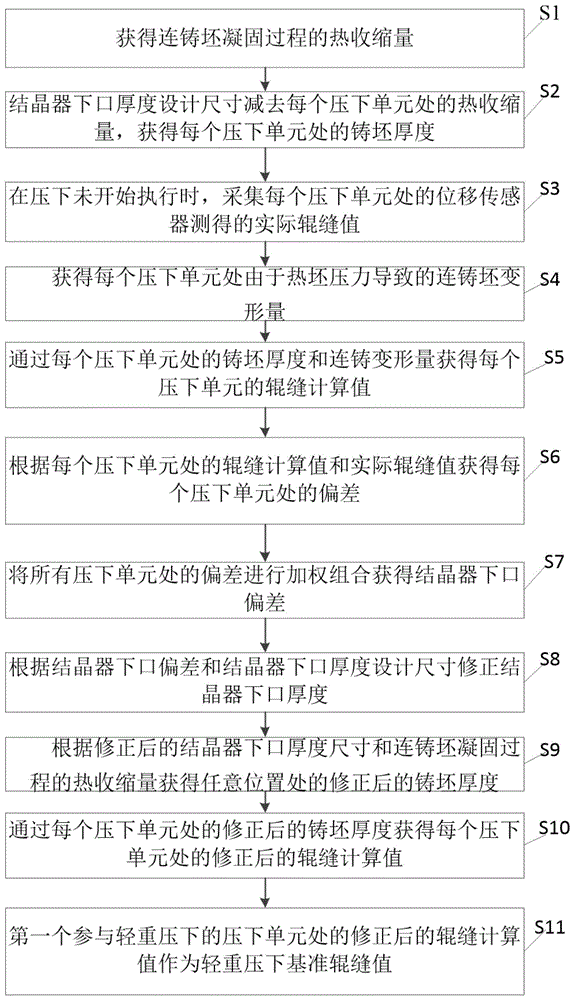
本发明涉及冶金
技术领域:
,更加具体地,涉及一种连铸轻重压下基准辊缝确定方法及装置。
背景技术:
:连铸是钢材生产中的一个重要工序,连铸坯质量好坏不仅和钢材的最终质量密切相关,还影响整个钢铁企业的生产效率。由于连铸是一个边充填、边凝固并涉及凝固体高温塑性变形的复杂的动态凝固工艺,尤其在凝固末期,处于半凝固状态的钢材内部温降大大快于外部温降,直接导致铸坯内部收缩较大,从而产生空隙,此时富含多种溶质的钢液流动到空隙中,易产生中心疏松、中心偏析等缺陷,严重影响了钢材的内部质量。为了改善浇注过程中,由于铸坯凝固收缩导致的连铸坯中心偏析、疏松和缩孔等内部质量问题,通常对铸坯施行一定的压下量以补偿凝固收缩,即轻压下或重压下。在执行压下工艺过程中,一般首先设定一个基准辊缝值,然后通过基准辊缝值减去压下量计算得到目标辊缝值,控制压下设备的辊缝到目标辊缝值,实现铸坯压下的工艺目标。基准辊缝值的准确与否,将直接影响着压下工艺的实际冶金效果。目前有两种方法设定基准辊缝值,第一种是在压下单元执行前,设置铸坯测厚辊,通过位移传感器和压力传感器测定测量铸坯厚度,以此作为压下基准辊缝值,实际生产中,设备长期处于高温状态下,测厚辊的辊子转动性和位移传感器的信号漂移都会影响测厚数据准确性,如果出现测厚数据偏差较大,及时处理情况下,导致压下功能不能正常使用,若未及时处理,将导致压下量过大,导致铸坯压下裂纹等质量事故,严重时,导致滞坯和损坏压下设备等生产事故。第二种方法是根据生产的结晶器下口厚度尺寸和预估的铸坯凝固收缩量离线固定基准辊缝值,此种方法不受生产执行设备的干扰,但是由于连铸坯的凝固收缩受钢水浇注温度、拉坯速度、冷却制度的影响,铸坯凝固收缩量是变化的,此外,结晶器的磨损也会导致结晶器下口厚度尺寸变大,从而导致基准辊缝值偏大或者偏小,进一步导致压下工艺设定目标辊缝偏大或者偏小,影响压下工艺使用的冶金效果。技术实现要素:本发明是为了解决现有技术中存在的上述技术问题而做出,其目的在于提供一种提高轻重压下基准辊缝的准确性和稳定性的连铸轻重压下基准辊缝确定方法及装置。根据本发明的一个方面,提供一种连铸轻重压下基准辊缝确定方法,用于确定压下单元的基准辊缝值,包括:获得连铸坯凝固过程的热收缩量;结晶器下口厚度设计尺寸减去每个压下单元处的热收缩量,获得每个压下单元处的铸坯厚度;在压下未开始执行时,采集每个压下单元处的位移传感器测得的实际辊缝值;获得每个压下单元处由于热坯压力导致的连铸坯变形量;通过每个压下单元处的铸坯厚度和连铸变形量获得每个压下单元的辊缝计算值;根据每个压下单元处的辊缝计算值和实际辊缝值获得每个压下单元处的偏差;将所有压下单元处的偏差进行加权组合获得结晶器下口偏差;根据结晶器下口偏差和结晶器下口厚度设计尺寸修正结晶器下口厚度;根据修正后的结晶器下口厚度尺寸和连铸坯凝固过程的热收缩量获得任意位置处的修正后的铸坯厚度;通过每个压下单元处的修正后的铸坯厚度获得每个压下单元处的修正后的辊缝计算值;第一个参与轻重压下的压下单元处的修正后的辊缝计算值作为轻重压下基准辊缝值。