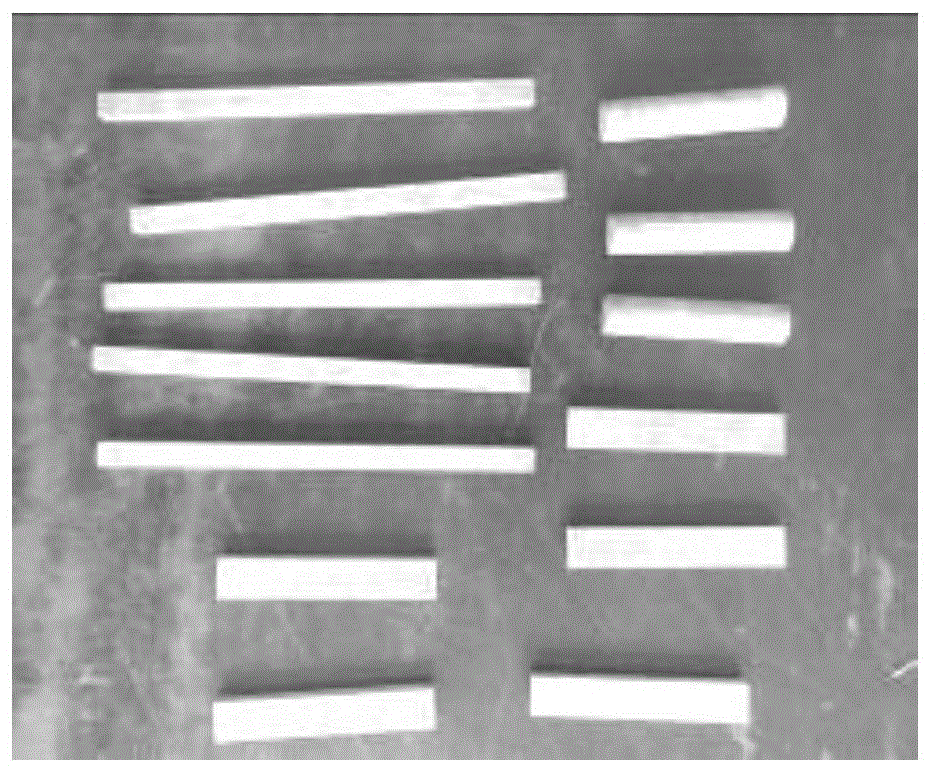
本发明涉及特种铸造
技术领域:
,尤其涉及一种纤维增强陶瓷型芯的制备方法。
背景技术:
:熔模精铸作为一种材料近净成形技术,不仅能铸出形状十分复杂的零件,还可以铸造组合的、整体的铸件,常用于复杂航空、航天、汽车工业耐热构件的成形。随着技术发展,熔模精铸已可以生产出更大、更精、更薄、更强的产品。制备具有复杂空腔结构的熔模铸件则要用到陶瓷型芯,其作用是形成空心铸件的内腔形状。在铸件浇注和凝固过程中,型芯需要承受高温金属液带来的压力作用和冲击作用,这对型芯的高温强度及尺寸稳定性等提出了更高的要求。技术实现要素:本发明的目的在于提供一种纤维增强陶瓷型芯的制备方法,本发明提供的制备方法能够提高陶瓷型芯的抗弯强度和气孔率、降低陶瓷型芯的收缩率,进而提高型芯的高温强度和尺寸稳定性。为了实现上述发明目的,本发明提供以下技术方案:本发明提供了一种纤维增强陶瓷型芯的制备方法,包括以下步骤:(1)采用偶联剂对纤维进行表面处理;(2)将表面处理后的纤维、水和分散剂混合,得到纤维的分散液;(3)将所述纤维的分散液与基体粉料混合,依次经过蒸干、过筛和干燥,得到纤维基体混合料;(4)将所述纤维基体混合料与熔融态的增塑剂混合,得到陶瓷浆料;(5)将所述陶瓷浆料依次进行压制和焙烧,得到陶瓷型芯。优选的,所述步骤(1)中纤维与偶联剂的固液比为1g:18~22ml。优选的,所述步骤(1)中的偶联剂为硅烷偶联剂。优选的,所述步骤(1)中表面处理的环境为酸性环境。优选的,所述步骤(1)中纤维为硅酸铝陶瓷纤维或碳化硅纤维,所述纤维的长度为2~7mm,直径为4~8μm。优选的,所述步骤(3)中纤维的分散液中分散剂的质量为基体粉料质量的0.2~0.7%。优选的,所述步骤(3)中纤维的分散液中纤维的质量为基体粉料质量的0.5~1.5%。优选的,所述步骤(4)中增塑剂为步骤(3)中基体粉料质量的16~20%。优选的,所述步骤(5)中的压制采用热压注法,所述热压注法包括:将陶瓷浆料注入到压注模具中,在压注机的压力作用下成形。优选的,所述焙烧的温度为1300~1400℃,焙烧的保温时间为1.5~2.5h。本发明提供了一种纤维增强陶瓷型芯的制备方法,包括以下步骤:(1)采用偶联剂对纤维进行表面处理;(2)将表面处理后的纤维、水和分散剂混合,得到纤维的分散液;(3)将所述纤维的分散液与基体粉料混合,依次经过蒸干、过筛和干燥,得到纤维基体混合料;(4)将所述纤维基体混合料与熔融态的增塑剂混合,得到陶瓷浆料;(5)将所述陶瓷浆料依次进行压制和焙烧,得到陶瓷型芯。本发明采用偶联剂对纤维进行表面处理,可以改善纤维的分散性,较未进行表面处理的纤维而言,得到的纤维的分散液中纤维的分散性更好,同时使纤维在与基体粉料混合时纤维与基体粉料更易结合,使得纤维能够均匀地分散到基体粉料中,确保得到的陶瓷型芯中纤维的均匀分散。均匀分散的纤维的桥接作用限制了微观裂纹的发展,纤维承受外力作用时,纤维拔出及断裂的失效形式消耗了能量,进而提升型芯的抗弯强度;另外,纤维对基体的致密化过程产生了抑制和阻碍作用,均匀分散的纤维抑制了型芯的烧结收缩,在型芯内部产生了较多的气孔和疏松孔洞,增大了型芯的气孔率,降低了型芯的收缩率,进而能够提高型芯的尺寸稳定性。