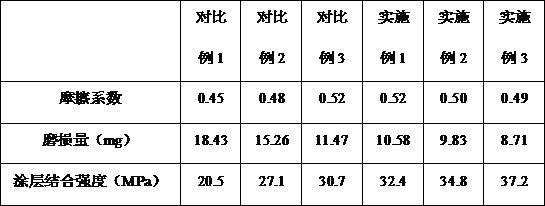
1.本发明涉及一种镁合金表面冷喷涂铝基复合耐磨涂层的制备方法,属于金属表面增材制造技术领域。
背景技术:2.在我国,已将镁合金的应用列入重点发展研究课题,在军工、航空航天开始得到重要应用。在航空航天工业上,除少数型号外,几乎所有在制和新研制的飞机(歼灭机、轰炸机、直升机、运输机、民用飞机等)发动机、机载雷达、地空导弹、运载火箭、人造卫星、飞船上均选用了镁合金构件。同时,如战术导弹、轻型车辆等武器装备对减轻重量都提出了迫切的要求。
3.然而,镁合金材料现有使用状况远没有充分发挥其潜在优势,在实际工业应用方面的发展远不及铝合金和钢铁。当镁合金零部件受损伤破坏时,应进行再制造修复以提高其耐磨防护能力。镁合金材料作为结构部件,有时会受到动态载荷的作用,使其在短时间产生极大的变形,这就要求材料的表面涂层具有优良的动态力学性能。当运动部件,如活塞、阀门或其他滑动部件采用镁合金时,可以降低摩擦力,节约能源。由于镁合金的耐磨性较弱,如何通过表面技术解决镁合金表面耐磨问题是提高镁合金使用寿命、拓宽镁合金应用范围的关键之一。
4.目前提高镁合金表面耐磨性能的方法主要有等离子体微弧阳极氧化、电镀、化学镀、气相沉积、激光改性、热喷涂等。近年来,冷喷涂逐渐被人们接受,其具有在喷涂过程中低于给料熔点的工作温度,涂层氧化率低,不存在相变、晶粒长大、化学成分变化等缺陷。由于冷喷涂过程中给料极高的动能及沉积中的夯实作用,涂层孔隙率极低,电导率相较于涂层块状材料而言变化极小,残余应力小等优点,有望在镁合金表面获得界面结合好、表面质量高、耐磨性强的复合涂层。
5.因此,开展镁合金表面冷喷涂铝基复合耐磨涂层的界面研究,将对保证军事装备运行的可靠性,提高关键零部件的轻量化指标,满足增材制造耐磨需要,推动我国军事装备发展产生重要的影响。
6.目前有关镁合金的增材制造专利主要集中解决镁合金的腐蚀问题,cn105256307a公开了一种镁合金表面耐腐蚀铝基或锌铝基金属涂层的冷喷涂制备方法,将铝基或锌铝基金属粉末与硬质金属粉末混合,制得用于冷喷涂的混合粉末;采用冷喷涂工艺,在经过预处理的镁合金基体上喷涂混合粉末,在镁合金基体表面制得耐腐蚀铝基或锌铝基金属涂层。该发明虽然提高了镁合金基体的耐腐蚀性能,但并未涉及磨损性能的评价。
7.cn105543835a公开了一种冷喷涂铝基耐蚀涂层的制备方法,所述涂层包括al和al2o3以及m,所述m为铝稀土合金和/或铝镁合金;所述al和al2o3中,al2o3体积比x为10%-35%;m为铝镁合金时,mg元素在涂层中的质量总占比为0.15%-2.5%;m为铝稀土合金时,re元素在涂层中的质量总占比为0.02%-0.58%;m为两者的混合物时,re元素和mg元素的质量之比和在涂层中的总占比为0.02%-2.80%。该发明值得的涂层具有优异的耐腐蚀性能,克服了
铝涂层自身存在强度和硬度较低的缺陷,但并没有考虑涂层与界面的结合力。
技术实现要素:8.本发明的目的是提供一种镁合金表面冷喷涂铝基复合耐磨涂层的制备方法,以解决现有技术中涂层和界面结合力差,涂层容易脱落,造成耐磨性较差的问题。
9.本发明是通过如下技术方案实现的:一种镁合金表面冷喷涂铝基复合耐磨涂层的制备方法,其特征在于,所述制备方法包括以下步骤:步骤1,将al和al2o3的混合粉末冷喷涂沉积在镁合金表面形成复合涂层;其中,al2o3的体积比为:15%~45%,al的体积比为:85%~55%;冷喷涂的工艺参数如下:喷距25~40mm,载气压力1.0~2.2mpa,载气温度220~240℃,送粉电压25~30mv;步骤2,将复合涂层进行低温退火处理,形成连续镁铝金属间化合物冶金扩散层,即得复合耐磨涂层;其中,低温退火温度:250~350℃;低温退火时间为8h~24h;所述低温退火处理在无氧环境下进行。
10.进一步的:步骤1中,al颗粒为球形或类球形粉末,al2o3颗粒为板条状或球形,al和al2o3颗粒的平均粒径均为25~50μm。
11.本发明的优点是:本发明制备的镁合金表面冷喷涂铝基复合耐磨涂层,冷喷涂和热处理工艺简单。本发明制备的镁合金表面冷喷涂铝基复合耐磨涂层,具有优异的耐磨性和界面结合强度,克服了铝基复合材料存在易脱落,耐磨性差的缺陷,本发明可为轻质合金耐磨涂层的设计和制备提供研究基础,可以为轻量化装备的长期安全服役提供一种可靠的耐磨技术。
具体实施方式
