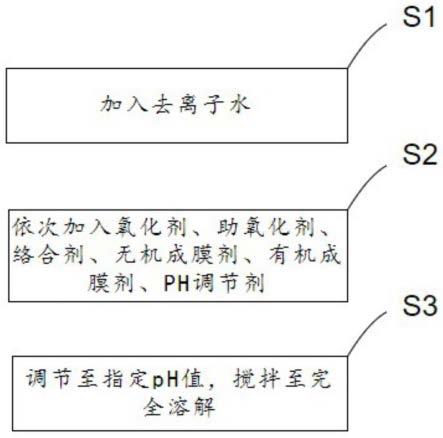
一种水基7系铝合金浸泡缓蚀剂及其制备方法
【技术领域】
1.一种水基7系铝合金浸泡缓蚀剂及其制备方法,特别涉及一种用于7系铝合金在cnc、抛光或者阳极氧化等表面处理过程中水基浸泡缓蚀剂及其制备方法。
背景技术:2.随着3c产品的高速发展,5、6系铝合金的强度要求已经满足不了材料性能及市场的需求。7系铝合金因为具有外观靓丽、质量轻、强度高性能优异,并且对人体皮肤不会产生过敏等特性成为许多3c产品青睐的材料。
3.7系铝合金强度高,但7系铝合金锌含量比6系铝合金高因此其耐蚀性较差,以7075铝合金为例:锌含量为 5.1~6.1(m%),zn和al存在电势差,在潮湿环境或者电解质存在的情况下会发生电子转移,加速7系铝合金腐蚀;使得7系铝合金在加工过程中难度加大。防止7系铝合金加工过程中等待或者运输时造成的腐蚀,是保证7系铝合金顺利加工的前提。
4.目前针对于铝合金的防护,应用最普遍的防腐技术有阳极氧化、涂料和缓蚀剂。缓蚀剂的作用机制是形成一层将金属表面与腐蚀介质相隔开的缓释保护膜。根据这层缓释膜的形成特点分为三种:1.氧化性缓释膜:通过其氧化性在金属表面形成一层纳米级别氧化膜;2.沉淀模型氧化膜:在溶液离子的作用下形成难溶物,因而沉在金属表层成为缓释膜;3.吸附膜型缓释膜:含有极性基团的有机物,被金属离子的电荷吸附形成较薄的憎水膜,进而减少腐蚀。可是,存在钝化不均、成膜性不好可造成加工过程中对基材的腐蚀,从而导致缺陷,从而影响粗糙度、光泽度。
技术实现要素:5.针对上述问题,本发明提供了一种水基7系铝合金缓释浸泡液,具备可溶、寿命长、酸碱度中性等优点:浸泡液中各种成分协同作用,对7系铝合金各金属优质的选择比,使工件在附带切削液或者抛光液等电解质的情况下浸泡使用,表面光泽好,无腐蚀斑点。浸泡液各种成分全部溶于水,不含重金属,不含磷。浓度降低时添加浸泡液即可,更加环保、经济、方便。并且,废液处理比较简单。
6.一种水基7系铝合金浸泡缓蚀剂及其制备方法,特别是提供一种可溶、寿命长、酸碱度中性的铝合金缓蚀剂,包括如下步骤:
7.s1:取去离子水20-100份;
8.s2:依次加入4-20份氧化剂、助氧化剂、络合剂、无机成膜剂剂、有机成膜剂、ph调节剂;
9.s3:调节ph值至6.5-7.5,搅拌至完全溶解,得到水基7系铝合金浸泡缓蚀剂;
10.优选地,包括如下重量份的组分制得:氧化剂1-5 份、助氧化剂1-5份、络合剂0.1-1份、无机成膜剂1-4 份、有机成膜剂1-4份、ph调节剂0.01-0.1份、去离子水20-100份;
11.优选地,所述氧化剂选自硝酸钠、过硫酸钾、过硫酸钠、过碳酸钠的一种或多种;
12.优选地,所述助氧化剂选自2.2.6.6-四甲基哌啶氧化物、4.甲基吗啉-n-氧化物的
一种或多种;
13.优选地,所述络合剂,选自乙二胺四乙酸、乙二胺四乙酸二钠、乙二胺四乙酸四钠、柠檬酸、酒石酸、氨基乙酸的一种或多种;
14.优选地,所述无机成膜剂选自六偏磷酸钠、三聚磷酸钠、焦磷酸钠、四硼酸钠、硅酸钠、硫酸钠的一种或多种;
15.优选地,所述有机成膜剂选自γ-氨丙基三乙氧基硅烷、γ-缩水甘油醚氧丙基三甲氧基硅烷、三乙醇胺、苯甲酸钠、苯并三氮唑的一种或多种;
16.优选地,所述ph调节剂选自碳酸钠、碳酸氢钠、碳酸钾、碳酸氢钾的一种或多种;