所述的连铸轻重压下基准辊缝确定方法,其中,所述获得连铸坯凝固过程的热收缩量的步骤包括:根据连铸凝固过程钢水传热控制方程以及初始条件和边界条件,建立连铸坯凝固传热数学模型;在线采集连铸实际生产工艺参数,根据上述连铸坯凝固传热数学模型,实时监测钢水凝固过程中的温度场分布;根据温度与膨胀系数对应的钢种热膨胀曲线,通过上述温度场分布获得连铸坯凝固过程的热收缩量。所述的连铸轻重压下基准辊缝确定方法,其中,所述获得每个压下单元处由于热坯压力导致的连铸坯变形量的步骤包括:根据每个压下单元处的温度场分布、屈服强度曲线和热坯压力,获得由于热坯压力导致的连铸坯变形量。所述的连铸轻重压下基准辊缝确定方法,其中,所述获得每个压下单元处由于热坯压力导致的连铸坯变形量的步骤包括:根据热坯压力和液压缸活塞有效作用面积获得压下单元作用在铸坯上的压力,f=p·s0其中,f为压下单元作用在铸坯上的压力,p为热力压力,s0为液压缸活塞有效作用面积;根据连铸压下单元作用在铸坯上的压力获得连铸坯压下变形区面积,s=f/σ其中,s为压下变形区面积,σ为连铸坯屈服强度;根据连铸坯压下变形区面积、压下辊尺寸和铸坯尺寸通过下式获得连铸坯变形量其中,δpi为连铸坯变形量,r为压下单元压下辊的半径;w为连铸坯宽度。所述的连铸轻重压下基准辊缝确定方法,其中,所述将所有压下单元处的偏差进行加权组合获得结晶器下口偏差的步骤包括:将所有压下单元处的偏差的中位数或中位数的平均数作为结晶器下口偏差。根据本发明的另一个方面,提供一种连铸轻重压下基准辊缝确定装置,用于确定压下单元的基准辊缝值,包括:热收缩量获得模块,获得连铸坯凝固过程的热收缩量;第一铸坯厚度获得模块,结晶器下口厚度设计尺寸减去上述热收缩量获得模块获得的每个压下单元处的热收缩量,获得每个压下单元处的铸坯厚度;实际辊缝值获得模块,在压下未开始执行时,采集每个压下单元处的位移传感器测得的实际辊缝值;铸坯变形量获得模块,获得每个压下单元处的铸坯由于热坯压力导致的连铸坯变形量;第一辊缝计算值获得模块,通过每个压下单元处的铸坯厚度和连铸变形量获得每个压下单元的辊缝计算值;偏差获得模块,根据每个压下单元处的辊缝计算值和实际辊缝值获得每个压下单元处的偏差;结晶器下口偏差获得模块,将所有压下单元处的偏差进行加权组合获得结晶器下口偏差;修正模块,根据结晶器下口偏差和结晶器下口厚度设计尺寸修正结晶器下口厚度;第二铸坯厚度获得模块,根据修正后的结晶器下口厚度尺寸和连铸坯凝固过程的热收缩量获得任意位置处的修正后的铸坯厚度;第二辊缝计算值获得模块,通过每个压下单元处的修正后的铸坯厚度获得每个压下单元处的修正后的辊缝计算值;基准辊缝值获得模块,第一个参与轻重压下的压下单元处的第二辊缝计算值获得模块获得的修正后的辊缝计算值作为轻重压下基准辊缝值。