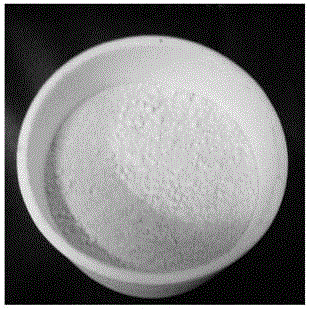
本发明涉及化学或化工工程,更具体地,涉及一种用于对烷基化废硫酸进行无害化处理和利用的方法。
背景技术:
:以下对本发明的相关技术背景进行说明,但这些说明并不一定构成本发明的现有技术。炼油厂在烷基化过程中使用浓硫酸作为催化剂。在烷基化反应中,浓硫酸中不断有烯烃和水溶入,降低了浓硫酸的浓度,当浓度小于90%时,就失去了催化活性,只能当作废品排出。废硫酸呈黑色不透明液体,散发特殊气味,如果随意排放会对环境造成严重污染。炼油厂废酸的排量和使用新硫酸的量大体相当,6万吨/年的烷基化装置年排酸量达3000-9000吨。世界各国对于炼油厂废硫酸的处理作了长期大量的研究工作,还不尽理想。目前有如下几种主要的处理方案:(1)直接利用;(2)硫资源回收;(3)废硫酸有机物脱碳再生。最主流的处理方法是把废硫酸中的硫资源以三氧化硫、二氧化硫或硫元素形态回收。该方法的传统处理方式是建设热裂解装置,用天然气(或燃料油)在裂解炉中燃烧放热,以废硫酸制酸。这一技术尽管成熟,但存在投资大成本高的问题。有机物脱碳再生方法是采用溶剂油提取有机物或者强氧化剂氧化有机物,使废酸再生重复利用。该技术也同样存在成本高的问题,未形成大规模工业生产。废硫酸直接利用的途径有多种。例如废硫酸分解石灰石生产石膏,分解磷矿石生产普钙磷肥,用于油田回注、改良盐碱地和生产其他化学品等。废硫酸在生产磷肥方面的应用,大多都是地方小磷肥厂采用。由于小磷肥工业工艺简陋,除油措施不健全导致产品质量差,非密封操作导致工作环境污染相当严重。在不能够经济有效地解决污染和彻底分油问题的前提下,不是一条可靠的废硫酸处理方式。废硫酸用于油田回注可以溶蚀地下含油层石灰岩,增产原油产量,但是有一系列复杂问题,如高压酸泵、井口和井管耐酸材料的选择存在困难,采出原油的酸性和含硫量增加会导致生产和储运方面的难题。废硫酸用于盐碱地改良,虽然国外有成功的经验,但是技术细节不明。废硫酸用于生产其他化学品,理论上和工业实施上可行,但是需要对废硫酸作必要的预处理,尚未形成大规模应用。用废硫酸分解石灰石生产石膏,具有工艺简单,操作方便等特点。在上世纪80年代有炼油厂曾经做过尝试,但出于当时现实需求方面的原因,采取了其他治理途径。利用石灰石作为反应物,具有以下缺点:第一,石灰石需要进行粉碎,而这一点会占据生产成本的主要部分。第二点,石灰石和硫酸反应不彻底,需要一个相当长的熟化时间,这会导致对仓储场地的大量需求。第三点,制备的石膏含有大量有机废物,品质不高,限制了其应用领域。因此,现有技术中需要一种能够解决现有技术中存在的烷基化硫酸废液不能被无害化处理或处理成本较高的问题的解决方案。技术实现要素:本发明的目的在于提出一种能够有效处理烷基化硫酸废液的方法,从而能够以成本较低的方式实现烷基化硫酸废液的无害化处理,并且将有害物变废为宝,从而最大限度地节约资源,减轻对环境的污染。本发明提供一种烷基化硫酸废液的处理方法,其包括以下步骤:对烷基化硫酸废液进行稀释处理;对稀释后的烷基化硫酸废液进行降温,并去除降温后的烷基化硫酸废液中的有机物;向烷基化硫酸废液中加入熟石灰粉,从而生成石膏,直至烷基化硫酸废液中不再继续产生石膏为止;以及对所产生的石膏进行煅烧,从而去除其中残留的有机物。