超声处理在前面可以提高金属表面的杂质去除,可以更快使得金属表面处于一种较为洁净的状态,且本技术采用了交变频率,可以进一步促使金属表面不同杂质可以得到更全面的冲洗作业。
17.所述s2具体为:烘干时采用120℃-135℃温度进行进行持续5min-6.5min的作业,进而将工件放入真空室中进行气压为3.0
×
10pa的负压真空作业。
18.需要说明的是,烘干温度120℃-135℃可以保证低温金属表面可以处于一种表面流体更快烘干的状态,因为本技术是针对250℃以下金属表面的温度进行,因此烘干温度的提升可以更好进行烘干,在快速烘干下,再进行负压真空处理,可以促使金属表面具有较高的离化率。
19.所述s3具体为:恒温静置处理时间为60min-75min。
20.需要说明的是,恒温静置处理时间区别现有技术的30min-40min的处理时间,可以最大程度保证恒温处理后,金属表面可以保证温度的稳定,保证金属表面分子的稳定性。
21.所述s4具体为:脉冲偏压的电压为700v,占空比为65%-75%,辉光清洗持续时间为10min-15min,其中氩气的通入为80sccm-120sccm。
22.需要说明的是,加入脉冲偏压后,进行辉光清洗,区别现有技术的直接清洗,可以最大程度提高250℃以下金属产品的表面质量,保证表面质量较高,这一点是本领域技术人员容易忽略的。
23.所述s5具体为:通入氩气为90sccm
‑‑
120sccm,开启离子源,继而电压设置为1000v-2000v,随即再次开启脉冲偏压调节偏压至100v-300v,占空比为50%-70%,离子刻蚀持续10min-12min。
24.需要说明的是,在通入氩气后进行离子源与脉冲偏压的加工,可以较大改进占空比,保证离子刻蚀持续时间10min-12min,可以有效提高刻蚀效果。
25.所述s6具体为:通入氩气量为100sccm后开启离子源,调节离子源电源电压为2000v-3000v,随即再次开启偏压,调节电压至200v-500v,占空比为50%-90%,继而开启氮气,调整氮气量为200sccm,氮化持续60min。
26.需要说明的是,经过离子源、脉冲偏压处理后,再次进行电压调节以及氮气量调节处理,可以最大程度保证250℃以下金属表面的活性以及离子率,缩短氮化处理时长。
27.所述s7具体为:关闭弧离子源,关闭气体源,关闭脉冲偏压,氮化过程结束,冷却至150℃后结束。
28.需要说明的是,针对金属表面温度为250℃以下的金属,需要进行冷却处理,区别于其余温度的金属处理,可以在不冷却下即可进行后续操作,同时申请人经过长时间研究发现,将温度冷却至150℃后,可以较高的保持处理活性。
29.本发明与现有技术相比,具有如下的优点和有益效果:
30.1.利用高压放电引出强大高能电子流增强离子氮化时氩氮辉光放电等离子体和含氮气体分子和原子而形成的离子,其有效提高了氮化效率,减少能源消耗和气体排放的
问题;
31.2.依靠高电压来产生等离子体,可以改变传统离子氮化炉的装夹方式,减少假负载的使用;
32.3.利用高压放电结合辉光处理,可以在氮化工艺开始之前对产品的表面进行刻蚀,可以去除钝化膜以及工件表面的微氧化层。
附图说明
33.图1是本发明的工艺步骤示意图。
具体实施方式
34.请参考说明附图1,本实施例提供了一种金属材料表面高压低温氮化工艺,该金属材料表面高压低温氮化工艺主要用于解决现有技术无法针对250℃以下的金属表面进行氮化处理的问题,该金属材料表面高压低温氮化工艺已经处于实际实验测试阶段,即将进行实际使用。
35.首先需要说明的是,本技术是针对金属工件表面为250℃以下进行,区别于现有技术针对300℃以上的温度进行的加工,具体作业原理为:在真空镀膜室内,工件施加负偏压,炉壁连接偏压电源正极并接地,炉内通入氩氮混合气,接通偏压电源,炉内产生辉光放电氩氮等离子体。利用氮化装置,引燃辉光放电,产生高压辉光放电等离子体,把高压放电强大的电子流引入到真空镀膜室中,让高能电子与氩氮辉光放电等离子体的粒子碰撞和能量交换,提高其离化率、粒子能量和等离子体浓度,即增强了原来氩氮辉光放电等离子体的性能水平,利用这种增强氩氮等离子体来进行离子氮化。