所述的连铸轻重压下基准辊缝确定装置,其中,所述热收缩量获得模块包括:连铸坯凝固传热数学模型构建单元,根据连铸凝固过程钢水传热控制方程以及初始条件和边界条件,建立连铸坯凝固传热数学模型;温度场分布监测单元,在线采集连铸实际生产工艺参数,根据上述连铸坯凝固传热数学模型,实时监测钢水凝固过程中的温度场分布;热膨胀曲线构建单元,根据温度与膨胀系数对应的钢种热膨胀曲线,通过上述温度场分布获得连铸坯凝固过程的热收缩量。所述的连铸轻重压下基准辊缝确定装置,其中,所述铸坯变形量获得模块根据每个压下单元处的温度场分布、屈服强度曲线和热坯压力,获得由于热坯压力导致的连铸坯变形量。所述的连铸轻重压下基准辊缝确定装置,其中,所述铸坯变形量获得模块包括:压力获得单元,根据热坯压力和液压缸活塞有效作用面积获得压下单元作用在铸坯上的压力,f=p·s0其中,f为压下单元作用在铸坯上的压力,p为热力压力,s0为液压缸活塞有效作用面积;压下变形区面积获得单元,根据连铸压下单元作用在铸坯上的压力获得连铸坯压下变形区面积,s=f/σ其中,s为压下变形区面积,σ为连铸坯屈服强度;连铸坯变形量获得单元,根据连铸坯压下变形区面积、压下辊尺寸和铸坯尺寸通过下式获得连铸坯变形量其中,δpi为连铸坯变形量,r为压下单元压下辊的半径;w为连铸坯宽度。所述的连铸轻重压下基准辊缝确定装置,其中,所述结晶器下口偏差获得模块将所有压下单元处的偏差的中位数或中位数的平均数作为结晶器下口偏差。本发明上述连铸轻重压下基准辊缝确定方法及装置在轻重压下执行过程中,将第一个参与轻重压下的压下单元处的铸坯厚度计算值作为轻重压下基准辊缝值,实现轻重压下基准辊缝值实时在线测定,考虑了连铸坯凝固收缩受工艺参数的影响,也避免了位移传感器等设备不稳定造成的数据波动对压下工艺的影响,保证了基准辊缝值的准确性和稳定性,从而提高压下的准确性,确保了生产铸坯的质量。附图说明图1是本发明所述连铸轻重压下基准辊缝确定方法的流程图的示意图;图2是不同钢种的热膨胀曲线;图3是连铸坯凝固过程不同位置的热收缩量的示意图;图4是本发明所述连铸轻重压下基准辊缝确定方法一个优选实施例的流程图;图5是本发明所述本发明所述连铸轻重压下基准辊缝确定装置的构成框图的示意图。具体实施方式在下面的描述中,出于说明的目的,为了提供对一个或多个实施例的全面理解,阐述了许多具体细节。然而,很明显,也可以在没有这些具体细节的情况下实现这些实施例。在其它例子中,为了便于描述一个或多个实施例,公知的结构和设备以方框图的形式示出。下面将参照附图来对根据本发明的各个实施例进行详细描述。图1是本发明所述连铸轻重压下基准辊缝确定方法的流程图,如图1所示,所述连铸轻重压下基准辊缝确定方法用于确定压下单元的基准辊缝值,包括:步骤s1,通过钢种收缩特性与温度的热膨胀曲线获得连铸坯凝固过程的热收缩量,每一个钢种都有自己的热膨胀曲线,可在实验室通过高温热膨胀分析仪测得,如图2所示,几种钢种的热膨胀曲线,热膨胀曲线可以表示为δs=f(t),其中,δs为热收缩量,t为温度;步骤s2,结晶器下口厚度设计尺寸减去每个压下单元处的热收缩量(如图3所示,距离结晶器弯月面的不同位置的热收缩量的变化图),获得每个压下单元处的铸坯厚度δci=δm0-δsi(i为压下单元,i=1,2,……,n)。