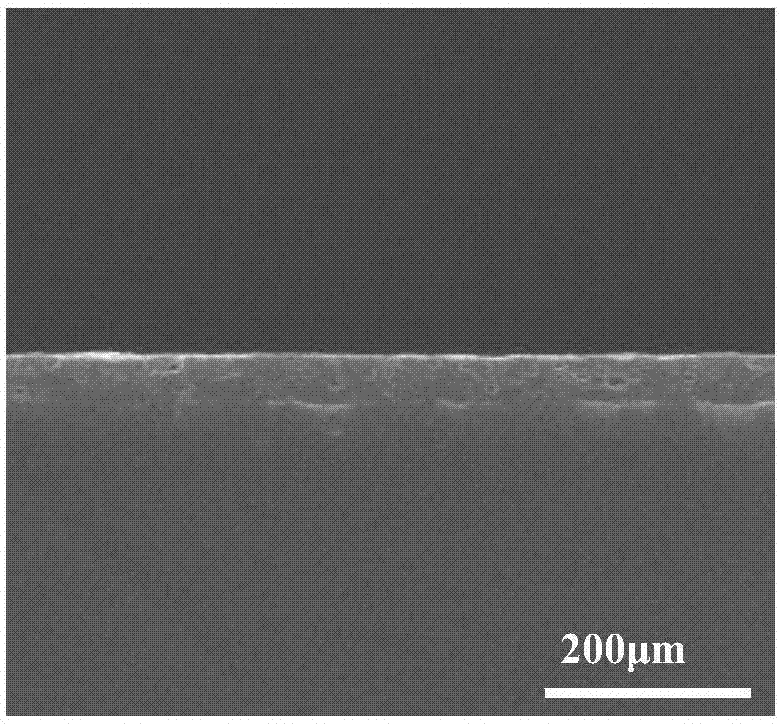
本发明涉及一种粉料、其制备方法及应用,尤其是一种玻璃粉料、其制备方法及应用。
背景技术:
:在多层陶瓷电子元器件领域,不同材质材料之间的异质共烧是研发制备高性能元器件的关键科学技术问题,要求异质材料之间结合紧密,界面平整,无显著的异质层互扩散、分层以及开裂、脱落等现象。传统的氧化铝绝缘层与ysz氧化锆(钇稳定氧化锆)基体在高温异质共烧过程中,由于二者材料烧结收缩不匹配,易导致氧化铝/氧化锆陶瓷在共烧完成后出现界面分层、外观翘曲变形等缺陷,影响产品尺寸精度,并且在应用时易出现断裂、缺损等现象。为了改善氧化铝/氧化锆共烧失配现象,行业内常采取添加低熔点氧化物,改善产品结构设计或采用特殊制备工艺等多重手段,调控al2o3和zro2的共烧收缩行为,实现两者的共烧匹配。例如,同济大学的张容榕等人采用溶剂热法制备纳米级ysz粉体,同时,在al2o3中添加cao、mgo和sio2等混合烧结助剂,降低al2o3的烧结温度;在此基础上,调整粉体中α相与γ相的比例改变其烧结收缩率,最终实现al2o3与ysz陶瓷在1400℃范围内的匹配共烧。华中科技大学的王晓昳等人通过改变生坯装载量和添加烧结助剂的方法,增大al2o3的烧结收缩率,同时采用增加ysz过渡层和压力限制烧结等手段,降低al2o3与氧化锆陶瓷的烧结失配,得到了翘曲变形小,微观无分层的多层异质陶瓷。目前,现有的氧化铝/氧化锆共烧匹配解决技术手段,成本高,工艺复杂,并且不利于实现批量化制备。技术实现要素:基于此,本发明的目的在于克服上述现有技术的不足之处而提供一种玻璃粉料,所述玻璃粉料可应用于氧化铝粉料中,降低其烧结温度,从而使其与氧化锆更好的形成共烧。为实现上述目的,本发明所采取的技术方案为:一种玻璃粉料,包括以下质量百分含量的成分:二氧化硅20~60%、氧化钙8~16%、氧化钡8~16%、氧化铝14~28%。本发明所述玻璃粉料中各成分共同作用,能起到较好的降低烧结温度的效果,其中,sio2是玻璃网络形成体氧化物,为玻璃的主体架构成分,具有高熔点、高粘度、低热膨胀系数和高的化学稳定性;cao为玻璃外体离子氧化物,具有强的极化性,能够减弱玻璃中硅氧键之间作用力,降低玻璃的高温粘度,降低玻璃熔点,主要起助熔作用;bao为玻璃外体离子氧化物,能有效降低玻璃熔点,主要起助熔作用;al2o3为玻璃中间体氧化物,有助于连接玻璃的网络结构,增加玻璃粘度和机械强度,提高玻璃熔点。优选地,所述玻璃粉料还包括氧化镁,所述氧化镁在所述玻璃粉料中的质量百分含量为8~16%。mgo在玻璃中常作为网络外体离子氧化物引入,能够降低玻璃析晶倾向,降低玻璃的粘度和熔点,增强玻璃的高温流动性。优选地,所述玻璃粉料还包含氧化钛,所述氧化钛在所述玻璃粉料中的质量百分含量为1~2%。tio2在玻璃中作为成核剂氧化物引入,少量添加时,能够以异质成核的形式促进玻璃的晶化,提高玻璃的机械强度和绝缘特性。