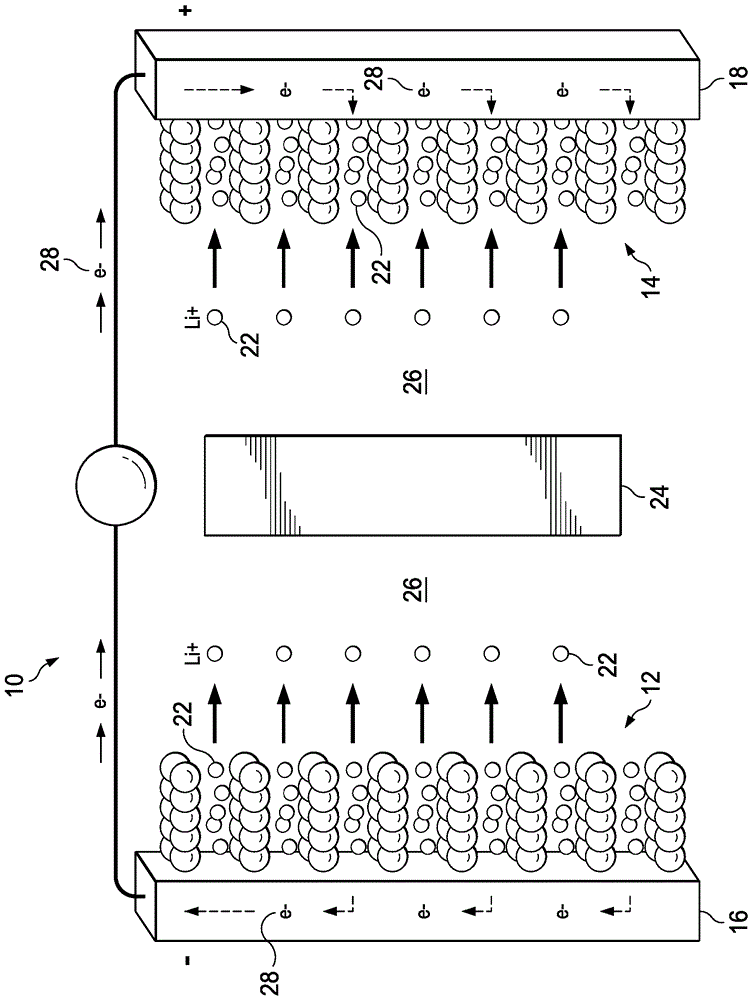
相关申请的交叉引用本申请要求2017年9月13日提交的标题为“batteryelectrodematerials”(电池电极材料)的美国临时申请号62/558107的优先权,其公开内容整体通过引用结合到本文中。背景本公开主要涉及用于锂离子电池的硅基高容量负极(阳极)活性材料。具体地讲,本公开描述一种硅基纤维材料,该材料显示与标准商业级硅相比改善的循环寿命以及与石墨阳极材料相比改善的容量。锂离子电池在过去的十年里激增,现在是为电子装置、无绳设备和车辆提供便携式电源的首选电源。随着技术变得越来越依赖锂离子电池电源,锂离子电池行业努力扩展其电池(cell)的性能,以便为最终用户提供最大的多功能性。石墨常用于锂离子电池,这是由于其能够经几百个循环保持稳定并发挥其功能,且几乎没有或没有容量损失。硅显示作为阳极材料的广阔前景,这是由于其相对于当前行业标准的石墨(372mah/g)的极高容量(4000mah/g)。然而,硅有在锂化时溶胀350%的限制。这种溶胀可导致严重破坏内部电池结构,并造成容量快速损失,因为电池组件受损,且阳极自身碾压成更小的碎片,并最终失去电连接性。因此,持续需要改进的硅基阳极材料和制备这种硅基阳极材料的方法。附图简述包括以下附图是为了说明本发明的某些方面,而不应将其视为排它性实施方案。所公开的主题能够在形式和功能上进行相当多的修改、变更和等同,这些会被在本领域且受益于本公开的普通技术人员想到。图1示出包含阳极和阴极的锂离子电池的示意图;图2为实施例1的还原混合物的x-射线衍射(xrd)扫描图;图3为在用酸洗涤后实施例1的还原混合物的x-射线衍射(xrd)扫描图;图4示出根据本公开的实施方案mg/sio2比率对sio2转换成si的百分数的影响;图5示出根据本公开的实施方案mg/sio2比率对硅基纤维表面积的影响;图6示出根据本公开的实施方案mg/sio2比率对硅基纤维中值孔径的影响;图7示出根据本公开的实施方案mg/sio2比率对硅基纤维孔隙率的影响;图8为商业硅的第一循环结果的曲线图;图9为商业石墨的第一循环结果的曲线图;图10为根据本公开的实施方案的实施例3和4的样品1的第一循环结果的曲线图;图11为根据本公开的实施方案的实施例3和4的样品5的第一循环结果的曲线图;图12为根据本公开的实施方案的实施例3和4的样品2的第一循环结果的曲线图;图13为根据本公开的实施方案的实施例3和4的样品10的第一循环结果的曲线图;图14为根据本公开的实施方案的实施例3和4的样品11的第一循环结果的曲线图;图15为商业硅的容量对循环的曲线图;图16为商业石墨的容量对循环的曲线图;图17为根据本公开的实施方案的实施例3和4的样品1的容量对循环的曲线图;图18为根据本公开的实施方案的实施例3和4的样品5的容量对循环的曲线图;图19为根据本公开的实施方案的实施例3和4的样品2的容量对循环的曲线图;图20为根据本公开的实施方案的实施例3和4的样品10的容量对循环的曲线图;并且图21为根据本公开的实施方案的实施例3和4的样品11的容量对循环的曲线图。详述本公开描述了具有约0.1微米至约20微米直径、高表面积(例如,约5至约400m2/g表面积)和互连或离散孔隙的多孔还原二氧化硅纤维。本文所用“表面积”为通过brunauer-emmett-teller(bet)技术测定的表面积。在一些实施方案中,多孔还原二氧化硅纤维具有约30至约300m2/g的表面积。在本文中提及任何范围的数字时,在本文中具体包括该范围内的每个数字。在各种实施方案中,多孔还原二氧化硅纤维基本不含二氧化硅。“基本不含”是指小于20重量%,例如小于10重量%,小于5重量%,或小于1重量%。在一些实施方案中,多孔还原二氧化硅纤维具有约0.1至约0.7cm3/g的孔隙率。在其它实施方案中,多孔还原二氧化硅纤维具有约0.01至约1.5cm3/g的孔隙率。通过在多孔还原二氧化硅纤维内提供内部孔隙,产生内部体积,其可容纳至少一部分硅膨胀,而不破坏纤维外部或电极结构。多孔还原二氧化硅纤维能够从电解质接受锂离子和使锂离子释放到电解质。本公开还描述了制造在锂离子电池中用作阳极的多孔还原二氧化硅纤维的方法。这些方法依靠形成sio2基纤维(即,二氧化硅基前体),并且使其经过各种过程,以使其纯化成主要二氧化硅化学物质,和/或在二氧化硅基前体纤维中产生内部孔隙。然后使二氧化硅基前体纤维经过热化学还原过程,以得到包含硅和任选夹杂sio和/或sio2的还原二氧化硅纤维。如下进一步描述,二氧化硅基前体纤维可通过玻璃熔融或化学方法例如溶胶-凝胶法产生。在各种实施方案中,二氧化硅基前体纤维的孔隙通过如下来有意引入:通过化学浸提,通过热处理,通过用溶胶-凝胶法从胶体微粒的聚集体形成二氧化硅基前体纤维,或通过从溶液形成二氧化硅基前体纤维,和将精细分散的聚合物引入纤维化溶液,该纤维化溶液在烧尽时在纤维中留下多孔腔体(即,聚合物模板化),或它们的任何组合。然后执行化学还原过程和随后的纯化方法,以从二氧化硅基前体纤维去除一些或全部化学结合氧,从而留下具有包括硅(si)和/或一氧化硅(sio)的化学物质的材料。该材料还可包括残留硅石或二氧化硅(sio2)。将该材料称为还原二氧化硅纤维。在几个实施方案中,用标准电池制造技术从还原二氧化硅纤维形成电极。在用于锂离子半电池或全电池时,这种电极有利具有比现有石墨电极更高的容量,并且具有与可比商业硅相比改善的循环寿命。在其它实施方案中,将由还原二氧化硅纤维形成的纤维纸用作阳极,从而排除对集电器的需求。在某些实施方案中,制造具有约0.1微米至约20微米直径的熔融得到的二氧化硅基前体纤维。然后可化学处理(即,浸提)这种纤维,以去除非二氧化硅成分,从而留下主要二氧化硅组成的纤维。然后可使这种纤维经过热还原步骤,以通过去除氧使二氧化硅转化成金属硅。在其它实施方案中,通过溶胶-凝胶法制造直径约0.1微米至约20微米且有受控孔隙率的二氧化硅基前体纤维,然后经过还原步骤,以产生还原二氧化硅纤维。还原二氧化硅纤维的尺寸和/或孔隙率可足以在锂化时容纳高膨胀,从而避免损伤阳极,并因得益于硅的高容量而实现长电池寿命。本文所用“容量”是指可被电池输送的总电荷的量度,并决定了电池在指定负载条件下可提供的运行时间。在实际意义上,容量决定了电池的使用小时数。将容量测定为输送电流乘以输送持续时间的乘积。通常以安培·小时或毫安·小时(mah)引述。比容量由电池的每单位重量或体积的总容量定义。