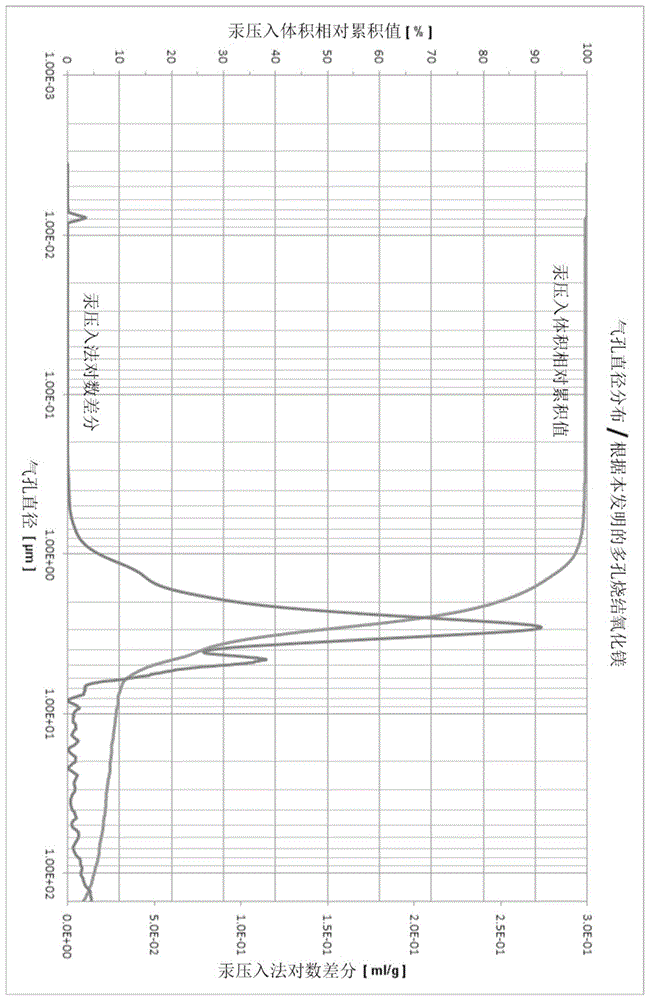
本发明涉及的生产和制备方法,针对多孔烧结氧化镁,及针对在生产粗陶瓷耐火定型或不定型产品时所使用的含有多孔烧结氧化镁的回填料,另外,还针对由该回填料制作的同类产品及这些产品的制备方法。更进一步地,本发明还针对内衬,尤其是大容量工业炉的工作衬和/或后墙,且这里的内衬,尤其指工作衬和/或后墙,至少拥有一件同类产品,及属于同类工业炉。
背景技术:
:本发明中的“耐火”概念应不止限于,而是根据iso836及din51060中定义的示温锥当量>1500℃。根据本发明的耐火产品按照dineniso1893:2009-09具有t0.5≥600℃,优选t0.5≥800℃的受压软化点。因此根据本发明的耐火或防火粒状材料及颗粒适用于具有上述受压软化点t0.5的耐火产品。根据本发明的耐火产品可用于处在600-2000℃温度控制之下的集料内,特别是1000℃-1800℃温度范围内,用来保护集料结构。根据本发明的本意,“颗粒”及“粒状材料”概念涵盖的是由许多固态小颗粒所组成的松散可倾倒固体材料。若颗粒尺寸≤200μm,即为粉面或粉末。这些颗粒是通过如打碎和碾碎这样的机械粉碎方法来制作的。通常通过筛滤的方法,来调整设定这些颗粒的颗粒分布。业内周知,耐火材料是以六种难熔碱性氧化物和碳以及难熔碳化合物为基础的,比如在vulkan出版社geraldroutschka/harmutwuthnow著作的“耐火材料”实践手册第5版(以下仅称为“实践手册”)s.1-7页中有关于这些物质的描述和分类。按照dineniso10081:2005-05,基于化学反应表现的不同,有碱性和非碱性耐火产品之区分。非碱性产品类包括sio2-al2o3系及其他的按照其化学反应表现无法进行进一步分类的材料,如sic产品及碳产品。含有高成分sio2的材料则称为酸性。多数碱性产品的本质特征在于,mgo和cao氧化物的总量占据主要成分。除此以外,虽然铬铁矿石、镁铬矿石、尖晶石和镁橄榄石近乎为中性,它们仍被看作是碱性产品。属于定型碱性产品类的,特别是含有氧化镁的产品,尤其是氧化镁产品、氧化镁铬铁产品、氧化镁尖晶石产品、氧化镁氧化锆产品、氧化镁镁铁尖晶石产品、氧化镁镁尖晶石产品、氧化镁尖晶石铁氧体产品、氧化镁白云石产品(请同时参见实践手册,第99页,表4.26)。碱性不定型产品则是其中使用的添加剂主要由氧化镁、白云石、铬镁石、铬矿石和尖晶石等的产品(请同时参见实践手册,第146页)。用来生产氧化镁产品的典型的氧化镁原料为由烧结和/或熔体氧化镁所构成的颗粒或丸料。烧结氧化镁是在温度>1700℃,优选>1800℃的温度的条件下进行燃烧,这样即可获得尽可能高的体积密度。熔体氧化镁是在>2800℃的温度条件下生产制备的,以便同样能达到尽可能高的体积密度及尽可能低的颗粒显气孔率。普通的烧结氧化镁品种具有>3.10g/cm3的体积密度。该值应争取达到>3.30–3.40g/cm3。相应的颗粒显气孔率(总显气孔率)一般在4-10%体积百分比左右。由熔体氧化镁制作的颗粒通常具有>3.50g/cm3的体积密度,及<2.5%体积百分比的颗粒显气孔率(总显气孔率)。符合本发明的定型产品为经过煅烧或未经煅烧,尤其是经过压制处理,优选在陶瓷厂内所制作的陶瓷产品,尤其指型砖或板料。定型产品,尤其是定型型砖,优选利用砂浆或也可无砂浆(“无接缝”)完成筑墙作业,以便形成炉衬或炉后墙。根据本发明的不定型产品则多数时候是由应用方采用不定型的团料,通过比如浇筑或喷射这样的方式来自行制作的产品。不定型产品多数时候需要在应用现场,放置占地较大的模板后方,待其硬化后形成炉衬或炉后墙。根据本发明的产品以在工业化燃烧或熔化或其他集火工业设备内应用为宜,比如应用在大容量工业炉内,以便形成耐火、临火侧及设备内侧的防护衬(工作衬)。这种产品宜作为非金属工业的燃烧炉内的内衬,尤其是应用在水泥炉设备、石灰井式炉或石灰旋转粗炼炉、或加热炉或能量炉或炼钢或有色金属工业中的火炉之内。