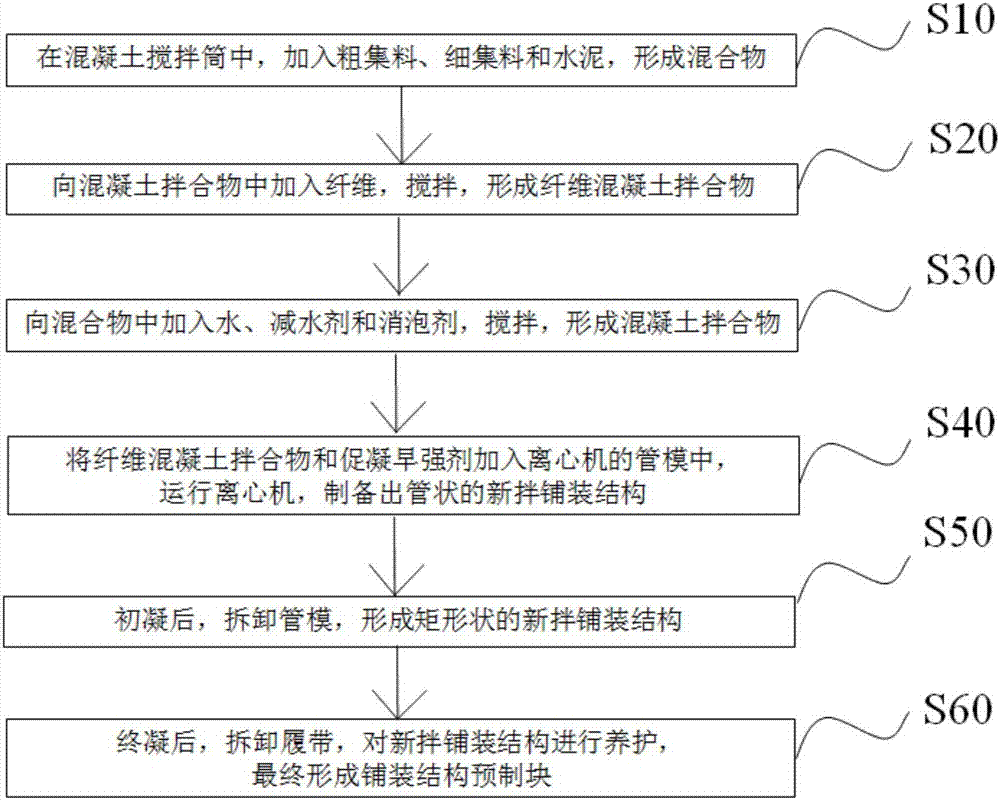
本发明属于道路材料领域,具体来说,涉及一种道路路面或机场道面铺装结构的制备方法。
背景技术:
:道路路面、机场道面常采用水泥混凝土作为道路路面和机场道面材料,水泥混凝土具有其原材料来源广泛、制作工艺简便,应用方便等优点。然而水泥混凝土路面板、道面板也存在抗拉强度低、韧性差和裂缝易扩展等缺点,混凝土的抗弯拉强度比抗压强度低得多,在轮载作用下当弯拉应力超过混凝土的极限抗弯拉强度时,水泥混凝土面板便会产生断裂破坏,且在荷载重复作用下,由于疲劳效应混凝土板会在低于其极限抗弯拉强度时出现破坏。此外,混凝土板厚度方向的温差会使板产生温度翘曲应力,对混凝土板受力不利。水泥混凝土是脆性材料,它在断裂时的相对拉伸变形很小,对地基变形的适应能力不足,土基和基层的变形对混凝土板的影响很大,不均匀的基础变形会造成混凝土板与基层脱空,产生过大的弯拉应力。根据《公路水泥混凝土路面设计规范jtgd40-2011》,进行水泥混凝土路面设计时,取混凝土板的抗弯拉强度作为设计指标,满足荷载疲劳应力与温度疲劳翘曲应力之和不超过混凝土的抗弯拉强度。水泥混凝土机场道面设计与路面设计类似,根据板边临界荷位处的弯拉应力来进行设计。由于水泥混凝土的这些特点,加上环境因素(水分等)的作用,容易造成由板底开裂向上扩展形成的裂缝,以及板底脱空现象,进而导致断板等严重病害,这些缺点严重影响了混凝土路面(道面)面层材料的耐久性和使用寿命,因此改善水泥混凝土路面(道面)材料的性能,尤其是抗弯拉性能显得尤为重要。实际水泥混凝土路面(道面)在车辆荷载(飞机荷载)作用下,由于水泥混凝土为脆性材料,抗压模量高,而抗拉强度远低于抗压强度,所以首要考虑水平拉应力的影响。荷载作用下路面(道面)面层内水平应力状况可以简述为:上部区域受高压应力、中部区域为应力过渡区域、下部区域受高拉应力,从上至下为最大水平压应力到最大水平拉应力逐渐过渡,尤其是在底部对混凝土的抗拉性能要求最高。然而普通的混凝土由于施工时为均匀拌和,可以视为均质的材料,其各个位置的力学性能基本一致,水泥混凝土板力学性能沿着板厚方向是无变化的,这并不符合路面(道面)面层内部的实际应力分布的特点,尤其是抗拉强度沿厚度方向一致,在实际荷载作用下水泥混凝土板板底处产生的最大拉应力易超过抗拉强度而产生裂缝而破坏。另外,普通水泥混凝土为脆性材料,变形能力较差,其弹性模量远高于基层(如水泥稳定粒料),因而两者之间的变形协调能力较差,致使混凝土板板底容易因脱空而产生过大的弯拉应力,进而导致开裂破坏。所以,对路面(道面)面层结构的性能改善使其力学性能能够渐变,更为契合混凝土路面(道面)面层的实际受力状况,并且降低混凝土路面(道面)面层底部的模量并增强其变形性能,使其与基层具有良好的变形协调能力,以满足路面(道面)的使用要求具有重要研究意义。技术实现要素:技术问题:本发明实施例所要解决的技术问题是:提供一种道路路面或机场道面铺装结构的制备方法,能够制备出性能梯度分布的铺装结构。技术方案:为解决上述技术问题,本发明实施例采用如下的技术方案:一种上述的道路路面或机场道面铺装结构的制备方法,该制备方法包括以下步骤:s10:在混凝土搅拌筒中,加入粗集料、细集料和水泥,形成混合物;干拌混合物,使得各组分混合均匀;s20:向混合物中加入水、减水剂和消泡剂,然后搅拌,形成混凝土拌合物;s30:向步骤s20制备的混凝土拌合物中加入纤维,搅拌均匀,得到纤维混凝土拌合物;s40:将步骤s30制备的纤维混凝土拌合物和促凝早强剂加入离心机的管模中,运行离心机,使纤维混凝土拌合物沿管模内壁均匀分布,且内部形成空腔;然后逐步提高转速,增大离心力,在离心机中逐渐形成铺装结构的粗集料层、粗细集料过渡层、细集料层和纤维层,制备出管状的新拌铺装结构;s50:管状的新拌铺装结构初凝后,拆卸管模,将管状的新拌铺装结构取出并摊平,形成矩形状;s60:矩形状的新拌铺装结构终凝后,将履带从新拌铺装结构上拆卸,对新拌铺装结构养护,从而制成铺装结构预制块。