根据本发明的烷基化硫酸废液的处理方法能够利用较为简单有效的方法将烷基化硫酸废液进行无害化处理,大大降低了浓硫酸废液处理的成本。另外,不仅对浓硫酸废液进行了无害化处理,而且使其转化成了品质较高的石膏,从而大大提高了废液处理后的效益。根据本发明的烷基化硫酸废液的处理方法的一个优选的实施例,对烷基化硫酸废液进行稀释处理的步骤包括利用水将烷基化硫酸废液的浓度稀释至60%以下。在根据本发明的烷基化硫酸废液的处理方法的另一个优选的实施例中,对稀释后的烷基化硫酸废液进行降温的步骤包括使所述烷基化硫酸废液的温度降低至30℃以下。根据本发明的烷基化硫酸废液的处理方法的再一个优选的实施例,去除降温后的烷基化硫酸废液中的有机物的步骤包括通过溢流方式或冷却方式去除所述烷基化硫酸废液中的有机物。在根据本发明的烷基化硫酸废液的处理方法的又一个优选的实施例中,熟石灰粉通过在生石灰中加水使其粉碎成粉末而获得。根据本发明的烷基化硫酸废液的处理方法的还一个优选的实施例,所生成的石膏的煅烧温度为300℃-800℃。进一步有利地,所生成的石膏的煅烧温度为500℃。在根据本发明的烷基化硫酸废液的处理方法的另一个优选的实施例中,所生成的石膏的煅烧时间为1小时-3小时。进一步有利地,所生成的石膏的煅烧时间为2小时。根据本发明的烷基化硫酸废液的处理方法的再一个优选的实施例,该烷基化硫酸废液的处理方法还包括通过催化氧化净化系统对在所述处理方法中产生的废气进行无害化处理。根据本发明的烷基化硫酸废液的处理方法的生产流程和工艺简单,成本较低,其中的中和反应所需时间短,反应彻底,因此对硫酸废液的处理比较彻底。进一步地,本发明利用生石灰加水的方式获得熟石灰,期间生石灰能够自动粉碎并生成熟石灰,由此避免了机械粉碎的操作过程,大大降低了生产成本。此外,反应过程不生成大量气体产物,因此不需要建设吸收塔。而且,通过根据本发明的方法制备的石膏品质高,效益好。根据本发明的生产过程所生成的少量含有机物的废气可以通过催化氧化系统进行处理。因此,根据本发明的处理方法没有害废水、废气和固体废弃物排放,不会对环境产生污染。附图说明通过以下参照附图而提供的具体实施方式部分,本发明的特征和优点将变得更加容易理解,在附图中:图1是根据本发明的烷基化硫酸废液的处理方法的流程图。图2是利用根据本发明的烷基化硫酸废液的处理方法制得的石膏在煅烧之前的视图。图3是利用根据本发明的烷基化硫酸废液的处理方法制得的石膏在煅烧之后的视图。具体实施方式下面参照附图对本发明的示例性实施方式进行详细描述。对示例性实施方式的描述仅仅是出于示范目的,而绝不是对本发明及其应用或用法的限制。本发明根据现有技术的不足,提出了一种实现烷基化废硫酸无害化处理和利用的方法,解决了废硫酸难处理的问题。本发明提出一种利用烷基化硫酸废液制备石膏的生产方法,主要包括稀释除油、粉碎石灰、中和反应和煅烧等几个主要步骤。硫酸废液在反应釜中加水稀释,由于稀释是放热反应,温度升高,稀硫酸溶液溶解有机物的能力下降,有机物悬浮在溶液上面并与酸分离,可以通过溢流或者冷却使油层凝固等方法来除去大部分的有机物;生石灰加水自动粉碎成很细的熟石灰粉末;利用熟石灰粉末和稀硫酸进行中和反应;把生成的石膏产物进行高温煅烧,除去其中有气味的有机物;中和反应和煅烧过程中释放出来的包含有机物的气体通过催化氧化系统进行处理。在该化学工艺过程中的主要化学反应方程式为:CaO+H2O→Ca(OH)2;以及H2SO4+Ca(OH)2→CaSO4+2H2O。