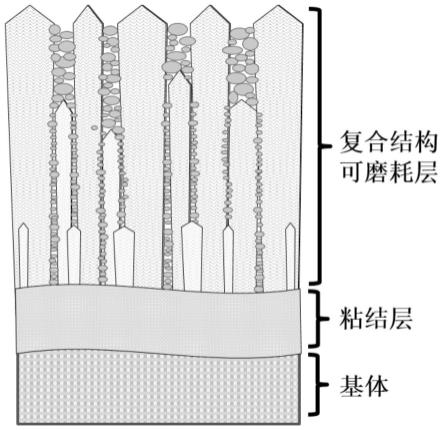
1.本发明属于封严涂层技术领域,涉及一种多相共沉积复合结构可磨耗封严涂层及其制备方法,更具体是指用等离子蒸发沉积技术快速制备一种可磨耗性好、抗热冲击性好、以柱状晶为骨架的复合结构可磨耗封严涂层陶瓷层。
技术背景
2.可磨耗封严涂层,一般是采用热喷涂技术在压气机机匣内表面喷涂耐高温、抗氧化、质软多孔,能够与压气机叶片尖端形成一对可磨耗封严摩擦副的涂层。在运行过程中形成理想的径向气流间隙,获得最大压差,从而提高发动机效率,降低能耗,简化气路密封结构设计,延长使用寿命,是航空发动机和燃气轮机涂层技术中的一种关键技术。
3.目前,制备可磨耗封严涂层的方法主要是等离子喷涂和火焰喷涂。等离子喷涂技术的优势在于喷涂效率高,成本低。然而,由于涂层一般为层片状结构,与基体间的结合方式为机械结合,喷涂后对涂层聚合物的热处理使得涂层疏松,因此,等离子喷涂制备的涂层抗热冲击能力差,使用寿命短。而火焰喷涂技术对粉末的加热能力低,一般用于制备中低温的、金属基的可磨耗封严涂层,无法制备高温和超高温陶瓷基可磨耗封严涂层。
技术实现要素:4.为了解决封严涂层抗热冲击和服役寿命等问题,本发明采用等离子蒸发沉积技术(ps-pvd),制备纯陶瓷材料的封严涂层,且具有柱状晶+颗粒的复合结构,实现可磨耗封严和提高抗热冲击性能的协同效果。本发明采用如下技术方案:
5.一种多相共沉积复合结构可磨耗封严涂层,包括在高温合金基体上依次沉积的金属粘结层和复合结构陶瓷层,其中所述复合结构陶瓷层是复合结构ysz陶瓷层或复合结构镧系锆酸盐陶瓷层,由作为骨架的柱状晶和填充在柱状晶间隙的颗粒构成,柱状晶骨架占比为50~80vol.%,颗粒占比10~40vol.%,孔隙率占比为1~10vol.%,三者比例相关联,协同调控。
6.进一步的,所述金属粘结层为三种材质的任一种:第一种为nicocraly,其组分包括40~60wt.%的ni,15~25wt.%的co,16~27wt.%的cr,5~10wt.%的al,0.05~2wt.%的y;第二种为nialx,x选择dy、hf或zr中的任一种,其组分包括40~60mol%的ni,38~60mol%的al,0.05~1.5mol%的x;第三种为nialpt,其组分包括40~60mol%的ni,34~46mol%的al,4~20mol%的pt。
7.进一步的,所述金属粘结层厚度为20~100μm,所述复合结构陶瓷层厚度为100~2000μm。
8.一种多相共沉积复合结构可磨耗封严涂层的制备方法,包括以下步骤:
9.第一步,高温合金基体预处理;
10.第二步,高温合金基体上制备金属粘结层,金属粘结层制备完毕后取出高温合金基体并对其进行真空热处理,温度1000~1100℃,时间为3~5h,真空度7~9
×
10-5
mbar,随
炉冷却至室温后取出;
11.第三步,采用等离子蒸发沉积在金属粘结层上制备复合结构陶瓷层,ysz粉末或镧系锆酸盐粉末经过等离子束流的加热后形成固、液、气三相,气相原子在固相颗粒上沉积并生长成柱状结构,同时伴随固相颗粒多次形核和液相的沉积,形成以柱状晶为骨架、颗粒填充柱状晶间隙的复合结构陶瓷层,柱状晶骨架占比为50~80vol.%,颗粒占比10~40vol.%,孔隙率占比为1~10vol.%。
12.进一步的,所述第二步,采用下述三种方式的任一种制备粘结层:采用真空等离子喷涂方法制备nicocraly金属粘结层;采用电子束物理气相沉积方法制备nialx金属粘结层,x选择dy、hf或zr中的任一种;采用电镀和包埋渗的方法制备nialpt金属粘结层。
13.进一步的,采用真空等离子喷涂方法制备nicocraly金属粘结层具体为:将第一步预处理后的高温合金基体安装在真空室的自动工件运动台上,调整主要工艺参数:喷涂功率为50~55kw,喷涂电流为1400~1550a,送粉率15~20g/min,喷涂距离550~600mm,主气流量ar 30~35slpm,he 55~60slpm,真空度70~75mbar;沉积2~3min,得到厚度20~100μm的粘结层。