可引述比容量用于单独活性材料(阳极或阴极材料)、单个电池(包括活性材料、集电器、电解质和“罐”或壳)或整个电池包。单位通常引述为安培小时每克(a·h/g)或安培小时每立方厘米(a·h/cm3)。本文所用“循环寿命”是指在电池的容量下降到低于其原始容量的80%之前电池能够支持的完全充电/放电循环次数。本文所用“容量保持率”是指电池在已循环或储存一段时间后,在规定放电条件下可从电池获得的全部容量的分数。随着使用和时间的流逝,电池会经历其内部组件的物理变化。这可能由电解质的消耗/转化、在阳极和阴极上形成经反应层(称为固体电解质界面或sei)或由于随充电/放电循环发生的溶胀/收缩物理而损坏内部电池结构(通常会损失组成阳极或阴极的颗粒之间的电连接性)来驱动。总体结果是总电池容量减少。在电池的整个工作寿命得到的放电曲线表明容量逐渐减少。电池有效寿命结束的定义有些随意,但通常认为是容量减少20%,剩下原始容量的80%可供使用。除了更高的容量和改善的循环寿命,由还原二氧化硅纤维制成的电极还可促进改善充电/放电速率。还原二氧化硅纤维具有高表面积和减小的体积(高sa/v比)。这允许锂迅速进入和离开结构(表面限制的反应),并且还减小了锂一旦进入结构必须扩散的距离。本文所用“充电速率”是指将电流施加到电池以恢复其容量的速率。电池速率性能是电池向负载输送指定电流或在充电过程中接受指定电流的能力的量度。速率性能由放电曲线表示,该曲线标绘了指定充电/放电电流下的电池电压(垂直轴)对时间(水平轴)。已发现,随着电流增加,电池经长时间段接受或提供稳定电压的能力会减弱。在这个意义上,电池容量往往随着速率增加而降低。使锂移入和移出阴极和阳极材料的能力是以高速率获得稳定电压和长运行时间的限制因素。作为动力学参数,充电/放电速率也与电池的温度性能相关。本行业期望能够在使用中通常遇到的极端温度下令人满意地工作的电池。通常将速率称为“c”值。“c”充电速率将在1小时内充满指定电池的全部容量。“2c”充电速率将在30分钟内充满相同的电池。“c/2”充电速率将在2小时内充满相同的电池。锂离子电池结构典型的锂离子电池组电池包括金属外壳。在金属外壳内封闭阴极(即,正极)、阳极(即,负极)和隔板。在典型的圆柱形锂离子电池中,阴极、阳极和隔板以薄片的长螺旋卷的形式提供。或者,在软包电池或币式电池的情况下,它们可以堆叠或z形折叠构造提供。使阴极片、阳极片和隔板片浸入充当电解质的溶剂中。隔板在物理上和电学上分隔阳极和阴极,同时允许锂离子通过它。在典型的锂离子电池中,阴极由混合的锂-金属氧化物材料制成,例如,氧化钴锂(licoo2)、磷酸铁锂(lifepo4)或氧化锰锂(limn2o4)。其它阴极材料尤其包括亚锰酸锂(li2mno3)和钛酸锂(li4ti5o12)。在普通的常规锂离子电池中,阳极由碳制成,例如石墨。在电池吸能的充电过程中,锂离子从阴极通过电解质移到阳极,并附着到碳或与碳缔合。在电池供能的放电过程中,锂离子从碳阳极通过电解质移回到锂-金属氧化物阴极。锂离子电池中的液体电解质包括有机溶剂中的锂盐,有机溶剂如碳酸亚乙酯、碳酸二甲酯和碳酸二乙酯,锂盐如六氟磷酸锂(lipf6)、四氟硼酸锂(libf4)或高氯酸锂(liclo4)。在充电和放电两个过程中,锂离子穿过隔板层,隔板层通常可以为穿孔的塑料薄片,其分隔阴极和阳极,但允许锂离子流动。现在转向图1,图1显示包含阳极和阴极的锂离子电池的示意图。锂离子电池10包括负极或阳极12和正极或阴极14。根据本公开,阳极12包括具有细直径、高表面积以及互连或离散孔隙的还原二氧化硅纤维。阴极14可包括具有细直径、高表面积以及互连或离散孔隙的包含锂的混合金属氧化物纤维。铜集电器16与阳极12电接触并缔合,铝集电器18与阴极14电接触并缔合。锂离子22与阳极和阴极材料缔合。渗透性聚合物隔板24使正极材料与负极材料隔开,但允许锂离子22穿过电极12,14之间的电解质26。在锂离子电池10放电期间,锂离子22从阳极12通过电解质26移到阴极14,使电子28围绕电路以相反的方向移动,从而为负载供电。给电池10充电迫使锂离子22跨过隔板24移回,以与阳极12缔合,从而允许下一个放电循环。通常,形成本公开的硅基阳极的方法包括四个步骤:(1)制造前体二氧化硅纤维;(2)使前体二氧化硅纤维经过还原步骤,以去除氧,并产生还原二氧化硅纤维;(3)洗涤和纯化还原二氧化硅纤维;和(4)用经洗涤和纯化的还原二氧化硅纤维形成电极,以用于锂离子电池。通过纤维溶液纺丝法制造二氧化硅基前体根据几个实施方案,二氧化硅基前体纤维通过用溶胶-凝胶或溶液纺丝过程产生二氧化硅纤维来制造,然后可使其进一步还原成硅。在此过程中,将二氧化硅前体与其它化学物质一起放入溶液或分散体(溶胶),以产生缩合/交联反应,所述二氧化硅前体为例如胶体二氧化硅;硅氧烷,例如五乙氧基丙烷二硅氧烷(peds);水玻璃(可溶性碱性硅酸盐(例如硅酸钠));或烷氧基硅,例如原硅酸四乙酯(teos)、原硅酸四甲酯(tmos)、甲基三乙氧基硅烷(mtes)或甲基三甲氧基硅烷(mtms)。胶体二氧化硅可包括可得自akzonobel的levasil®或可得自cwk、grace、merck、bayer、nalco或dow的其它胶体二氧化硅产品。另外,通过向纺丝溶液引入具有适合溶解度/浊点特性的聚合物/表面活性剂,可在纺丝产品中产生模板化孔隙,如下和欧洲专利申请0318203和美国专利号5,176,857中更详细地描述,各文献的公开内容整体通过引用结合到本文中。表面活性剂的实例包括烷基乙氧基化物、烷基苯基乙氧基化物、聚环氧丙烷-聚环氧乙烷嵌段共聚物、梳型硅氧烷-聚乙氧基化物共聚物和聚乙氧基化胺。这在初生纤维中引入胶束,其在最终的纤维结构中留下受控尺寸的孔。通过控制表面活性剂的加入和溶液或溶胶中所得胶束的尺寸,可直接控制最终产品中孔的体积和尺寸。可将孔径向下控制到几十埃或纳米的水平。通过控制溶液的温度,可使纤维化发生在聚合物/表面活性剂的浊点或刚好高于该浊点。“聚合物的浊点”定义为聚合物变得不溶于溶液并开始形成细分的第二相所在的温度。所得聚合物胶束用于在溶液中形成模板化聚合物相区。随着材料拉丝(attenuating,即,拉伸)成纤维形状,聚合物相伸长,形成轴向取向的孔隙。通过使用特定浓度的聚合物,控制溶液、纤维化和纤维化气氛中的温度、剪切速率、纤维化气氛的相对湿度以及其它变量,可控制孔径和体积。一旦形成,就可使纤维经过特定热处理方案,以分解有机物质(例如,纤维化助剂和模板聚合物),并实现胶体二氧化硅内的交联和结合。