以下结合附图1对根据本发明的烷基化硫酸废液的处理方法进行具体说明。根据本发明的烷基化硫酸废液的处理方法包括以下步骤,首先,在步骤102对烷基化硫酸废液进行稀释处理,在此,可以通过向存放烷基化硫酸废液的容器内加入水来对烷基化硫酸废液进行稀释处理。烷基化硫酸废液的浓度一般在90%左右,需要将其加水稀释到60%或以下的浓度。硫酸在稀释过程中会放出热量,因此,需要将稀释后的硫酸废液降温后进行进一步的处理。接着,在步骤104中,对稀释后的烷基化硫酸废液进行降温,并去除降温后的烷基化硫酸废液中的有机物,浓硫酸作为催化剂在使用过程中会有水以及有机物渗入,因此,在处理时需要将其中的有机物滤除。进一步地,在步骤106中,向烷基化硫酸废液中加入熟石灰粉,从而生成石膏,直至烷基化硫酸废液中不再继续产生石膏为止,也就是说,向烷基化硫酸废液中加入足够量的熟石灰粉末,与其中的硫酸废液完全反应,从而使硫酸废液完全转变成石膏。最后,在步骤108中,对所产生的石膏进行煅烧,从而去除其中残留的有机物。可以在300℃至800℃的温度下对石膏进行煅烧作业,从而将石膏中的有机物杂质转变成气体排出,由此提高了石膏的品质和纯度。进一步地,根据本发明的烷基化硫酸废液的处理方法中的对烷基化硫酸废液进行稀释处理的步骤可以包括利用水将烷基化硫酸废液的浓度稀释至60%以下。通过将浓度为90%左右的烷基化硫酸废液稀释至60%的浓度以下,从而析出其中的有机物,然后通过本领域已知的分离方法将有机物分离。接着,对稀释后的烷基化硫酸废液进行降温的步骤可以包括使烷基化硫酸废液的温度降低至30℃以下。通过降低烷基化硫酸废液的温度能够使硫酸废液中的有机物更好地析出。进一步地,可以在烷基化硫酸废液降温之后通过溢流方式或冷却方式去除烷基化硫酸废液中的有机物。比如,可以通过溢流方式使液体状态的烷基化硫酸废液从容器中溢流出,而在容器中留下作为固体的有机物。另外,可以通过冷却方式将有机物冷却成硬度较高的固体块,从而可以从容器中去除固化的有机物,获得有机物含量较少的烷基化硫酸废液。在根据本发明的烷基化硫酸废液的处理方法中,熟石灰粉可以通过在生石灰中加水使其粉碎成粉末而获得,并将获得的熟石灰粉加入到烷基化硫酸废液中。进一步地,煅烧所生成的石膏的温度为300℃-800℃,有利地,煅烧所生成的石膏的温度为500℃。煅烧所生成的石膏的时间为1小时-3小时,有利地,煅烧所生成的石膏的时间为2小时。此外,根据本发明的烷基化硫酸废液的处理方法还包括通过催化氧化净化系统对在该处理方法中产生的废气进行无害化处理,由此可以尽可能地减少烷基化硫酸废液的处理过程中所产生的环境不利影响。根据本发明的烷基化硫酸废液的处理方法的生产流程和工艺简单,成本较低,其中的中和反应所需时间短,反应彻底,因此对硫酸废液的处理比较彻底。进一步地,本发明利用生石灰加水的方式获得熟石灰,期间生石灰能够自动粉碎并生成熟石灰,由此避免了机械粉碎的操作过程,大大降低了生产成本。此外,反应过程不生成大量气体产物,因此不需要建设吸收塔。而且,通过根据本发明的方法制备的石膏品质高,效益好。根据本发明的生产过程所生成的少量含有机物的废气可以通过催化氧化系统进行处理。因此,根据本发明的处理方法没有害废水、废气和固体废弃物排放,不会对环境产生污染。本发明所述实施例中采用的生石灰的化学成分组成如以下表1所示。