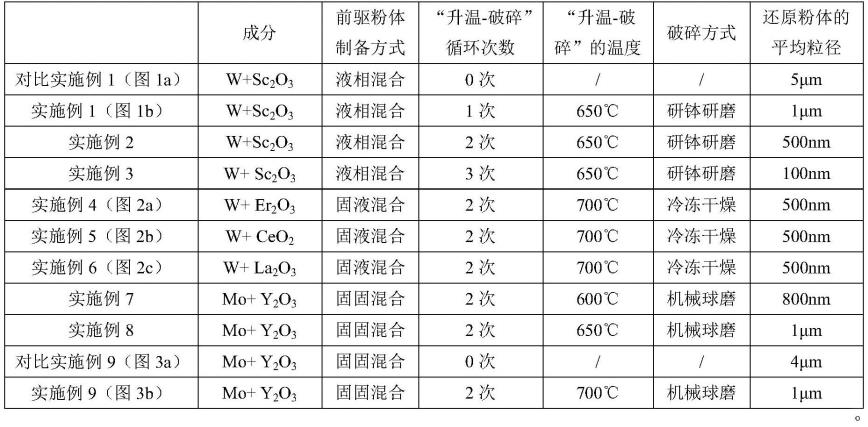
1.本发明提出了一种基于对稀土氧化物复合难熔金属粉体还原过程中的中间产物进行一次或多次循环破碎,实现难熔金属粉体细化程度控制的方法。该方法操作简便,可流程化作业,能够实现大规模工业化应用。方法主要适用于获得用于粉末冶金的细颗粒粉体。
技术背景
2.难熔金属材料是非常重要的金属材料,难熔金属及其合金材料在能源冶金、电子信息产业、航空航天和国防军工等领域的作用是其他材料不可替代的。而难熔金属及其合金粉末对制备难熔金属材料的性能影响很大,且很多时候甚至都制约着难熔金属材料的发展,所以制备出高性能的难熔金属及其合金粉末对制备高性能难熔金属材料至关重要。
3.提高难熔金属及其合金性能的有效途径是减少粒径的尺寸。研究表明,通过添加稀土元素可以显著地改善粉体粒径尺寸从而提高合金的综合性能。制备超细稀土复合难熔金属粉体的方法主要为球磨法和化学法。球磨法得到的粉末会引入大量杂质,且随着球磨时间延长,细化晶粒的效果越不显著,并且团聚非常严重。目前得到超细稀土复合难熔金属粉体的方法主要为化学法,包括湿化学沉淀法、溶胶凝胶法、喷雾干燥法、冷冻干燥法等。这些方法都是细化了前驱体粉末,并且可以达到原子级别的均匀性掺杂。然而,相关科研人员往往只重视了细化前驱体粉末,而忽视了对后续还原工艺的改进。传统的难熔金属例如钨粉常采用两段式还原法,即一次升温到中间温度后保温一段时间,继续升温到终段温度后保温。采用传统的两段式还原大多情况下只能制备微米、亚微米粉体,粉体颗粒生长不均匀且稀土氧化物在粉体中分散程度不佳,导致出现部分团聚的现象。
技术实现要素:4.本发明主要发明内容为在稀土氧化物复合难熔金属粉体还原过程中,将未彻底还原的中间产物采用研钵研磨、机械球磨、冷冻干燥等破碎方法进行颗粒细化,之后再对粉体进行还原,同时根据需要通过调整中间产物的成分、破碎程度以及破碎-再还原循环次数结合还原工艺的优化,制备了具有均匀的细小颗粒的难熔金属粉体。
5.本发明提供了一种基于中途循环破碎控制稀土复合难熔金属粉体细化程度的方法,包括以下步骤:
6.步骤(1),对原料进行混合,制备前驱体制备;采用液相混合、固液混合或者固固混合的方式制备氧化钨/钼中与稀土氧化物前驱体;其中,液相混合的原料为偏钨酸铵/钼酸铵、稀土硝酸盐,固液混合的原料为偏钨酸铵/钼酸铵、稀土氧化物,固固混合的原料为氧化钨/钼、稀土氧化物;原料以液相混合、固液混合、固固混合的方式分别对应制备成凝胶、浆液以及粉体;
7.步骤(2),对前驱体进行预处理获得待还原粉体;其中采用液相混合制备的凝胶以及固液混合制备的浆液先置于干燥箱中进行加热烘干后再放入空气气氛的马弗炉中进行
分解煅烧,保证粉体中对应的c、n等元素完全排除;固固混合和固液混合的粉体进行机械球磨,保证稀土氧化物在粉体中分散均匀。
8.步骤(3),对步骤(2)待还原粉体进行第一步氢气还原,氢气还原温度通常为300-700℃之间;同时通过控制氢气流量或流速等工艺条件,初步排出粉体中的部分氧含量,使得钨或钼未完全还原,最终得到未完全还原的钨的氧化物或未完全还原的钼的氧化物,未完全还原的钨的氧化物以wo
2.9
、wo
2.72
、wo2以及β-w单相或者多相混合的中间产物;未完全还原的钼的氧化物以moo
2.8
、moo
2.75
、moo2单相或者多相混合的中间产物;
9.步骤(4),对步骤(3)经过第一次还原得到的中间粉体进行粉碎和细化颗粒处理,采用方法可以但不限于机械研磨、粉碎、冷冻干燥。
10.步骤(5),根据工艺需求对粉体进行再次还原,其,对粉体进行步骤(3)(4)的还原-粉碎的多次循环操作,然后将粉体置于700℃以上氢气氛围中还原制备获得以难熔金属单质钨或钼和稀土氧化物为主要物相的混合粉体。