根据本发明的产品还可作为上述炉内的绝缘后墙来使用。总的来说,这种类型的耐火产品因此通常需要具有很低的热导率及高的耐渗透性。更进一步地,它在应用温度下还应具有良好的耐温性、化学耐受性、耐热冲击性、良好的微观结构弹性、相宜的受压软化性能及很低的透气性和高的耐热弯曲强度。另外,定型产品还应具有与应用用途相匹配的低温耐压强度,尤其出色的易操作性,并且在生产完成后及温度变化后仍具有足够性能。总的来说,de102006040269a1和de102013020732a1中这种类型的耐火产品已为人熟知。对于这种产品,将通过颗粒尺寸分布,设定所需的显气孔率:de102006040269a1中,由不同耐火材料所构成的经过焙烧的粗陶瓷耐火产品已为人熟知,这种产品也有可能作为工作衬投入应用,并且由于具有>10%体积百分比这样疏松的显气孔率,也同样具有相对很低的热导率。这里涉及的是细颗粒的产品,它们是由一种50-90%重量百分比均由颗粒尺寸d90<100μm的细颗粒耐火材料所构成的回填料而制得的,其中,颗粒尺寸在100-500μm之间的d90占有份额限制在≤10%重量百分比的界限以内。由此得出d90>500μm的粗颗粒占有份额的重量百分比在10-50%范围内,并且这里,回填料选择特定的颗粒占比,将对该烧制产品的微观结构及其特性起到决定性作用。产品具有的疏松的显气孔率,一半以上是由直径d90<15μm的气孔以及超过1/10是由直径d90>100μm的气孔所形成的。其中,在15-100μm的气孔的显气孔率占有份额最多占疏松的总显气孔率的1/7。de102013020732a1中,突出表现的是一种由至少一种颗粒耐火材料所构成的粗陶瓷耐火产品,这种耐火材料所具有的疏松显气孔率的体积百分比在22-45%之间,更好则在23-29%之间,并且它具有这样一种颗粒结构,在这种结构下,颗粒尺寸为0.1-0.5mm之间的中等大小颗粒占有份额的重量百分比在10-55%,更好则是在35-50%,同时,颗粒结构中的剩余部分为颗粒尺寸在0.1mm以下的细粉颗粒部分,和/或颗粒尺寸大于0.5mm以上的粗颗粒部分。这种耐火产品尤其适用于制作大容量工业炉的工作衬。us-ps4,927,611中描述的氧化镁熟料具有占体积百分比>40%的显气孔率,以体积百分比在50-70%的范围内为宜,以及体积密度<2.0g/cm3。另外,有超过90%体积百分比的气孔具有<50μm的气孔尺寸。这种氧化镁熟料是通过以下成分利用粒化方法来制作的,一种是可形成镁氧化物且颗粒尺寸<150μm(100目)的成分,一种是疏松可燃烧的物质,其添加量占重量百分比10-40%,以及再额外添加重量百分比为1-15%的镁盐,随后在1300-1600℃下进行煅烧。这样制作而得的氧化镁熟料可以用喷射悬浮液的方式来用喷嘴及分配器口涂覆涂层。另外,由wenyan等人在unitecr2015,proc.128中的“轻量化轻集料尖晶石含量对方镁石-尖晶石耐火材料与水泥熟料反应特性的影响”,以及wenyan等人在关键工程材料杂志(keyengineeringmaterials),697卷,581-585页中的“尖晶石含量对多孔方镁石-尖晶石陶瓷与水泥熟料反应的影响”中,对以氧化镁-尖晶石为基础的轻重量化碱性颗粒的使用进行了说明。之后,由mgo及由mgo-尖晶石-混合物生成颗粒,也就是mgo及mgo-尖晶石-混合-熟料,其显气孔率占重量百分比24.8-30.0%,随后用氧化镁作为骨料加以混合、模具定型并在1550℃温度下进行煅烧。定型后的产品,其特征在于显气孔率大约为30%的体积百分比。mgo颗粒在气孔尺寸分布方面,气孔直径的最大值为50μm;mgo-尖晶石-混合-熟料-谷物颗粒的平均气孔直径的值在11.33μm和27.58μm之间,骨料的平均气孔直径在50.52μm左右。通常来说,随着尖晶石含量的提高,水泥熟料侵蚀脆弱性也随之上升。纯氧化镁产品及含有的混合熟料是由75%氧化镁和25%尖晶石所构成的产品具有最大抗性。