表1:生石灰成分比例成分CaOSiO2Al2O3MgO其它质量百分比(%)90.487.211.600.530.18以下结合具体实施例对根据本发明的烷基化硫酸废液的处理方法进行说明。实施例1:第一,取500毫升水放入容量为2升的烧杯内,然后缓慢放入850克浓度为85%的硫酸废液,硫酸废液稀释放热,烧杯内温度可以达到90℃-120℃左右,静置2小时,硫酸废液中的有机物析出,浮于容器中液体的表面之上。等到硫酸废液冷却到低于30℃的温度时,从硫酸废液中析出的有机物凝固,可以将有机物从烧杯内捞出。第二,取含钙量为90%的生石灰,撒入适量水,放置4小时—12小时,直到生石灰自动粉碎成熟石灰粉。对熟石灰粉进行过筛,把其中的石头和较大的颗粒去除,随后获得熟石灰粉460克。第三,将所获得的熟石灰粉缓慢加入到烧杯内与稀释后的硫酸废液反应,缓慢搅拌,避免粉尘飘扬。第四,待熟石灰与硫酸废液反应完成后,生成物为半湿的石膏固体。从烧杯内取出石膏,放入马弗炉内,在800℃下进行煅烧,煅烧时间为2小时,然后煅烧完成后等其自然冷却。即能获得最终产品,即为无水石膏粉末,颜色呈白色,其成分如表2所示,其中有机物(COD)的含量低于0.005%。表2:实施例1中所生成的无水石膏的组成成分成分CODCaSiAlMgSO42-其他质量百分比(%)0.00528.711.490.370.1468.490.24实施例2:把250升水放入容积为1000升的反应釜中,然后把360公斤浓度为90%的硫酸废液缓慢加入反应釜中,在稀释过程中可以通过水冷把反应釜的温度控制在100℃以下。静置一段时间之后使大部分有机物浮在上面与硫酸废液分离开,等到冷却至30℃以下时,把漂浮在液面以上的已经凝固的有机物捞取出来,反应釜中剩余基本纯净的硫酸废液。在含钙量为大约85%的生石灰中加入适量水,等待一段时间,待生石灰完全粉碎生成熟石灰粉之后,通过100目筛过筛,把其中的石块和较大颗粒等分离出来。取220千克熟石灰粉逐渐加入反应釜内,并进行适当搅拌,促进中和反应的进行,通过水冷系统控制反应釜的温度,随着石灰粉加入量的增加,需要加强搅拌,直至计量的熟石灰粉全部加入为止。反应过程中所释放出来的夹杂有有机物的少量水蒸气通过催化氧化系统进行处理。反应物料在反应釜内保持一段时间,反应充分之后将石膏料取出。把生产的石膏料放入燃气窑炉内,窑炉的温度控制在700℃-800℃之间,煅烧2小时,由此可以消除石膏料中的有机物。煅烧过程中释放出来的包含有机物的气体通过催化氧化系统进行处理。煅烧完毕的石膏即为最终产品。煅烧后的石膏的成分如表2所示,其中有机物(COD)的比例低于0.006%。表3:实施例2中所生成的无水石膏的组成成分成分CODCaSiAlMgSO42-其他质量百分比(%)0.00628.851.480.360.1368.400.22根据本发明的烷基化硫酸废液的处理方法能够利用较为简单有效的方法将烷基化硫酸废液进行无害化处理,大大降低了浓硫酸废液处理的成本。另外,不仅对浓硫酸废液进行了无害化处理,而且使其转化成了品质较高的石膏,从而大大提高了废液处理后的效益。虽然参照示例性实施方式对本发明进行了描述,但是应当理解,本发明并不局限于文中详细描述和示出的具体实施方式,在不偏离权利要求书所限定的范围的情况下,本领域技术人员可以对所述示例性实施方式做出各种改变。当前第1页1 2 3