实施例结果表明,采用本发明提供的制备方法得到的陶瓷型芯较未添加纤维得到的陶瓷型芯的强度提高34%以上,收缩率从0.889下降至0.335。此外,采用本发明提供的制备方法制备陶瓷型芯,由于陶瓷型芯的内部产生了较多的气孔和疏松孔洞,增大了型芯的气孔率,有利于脱芯。附图说明图1为实施例3的陶瓷型芯的试样。图2为实施例3陶瓷型芯试样的断口微观形貌图。具体实施方式本发明提供了一种纤维增强熔模精铸陶瓷型芯的制备方法,其特征在于,包括以下步骤:(1)采用偶联剂对纤维进行表面处理;(2)将表面处理后的纤维、水和分散剂混合,得到纤维的分散液;(3)将所述纤维的分散液与基体粉料混合,依次经过蒸干、过筛和干燥,得到纤维基体混合料;(4)将所述纤维基体混合料与熔融态的增塑剂混合,得到陶瓷浆料;(5)将所述陶瓷浆料依次进行压制和焙烧,得到陶瓷型芯。本发明采用偶联剂对纤维进行表面处理。在本发明中,所述纤维与偶联剂的固液比优选为1g:18~22ml,进一步优选为1g:20ml。在本发明中,所述偶联剂优选为硅烷偶联剂,进一步优选为kh560。本发明对所述偶联剂的来源没有特殊要求,采用本领域技术人员熟知来源的偶联剂即可。在本发明中,所述纤维优选为硅酸铝陶瓷纤维或碳化硅纤维;所述纤维的长度优选为2~7mm,进一步优选为2~6mm;所述纤维的直径优选为4~8μm,进一步优选为3~7μm。在性能上,本发明所述纤维的拉伸强度优选为3900~4100mpa,进一步优选为4000~4100mpa;所述纤维的弹性系数优选为280~300gpa,进一步优选为290~300gpa;所述纤维的熔点优选为1750~1850℃,进一步优选为1800~1850℃。在本发明中,所述偶联剂优选以偶联剂醇溶液的形式进行表面处理;所述表面处理的环境优选为酸性环境。本发明所述表面处理的步骤优选包括:将偶联剂、无机酸和有机醇混合,得到呈酸性的偶联剂醇溶液;将纤维与呈酸性的偶联剂醇溶液混合,依次经过搅拌、浸泡和过滤,得到表面处理后的纤维。本发明将偶联剂、无机酸和有机醇混合,得到呈酸性的偶联剂醇溶液。在本发明中,所述无机酸优选为醋酸,所述有机醇优选为甲醇、乙醇或异丙醇。本发明对所述无机酸的用量没有特殊要求,能够使偶联剂的醇溶液呈酸性即可。在本发明中,所述偶联剂、无机酸和有机醇的体积比优选为1:1:1~4。得到呈酸性的偶联剂醇溶液后,本发明优选将纤维与所述呈酸性的偶联剂醇溶液混合,依次经过搅拌、浸泡和过滤,得到表面处理后的纤维。本发明对所述混合的方式没有特殊要求,采用本领域技术人员熟知的混合方式即可。在本发明中,所述搅拌的时间优选为5~10min,所述搅拌的速率优选不超过300r/min,以防止纤维断裂。搅拌之后,本发明对搅拌后的纤维继续浸泡。在本发明中,所述浸泡的时间优选为15~20min。浸泡之后,本发明将纤维从偶联剂的醇溶液中过滤出来。本发明对所述过滤的实施方式没有特殊要求,采用本领域技术人员熟知的过滤方式即可。过滤之后,本发明优选还包括对过滤后的纤维进行清洗和干燥,得到表面处理后的纤维。在本发明中,所述清洗的清洗液优选为丙酮,本发明对所述清洗的步骤没有特殊要求,采用本领域技术人员熟知的清洗步骤即可。本发明对所述干燥的实施方式没有特殊要求,采用本领域技术人员熟知的干燥方式即可。