技术方面其他重要规格,如强度、耐火强度、弹性(弹性模数、抗剪模数)、耐温度变化稳定性、体积稳定性等等,未进行阐述。据此推测,这种型砖,由于技术特性缺陷,无法用在水泥旋转炉内。值得注意的是大的气孔直径,在使用有疏松燃料情况下,可促成闭合(有机结合、氢氧化物、碳酸盐),这种情况也恰如同一位作者(wenyan等人在ceram.int.2015年1月,第515-520页中的“原位分解成孔技术制备多孔mgo-al2o3耐火集料及其表征”)所说明的一样。cn106747594a公开了由重量百分比占5-95%的mgo轻烧镁粉及重量百分比占5-95%镁磷矿粉所构成的混合物生产制备颗粒的方法。这种混合物将与木质素磺酸盐相混合,并且压制成压制品。压制品持续20至50小时进行干燥处理,随后送入高温隧道窑或梭式窑以1450-1700℃的温度,持续10-20小时进行煅烧。比如以重量百分比占95%的mgo轻烧粉及重量百分比占5%的菱镁矿粉制作出的颗粒基质,具有16.5%体积百分比的显气孔率及2.97g/cm3的体积密度。技术实现要素:本发明的任务是,为生产制备耐火产品所需的具有高的显气孔率及低的热导率的回填料,提供具有良好颗粒强度的烧结氧化镁,并且其特性需要满足大容量工业炉内应用之需,尤其需要具有高耐碱渗透性。本发明的进一步任务是,提供这种类型的回填料及由该回填料所制作的定型或不定型耐火产品,以及其生产和制备方法。另外,本发明的任务还包括,为大容量工业炉提供耐火内衬,尤其指非金属工业的燃烧炉的内衬,优选适用于水泥炉设备、石灰井式炉或石灰旋转粗炼炉,用来生产氧化镁或白云石的炉或用来产生能源的炉,或也可用于含有至少一件或由至少一件根据本发明的产品而构成的有色金属工业或钢铁工业的火炉。内衬可以采用多层结构,比如具有一层临火侧或高温侧内衬或设备内侧的内衬,其后布置一层起到绝缘作用的后墙。通过权利要求1、15、25、26、38、40、41和45阐述的特征,圆满解决了上述任务。本发明的有益设计是在相关的从属权利要求中体现的。附图说明以下将附图示例,对本发明进行进一步的阐述。附图包括:图1:根据本发明由多孔烧结氧化镁构成颗粒的气孔直径分布示意图;图2:根据本发明的定型型砖的气孔直径分布示意图;图3:根据本发明的烧结氧化镁的光学显微镜照片(反射光),在ht炉内以1530℃温度持续6小时煅烧。具体实施方式本发明中令人惊讶的发现是,通过对压制品,尤其指对颗粒的烧结,尤其是由mgo粉构成的颗粒,优选由mgo轻烧粉构成的颗粒,在降低最高燃烧温度情况下(取代通常的>1700℃的温度),并且随后用机械粉碎压制品所制作的烧结氧化镁,具有符合dinen993-1:1195-04和dinen993-18:1999-01要求的占体积百分比为15-38%,优选为20-38%的颗粒显气孔率(总显气孔率)。这种mgo粉也可由比如说烧结的氧化镁(dbm)或熔体氧化镁所构成,不过首选仍为mgo轻烧粉。并且使用这种颗粒状多孔烧结氧化镁的情况下,可以制备具有典型机械特性和化学特性的耐火产品,相比迄今所使用的产品,具有更高的显气孔率,继而带来更低的热导率,但渗透性稍差。本发明中特别发现之处在于,不额外添加疏松燃料也是可行的,其方法是仅需要降低最高燃烧温度,而并非通常的>1700℃,从由mgo粉状颗粒,优选采用mgo轻烧粉粒子所构成的压制品,来制得由烧结氧化镁构成的颗粒,这种颗粒相较于已知的烧结氧化镁和熔体氧化镁来说,具有明显更低的体积密度及明显更高的空隙度,继而使得用此方式制得的产品的特性得以改善。烧结作业或烧结流程的煅烧持续时间及烧结温度,也就是温度趋势或温度控制或温度曲线,根据本发明应这样来调整设定,使根据本发明的由多孔烧结氧化镁构成的颗粒具有符合din993-18:2002-11和din993-1:1995-4的15-38%体积百分比,优选为20-38%的体积百分比的颗粒显气孔率(总显气孔率)即可;及按照din993-18:2002-11以2.20-2.85g/cm3为宜,优选为2.20-2.75g/cm3的体积密度。这里,温度控制取决于比如说氧化镁的种类(其反应性)及mgo粉的颗粒尺寸。