优选地,所述玻璃粉料还包含氧化锆,所述氧化锆在所述玻璃粉料中的质量百分含量为1~2%。zro2在玻璃中作为成核剂氧化物引入,少量添加时,能够以异质成核的形式促进玻璃的晶化,提高玻璃的机械强度和绝缘特性。优选地,所述二氧化硅、氧化铝、氧化钙、氧化镁、氧化钡、氧化钛、氧化锆的粒径均不大于15μm,纯度均为分析纯;所述氧化钛的粒径不大于10μm,纯度均为分析纯;所述氧化锆的粒径不大于1μm,纯度均为分析纯。同时,本发明还提供一种所述玻璃粉料的制备方法,包括如下步骤:(1)将玻璃粉料中的各成分混合、球磨、烘干、粉碎,得到粉料;(2)将步骤(1)所得粉料在空气气氛下,加热到1350~1450℃,保温,再降温至1160~1220℃,将降温后的粉料进行水淬,然后将水淬后的粉料进行过筛、退火处理,即得到本发明所述玻璃粉料。优选地,所述步骤(2)中,以2~8℃/min的升温速率加热到1350~1450℃,保温2~6小时,再以1~3℃/min速率降温至1160~1220℃。优选地,所述步骤(1)中,球磨的过程为:以无水乙醇为球磨介质,将所述玻璃粉料各成分加入球磨罐中,球磨8~16小时。优选地,所述步骤(1)中,烘干的过程为:将球磨后的粉料在100℃烘干10小时。优选地,所述步骤(2)中,过筛的过程为:将水淬后的粉料过200目筛网。优选地,所述步骤(2)中,退火处理的过程为:将过筛后的粉料在500~600℃退火处理6小时。此外,本发明还提供一种包含所述玻璃粉料的氧化铝粉料。本发明氧化铝粉料,由于添加了玻璃料,使其烧结温度降低,能与氧化锆更好的形成共烧。优选地,在所述氧化铝粉料中,所述氧化铝粉的质量百分含量为95~98%,所述玻璃粉料的质量百分含量为2~5%。在混合体系中,氧化铝为功能相,与粉料的电学性能、机械性能密切相关;氧化铝含量过高会导致粉料烧结温度提高,氧化铝含量降低,则会恶化材料性能,比如使材料的绝缘电阻率降低,热膨胀系数增大,抗折强度降低,因此选择氧化铝含量为95~98%;玻璃组分主要起助熔、降低烧结温度和增加陶瓷层见结合力的作用,然而含量过高时会恶化材料性能,因此含量为2~5%。优选地,所述氧化铝粉的粒径不大于1μm,纯度为分析纯。同时,本发明还提供一种上述氧化铝粉料的制备方法,所述方法为:将氧化铝粉和玻璃粉球磨、烘干、过筛,得到所述氧化铝粉料。此外,值得注意的是,上述球磨、烘干、过筛的过程可以为本发明上文记载的过程,本领域技术人员也可以根据实际需要进行常规选择,本发明对此并没有特别的限定。再次,本发明还提供一种包含所述氧化铝粉料的氧化铝浆料。所述氧化铝浆料可以很好的与氧化锆实现共烧。优选地,所述氧化铝浆料包括以下重量份的成分:氧化铝粉料100份、乙醇30~40份、三乙醇胺20~35份、聚乙烯醇缩丁醛10~15份、邻苯二甲酸丁苄酯3~6份。同样,本发明还提供一种上述氧化铝浆料的制备方法,包括如下步骤:在球磨机中加入乙醇、三乙醇胺,球磨15~30min后,再向球磨机中加入氧化铝粉料、聚乙烯醇缩丁醛、邻苯二甲酸丁苄酯,球磨8~16小时,得到所述氧化铝浆料。