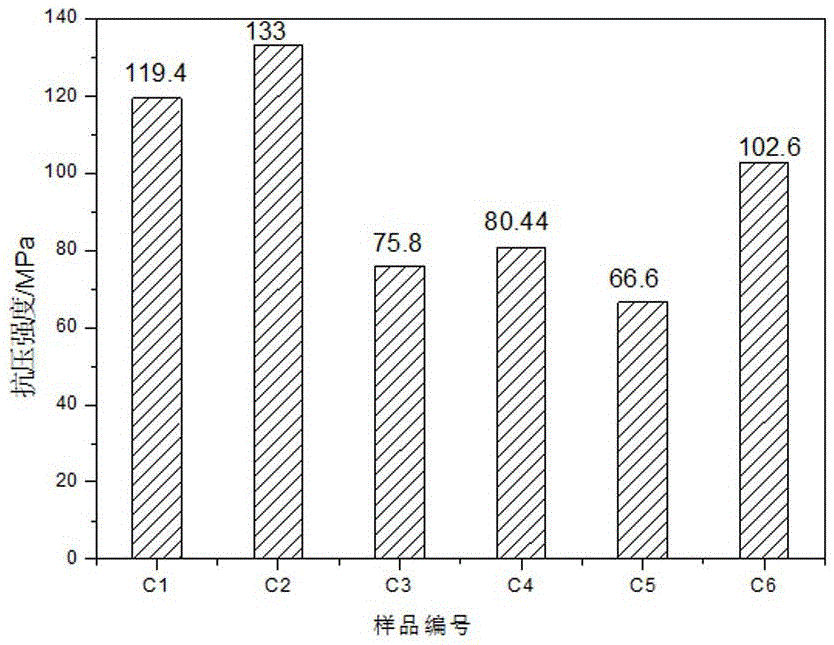
本发明涉及一种新型建筑材料,特别是一种综合利用工业副产石膏与铝硅酸盐类工业废渣耦合制造建筑材料的方法。
背景技术:
:氟石膏是氢氟酸生产过程中的副产品,由硫酸与萤石反应产出的以含硫酸钙为主的废渣,主要产自无机氟化物和有机氟化物生产厂及其他氢氟酸生产厂,产量相当可观,每生产lt氢氟酸约产氟石膏4t以上,每年我国氟化盐厂排出的氟石膏量达100多万吨。刚出装置时氟石膏中含有残余的萤石与硫酸,其中氟及硫酸含量较高,都超过危险废物鉴别标准所规定的限值,属腐蚀性强的有害固体废弃物,对植物、动物和人都具有极大的副作用。其活性小,不能单独作为一种胶凝材料使用,大部分在稍加中和处理后就作为一般固体废弃物堆存,直接堆存不仅占用土地,还污染土壤和地下水环境。因此,处理和利用氟石膏,对生态环境具有十分重要的意义。由于生产氟化氢所用的原料酸级萤石纯度很高,反应过程处于无水状态,所副产的氟石膏为无水石膏,其中CaSO4含量很高达95%以上,氟石膏晶体颗粒表面光滑,其中细小颗粒较多,呈粒状或球状。其属于二型无水石膏的一个变体,具有水化生成二水石膏的能力,但无水氟石膏酸性强、水化活性低,水化速度小。利用氟石膏开发生产出了石膏砖和石膏彩砖。由于氟石膏本身的一些特性对石膏砖的体积稳定性和强度造成了一定的影响。如彩砖的抗压强度仅为15MPa,低于20MPa的国家建材标准要求。这些质量缺陷的存在,极大地限制了其市场的推广。钛石膏是采用硫酸酸解钛铁矿生产钛白粉时,加入石灰或电石渣中和大量的酸性废水所产生的以二水石膏为主要成分的废渣。其处理过程是先用石灰石中和至PH为7。然后加入絮凝剂在增稠器中沉降,清液合理溢流排放。下层浓浆通过压滤机压滤.压滤后的滤渣即为钛石膏,每生产1吨钛白粉副产10吨钛石膏。全世界每年钛石膏的排放量为1775万吨;我国每年约为715万吨。钛石膏含水量高、粘度大、杂质含量高,呈弱酸性,从废渣处理车间出来时。先是灰褐色。置于空气中二价铁离子逐渐被氧化成三价铁离子而变成红色(偏黄),故又名红泥,红、黄石膏。可用煅烧的钛石膏、粉煤灰、矿渣、硅酸盐水泥、激发剂配制复合胶结材料,或钛石膏烘干后用做水泥缓凝剂,以高钙灰与钛石膏复合制作路基材料等。值得注意的是。和天然石膏相比,钛石膏中的铁含量较高。因此.钛石膏具有黏度大、置于空气中易变成红色等特点.这给钛石膏的处理工艺带来一定困难。盐石膏在海水制盐过程中排放的固体废渣通常称为盐石膏。氯化钠NaCl是化学工业的重要原料,盐场用海水晒盐制造的过程中需产生大量的固体废渣盐石膏(俗称硝皮)。每生产20吨原盐大约产生1吨盐石膏。盐石膏外观呈灰黄色,主要成分是二水硫酸钙,多为柱状结晶体,并含有少量Mg2+、Al3+、Fe3+等无机盐类和大量泥沙。因掺有大量杂质以废弃物形式堆放填埋,不但占用土地污染环境,还给盐场再扩建带来一定的困难,如何将大量废渣处理再利用是企业亟待解决的问题。柠檬酸石膏是食品化工业采用石灰法制取柠檬酸时的一种化学沉积物,渣量与产品量基本相当,因此产生的工业废渣较多。我国柠檬酸年产量达70余万吨,柠檬酸石膏排放量达105万吨,占全世界排放总量的63%左右。柠檬酸石膏细度大(4900孔筛筛余为25%~40%),三氧化硫含量高达45%以上,R2O等有害成分较少。柠檬酸石膏的矿物组成主要为二水硫酸钙,含量达90%以上,根据其矿物组成分析可以替代天然二水石膏。但其含水量大,可达30%~40%且含有一定的残余酸和有机物(菌丝体),使其凝结时间变长,利用困难。以上所述的工业副产石膏都是在工业生产中产生的以硫酸钙为主要成分的工业废料,堆放这些废料不仅占用大量土地,而且污染环境和地下水资源。