14.进一步的,采用电子束物理气相沉积方法制备nialx金属粘结层具体为:使用电弧熔炼的方法配制靶材热处理后置于坩埚中,抽真空至3
×
10-3
pa;将第一步预处理后的高温合金基体预热至850~900℃,调节电子束电压为18~20kv,电子束电流为1.3~1.5a,高温合金基体旋转速率为10~15r/min,靶材的上升速率为0.3mm/min,沉积时间为40~50min,得到厚度80~100μm的粘结层。
15.进一步的,采用电镀和包埋渗的方法制备nialpt金属粘结层具体为:配置pt的电镀液,选取成分为:亚硝酸二氨铂(pt(nh3)2(no2)2)含量17g/l,硝酸铵(nh4no3)含量100g/l,亚硝酸钠(nano2)含量10g/l,氨水(nh3·
h2o)含量50g/l;加热镀液温度至80℃,将高温合金基体放入pt电镀液中,设置电流为0.8-1ma/mm2,电镀时间为55~60min,制备得到的电镀pt层的厚度为4~5μm;利用包埋渗方法渗铝,包埋渗的工艺参数为:保温温度950~1000℃,保温时间90~100min,最终制备得到厚度60~65μm的nialpt粘结层。
16.进一步的,所述第三步包含以下子步骤:
17.(1)将制备好粘结层的高温合金基体装入夹具中,固定到真空室内的自动工件转台上;
18.(2)关闭真空室,抽真空,直至真空室内的压力低于0.08mbar;
19.(3)打开工作气体阀门,向真空室内充入保护性气体氩气到130mbar;
20.(4)设定喷涂电流为1800a~2200a,引弧,待等离子电弧稳定后,抽真空至2mbar,逐步调整气体流量为ar 20~40slpm,he 50~70slpm;
21.(5)调整等离子枪与高温合金基体表面的距离为1000~1400mm,利用等离子射流加热高温合金基体到800~900℃,持续保温,并采用红外探头持续监测高温合金表面温度;
22.(6)将送粉器中的ysz粉末加热到60℃,打开送粉器,沉积ysz陶瓷层;工艺参数为:送粉率1~10g/min,送粉角度60~80
°
,送粉载气速率8~13l/min,喷涂功率60kw~100kw,喷涂距离为1000~1400mm,沉积时间为10min~30min;制得厚度为100~2000μm的ysz涂层;
23.若制备复合结构的镧系锆酸盐涂层,采用与上述制备ysz的相同工艺参数;
24.(7)逐步减小等离子气体流量、喷涂电流,向真空室内充入氩气至真空室气压超过
70mbar后,灭弧,待真空室冷却后,放气,打开真空室并取出高温合金基体。
25.本发明的优点在于:
26.1.采用本发明提供的制备方法,可以制备得到具有高孔隙率的,以柱状晶为骨架以及填充在柱状晶间隙颗粒的复合结构可磨耗封严涂层陶瓷层。
27.2.采用本发明提供的制备方法制备封严涂层沉积效率高,组织均匀。本发明采用等离子蒸发沉积技术,通过设置关键工艺参数(喷涂功率、喷涂距离、送粉速率等),控制基板温度、粉末在等离子焰流中的被加热程度等核心技术,实现在气相沉积(生成柱状晶骨架)同时,引入液相+固相(不同尺寸、形状的颗粒)沉积过程,使得涂层沉积效率达到50~100μm/min。相较等离子蒸发沉积技术制备气相沉积涂层的效率提高了2~5倍,并且保持了涂层良好的均匀性。
28.3.以柱状晶为骨架,柱间隙填充颗粒的复合结构可磨耗封严涂层,制备工艺流程简单,且疏松结构使涂层具有良好的可磨耗性能。常规等离子喷涂制备的可磨耗封严涂层,需要添加造孔剂(有机物成分),并在涂层制备后需要一个除造孔剂的热处理过程,用以获得疏松、可磨耗的涂层结构。本发明通过协调调控关键参数(例如:降低喷涂功率,或增大送粉速率,或增大喷涂距离等,降低气相沉积比例,提高液相/固相比例),获得不同柱状晶骨架与颗粒、间隙的比例,实现涂层强度与可磨耗功能的良好匹配。本发明的涂层制备流程不用引入造孔剂等有机物,也不需要关联的热处理工艺,简化了涂层工艺流程。