可将某些聚合物加到该溶液或溶胶,以提供纤维化必需的流变性,这些聚合物例如聚环氧乙烷、聚乙烯醇、聚乙二醇;纤维素,例如甲基纤维素或乙基纤维素;聚乙烯吡咯烷酮;或淀粉。可通过本领域普通技术人员已知用于溶胶-凝胶纤维化的任何方法进行纤维化,例如溶液纺丝、挤出、吹制或电纺丝。在一些实施方案中,用于制造前体二氧化硅纤维的溶胶-凝胶过程包括使具有约1和约1000泊之间粘度的液体纤维化,例如约70和约300泊之间,在另一个实例中约100至约450泊。由于水的成本低、可用性和低毒性,用于溶胶-凝胶过程的一种适合的溶剂为水。在某些情况下可使用其它极性溶剂,例如甲醇、乙醇和丙酮,其条件为选择适当的氧化物前体。也可使用一些非极性化合物,例如辛烷、苯或甲苯。液体通过任何便利的方法纤维化,例如离心纺丝、电纺丝、拉伸、吹制、粘着纺丝(tack-spinning)、通过喷丝头挤出液体、或它们的适合组合。可用对本领域普通技术人员显而易见的任何方法将液体纺丝。在液体纤维化(例如通过纺丝)后,干燥和加热所得纤维,任选在含氧气氛中经足够的时间和在足够的温度,以在纤维中使化合物转化成氧化物。通过任何适合的方法干燥纤维,例如通过在约30℃至约150℃的温度下、任选在减压下加热纤维。可用任何其它适合的方法干燥纤维,例如,通过使经去湿空气或气体围绕纤维循环。经干燥纤维加热足够的时间和在足够的温度,以去除溶胶的有机成分。用于二氧化硅/硅纤维的加热温度可在约400℃和约1000℃之间,例如在约650℃和约750℃之间。加热时间可超过约15分钟,并可超过约1小时。在某些实施方案中,溶胶-凝胶过程提供具有高比例轴向排列孔的二氧化硅基前体纤维的制造。在各种实施方案中,在二氧化硅基前体纤维中总孔隙的至少25%且通常比25%高得多的比例由轴向排列的孔提供,。在一些实施方案中,通过将一种溶液或溶胶纺成纤维得到轴向排列的孔,所述溶液或溶胶包含在加热时可分解成二氧化硅的化合物以及具有在纺丝溶液中高于纺丝温度但不高于纺丝温度之上20℃的浊点的非离子表面活性剂。随后加热纤维,以使化合物转化成二氧化硅。在一个实施方案中,纺丝温度为约25℃,并且表面活性剂具有在纺丝溶液中低于45℃的浊点。随着纺丝温度升高,表面活性剂的可接受浊点也升高。例如,对于约50℃纺丝温度,表面活性剂的浊点将低于70℃。在某些实施方案中,表面活性剂的浊点高于纺丝温度至少5℃,但不高于纺丝温度之上15℃。本文所用“纺丝温度”是指纺丝溶液或溶胶在纤维形成过程的挤出和垂伸(伸长)阶段达到的最高温度。因此,将溶液或溶胶挤出到加热的环境中将导致在垂伸(伸长)成生纤维期间溶液或溶胶中的温度升高。在这种情况下,纺丝温度为在完成垂伸(伸长)之前溶液或溶胶(生纤维)达到的最高温度。通常,纺丝温度将为拉丝空气的湿球温度。本文所用“表面活性剂的浊点”是指在加热时包含表面活性剂的纺丝溶液变得浑浊的温度。非离子表面活性剂的水溶液在加热时会变浑浊,这些的浊点可通过将装有约10ml溶液的沸腾管浸入冷的搅拌水浴,然后以1℃/分钟的速率加热浴来测定。管中的溶液不搅拌,或用刮铲非常轻地搅拌(以免产生气泡)。溶液在1-2℃内的窄温度范围变浑浊,然后可记下浊化温度或浊点。可使用几种化学类型的表面活性剂(如上所述)。应理解,在每一种这些化学种类的表面活性剂中,可能有浊点太高而不能在过程中使用的那些以及在过程中可用的那些。然而,测定表面活性剂的浊点以确定其在过程中的适用性是简单的常规实验事项。可用表面活性剂的共混物或混合物提供适合的浊点。在纺丝溶液中使用的表面活性剂的量可在宽范围内变化,但通常为基于纺丝溶液至少1%重量。该量可以为溶液重量的1%至30%,并且在某些实施方案中,为溶液重量的约3%至约10%。在几个实施方案中,除了表面活性剂外,纺丝溶液或溶胶还包含用于纤维的稳定添加剂和/或烧结添加剂的前体。在一个具体实施方案中,表面活性剂本身就可以为所得纤维中的相稳定剂或烧结剂的来源。例如,在加热纤维以使二氧化硅前体分解成二氧化硅时,用硅氧烷共聚物作为表面活性剂引起纤维中二氧化硅的生成。因此,对于二氧化硅纤维而言,其前体可掺入纺丝溶液或溶胶中的稳定剂为二氧化硅,例如硅溶胶。以这种方式产生的二氧化硅基前体纤维的直径可以为约0.1微米至约20微米,具体地讲,低于约10微米。在一个实施方案中,二氧化硅纤维的直径为约2微米至约15微米。这样的直径由纤维化条件(例如喷丝孔孔径)和被纤维化液体的特性(特别是液体的粘度)和液体中可氧化化合物的百分数来决定。液体中较高的粘度和较高的固体含量产生较大直径的纤维。二氧化硅纤维的密度在很大程度上取决于纤维已经历的热处理。在纺丝并至少部分干燥后,通常在约200℃至约600℃的温度加热二氧化硅基前体纤维,以分解有机氧化物前体。该加热步骤可使用或可不使用蒸汽。进一步加热纤维烧尽任何有机残余物,并交联所得二氧化硅纤维,然后任选更进一步加热纤维,以烧结二氧化硅纤维。在蒸汽处理后,二氧化硅纤维高度多孔,并且在对二氧化硅纤维加热到例如600℃至700℃期间保持高孔隙率。因此,通过控制烧结温度和存在的相稳定剂的量,可获得高孔隙率的低密度纤维。通常,较高的处理温度会使纤维收缩,并降低孔隙率。纤维可通过本领域普通技术人员已知的任何纤维形成技术来生产。例如,短纤维(切段纤维)和名义连续纤维都可通过吹纺技术或离心纺丝技术生产。连续纤维可通过常规挤出/卷绕技术来生产。在通过吹纺技术或离心纺丝技术生产的二氧化硅基前体纤维中,可使纺丝制剂形成多个纤维前体流,使其至少部分在飞行中干燥,以产生凝胶纤维,然后收集在适合的装置上,例如,在短(切段)纤维的情况下,所述装置为丝网,或者,在名义连续纤维的情况下,所述装置为高速旋转的卷筒。纺丝制剂可以为本领域普通技术人员已知用于生产溶胶-凝胶氧化物纤维的任何制剂,通常为不含或基本不含大小大于10微米的悬浮固体或凝胶颗粒的纺丝溶液或溶胶。在某些实施方案中,溶液或溶胶不含大小大于5微米的颗粒。所得二氧化硅基前体纤维基本为sio2,并且可包含由其胶体性质、由聚合物模板化过程或两者产生的孔隙。通过经浸提玻璃制造二氧化硅基前体纤维根据其它实施方案,二氧化硅基前体纤维可由熔融得到的二氧化硅基玻璃纤维制造,其组合物能够化学浸提以去除非二氧化硅成分,从而留下二氧化硅骨架。这样的组合物在行业上已知,并且可包括vycor®组合物(硼硅酸钠)、硅酸钠或能够通过化学处理(通常为酸处理,尽管可使用任何可行方法)浸出其非二氧化硅成分的任何其它组合物。