应用于建筑材料又存在性能差的缺点。技术实现要素:本发明要解决的技术问题是提供一种利用工业副产石膏制备建筑材料的方法,至少克服现有石膏类产品强度低、耐久性差的缺点。为解决以上技术问题,本发明采用的技术方案是:一种利用工业副产石膏制备建筑材料的方法,包括步骤:S1:以质量百分比计的如下原料制成干混料,工业副产石膏15%~65%,铝硅酸盐类工业废渣10%~60%,集料22%~35%,钙质胶凝材料3%~12%;S2:向步骤S1制得的干混料加入水或溶入了激发剂的水溶液湿混制得湿混料,其中水占全部固体物料干基质量的12%~20%,激发剂为铝硅酸盐类工业废渣干基质量的0.2%~1.5%;S3:将湿混料进行静置,静置时间为15min~2h;S4:将经步骤S3处理的物料进行静压成型得到坯体,成型压力为20MPa~50MPa,保压时间为15s~1min;S5:将步骤S4制得的坯体进行自然养护28天或经静停0.5h~3h后蒸汽养护3h~24h,制得所述材料,其中蒸汽养护温度为70℃~100℃。作为优选的技术方案,所述的工业副产石膏是以硫酸钙矿物为主要成分的工业废渣。作为优选的技术方案,所述的工业副产石膏为氟石膏、钛石膏、盐石膏、柠檬酸石膏中的一种或几种的组合。所述的铝硅酸盐类工业废渣优选自矿渣、水淬矿渣、粉煤灰、铝锌渣、磷渣中的一种或几种的组合。作为优选的技术方案,所述的钙质胶凝材料是以氧化钙、硅酸钙或铝酸钙为主要矿物的材料。作为优选的技术方案,钙质胶凝材料是指石灰、电石渣、水泥熟料和水泥中的一种或多种的组合。作为优选的技术方案,所述的集料是粒径在0.1~10mm的河砂、机制砂、水淬镍铁渣颗粒、矿渣颗粒、炉渣颗粒、建筑垃圾再生细集料、各种尾矿中的一种或几种的组合。作为优选的技术方案,工业副产石膏、铝硅酸盐类工业废渣和钙质胶凝材料采用单独粉磨后混合或者混合后粉磨的方式处理,制得混合粉体,控制混合粉体的比表面积在400m2/kg~800m2/kg。作为优选的技术方案,混合粉体与集料按比例混合3~5min制得所述的干混料。作为优选的技术方案,干混料加入水或溶入了激发剂的水混合3~10min制得湿混料。本发明利用工业副产石膏与铝硅酸盐类工业废渣耦合制备超高强材料的机理:(1)根据材料最紧密堆积原理和水化活性增强原理设计粉体材料(工业副产石膏、铝硅酸盐类工业废渣、钙质胶凝材料)与集料最佳配比范围,与水混合后在较高压力下(以集料抗压强度为限)静压模压成型,获得致密坯体。(2)经过细磨的工业副产石膏在致密坯体孔隙液中发生溶解和再结晶反应,受到致密坯体孔隙大小和相貌的影响,生成数量巨大的纳米石膏晶须(见图1),穿插在孔隙中和铝硅酸盐矿物的水化产物中,起到了进一步增加致密度和纤维增强作用,极大程度提高了材料强度。(3)石膏中的硫酸根离子、钙离子与冶金矿渣、硅铝质辅助胶凝材料水化产物反应生成钙矾石,既提高了坯体致密度,提高材料强度,又提高了材料的耐水性。(4)冶金矿渣水化产物在碱激发剂作用下还与硫酸根离子(或石膏)反应生成水合硫酸方柱石,如:(CaO,xNa2O)[ySiO2·zAl2O3]SO3·nH2O)(见图2),使得矿渣水化产物与石膏晶体或晶须表面薄弱结合区减少,提高了材料的强度和耐水性。本发明与现有方法相比,具有如下有益效果:(1)强度高,各种冶金矿渣的强度如表1所示,是现有常规方法制备的石膏基材料强度(10~30MPa)或铝硅酸盐类工业废渣基材料(10~40MPa)的数倍,甚至十多倍,实现了此类材料强度突破;表1工业副产石膏种类氟石膏钛石膏盐石膏柠檬酸石膏强度(单位:MPa)60~15060~18060~15060~200(2)耐水性好,克服了石膏制品耐水性差的致命缺陷;(3)生产工艺简单,可以通过对现有粉煤灰免烧砖生产线进行简单改造即可实现规模化生产;(4)产品品种调节容易,以实现功能化。