作为优选例,所述的步骤s10中,搅拌筒的转速为60~100r/min,干拌时间为2~3min。作为优选例,所述的步骤s20中,搅拌筒的转速为60~100r/min,搅拌时间8~10min。作为优选例,所述的步骤s30中,搅拌筒的转速为150~240r/min,搅拌时间为16~20min;所述的纤维的密度为1.2~1.6g/cm3,拉伸强度大于1000mpa。作为优选例,所述的步骤s40中,在管模内壁固定一层履带,并在履带的表面涂刷隔离剂;履带内表面设有平行于履带宽度方向的凸起条纹,相邻条纹间距不相等。作为优选例,所述的步骤s40中,离心机的起始转速为45~60r/min,运行时间为3~5min,使纤维混凝土拌合物沿管模内壁均匀分布,且内部形成空腔。作为优选例,所述的步骤s40中,逐步提高转速是指:先逐渐提升转速至130~140r/min,并维持5~7min,在最外侧形成粗集料层;然后逐渐提升转速至160~180r/min,并维持8~10min,在粗集料层内侧逐渐形成粗细集料过渡层和细集料层;最后逐渐提升转速至200~215r/min,并维持6~9min,在细集料层内侧形成纤维层。作为优选例,所述的步骤s50中,初凝时间为80~90min;所述的步骤s60中,终凝时间为270~285min,所述的养护是对铺装结构覆盖塑料薄膜进行养护,养护时间为28天。有益效果:与现有技术相比,本发明实施例具有以下有益效果:第一、本发明采用离心法制备性能梯度分布的铺装结构,能充分实现材料的组成成分沿着厚度方向由一侧到另一侧呈梯度逐渐变化,从而实现该材料的力学性能沿着厚度方向渐变,主要表现为:在厚度方向上,抗压强度从铺装结构底面到表面逐渐增大,而抗拉强度相反,从表面到底面逐渐增大。第二、与上下表面力学性能一致的素混凝土板相比,本实施例的铺装结构的力学性能沿着厚度方向渐变,更加符合混凝土路面(道面)面层在实际轮载作用下所受应力渐变的状况,即表面受最大水平压应力,底面受最大水平拉应力,中间应力连续过渡。铺装结构的力学性能梯度分布符合层位设计要求。第三、本实施例的铺装结构表面的粗集料层因为富集抗压性能优越的粗集料,所以具有优良的抗压性能和耐磨性能;中间的粗细集料过渡层及细集料层的级配密实,能使荷载作用下产生的应力良好过渡;下部区域的纤维层,由于富集了大量高强纤维,所以大大提高了铺装结构的抗弯拉强度和极限拉伸应变,能有效抵抗路面(道面)底部拉应力、应变,抵抗疲劳开裂破坏,同时纤维的梯度分布大大节约了纤维的用量,显著降低了成本。第四、本实施例的铺装结构的纤维层中添加的高强纤维,使混合料具备良好的拉伸变形能力,并且添加促凝早强剂控制其凝结时间,利用水泥混凝土初凝时间前的良好的塑性变形能力,通过履带将管状的试件取出并摊平成矩形混凝土预制板。第五、本实施例的铺装结构在成型时即具有优良的抗滑构造,满足道路路面(机场道面)使用的抗滑要求。由于用于取出试件的履带内表面设有不等间距的凸起纹理,使得到的铺装结构表面在脱模成型时即具备合理的宏观抗滑纹理,从而赋予混凝土板表面优越的抗滑性能、散光防眩性能及排水性能,相比于普通混凝土表面抗滑纹理的二次加工方法(拉毛、刻槽等),本方法方便快捷、节省人力物力;第六,本方明制备的铺装结构为预制块,可在在室内批量成型,质量可控,运输至施工现场后可快速铺筑,施工快捷。