36.本发明的具体实施方式为:
37.实施例1
38.包括以下步骤:s1.预处理,将待加工金属工件表面进行抛光,随后加入到含有85%的酒精溶液中进行清洗,其中清洗过程采用超声清洗,得到清洗中间件;s2.负压真空,将中间件表面进行丙酮擦拭处理,随即进行加热烘干处理,烘干后,进行负压抽真空处理;s3.预热,将负压真空后的工件进行230℃的高温加热处理,加热处理后进行恒温静置;s4.ar离子清洗,恒温静置后,在金属工件表面通入氩气处理,通入气压为1pa,随即接入脉冲偏压,进行辉光清洗;s5.高压低温刻蚀,辉光清洗后加入再次加入氩气并同时开启离子源进行刻蚀,刻蚀持续时间10min;s6.氮化处理,再次进行刻蚀后,开启氮气持续氮化处理60min;s7.冷却,静置冷却,直至工件表面温度降至140℃以下,停止静置;s8.循环上述步骤。其中s1具体为:超声清洗持续时长为8min,其中超声清洗过程中采用交变频率波进行持续清洗,s2具体为:烘干时采用120℃温度进行进行持续5min的作业,进而将工件放入真空室中进行气压为3.0
×
10pa的负压真空作业,s3具体为:恒温静置处理时间为60min,s4具体为:脉冲偏压的电压为700v,占空比为65%,辉光清洗持续时间为10min,其中氩气的通入为80sccm,s5具体为:通入氩气为90sccm,开启离子源,继而电压设置为1000v,随即再次开启脉冲偏压调节偏压至100v,占空比为50%,离子刻蚀持续10min,s6具体为:通入氩气量为100sccm后开启离子源,调节离子源电源电压为2000v,随即再次开启偏压,调节电压至200v,占空比为50%,继而开启氮气,调整氮气量为200sccm,氮化持续60min,s7具体为:关
闭弧离子源,关闭气体源,关闭脉冲偏压,氮化过程结束,冷却至150℃后结束。
39.实施例2
40.本实施例仅记载与实施例1不同的部分,具体为:包括以下步骤:s1.预处理,将待加工金属工件表面进行抛光,随后加入到含有85%的酒精溶液中进行清洗,其中清洗过程采用超声清洗,得到清洗中间件;s2.负压真空,将中间件表面进行丙酮擦拭处理,随即进行加热烘干处理,烘干后,进行负压抽真空处理;s3.预热,将负压真空后的工件进行240℃的高温加热处理,加热处理后进行恒温静置;s4.ar离子清洗,恒温静置后,在金属工件表面通入氩气处理,通入气压为1.5pa,随即接入脉冲偏压,进行辉光清洗;s5.高压低温刻蚀,辉光清洗后加入再次加入氩气并同时开启离子源进行刻蚀,刻蚀持续时间13min;s6.氮化处理,再次进行刻蚀后,开启氮气持续氮化处理60min;s7.冷却,静置冷却,直至工件表面温度降至150℃以下,停止静置;s8.循环上述步骤。其中s1具体为:超声清洗持续时长为9min,其中超声清洗过程中采用交变频率波进行持续清洗,s2具体为:烘干时采用130℃温度进行进行持续6min的作业,进而将工件放入真空室中进行气压为3.0
×
10pa的负压真空作业,s3具体为:恒温静置处理时间为70min,s4具体为:脉冲偏压的电压为700v,占空比为70%,辉光清洗持续时间为13min,其中氩气的通入为100sccm,s5具体为:通入氩气为100sccm,开启离子源,继而电压设置为2000v,随即再次开启脉冲偏压调节偏压至200v,占空比为60%,离子刻蚀持续11min,s6具体为:通入氩气量为100sccm后开启离子源,调节离子源电源电压为3000v,随即再次开启偏压,调节电压至400v,占空比为70%,继而开启氮气,调整氮气量为200sccm,氮化持续60min,s7具体为:关闭弧离子源,关闭气体源,关闭脉冲偏压,氮化过程结束,冷却至150℃后结束。
41.实施例3