利用本发明的技术,可通过变化成型模具方法制备高强建筑砖、高强道路砖、高强透水砖、路沿石、各种装饰板材等各种高强、高耐久性产品;(5)本发明的实施属于工业固废资源化利用采用本发明的技术方案,对工业副产石膏等固体废弃物的利用率可达90%以上,因此,它可以提高固体废弃物的附加值,真正地实现变废为宝。附图说明图1为水化产物特征(晶须增强)。图2为实施例1-4材料的强度。图3为实施例5-8材料的强度。图4为实施例9-12材料的强度。图5为实施例13-16材料的强度。具体实施方式为了使本领域技术人员更好的理解本发明,以下结合实施例对本发明作进一步清楚、完整的说明。需要说明的是,在不冲突的情况下,本申请中的实施例及实施例中的特征可以相互组合。实施例1将比表面积600m2/kg氟石膏400g(40%)、比表面积600m2/kg矿渣300g(30%)、比表面积780m2/kgP·O42.5水泥50g(5%)和细度模数为2.8的河砂250g(25%)在混合机中干混3min;然后加入180g水(全部固体物料干基质量的18%),水中额外加入1.5g碱性激发剂(占矿渣粉的0.5%),湿混10min;静置15min后在40MPa下保压30s,制得超强材料坯体;在混凝土养护室内常温饱水养护28天得超高强材料C1,经静停1h后在100℃下饱和蒸汽养护9h,制得超高强材料C2,抗压强度见图2。实施例2将氟石膏2500g、磷渣2500g放入500×500mm标准球磨机粉磨50min,制得比表面积650m2/kg的混合料,取620g混合料(其中干氟石膏占总干基物料的31%,磷渣占总干基物料的31%),与比表面积480m2/kgP·O42.5水泥80g(占总干基物料的8%)和细度模数为2.8的河砂300g(占总干基物料的30%)在混合机中干混4min;然后加入180g的水(加上石膏带入的水占总干基物料的18%),水中额外加入1.8g碱性激发剂(占CFB粉的0.6%),湿混8min;静置30min后在45MPa下保压15s,制得超强材料坯体;在实验室(温度20℃~31℃)常温饱水养护28天得超高强材料C3,经静停1h后在75℃下饱和蒸汽养护12h,制得超高强材料C4,抗压强度见图2。实施例3将氟石膏2800g、水淬矿渣2200g放入500×500mm标准球磨机粉磨65min,制得比表面积580m2/kg的混合料,取670g混合料(其中氟石膏占总干基物料的37.5%,水淬矿渣占总干基物料的29.5%),与比表面积600m2/kgP·O42.5水泥90g(占总干基物料的9%)和细度模数为3.2的机制砂240g(占总干基物料的24%)在混合机中干混3min;然后加入200g的水(加上石膏带入的水占总干基物料的20%),水中额外加入1.4g碱性激发剂(占水淬矿渣粉的0.47%),湿混9min;静置30min后在45MPa下保压50s,制得超强材料坯体;经静停3h后在90℃下饱和蒸汽养护6h,制得超高强材料C5,抗压强度见图2。实施例4将氟石膏2400g、粉煤灰2200g和石灰400g放入500×500mm标准球磨机粉磨60min,制得比表面积532m2/kg的混合料,取700g混合料(其中粉煤灰占总干基物料的30.8%、干氟石膏占总干基物料的33.6%、石灰占总干基物料的5.6%),和细度模数为2.8的砂浆再生集料300g(占总干基物料的30%)在混合机中干混3min;然后加入190g的水(占总干基物料的19%),湿混7min;静置30min后在43MPa下保压45s,制得超强材料坯体;经静停2h后在90℃下饱和蒸汽养护6h,制得超高强材料C6,抗压强度见图2。