烧结作业以在最高温度≤1600℃下进行为宜,进一步地优选分别为≤1550℃、≤1500℃,最佳则在≤1400℃。或者烧结作业以在1100-1600℃之间的一个最高温度下进行为宜,进一步地优选分别为1200-1600℃、1200-1550℃,最佳则在1200-1500℃之间。最高温度下生产制备根据本发明的烧结氧化镁所需的煅烧持续时间以0.5-7小时为宜,优选为2-6小时。总的煅烧持续时间以等同于普通方式制备烧结氧化镁的时间为宜。煅烧以在氧化环境下进行为宜,不过也可在还原环境下进行。煅烧之后,对烧结氧化镁进行机械粉碎,尤其要打碎,并且通过筛滤进行分类。所使用的粉状的mgo轻烧料或mgo轻烧粉以普通生产方式由氢氧化镁或由碳酸镁制备为宜。另外,所使用的mgo粉,优选采用mgo轻烧粉,颗粒尺寸分布具有以下值为宜:d90在80-100μm之间,和/或d50在5-15μm之间,和/或d10在1-3μm之间。这里的dx值众所周知意味着,粒子的x%重量百分比小于给定值。按照diniso13320:2009,借助激光粒度仪来确定此值。为此,借助超声波将氧化镁粉末分散在乙醇中。另外,所使用的mgo粉,优选采用mgo轻烧粉,以最少含有88%重量百分比的mgo为宜,优选含有至少95%重量百分比的mgo,最佳含有至少97%重量百分比的mgo,按照din12677:2013-02借助x射线荧光分析法(rfa)来测定。更进一步地,所使用的mgo粉,优选采用mgo轻烧粉,以最多含有4%重量百分比的cao为宜,优选最多含2%重量百分比cao,按照din12677:2013-02借助x射线荧光分析法(rfa)来测定。mgo粉,优选采用mgo轻烧粉,除了在普通的压力机上以外,优选采用制丸压力机或颗粒压力机或液压式压力机,将其压制为具有din66133:1993-06所要求的1.8-2.3g/cm3、优选1.9-2.2g/cm3的体积密度的压制品,以及din66133:1993-06所要求的32-52%体积百分比、优选35-45%体积百分比的显气孔率。这里的压制品以颗粒为宜,不过考虑到能带来的优点,也可以是饼料或型砖。这里以仅采用mgo粉、优选采用mgo轻烧粉为宜,酌情添加一些水进行压制,也就是无粘合剂,继而无需任何疏松燃料。这样形成的压制品,相对于其干物质总量来说,以具有至少96%重量百分比为宜,优选至少占98%,最佳则占100%重量百分比,均由mgo粉,优选由mgo轻烧粉所构成。压制品中尤其是不含有菱镁矿粉。煅烧持续时间及烧结温度,如前所述,应这样来调整设定,使得根据本发明的由多孔烧结氧化镁构成的颗粒,具有符合din993-18:2002-11及din993-1:1995-4所要求的15-38%体积百分比,优选为20-38%的颗粒显气孔率(总显气孔率)即可,并且以具有符合din993-18:2002-11所要求的为2.20-2.85g/cm3的体积密度为宜,优选为2.20-2.75g/cm3。这种设定也适用于针对颗粒的其他特性。根据本发明的由多孔烧结氧化镁构成的颗粒,其特别之处在于,以具有从0.1-10μm为宜、优选2-8μm这样的很低的平均气孔直径d50,按照din66133:1993-06测定。这里的气孔直径分布可以是的单峰分布(参见图1)。图3显示根据本发明的烧结氧化镁的微观结构。它具有均匀的氧化镁颗粒1分布及小气孔2。没有识别到更大的气孔。颜色浅一些的气孔2是灌注有环氧树脂的气孔,略深一些的气孔没有被灌注。另外,根据本发明的由多孔烧结氧化镁构成的颗粒,仿照din13055:2016-11的要求(替代20mm为10mm),以具有10-30mpa的颗粒耐压强度为宜,优选具有11-25mpa的强度。根据本发明的由多孔烧结氧化镁构成的颗粒,另外还以具有符合dinen821-2:1997-08要求的以下热导率(wlf)为宜:表1:根据本发明的烧结氧化镁的优选热导率热导率优选400℃[w/mk]3-94-8800℃[w/mk]2-73-61200℃[w/mk]2-73-6根据本发明的颗粒,特别具有以下特性:表2:本发明多孔的和紧实烧结氧化镁的特性如前述,根据本发明的烧结氧化镁可用于根据本发明的回填料中,以便用来生产制备根据本发明的、定型的或不定型的耐火产品。