29.4.相比常见的采用等离子进行液相喷涂的多孔封严涂层,本发明的多相共沉积复合结构涂层,具有的柱状晶骨架能给涂层在高温下带来更高的应变容限,有效提高涂层的抗热冲击性能,使服役寿命长。
附图说明
30.图1是本发明制备的具有柱状晶+颗粒复合结构的可磨耗封严涂层(复合结构陶瓷层为ysz陶瓷层或镧系锆酸盐陶瓷层)的结构示意图;
31.图2是用等离子蒸发沉积系统制备的nicocraly金属粘结层+多相共沉积ysz陶瓷层的可磨耗封严涂层的电子背散射衍射图像;
32.图3是用等离子蒸发沉积系统制备的nialdy金属粘结层+多相共沉积gd2zr2o7陶瓷层的可磨耗封严涂层的电子背散射衍射图像;
33.图4是用等离子蒸发沉积系统制备的可磨耗封严涂层的gd2zr2o7陶瓷层电子背散射衍射图像。
具体实施方式
34.本发明提供一种多相共沉积复合结构可磨耗封严涂层的制备方法,包括以下步骤:
35.第一步,高温合金基体预处理。
36.准备高温合金基体打磨表面,分别经过120#、400#、600#、800#砂纸上打磨表面,放入丙酮中进行超声波清洗5min,然后进行喷砂预处理增加高温合金基体表面粗糙度(ra《1),备用。
37.第二步,高温合金基体上制备粘结层。
38.采用真空等离子喷涂方法制备nicocraly金属粘结层;采用电子束物理气相沉积方法制备nialx(x选择dy、hf或zr)金属粘结层;采用电镀和包埋渗的方法制备nialpt金属粘结层;
39.(a)采用真空等离子喷涂方法制备nicocraly金属粘结层;
40.将第一步预处理后的高温合金基体安装在真空室的自动工件运动台上,调整主要工艺参数:喷涂功率为50~55kw,喷涂电流为1400~1550a,送粉率15~20g/min,喷涂距离550~600mm,主气流量ar 30~35slpm,he 55~60slpm,真空度70~75mbar。沉积2~3min,得到厚度20~100μm的粘结层。
41.(b)采用电子束物理气相沉积方法制备nialx(x选择dy、hf或zr等)金属粘结层;
42.使用电弧熔炼的方法配制靶材热处理后置于坩埚中,抽真空至3
×
10-3
pa;将第一步预处理后的金属基体预热至850~900℃,调节电子束电压为18~20kv,电子束电流为1.3~1.5a,高温合金基体旋转速率为10~15r/min,靶材的上升速率为0.3mm/min,沉积时间为40~50min,得到厚度80~100μm的粘结层。
43.(c)采用电镀和包埋渗的方法制备nialpt金属粘结层;
44.配置pt的电镀液,选取成分为:亚硝酸二氨铂(pt(nh3)2(no2)2)含量17g/l,硝酸铵(nh4no3)含量100g/l,亚硝酸钠(nano2)含量10g/l,氨水(nh3·
h2o)含量50g/l。加热镀液温度至80℃,将高温合金基体放入pt电镀液中,设置电流为0.8-1ma/mm2,电镀时间为55~60min,制备得到的电镀pt层的厚度为4~5μm。利用包埋渗方法渗铝,包埋渗的工艺参数为:保温温度950~1000℃,保温时间90~100min,最终制备得到厚度60~65μm的nialpt粘结层。
45.金属粘结层制备完毕后取出高温合金基体并对其进行真空热处理,温度1000~1100℃,时间为3~5h,真空度7~9
×
10-5
mbar,随炉冷却至室温后取出。
46.第三步,在金属粘结层上制备复合结构的陶瓷层,具体步骤如下:
47.(1)将制备好粘结层的高温合金基体装入夹具中,固定到真空室内的自动工件转台上;
48.(2)关闭真空室,抽真空,直至真空室内的压力低于0.08mbar;
49.(3)打开工作气体阀门,向真空室内充入保护性气体氩气到130mbar;
50.(4)设定喷涂电流为1800a~2200a,引弧,待等离子电弧稳定后,逐步调整气体流量为ar 20~40slpm,he 50~70slpm;