一种这样的组合物包括铝硅酸钠(由unifraxspecialtyfibers,unifraxillc,tonawanda,n.y.生产),并用作经浸提二氧化硅纤维的前体。二氧化硅基前体纤维可通过任何适用的方法由二氧化硅基玻璃熔体生产,包括但不限于:吹制、离心纺丝、旋转纺丝、火焰吹制、漏板挤出、单丝挤出或电纺丝。由于化学浸提,二氧化硅基前体纤维可具有孔隙,并且这被认为为有益的,因为它增加表面积,并因此增加锂化的动力学,并且提供用于在锂化期间膨胀的空间。具体地讲,vycor®组合物具有相分离的益处。玻璃的可溶成分作为单独的相存在,其微结构可通过改变热处理的时间和温度来控制。这种微结构由以下相组成:一相,该相包含高浓度的氧化钠(na2o)和三氧化二硼(b2o3),其高度可溶于酸;和第二相,该相由约96%sio2组成,其相对不溶于酸。通过使这种材料经过酸浸提步骤,可去除na2o和b2o3酸可溶相,只留下96%sio2相。所得材料不仅具有高sio2含量,而且包含相当大的内部孔隙率。通过进一步热处理,从而引起孔隙的聚结,可调节孔隙率。这可形成互连或非互连的结构。利用vycor®组合物,可调节孔径和孔结构,以得到优选的结果。孔可调整成大或小,例如直径在约1埃(å)至约200å级,例如40å至约80å,和/或调整成互连或离散。这一特征适用于相分离玻璃(熔体或纤维)组合物,其中一相包含优先可溶物质。一个另外的实例为生产经浸提二氧化硅玻璃,例如作为belchem®纤维材料或valmiera纤维销售的材料。在这些材料中,玻璃纤维由可浸提玻璃组合物制造。然后使这些纤维在酸(通常hcl)中经过浸提步骤,以通过离子交换或浸提过程浸提出na2o或其它可溶成分,从而留下纤维状二氧化硅结构。这个策略可扩展到由二氧化硅基质组成且添加可浸提成分的相似可溶玻璃纤维的任何范围,所述可浸提成分如na2o、b2o3、氧化钾(k2o)、氧化锂(li2o)、氧化钙(cao)、五氧化二磷(p2o5)或氧化镁(mgo)等。这些纤维可在酸性、中性或碱性溶液中经过浸提,以实现生产二氧化硅纤维所需的浸提。根据玻璃和浸提条件,这些材料也可显示高表面积和显著的内部孔隙率。要用作原料的示例玻璃纤维包括低生物持久性耐火纤维,例如isofrax®纤维、insulfrax®纤维、superwool纤维或superwoolht纤维,或stonewool类型的产品,例如stonewoolht纤维。在一些实施方案中,二氧化硅基前体纤维由玻璃纤维制备。由玻璃纤维制备二氧化硅纤维的方法描述于美国专利号2,215,039、2,221,709、2,461,841、2,491,761、2,500,092、2,624,658、2,635,390、2,686,954、2,718,461和2,730,475,各文献的公开内容整体通过引用结合到本文中。具有高比表面积、高拉伸强度、一致的玻璃化学性质和纯度的玻璃纤维可从unifraxspecialtyfibers(tonawandan.y.)获得。这些纤维通过旋转和火焰拉丝制造过程生产。平均纤维直径范围从极细0.1µm到5.0µm。在下表列出了典型的玻璃纤维组成。表1:玻璃纤维组成(重量百分数)*b2o3包含31.1%重量硼。a玻璃中的最大容许硼含量为0.028%。通过从玻璃纤维提取单价、二价和三价金属氧化物成分以留下纤维,可使玻璃纤维转变成更纯的高二氧化硅纤维,留下的纤维基本由二氧化硅组成,并且包含相比90份二氧化硅小于10份此类金属氧化物、甚至低至1或2份此类氧化物的比率,剩余氧化物部分为二氧化硅。这可通过以足以提取二氧化硅以外的基本所有氧化物的时间和温度用侵蚀二氧化硅的氢氟酸或磷酸以外的酸浸提为疏松块或为制成形式的纤维来实现。然后,经处理纤维洗涤成基本无酸,并且如果需要,可在高温下加热,以使纤维脱水和收缩。以上过程可使纤维在直径和纵向同时收缩。适合的浸提酸包括例如盐酸(hcl)、硫酸(h2so4)、硝酸(hno3)、乙酸(ch3cooh)、氯乙酸(clch2cooh)和氯化的低分子量脂肪酸,例如,三氯乙酸。酸的强度可在宽范围内变化,例如0.1n至5n或更高。浸提过程可在100℉至酸的沸点或高于沸点的高温下通过在高压釜中超大气压下进行浸提来发生。可能合宜的是如下使纤维收缩,通过在高温下脱水足够的时间,以去除基本上所有的水合水和所有的吸附水,例如,通过加热到约400℉至500℉或更高的温度足以去除水合水和吸附水的时间,而不使纤维实质收缩。可很容易用酸浸提硼硅酸盐玻璃纤维,以去除二氧化硅以外的金属氧化物,并且可通过加热到约1000℉的温度来脱水,例如在约1400℉至约1600℉的范围内。通过适当控制酸提取过程,在烧制后得到的纤维包含高含量二氧化硅,通过湿化学法测定,可高达90%,甚至基本上为99.9%二氧化硅。由二氧化硅基前体纤维生产还原二氧化硅纤维在形成硅基前体纤维后,脱去至少某一部分化学结合的氧,以获得包含单质硅的纤维。为了用作电池阳极,所得产物可包含金属硅、一氧化硅和/或二氧化硅。硅、一氧化硅及其合金和组合具有电化学活性,并且可用作锂离子电池中的阳极材料。在某些情况下,混合的合金态可能特别合宜,因为它允许在锂化时控制材料膨胀(取决于合金状态),并且可能匹配可用的孔空间,从而可在孔空间中容纳膨胀。从材料去除结合氧的热化学方法在本文中称为“还原”。这可通过任何种类已建立的方法来完成,包括在一氧化碳(co)气氛、氢气氛中与镁、铝或碳接触或任何其它有效方法还原。可严格控制这个反应的温度,以影响或保持纤维的多孔结构,确保其处于希望或最佳的范围。这个类型的反应通常在采矿和金属行业中用于使材料的天然存在氧化态转化成还原态,在还原态它不再与氧化合,而以金属态存在。含有氧化铁(fe2o3)的铁矿转化成金属铁是还原反应的一个实例。另一个是铝热反应,其中将氧化铁与铝粉混合并点燃,使氧从氧化铁脱去并与铝化合,留下氧化铝和金属铁。通过使要还原的氧化物与对氧具有更大化学亲和力的第二材料的金属形式混合,可实现还原。然后将这种混合物加热到高温,以使反应能够自发发生。在二氧化硅的情况下,可使用诸如碳(碳热还原)或铝(铝热还原)或钙的材料。然而,这些过程的缺点是需要过高的温度,这会影响所得硅的物理状态,导致其熔融,或严重降低孔隙率或表面积以及通过烧结生长晶粒。除了高氧亲合力的固体外,还可用诸如氢气(h2)和一氧化碳之类的气体实现还原。然而,它们还原二氧化硅的能力略受限制。用镁还原二氧化硅(镁热还原)是非常有用的方法,因为它可在相对较低的温度(600℃–700℃)下完成,并允许保留前体二氧化硅材料中可能存在的微结构。