根据本发明的回填料包含有内含本发明的烧结氧化镁的干物质混合物及粘合剂。这是指,需要添加进一定量的粘结剂(干性的或流体的),并计入到干性物质混合物的干物质总量。视情况而定,其中还可以再含有一种流体的添加剂,这同样需要定量添加,并计入到干性物质混合物的干物质总量。这种由粘合剂和干性物质混合物所构成的回填料,相对于回填料的干物质总量而言,以重量百分比至少占90%为宜,优选至少占99%,最优则占100%。相对于干性物质混合物的干性物质总量而言,这种干性物质混合物分别以具有以下成分为宜(量的数据说明给出的是相应成分的总和,也就是举例来说,给出的是根据本发明的烧结氧化镁所构成的粗颗粒方面的总含量,粉状颗粒方面的总含量或其他颗粒方面的总含量):a)至少一种由根据本发明的烧结氧化镁所构成的粗颗粒,颗粒尺寸>200μm,以重量百分比占10-90%的量为宜,优选占20-80%;b)至少一种由氧化镁所构成的粉状颗粒,比如由根据本发明的烧结氧化镁所构成的,颗粒尺寸≤200μm,以重量百分比占90-10%的量为宜,优选占80-20%;c)酌情至少一种由某种耐火材料构成的其他颗粒,其他颗粒总量以占重量百分比0.5-40%为宜,优选占3-30%;d)酌情至少一种耐火材料添加物,总量以重量百分比占<5%为宜;e)酌情至少一种耐火材料添加剂,总量以重量百分比占<5%为宜;这些成分可以任意组合包含在干物质混合物内。根据本发明的回填料还包括,如前所述,在干性物质混合物以外至少添加有一种耐火材料液态或固态的粘合剂,相对于干性物质混合物的干性物质总量而言,以在总量里占重量百分比1-9%为宜,优选占2.5-6%。如果是不定型产品,这种液态粘合剂以随附包装形式装在与回填料干性组成成分分开的容器内为宜。更进一步地,由根据本发明的烧结氧化镁所构成的粗颗粒,以具有最大8mm的颗粒尺寸为宜,优选至最大6mm以下,最佳则至最大4mm以下。由根据本发明的烧结氧化镁及/或根据本发明的干性物质混合物所构成的粗颗粒的颗粒分布,以连续曲线为宜,优选按照litzow、furnas或fuller级配曲线或高斯分布。其他颗粒以由一种提供弹性的原料构成为宜,也就是能起到典型降低弹性模量作用的原料。这些其他颗粒下选自以下原料所构成组:镁铝尖晶石、铝土矿、矾土、铁铝尖晶石、镁铁尖晶石、铬矿石、铁镁尖晶石、氧化锆、橄榄石和/或镁橄榄石。本发明特别有效之处在于采用了由以下物质所构成的干性物质混合物:氧化镁含镁铝尖晶石的氧化镁含铁铝尖晶石的氧化镁含镁橄榄石的氧化镁含镁铁尖晶石或含镁的铁尖晶石的氧化镁含铬矿石的氧化镁含氧化锆的氧化镁。如前所述,由不同的其他颗粒加以组合也是可行的,优选一种的其他颗粒由铁铝尖晶石构成同时搭配以另一种其他颗粒由镁铝尖晶石所构成。更进一步地,这些其他颗粒以具有颗粒尺寸最大值≤8mm为宜,优选≤6mm,最佳≤4mm。如果是干性粘合剂,它应为适合于耐火产品的粘合剂。比如在实践手册,第28页/3.2条中有这些粘合剂的说明。如果是液态粘合剂,选自以下粘合剂所构成的组为宜:热硬化合成树脂粘合剂,尤其指酚醛树脂,或糖蜜或木质素磺酸盐;或者以无硫粘合剂为宜,尤其指具有以下基质的粘合剂、葡萄糖、有机酸、蔗糖、al2o3粘合剂、磷酸、磷酸盐类粘合剂、水玻璃、硅酸乙酯,或硫酸盐,比如硫酸镁或硫酸铝,或溶胶凝胶(sol-gel)类。如果是干性添加物,涉及的是适合用于耐火产品的添加物。比如在实践手册,第28页/3.3条中所列举的添加物。它们用来改善加工性能或变形性能或修改产品的微观结构,以便达到特殊特性。如上所述,根据本发明的回填料用于生产制备根据本发明的耐火定型或不定型产品。为了生产制备定型产品,尤其指型砖,需要拌以至少一种液态的和/或固态的粘合剂和/或水,混入根据本发明的回填料干性混合物,制备出新的混合物或可塑性的团料。