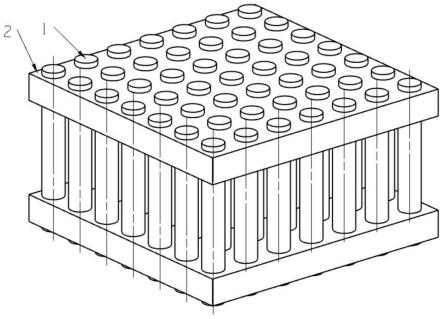
1.本发明属于多材料增材制造技术领域,更具体地,涉及一种基于粉末床熔融的原位金属陶瓷多材料制备方法。
背景技术:2.陶瓷材料具有耐高温、高强度、高硬度、耐磨损、耐腐蚀等优异性能,适用于航空航天、电力电子、能源交通等领域。但材料本身脆性大,难以加工形成大尺寸的形状复杂的零件。金属材料具有良好的导电性、延展性、导热性,在性能上与陶瓷具有互补的关系。金属和陶瓷材料的冶金结合,能够充分利用两种材料各自的优良性能,在同一组件中实现导电-介电、高延展-高强硬度等,满足复杂的构件需求。
3.然而由于陶瓷共价键与金属键存在差异、陶瓷界面润湿性差、二者热膨胀系数差异大带来过大的残余应力等问题,金属和陶瓷界面往往难以实现良好的冶金结合。传统手段如钎焊、固相扩散连接、熔化焊、摩擦焊、超声连接等,虽然一定程度上可以实现金属和陶瓷的结合,但只能加工棒状、板状、块状等简单形状的零件,对于复杂零件无法加工。增材制造技术是一种有效的多材料零件加工方式,可以实现复杂形状的多材料零件定制成形。对于现有的粉末床熔融增材制造技术,加工金属和陶瓷多材料存在一定的困难。成形过程容易造成粉末混合浪费,而且更换粉末操作繁杂,效率低下,只能成形沉积方向的多材料零件,难以实现水平面内的多材料构件。此外,由于金属和陶瓷性质差异较大,现有的粉末床熔融技术成形后的零件很容易开裂、分层,导致零件报废。
4.综上所述,现有的粉末床熔融技术缺乏一种能够高效实现金属陶瓷多材料零件的原位制备方法。
技术实现要素:5.针对现有技术的以上缺陷或改进需求,本发明提供了一种基于粉末床熔融的原位金属陶瓷多材料制备方法,其目的在于通过调整增材制造过程中的腔体气氛进行打印,由此解决目前更换粉末操作繁杂,效率低下,金属和陶瓷性质差异较大,成形后的零件很容易开裂、分层的技术问题。
6.为实现上述目的,按照本发明的一个方面,提供了一种基于粉末床熔融的原位金属陶瓷多材料制备方法。一种基于粉末床熔融的原位金属陶瓷多材料制备方法,所述方法包括:
7.(1)对零件的三维结构划分金属区与陶瓷区;
8.(2)沿着打印方向,判断待打印处是金属区还是陶瓷区,若是金属区,采用相对较低的激光能量密度,并在保护气氛下,采用增材制造技术根据三维结构打印零件的金属区;若是陶瓷区,采用相对较高的激光能量密度,并在含有氧气或氮气的气体氛围下,采用增材制造技术根据三维结构打印零件的陶瓷区;其中,激光能量密度e=p/vht,式中p为激光功率,v为扫描速度,h为填充间距(本发明中为常数),t为层厚(本发明中为常数),本发明中陶
瓷区的h值与金属区的h值是相同的,陶瓷区的t值与金属区的t值是相同的。
9.(3)重复步骤(2),直至完成零件的打印;其中,金属区与陶瓷区采用成分相同的金属合金粉末作为原料进行打印。
10.优选地,所述相对较低的激光能量密度通过激光功率为50w-150w,扫描速度为800mm/s-1400mm/s实现。
11.优选地,所述相对较高的激光能量密度通过激光功率为200w-400w,扫描速度为300mm/s-700mm/s实现。
12.优选地,所述含有氧气或氮气的气体氛围为,在保护气氛中含有氧气或氮气,并使氮气或者氧气的体积占比为10%-30%。
13.优选地,所述金属合金粉末为能够与氧或氮元素形成陶瓷相的合金粉末,优选地,所述金属合金粉末为铝合金、钛合金或镁合金。
14.优选地,所述金属合金粉末的平均粒径为20-60μm,球形率为99.9%。
15.优选地,在步骤(2)之前还包括:将基板喷砂处理,然后在基板上预铺一层金属合金粉末,该层金属合金粉末厚度为30-60μm。
16.优选地,所述步骤(2)中,在保护气氛下,采用增材制造技术根据三维结构打印零件的金属区,具体为在氩气保护下,并使得氧气含量低于40ppm。
17.按照本发明的另一个方面,提供了一种原位金属陶瓷多材料。
18.总体而言,通过本发明所构思的以上技术方案与现有技术相比,至少能够取得下列有益效果。