由该方法制备的氧化铝浆,工艺简单,可用于实现氧化锆与氧化铝陶瓷的匹配共烧,共烧陶瓷结合紧密、界面平整、外观无翘曲变形。本发明还提供一种所述氧化铝粉料在制备氧化锆与氧化铝共烧用氧化铝浆料中的应用。相对于现有技术,本发明的有益效果为:本发明所述玻璃粉料可应用于氧化铝粉料中,降低其烧结温度,从而使其与氧化锆更好的形成共烧。本发明所制备的氧化锆与氧化铝匹配共烧用氧化铝粉料,烧结过程中由于熔融玻璃粉的流动性,促进了陶瓷的液相烧结,熔融玻璃的钎合作用有助于在锆铝界面形成具有高结合力的致密层,可显著增强共烧陶瓷的抗弯强度。与现有的氧化锆/氧化铝共烧用氧化铝浆料相比,本发明氧化铝浆料具有明显改善的界面整平效果,共烧后得到界面结合致密,无开裂、无翘曲的基片样品。附图说明图1为实施例1中锆铝共烧陶瓷样品的断面sem显微形貌图;图2为实施例2中锆铝共烧陶瓷样品的断面sem显微形貌图;图3为实施例3中锆铝共烧陶瓷样品的断面sem显微形貌图;图4为实施例4中锆铝共烧陶瓷样品的断面sem显微形貌图;图5为实施例5中锆铝共烧陶瓷样品的断面sem显微形貌图;图6为实施例6中锆铝共烧陶瓷样品的断面sem显微形貌图;图7为实施例7中锆铝共烧陶瓷样品的断面sem显微形貌图。具体实施方式为更好的说明本发明的目的、技术方案和优点,下面将结合附图和具体实施例对本发明作进一步说明。实施例1本发明所述玻璃粉料的一种实施例,本实施例所述玻璃粉料的成分及各成分含量见表1。表1实施例1中玻璃粉料的组成及含量玻璃粉料的制备:按表1所述玻璃粉成分及其质量配比,称取相应氧化物原料,以无水乙醇为球磨介质,将称取的原料加入球磨罐中,球磨8h;出料后在烘箱中于100℃烘干10h。取出烘干后的粉料在碾钵中磨碎,放入99铝质坩埚,在马弗炉中,于空气气氛下以3℃/min的升温速率加热到1400℃,保温4小时,再以1℃/min速率降温至1200℃,在1200℃时取出坩埚中的玻璃料水淬。将水淬的玻璃料磨碎,过200目筛网,在500℃退火6小时制得玻璃粉料。氧化锆与氧化铝共烧用氧化铝粉料的制备:称取285g的氧化铝和15g的玻璃料,混合后与360ml的无水乙醇加入行星球磨机球磨8h得到混合研磨料浆,将混合研磨料浆于100℃烘干12h,取出烘干后的粉料在碾钵中磨碎,过200目筛网,制得氧化锆与氧化铝共烧用氧化铝粉料。氧化锆与氧化铝共烧用氧化铝浆料的制备:加入占氧化铝粉料(含玻璃粉料)质量30wt%的乙醇,和占氧化铝粉料质量20wt%的三乙醇胺,在球磨机中混合20min;再加入含有玻璃粉料的氧化铝粉料,并加入占氧化铝粉料质量10wt%的聚乙烯醇缩丁醛,和占氧化铝粉料质量3wt%的邻苯二甲酸丁苄酯,球磨8h后,取出,制得用于氧化锆与氧化铝匹配共烧的氧化铝浆料。利用本实施例制得的氧化铝浆料,能够实现与5ysz(添加5mol%y2o3的zro2)之间的匹配共烧,共烧温度为1450℃。将共烧样品进行扫描电子显微分析得到其断面的放大400倍的sem图像,如图1所示。