其中,δci为第i个压下单元处的铸坯厚度,δsi为第i个压下单元处铸坯的热收缩量,δm0为结晶器下口厚度设计尺寸;步骤s3,在压下未开始执行时,采集每个压下单元处的位移传感器测得的实际辊缝值δgi(单位mm,i为压下单元,i=1,2,……,n),位移传感器位移行程范围0-l,上下辊的辊缝即开口度行程l1-l2,位移传感器位移行程范围(0-l)与上下辊的辊缝即开口度行程(l1-l2)的对应关系是线性的,即位移传感器的某一位移与某一辊缝值对应,通过位移传感器的读数即可获得实际辊缝值;步骤s4,获得每个压下单元处由于热坯压力导致的连铸坯变形量δpi(单位mm,i为压下单元,i=1,2,……,n);步骤s5,通过每个压下单元处的铸坯厚度和连铸变形量获得每个压下单元的辊缝计算值δri,δri=δci-δpi;步骤s6,根据每个压下单元处的辊缝计算值和实际辊缝值获得每个压下单元处的偏差δδi,δδi=(δci-δpi)-δgi;步骤s7,将所有压下单元处的偏差进行加权组合获得结晶器下口偏差δδ,优选地,将所有压下单元处的偏差的中位数或中位数的平均数作为结晶器下口偏差;步骤s8,根据结晶器下口偏差和结晶器下口厚度设计尺寸修正结晶器下口厚度δm,δm=δm0+δδ;步骤s9,根据修正后的结晶器下口厚度尺寸和连铸坯凝固过程的热收缩量获得任意位置处的修正后的铸坯厚度δ'ci,δ'ci=δm-δsi;步骤s10,通过每个压下单元处的修正后的铸坯厚度获得每个压下单元处的修正后的辊缝计算值δ'ri,δ'ri=δ'ci-δpi=δm-δsi-δpi;步骤s10,第一个参与轻重压下的压下单元处的修正后的辊缝计算值作为轻重压下基准辊缝值。在步骤s1中,包括:根据连铸凝固过程钢水传热控制方程以及初始条件和边界条件,建立连铸坯凝固传热数学模型;在线采集连铸实际生产工艺参数,根据上述连铸坯凝固传热数学模型,实时监测钢水凝固过程中的温度场分布;根据温度与膨胀系数对应的钢种热膨胀曲线,通过上述温度场分布获得连铸坯凝固过程的热收缩量。在步骤s4中,包括:根据每个压下单元处的温度场分布、屈服强度曲线和热坯压力,获得由于热坯压力导致的连铸坯变形量,具体地,包括:根据热坯压力和液压缸活塞有效作用面积获得压下单元作用在铸坯上的压力,热坯压力是液压系统给定的压力,可从液压系统的压力传感器读取,f=p·s0其中,f为压下单元作用在铸坯上的压力,p为热力压力,s0为液压缸活塞有效作用面积;根据连铸压下单元作用在铸坯上的压力获得连铸坯压下变形区面积,s=f/σ其中,s为压下变形区面积,σ为连铸坯屈服强度;根据连铸坯压下变形区面积、压下辊尺寸和铸坯尺寸通过下式获得连铸坯变形量其中,δpi为连铸坯变形量,r为压下单元压下辊的半径;w为连铸坯宽度。