附图说明图1是本发明实施例中铺装结构摊平后的剖面图;图2是本发明实施例中制备方法的流程图;图3是本发明实施例中管模片和隔离块的装配图;图4是本发明实施例中管模的结构图;图5是本发明实施例中,试件在管模中成型的结构图;图6是本发明实施例中,试件从管模中取出的结构图;图7是本发明实施例中,试件的抗拉强度随深度变化的趋势图;图8是本发明实施例中,试件的抗压强度随深度变化的趋势图。图中有:粗集料层1、粗细集料过渡层2、细集料层3、纤维层4、管模片5、隔离块6、履带7、试件8、第一管模片501、第二管模片502、第三管模片503、铰接螺栓504和铰接螺栓505。具体实施方式下面结合附图,对本发明的技术方案进行详细的说明。如图1所示,本发明的一个实施例提供一种道路路面或机场道面铺装结构,包括以下组分:粗集料、细集料、水泥、水、纤维、减水剂、促凝早强剂和消泡剂,组成比例为:按重量计,粗集料60~65份,细集料39~43份,水泥25~28份,水11~13份,减水剂0.5~0.6份,促凝早强剂0.012~0.016份,消泡剂0.05~0.06份,纤维体积占铺装结构总体积的0.60%~0.85%。该铺装结构包括从顶面到底面依次设置的粗集料层1、粗细集料过渡层2、细集料层3和纤维层4,其中,粗集料层1包括粗集料、细集料、纤维、水泥和水;在粗集料层1中,粗集料的体积含量介于52%~60%,细集料的体积含量介于10%~13%;粗细集料过渡层2包括粗集料、细集料、纤维、水泥和水;在粗细集料过渡层2中,粗集料的体积含量介于39%~45%,细集料的体积含量介于25%~30%;细集料层3包括细集料、纤维、水泥和水;在细集料层3中,细集料的体积含量介于50%~55%,纤维在在细集料层3的体积含量占纤维总体积含量的17%~22%;纤维层4包括纤维、细集料、水泥和水;在纤维层4中,细集料的体积含量介于36%~40%,纤维在纤维层4的体积含量占纤维总体积含量的50%~55%;粗集料和细集料组成的集料的平均粒径沿着厚度方向从粗集料层1顶面到纤维层4底面呈梯度逐渐减小;从粗集料层1的顶面到粗细集料过渡层2的底面,粗集料的体积含量呈梯度逐渐减小;从粗集料层1的顶面到细集料层3的底面,细集料的体积含量呈梯度逐渐增大;从粗集料层1的顶面到纤维层4的底面,纤维的体积含量呈梯度逐渐增大。荷载作用下混凝土板内水平应力状况可以简述为:上部区域受高压应力、中部区域为应力过渡区域、下部区域受高拉应力,从上至下为最大水平压应力到最大水平拉应力逐渐过渡,尤其是在板底部位对混凝土的抗拉性能要求最高。然而普通的混凝土由于施工时为均匀拌和,可以视为均质的材料,其各个位置的力学性能基本一致,水泥混凝土面板力学性能沿着板厚方向是无变化的,这并不符合水泥混凝土板内部实际应力分布的特点,尤其是抗拉强度沿厚度方向一致,在实际荷载作用下板底处产生的最大拉应力易超过抗拉强度而导致混凝土板裂缝而破坏。本发明实施例的铺装结构,其在厚度方向上力学性能表现为:上部抗压性能优越,下部抗拉性能优越,并且抗压强度从底面到顶面逐渐增大,抗拉强度从顶面到底面逐渐增大,以适应水泥混凝土板水平应力沿板厚方向的渐变分布的规律,位于上部的粗集料层因为富集抗压性能优越的粗集料,所以具有优良的抗压性能;位于中部的粗细集料过渡层和细集料层的级配密实,能实现荷载作用产生的应力良好过渡;位于下部的纤维层,由于富集了大量高强纤维,所以大大提高了混凝土板的抗弯拉强度和板底部位的极限拉伸应变,能有效抵抗混凝土面板下的拉应力、应变,抵抗疲劳开裂破坏。