具体地讲,可通过低温镁热还原保留和/或增强通过聚合物模板化或其它方法获得的多孔高表面积结构。在一个实施方案中,二氧化硅基前体纤维可通过用镁粉的高温处理来还原,并转化成包含硅(si)或其它sio2的还原形式的结构。与其它方法例如碳热还原(>1600℃)或电化学还原相比,通过镁还原二氧化硅可以低得多的温度(650℃)和更短的持续时间(30分钟)操作。通过将材料浸入1-2mhcl溶液,可从还原的混合物提取还原二氧化硅纤维,所述hcl溶液溶解mg基成分而不影响si种类,从而保持纤维形态。还原二氧化硅纤维的洗涤/纯化在还原后,所需的si/sio材料与来自还原的其它反应产物紧密结合存在,所述其它反应产物例如氧化镁(mgo)、硅化镁(mg2si)和镁橄榄石(mgsio4),在此只举几个例子。需要纯化该材料,以去除不需要的物质,从而留下相对较纯的si/sio。这可通过在酸、特别是hcl中洗涤该材料来完成。反应产物mgo、mg2si、mgsio4等可溶于酸,而si、sio和sio2不溶于酸。因此,洗涤过程去除了不需要的成分,并留下硅合金,可通过过滤溶液回收硅合金。用经洗涤/纯化的还原二氧化硅纤维形成电极用于锂离子电池用上述方法合成的包含siox(x=0–2)的还原二氧化硅纤维可用于其中siox可能有用的任何应用。这可包括传感器、微电子器件,尤其是锂离子电池。硅作为阳极材料在锂电池组电池中得到了应用,用于在电池处于充电状态时储存锂。当需要来自电池的电流时,阳极将其锂内容物释放到电解质,在此它在电池放电时扩散进入反电极。由于能够经几百个循环保持稳定并发挥其功能,且没有容量损失,石墨常用于锂离子电池。硅的优点是,与石墨相比,能够保持每单位重量超过10倍量的锂。然而,如前所述,硅具有在锂化时显著溶胀的缺点。通过合成具有内部孔隙的硅材料,可以预料,通过酌留让膨胀占据的内部空间,会减轻溶胀的负面影响。在构造锂电池组电池阳极时,通常使电化学活性阳极材料与其它组分混合,形成粘性浆料,并施加到铜箔集电器上。一旦施加到集电器,一般就将电化学活性材料和添加剂与集电器的组合称为阳极。可以类似于标准石墨和硅/siox粉末的方法用还原二氧化硅纤维制备阳极。它可以纤维形式使用,或者可研磨到任何纤维长度范围,或者可研磨或粉碎成粉末,使得纤维长径比不再存在。还原二氧化硅纤维可用作唯一的活性材料,或者可与其它活性材料共混,其它活性材料包括但不限于石墨、其它硅合金材料、氧化锡(sno)或有作为阳极材料的实用性的任何其它材料。这些活性材料可进一步与其它电极组分混合。例如,它们可与炭黑或碳纳米管混合,以提供通过电极材料的电连接性。它们也可与粘合剂混合,一旦材料置于集电器上,粘合剂就可用来使该材料保持在一起。然后通过任何适合的方法,例如辊涂、浸涂或刮刀涂覆,将阳极材料和粘合剂/粘度调节剂的混合物施加到铜箔集电器上。在一些情况下,还原二氧化硅纤维可形成由纤维和任选粘合剂组成的纸,或者该纤维可简单地自缠结,而没有粘合剂。硅基纤维纸可包含用于电连接的先前所述的其它添加剂——炭黑或碳纳米管。它可包含增加机械完整性的载体纤维,或出于任何原因认为必要的任何其它添加剂。还原二氧化硅纤维也可用任何认为有利的材料涂覆。具体地讲,可将薄的碳涂层施加到纤维上,以通过提高纤维电导率和/或抑制过量sei形成来帮助循环寿命。也可出于任何其它原因来施加涂层。将碳涂层施加到还原二氧化硅纤维的一种有利方法包括热解气相沉积法。在这种方法中,将还原二氧化硅纤维在受控惰性气氛中在高温(例如,在氩气/氢气(ar/h2)(形成气体)下950℃)保持。引入包含含碳成分的气体(例如乙炔或其它烃气体),并经过分解,从而在纤维表面上留下碳沉积物。可使用多种惰性气氛,例如,氦气(he)或氩气(ar)或其组合。根据反电极的性质,可将用此方式制成的电极以阳极或阴极的角色用于锂离子电池。阴极纤维在各种实施方案中,提供包括混合金属氧化物纤维的锂离子电池阴极材料,所述混合金属氧化物纤维具有约0.1至约20微米范围的直径、高表面积以及互连或离散的孔隙,其中阴极材料能够从电解质接受锂离子和使锂离子释放到电解质。根据某些实施方案,混合金属氧化物纤维可具有约5至约400m2/g的表面积,或者,在一些实施方案中,约60至约140m2/g的表面积。根据某些实施方案,混合金属氧化物纤维可具有约5%至约60%的孔隙率。根据某些实施方案,混合金属氧化物纤维可包括锂的氧化物以及铝、钴、铁、锰、镍、钛和钒中至少一种的氧化物。根据某些实施方案,混合金属氧化物纤维可包括氧化钴锂(licoo2)、氧化钴锰镍锂(lini0.33mn0.33co0.33o2)、氧化铝钴镍锂(lini0.8co0.15al0.05o2)、高锰酸锂(limno4)、磷酸铁锂(lifepo4)、氧化锰锂(limn2o4)、亚锰酸锂(li2mno3)和钛酸锂(li4ti5o12)中至少一种。根据某些实施方案,混合金属氧化物纤维包括直径0.1至约100nm或约0.5至约25nm的孔。阴极纤维的形成在整个行业中,将各种各样的材料用于锂离子电池阴极。这些材料通常为含锂的金属氧化物,可包括(但不限于)二硫化钛锂(litis2)、氧化钴锂(licoo2)、氧化钴锰镍锂(lini0.33mn0.33co0.33o2)、氧化铝钴镍锂(lini0.8co0.15al0.05o2)、高锰酸锂(limno4)或磷酸铁锂(lifepo4)。已用很多合成路线生产了阴极材料,包括溶胶-凝胶法,这将在下面进一步描述。在溶胶-凝胶法中,金属盐可在溶液中溶解并混合,然后沉淀成胶体悬浮液(溶胶)。该胶体悬浮液可通过减小水含量来胶凝。然后将材料干燥,使组分之间发生无机聚合反应。进一步热处理导致去除盐阴离子和任何有机物质,并使剩余的氧化物材料增浓和结晶。在各种实施方案中,高表面积阴极材料通过以下方法制备。首先,形成一种溶液或溶胶,该溶液或溶胶包含实现阴极材料适合化学计量所需比例的所需金属盐或化合物。在某些实施方案中,液体包含约10至约70重量%的将要包含在锂离子电池电极中的无机氧化物的可氧化前体化合物。前体化合物可包括电极金属的溶剂可溶盐。适合无机盐的实例为金属硝酸盐、氯化物和氯氧化物。适合有机盐的实例为低级烷基有机酸的金属盐,例如乙酸盐、氯乙酸盐、甲酸盐、羟基乙酸盐、丙酸盐或丁酸盐;或低级烷基羟基酸的金属盐,例如乳酸盐。另外,一些盐可以共混物或混合物形式使用。