实施例5将比表面积450m2/kg钛石膏400g(40%)、比表面积600m2/kg水淬矿渣粉300g(30%)、比表面积380m2/kgP·O42.5水泥50g(5%)和细度模数为2.8的河砂250g(25%)在混合机中干混3min;然后加入180g水(全部固体物料干基质量的18%),水中额外加入1.5g碱性激发剂(占矿渣粉的0.5%),湿混10min;静置15min后在40MPa下保压30s,制得超强材料坯体;在混凝土养护室内自然养护28天得超高强材料F1,经静停1h后在100℃下饱和蒸汽养护9h,制得超高强材料F2,抗压强度见图3。实施例6将烘干钛石膏2500g、干磷渣2500g放入500×500mm标准球磨机粉磨50min,制得比表面积583m2/kg的混合料,取620g混合料(其中钛石膏占总干基物料的31%,磷渣占总干基物料的31%),与比表面积380m2/kgP·O42.5水泥80g(占总干基物料的8%)和细度模数为2.8的河砂300g(占总干基物料的30%)在混合机中干混4min;然后加入180g的水(加上石膏带入的水占总干基物料的18%),水中额外加入1.8g碱性激发剂(占CFB粉的0.6%),湿混8min;静置30min后在45MPa下保压15s,制得超强材料坯体;在实验室(温度20℃~31℃)自然养护28天得超高强材料F3,经静停1h后在75℃下饱和蒸汽养护12h,制得超高强材料F4,抗压强度见图3。实施例7将烘干钛石膏2400g、水淬矿渣2400g放入500×500mm标准球磨机粉磨65min,制得比表面积611m2/kg的混合料,取670g混合料(其中钛石膏占总干基物料的33.5%,水淬矿渣占总干基物料的33.5%),与比表面积380m2/kgP·O42.5水泥90g(占总干基物料的9%)和细度模数为3.2的机制砂240g(占总干基物料的24%)在混合机中干混3min;然后加入200g的水(加上石膏带入的水占总干基物料的20%),水中额外加入1.4g碱性激发剂(占水淬矿渣粉的0.47%),湿混9min;静置30min后在45MPa下保压50s,制得超强材料坯体;经静停3h后在90℃下饱和蒸汽养护6h,制得超高强材料F5,抗压强度见图3。实施例8将烘干钛石膏2200g、粉煤灰2400g和石灰400g放入500×500mm标准球磨机粉磨60min,制得比表面积586m2/kg的混合料,取700g混合料(其中粉煤灰占总干基物料的33.6%、钛石膏占总干基物料的30.8%、石灰占总干基物料的5.6%),和细度模数为2.8的砂浆再生集料300g(占总干基物料的30%)在混合机中干混3min;然后加入190g的水(占总干基物料的19%),湿混7min;静置30min后在43MPa下保压45s,制得超强材料坯体;经静停2h后在90℃下饱和蒸汽养护6h,制得超高强材料F6,抗压强度见图3。实施例9将比表面积400m2/kg盐石膏400g(40%)、比表面积600m2/kg水淬矿渣粉300g(30%)、比表面积380m2/kgP·O42.5水泥50g(5%)和细度模数为2.8的河砂250g(25%)在混合机中干混3min;然后加入180g水(全部固体物料干基质量的18%),水中额外加入1.5g碱性激发剂(占水淬矿渣粉的0.5%),湿混10min;静置15min后在40MPa下保压30s,制得超强材料坯体;在混凝土养护室内自然养护28天得超高强材料E1,经静停1h后在100℃下饱和蒸汽养护9h,制得超高强材料E2,抗压强度见图4。