图4是本发明所述连铸轻重压下基准辊缝确定方法的一个优选实施例的示意图,如图4所示,所述连铸轻重压下基准辊缝确定方法包括:实时数据采集,包括:采集位移传感器的读数,获得压下单元实际辊缝;采集压下单元的压力传感器的读数,获得压下单元的热坯压力;根据连铸凝固过程钢水传热控制方程以及初始条件和边界条件,建立连铸坯凝固传热数学模型;在线采集连铸实际生产工艺参数,根据上述连铸坯凝固传热数学模型,实时监测钢水凝固过程中的温度场分布;根据温度与膨胀系数对应的钢种热膨胀曲线,通过上述温度场分布获得连铸坯凝固过程的热收缩量;结晶器下口厚度设计尺寸减去每个压下单元处的热收缩量,获得每个压下单元处的铸坯厚度;在压下未开始执行时,根据每个压下单元处的温度场分布、屈服强度曲线和热坯压力,获得由于热坯压力导致的连铸坯变形量;通过每个压下单元处的铸坯厚度和连铸变形量获得每个压下单元的辊缝计算值,根据每个压下单元处的辊缝计算值和实际辊缝值获得每个压下单元处的偏差;将所有压下单元处的偏差的中位数或中位数的平均数作为结晶器下口偏差;根据结晶器下口偏差和结晶器下口厚度设计尺寸修正结晶器下口厚度;根据修正后的结晶器下口厚度尺寸和连铸坯凝固过程的热收缩量获得任意位置处的修正后的铸坯厚度,通过每个压下单元处的修正后的铸坯厚度获得每个压下单元处的修正后的辊缝计算值,在执行压下时,第一个参与轻重压下的压下单元处的修正后的辊缝计算值作为轻重压下基准辊缝值;在浇注结束前,重复上面所有步骤。图5是本发明所述连铸轻重压下基准辊缝确定装置的构成框图,如图5所示,所述连铸轻重压下基准辊缝确定装置用于确定压下单元的基准辊缝值,包括:热收缩量获得模块1,获得连铸坯凝固过程的热收缩量;第一铸坯厚度获得模块2,结晶器下口厚度设计尺寸减去上述热收缩量获得模块获得的每个压下单元处的热收缩量,获得每个压下单元处的铸坯厚度;实际辊缝值获得模块3,在压下未开始执行时,采集每个压下单元处的位移传感器测得的实际辊缝值;铸坯变形量获得模块4,获得每个压下单元处的铸坯由于热坯压力导致的连铸坯变形量;第一辊缝计算值获得模块5,通过每个压下单元处的铸坯厚度和连铸变形量获得每个压下单元的辊缝计算值;偏差获得模块6,根据每个压下单元处的辊缝计算值和实际辊缝值获得每个压下单元处的偏差;结晶器下口偏差获得模块7,将所有压下单元处的偏差进行加权组合获得结晶器下口偏差;修正模块8,根据结晶器下口偏差和结晶器下口厚度设计尺寸修正结晶器下口厚度;第二铸坯厚度获得模块9,根据修正后的结晶器下口厚度尺寸和连铸坯凝固过程的热收缩量获得任意位置处的修正后的铸坯厚度;第二辊缝计算值获得模块10,通过每个压下单元处的修正后的铸坯厚度获得每个压下单元处的修正后的辊缝计算值;基准辊缝值获得模块11,第一个参与轻重压下的压下单元处的第二辊缝计算值获得模块获得的修正后的辊缝计算值作为轻重压下基准辊缝值。优选地,上述热收缩量获得模块1包括:连铸坯凝固传热数学模型构建单元,根据连铸凝固过程钢水传热控制方程以及初始条件和边界条件,建立连铸坯凝固传热数学模型;温度场分布监测单元,在线采集连铸实际生产工艺参数,根据上述连铸坯凝固传热数学模型,实时监测钢水凝固过程中的温度场分布;热膨胀曲线构建单元,根据温度与膨胀系数对应的钢种热膨胀曲线,通过上述温度场分布获得连铸坯凝固过程的热收缩量。