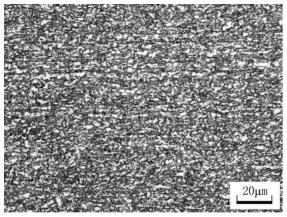
980mpa级热轧dh钢板及其使用薄板坯生产的方法
技术领域
1.本发明涉及热轧高强钢技术领域,具体涉及一种980mpa级热轧dh钢板及其使用薄板坯生产的方法。
背景技术:2.随着汽车行业排放法规的日益严苛、车身安全性需求的提高和轻金属材料的挑战,车用钢铁材料得到了快速发展,汽车结构件用钢强塑性得到显著提高。以qp钢、中锰钢、轻质钢为代表的第三代超高强钢的开发,为车身提供了更加丰富的材料选择,先进高强钢未来一段时间仍然是实现车身轻量化、高安全、低成本的最佳选择。较于第一代先进高强钢,第三代先进高强钢虽然具有更优的力学性能,但也增加了制造难度和成本,特别是成分设计中mn、si、al等合金元素使用的增加,使其在制造端会出现边裂、厚差等问题。因此,开发兼具低成本、易制造、高性能的汽车用先进高强钢意义重大。
3.经初步检索,专利申请号为cn201610451301.5的文献,提供了一种980mpa级热轧双相钢及其制造方法,其屈服强度≥500mpa,抗拉强度≥980mpa,延伸率a80在12%左右,表现出优异的强度、塑性和韧性匹配,同时具有较低的屈强比,可应用于车轮等需要良好成形性能和高强减薄的部位。
4.专利号为cn200610098392.5的文献公开了一种薄板坯连铸连轧生产热轧双相钢的工艺,包括转炉冶炼工序,lf炉精炼工序,薄板坯连铸工序,与现有技术相比:生产的热轧双相钢,具有强度高、成形性能好、耐磨损等优点,可提高汽车结构件加工成材率,并可提高其使用寿命。
5.上述专利介绍了980mpa级热轧双相钢的生产方法以及用薄板坯连铸连轧工艺生产热轧双相钢的工艺,但是目前生产的双相钢延伸率较低,一般延伸率a80在12%左右,难以满足汽车用钢更高塑性的要求。
技术实现要素:6.本发明的目的就是针对上述技术的不足,提供一种980mpa级热轧dh钢板及其使用薄板坯生产的方法,热轧钢板的抗拉强度≥980mpa、延伸率≥15%,晶粒尺寸细小,晶粒度≥10级,具有优异的强度、塑性和韧性匹配。
7.为实现上述目的,本发明所设计的980mpa级热轧dh钢板,其化学成分的质量百分比为:c:0.175~0.213%,si:1.65~1.83%,mn:1.85~2.03%,p≤0.015%,s≤0.002%,其余为fe和不可避免的杂质。
8.本发明中主要组分及工艺的作用及控制的理由:
9.c:c是廉价的固溶强化元素,是影响屈服强度和抗拉强度的主要因素之一,同时,碳元素对材料的焊接性能也有重要影响。一般而言,钢中的碳元素含量越高,屈服强度和抗拉强度也随之提高,而焊接性能则随之降低。本发明为了保证钢板获得抗拉强度在980mpa级别的钢板,碳含量至少要达到0.17%以上,否则板材的抗拉强度难以满足要求。另一方
面,如果碳含量过高并超过0.22%,将会对板材的焊接性能造成影响,从而降低材料的使用价值。因此综合考虑碳元素对强度和焊接性能的影响,钢中的碳含量应当控制在0.175~0.213%,优选0.198~0.202%。
10.si和mn:si和mn是本发明采用的重要合金元素,传统高强钢通过添加贵重金属元素如cr、mo等提高固溶强化效果或则nb、ti等提高析出强化效果,本发明采用低成本的si和mn元素添加,因为si和mn是奥氏体形成元素,添加一定量的si和mn使得在室温状态下仍能保留一部分的残余奥氏体,这一部分的残余奥氏体在室温变形过程中产生trip效应,大大提高塑性。但是si和mn含量都不能过高,si含量过高,降低钢板表面质量,如果mn含量过高,那么将会显著增加板坯开裂的风险,因此si为1.65~1.83%,优选1.808~1.812%,mn为1.85~2.03%,优选1.983~2.015%