如果回填料含有液态粘合剂,则没必要加水,但加水也是可行的。为了使一种或多种粘合剂和/或水能够达到最佳分布效果,需要花费比如说3至10分钟的时间进行混合。将混合物注入模具和压制成型。压制压力在普通范围内即可,比如在60-180mpa之内,优选为100-150mpa。压制之后进行干燥,以在比如说60-200℃之间为宜,优选90-140℃之间。干燥作业以进行至剩余湿度占重量百分比的0.1-0.6%之间时停止为宜,优选0.2-0.5%之间,按照din51078:2002-12测定。至此,本发明已证实,用普通的压制压力来生产制备模型体是可行的,完全可以达到所述的显气孔率要求且兼具相应的机械特性和热特性。本发明中的烧结氧化镁所具有的显气孔率,尤其适用于材料混合遵照fuller或litzow颗粒分布的普通颗粒上,为整体的颗粒级配混合物,尤其当压制时,能明显地带来符合本发明的气孔容积,而无需按照de102013020732a1要求的,颗粒必须在微观结构上形成支撑骨架。根据本发明的模型体,尤其是型砖,使用时可不煅烧,或也可退火或煅烧处理。不过一般首选经过煅烧后使用。新鲜压制的型砖在陶瓷燃烧炉内进行退火处理,比如在隧道式火炉内,在400和1000℃之间,优选在500和800℃之间。煅烧作业则首选将干燥、压制后的型砖放在陶瓷燃烧炉内进行,比如在隧道式火炉内,陶瓷煅烧,以在1200和1800℃之间为宜,优选在1400和1700℃之间。氧化煅烧为首选,不过也可取决于材料成分,视带来的优点而定进行还原煅烧。按照din993-15:2005-14用平行热线法测定的根据本发明的烧结定型产品,尤其是型砖的热导率在300℃时以4.0-6.0w/mk为宜,优选4.5-5.8w/mk,在700℃时以3.0-5.0w/mk为宜,优选3.0-4.8w/mk,及在1000℃时以2.0-3.5w/mk为宜,优选2.0-3.2w/mk。烧结定型产品,尤其是型砖,以具有体积百分比占22-45%的疏松的显气孔率为宜,优选为23-35%,根据dinen993-1:1995-04测定。更进一步地,这种产品,以具有0.5-10μm的气孔尺寸分布平均值d50为宜,优选2-8μm,根据din66133:1993-06测定。另外,烧结定型产品,尤其是型砖,以具有1.9-2.9g/cm3的很低的体积密度值为宜,优选2.0-2.8g/cm3,根据din993-1:1995-04测定。根据本发明的烧结定型产品,尤其是型砖,根据dinen993-5:1998-12,其低温耐压强度以30和100mpa为宜,优选45和90mpa。根据本发明的烧结定型产品,尤其是型砖,根据dinen993-6:1995-04,其低温耐弯曲强度以2-18mpa为宜,优选3-10mpa。根据本发明的烧结定型产品,尤其是型砖,根据dinen993-4:1995-04,其空气渗透率以0.2-8npm为宜,优选0.5-6npm。根据本发明的烧结定型产品,尤其是型砖,根据dinen993-11:2008-03,针对1100℃的提高的检测温度下的空气,其耐温度变化稳定性以>20次淬火循环为宜,优选>30次淬火循环。生产制备不定型产品时,尤其是团料,优选采用喷射团料或震荡团料或浇铸团料或搅拌团料,需要同样地由根据本发明的干性物质混合物拌以一种干性的和/或液态的粘合剂和/或水来生产制备出混合物。如果回填料含有液态粘合剂,则没必要加水,但加水也是可行的。综合所述,本发明提供的是出色的耐火产品,尽管具有高疏松度,然而在热导率和气孔尺寸方面以及继而对透气性的影响方面又不失良好的性能,既适合作为工作内衬也适合作为后墙来使用。特别优越之处在于,根据本发明的烧结氧化镁具有很低的、以2-8μm为宜的平均气孔直径d50,甚至在制成的产品内,骨料的平均气孔直径d50旁边仍能呈现为约4μm(参见图2)。根据本发明的定型的,尤其是经过压制的,或者不定型的粗陶瓷耐火产品,虽然具有高疏松度,仍可以应用在集火的工业炉设备内,因为此产品完全具备工作内衬所要求的机械特性、热特性及热化学特性。