11.上述发明步骤(2)中,稀土氧化物的比例为总质量的0.01%-10%。
12.上述发明步骤(3)中,第一次氢气还原温度为300-700℃。
13.上述发明步骤(3)中,第一次还原的中间产物主要为wo3到w还原过程中依旧富含o元素的wo
2.72
、wo
2.9
、wo2、β-w或moo3到mo还原过程中依旧富含o元素的moo
2.8
、moo
2.75
、moo2,同时粉体中含有稀土元素和难熔金属元素形成的复合氧化物或者单纯的稀土氧化物。
14.上述发明步骤(4)中,破碎方式为研钵研磨、机械球磨或冷冻干燥。
15.上述发明步骤(5)中,根据制备需求循环步骤(3)至步骤(4)2-3次后再进行高温还原,通过控制循环次数达到控制细化程度的方法,其中高温还原温度为700-1500℃。
16.多次中途破碎再还原获得的粉体较一次连续升温还原获得粉体粒径更加均匀且颗粒粒径更加细小。
附图说明
17.图1中a是实施例1制备的前驱粉体经过一次连续升温至900℃的sem,平均粒径尺寸约为5μm;b是实施例1制备的复合钨粉体的sem,平均粒径尺寸约为1μm。经过图1中的对比可见,与一次连续升温还原获得的粉体相比,经过一次中途研磨破碎再还原获得的粉体粒径更加均匀且颗粒粒径更加细小。
18.图2中a是实施例4制备的复合钨粉体的sem,平均粒径尺寸约为0.5μm;b是实施例5制备的复合钨粉体的sem,平均粒径尺寸约为0.5μm;c是实施例6制备的复合钨粉体的sem,平均粒径尺寸约为0.5μm。经过图2中的结果可见,稀土氧化物复合难熔金属粉体通过冷冻干燥破碎再还原的循环能够有效地细化晶粒。
19.图3中a是实施例9制备的前驱粉体经过一次连续升温至900℃的sem,平均粒径尺寸约为4μm;b是实施例9制备的复合钨粉体的sem,平均粒径尺寸约为1μm。经过图3中的对比可见,与一次连续升温还原获得的粉体相比,经过中途机械球磨破碎再还原获得的粉体粒径更加均匀且颗粒粒径更加细小。
20.表1是不同成分、不同前驱粉体制备方式、不同“升温-破碎”循环次数、不同“升温-破碎”温度以及不同破碎方式制备的粉体的平均粒径汇总表。
具体实施方式
21.下面结合实施例对本发明做进一步说明,但本发明并不限于以下实施例。
22.实施例1
23.实施例1:分别将102.6g的偏钨酸铵、13.33g的硝酸钪以及92.744g的柠檬酸分别溶入去离子水中形成溶液。将三份溶液混合,使用磁力搅拌器在温度为90℃的恒温条件下持续搅拌得到黄色湿凝胶。将湿凝胶置于100℃的烘箱烘干。将烘干后的凝胶放入马弗炉中分解,马弗炉中氧化分解温度为650℃,分解保温时间为5小时,待冷却后取出可得到黄色粉末状的前驱粉体。将得到的前驱粉体在氢气气氛中还原;第一次氢气还原温度为650℃;随后待粉体降至室温状态后将其从管式炉中取出,利用玛瑙研钵进行充分研磨;随后进行最后一次氢气还原,还原温度为900℃。
24.实施例2
25.实施例2:分别将102.6g的偏钨酸铵、13.33g的硝酸钪以及92.744g的柠檬酸分别溶入去离子水中形成溶液。将三份溶液混合,使用磁力搅拌器在温度为90℃的恒温条件下持续搅拌得到黄色湿凝胶。将湿凝胶置于100℃的烘箱烘干。将烘干后的凝胶放入马弗炉中分解,马弗炉中氧化分解温度为650℃,分解保温时间为5小时,待冷却后取出可得到黄色粉末状的前驱粉体。将得到的前驱粉体在氢气气氛中还原;第一次氢气还原温度为650℃;随后待粉体降至室温状态后将其从管式炉中取出,利用玛瑙研钵进行充分研磨破碎;随后再次循环上述650℃还原-研磨破碎的操作;进行最后一次氢气还原,还原温度为900℃。