11.s:s是钢中的杂质元素,如果硫含量过高,将会增加钢材的热脆倾向。钢中的s常以锰的硫化物形态存在,这种硫化物夹杂对钢的冲击韧性是十分不利的,并造成性能的各向异性,因此,需将钢中硫含量控制得越低越好。因此,将钢中硫含量控制在0.002%以下,优选p≤0.0099%。
12.p:p是钢中的杂质元素,如果p含量过高,将会在钢坯凝固时析出fe2p共晶组织并导致冷脆现象。因此p元素的含量越低越好,实际生产时一般控制在0.015%以下,优选s≤0.0013%。
13.除了对以上化学成分的范围作了限定以外,从提高材料成形性、经济性的观点出发,本发明未添加cu、cr、ni、mo、nb、ti等贵重合金元素。
14.一种所述980mpa级热轧dh钢板使用薄板坯生产的方法,包括如下步骤:
15.a)冶炼:按所述成分及质量百分比混合均匀进行冶炼取得铁水;
16.b)精炼;
17.c)连铸:精炼结束后进行连铸取得铸坯,中包钢水过热度为15~30℃,铸坯厚度为52~55mm,拉坯速度为3.5~5.0m/min,本发明中,过热度为15~30℃,过热度过低会导致大包钢水凝固造成钢水无法浇铸,因此过热度不能太低,本发明过热度是针对薄板坯连铸连轧流程和本发明的dh钢专门设计,采用低过热度浇铸dh钢可以优化常规浇铸的一些缺点,比如能减少甚至消除马氏体钢的缩孔、疏松、粘沙和气孔现象,此外,低的过热度可以有效的降低铸坯的中心偏析,有利于提高组织均匀性;
18.d)加热:对铸坯进行加热;
19.e)除鳞:对铸坯进行高压水除鳞;
20.f)轧制:控制第一道次压下率为52~63%,第二道次压下率为50~60%,确保轧制过程中通过大变形使得奥氏体完全再结晶,形成细小的原奥氏体晶粒,末道次压下率为10~16%,轧制速度为8~12m/s,并在第一道次及第二道次之间进行中压水除鳞,除鳞水压力为200~280bar,终轧温度为860~900℃,确保轧制过程都是在奥氏体区轧制,实现奥氏体轧制过程中完全再结晶;
21.g)层流冷却:冷却方式为三段式冷却,第一段冷却速度为50~75℃/s,冷却至中间温度t,t=终轧温度-200[c]-25[mn]-18[si],目的是快速冷却至铁素体转变温度形成15~20%的铁素体组织,由于c、si、mn都是奥氏体稳定元素,因此中间温度随其含量而变化,c、si、mn含量越高时,需要冷却至更低的铁素体转变温度才能获得所需的铁素体组织,第二段
为空冷,冷速为5~15℃/s,冷却时间3~5s,此阶段主要为铁素体转变阶段,因为铁素体转变速度并没有马氏体转变速度那么快,因此需要3~5s转变时间,时间过短铁素体量不足,时间过长,铁素体量过多;第三段冷却速度100~200℃/s,冷却至300~350℃卷取,主要是为了快速冷却形成马氏体组织;
[0022]
h)卷取。
[0023]
优选地,所述步骤a)中,对冶炼后的铁水进行脱硫,脱硫目标:s≤0.002%,扒渣后铁水裸露面≥95%。
[0024]
优选地,所述步骤d)中,铸坯入炉温度为800~950℃,在炉时间≥20min,出炉温度为1160~1200℃,能够保证轧钢过程中钢板的温度满足各环节的要求,从氧化动力学和热力学原理上来看,加热温度过高和保温时间过长,会导致轧制前的原始奥氏体晶粒粗大,这会造成后续的轧制过程无法完成奥氏体完全再结晶过程,使最终产品发生混晶(即产品晶粒大小不均匀),严重影响产品质量,但是如果加热温度过低和保温时间过短,会导致轧制前初始奥氏体晶粒过小,后续轧制过程变形抗力过大超过轧钢设备极限能力,而无法完整个轧制过程,此外,加热温度过高和保温时间过长,还会增加产品表面脱碳,导致产品质量下降,直接影响产品的关键性能。
