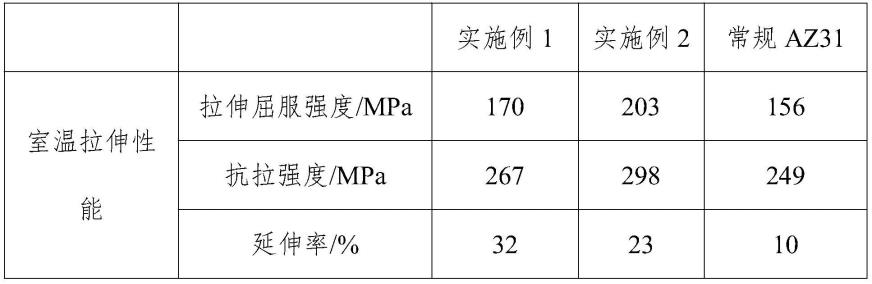
1.本发明涉及镁合金生产加工技术领域,具体涉及一种可冷成型镁合金锭坯及其加工方法。
背景技术:2.随着通信和数字技术的飞速发展,电子信息产品趋向于高性能、微型化、集成化发展,这对移动通讯装备材料的散热性能,比强度,轻质化提出了更高的要求。现在常用手机壳体材料为工程塑料(pc、ps、abs)、金属(不锈钢(304)、铝合金(6063))、复合材料(碳纤维+塑料)等。塑料外壳质量轻,但散热性能差,不耐热易老化;金属材料(不锈钢和铝合金)强度高,散热性能较好,但质量重,不便携。而镁合金由于密度低、比强度高,优良的热传导性(热传导系数是工程塑料的300倍以上),电磁屏蔽性佳等优点成为最具应用前景的壳体材料。
3.新能源汽车电机周围相关零件,由于采用铸造的方法难以达到强度要求,因此一般都采用冲压制备。这就要求使用材料具有高散热,轻量化,可冲压的性能,现在常用的是铝合金材料。与铝合金相比,镁合金具有散热性能更佳,质量更轻的优势,但镁合金由于其晶体结构特性,一般均通过热变形方式成型,这会导致生产成本的增加。
4.与铝、钢等材料相比,镁合金塑性变形能力有限,在室温下变形能力差,故一般采用热变形方法成型(一般要加热到200℃以上)。在此温度下,它比铝、钢的冲压性能还好。但镁合金板材在进行温冲压生产时,需要加热和保温设备,不仅增加了能耗,还可能存在加热不均匀、氧化的问题,这会导致材料在拉深过程中极易开裂,产品质量难以保证,降低了生产效率。因此如果实现镁合金室温成型,则打破了该技术领域的瓶颈,便于实现镁合金规模化生产和拓宽镁合金的应用。而目前现有镁合金的塑性变形能力还有待进一步提升,因此需要设计一款具有优异的塑性变形能力的镁合金。
技术实现要素:5.为此,本发明提供一种可冷成型镁合金锭坯及其加工方法,通过合金成分设计,然后进行铸锭均匀化处理、塑性变形处理能够获得组织均匀和性能优异、具备冷塑性变形能力的镁合金,以解决上述背景技术中提出的问题。
6.为了实现上述目的,本发明实施例提供如下技术方案:一种可冷成型镁合金锭坯,包括以下组成成分(按质量百分):zn1.0~6.0%、mn0.25~0.5%、ca0.10~0.35%、re0.15~2.5%,其余为mg和不可避免、总量少于0.15%的杂质,设计合金的简称为zxm镁合金。
7.进一步地,所述re包括sc、gd、la、ce或la+ce混合物中的一种,每种元素所占的质量百分数为sc0.0~1.5%、gd0.0~1.5%、la0.10~0.50%、ce0.10~0.35%或la+ce混合物0.20~0.5%,余量为镁。
8.进一步地,所述不可避免杂质总含量小于等于0.15%。
9.进一步地,根据不同的冷成型场景,zn的含量有所不同,其中对于强度要求低、塑性要求高的精密件复杂件,zn含量控制在1.0~3.0wt%;对于强度要求高、塑性要求低的形
状简单的零件,zn含量控制在4.0~6.0wt%。
10.本发明还包括一种可冷成型镁合金锭坯加工方法,包括以下具体步骤:
11.步骤一、称取配料:按照各组分比例称取原料,其中,mg与zn采用纯镁、纯锌锭形式添加,mn和ca采用镁锰中间合金、镁钙中间合金的形式添加,稀土元素采用与mg所形成的中间合金的形式添加;
12.步骤二、熔炼:先将原料放入烘箱中进行预热,然后在混合气体保护或溶剂保护下,先将预热后的纯mg在670℃~680℃保温全部融化后,再加入预热的、锌锭,熔化后保温10min;升温到700℃,加入镁锰中间合金和镁钙中间合金,熔化后保温10min;再加入纯稀土元素或稀土与mg的中间合金,升温至740℃熔化后保温10min;待原料完全熔解后,去掉表面浮渣,进行机械搅拌,然后保温静置30分钟,然后降温到700℃,倒入到钢模中浇铸成铸锭;
13.进一步地,预热温度为200~300℃,预热时间为3~4h,机械搅拌的时间为2~5min,转速为10~100rpm/min;
14.步骤三、均质化热处理:在工业氩气或氟化硫+干燥空气或工业氮气或工业二氧化碳气,比例为sf60.5~1.5%+干燥空气98.5~99.5%氛围保护下,将铸锭放置在电阻式带炉衬或筒加热炉中,并在炉温为340~490℃的条件下保温8~24h,然后随炉冷却至200℃后空冷至室温,并去除其表面氧化或污染层;