图1中,中间层为添加有玻璃成分的al2o3层,上下层为5ysz层,可见al2o3与ysz共烧后界面平整且结合紧密,样品外观无明显的翘曲和变形,经测量,样品抗折强度≥300mpa。实施例2本发明所述玻璃粉料的一种实施例,本实施例所述玻璃粉料的成分及各成分含量见表2。表2实施例2中玻璃粉料的组成及含量玻璃粉料的制备:按表2所述玻璃粉成分及其质量配比,称取相应氧化物原料,以无水乙醇为球磨介质,将称取的原料加入球磨罐中,球磨16h;出料后在烘箱中于100℃烘干10h。取出烘干后的粉料在碾钵中磨碎,放入99铝质坩埚,在马弗炉中,于空气气氛下以2℃/min的升温速率加热到1350℃,保温2小时,再以1℃/min速率降温至1160℃,在1160℃时取出坩埚中的玻璃料水淬。将水淬的玻璃料磨碎,过200目筛网,在600℃退火6小时制得玻璃粉料。氧化锆与氧化铝共烧用氧化铝粉料的制备:称取285g的氧化铝和15g的玻璃料,混合后与360ml的无水乙醇加入行星球磨机球磨8h得到混合研磨料浆,将混合研磨料浆于100℃烘干12h,取出烘干后的粉料在碾钵中磨碎,过200目筛网,制得氧化锆与氧化铝共烧用氧化铝粉料。氧化锆与氧化铝共烧用氧化铝浆料的制备:加入占氧化铝粉料(含玻璃粉料)质量40wt%的乙醇,和占氧化铝粉料质量35wt%的三乙醇胺,在球磨机中混合30min;再加入含有玻璃粉料的氧化铝粉料,并加入占氧化铝粉料质量15wt%的聚乙烯醇缩丁醛,和占氧化铝粉料质量6wt%的邻苯二甲酸丁苄酯,球磨16h后,取出,制得用于氧化锆与氧化铝匹配共烧的氧化铝浆料。利用本实施例制得的氧化铝浆料,能够实现与5ysz(添加5mol%y2o3的zro2)之间的匹配共烧,共烧温度为1440℃。将共烧样品进行扫描电子显微分析得到其断面的放大400倍的sem图像,如图2所示。图2中,上层为添加有玻璃成分的al2o3层,下层为5ysz层,可见al2o3与ysz共烧后界面平整且结合紧密。样品外观无明显的翘曲和变形,将测量,样品抗折强度≥290mpa。实施例3本发明所述玻璃粉料的一种实施例,本实施例所述玻璃粉料的成分及各成分含量见表3。表3实施例3中玻璃粉料的组成及含量玻璃粉料的制备:按表3所述玻璃粉成分及其质量配比,称取相应氧化物原料,以无水乙醇为球磨介质,将称取的原料加入球磨罐中,球磨10h;出料后在烘箱中于100℃烘干10h。取出烘干后的粉料在碾钵中磨碎,放入99铝质坩埚,在马弗炉中,于空气气氛下以8℃/min的升温速率加热到1450℃,保温6小时,再以3℃/min速率降温至1220℃,在1220℃时取出坩埚中的玻璃料水淬。将水淬的玻璃料磨碎,过200目筛网,在500℃退火6小时制得玻璃粉料。氧化锆与氧化铝共烧用氧化铝粉料的制备:称取285g的氧化铝和15g的玻璃料,混合后与360ml的无水乙醇加入行星球磨机球磨8h得到混合研磨料浆,将混合研磨料浆于100℃烘干12h,取出烘干后的粉料在碾钵中磨碎,过200目筛网,制得氧化锆与氧化铝共烧用氧化铝粉料。