51.(5)调整等离子枪与高温合金基体表面的距离为1000~1400mm,通过控制喷涂距离来获得不同微观结构的涂层,实现可磨耗与涂层长寿命的功能协同效果;利用等离子射流加热高温合金基体到800~900℃,持续保温,并采用红外探头对高温合金表面温度持续监测;
52.(6)将送粉器中的ysz粉末加热到60℃,打开送粉器,沉积ysz陶瓷层;工艺参数为:送粉率1~10g/min,送粉角度60~80
°
,送粉载气速率8~13l/min,喷涂功率60kw~100kw,喷涂距离为1000~1400mm,沉积时间为10min~30min;制得厚度为100~2000μm的ysz涂层。
53.若制备复合结构的镧系锆酸盐涂层,采用与上述制备ysz的相同工艺参数;
54.(7)逐步减小等离子气体流量、喷涂电流,向真空室内充入氩气至真空室气压超过70mbar后,灭弧,待真空室冷却后,放气,打开真空室并取出高温合金基体。
55.实施例1:
56.在高温合金基体表面真空等离子喷涂nicocraly金属粘结层+等离子蒸发沉积复合结构的陶瓷层ysz,具体步骤如下:
57.第一步,准备高温合金基体原片,尺寸为φ25
×
4mm,分别经过120#、400#、600#、800#砂纸上打磨表面,放入丙酮中进行超声波清洗5min,然后进行喷砂预处理增加高温合金基体表面粗糙度(ra《1),备用;
58.第二步,在高温合金基体上制备nicocraly金属粘结层。
59.采用真空等离子喷涂方法制备nicocraly金属粘结层,将第一步预处理后的高温合金基体安装在真空室的自动工件运动台上,调整主要工艺参数:喷涂功率为55kw,喷涂电流为1550a,送粉率20g/min,喷涂距离600mm,主气流量ar 35slpm,he 60slpm,真空度75mbar。沉积1min30s,得到厚度约为50μm的粘结层。
60.将制备好的nicocraly金属粘结层的高温合金基体从设备中取出后放入真空热处理炉中,设置热处理温度为1050℃,保温时间4h,真空度9
×
10-5
mbar,进行扩散处理,提高涂层与高温合金基体的结合力,随炉冷却至室温后取出。
61.第三步,在金属粘结层上制备准柱状结构的陶瓷层,具体如下:
62.(1)将制备好粘结层的高温合金基体装入夹具中,固定到真空室内的自动工件转动台上;
63.(2)关闭真空室,抽真空,直到真空室内的压力低于0.08mbar;
64.(3)打开工作气体阀门,向真空室中充入保护性气体ar至130mbar;
65.(4)设定喷涂电流1800a,引弧,待等离子电弧稳定后,抽真空至2mbar,逐步调整气体流量到指定气体流量,ar 30slpm,he 60slpm;
66.(5)调整喷枪与高温合金基体间的距离为1000mm,利用等离子射流加热高温合金基体到800℃,并用红外探头对高温合金基体温度进行监测;
67.(6)将送粉器中的ysz粉末加热到60℃,打开送粉器,调整送粉率3g/min,送粉角度60
°
,送粉载气速率8l/min,喷涂功率60kw,喷涂距离1000mm,开始沉积ysz陶瓷层,20min后得到厚度为150μm的复合结构ysz陶瓷层;
68.(7)逐步减小等离子气体流量、喷涂电流,再逐步减小真空度,向真空室内充入ar至真空室气压超过70mbar后,灭弧;待真空室冷却后,放气,打开真空室并取出高温合金基体。
69.对制备好的涂层微观结构和厚度进行了测试。通过扫描电镜发现,制备得到了具有复合结构ysz陶瓷层的可磨耗封严涂层,nicocraly粘结层厚度约为50μm,ysz陶瓷层厚度约为150μm。ysz陶瓷层为作为骨架的柱状晶和填充在柱状晶间隙颗粒的复合结构涂层,且柱状晶和颗粒之间存在一定孔隙,其示意图为图1。对不同位置的涂层形貌采集图像进行分析,获取平均值为:柱状晶骨架占比为75
±
5vol.%,颗粒占比为19
±
3vol.%,孔隙率为6
±
3vol.%。对涂层进行维氏硬度测试,测试条件为0.1kgf,维氏硬度为110
±