17.优选地,调节ph值至6.5-7.5。
18.相对于现有技术,本发明具有如下优点:
19.1、配方所有成份均为可溶性物质,各组份分配合理。缓蚀效果好、应用条件广泛,在7系铝合金cnc、抛光等加工过程中浸泡使用能有效防止残留加工液对基材的腐蚀,缓蚀时间可高达24h;缓蚀剂不会影响基材粗糙度、光泽等外观和性能。此生产方法制备工艺简单、成本低,适合批量生产。
20.2、本发明产品稳定性好寿命长,放置一年仍能保持原有效果。
21.3、本发明产品具有优良的缓蚀性能,浸泡后产品表面光泽、粗糙度无改变,不会造成黑点腐蚀,浸泡后清洗简单。使用方便,浓度降低只需加入适量浸泡液即可,适合自动化程度比较高的生产模式,节省人力、无需特别维护。不会对工人身体健康造成危害。
【附图说明】
22.图1是本发明一种水基7系铝合金缓释浸泡液的流程示意图;
【具体实施方式】
23.为了使本发明的目的、技术方案及优点更加清楚明白,以下结合附图及实施实例,对本发明进行进一步详细说明。应当理解,此处所描述的具体实施例仅用于解释本发明,并不用于限定本发明。根据本发明实施例的缓蚀剂的生产方法没有特别限制;
24.请参阅图1,本发明提供了一种水基7系铝合金浸泡缓蚀剂及其制备方法,包括如下步骤:
25.针对上述问题,本发明提供了一种水基7系铝合金缓释浸泡液:浸泡液中各种成分协同作用,对7系铝合金各金属优质的选择比,使工件在附带切削液或者抛光液等电解质的情况下浸泡使用,表面光泽好,无腐蚀斑点。浸泡液各种成分全部溶于水,不含重金属,不含磷,对身体健康无危害。浓度降低时添加浸泡液即可,更加环保、经济、方便。废液处理比较简单。
26.一种水基7系铝合金浸泡缓蚀剂及其制备方法,特别是提供一种可溶、寿命长、酸碱度中性的铝合金缓蚀剂,包括如下步骤:
27.s1:取去离子水20-100份;
28.s2:依次加入4-20份氧化剂、助氧化剂、络合剂、无机成膜剂剂、有机成膜剂、ph调节剂;
29.s3:调节ph值至6.5-7.5,搅拌至完全溶解,得到水基7系铝合金浸泡缓蚀剂;
30.在本发明的步骤s1和s2中,包括如下重量份的组分制得:氧化剂1-5份、助氧化剂1-5份、络合剂0.1-1 份、无机成膜剂1-4份、有机成膜剂1-4份、ph调节剂 0.01-0.1份、去离子水20-100份;
31.在本发明的步骤s2中,所述氧化剂选自硝酸钠、过硫酸钾、过硫酸钠、过碳酸钠的一种或多种;
32.在本发明的步骤s2中,所述助氧化剂选自2.2.6.6
‑ꢀ
四甲基哌啶氧化物、4.甲基吗啉-n-氧化物的一种或多种;
33.在本发明的步骤s2中,所述络合剂,选自乙二胺四乙酸、乙二胺四乙酸二钠、乙二胺四乙酸四钠、柠檬酸、酒石酸、氨基乙酸的一种或多种;
34.在本发明的步骤s2中,所述无机成膜剂选自六偏磷酸钠、三聚磷酸钠、焦磷酸钠、四硼酸钠、硅酸钠、硫酸钠的一种或多种;
35.在本发明的步骤s2中,所述有机成膜剂选自γ-氨丙基三乙氧基硅烷、γ-缩水甘油醚氧丙基三甲氧基硅烷、三乙醇胺、苯甲酸钠、苯并三氮唑的一种或多种;
36.在本发明的步骤s2中,所述ph调节剂选自碳酸钠、碳酸氢钠、碳酸钾、碳酸氢钾的一种或多种;
37.在本发明的步骤s3中,调节ph值至中性液6.5-7.5。
38.实施例1:
39.本实施例缓释液的配方为:
40.质量组分:硝酸钠1份,2.2.6.6-四甲基哌啶氧化物 1份,乙二胺四乙酸二钠1份,三聚磷酸钠1份,γ-氨丙基三乙氧基硅烷1份,碳酸氢钠0.1份;