如图2所示,本发明的另一实施例提供上述道路路面或机场道面铺装结构的制备方法,该制备方法包括以下步骤:s10:在混凝土搅拌筒中,加入粗集料、细集料和水泥,形成混合物;干拌混合物,使得各组分混合均匀。所述的粗集料和细集料的级配进行了设计和控制,粗集料采用的级配范围是:方筛孔尺寸(mm)31.5、26.5、19、16、9.5、4.75和2.36,对应的累计筛余量(%)分别为2~3、25~30、45~55、60~70、80~85、93~97和97~98;细集料采用的级配范围是:方筛孔尺寸(mm)4.75、2.36、1.18、0.6、0.3和0.15,对应的累计筛余量(%)分别为2~5、15~21、42~48、62~67、79~83和94~97。干拌时搅拌筒的转速为60~100r/min,干拌时间为2~3min。s20:向混合物中加入水、减水剂和消泡剂,然后搅拌,形成混凝土拌合物。搅拌筒的转速为60~100r/min,搅拌时间8~10min。s30:向步骤20制备的混凝土拌合物中加入纤维,搅拌均匀,得到纤维混凝土拌合物。搅拌筒的转速为150~240r/min,搅拌时间为16~20min;所述的纤维的密度为1.2~1.6g/cm3,拉伸强度大于1000mpa。s40:将步骤30制备的纤维混凝土拌合物和促凝早强剂加入离心机的管模中,运行离心机,使纤维混凝土拌合物沿管模内壁均匀分布,且内部形成空腔;然后逐步提高转速,增大离心力,在离心机中逐渐形成铺装结构的粗集料层(1)、粗细集料过渡层(2)、细集料层(3)和纤维层(4),制备出管状的新拌铺装结构。加入拌合物前,在管模内壁固定一层履带,并在履带的表面涂刷隔离剂;履带内表面设有平行于履带宽度方向的凸起条纹,相邻条纹间距不相等,用于形成良好的表面抗滑纹理。凸起条纹的截面为矩形,宽度为3~5mm,高度为4~6mm。由于横向等间距刻槽路面易产生峰值噪声,刺激人耳,所以履带表面的凸起纹理按不等间距布置,提升抗滑性能的同时能有效降低噪音的产生。离心机的起始转速为45~60r/min,运行时间为3~5min,使纤维混凝土拌合物沿管模内壁均匀分布,且内部形成空腔。在步骤s40中,提高转速是指:先逐渐提升转速至130~140r/min,并维持5~7min,在最外侧形成粗集料层;然后逐渐提升转速至160~180r/min,并维持8~10min,在粗集料层内侧逐渐形成粗细集料过渡层和细集料层;最后逐渐提升转速至200~215r/min,并维持6~9min,在细集料层内侧形成纤维层,从而得到新拌铺装结构。s50:管状的新拌铺装结构初凝后,拆卸管模,将管状的新拌铺装结构取出并摊平,形成矩形状的新拌铺装结构。初凝时间为80~90min;s60:矩形状的新拌铺装结构终凝后,终凝时间为270~285minmin,将履带从新拌铺装结构上拆卸,对新拌铺装结构养护,从而制成铺装结构预制块。养护是对新拌铺装结构覆盖塑料薄膜进行养护,养护时间为28天。本发明实施例通过结构、材料的设计和转速的控制,使离心法可用于制备路面(道面)铺装结构。另外,通过添加促凝早强剂对混凝土材料的硬化性能的控制和改良材料组分所带来的变形性能的提高,使离心法制备的几何形状为管状的新拌铺装结构能够摊铺展平,制备出几何形状为矩形的铺装结构预制块。同时对混凝土离心装置作特殊设计,即在内壁附上特殊设计的履带,既方便管状铺装结构从离心机中取出并摊铺展平,又可通过对履带表面作特殊的纹理设计赋予铺装结构表面优越的抗滑性能。为了提高离心机内管状新拌铺装结构的拉伸变形能力以及制备出的铺装结构预制块的抗弯拉强度,通过改良它的材料组分——添加纤维赋予其高延性。由于纤维具有的超高韧性,能够很好地解决传统混凝土材料易脆性、弱拉伸性、裂缝宽度无法控制等种种缺陷。