20hv0.1。在喷涂过程中,粉末经过等离子束流的加热后形成固、液、气三相,气相原子在固相颗粒上的沉积并生长成柱状结构,同时伴随有固相颗粒多次形核和液相的沉积,最后形成以柱状晶为骨架、颗粒填充柱状晶间隙的复合结构涂层。所述的可磨耗封严涂层的电子背散射衍射图像如图2所示。
70.实施例2:
71.在高温合金基体表面电子束物理气相沉积nialdy金属粘结层+等离子蒸发沉积的复合结构陶瓷层gd2zr2o7,具体步骤如下:
72.第一步,准备高温合金基体原片,尺寸为φ25
×
4mm,分别经过120#、400#、600#、800#砂纸上打磨表面,放入丙酮中进行超声波清洗5min,然后进行喷砂预处理增加高温合金基体表面粗糙度(ra《1),备用;
73.第二步,在高温合金基体上用电子束物理气相沉积方法制备nialdy粘结层,制备步骤如下:
74.(1)使用高纯镍(ni含量》99.99wt.%),高纯铝(al含量》99.999wt.%)及纯度99.7wt.%的镝(dy),按照设计成分配比,al含量为50at.%,dy含量为0.5at.%,余量为ni。对镍块、铝块表面进行打磨,除去表面的氧化膜,然后用无水酒精和丙酮进行超声波清洗10min,烘干后,对配制的合金使用电弧熔炼的方法,制备出φ70mm
×
100mm靶材;
75.(2)将上述靶材在真空热处理炉中进行1200℃均匀化热处理24h;
76.(3)将靶材放进电子束物理气相沉积设备的坩埚中,抽真空至3
×
10-3
pa,把高温合金基体整体预热至900℃,调节电子束电压为20kv,电子束电流为1.5a,高温合金基体旋转速率为15r/min,靶材的上升速率为0.3mm/min。沉积时间50min,得到厚度为90μm的粘结层;
77.(4)将制备好nialdy金属粘结层的高温合金基体从设备中取出后放入真空热处理炉中,进行扩散热处理,温度为1100℃,保温时间3h,真空度7
×
10-5
mbar,使粘结层的成分均匀,同时提高粘结层与高温合金基体的结合力,随炉冷却至室温后取出。
78.第三步,在nialdy金属粘结层上制备具有准柱状结构的gd2zr2o7陶瓷层,具体如下:
79.(1)将制备好粘结层的高温合金基体装入夹具中,固定到真空室内的自动工件转动台上;
80.(2)关闭真空室,抽真空,直到真空室内的压力低于0.08mbar;
81.(3)打开工作气体阀门,向真空室中充入保护性气体氩气(ar)到130mbar;
82.(4)设定喷涂电流2000a,引弧,待等离子电弧稳定后,抽真空至2mbar,逐步调整气体流量到指定气体流量,ar 30slpm,he 60slpm;
83.(5)调整喷枪与高温合金基体间的距离为1200mm,利用等离子射流加热高温合金基体到800℃,并用红外探头对高温合金基体温度进行监测;
84.(6)将送粉器中的gd2zr2o7粉末加热到60℃,打开送粉器,调整送粉率6g/min,送粉角度80
°
,送粉载气速率10l/min,喷涂功率65kw,将喷涂距离调至1200mm,开始沉积gd2zr2o7陶瓷层,20min后得到厚度为250μm的复合结构gd2zr2o7陶瓷层;
85.(7)逐步减小等离子气体流量、喷涂电流,再逐步减小真空度,向真空室内充入ar至真空室气压超过70mbar后,灭弧;待真空室冷却后放气并取出高温合金基体。
86.对制备好的涂层微观结构和厚度进行了测试。通过扫描电镜发现,制备得到了具有高孔隙率复合结构gd2zr2o7陶瓷层的可磨耗封严涂层,nialdy粘结层厚度约为90μm,gd2zr2o7陶瓷层厚度约为250μm。gd2zr2o7陶瓷层主要由作为骨架的柱状晶和填充在柱状晶间隙颗粒构成,且柱状晶和颗粒之间存在一定孔隙。涂层组织结构稳定,沉积效率高。对不同位置的涂层形貌采集图像进行分析,获取平均值为:柱状晶骨架占比为68
±
3vol.%,颗
粒占比为24
±
3vol.%,孔隙率为8
±
2vol%。对涂层进行维氏硬度测试,测试条件为0.1kgf,维氏硬度为85