应了解,基本上任何可在溶剂中溶解形成可纤维化的溶液并且在含氧气氛中加热到足够温度时产生金属氧化物纤维的化合物都可用作无机氧化物前体,例如硅的烷氧化物和金属铝(al)、钴(co)、铁(fe)、锰(mn)、镍(ni)、钛(ti)和钒(v)的烷氧化物。在一个实施方案中,在溶液或溶胶中包含纺丝助剂,例如有机聚合物,作为纺丝助剂提供纤维化所需的流变性。也可包括被认为对成品合乎需要的任何其它材料(包括但不限于相变抑制剂或金属氧化物粉末,用于增强性能)。可用建立的纤维化方法使从溶液或溶胶得到的材料纤维化。此类方法包括但不限于(1)将溶液或溶胶提供到旋转盘,在此可将其离心挤出成纤维;(2)将溶液或溶胶提供到挤出喷嘴(或其组合件),并将溶液或溶胶(利用或不用拉丝气流)挤出为连续或不连续的纤维;或(3)电纺丝。在制造纤维状阴极材料的过程中,可通过在包含前体金属盐的溶液相中包含非离子表面活性聚合物试剂,将孔隙引入纤维结构,如下和欧洲专利申请0318203和美国专利号5,176,857中更详细地描述的,各文献的公开内容整体通过引用结合到本文中。表面活性剂的实例包括烷基乙氧基化物、烷基苯基乙氧基化物、聚环氧丙烷-聚环氧乙烷嵌段共聚物、梳型硅氧烷-聚乙氧基化物共聚物和聚乙氧基化胺。通过控制表面活性剂的加入和溶液或溶胶中所得胶束的尺寸,可直接控制最终产品中孔的体积和尺寸。可将孔径向下控制到几十埃或纳米的水平。使所得纤维经过干燥和煅烧步骤,以去除水、残余有机成分和挥发性盐阴离子。在一些实施方案中,可使纤维经过进一步热处理,以产生用于最佳阴极性能的结晶结构。最后,将纤维布置在电极结构中,所述电极结构适合用作锂离子电池的阴极或包含在其中。所得纤维状材料的直径范围可以为约0.1微米至约20微米。通过驱使活性物质颗粒结构达到较小尺寸,表面积/体积比提高,从而通过减小扩散距离和增加表面积用于锂离子进入或离开该结构,允许更快的锂离子插入或去除的动力学。孔隙的存在驱使表面积/体积比达到比单独纤维更高的值,从而进一步改善充电和放电(即锂离子去除和插入电极结构)的动力学。用作阴极可将多孔高表面积阴极纤维制成用于锂离子电池的电极。该纤维可用作唯一的活性阴极材料,或与其它活性阴极材料混合。该材料可与其它成分混合,例如导电添加剂,例如炭黑或碳纳米纤维,或粘合剂。然后可将这些混合物施加到铝集电器上,并用作锂离子电池的阴极部分。根据几个示例性实施方案,提供一种具有约0.1至约20微米直径和约5m2/g至约400m2/g表面积的多孔还原二氧化硅纤维材料。根据几个示例性实施方案,多孔还原二氧化硅纤维材料的直径为约2至约15微米。根据几个示例性实施方案,多孔还原二氧化硅纤维材料包含硅、一氧化硅和二氧化硅,其中硅以大于约20重量%的量存在。根据几个示例性实施方案,多孔还原二氧化硅纤维材料的孔径为约0.1nm至约150nm。根据几个示例性实施方案,多孔还原二氧化硅纤维材料的孔径为约1nm至约100nm。根据几个示例性实施方案,一种用于制造多孔还原二氧化硅纤维材料的方法包括:提供包含二氧化硅前体、聚合物和表面活性剂的溶液;使溶液纤维化,以产生纤维;加热纤维,以产生二氧化硅基前体纤维;使二氧化硅基前体纤维经过镁热还原,以从二氧化硅基前体纤维去除至少一些氧,并产生还原二氧化硅纤维;并且在酸中洗涤还原二氧化硅纤维,以去除含镁的反应产物,并产生多孔还原二氧化硅纤维材料。根据几个示例性实施方案,一种用于制造多孔还原二氧化硅纤维材料的方法包括:提供包含二氧化硅(sio2)以及氧化钠(na2o)、三氧化二硼(b2o3)、氧化锂(li2o)、氧化钙(cao)和氧化镁(mgo)中至少一种的熔体;使熔体纤维化,以产生纤维;处理纤维,以去除非二氧化硅成分,并产生二氧化硅基前体纤维;使二氧化硅基前体纤维经过镁热还原,以从二氧化硅基前体纤维去除至少一些氧,并产生还原二氧化硅纤维;并且在酸中洗涤还原二氧化硅纤维,以去除含镁的反应产物,并产生多孔还原二氧化硅纤维材料。根据几个示例性实施方案,提供一种具有约0.1至约20微米直径、约5m2/g至约400m2/g表面积且基本不含二氧化硅的多孔还原二氧化硅纤维材料。根据几个示例性实施方案,多孔还原二氧化硅纤维材料具有约30m2/g至约300m2/g的表面积。根据几个示例性实施方案,多孔还原二氧化硅纤维材料具有约0.01cm3/g至约1.5cm3/g的孔隙率。根据几个示例性实施方案,多孔还原二氧化硅纤维材料具有约1nm至约90nm的中值孔径。根据几个示例性实施方案,多孔还原二氧化硅纤维材料具有许多轴向排列的孔。根据几个示例性实施方案,多孔还原二氧化硅纤维材料的孔径为约0.1nm至约80nm。根据几个示例性实施方案,多孔还原二氧化硅纤维材料的孔径为约4nm至约40nm。根据几个示例性实施方案,提供一种电池电极,该电池电极包含粘合剂和多孔还原二氧化硅纤维。根据几个示例性实施方案,电池电极具有约30%至约100%的库仑效率。根据几个示例性实施方案,电池电极具有约0.4至约1.0的容量比率c3/c1。根据几个示例性实施方案,电池电极具有约0.1至约1.0的容量比率c10/c1。根据几个示例性实施方案,提供一种包括电池电极的锂离子电池。根据几个示例性实施方案,提供一种具有约0.1至约20微米直径和约5m2/g至约400m2/g表面积的多孔混合金属氧化物纤维材料。根据几个示例性实施方案,多孔混合金属氧化物纤维材料具有约30m2/g至约300m2/g的表面积。根据几个示例性实施方案,多孔混合金属氧化物纤维材料具有约5%至50%体积的孔隙率。根据几个示例性实施方案,多孔混合金属氧化物纤维材料包括锂的氧化物以及至少铝、钴、铁、锰、镍、钛和钒中至少一种的氧化物。根据几个示例性实施方案,多孔混合金属氧化物纤维材料包括licoo2、lini0.33mn0.33co0.33o2、lini0.8co0.15al0.05o2、limno4、lifepo4、limn2o4、li2mno3和li4ti5o12中至少一种。根据几个示例性实施方案,多孔混合金属氧化物纤维材料的孔径为约0.1nm至约150nm。根据几个示例性实施方案,多孔混合金属氧化物纤维材料的孔径为约1nm至约100nm。根据几个示例性实施方案,多孔混合金属氧化物纤维材料通过溶胶-凝胶纤维化来制备。根据几个示例性实施方案,提供包含粘合剂和多孔混合金属氧化物纤维材料的锂基电池电极。根据几个示例性实施方案,提供一种包括锂基电池电极的锂离子电池。以下实施例为以上讨论的材料和方法的说明,而不旨在为限制。