本发明采用偶联剂对纤维进行表面处理,可以改善纤维的分散性,进而有利于纤维在型芯中的均匀分散。得到表面处理后的纤维,本发明将表面处理后的纤维、水和分散剂混合,得到纤维的分散液。在本发明中,所述分散剂优选为纤维素,进一步优选为羟丙基甲基纤维素。在本发明中,所述分散剂的质量优选为基体粉料质量的0.2~0.7%,进一步优选为0.3~0.6%。本发明对所述水的用量没有特殊要求,能够将各组分混合均匀即可。得到纤维的分散液后,本发明将所述纤维的分散液与基体粉料混合,依次经过蒸干、过筛和干燥,得到纤维基体混合料。在本发明中,所述基体粉料优选为石英玻璃粉或氧化铝粉,所述基体粉料的粒径优选为400目。从化学成分上看,所述石英玻璃粉的质量组成优选为:sio299.7%,al2o30.07%,mgo0.03%,fe2o30.03%,k2o0.01%,na2o0.01%,cao0.01%,tio20.01%和余量的杂质。本发明优选先将基体粉料与有机醇混合,得到基体粉料的悬浮液,然后再将基体粉料的悬浮液与纤维的分散液混合。本发明先将基体粉料与有机醇混合,得到基体粉料的悬浮液。在本发明中,所述基体粉料与有机醇的混合优选为搅拌混合。本发明对所述搅拌混合的速率和时间没有特殊要求,能够使基体粉料在有机醇中均匀分散开来即可。本发明对所述有机醇的种类没有特殊要求,任意有机醇均可。在本发明的具体实施方式中,所述有机醇优选为乙醇。在本发明中,所述基体粉料的悬浮液中基体粉料的质量浓度优选为25~35%,进一步优选为30%。得到基体粉料的悬浮液后,本发明优选将基体粉料的悬浮液与纤维的分散液混合。在本发明中,所述纤维的分散液中纤维的质量优选为基体粉料质量的0.5~1.5%,进一步优选为0.5~1%。本发明所述基体粉料的悬浮液与纤维的分散液的混合优选在搅拌条件下进行。在本发明中,所述搅拌的速率优选为300r/min以下。本发明对所述搅拌的时间没有特殊要求,搅拌至液体表面无明显纤维存在即可。在本发明的具体实施方式中,所述搅拌的时间优选为3~5min。将纤维的分散液与基体粉料的悬浮液混合均匀后,本发明将二者的混合料液蒸干,以除去溶剂。本发明对所述蒸干的实施方式没有特殊要求,采用本领域技术人员熟知的蒸干方式即可。蒸干之后,本发明对蒸干后的混合料进行过筛,以使蒸干后结块的物料分散开来。本发明优选过400目筛。过筛之后,本发明将筛后物料进行干燥,得到纤维基体混合料。本发明对所述干燥的实施方式没有特殊要求,采用本领域技术人员熟知的干燥方式即可。得到纤维基体混合料之后,本发明将所述纤维基体混合料与熔融态的增塑剂混合,得到陶瓷浆料。在本发明中,所述增塑剂优选为石蜡、蜂蜡和硬脂酸中的一种或多种,进一步优选为石蜡和蜂蜡。当所述增塑剂为石蜡和蜂蜡时,所述石蜡和蜂蜡的质量比优选为7:3。在本发明中,所述增塑剂的质量优选为所述纤维基体混合料制备步骤中所用基体粉料质量的16~20%,进一步优选为18~19%。本发明优选对增塑剂进行加热,以得到熔融态的增塑剂。在本发明中,所述加热的温度优选为90~110℃,进一步优选为100~110℃。本发明对所述加热的时间没有特殊要求,直至增塑剂全部融化即可。得到熔融态的增塑剂后,本发明将纤维基体混合料与熔融态的增塑剂混合,得到陶瓷浆料。本发明优选保持增塑剂的加热温度不变,在搅拌条件下将纤维基体混合料加入到熔融态的增塑剂中进行混合。