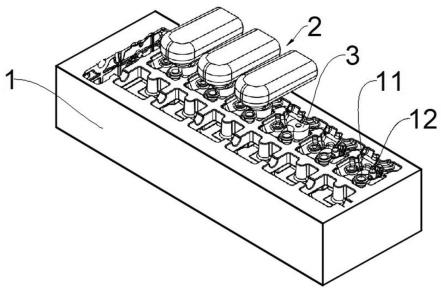
1.本实用新型涉及柴油发动机缸盖铸造技术领域,具体涉及一种蠕墨铸铁立浇缸盖罩面芯的制芯工艺结构。
背景技术:2.目前高牌号蠕墨铸铁气缸盖铸造工艺设计方法通常采用立浇工艺,根据生产线选择一箱两件布局,生产中由于气缸盖螺栓孔、导管孔以及喷油嘴等热节部位较多,温度场复杂,再加上铸件轻量化带来的壁厚薄壁化,加剧缩孔缩松倾向,另外高牌号蠕墨铸铁本身凝固的特性导致热节部位得不到有效补缩,形成孤立液相区,产生缩孔缩松缺陷。
3.中国发明cn113182496a公开了一种高牌号蠕墨铸铁气缸盖的铸造工艺设计方法,采用一箱两件立浇工艺,包括如下步骤:s1、确定浇注系统为中注式,浇注系统设计在两个组合芯之间,全包砂芯设计;s2、确定内浇口的位置,内浇口的位置设在铸件螺栓孔热节部位附近;在所述底盘芯的底面设计浇注系统,2个底盘芯的底面各形成一半浇注系统,合芯后2个底盘芯的底面形成完整的浇注系统;s3、确定排气系统形成方式;s4、采用无冷铁工艺;s5、将气缸盖所有砂芯进行组芯合芯,并用锁芯螺杆锁紧,然后进行下芯,合箱,等待浇注;s6、铸件浇注。该发明通过将内浇口的位置设在铸件螺栓孔热节部位附近,解决气缸盖的缩松问题。但在缸盖的生产实践中发现,喷油嘴位置缩松问题更为普遍,而且比例较高。严重影响成品率和产品交付率,喷油嘴在缸盖的中部位置,底注的工艺设计无法将内浇口位置设置在此处以解决缩松问题。常规的解决缩松的方式有两种,在热节处放置冷铁使之实现顺序凝固或在易产生缩松的位置放置冒口进行补缩,而缸盖的喷油嘴处空间狭小且结构复杂,难以放置冷铁或者冒口。
技术实现要素:4.本实用新型为解决缸盖喷油嘴位置由于空间狭小结构复杂难以设置冒口的技术问题,提供一种可以在喷油嘴位置设置冒口的蠕墨铸铁立浇缸盖罩面芯的制芯工艺结构,从而有效解决喷油嘴位置的缩松问题。
5.本实用新型采用的技术方案是,一种蠕墨铸铁立浇缸盖罩面芯的制芯工艺结构,包括模具,模具中部有喷油嘴部,喷油嘴部上侧有罩面搭子部,其中,模具里的设置有冒口,冒口包括冒口本体,冒口本体的侧面设有连接模具的连接座,连接座中间设有补缩孔,补缩孔与罩面搭子部对齐,使冒口可以通过罩面搭子对喷油嘴位置进行补缩,模具与连接座之间还设置有冒口底座芯,冒口底座芯的背面与连接座面接触,冒口底座芯的正面与模具面接触,冒口底座芯的侧面,部分与模具面接触,面接触的边缘线随形延伸到背面形成随形面,不与模具面接触的部分为自由面,自由面与随形面相连接,冒口底座芯在罩面搭子部正上方设有连通孔,用于连通补缩孔。
6.进一步地,自由面为圆弧面。
7.进一步地,圆弧面与连通孔的轴线重合。
8.进一步地,自由面在连接座外周轮廓的外侧。
9.进一步地,冒口底座芯的背面高于模具上罩面的最高点。
10.本实用新型通过设置冒口底座芯,使缸盖喷油嘴位置可以设置冒口,冒口底座芯背面的大平面,方便冒口定位和放置,填砂也不受影响,冒口可对喷油嘴位置进行补缩,解决缸盖缩松问题。
附图说明
11.图1是本实用新型的结构示意图。
12.图2是本实用新型的俯视图。
13.图3是本实用新型冒口与冒口底座芯组合的示意图。
14.图4是本实用新型冒口的示意图。
15.图5是本实用新型冒口底座芯的示意图。
16.图标:1、模具;11、喷油嘴部;12、罩面搭子部;2、冒口;21、冒口本体;22、连接座;23、补缩孔;3、冒口底座芯;31、随形面;32、自由面;33、连接孔。
具体实施方式
17.为了更好地了解本实用新型的目的、结构及功能,下面结合附图,对本实用新型的蠕墨铸铁立浇缸盖罩面芯的制芯工艺结构做进一步详细的描述。