d90<100μm、重量百分比约占50-90%的细磨粉材料,在这里是没必要使用的,而是可以采用耐火技术中常用的在8mm以下的普通颗粒即可正常工作。由此可降低颗粒准备工作所带来的生产成本,尤其可以节省磨碎成粉所需的能量。另外,根据本发明的烧结氧化镁由于煅烧温度更低,从而降低了co2排放。根据本发明,还可以放弃添加疏松燃料,这种为了回填料内保持均匀分布而添加的疏松燃料,不仅昂贵,还会通过co2的排放而加重环境负担。另外,为同等容积提供保护的内衬,所需的材料成本及重量成本也具有优势。迄今为止,耐火内衬多数情况下是通过由工作层和绝缘层所构成的多层内衬布局来降低热导率的。特别是活动式的设备上,比如水泥旋转粗炼炉,这种多层内衬机械方面是非常脆弱的或者说容易断裂。除此以外,安装工作也耗费巨大。为了避免由于这种带有中间隔层的内衬引发运行不安全问题,安装工作衬时不带绝缘层也是常见做法。但由此带来的是设备内衬材料需要承受更高温度负荷,以及更高的热损耗。根据本发明的工作衬,由于具有很低的热导率,完全可以不带中间内衬隔层地投入应用。借助以下示例,可以明显看出根据本发明的粗陶瓷产品,对比依据de102013020732a1最近技术水准的产品,以及对比已知的紧实产品,所具有的独特优势。示例1到3根据本发明的烧结氧化镁的生产制备:由多孔烧结氧化镁构成的颗粒的制备过程如下:将利用真空压力机由mg(oh)2悬浮液制得的,固态物质含量>50%的滤饼送入炉内干燥,然后在1100℃下煅烧和粉碎,这样即可由mg(oh)2形成氧化镁,其典型的颗粒尺寸分布为d50=10μm。利用颗粒压制机,将苛性镁压制成13x20x30mm3尺寸的杏仁状颗粒。新制颗粒具有2.0g/cm3的体积密度。这些颗粒将在高温实验室炉内采用一种温度曲线图进行烧结,在此温度走向下,温度以2k/min升高到800℃。经过6小时的逗留时间后,继续以2k/min使温度升高到1450℃。该温度下的逗留时间为5小时。冷却则通过高温实验室炉向周边环境散热而连续实现。接下来打碎多孔烧结氧化镁,进行筛滤分类。根据本发明的由多孔烧结氧化镁构成的颗粒具有2.59g/cm3的体积密度。相应的疏松显气孔率占体积百分比为25.8%(dinen993-18:2002-11;dinen993-1:1195-04)。示例1:示例1当中,以同样材料及同样矿物质成分(重量百分比占84%的氧化镁,重量百分比占16%的烧结尖晶石,由紧实烧结氧化镁构成的氧化镁粉)为基础生产制备型砖:表3:示例1中的回填料的组成成分所使用的原材料具有以下特性:表4:根据本发明的烧结氧化镁的特性表5:型砖b)和c)的紧实烧结氧化镁的特性表6:型砖a),b)和c)的烧结尖晶石的特性型砖a)至c)的生产制备分别如下:将相应的原材料按照表3、颗粒尺寸分布按照fuller,放在一个混合容器内进行3分钟干式混合,倒入液态粘合剂,继续混合5分钟。将这些混合物放到一台液压式压力机上,按照表3的压制压力,压制成旋转炉型砖所需的b-型。将这些型砖放在一台干燥机内以大约130℃进行干燥,随后在一个隧道式火炉内以1600℃进行50小时氧化煅烧。最高温度下的逗留时间为5小时。通过测量外形尺寸测得煅烧干缩率,通过测量外形尺寸和称重测得成品体积密度,按照dinen993-1:1995-04测定疏松显气孔率,按照dinen993-5:1998-12测定低温耐压强度,按照dinen993-6:1995-04测定低温耐弯曲强度,按照dinen993-4:1995-04测定透气率,以及按照dinen993-15:2005-14根据平行热线法测定热导率。