作为进一步优选的方案,本发明选优分批次加入纤维基体混合料进行混合,以防止搅拌阻力过大不利于混合均匀。将所述纤维基体混合料与熔融态的增塑剂混合时,本发明优选还包括向混合体系中加入油酸。在本发明中,所述油酸的加入量优选为所述纤维基体混合料制备步骤中所用基体粉料质量的0.25~0.5%。本发明所述油酸能够起到润湿纤维基体混合料,减小搅拌阻力的作用。得到陶瓷浆料后,本发明将所述陶瓷浆料依次进行压制和焙烧,得到陶瓷型芯。本发明对所述陶瓷浆料进行压制,得到芯坯。在本发明中,所述压制优选采用热压注法,所述热压注法的优选包括:将陶瓷浆料注入到压注模具中,在压注机的压力作用下成形。本发明对所述压注模具的规格尺寸没有特殊要求,采用本领域技术人员所熟知的以能得到目标形状的芯型即可。在本发明中,所述压注模具的温度优选为25℃,所述压注的压力优选为4mpa,保压时间优选为10s,所述压注时陶瓷浆料的温度优选为90℃。在进行压制前,本发明优选还包括对压注模具进行清理,并在分型面上涂刷分型剂。本发明对所述压注模具的清理方式没有特殊要求,采用本领域技术人员熟知的清理方式即可。本发明对所述分型剂的种类没有特殊要求,采用本领域技术人员熟知的分型剂即可。在本发明的具体实施例中,所述分型剂具体为硅油。本发明对所述分型剂的涂刷量没有特殊要求,采用本领域技术人员熟知的涂刷量即可。压制完成后,本发明优选还包括对压制坯料进行修整校正,得到规整的芯坯。本发明对所述修整校正的实施方式没有特殊要求,采用本领域技术人员熟知的修整校正方式即可。得到芯坯后,本发明对所述芯坯进行焙烧。本发明通过造型的方式进行焙烧,以防止焙烧过程中陶瓷型芯发生变形。在本发明中,所述造型的步骤优选包括:先在烧钵内装入松散的填料,厚度为35~45mm,然后装入芯坯,再填入松散的填料盖住芯坯,保证芯坯上层填料厚度为20~30mm,芯坯距钵体边缘不少于3~5mm,芯坯间距不少于3~5mm。在本发明中,所述填料优选为工业氧化铝。造型之后,本发明将造型后的芯坯进行焙烧。在本发明中,所述焙烧的温度优选为1300~1400℃,进一步优选为1350℃,所述焙烧保温的时间优选为1.5~2.5h,进一步优选为2h。本发明对所述造型后的芯坯进行焙烧时,优选放置于炉膛温度均匀区,避免放在低温区。在本发明中,所述焙烧的氛围优选为空气氛围。烧结后,均匀分布在型芯中的纤维与基体粉料紧密结合,形成交织网络骨架,大大的提升了型芯承载外加弯曲力的能力。下面结合实施例对本发明提供的陶瓷型芯的制备方法进行详细的说明,但是不能把它们理解为对本发明保护范围的限定。实施例1步骤一,纤维表面处理:将20ml偶联剂kh560、72ml乙醇和20ml醋酸混合,得到混合液;向混合液中加入基体粉料质量0.5%的陶瓷纤维,其长度为4mm,直径为4~8μm,搅拌10min,再浸泡20min后过滤,用丙酮水溶液清洗,然后放入干燥箱中干燥待用。步骤二,制备纤维-水溶液:将步骤一得到的陶瓷纤维倒入盛有定量蒸馏水的烧杯中,加入基体粉料质量0.5%的羟丙基甲基纤维素作为分散剂,用电动搅拌器对溶液进行搅拌,转速不超过300r/min,一定时间后获得分散均匀的纤维-水溶液。步骤三,添加陶瓷纤维:向称量好的200g基体粉料中倒入定量无水乙醇溶液,用玻璃棒不断搅拌,直至粉料完全混合在乙醇溶液中形成悬浮液。