19.(1)本发明通过改变成形腔室内的气体氛围,通入或不通入氮气/氧气,结合高激光能量密度和低激光能量密度,实现了使用同一种金属粉末的情况下,原位形成金属陶瓷多材料零件。相比传统粉末床熔融,避免了多材料成形过程中粉末更换的繁杂操作,而且无需改进设备成形系统,降低了成本。解决了只能成形沉积方向的多材料零件,难以实现水平面内的多材料构件的问题。
20.本发明实现使用同一种金属粉末的情况下,原位形成金属陶瓷多材料零件原理为:在激光能量密度相对较低时(例如激光功率为50w-150w,扫描速度为800mm/s-1400mm/s时),能够在熔化金属粉末的同时不被腔室内的氧气氧化或氮气氮化,这是由于熔池存在时间较短,在液态金属被氧化或者氮化之前已经冷却为固态,此时成形的零件为金属合金。在激光能量密度相对较高时(例如激光功率为200w-400w,扫描速度为300mm/s-700mm/s),熔化的金属粉末很容易被腔室内的氧气氧化或氮气氮化,形成氧化物陶瓷或氮化物陶瓷,这是由于熔池存在时间较长,处于高温态的液态金属被氧化或者氮化,形成氧化物或氮化物陶瓷相。
21.(2)本发明中由于原位形成的金属和陶瓷根本上来源于同一种粉末,在通过激光工艺来分别调整金属和陶瓷的形成时,界面处会形成一定的过渡区,因为高激光功率密度参数在扫描时会部分重熔之前成形的区域,如形成铝合金到氧化铝的过渡区域,相比现有的粉末床熔融成形,避免了界面急剧变化,界面结合效果更好。
22.(3)本发明只需根据设计的三维模型,并配合本发明提供的激光工艺参数,便可以设计生产任意定制的金属陶瓷多材料零件。可以方便实现如导电-介电,高延展-高硬度等特殊的组合性能。
附图说明
23.图1为本发明实施例1中镁合金和氧化镁陶瓷多材料构件示意图;
24.图2为本发明实施例2中钛合金和氮化钛陶瓷多材料构件示意图;
25.图3为本发明实施例3中铝合金和氧化铝陶瓷多材料构件示意图。
26.附图标记为:1、金属区,2、陶瓷区。
具体实施方式
27.为了使本发明的目的、技术方案及优点更加清楚明白,以下结合附图及实施例,对本发明进行进一步详细说明。应当理解,此处所描述的具体实施例仅仅用以解释本发明,并不用于限定本发明。此外,下面所描述的本发明各个实施方式中所涉及到的技术特征只要彼此之间未构成冲突就可以相互组合。
28.实施例1
29.本实施例提供一种基于粉末床熔融的原位金属陶瓷多材料制备方法,包括以下步骤:
30.(1)利用三维建模软件对所要成形的金属陶瓷多材料零件建模设计,导出为stl格式,输入到粉末床熔融系统中。
31.其中,零件三维模型如图1所示,金属区1与陶瓷区2整体属于同一个零件。
32.(2)多材料打印使用的粉末为金属合金粉末,然后将基板喷砂处理,然后在基板上预铺一层金属合金粉末。该金属合金粉末为镁合金粉末,其平均粒径为40μm,球形率99.9%。所述一层金属合金粉末厚度为50μm。
33.(3)沿着打印方向,判断待打印处是金属区还是陶瓷区,若是金属区,采用相对较低的激光能量密度,并在保护气氛下,采用增材制造技术根据三维结构打印零件的金属区;若是陶瓷区,采用相对较高的激光能量密度,并在含有氧气或氮气的气体氛围下,采用增材制造技术根据三维结构打印零件的陶瓷区。
34.打印气体氛围的控制具体为:关闭成形腔室舱门,通过进气口控制腔室内气体氛围。保护气氛为:打开保护气进气阀、泄压阀,通入氩气排除腔室内的氧气,其氧气含量低于40ppm。含有氧气或氮气的气体氛围为:打开第二进气阀,控制氧气或氮气的相对流量,使腔室内的氧气或氮气比例处于预设范围内。待腔室内的气体比例复合加工要求后,采用优化的成形工艺成形金属陶瓷多材料零件。
35.本实施例中,金属区成形工艺激光功率为50w,扫描速度为800mm/s,激光能量密度较低,且保护气体为氩气,其氧气含量低于40ppm;陶瓷区成形工艺激光功率为200w,扫描速度为300mm/s,激光能量密度较高,且腔室内的氧气比例处于10%-20%,该比例指体积占比。
36.(4)重复步骤(3),直至完成打印。
37.(5)零件加工完成后,通过线切割将零件与基板分离。
38.实施例2
39.本实施例提供一种基于粉末床熔融的原位金属陶瓷多材料制备方法,包括以下步骤:
40.(1)利用三维建模软件对所要成形的金属陶瓷多材料零件建模设计,导出为stl格
式,输入到粉末床熔融系统中。
41.其中,零件三维模型如图1所示,金属区1与陶瓷区2整体属于同一个零件。
42.(2)多材料打印使用的粉末为金属合金粉末,然后将基板喷砂处理,然后在基板上预铺一层金属合金粉末。该金属合金粉末为金属合金粉末为钛合金粉末,其平均粒径为53μm,球形率99.9%。所述一层金属合金粉末厚度为50μm。
43.(3)沿着打印方向,判断待打印处是金属区还是陶瓷区,若是金属区,采用相对较低的激光能量密度,并在保护气氛下,采用增材制造技术根据三维结构打印零件的金属区;若是陶瓷区,采用相对较高的激光能量密度,并在含有氧气或氮气的气体氛围下,采用增材制造技术根据三维结构打印零件的陶瓷区。
44.打印气体氛围的控制具体为:关闭成形腔室舱门,通过进气口控制腔室内气体氛围。保护气氛为:打开保护气进气阀、泄压阀,通入氩气排除腔室内的氧气,其氧气含量低于40ppm。含有氧气或氮气的气体氛围为:打开第二进气阀,控制氧气或氮气的相对流量,使腔室内的氧气或氮气比例处于预设范围内。待腔室内的气体比例复合加工要求后,采用优化的成形工艺成形金属陶瓷多材料零件。
45.本实施例中,金属区成形工艺激光功率为150w,扫描速度为900mm/s,激光能量密度较低,且保护气体为氩气,其氧气含量低于40ppm;陶瓷区成形工艺激光功率为300w,扫描速度为500mm/s,激光能量密度较高,且腔室内的氮气比例处于20%-30%,该比例指体积占比。
46.(4)重复步骤(3),直至完成打印。
47.(5)零件加工完成后,通过线切割将零件与基板分离。
48.请参阅图2所示,本实施例制备得到的零件,包括内部的钛合金成型件及其外围与之连接的氮化镁陶瓷件,基于内部钛合金的强度和韧性,结合外围氮化镁陶瓷的高耐磨、高熔点,形成外硬里韧的组合性能。
49.实施例3
50.本实施例提供一种基于粉末床熔融的原位金属陶瓷多材料制备方法,包括以下步骤:
51.(1)利用三维建模软件对所要成形的金属陶瓷多材料零件建模设计,导出为stl格式,输入到粉末床熔融系统中。
52.其中,零件三维模型如图1所示,金属区1与陶瓷区2整体属于同一个零件。
53.(2)多材料打印使用的粉末为金属合金粉末,然后将基板喷砂处理,然后在基板上预铺一层金属合金粉末。金属合金粉末为铝合金粉末,其平均粒径为30μm,球形率99.9%。所述一层金属合金粉末厚度为30μm。
54.(3)沿着打印方向,判断待打印处是金属区还是陶瓷区,若是金属区,采用相对较低的激光能量密度,并在保护气氛下,采用增材制造技术根据三维结构打印零件的金属区;若是陶瓷区,采用相对较高的激光能量密度,并在含有氧气或氮气的气体氛围下,采用增材制造技术根据三维结构打印零件的陶瓷区。
55.打印气体氛围的控制具体为:关闭成形腔室舱门,通过进气口控制腔室内气体氛围。保护气氛为:打开保护气进气阀、泄压阀,通入氩气排除腔室内的氧气,其氧气含量低于40ppm。含有氧气或氮气的气体氛围为:打开第二进气阀,控制氧气或氮气的相对流量,使腔
室内的氧气或氮气比例处于预设范围内。待腔室内的气体比例复合加工要求后,采用优化的成形工艺成形金属陶瓷多材料零件。
56.本实施例中,金属区成形工艺激光功率为100w,扫描速度为1000mm/s,激光能量密度较低,且保护气体为氩气,其氧气含量低于40ppm;陶瓷区成形工艺激光功率为250w,扫描速度为600mm/s,激光能量密度较高,且腔室内的氧气比例处于10%-30%,该比例指体积占比。
57.(4)重复步骤(3),直至完成打印。
58.(5)零件加工完成后,通过线切割将零件与基板分离。
59.请参阅图3所示,本实施例制备得到的零件,包括阵列的柱状铝合金成型件及其两边与之连接的氧化铝陶瓷件,基于铝合金的导电性,结合两边氧化铝陶瓷的介电性,形成多个导电-介电的组合性能。
60.本领域的技术人员容易理解,以上所述仅为本发明的较佳实施例而已,并不用以限制本发明,凡在本发明的精神和原则之内所作的任何修改、等同替换和改进等,均应包含在本发明的保护范围之内。