加入适量高强纤维离心制备管状铺装结构时利用离心力的作用,可以使纤维呈梯度分布,在管状混凝土内侧区域富集,在最内侧形成一个纤维含量达到总纤维含量50%以上的纤维层,纤维层具有较高的抗拉强度、优越的拉伸变形能力和控制裂缝开展的能力,大幅改善了铺装结构预制块的抵抗底部拉应力和拉应变的能力,从而抵抗开裂破坏,大幅提高路面(道面)面层的使用寿命,同时纤维集中分布底部区域大大节约了纤维的用量,显著降低了造价。本发明制备的铺装结构预制块在成型时即表面具有优越的抗滑性能、散光防眩性能、耐磨性能及排水性能,而无需二次加工处理,直接制备、方便快捷。水泥混凝土面板具有抗滑的要求,传统的素混凝土面板进行抗滑构造处理时一般采用拉毛法、压槽法、刻槽法、露石法等方法,存在需要二次加工、消耗人力成本、施工质量要求高的缺点。其中压槽和拉槽都是在新浇混凝土表面上通过一定的附加外力完成的,所制作的沟槽存在明显的不均匀现象。同时,由于拉压槽时对表面砂浆的推挤作用,纹理深度不均匀,还易出现局部翻砂现象,影响混凝土表面平整度;而刻槽法和露石法需要专用设备和材料,所需成本高。本发明实施例在履带内表面设有平行于履带宽度方向的凸起条纹,凸起条纹的截面为矩形,宽度为3~5mm,高度为4~6mm,使铺装结构在成型时即具备良好的表面抗滑纹理而无需二次加工。同时,由于横向等间距刻槽路面易产生峰值噪声,刺激人耳,所以履带表面的凸起纹理按不等间距布置,如间距依次为:19、25、23、25、19、22、25、22、17、25、26、32、28、22、25、20、25,单位:mm,提升抗滑性能的同时能有效降低噪音的产生。本实施例的制备方法利用离心力作用使拌合物密实,并使材料组成成分沿厚度方向梯度逐渐变化,从而使其力学性能也沿厚度方向梯度逐渐变化,并且内部没有明显的界面,各个功能梯度层位的力学性能契合实际情况下路面(道面)面层所受应力渐变的情况。混凝土拌合物中水泥、粗集料、细集料、纤维等各种组分在离心机中在作圆周运动时所产生的离心力,是和材料的质量、角速度的二次方、旋转半径成正比的,计算式为:f=mω2r=ρvω2r式中:f表示材料受到的离心力;m表示材料的质量;ω表示材料作圆周运动的角速度;r表示材料的旋转半径;ρ表示材料密度;v表示材料体积。由于拌合物中水泥、粗集料、细集料、纤维等多种材料的体积、密度不同,即使旋转速度和旋转半径相同,各自的离心力也相差很大。在流动度较大的混凝土拌合物中,根据胶浆理论,可以分为三级,粗分散系:以粗集料为分散相,悬浮在纤维砂浆介质中,细分散系:以细集料为分散相,悬浮在纤维水泥浆介质中,微分散系:以纤维为分散相,悬浮在水泥浆介质中,而水泥颗粒是悬浮在水内。离心机钢模快速旋转时,水泥胶浆混合物中的各种成分由于体积和密度不同,所受离心力的相差悬殊,在旋转过程中相互之间就会发生相对位移,总体表现为:粒径和密度越大的成分所受离心力越大,倾向于向外移动,而粒径和密度越小的成分所受离心力越小,则倾向于相对向内移动。离心过程中各种成分之间的嵌挤和摩阻作用以及细料对空隙的填充作用,最终与离心作用力达到平衡后,则得到平均粒径由外而内逐渐减小的密实型铺装结构。