耐温度变化稳定性根据din993-11:2008-03,针对1100℃的提高的检测温度下的空气来进行测定:表7:示例1中的经过焙烧的型砖的特性型砖a)型砖b)型砖c)体积密度[g/cm3]2.682.952.63显气孔率,占重量百分比[%]24.116.025.2低温耐压强度[mpa]887080低温耐弯曲强度[mpa]5.985.66.0空气渗透率[npm]0.851.61.2煅烧干缩率[%]1.180.300.60d50气孔直径[μm]3.814.210.4耐温度变化稳定性[循环次数]>30>30>30热导率300℃[w/mk]5.46.75.5700℃[w/mk]3.55.13.61000℃[w/mk]2.64.02.8与传统紧实的型砖b)相比较,a)同时还有c)的型砖特性均有变化,显气孔率明显更高,体积密度明显降低,但对于其他的型砖特性并没有带来负面影响。根据本发明的型砖,尤其在透气性及气孔直径方面是有所降低的。根据本发明的a)情况下,颗粒是由根据本发明的多孔氧化镁而构成的,对比b)来说,体积密度有着明显降低同时疏松显气孔率有着明显提高。另外,对比b)和c),平均气孔直径d50有着很大幅度的降低,这样一来,抗碱及抗熟料熔体的抗渗透性能有所下降。对比b)来说,低温耐压强度及低温耐弯曲强度仍稳定保持在对于紧实型砖来说的典型范围内。>30次淬火循环次数而不出现断裂现象,对于所有型砖种类来说,耐温度变化稳定性均保持在同样的必要的高水平上。同时结果还表明,根据本发明的a)型砖对比紧实的氧化镁尖晶石型砖b)来说,导热率的数值有着明显降低。示例2:代替示例1中采用的烧结尖晶石,示例2中的型砖d)采用多孔尖晶石:表8:示例2中的回填料的组成成分d)的根据本发明的氧化镁的特性相当于示例1中的相应特性。表9:型砖d)采用的多孔烧结氧化镁的特性型砖d)采用类似于示例1的方式来生产制备及检验:表10:示例2中的经过焙烧的型砖的特性型砖a)型砖b)型砖d)体积密度[g/cm3]2.682.952.64显气孔率,占体积百分比[%]24.116.025.2低温耐压强度[mpa]887085低温耐弯曲强度[mpa]5.985.66.4空气渗透率[npm]0.851.60.92煅烧干缩率[%]1.180.301.2d50气孔直径[μm]3.814.24.2耐温度变化稳定性[循环次数]>30>30>30热导率300℃[w/mk]5.46.75.2700℃[w/mk]3.55.13.31000℃[w/mk]2.64.02.4相比示例1中的型砖,采用了多孔氧化镁和多孔尖晶石后,型砖特性仅出现很少的变化,但可以观察到,热导率继续有所下降。所有其他的有积极作用的机械特性和热特性保持不变。示例3:在第一个和第二个示例当中已针对根据本发明的多孔烧结氧化镁对于氧化镁尖晶石型砖所带来的优点进行了阐述。为了证明本发明对于由其他他耐火材料所构成的产品也具有有效性,在示例3当中,已针对基质为烧结氧化镁同时组合有熔体镁铁尖晶石(镁铁熔体尖晶石)的型砖进行了研究。型砖e)采用根据本发明的烧结氧化镁为基质,用来比较的型砖f)为含有紧实烧结氧化镁的型砖。生产制备如同示例1,煅烧温度为1450℃:表11:示例3中的回填料的组成成分型砖e)型砖f)根据本发明的氧化镁0-4mm占重量百分比[%]54紧实烧结氧化镁0-4mm占重量百分比[%]54熔体镁铁尖晶石0-4mm占重量百分比[%]1616氧化镁粉,≤200μm3030木质素磺酸盐粘合剂,相对于干物质总量,占重量百分比[%]3.73.7压实度[mpa]130130煅烧温度[℃]14501450表12:型砖e)和f)的熔体镁铁尖晶石的特性以下表格显示示例3的结果:表13:示例3中的经过焙烧的型砖的特性型砖e)型砖f)体积密度[g/cm3]2.663.00显气孔率,占体积百分比[%]24.815.7低温耐压强度[mpa]98100低温耐弯曲强度[mpa]6.256.75空气渗透率[npm]0.981.45煅烧干缩率[%]1.120.20d50气孔直径[μm]4.814.6耐温度变化稳定性[循环次数]>30>30热导率300℃[w/mk]5.36.9700℃[w/mk]3.45.31000℃[w/mk]2.54.2表4显示,根据本发明的多孔烧结氧化镁也可以用于氧化镁镁铁尖晶石型砖上,由于使用了根据本发明的烧结氧化镁,多孔度有显著提高,所有积极作用的机械特性和热特性保持不变。当前第1页12