实施例10将盐石膏2500g、干磷渣(CFB)2500g放入500×500mm标准球磨机粉磨50min,制得比表面积564m2/kg的混合料,取620g混合料(其中盐石膏占总干基物料的31%,磷渣占总干基物料的31%),与比表面积380m2/kgP·O42.5水泥80g(占总干基物料的8%)和细度模数为2.8的河砂300g(占总干基物料的30%)在混合机中干混4min;然后加入180g的水(加上石膏带入的水占总干基物料的18%),水中额外加入1.8g碱性激发剂(占CFB粉的0.6%),湿混8min;静置30min后在45MPa下保压15s,制得超强材料坯体;在实验室(温度20℃~31℃)自然养护28天得超高强材料E3,经静停1h后在75℃下饱和蒸汽养护12h,制得超高强材料E4,抗压强度见图4。实施例11将盐石膏2800g、水淬矿渣2200g放入500×500mm标准球磨机粉磨65min,制得比表面积608m2/kg的混合料,取670g混合料(其中盐石膏占总干基物料的37.5%,水淬矿渣占总干基物料的29.5%),与比表面积380m2/kgP·O42.5水泥90g(占总干基物料的9%)和细度模数为3.2的机制砂240g(占总干基物料的24%)在混合机中干混3min;然后加入200g的水(加上石膏带入的水占总干基物料的20%),水中额外加入1.4g碱性激发剂(占水淬矿渣粉的0.47%),湿混9min;静置30min后在45MPa下保压50s,制得超强材料坯体;经静停3h后在90℃下饱和蒸汽养护6h,制得超高强材料E5,抗压强度见图4。实施例12将盐石膏2400g、粉煤灰2200g和石灰400g放入500×500mm标准球磨机粉磨60min,制得比表面积532m2/kg的混合料,取700g混合料(其中粉煤灰占总干基物料的30.8%、盐石膏占总干基物料的33.6%、石灰占总干基物料的5.6%),和细度模数为2.8的砂浆再生集料300g(占总干基物料的30%)在混合机中干混3min;然后加入190g的水(占总干基物料的19%),湿混7min;静置30min后在43MPa下保压45s,制得超强材料坯体;经静停2h后在90℃下饱和蒸汽养护6h,制得超高强材料E6,抗压强度见图4。实施例13将比表面积489m2/kg柠檬酸石膏400g(40%)、比表面积600m2/kg矿渣300g(30%)、比表面积380m2/kgP·O42.5水泥50g(5%)和细度模数为2.4的河砂250g(25%)在混合机中干混3min;然后加入150g水(全部固体物料干基质量的15%),水中额外加入1.5g碱性激发剂(占矿渣粉的0.5%),湿混10min;静置15min后在40MPa下保压30s,制得超强材料坯体;在混凝土养护室内自然养护28天得超高强材料D1,经静停1h后在80℃下饱和蒸汽养护9h,制得超高强材料D2,抗压强度见图5。实施例14将含水率10%柠檬酸石膏2500g、干磷渣2500g放入500×500mm标准球磨机粉磨55min,制得比表面积601m2/kg的混合料,取620g混合料(其中干柠檬酸石膏占总干基物料的28.8%,磷渣占总干基物料的32%),与比表面积380m2/kgP·O42.5水泥60g(占总干基物料的6.2%)和细度模数为2.4的河砂320g(占总干基物料的33%)在混合机中干混4min;然后加入150g的水(加上石膏带入的水占总干基物料的18.7%),水中额外加入1.8g碱性激发剂(占CFB粉的0.6%),湿混8min;静置30min后在45MPa下保压15s,制得超强材料坯体;在实验室(温度20℃~31℃,相对湿度67%~83%)自然养护28天得超高强材料D3,经静停1h后在75℃下饱和蒸汽养护12h,制得超高强材料D4,抗压强度见图5。