具体梯度形成的原理为:形成空腔后初步提高转速,粗集料颗粒由于体积最大,所受的离心力最大,因此开始逐步外移,移向管模模壁,与少部分细集料、水泥和纤维达到稳定后组成紧密的骨架密实结构,从而在离心机最外侧形成一个成分以粗集料为主的粗集料层;接着提高离心机的转速即增大离心力,粗集料层(粗集料为主,含少量细集料)由于骨架嵌挤、内摩阻力较大,其组分相对稳定,而其余的细集料则进一步发生相对位移,在粗集料层内侧与剩余的粗集料混合形成粗细集料过渡层,并逐渐密实稳定;随着离心时间的延长,又有部分细集料在离心作用下与水泥纤维混合密实,逐渐达到稳定,在粗细集料过渡层内侧形成一层成分以细集料为主的细集料层;纤维的密度最低,且较水略大,所受离心作用要小于集料,所以在整个离心过程中会逐步相对向内侧移动,最终在内侧聚集大量的纤维,增大离心力后与剩余的细集料和水泥达到密实稳定,在最内侧形成纤维含量较高的纤维层。最终得到集料的平均粒径和体积含量沿厚度方向逐渐过渡,且表面抗滑、耐磨和抗压性能优良及底层抗拉性能优越的铺装结构预制块。在离心机中旋转成型时,转速控制及其作用如下:(1)起始转速为45~60r/min,时间为3~5min,使拌合物沿模板内壁均匀分布,内部形成空腔;(2)接着逐渐将转速提升至130~140r/min,并维持5~7min,使粗分散系中的分散相——粗集料从水泥浆介质中逐渐分离外移,组成紧密的粗集料骨架,粗集料的体积含量介于52%~60%,同时细集料、水泥和纤维填充粗集料的骨架空隙,形成骨架密实结构,在最外侧形成主要成分为粗集料的粗集料层。同时在离心过程中部分细料(细集料、水泥和纤维)向内侧移动;(3)然后逐渐将转速提升至160~180r/min,并维持8~10min,离心力的增大使剩余的粗集料继续向外侧移动,在粗集料层内侧聚集,与部分细集料混合形成粗细集料过渡层,其中粗集料的体积含量介于39%~45%,细集料的体积含量介于25%~30%;旋转过程中细分散系中的分散相——细集料从水泥浆介质中进一步分离相对内移,随着离心时间的延长,细集料在粗细集料过渡层内侧聚集并与水泥和纤维混合达到密实稳定,形成以细集料为主要成分的细集料层,其中细集料的体积含量介于50%~55%。粗细集料过渡层和细集料层为悬浮密实结构,同时纤维的体积含量逐渐增大,能实现压应力和拉应力的良好过渡。同时在离心过程中部分水泥和纤维继续相对向内侧移动;(4)最后逐渐将转速在提升至200~215r/min,并维持6~9min,使微分散系中的分散相——纤维从水泥浆介质中进一步分离相对内移,并与剩余的细集料和水泥混合逐渐达到密实稳定,形成纤维含量较高的纤维层,并成型密实的梯度分布水泥混凝土铺装结构。纤维层中纤维的含量占总纤维含量的50%~55%,占本层的体积含量达到3%左右,较高的纤维含量赋予了铺装结构底层良好的抗拉性能和耐疲劳性能,有效抵抗疲劳开裂破坏。如图3至图5所示,上述制备方法中采用的管模,包括至少3个管模片5、隔离块6和履带7,相邻管模片5之间活动连接,且隔离块6位于两个管模片5之间,隔离块6分别与相邻的管模片5固定连接,管模片5和隔离块6形成一环形体;履带7固定连接在管模片5的内壁上,离心机中隔离块6内表面与履带7内表面之间的距离大于管状的新拌铺装结构的厚度。以3个管模片5的离心机为例,管模片包括第一管模片501、第二管模片502和第三管模片503,其安装过程如下:(1)首先将管模片之间的铰接螺栓504和铰接螺栓505旋松,将第一管模片501和第三管模片503展开,然后通过螺栓将履带7固定在第二管模片502上;(2)接着将第一管模片501和第三管模片503合拢,并继续将履带7固定在第一管模片501和第三管模片503上,使履带与管模壁紧密贴合,从而得到带有缺口的圆环形管模;(3)将隔离块6组装到管模的缺口上,组装分为两步:第一步是将履带7的两个端部装入隔离块6两侧的预留槽将其固定;第二步是将隔离块6与管模片之间的固定螺栓旋紧,以固定隔离块6,从而得到用于成型试件8的管模。使用管模时,从离心机管模两侧加入混凝土拌合物原料,最后用封盖封闭管模两端,即可开始离心旋转,成型试件8。