41.本实施例缓释液的制备方法如下:
42.先用量筒量取93.4份的纯水,将称量好的硝酸钠、γ-氨丙基三乙氧基硅烷混合一起,充分搅拌10min,并依序将称量好的硝酸钠、乙二胺四乙酸二钠、三聚磷酸钠、碳酸氢钠投入,并不停地搅拌,搅拌至溶液完全分散,时间大致需要20-60min。
43.实施例2:
44.本实施例缓释液的配方为:
45.质量组分:过硫酸钠1份,2.2.6.6-四甲基哌啶氧化物1份,乙二胺四乙酸二钠1份,三聚磷酸钠1份,γ
‑ꢀ
氨丙基三乙氧基硅烷1份,碳酸氢钠0.1份;
46.本实施例缓释液的制备方法如下:
47.先用量筒量取93.4份的纯水,将称量好的硝酸钠、γ-氨丙基三乙氧基硅烷混合一起,充分搅拌10min,并依序将称量好的过硫酸钠、乙二胺四乙酸二钠、三聚磷酸钠、碳酸氢钠投入,并不停地搅拌,搅拌至溶液完全分散,时间大致需要20-60min。
48.实施例3:
49.本实施例缓释液的配方为:
50.质量组分:过碳酸钠1份,2.2.6.6-四甲基哌啶氧化物1份,乙二胺四乙酸二钠1份,三聚磷酸钠1份,γ
‑ꢀ
氨丙基三乙氧基硅烷1份,碳酸氢钠0.1份;
51.本实施例缓释液的制备方法如下:
52.先用量筒量取93.4份的纯水,将称量好的硝酸钠、γ-氨丙基三乙氧基硅烷混合一起,充分搅拌10min,并依序将称量好的过碳酸钠、乙二胺四乙酸二钠、三聚磷酸钠、碳酸氢
钠投入,并不停地搅拌,搅拌至溶液完全分散,时间大致需要20-60min。
53.实施例4:
54.本实施例缓释液的配方为:
55.质量组分:硝酸钠2份,2.2.6.6-四甲基哌啶氧化物 2份,乙二胺四乙酸二钠2份,三聚磷酸钠2份,γ-氨丙基三乙氧基硅烷2份,碳酸氢钠0.2份;
56.本实施例缓释液的制备方法如下:
57.先用量筒量取88.8份的纯水,将称量好的硝酸钠、γ-氨丙基三乙氧基硅烷混合一起,充分搅拌10min,并依序将称量好的硝酸钠、乙二胺四乙酸二钠、三聚磷酸钠、碳酸氢钠投入,并不停地搅拌,搅拌至溶液完全分散,时间大致需要20-60min。
58.实施例5:
59.本实施例缓释液的配方为:
60.质量组分:硝酸钠2份,2.2.6.6-四甲基哌啶氧化物 2份,酒石酸2份,三聚磷酸钠2份,γ-氨丙基三乙氧基硅烷2份,碳酸氢钠0.2份;
61.本实施例缓释液的制备方法如下:
62.先用量筒量取88.8份的纯水,将称量好的硝酸钠、γ-氨丙基三乙氧基硅烷混合一起,充分搅拌10min,并依序将称量好的硝酸钠、酒石酸、三聚磷酸钠、碳酸氢钠投入,并不停地搅拌,搅拌至溶液完全分散,时间大致需要20-60min。
63.实施例6:
64.本实施例缓释液的配方为:
65.质量组分:硝酸钠2份,2.2.6.6-四甲基哌啶氧化物 2份,氨基乙酸2份,三聚磷酸钠2份,γ-氨丙基三乙氧基硅烷2份,碳酸氢钠0.2份;
66.本实施例缓释液的制备方法如下:
67.先用量筒量取88.8份的纯水,将称量好的硝酸钠、γ-氨丙基三乙氧基硅烷混合一起,充分搅拌10min,并依序将称量好的硝酸钠、氨基乙酸、三聚磷酸钠、碳酸氢钠投入,并不停地搅拌,搅拌至溶液完全分散,时间大致需要20-60min。
68.实施例7:
69.本实施例缓释液的配方为:
70.质量组分:硝酸钠2份,4.甲基吗啉-n-氧化物1 份,乙二胺四乙酸二钠2份,三聚磷酸钠0.2份,γ-氨丙基三乙氧基硅烷2份,碳酸氢钠0.2份;