18.如图1-5所示,一种蠕墨铸铁立浇缸盖罩面芯的制芯工艺结构,包括模具1,模具1中部有喷油嘴部11,喷油嘴部11上侧有罩面搭子部12,模具1里设置有冒口2,冒口2包括冒口本体21,冒口本体21的侧面设置有连接模具1的连接座22,连接座22中间设有补缩孔23,补缩孔23与罩面搭子部12连接,使冒口2可以通过罩面搭子对喷油嘴位置进行补缩,罩面搭子部12与连接座22之间设置有冒口底座芯3,冒口底座芯3的背面为平面,与连接座22面接触,冒口底座芯3的正面与异形的模具1贴合面接触,冒口底座芯3的侧面,部分与模具1面接触,面接触的边缘线随形延伸到背面形成随形面31,不与模具1面接触的部分为自由面32,自由面32与随形面31相连接,冒口底座芯3在罩面搭子部12正上方设有连通孔33,用于连通补缩孔23。本实用新型通过设置冒口底座芯3,使空间狭小、结构复杂的缸盖喷油嘴位置可以设置冒口2,冒口2可对喷油嘴位置进行补缩,以解决缸盖缩松问题。同时,冒口底座芯3背面的大平面,方便冒口定位和放置,填砂也不受影响。
19.本实施例中,自由面32为圆弧面,圆弧面与连通孔33的轴线重合,便于冒口2的定位。同时,自由面32延伸到连接座22外周轮廓的外侧,便于冒口2的安装,也可避免冒口2安装后在连接座22下方产生虚砂。冒口底座芯3的背面高于模具1上罩面的最高点,防止首次放砂过程中,型砂覆盖冒口底座芯。
20.本实用新型的制芯工艺,通过设置的冒口底座芯3,使缸盖喷油嘴位置可以容易地设置冒口2,冒口底座芯3背面的大平面,方便冒口2定位和放置,填砂也不受影响,采用本实用新型制芯工艺,在缸盖罩面喷油嘴对应的位置,每一个喷油嘴处设置一个对应的冒口2,冒口2对喷油嘴位置起到铁水溢流补缩的作用,能很好的减少立浇缸盖喷油嘴位置的缩松比例,提高铸件的成品率,减少加工成本,提高交付率。
21.可以理解,本实用新型是通过一些实施例进行描述的,本领域技术人员知悉的,在
不脱离本实用新型的精神和范围的情况下,可以对这些特征和实施例进行各种改变或等效替换。另外,在本实用新型的教导下,可以对这些特征和实施例进行修改以适应具体的情况及材料而不会脱离本实用新型的精神和范围。因此,本实用新型不受此处所公开的具体实施例的限制,所有落入本申请的权利要求范围内的实施例都属于本实用新型所保护的范围内。
技术特征:1.一种蠕墨铸铁立浇缸盖罩面芯的制芯工艺结构,包括模具(1),模具(1)中部有喷油嘴部(11),喷油嘴部(11)上侧有罩面搭子部(12),其特征在于,模具(1)里的设置有冒口(2),冒口(2)包括冒口本体(21),冒口本体(21)的侧面设有连接模具(1)的连接座(22),连接座(22)中间设有补缩孔(23),补缩孔(23)与罩面搭子部(12)对齐,使冒口(2)可以通过罩面搭子对喷油嘴位置进行补缩,模具(1)与连接座(22)之间还设置有冒口底座芯(3),冒口底座芯(3)的背面与连接座(22)面接触,冒口底座芯(3)的正面与模具(1)面接触,冒口底座芯(3)的侧面,部分与模具(1)面接触,面接触的边缘线随形延伸到背面形成随形面(31),不与模具面接触的部分为自由面(32),自由面(32)与随形面(31)相连接,冒口底座芯(3)在罩面搭子部(12)正上方设有连通孔(33),用于连通补缩孔(23)。2.根据权利要求1所述的蠕墨铸铁立浇缸盖罩面芯的制芯工艺结构,其特征在于,自由面(32)为圆弧面。3.根据权利要求2所述的蠕墨铸铁立浇缸盖罩面芯的制芯工艺结构,其特征在于,圆弧面与连通孔(33)的轴线重合。4.根据权利要求1所述的蠕墨铸铁立浇缸盖罩面芯的制芯工艺结构,其特征在于,自由面(32)在连接座(22)外周轮廓的外侧。5.根据权利要求1所述的蠕墨铸铁立浇缸盖罩面芯的制芯工艺结构,其特征在于,冒口底座芯(3)的背面高于模具(1)上罩面的最高点。
技术总结本实用新型公开了一种蠕墨铸铁立浇缸盖罩面芯的制芯工艺结构,包括模具,模具中部有喷油嘴部,喷油嘴部上侧有罩面搭子部,其中,模具里的设置有冒口,冒口包括冒口本体,冒口本体的侧面设有连接模具的连接座,连接座中间设有补缩孔,补缩孔与罩面搭子部对齐,使冒口可以通过罩面搭子对喷油嘴位置进行补缩,模具与连接座之间还设置有冒口底座芯,冒口底座芯的背面与连接座面接触,冒口底座芯的正面与模具面接触,冒口底座芯的侧面,部分与模具面接触,冒口底座芯在罩面搭子部正上方设有连通孔,用于连通补缩孔。设置冒口底座芯,使缸盖喷油嘴位置可以设置冒口,冒口可对喷油嘴位置进行补缩,解决缸盖缩松问题。解决缸盖缩松问题。解决缸盖缩松问题。
技术研发人员:赵鹏 郭康康 井园园
受保护的技术使用者:亚新科国际铸造(山西)有限公司
技术研发日:2022.09.01
技术公布日:2023/3/13