取步骤二中分散好的纤维添加到基体粉料的乙醇悬浮液中,搅拌3-5min直至混合均匀且液体表面无明显纤维存在。置于电子万用炉上加热蒸干,对所得的粉料过筛,放入干燥箱中干燥待用。步骤四,浆料配制:向干燥的坩埚内,加入基体粉料重量18%的增塑剂(增塑剂配方为石蜡:蜂蜡=7:3),加热至增塑剂完全融化;保持温度为100℃,在不断搅拌的条件下,陆续加入步骤三中干燥好的陶瓷粉料,一次性加入量不可过多,并且加入基体粉料0.3%的油酸,恒温持续搅拌2小时,直至浆料均匀无气泡,且具有良好的流动性。步骤五,压制型芯:采用的热压注法压制型芯,先对模具进行清理,并在分型面上刷好硅油作为分型剂,将步骤四中搅拌好的型芯浆料快速加入到压注模具中,在压注机的压力作用下压制成型,在型芯取出一段时间后,切除残余的注料口,清理飞边和披缝,同时修整型芯缺陷,校正型芯,要求所制得的型芯不允许有裂纹、冷隔、严重气泡、缺损、油纹和划伤等缺陷。步骤六,造型焙烧:对步骤五的型芯进行修整校正后,装入烧钵中造型焙烧,先在烧钵内装入松散的填料(工业氧化铝粉),厚度约40mm,然后装入型芯(放置应有利于防止型芯变形),再填入过筛松散的氧化铝粉盖住型芯,保证型芯上层填料厚度为25mm,型芯距钵体边缘5mm,型芯间距5mm,型芯装钵好之后,将烧钵送炉焙烧,装炉时烧钵应放置于炉膛温度均匀区内,避免放在低温区。实施例2按照实施例1的方法跟用量制备纤维增强陶瓷型芯,不同之处在于步骤1中陶瓷纤维的质量为基体粉料质量的1%,其长度为4mm,直径为4~8μm。实施例3按照实施例1的方法跟用量制备纤维增强陶瓷型芯,不同之处在于步骤1中陶瓷纤维的质量为基体粉料质量的1%,陶瓷纤维的长度为2mm,直径为4~8μm。实施例3得到的陶瓷型芯试样见图1,陶瓷型芯试样的断口微观形貌见图2。由图2可知,经过煅烧后,陶瓷纤维还以纤维的形式存在于陶瓷型芯中,因此有利于增强陶瓷型芯的强度。对比例1按照实施例1的方法跟用量制备陶瓷型芯,不同之处在于没有采用纤维,而是直接将基体粉料与增塑剂混合,然后进行后续步骤制备陶瓷型芯。按照标准hb5353-2004,对实施例1~3及对比例1制备的陶瓷型芯进行性能测试,测试结果见表1。表1实施例1~3及对比例1的陶瓷型芯的性能数据表性能实施例1实施例2实施例3对比例1抗弯强度/mpa16.5420.4815.8315.19气孔率/%35.5835.7635.6334.06收缩率/%0.4530.3350.3860.889由表1的数据可知,本发明采用表面处理后的纤维制备的陶瓷型芯的抗弯强度为15.83~20.48mpa,而未采用纤维得到的陶瓷型芯的抗弯强度为15.19mpa,说明本发明提供的制备方法制备的陶瓷型芯具有更高的抗弯强度。此外,本发明采用表面处理后的纤维制备的陶瓷型芯的气孔率和收缩率分别为35.58~35.76%和0.335~0.453%,而未采用纤维得到的陶瓷型芯的气孔率和收缩率分别为34.06%和0.889%,说明本发明提供的制备方法制备的陶瓷型芯收缩率明显降低,有利于型芯的尺寸稳定性,最终提高铸件质量。以上所述仅是本发明的优选实施方式,应当指出,对于本
技术领域:
的普通技术人员来说,在不脱离本发明原理的前提下,还可以做出若干改进和润饰,这些改进和润饰也应视为本发明的保护范围。当前第1页12