实施例1:制备二氧化硅基前体纤维通过溶液纺丝形成二氧化硅基前体纤维用具有约15nm胶体大小的levasil®200s胶体二氧化硅(包含30%胶体二氧化硅的溶液)作为二氧化硅纤维的二氧化硅源。将硅氧烷(2份evonik5850和1份xiameter™ofx-0193流体)加到胶体二氧化硅,用于聚合物模板化孔隙。添加聚环氧乙烷(peo)(polyox™wsrn-750)作为纺丝助剂,使溶液具有流变性,以允许通过挤出/吹制过程形成纤维。将所得溶液在桨式混合器中充分混合。这得到具有以下固体比的溶液:450gsio2(来自胶体二氧化硅)、22.5gsio2(来自硅氧烷)和39gpeo。溶液在30℃的粘度为1-5泊。然后通过挤出-吹制过程使溶液转化成纤维。这得到一种二氧化硅纤维,其中值直径为约3微米且标准偏差为1.3微米,表面积为153m2/g,孔体积为0.285cm3/g,中值孔径为7.6nm。将二氧化硅基前体纤维还原使2.2克如上所述制造的二氧化硅基前体纤维与1.74克镁金属粉末(可从alfaaesar获得,99.6%金属基本成分,粒度-100至+200目)在手套箱中氩气气氛下充分混合。将这种混合物装入不锈钢管(外径1/2”,壁厚0.035”),并用不锈钢端盖密封。然后将经组装的气密单元放入lindberg/bluem™高温炉中,以5℃/min坡升至700℃,并在700℃保持2小时,以使还原反应发生。在还原处理结束时,使材料炉冷,并回收得到的混合物。随后x-射线衍射(xrd)分析显示,所得材料为17.4重量%si、61.1重量%mgo、10.9重量%mg2si、2.0重量%al、5.9重量%mg2sio4和2.7重量%mgal2o4。图2为所得混合物的xrd扫描图。实际上,可使用任何适用容器,条件是其保持还原所需的无氧气氛。另外,还可使用氩以外的其它气体,例如,可使用h2、氦(he)或ar和h2的组合(即,形成气体),条件是它们不与过程中使用的二氧化硅或镁反应。另外,不必使用密闭容器。只要保持适合的气氛,也可使反应在开放环境或流通环境中进行。将经还原材料酸洗然后使来自上面的还原材料经过酸洗,以去除硅以外的成分。这通过将材料加到2mhcl并搅拌3小时来进行。在酸步骤结束时,将材料通过whatman™44滤纸过滤,在去离子水中洗涤滤液两次,以去除酸残余物,进行最终过滤,然后在80℃干燥3小时。然后使回收的材料经过xrd分析,发现其为41.7重量%si、2.1重量%mgal2o4、6.8重量%mg2sio4和0.1重量%mgo。发现存在49.3重量%非晶峰。图3为酸洗后还原材料的xrd扫描图。本领域的普通技术人员应理解,可将多种酸和浓度的任何一种用于洗涤步骤,只要si金属和sio相对不溶于溶液,且mgo、mgsio3、mg2si和其它副产物相对可溶。在酸洗过程中,在材料接触酸时观察到火花,确定这是由于mg2si在酸中分解生成硅烷气体(sih4)所致。已知硅烷高度易燃,并且在存在氧气时能够自燃,这种氧化反应会生成sio2,并可能导致污染产物。在后面的实验中,通过在氮气覆盖下将还原混合物加到酸来抑制这个反应。以此方式,保持氧气远离硅烷,从而抑制其氧化和转化成sio2。实际上,可使用任何适合的惰性气体,包括氩气、氦气、二氧化碳或其它。实施例2:制造和试验半电池为了评估还原二氧化硅纤维材料作为阳极的性能,用还原二氧化硅纤维材料构造一组半电池,以测定电池的电化学容量和循环寿命性能。使70重量%来自实施例1的还原二氧化硅纤维与20%lith-x™50炭黑导电添加剂和10%可从targraytechnologyinternationalinc获得的苯乙烯-丁二烯橡胶(sbr)粘合剂混合。根据需要加水,以达到适当粘度,然后将混合物充分掺混,以得到均匀的混合物。然后将其以200微米的厚度进行刮刀涂覆到用作集电器的铜箔片上。然后使涂层在部分真空下在约90℃干燥。然后用阳极材料与celgard®2325隔板和锂箔反电极结合制造币式半电池。加入由3:7碳酸亚乙酯(ec):碳酸甲乙酯(emc)中的1.2m六氟磷酸锂(lipf6)组成的电解质,将电池密封,并使其内部平衡约24小时。然后通过充放电使锂离子插入硅材料或从硅材料提取锂离子,使币式半电池经过循环试验。在这种具体情况下,前2个循环以c/40的充/放电速率(电池在40小时内完全充/放电)进行,随后以c/20(电池在20小时内充/放电)进行3个循环,且随后的循环以c/10。这就允许测定初始容量(mah/g硅材料)以及第一循环库仑效率(锂插入与锂提取的比率)和循环寿命,这由跟踪提取容量相对循环来确定。还试验了利用标准商业石墨阳极(可从hitachichemical获得的mage3石墨)和可从paracleteenergy获得的商业电池级硅的类似电池,以提供比较性样品。结果总结如下:表2:半电池试验结果nm=未测定。在表2中,“库仑效率”或“可逆容量”定义为指定循环的提取容量与插入容量的比率。通过计算指定循环(在这种情况下为循环3、循环10和循环40)的提取容量与第一个循环提取容量的比率,标为“容量比率”的列记录了随循环经历的容量衰减量。因此,容量比率为1表示没有随循环的容量衰减,比率为0.5表示在指定循环容量衰减50%,0表示对在指定循环没有剩余容量(即,完全电池失灵)。该数据表明,石墨的提取容量为342.9mah/g,商业硅的提取容量为1648.0mah/g,还原二氧化硅纤维的提取容量为1369.0mah/g,表明还原二氧化硅纤维的提取容量与硅相似。就循环稳定性而言,石墨具有极其稳定的循环,库仑效率为93.1%,c3/c1容量比率为1,而硅显示库仑效率较低,为43.3%,在3个循环后没有残余容量。相比之下,还原二氧化硅纤维显示库仑效率为68.2%,循环时的衰减慢得多,这是与商业硅相比的改善。实施例3:还原试验由于已知材料加工和微结构可在性能中起重要作用,因此用实施例1的二氧化硅基前体纤维进行进一步研究。使这种材料经受各种还原条件,包括(1)改变二氧化硅与镁的比率(以化学计量(1mg/o)至50%化学计量(1mg/2o)范围的量);(2)使高于400℃的温度下的加热速率从1℃/min变到5℃/min;(3)使最高温度从650℃变到700℃;以及(4)使该温度下的保持时间从2小时变到达7小时。在还原过程后,用xrd检验材料,以确定材料的晶相组成。在如实施例1中所述酸洗后,对材料进行bet分析,以确定表面积、中值孔径和总孔隙率。该研究的样本矩阵显示于下表中。虽然这项研究代表还原变量的具体有限范围,但应理解,在这些之外的材料比率、坡升速率、保持温度和保持时间也是可行的。