当试件8成型后,从离心机上取出管模,首先拆卸固定履带7的螺栓,然后将三个管模片之间的铰接螺栓旋松,并拆卸连接隔离块6与管模片的螺栓,解除隔离块对履带两个端部的锁定,移除隔离块,将履带的两个端部夹住,然后将第一管模片501和第三管模片503同时逐渐向两侧展开,展开的同时将履带7展开、提起并摊平,将试件8展平后,终凝后拆除履带,在标准条件(温度为20±2℃,相对湿度为95%)下养护28天。下面例举一实例。一种路面或道面铺装结构,采用的原材料包括:玄武岩碎石(即粗集料,其级配范围见表1)、石英砂(即细集料,其级配范围见表2)、硅酸盐水泥(42.5r)、pva纤维(长度20mm,直径50μm,密度1.3g/cm3,拉伸强度1200mpa)、水、聚羧酸高效减水剂、促凝早强剂及消泡剂。表1粗集料级配范围方筛孔尺寸(mm)31.526.519169.54.752.36累计筛余量(%)2.527.5506582.59597.5表2细集料级配范围方筛孔尺寸(mm)4.752.361.180.60.30.15累计筛余量(%)31845658195各组分的质量比为:粗集料∶细集料∶硅酸盐水泥∶水∶聚羧酸高效减水剂∶促凝早强剂∶消泡剂=3∶1.5∶1∶0.6∶0.01∶0.0008∶0.002;纤维体积占混合料总体积的0.75%。制备路面和道面铺装结构的步骤如下:步骤10:在混凝土搅拌筒中,加入粗集料、细集料和水泥,形成混合物;以90r/min的速率搅拌3分钟,使得各组分混合均匀。步骤20:向混合物中加入水、减水剂和消泡剂,然后以90r/min搅拌8分钟,形成混凝土拌合物。步骤30:向步骤20制备的浆体中加入pva纤维,以180r/min搅拌16分钟,形成纤维混凝土拌合物。步骤40:将步骤30制备的纤维混凝土拌合物和促凝早强剂加入离心机的管模中,以起始转速为50r/min运行离心机,运行时间为3~5min,使纤维混凝土拌合物沿管模内壁均匀分布,且内部形成空腔;然后逐渐将转速提升至140r/min,并维持6min,然后逐渐将转速提升至170r/min,并维持9min;最后逐渐将转速提升至210r/min,并维持8min,制备出管状的新拌铺装结构。步骤50:管状的新拌铺装结构初凝后,拆卸管模,将管状的新拌铺装结构取出并摊平,形成矩形状的新拌铺装结构;步骤60:管状的新拌铺装结构终凝后,将履带从新拌铺装结构上拆卸,对新拌铺装结构养护,从而制成铺装结构预制块。对比例1:采用上述实例1的材料,按同样的配比,但不含pva纤维,以现有的普通搅拌方法即均匀拌合方法,浇筑一块等厚度的混凝土板。对比例2采用上述实例1的材料,按同样的配比,含pva纤维,以现有的普通搅拌方法即均匀拌合方法,浇筑一块等厚度的混凝土板。将实例1、对比例1和对比例2得到的样品放置于同一养护室,在温度为20±2℃,相对湿度为95%的条件下,养护28天。下面对实例1、对比例1和对比例2制备的三块样品进行抗压强度和抗弯拉强度试验。养护结束后,将三块样品切割成小梁试件(每块3个,共9个)、立方体试件(每块3个,共9个),分别进行四点弯曲试验、抗压强度试验,取平均值进行计算和比较。试件要保留厚度方向上所有层位,试件实际尺寸见表3。试验结果如表4所示。表3试件尺寸试件小梁试件立方体试件试件尺寸(mm)195×195×750195×195×195表4抗弯拉、立方体抗压强度试验结果抗弯拉强度比较:表4的试验数据表明,实例1的抗弯拉强度比未掺纤维的普通混凝土(即对比例1)高40.0%,比掺纤维的混凝土(即对比例2)高14.8%。实例1的极限挠度比对比例2高14.3%,由于对比例1中没有纤维的增强约束作用,所以挠度则比实例1和对比例2低得多。