12.本发明公开了一种镁合金表面冷喷涂铝基复合耐磨涂层的制备方法,所述制备方法包括以下步骤:步骤1,将al和al2o3的混合粉末冷喷涂沉积在镁合金表面形成复合涂层;其中,al2o3的体积比为:15%~45%,al的体积比为:85%~55%;冷喷涂的工艺参数如下:喷距25~40mm,载气压力1.0~2.2mpa,载气温度220~240℃,送粉电压25~30mv;步骤2,将复合涂层进行低温退火处理,处理后,可形成连续镁铝金属间化合物冶金扩散层,从而制备得复合耐磨涂层;其中,低温退火温度:250~350℃;低温退火时间为8h~24h;所述低温退火处理在无氧环境下进行。
13.优选的:步骤1中,al颗粒为球形或类球形粉末,al2o3颗粒为板条状或球形,al和al2o3颗粒的平均粒径均为25~50μm。
14.优选的:所述复合耐磨涂层厚度为1mm。
15.优选的:在冷喷涂前,对镁合金基体表面进行预处理,具体可采用丙酮超声清洗及喷砂表面粗化处理等方式进行。
16.优选的:喷涂时的工作气体为氮气。
17.优选的:所述混合粉末是将al和al2o3的粉末在高速混合机混合制备而成,混合时
间8h。
18.下面结合实施例对本发明做进一步详细的描述,但本发明的实施方式不限于此。
19.对比例1将平均粒径为25μm左右、体积百分数为15%的al2o3与85%的al(即铝粉),在高速混合机中混合,混合时间为8h。采用冷喷涂方法将al和al2o3的混合粉末喷涂在镁合金表面,冷喷涂过程中,喷距为25mm,载气压力为1.6mpa,载气温度为23℃,送粉电压为28mv,涂层的厚度为1mm。
20.对所制备的涂层进行测试。在干摩擦条件下测试镁合金铝基复合涂层的耐磨性,采用往复摩擦试验机,载荷为5n,往复行程为20mm,频率为1hz,磨损时间为1h。使用e7粘接剂将喷有涂层的试样上下表面粘接于钢质拉伸夹具上,在轴向拉伸试验机上进行铝基复合耐磨涂层的涂层结合强度测试,其试验结果见表1。
21.对比例2将对比例1中的体积分数改为30%的al2o3粉末与70%的al;其他制备工艺参数不变,得到镁合金铝基复合涂层。测试方法如对比例1,结果见表1。
22.对比例3将对比例1中的体积分数改为45%的al2o3粉末与55%的al;其他制备工艺参数不变,得到镁合金铝基复合涂层。测试方法如对比例1,结果见表1。
23.实施例1将平均粒径为25μm左右、体积百分数为45%的al2o3粉末与55%的al,在高速混合机中混合,混合时间为8h。采用冷喷涂方法将al和al2o3的混合粉末喷涂在预处理后的镁合金表面,冷喷涂过程中,喷距为25mm,载气压力为1.6mpa,载气温度为230℃,送粉电压为28mv,涂层的厚度为1mm。
24.将镁合金铝基复合涂层在330℃无氧环境下退火8h,制得最终复合涂层。
25.对所制备的涂层进行测试。在干摩擦条件下测试镁合金铝基复合涂层的耐磨性,采用往复摩擦试验机,载荷为5n,往复行程为20mm,频率为1hz,磨损时间为1h。使用e7粘接剂将喷有涂层的试样上下表面粘接于钢质拉伸夹具上,在轴向拉伸试验机上进行铝基复合耐磨涂层的涂层结合强度测试,其试验结果见表1。
26.实施例2按实施例1的条件制备复合涂层。将镁合金铝基复合涂层在330℃无氧环境下退火16h。测试方法如实施例1,结果见表1。
27.实施例3按实施例1的条件制备复合涂层。将镁合金铝基复合涂层在330℃无氧环境下退火24h。测试方法如实施例1,结果见表1。
28.表1 测试结果
由表1所示,实施例3中,45%的al2o3体积含量的铝基复合涂层,在330℃、24h退火处理后取得了良好的减摩耐磨性。本发明所述的铝基复合涂层,通过调整al2o3的特定比例,并且增设特定条件下的退火处理,从而使铝基复合涂层获得了较好的耐磨减摩效果。本方案中,al2o3的比例设定,使体系中al2o3硬质颗粒的含量更为合理,相较现有涂层的强度和硬度升高,孔隙率降低,从而使铝基复合涂层的耐磨性增强。通过在无氧环境下的退火处理,使纯铝粉末发生软化,进一步填充冷喷涂产生的涂层孔隙,不仅减少了腐蚀介质浸入的可能,提高了防腐性能,并且使铝粉与al2o3之间的结合增强,释放了内部应力,提高了涂层内部的韧性。同时退火处理还使得镁基体与铝粉之间界面处发生扩散等,形成金属间化合物。长时间的退火使得扩散层增厚和均化,大大提高了界面结合能力,即提高了涂层与基体之间的结合力,镁合金的使用寿命大幅度延长。