实施例15将含水率7%柠檬酸石膏2800g、水淬矿渣2200g放入500×500mm标准球磨机粉磨54min,制得比表面积590m2/kg的混合料,取670g混合料(其中干柠檬酸石膏占总干基物料的35.8%,水淬矿渣占总干基物料的30.3%),与比表面积380m2/kgP·O42.5水泥90g(占总干基物料的9.2%)和细度模数为3.2的机制砂240g(占总干基物料的24.6%)在混合机中干混3min;然后加入140g的水(加上石膏带入的水占总干基物料的16.6%),水中额外加入1.4g碱性激发剂(占水淬矿渣粉的0.47%),湿混9min;静置30min后在45MPa下保压50s,制得超强材料坯体;经静停3h后在90℃下饱和蒸汽养护6h,制得超高强材料D5,抗压强度见图5。实施例16将含水率0%柠檬酸石膏2300g、粉煤灰2200g和石灰500g放入500×500mm标准球磨机粉磨60min,制得比表面积512m2/kg的混合料,取700g混合料(其中粉煤灰占总干基物料的30.8%、干柠檬酸石膏占总干基物料的32.3%、石灰占总干基物料的7%),和细度模数为2.8的砂浆再生集料300g(占总干基物料的30%)在混合机中干混3min;然后加入150g的水(占总干基物料的15%),湿混7min;静置30min后在43MPa下保压45s,制得超强材料坯体;经静停2h后在90℃下饱和蒸汽养护6h,制得超高强材料D6,抗压强度见图5。实施例17将钛石膏3900g、粉煤灰600g放入500×500mm标准球磨机粉磨67min,制得比表面积400m2/kg的混合料,取750g混合料(其中钛石膏占总干基物料的65%,粉煤灰占总干基物料的10%),与比表面积800m2/kgP·O42.5电石渣30g(占总干基物料的3%)和细度模数为3.2的炉渣颗粒220g(占总干基物料的22%)在混合机中干混5min;然后加入120g的水(占总干基物料的12%),水中额外加入0.2g碱性激发剂(占粉煤灰的0.2%),湿混3min;静置2h后在20MPa下保压1min,制得坯体;经静停0.5h后在70℃下饱和蒸汽养护3h,制得超高强材料F7。实施例18将盐石膏900g、磷渣3600g放入500×500mm标准球磨机粉磨58min,制得比表面积624m2/kg的混合料,取750g混合料(其中盐石膏占总干基物料的15%,磷渣占总干基物料的60%),与比表面积380m2/kgP·O42.5水泥30g(占总干基物料的3%)和细度模数为2.4的河砂100g和机制砂120g(总共占总干基物料的22%)在混合机中干混5min;然后加入150g的水(占总干基物料的15%),水中额外加入9.0g碱性激发剂(占磷渣的1.5%),湿混10min;静置30min后在50MPa下保压15s,制得坯体;在实验室(温度20℃~31℃,相对湿度67%~83%)自然养护28天得超高强材料F8,经静停2h后在100℃下饱和蒸汽养护24h,制得超高强材料F9。实施例19将氟石膏1500g、磷渣1000g和水淬镍铁渣680g放入500×500mm标准球磨机粉磨58min,制得比表面积624m2/kg的混合料,取530g混合料(其中氟石膏占总干基物料的25%,磷渣和水淬镍铁渣占总干基物料的28%),与比表面积380m2/kgP·O42.5水泥100g和石灰20g(总共占总干基物料的12%)和细度模数为2.4的河砂350g(占总干基物料的35%)在混合机中干混4min;然后加入180g的水(占总干基物料的18%),水中额外加入2.8g碱性激发剂(占磷渣和水淬镍铁渣1.0%),湿混5min;静置60min后在30MPa下保压30s,制得坯体;经静停1h后在75℃下饱和蒸汽养护10h,制得超高强材料F10。当前第1页1 2 3