15.进一步地,采用车床或铣床去除铸锭表面的氧化层或污染层,其中车床针对的是圆形铸锭,铣床针对的是扁形铸锭,根据zn含量的不同所采用均质化热处理的方式也不一致:对于zn含量为0~3wt%的mg-zn合金,均匀化处理工艺为400~490℃,8~24h;对于zn含量为3~4wt%的mg-zn合金,均匀化处理为350~400℃,8~24h;对于zn含量为4~6wt%的mg-zn合金,均匀化处理为300~350℃,8~24h;
16.步骤四、热塑变形:在温度为270~390℃、挤压比为5~100、挤压速度为2.0~10.0m/min的条件下进行等温挤压;随后在电阻炉或具有还原性炉气的燃气炉中进行加热至150~300℃,保温15~60分钟、随炉冷却至200℃以下,出炉继续冷却至室温的热处理;
17.进一步地,热塑变形的方式还包括3d锻造、高压扭转、等径角挤压;
18.步骤五、冷塑成型:在室温下选取精密模锻、拉拔、挤压或冲压中的一种方式对其进行精密成型加工,成为机器零件;
19.进一步地,根据成型零件的形状要求选取不同的冷塑成型的方式:对于需要冷成型杯状或碗状零件,则采用挤压的方式,将材料挤压为板材形式,然后再通过冷冲压的方式成型;对于需要冷成型汽车发动机周围相关的壳体零件,则先采用挤压成板材的预先热塑性变形方式,然后再通过精密模锻的方式进行冷塑成型。
20.本发明解决如下行业困难:
21.1、本发明通过合金成分设计,然后对铸锭进行均匀化处理、塑性变形处理,在保证强度的基础上,有效提高镁合金的塑性,从而制备出可冷成型的镁合金锭坯,极大的降低了镁合金成型的成本,拓宽了镁合金在装备轻量化中的应用。
22.2、在本发明中,经过冷塑性成型后的材料仍然能保证其高强度和高性能,确保了其优异的服役性能。
具体实施方式
23.以下由特定的具体实施例说明本发明的实施方式,熟悉此技术的人士可由本说明书所揭露的内容轻易地了解本发明的其他优点及功效,显然,所描述的实施例是本发明一部分实施例,而不是全部的实施例。基于本发明中的实施例,本领域普通技术人员在没有做出创造性劳动前提下所获得的所有其他实施例,都属于本发明保护的范围。
24.实施例1
25.本发明提供的一种可冷成型镁合金锭坯,包括以下组成成分(按质量百分):zn1.0~6.0%(根据不同的冷成型场景,zn的含量有所不同,其中对于强度要求低、塑性要求高的精密件复杂件,zn含量控制在1.0~3.0wt%;对于强度要求高、塑性要求低的形状简单的零件,zn含量控制在4.0~6.0wt%)、mn0.25~0.5%、ca0.10~0.35%、re0.15~2.5%,其余为mg和不可避免、总量少于0.15%的杂质,所述re包括sc、gd、la、ce或la+ce混合物中的一种,每种元素所占的质量百分数为sc0.0~1.5%、gd0.0~1.5%、la0.10~0.50%、ce0.10~0.35%或la+ce混合物0.20~0.50%,余量为镁。
26.具体到本实施例中,zn3.0%、mn0.35%、ca0.1%、re0.15%,其余为mg和不可避免杂质,稀土元素选用sc,其质量百分数为0.15%。
27.加工方法包括以下具体步骤:
28.步骤一、称取配料:按照各组分比例称取原料,其中,mg与zn采用纯镁、纯锌锭形式添加,mn和ca采用镁锰中间合金、镁钙中间合金的形式添加,稀土元素采用与mg所形成的中间合金的形式添加;
29.步骤二、熔炼:先将原料放入烘箱中进行预热,然后在混合气体保护或溶剂保护下,先将预热后的纯mg在670℃保温全部融化后,再加入预热的锌锭,熔化后保温10min;升温到700℃,加入镁锰中间合金和镁钙中间合金,熔化后保温10min;再加入稀土元素与mg的中间合金,升温至740℃熔化后保温10min;待原料完全熔解后,去掉表面浮渣,进行机械搅拌,时间:2min,转速:30rpm/min,然后保温静置30分钟,然后降温到700℃,倒入到钢模中浇铸成铸锭;
30.步骤三、均质化热处理:在工业氩气+工业氮气的氛围保护下将铸锭放置在电阻式带炉衬加热炉中随炉升温至340℃保温2h,再升温至380℃保温6h,然后升温至400℃保温8h,最后随炉冷却至200℃后空冷至室温,并去除其表面氧化或污染层;