氧化锆与氧化铝共烧用氧化铝浆料的制备:加入占氧化铝粉料(含玻璃粉料)质量35wt%的乙醇,和占氧化铝粉料质量30wt%的三乙醇胺,在球磨机中混合30min;再加入含有玻璃粉料的氧化铝粉料,并加入占氧化铝粉料质量12wt%的聚乙烯醇缩丁醛,和占氧化铝粉料质量5wt%的邻苯二甲酸丁苄酯,球磨12h后,取出,制得用于氧化锆与氧化铝匹配共烧的氧化铝浆料。利用本实施例制得的氧化铝浆料,能够实现与5ysz(添加5mol%y2o3的zro2)之间的匹配共烧,共烧温度为1420℃。将共烧样品进行扫描电子显微分析得到其断面的放大400倍的sem图像,如图3所示。图3中,上层为添加有玻璃成分的al2o3层,下层为5ysz层,可见al2o3与ysz共烧后界面平整且结合紧密。样品外观无明显的翘曲和变形,经测量,样品抗折强度≥280mpa。实施例4本发明所述玻璃粉料的一种实施例,本实施例所述玻璃粉料的成分及成分含量见表4。表4实施例4中玻璃粉料的组成及含量玻璃粉料的制备:按表4所述玻璃粉成分及其质量配比,称取相应氧化物原料,以无水乙醇为球磨介质,将称取的原料加入球磨罐中,球磨10h;出料后在烘箱中于100℃烘干10h。取出烘干后的粉料在碾钵中磨碎,放入99铝质坩埚,在马弗炉中,于空气气氛下以3℃/min的升温速率加热到1400℃,保温4小时,再以1℃/min速率降温至1200℃,在1200℃时取出坩埚中的玻璃料水淬。将水淬的玻璃料磨碎,过200目筛网,在500℃退火6小时制得玻璃粉料。氧化锆与氧化铝共烧用氧化铝粉料的制备:称取288g的氧化铝和12g的玻璃料,混合后与360ml的无水乙醇加入行星球磨机球磨8h得到混合研磨料浆,将混合研磨料浆于100℃烘干12h,取出烘干后的粉料在碾钵中磨碎,过200目筛网,制得氧化锆与氧化铝共烧用氧化铝粉料。氧化锆与氧化铝共烧用氧化铝浆料的制备:加入占氧化铝粉料(含玻璃粉料)质量35wt%的乙醇,和占氧化铝粉料质量30wt%的三乙醇胺,在球磨机中混合30min;再加入含有玻璃粉料的氧化铝粉料,并加入占氧化铝粉料质量12wt%的聚乙烯醇缩丁醛,和占氧化铝粉料质量5wt%的邻苯二甲酸丁苄酯,球磨12h后,取出,制得用于氧化锆与氧化铝匹配共烧的氧化铝浆料。利用本实施例制得的氧化铝浆料,能够实现与5ysz(添加5mol%y2o3的zro2)之间的匹配共烧,共烧温度为1460℃。将共烧样品进行扫描电子显微分析得到其断面的放大400倍的sem图像,如图4所示。图4中,上层为添加有玻璃成分的al2o3层,下层为5ysz层,可见共烧后al2o3与ysz界面平整且结合紧密,样品外观无明显的翘曲和变形,经测量,样品抗折强度≥310mpa。实施例5本发明所述玻璃粉料的一种实施例,本实施例所述玻璃粉料的成分及各成分含量见表5。表5实施例5中玻璃粉料的组成及含量玻璃粉料的制备:按表5所述玻璃粉成分及其质量配比,称取相应氧化物原料,以无水乙醇为球磨介质,将称取的原料加入球磨罐中,球磨10h;出料后在烘箱中于100℃烘干10h。