42.本实施例仅记载与实施例2不同的部分,具体为:包括以下步骤:s1.预处理,将待加工金属工件表面进行抛光,随后加入到含有85%的酒精溶液中进行清洗,其中清洗过程采用超声清洗,得到清洗中间件;s2.负压真空,将中间件表面进行丙酮擦拭处理,随即进行加热烘干处理,烘干后,进行负压抽真空处理;s3.预热,将负压真空后的工件进行250℃的高温加热处理,加热处理后进行恒温静置;s4.ar离子清洗,恒温静置后,在金属工件表面通入氩气处理,通入气压为1.5pa,随即接入脉冲偏压,进行辉光清洗;s5.高压低温刻蚀,辉光清洗后加入再次加入氩气并同时开启离子源进行刻蚀,刻蚀持续时间15min;s6.氮化处理,再次进行刻蚀后,开启氮气持续氮化处理60min;s7.冷却,静置冷却,直至工件表面温度降至160℃以下,停止静置;s8.循环上述步骤。其中s1具体为:超声清洗持续时长为10min,其中超声清洗过程中采用交变频率波进行持续清洗,s2具体为:烘干时采用135℃温度进行进行持续6.5min的作业,进而将工件放入真空室中进行气压为3.0
×
10pa的负压真空作业,s3具体为:恒温静置处理时间为75min,s4具体为:脉冲偏压的电压为700v,占空比为75%,辉光清洗持续时间为15min,其中氩气的通入为120sccm,s5具体为:通入氩气为120sccm,开启离子源,继而电压设置为2000v,随即再次开启脉冲偏压调节偏压至300v,占空比为70%,离子刻蚀持续12min,s6具体为:通入氩气量为100sccm后开启离子源,调节离子源电源电压为3000v,随即再次开启偏压,调节电压至500v,占空比为90%,继而开启氮气,调整氮气量为200sccm,氮化持续60min,s7具体为:关闭弧离子源,关闭气体源,关闭脉冲偏压,氮化过程结束,冷却至150℃后结束。
43.对比例1
44.将清洗过的零件放入氮化炉中,在350-400℃下预氧化1-2h,接着通入氨气和催渗剂,并排气、升温至520-650℃,然后持续通入氨气和催渗剂,在520-650℃下保温氮化12-18h,再冷却至室温即可;其中通入的氨气流量为1.4-2.0m3/h,通入的催渗剂流量为2-4ml/min;保温氮化时,氮化炉的压力为0.4-1.0kpa,氨气分解率为20-70%。
45.对比例2
46.对炉罐抽真空;充氮气,均匀加热至520-570℃;在氮气气氛下充氧气。
47.根据上述内容,申请人进行了实验,得到了如下数据:
[0048][0049]
根据上表数据,申请人认为本技术可以利用高压放电引出强大高能电子流增强离子氮化时氩氮辉光放电等离子体和含氮气体分子和原子而形成的离子,其有效提高了氮化效率,减少能源消耗和气体排放的问题。氮化速度较快,可缩短氮化周期,离子氮化时间短,能缩短到离子氮化时间1/4~1/2。可节约能源和氨的消耗量,电能消耗为离子氮化的1/5~1/3,氨气消耗为零,利用高压放电引出强大高能电子流增强离子氮化时氩辉光放电等离子体和含氮气体分子和原子而形成的离子,大大降低了偏压电源的工作电压(低于300v),减少了打火次数,提高了产品表面质量,利用高压放电引出强大高能电子流增强离子氮化时氩辉光放电等离子体和含氮气体分子和原子而形成的离子,依靠高电压来产生等离子体,可以改变传统离子氮化炉的装夹方式,减少假负载的使用,利用高压放电引出强大高能电子流增强离子氮化时氩辉光放电等离子体,可以在氮化工艺开始之前对产品的表面进行刻蚀,可以去除钝化膜,工件表面的微氧化层,同时处理温度范围较宽,即使在较低的温度下也能获得一定厚度的渗氮层,绿色环保,无公害,离子氮化处理在很低的压力下进行,排出的废气极少,选择气源为氮气、氩气,基本上无有害物质产生,可以适用于各种材料,包括要求氮化温度高的不锈钢、耐热钢,氮化温度较低的工模具(工具钢)和精密零件。
[0050]
对所公开的实施例的上述说明,使本领域专业技术人员能够实现或使用本发明。
对这些实施例的多种修改对本领域的专业技术人员来说将是显而易见的,本文中所定义的一般原理可以在不脱离本发明的精神或范围的情况下,在其它实施例中实现。因此,本发明将不会被限制于本文所示的这些实施例,而是要符合与本文所公开的原理和新颖特点相一致的最宽的范围。