±
25hv0.1。在喷涂过程中,粉末经过等离子束流的加热后形成固、液、气三相;除气相形核生成柱状晶之外,还包括未充分加热的陶瓷粉末颗粒和液滴共同沉积,形成了典型的复合结构涂层。所述的可磨耗封严涂层的电子背散射衍射图像如图3所示。
87.实施例3:
88.在高温合金基体表面电镀和包埋渗法制nialpt金属粘结层+等离子蒸发沉积的复合结构陶瓷层gd2zr2o7,具体步骤如下:
89.第一步,准备高温合金基体原片,尺寸为φ25
×
4mm,分别经过120#、400#、600#、800#砂纸上打磨表面,放入丙酮中进行超声波清洗5min,然后进行喷砂预处理增加高温合金基体表面粗糙度(ra《1),备用;
90.第二步,采用电镀和包埋渗的方法在高温合金基体上制备nialpt金属粘结层,nialpt金属粘结层的制备步骤如下:
91.(1)配置pt的电镀液,选取成分为:亚硝酸二氨铂(pt(nh3)2(no2)2)含量17g/l,硝酸铵(nh4no3)含量100g/l,亚硝酸钠(nano2)含量10g/l,氨水(nh3·
h2o)含量50g/l。加热镀液温度至80℃,将高温合金基体放入pt电镀液中,设置电流为1ma/mm2,电镀时间为1h,制备得到的电镀pt层的厚度为5μm。
92.(2)利用包埋渗方法渗铝,包埋渗的工艺参数为:保温温度1000℃,保温时间90min,最终制备得到厚度60μm的nialpt粘结层。将制备好的nialpt金属粘结层的高温合金基体从设备中取出后放入真空热处理炉中,设置热处理温度为1000℃,保温时间5h,真空度9
×
10-5
mbar,进行扩散处理,提高涂层与高温合金基体的结合力,随炉冷却至室温后取出。
93.第三步,在nialpt金属粘结层上制备具有准柱状结构的gd2zr2o7陶瓷层,具体如下:
94.(1)将制备好粘结层的高温合金基体装入夹具中,固定到真空室内的自动工件转动台上;
95.(2)关闭真空室,抽真空,直到真空室内的压力低于0.08mbar;
96.(3)打开工作气体阀门,向真空室中充入保护性气体氩气(ar)到130mbar;
97.(4)设定喷涂电流2000a,引弧,待等离子电弧稳定后,抽真空至2mbar,逐步调整气体流量到指定气体流量,ar 30slpm,he 60slpm;
98.(5)调整喷枪与高温合金基体间的距离为1300mm,利用等离子射流加热高温合金基体到800℃,并用红外探头对高温合金基体温度进行监测,;
99.(6)将送粉器中的gd2zr2o7粉末加热到60℃,打开送粉器,调整送粉率9g/min,送粉角度60
°
,送粉载气速率12l/min,喷涂功率60kw,将喷涂距离调至1300mm,开始沉积gd2zr2o7陶瓷层,10min后得到厚度约为250μm的复合结构的gd2zr2o7陶瓷层;
100.(7)逐步减小气体流量、喷涂电流,再逐步减小真空度,向真空室内充入ar至真空室气压超过70mbar后,灭弧;待真空室冷却后放气并取出高温合金基体。对制备好的涂层微观结构和厚度进行了测试。
101.通过扫描电镜发现,制备得到厚度约为250μm的gd2zr2o7陶瓷层;gd2zr2o7陶瓷层主要由作为骨架的柱状晶和填充在柱状晶间隙颗粒构成,且柱状晶和颗粒之间存在一定孔
隙。颗粒粒径范围较大,最大至20μm,由未被气化和液化的粉末沉积形成。对不同位置的涂层形貌采集图像进行分析,获取平均值为:柱状晶骨架占比为58
±
3vol.%,颗粒占比为39
±
3vol.%,孔隙率为3
±
1vol%。对涂层进行维氏硬度测试,测试条件为0.1kgf,维氏硬度为95
±
20hv0.1。所述的可磨耗封严涂层的电子背散射衍射图像如图4所示。
102.以上实施例仅用于说明本发明的设计思想和特点,其目的在于使本领域内的技术人员能够了解本发明的内容并据以实施,本发明的保护范围不限于上述实施例。所以,凡依据本发明所揭示的原理、设计思路所作的等同变化或修饰,均在本发明的保护范围之内。