实验结果说明:纤维在实例1中的抗弯拉性能起到了很好的增强效果,表现为抗弯拉强度和韧性(变形能力)相对于素混凝土(即对比例1)得到极大提升,同时相同纤维含量下,与均匀拌合的纤维混凝土(即对比例2)相比也有一定幅度的提升。这是因为实例1可使纤维梯度分布,使其在铺装结构底部受拉部位分布率最高,从而提高了抗弯拉强度以及纤维的利用率,进而起到节约纤维用量的作用,具有良好的工程效益。抗压强度比较:实例1的抗压强度值较普通方法制备的混凝土有一定的增加,约比素混凝土(即对比例2)增加6%。可见,虽然梯度分布从一定程度上降低了粗集料的嵌挤作用,但离心作用使铺装结构变得更加密实,加上纤维的约束增强作用使铺装结构的抗压强度得到一定增强。虽然抗压强度增强并不明显,但其抗弯性能得到很大提高,而这正是我们实际使用中需要的材料性能。对实例1的试件进行抗滑能力测定,分别测定构造深度和摆值。试验结果如表5所示。表5抗滑试验结果抗滑指标指标值构造深度(mm)1.02摆值68抗滑试验结果表明:采用本发明制备的实例1由于表面具备规则纹理,所以表面具有优越的抗滑性能,构造深度达到1.02,远高于抗滑技术指标值0.55,摆值(摩擦系数)达68,高于抗滑技术指标值59。对上述实例的铺装结构材料的抗拉强度随深度变化进行测试。测试方法:将实例1的铺装结构试件样品在厚度方向上不同深度范围内切割为6个3cm×3cm×20cm小梁试件,截取的6个深度范围分别为:0~3cm、4~7cm、7~10cm、10.5~13.5cm,13.5~16.5cm,16.5~19.5cm,每个深度范围各取3个小梁试件,得到6组小梁试件。分别测量6组试件的抗拉强度并取平均值代表各组试件的抗拉强度,以这6个抗拉强度值近似表示样品在深度1.5cm、5.5cm、8.5cm、12cm、15cm、18cm处的抗拉强度。并绘制抗拉强度随深度变化的趋势图。结果如图7所示。图7中,横坐标表示抗拉强度,纵坐标表示试件的深度,以试件的顶面为基准面,即试件顶面的深度为零。从该图可以看出上述实例的铺装混凝土板,其抗拉强度随高度呈现出梯度变化的趋势,即抗拉强度由顶面到底面逐渐增大,证明材料抗拉性能具备梯度分布的特性。在底部的抗拉强度最大,底部小梁试件抗拉强度达到2.68mpa,相比于普通混凝土抗拉强度(约为1.75mpa)要大53%左右,有效增强了材料在实际应用时抵抗拉应力和拉应变的能力。对上述实例的铺装结构材料的抗压强度随深度变化进行测试。测试方法:将实例1的铺装结构试件样品在厚度方向上不同深度范围内切割为5个4cm×4cm×4cm立方体抗压强度试件,截取的5个深度范围分别为:0~4cm、4~8cm、8~12cm、12~16cm,15.5~19.5cm每个深度范围各取3个立方体试件,得到5组立方体试件。分别测量5组试件的抗压强度并取平均值代表各组试件的抗压强度,以这5个抗拉强度值近似表示样品在深度2cm、6cm、10cm、14cm、17.5cm处的抗压强度。并绘制抗压强度随深度变化的趋势图。结果如图8所示。图8中,横坐标表示抗压强度,纵坐标表示试件的深度,以试件的顶面为基准面,即试件顶面的深度为零。从该图可以看出:上述实例的铺装混凝土板的抗压强度随高度呈现出梯度变化的趋势,即抗压强度由试件的底面到顶面逐渐增大,证明材料抗压性能具备梯度分布的特性。顶部的抗压强度有一定增大,抗压强度达到51.7mpa,相比于普通混凝土顶部的抗压强度(约为45.84mpa)要大13%左右,在保证混凝土整体抗压性能的前提下,局部增强了顶部区域的抗压性能,更加适应实际情况下道路路面和机场道面的受力特征。当前第1页12