取出烘干后的粉料在碾钵中磨碎,放入99铝质坩埚,在马弗炉中,于空气气氛下以3℃/min的升温速率加热到1400℃,保温4小时,再以1℃/min速率降温至1200℃,在1200℃时取出坩埚中的玻璃料水淬。将水淬的玻璃料磨碎,过200目筛网,在500℃退火6小时制得玻璃粉料。氧化锆与氧化铝共烧用氧化铝粉料的制备:称取291g的氧化铝和9g的玻璃料,混合后与360ml的无水乙醇加入行星球磨机球磨8h得到混合研磨料浆,将混合研磨料浆于100℃烘干12h,取出烘干后的粉料在碾钵中磨碎,过200目筛网,制得氧化锆与氧化铝共烧用氧化铝粉料。氧化锆与氧化铝共烧用氧化铝浆料的制备:加入占氧化铝粉料(含玻璃粉料)质量35wt%的乙醇,和占氧化铝粉料质量30wt%的三乙醇胺,在球磨机中混合30min;再加入含有玻璃粉料的氧化铝粉料,并加入占氧化铝粉料质量12wt%的聚乙烯醇缩丁醛,和占氧化铝粉料质量5wt%的邻苯二甲酸丁苄酯,球磨12h后,取出,制得用于氧化锆与氧化铝匹配共烧的氧化铝浆料。利用本实施例制得的氧化铝浆料,能够实现与5ysz(添加5mol%y2o3的zro2)之间的匹配共烧,共烧温度为1480℃。将共烧样品进行扫描电子显微分析得到其断面的放大400倍的sem图像,如图5所示。图5中,中间层为添加有玻璃成分的al2o3层,上下层为5ysz层,可见共烧后al2o3与ysz界面平整,但略有分层,这主要与al2o3层中玻璃相含量较低有关;样品外观无明显的翘曲和变形,经测量,样品抗折强度≥335mpa。实施例6本发明所述玻璃粉料的一种实施例,本实施例所述玻璃粉料的成分及各成分含量见表6。表6实施例6中玻璃粉料的组成及含量玻璃粉料的制备:按表6所述玻璃粉成分及其质量配比,称取相应氧化物原料,以无水乙醇为球磨介质,将称取的原料加入球磨罐中,球磨10h;出料后在烘箱中于100℃烘干10h。取出烘干后的粉料在碾钵中磨碎,放入99铝质坩埚,在马弗炉中,于空气气氛下以3℃/min的升温速率加热到1400℃,保温4小时,再以1℃/min速率降温至1200℃,在1200℃时取出坩埚中的玻璃料水淬。将水淬的玻璃料磨碎,过200目筛网,在500℃退火6小时制得玻璃粉料。氧化锆与氧化铝共烧用氧化铝粉料的制备:称取294g的氧化铝和6g的玻璃料,混合后与360ml的无水乙醇加入行星球磨机球磨8h得到混合研磨料浆,将混合研磨料浆于100℃烘干12h,取出烘干后的粉料在碾钵中磨碎,过200目筛网,制得氧化锆与氧化铝共烧用氧化铝粉料。氧化锆与氧化铝共烧用氧化铝浆料的制备:加入占氧化铝粉料(含玻璃粉料)质量35wt%的乙醇,和占氧化铝粉料质量30wt%的三乙醇胺,在球磨机中混合30min;再加入含有玻璃粉料的氧化铝粉料,并加入占氧化铝粉料质量12wt%的聚乙烯醇缩丁醛,和占氧化铝粉料质量5wt%的邻苯二甲酸丁苄酯,球磨12h后,取出,制得用于氧化锆与氧化铝匹配共烧的氧化铝浆料。利用本实施例制得的氧化铝浆料,能够实现与5ysz(添加5mol%y2o3的zro2)之间的匹配共烧,共烧温度为1500℃。