31.步骤四、热塑变形:390℃的挤压温度,100:1的挤压比,10m/min的挤压速度进行等温挤压;随后在电阻炉中进行加热至300℃,保温60分钟、随炉冷却至200℃以下,出炉继续冷却至室温的热处理,热塑变形的方式还包括3d锻造、高压扭转、等径角挤压;
32.步骤五、冷塑成型:在室温下选取精密模锻、拉拔、挤压或冲压中的一种方式对其进行成型处理,对于不同形状特征以及成型零件的形状要求选取不同的冷塑成型的方式:对于需要冷成型杯状或碗状零件,则挤压的预先热塑性变形方式,将材料挤压为板材形式,然后再通过冷冲压的方式成型;对于需要冷成型汽车发动机周围相关的壳体零件,则先通过挤压成板材的预先热塑性变形方式,然后再通过精密模锻的方式进行冷塑成型。
33.实施例2
34.本发明提供的一种可冷成型镁合金锭坯,包括以下组成成分(按质量百分):zn1.0~6.0%(根据不同的冷成型场景,zn的含量有所不同,其中对于强度要求低、塑性要求高的
精密件复杂件,zn含量控制在1.0~3.0wt%;对于强度要求高、塑性要求低的形状简单的零件,zn含量控制在4.0~6.0wt%)、mn0.35~0.5%、ca0.1~0.3%、re0.15~0.3%,其余为mg和不可避免杂质,杂质总含量小于等于0.15%,所述re包括sc、gd、la、ce或la+ce混合物中的一种,每种元素所占的质量百分数为sc0.0~1.5%、gd0.0~1.5%、la0.10~0.50%、ce0.10~0.35%,或la+ce混合物0.2~0.5%,余量为镁。
35.具体到本实施例中,包括以下组成成分(按质量百分):zn6.0%、mn0.5%、ca0.3%、re0.3%,其余为mg和不可避免杂质,稀土元素选用la,la的含量为0.3%。
36.加工方法包括以下具体步骤:
37.步骤一、称取配料:按照各组分比例称取原料,其中mg与zn采用纯镁、纯锌锭形式添加mn和ca采用镁锰中间合金、镁钙中间合金的形式添加,稀土元素采用与mg所形成的中间合金的形式添加;
38.步骤二、熔炼:先将原料放入烘箱中进行预热,然后在混合气体保护或溶剂保护下,先将预热后的纯mg680℃保温全部融化后,再加入预热的、锌锭,熔化后保温10min;升温到700℃,加入镁锰中间合金和镁钙中间合金,熔化后保温10min;再加入稀土元素与mg的中间合金,升温至740℃熔化后保温10min;待原料完全熔解后,去掉表面浮渣,进行机械搅拌,时间:5min,转速:40rpm/min,然后保温静置30分钟,然后降温到700℃,倒入到钢模中浇铸成铸锭;
39.步骤三、均质化热处理:在氟化硫+干燥空气,比例为sf60.5%+干燥空气99.5%氛围保护下将铸锭放置在电阻式带炉筒加热炉中随炉升温至250℃保温2h,再升温至300℃保温8h,最后随炉冷却至200℃后空冷至室温,并除去其表面的氧化和污染层;
40.步骤四、热塑变形:铸锭以270℃的挤压温度、5:1的挤压比、2.0m/min的挤压速度的条件下进行等温挤压;随后在电阻炉或具有还原性炉气的燃气炉中进行加热至150℃,保温30分钟,出炉继续冷却至室温的热处理,热塑变形的方式还包括3d锻造、高压扭转、等径角挤压;
41.步骤五、冷塑成型:在室温下选取精密模锻、拉拔、挤压或冲压中的一种方式对其进行成型处理;对于不同形状特征以及成型零件的形状要求选取不同的冷塑成型的方式:对于需要冷成型杯状或碗状零件,则挤压的预先热塑性变形方式,将材料挤压为板材形式,然后再通过冷冲压的方式成型;对于需要冷成型汽车发动机周围相关的壳体零件,则先通过挤压成板材的预先热塑性变形方式,然后再通过精密模锻的方式进行冷塑成型。
42.实施例3
43.将市面上az31镁合金与实施例1和实施例2中所制备的镁合金分别进行室温拉伸(试验应变速率为1
×
10-3
),具体结果如下表所示:
[0044][0045]
通过上表中的试验数据可以直接看出,根据实施例1和实施例2的方法所制作出来的镁合金的抗拉性能与延伸率均强于市面上的常规az31镁合金。专利cn102601207a提出一种镁合金冷态冲压方法,所述的板料型号为az31x,板料的厚度为3~6mm,所以本发明的镁合金坯锭能够应用于冷成型加工工艺。
[0046]
虽然,上文中已经用一般性说明及具体实施例对本发明作了详尽的描述,但在本发明基础上,可以对之作一些修改或改进,这对本领域技术人员而言是显而易见的。因此,在不偏离本发明精神的基础上所做的这些修改或改进,均属于本发明要求保护的范围。