26.实施例3
27.实施例3:分别将102.6g的偏钨酸铵、13.33g的硝酸钪以及92.744g的柠檬酸分别溶入去离子水中形成溶液。将三份溶液混合,使用磁力搅拌器在温度为90℃的恒温条件下持续搅拌得到黄色湿凝胶。将湿凝胶置于100℃的烘箱烘干。将烘干后的凝胶放入马弗炉中分解,马弗炉中氧化分解温度为650℃,分解保温时间为5小时,待冷却后取出可得到黄色粉末状的前驱粉体。将得到的前驱粉体在氢气气氛中还原;第一次氢气还原温度为650℃;随后待粉体降至室温状态后将其从管式炉中取出,利用玛瑙研钵进行充分研磨破碎;随后循环两次上述650℃还原-研磨破碎的操作;进行最后一次氢气还原,还原温度为900℃。
28.实施例4
29.实施例4:将102.6g的偏钨酸铵溶入去离子水中形成溶液,加入4g的氧化铒和适量的无水乙醇,充分搅拌成浆液。随后烘干、分解得到前驱粉体的过程与实施例1所述一致。将得到的前驱粉体在氢气气氛中还原;第一次氢气还原温度为700℃;随后待粉体降至室温状态后将其从管式炉中取出,利用冷冻干燥进行破碎,冷冻温度为-60℃~-30℃,冷冻干燥12h;随后再次循环上述700℃还原-冷冻干燥破碎的操作;随后进行最后一次氢气还原,还原温度为900℃。
30.实施例5
31.实施例5:将102.6g的偏钨酸铵溶入去离子水中形成溶液,加入4g的氧化铈和适量的无水乙醇,充分搅拌成浆液。随后烘干、分解得到前驱粉体的过程与实施例1所述一致。将得到的前驱粉体在氢气气氛中还原;第一次氢气还原温度为700℃;随后待粉体降至室温状态后将其从管式炉中取出,利用冷冻干燥进行破碎,冷冻温度为-60℃~-30℃,冷冻干燥12h;随后再次循环上述700℃还原-冷冻干燥破碎的操作;随后进行最后一次氢气还原,还
原温度为900℃。
32.实施例6
33.实施例6:将102.6g的偏钨酸铵溶入去离子水中形成溶液,加入4g的氧化镧和适量的无水乙醇,充分搅拌成浆液。随后烘干、分解得到前驱粉体的过程与实施例1所述一致。将得到的前驱粉体在氢气气氛中还原;第一次氢气还原温度为700℃;随后待粉体降至室温状态后将其从管式炉中取出,利用冷冻干燥进行破碎,冷冻温度为-60℃~-30℃,冷冻干燥12h;随后再次循环上述700℃还原-冷冻干燥破碎的操作;随后进行最后一次氢气还原,还原温度为900℃。
34.实施例7
35.实施例7::分别将96g的氧化钼、4g的氧化钇以及球料比为1:1的钢球放入球磨罐中进行球磨,球磨时间为12h。将球磨后的粉体进行适当研磨后在氢气气氛中还原;第一次氢气还原温度为650℃;随后待粉体降至室温状态后将其从管式炉中取出,利用球磨机进行球磨破碎,球磨时间为6h;随后再次循环上述650℃还原-机械球磨破碎的操作随后进行最后一次氢气还原,还原温度为900℃。
36.实施例8
37.实施例8::分别将96g的氧化钼、4g的氧化钇以及球料比为1:1的钢球放入球磨罐中进行球磨,球磨时间为12h。将球磨后的粉体进行适当研磨后在氢气气氛中还原;第一次氢气还原温度为700℃;随后待粉体降至室温状态后将其从管式炉中取出,利用球磨机进行球磨破碎,球磨时间为6h;随后再次循环上述700℃还原-机械球磨破碎的操作随后进行最后一次氢气还原,还原温度为900℃。
38.实施例9
39.实施例9::分别将96g的氧化钼、4g的氧化钇以及球料比为1:1的钢球放入球磨罐中进行球磨,球磨时间为12h。将球磨后的粉体进行适当研磨后在氢气气氛中还原;第一次氢气还原温度为750℃;随后待粉体降至室温状态后将其从管式炉中取出,利用球磨机进行球磨破碎,球磨时间为6h;随后再次循环上述750℃还原-机械球磨破碎的操作随后进行最后一次氢气还原,还原温度为900℃。表1