优选地,所述铸坯变形量获得模块4根据每个压下单元处的温度场分布、屈服强度曲线和热坯压力,获得由于热坯压力导致的连铸坯变形量,具体地,包括:压力获得单元,根据热坯压力和液压缸活塞有效作用面积获得压下单元作用在铸坯上的压力,f=p·s0其中,f为压下单元作用在铸坯上的压力,p为热力压力,s0为液压缸活塞有效作用面积;压下变形区面积获得单元,根据连铸压下单元作用在铸坯上的压力获得连铸坯压下变形区面积,s=f/σ其中,s为压下变形区面积,σ为连铸坯屈服强度;连铸坯变形量获得单元,根据连铸坯压下变形区面积、压下辊尺寸和铸坯尺寸通过下式获得连铸坯变形量其中,δpi为连铸坯变形量,r为压下单元压下辊的半径;w为连铸坯宽度。优选地,上述结晶器下口偏差获得模块7将所有压下单元处的偏差的中位数或中位数的平均数作为结晶器下口偏差。在本发明的一个具体实施例中,以某钢厂180mm×180mm重压下连铸机为例,结晶器下口厚度设计尺寸为185.0mm,某次生产的铸坯凝固收缩各个位置的计算值见附图2,重压下压下单元由6架拉矫机组成,每架拉矫机的位置、热坯压力以及位移传感器检测的实际辊缝见表1。表1则可以得到每架拉矫机处的铸坯厚度计算值(辊缝计算值)及铸坯热坯压力下的变形量计算值,见表2。表2拉矫机热收缩量δsi,mm辊缝计算值δci,mm铸坯变形量,δpimm第1架1.483183.520.125第2架1.606183.390.125第3架1.817183.180.124第4架2.036182.960.124第5架2.194182.810.124第6架2.325182.680.123于是,可以计算出每架拉矫机处辊缝计算值和辊缝实际值的偏差,见表3,表3拉矫机辊缝计算值和实际值的偏差δδi,mm第1架0.10第2架0.09第3架-0.05第4架-0.07第5架-0.08第6架-0.08每架拉矫机处辊缝计算值和实测值的偏差数据中的中位数为:-0.05和-0.07,由于数据为偶数个,则中位数平均数为:-0.06mm。于是结晶器下口尺寸修正后的结晶器下口厚度δm为:185-0.06=184.94mm。则当连铸机执行重压下时,若重压下区间为第一到第四架拉矫机,则第一架拉矫机未执行压下前的铸坯计算厚度作为基准辊缝值,基准辊缝值=184.94-1.483-0.125=183.33mm。若重压下区间为第三到第六架拉矫机,则第三架拉矫机未执行压下前的铸坯计算厚度作为基准辊缝值,基准辊缝值=184.94-1.817-0.124=183.00mm。本发明所述连铸轻重压下基准辊缝值确定方法及系统采用数学模型对连铸坯凝固过程热收缩行为进行仿真,通过实测辊缝对结晶器磨损导致的辊缝补偿值进行修正,既考虑设备执行机构的影响,又考虑了连铸坯凝固收缩受工艺参数的影响,实时准确地测定基准辊缝值,保证了连铸轻重压下的顺利实施,提升连铸坯内部质量。尽管前面公开的内容示出了本发明的示例性实施例,但是应当注意,在不背离权利要求限定的本发明的范围的前提下,可以进行多种改变和修改。根据这里描述的发明实施例的方法权利要求的功能、步骤和/或动作不需以任何特定顺序执行。此外,尽管本发明的元素可以以个体形式描述或要求,但是也可以设想多个,除非明确限制为单数。当前第1页12