将共烧样品进行扫描电子显微分析得到其断面的放大400倍的sem图像,如图6所示。图6中,中间层为添加有玻璃成分的al2o3层,上下层为5ysz层,可见共烧后al2o3与ysz界面平整度降低,且有分层现象,这主要与al2o3层中玻璃相含量较低有关;样品外观无明显的翘曲和变形,经测量,样品抗折强度≥350mpa。实施例7未添加本发明所述玻璃粉料的一种实施例,氧化铝粉料为纯氧化铝体系。氧化锆与氧化铝共烧用氧化铝粉料的制备:称取300g的氧化铝粉料,与360ml的无水乙醇加入行星球磨机球磨8h得到混合研磨料浆,将混合研磨料浆于100℃烘干12h,取出烘干后的粉料在碾钵中磨碎,过200目筛网,制得氧化锆与氧化铝共烧用氧化铝粉料。氧化锆与氧化铝共烧用氧化铝浆料的制备:加入占氧化铝粉料(含玻璃粉料)质量35wt%的乙醇,和占氧化铝粉料质量30wt%的三乙醇胺,在球磨机中混合30min;再加入含有玻璃粉料的氧化铝粉料,并加入占氧化铝粉料质量12wt%的聚乙烯醇缩丁醛,和占氧化铝粉料质量5wt%的邻苯二甲酸丁苄酯,球磨12h后,取出,制得用于氧化锆与氧化铝匹配共烧的氧化铝浆料。利用本实施例制得的氧化铝浆料,烧结温度为1600℃,难以实现与5ysz(添加5mol%y2o3的zro2)之间的匹配共烧。将烧结后样品进行扫描电子显微分析得到其断面的放大400倍的sem图像,如图7所示。图7中,中间层为al2o3层,上下层为5ysz层,可见烧结后al2o3与ysz界面平整度不佳,且有明显的分层现象;经测量,样品抗折强度≥230mpa。实施例8将实施例1~7制备得到的氧化铝浆料在流延后的ysz生带表面经丝网印刷、叠层、等静压、切割及共烧工序制成锆铝共烧基板。采用三点弯曲试验方法测试基板样品的抗折强度,参照标准为jc/t676-1997玻璃材料弯曲强度试验方法对其抗折强度进行测量,具体实施例1~7氧化锆与氧化铝共烧样品的性能参数测量结果见表7。表7实施例1~7氧化锆与氧化铝共烧样品的性能参数样品实施例1实施例2实施例3实施例4实施例5实施例6实施例7共烧温度(℃)1450144014201460148015001600抗折强度(mpa)300290280310335350230从实施例1~7可知,通过调节玻璃粉料的组成及其玻璃粉料在氧化铝粉料中的含量,能够实现氧化锆与氧化铝匹配共烧用氧化铝粉料及其浆料的设计与制备,该氧化铝浆料能够与ysz在1420~1500℃温度范围内形成良好的匹配共烧。同时,与现有锆铝共烧粉体技术相比,本发明工艺简单,易于实现,成本低;而且经过共烧得到的锆铝基板样品,界面平整,结合紧密,样品外观无明显的翘曲和变形,抗折强度≥280mpa,能很好的满足锆铝基板应用要求。最后所应当说明的是,以上实施例仅用以说明本发明的技术方案而非对本发明保护范围的限制,尽管参照较佳实施例对本发明作了详细说明,本领域的普通技术人员应当理解,可以对本发明的技术方案进行修改或者等同替换,而不脱离本发明技术方案的实质和范围。当前第1页12