表3:还原试验的样品样品前体sio2纤维(克)mg(克)升温速率(℃/min)保持温度(℃)保持时间(hr)12.141.745700222.211.811650732.141.741700742.142.611700752.141.741700362.142.611700372.141.741650382.142.611650392.142.6116507102.21.3416507112.20.8916507所得相和形态显示于下表中。图4示出mg/sio2质量比率对sio2转化成si的百分数的影响。在低比率和高比率下,转化的sio2的百分数低于该比率为0.813时(化近似学计量,这意味每个氧原子存在一个镁原子,这将引起二氧化硅基前体纤维完全还原和镁完全氧化)。图5示出mg/sio2比率对还原硅材料的表面积的影响。随着比率增加,表面积减小。图6示出mg/sio2比率对中值孔径的影响。随着比率增加,中值孔径也增加。图7示出mg/sio2比率对还原二氧化硅材料的孔体积的影响。在低比率和高比率下,孔隙率低于比率接近0.813(化学计量)时。表4:还原试验的结果样品si(重量%)mgo(重量%)mg2si(重量%)mgsio4(重量%)其它(%重量)表面积(m2/g)孔径(中值,nm)孔隙率(cm3/g)117.461.110.95.94.735240.107218.370.111.60.2n/a150.7160.58317.264.514.43.9n/a110210.4644.857.237.40.5n/a92.125.50.416518.569.510.21.2n/a91.0210.38865.056.138.60n/a108.7250.406716.368.214.61.0n/a134.615.50.45283.057.637.80n/a116.2220.30993.958.936.80n/a104.8230.3641020.950.10028.427011.50.5801111.926.70060.62849.50.483由于还原二氧化硅纤维的微结构可能与电池中材料的电化学和循环性能相关,因此希望能够控制还原纤维的最终微结构。因此,重要的是保留最初二氧化硅基前体纤维(如通过浸提、聚合物模板化或其它过程产生的)的微结构特征,以及可能通过产生另外的孔体积和表面积来增强这些特征。控制还原过程对产生最佳的微结构至关重要。样品1和5在相似的条件下(在700℃下分别2和3小时)但以不同的加热速率还原。这给出相似的相结构(si、mgo、mg2si和mgsio4,),但形态特征却大不相同。以5℃/min加热的样品1,显示很低的表面积(35m2/g),相对较粗的中值孔径(24nm)和0.107cm3/g的低孔隙率。相比之下,具有较低加热速率的样品5显示更为多孔的结构,具有91m2/g表面积,21nm中值孔径和0.388cm3/g孔隙率,孔隙率的量超过3倍。xrd表明样品1和5中的硅晶体大小分别为132nm和31nm级。相信这一影响是由于还原反应的放热性质。快速加热速率(5℃/min)驱动反应在短时间/温度阶段发生。随着反应快速驱动到完成,来自反应的热量可能在反应器中积累,并使反应器温度升高到远高于周围环境。这可驱动样品中的烧结、晶粒生长和其它微结构固结。较低的加热速率(1℃/min)将使反应在更长的时间段内发生,这又可使反应热散发到环境中,从而在反应器中保持较低温度,并抑制温度驱动的微结构变化。在另一项比较性研究中,样品2、9、10和11均经历相同的热处理循环,但具有不同的mg与sio2的比率。样品2的mg与sio2的质量比率(mg/sio2)为0.813,这是从sio2完全去除氧的化学计量。样品9的比率为1.220,包含相对于完全还原sio2所需过量50%的mgo。样品10的比率为0.610,其相对于完全还原sio2所需的量少了25%(因此只应去除75%的氧原子),样品11的比率为0.405,只含完全还原sio2所需一半的mg。可以看出,富mg材料具有这组最小的表面积和孔隙率的值,和最粗的孔径。如图5中所示,随着mg含量变少,表面积显示逐渐增加。实施例4:实施例3某些样品的半电池试验虽然不希望受理论约束,但相信高孔体积有益于阳极性能。随着硅变得逐渐锂化,硅会膨胀到高达其未锂化体积的3.5倍的水平。该体积膨胀必须容纳在负极和电池设计内。从数据可以看出,由商业硅(作为直径0.1-1.0微米范围的颗粒和附聚物存在)构成的电池很快失去所有容量。相信这是由于硅的反复膨胀和收缩使电极涂层变形,并导致电极内电导率损失,造成其无法充入或放出电流。通过在硅基纤维内提供内部孔隙,产生内部体积,其可容纳至少一部分硅膨胀,而不破坏纤维外部或电极结构。将选择的样品制成阳极,并如实施例2中所述经过半电池试验,不同之处在于前3个循环在c/20进行,随后的循环如前,在c/10。表5:半电池试验的结果nm=未测定。在这个数据集中,见到在商业硅样品中插入容量最高,而在样品10和11中数值较低,这是由于在这些还原中使用的mg量较小。样品10和11未完全还原,因此可能包含si(3500mah/g)、sio(1710mah/g)和sio2的组合。如容量比率所示,循环寿命在石墨中最长,已知其具有长期稳定性。10个循环后,商业硅已失去所有容量。然而,硅基纤维材料保持10和40个循环的循环寿命,其中样品10和11具有最高的容量保持率。参考前面内部孔隙在容纳膨胀中潜在作用的讨论,由于氧化物材料的存在,样品10和11也可能经历减小的膨胀,因此在可更容易地被现有孔隙容纳的水平膨胀。在图8-14中提供了第一循环结果的各种曲线图。图8-14显示在0.01和1.5伏之间循环时插入阳极和从阳极提取的锂的量。下部曲线和下部标尺显示插入阳极的锂量或“插入容量”。上部曲线显示从阳极提取的锂量或“提取容量”。电池一式三份进行试验,因此每个试验有三(3)组曲线。在图15-21中提供了循环寿命的各种曲线图。图15-21显示了半电池的提取(或放电)容量以及随着电池逐渐循环它如何变化。每个数据点显示指定试验的提取容量。一式三份进行试验,因此每个曲线图中表示三个单独的数据集。虽然以上只详细描述了几个示例性实施方案,但本领域的普通技术人员应容易理解,在实质上不背离本发明的新颖教导和优点的情况下,可在示例性实施方案中作出很多其它修改。因此,所有这样的修改旨在包括在所附权利要求限定的本发明的范围内。当前第1页12