71.本实施例缓释液的制备方法如下:
72.先用量筒量取91.6份的纯水,将称量好的硝酸钠、γ-氨丙基三乙氧基硅烷混合一起,充分搅拌10min,并依序将称量好的硝酸钠、乙二胺四乙酸二钠、三聚磷酸钠、碳酸氢钠投入,并不停地搅拌,搅拌至溶液完全分散,时间大致需要20-60min。
73.实施例8:
74.本实施例缓释液的配方为:
75.质量组分:硝酸钠2份,4.甲基吗啉-n-氧化物1 份,乙二胺四乙酸二钠2份,三聚磷酸钠0.2份,三乙醇胺2份,碳酸氢钠0.2份;
76.本实施例缓释液的制备方法如下:
77.先用量筒量取91.6份的纯水,将称量好的硝酸钠、三乙醇胺混合一起,充分搅拌
10min,并依序将称量好的硝酸钠、乙二胺四乙酸二钠、三聚磷酸钠、碳酸氢钠投入,并不停地搅拌,搅拌至溶液完全分散,时间大致需要20-60min。
78.实施例9:
79.本实施例缓释液的配方为:
80.质量组分:硝酸钠2份,4.甲基吗啉-n-氧化物1 份,乙二胺四乙酸二钠2份,三聚磷酸钠0.2份,三甲基硅烷2份,碳酸氢钠0.2份;
81.本实施例缓释液的制备方法如下:
82.先用量筒量取91.6份的纯水,将称量好的硝酸钠、三甲基硅烷混合一起,充分搅拌10min,并依序将称量好的硝酸钠、乙二胺四乙酸二钠、三聚磷酸钠、碳酸氢钠投入,并不停地搅拌,搅拌至溶液完全分散,时间大致需要20-60min。
83.比较例1:
84.本比较例缓释液的配方为:
85.采用3份苯甲酸钠,4份乙二胺四乙酸二钠,2份三聚磷酸钠,2份柠檬酸,2份苯并三氮唑;
86.本实施例缓释液的制备方法如下:
87.先用量筒量取87份(质量组分)的纯水,并依序将称量好的苯甲酸钠、乙二胺四乙酸二钠、三聚磷酸钠、柠檬酸、苯并三氮唑投入,并不停地搅拌,搅拌至溶液完全分散,时间大致需要20-60min。
88.用以上4款7系铝合金浸泡缓蚀剂分别对100片砂光和100片镜面精抛的7系铝合金片进行浸泡缓蚀测试,前工序抛光分别酸性砂光液和碱性硅溶胶,该200片7 系铝合金片经过砂光和精抛后检查产品外观有无腐蚀 (发白、黑点、发黄)不良。实施例和比较例中现场良率检测结果总结在下面的表1中。浸泡前后采用光泽仪检测产品光泽度变化,型号:威福wg68;采用激光干涉仪,型号:zygo,pti250,进行表面粗糙度测量。7系铝合金砂光面浸泡缓蚀剂前后粗糙度变化总结在下面的表2中,7系铝合金镜面浸泡缓蚀剂前后粗糙度变化总结在下面的表3中。
89.表1
90.[0091][0092]
表2
[0093]
[0094][0095]
表3
[0096][0097]
从表1中能够发现:实例3.1良率最高;缓释效果 100%;从表2、3中能够发现,实例3.1浸泡24小时后光泽变化量最小,几乎无改变,并且表面粗糙度无变化;其差异在于在各组分协调下对7系铝合金氧化缓蚀效果更好,并且这种缓蚀氧化膜更均匀,更致密透明,最终达成更强的缓释效果,达成更光洁的表面,不存在其它类的不良。
[0098]
本发明的7系铝合金浸泡缓蚀剂成分合理、配制简单、无有害添加物、酸碱中性中性有助于安全生产、使用方便,便于大规模生产制备。应用范围广泛,在7系铝合金加工的cnc、抛光、等制程中均可使用;而且不影响产品外观效果及性能需求。
[0099]
专利范围,凡是在本发明的构思之内所作的任何修改,等同替换和改进等均应包含在本发明的专利保护范围内。