[0025]
优选地,所述步骤e)中,除鳞水压力为280~420bar。
[0026]
优选地,所述步骤e)中,卷取温度为300~350℃,卷取过程中马氏体中的c、si、mn元素向奥氏体中聚集并增加其热稳定性,最终钢卷冷却至室温时获得5~15%的残余奥氏体,卷取温度过高,则不能形成完全的马氏体组织,钢板抗拉强度不能满足需求,卷取温度过低,难以通过c、si、mn元素的富集形成残余奥氏体。
[0027]
本发明与现有技术相比,具有以下优点:采用合理的化学成分以及热轧工艺,获得晶粒尺寸细小的铁素体+马氏体组织,并且含有一定量的残余奥氏体组织,其中铁素体比例15~20%,马氏体比例60~80%,残余奥氏体比例5~15%,热轧钢板抗拉强度≥980mpa、延伸率≥15%,晶粒度≥10级,完全能满足汽车高强度安全件使用要求。
附图说明
[0028]
图1为本发明实施例1热轧dh钢板金相组织图(马氏体+铁素体+残余奥氏体)。
具体实施方式
[0029]
下面结合附图和具体实施例对本发明作进一步的详细说明。
[0030]
表1为本发明各实施例和对比例的化学成分列表;
[0031]
表2为本发明各实施例和对比例的主要工艺参数列表一;
[0032]
表3为本发明各实施例和对比例的主要工艺参数列表二;
[0033]
表4为本发明各实施例和对比例力学性能检测结果列表。
[0034]
本发明各实施例和对比例按照以下步骤生产:
[0035]
a)冶炼:按所述成分及质量百分比混合均匀进行冶炼取得铁水,对冶炼后的铁水进行脱硫,脱硫目标:s≤0.002%,扒渣后铁水裸露面≥95%;
[0036]
b)精炼;
[0037]
c)连铸:精炼结束后进行连铸取得铸坯,中包钢水过热度为15~30℃,铸坯厚度为
52~55mm,拉坯速度为3.5~5.0m/min;
[0038]
d)加热:对铸坯进行加热,铸坯入炉温度为800~950℃,在炉时间≥20min,出炉温度为1160~1200℃;
[0039]
e)除鳞:对铸坯进行高压水除鳞,除鳞水压力为280~420bar;
[0040]
f)轧制:控制第一道次压下率为52~63%,第二道次压下率为50~60%,末道次压下率为10~16%,轧制速度为8~12m/s,并在第一道次及第二道次之间进行中压水除鳞,除鳞水压力为200~280bar,终轧温度为860~900℃;
[0041]
g)层流冷却:冷却方式为三段式冷却,第一段冷却速度为50~75℃/s,冷却至中间温度t,t=终轧温度-200[c]-25[mn]-18[si],第二段为空冷,冷却速度为5~15℃/s,冷却时间3~5s,第三段冷却速度为100~200℃/s,冷却至300~350℃卷取;
[0042]
h)卷取,卷取温度为300~350℃。
[0043]
表1本发明各实施例和对比例的化学成分列表
[0044][0045]
表2本发明各实施例和对比例的主要工艺参数列表一
[0046]
[0047][0048]
表3本发明各实施例和对比例的主要工艺参数列表二
[0049][0050]
表4本发明各实施例和对比例力学性能检测结果列表
[0051][0052]
结合表4和图1可以很明显看出,采用本发明的化学成分以及热轧工艺,通过轧后三段式冷却,获得晶粒尺寸细小的铁素体+马氏体组织,并且含有一定量的残余奥氏体组织,其中铁素体比例15~20%,马氏体比例60~80%,残余奥氏体比例5~15%。热轧钢板抗拉强度≥980mpa、延伸率≥15%,晶粒度≥10级。
[0053]
相对地,对于未控制化学成分和热轧工艺参数的对比例1~3与实施例1~5相比,抗拉强度和延伸率无法满足要求。