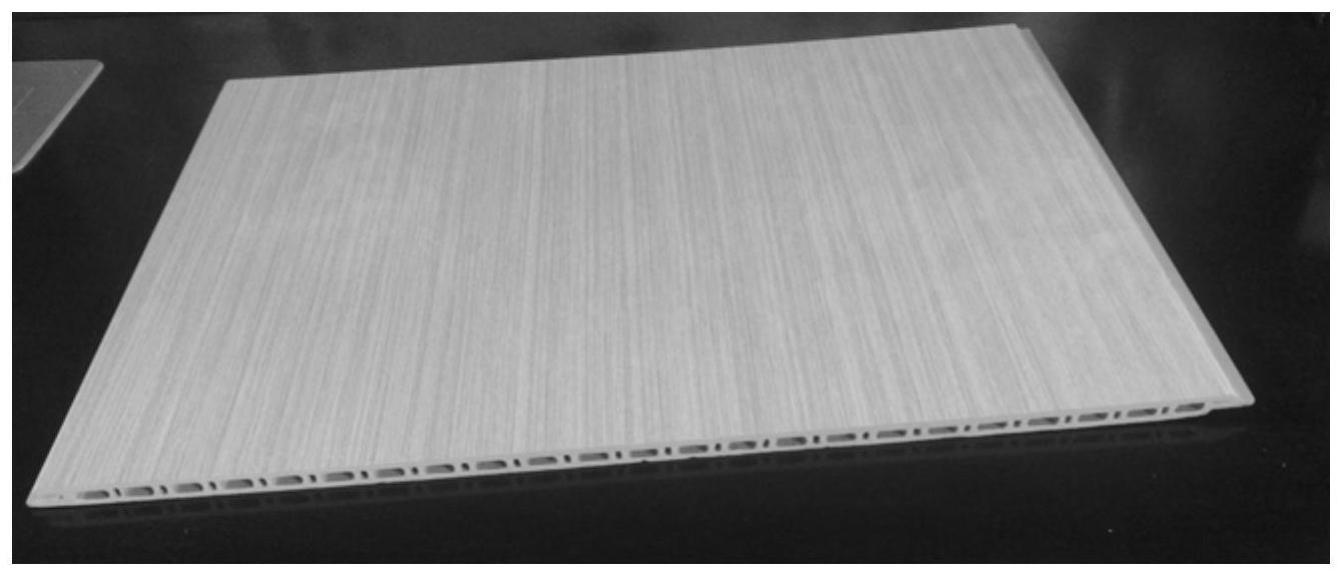
[0001]
本发明涉及复合板材制备技术领域,具体涉及一种利用菱镁尾矿粉大比例掺混原料制作复合板材的方法。所制备的复合板材用于绿色建筑和装饰板材。
背景技术:[0002]
杂质含量高的固体矿物质,由于其组分复杂,提纯成本高、难度大、污染严重等问题,成为资源化利用的难点问题,长期形成的“采富弃贫”的资源发展思路,导致资源难以获得有效利用,并导致新的矿物质或粉尘污染。
[0003]
菱镁矿是我国重要的资源型和优势矿种,长期以来都处于世界上资源占比的第一位。菱镁尾矿是在菱镁矿开发过程中,提取高精镁矿后,残余的废弃资源矿产品,除含有一定量如30%~45%的mgco3外,还含有caco3、sio2和al2o3等杂质化合物,低镁含量的菱镁尾矿是矿区深度发展的制约因素,技术上一直在寻找合适的途径提高废弃资源的利用率。
[0004]
上世纪90年代,一部分菱镁尾矿用于制造水泥凝胶预制型隔热墙体材料,但由于这种材料存在吸水“反卤”现象,造成墙体因季节变化吸水返潮,对室内环境和表面装饰造成不利影响,我国很多城市已经将这种水泥凝胶型菱镁矿建筑板材从推荐名录中删除,甚至在很多场合被禁用。例如专利申请号200810230864(一种菱镁复合板及生产方法)就提出菱镁水泥板中间加装泡沫板吸水解决菱镁板的反卤与反乳问题,但这种办法也是简单的加装泡沫板的吸水措施,治标不治本,其实很难从根本上解决凝胶型板材晶体间水分子析出问题。
[0005]
利用高分子材料与无机矿粉复合生产板材是一种新的无机矿粉利用新途径。授权公告号cn 102295822 b(粉煤灰节能环保复合板材及其制造方法)提出了将煤粉灰活化添加到特制的环氧树脂胶液中高温模压成型制备粉煤灰—环氧树脂复合板材,通过环氧树脂材料与无机矿粉的复合使用,避开了复合板材结合的凝胶吸水凝固成型环节,也就避免了材料的“反卤”现象。但这种无机矿粉的掺混量,当超过35~40%以后,材料的总体性能均呈现快速下降趋势,材料强度不足和破碎成为影响材料使用安全的重大隐患。
技术实现要素:[0006]
本发明的目的在于提供一种利用菱镁尾矿粉大比例掺混原料制作复合板材的方法,该方法能够提高菱镁尾矿粉掺混量,并制作出高性能复合板材。
[0007]
为实现上述目的,本发明所采用的技术方案如下:
[0008]
一种利用菱镁尾矿粉大比例掺混原料制作复合板材的方法,该方法包括如下步骤:
[0009]
(1)矿粉制备:对菱镁尾矿进行煅烧,获得物理化学性能稳定的无机矿粉,研磨矿渣至粒径小于25微米(相当于500目以上细度)的粉体(菱镁尾矿粉);
[0010]
(2)预塑化粉制作:将pvc粉、菱镁尾矿粉、木粉、增韧剂、稳定剂、偶联剂和润滑剂按照80:(60~90):(2~15):(2~10):(1~7):2:5的重量比例配料加入混料机,经过高速混
料机混料温度达到105℃-120℃后,待混合物料缓慢冷却到约40℃后,转入挤出机,挤出预塑化复合颗粒材料制成预塑化粉;
[0011]
(3)配料与混料:将pvc粉、预塑化粉、菱镁尾矿粉、偶联剂和发泡剂按照20:100:(10~50):(1~2):(1~5)的重量比例配料并加入混料机,经过高速混料机混料温度达到105℃-120℃后,低温混料冷却到约40℃获得混合原料粉,待用;
[0012]
(4)板材挤出成型:将步骤(3)所得混合原料粉通过挤出机挤出熔体达到预期效果并成型稳定后,将模具物料出口与定型台对接,借助10~25℃冷却水降低挤出成型板材的温度,利用牵引机将板材引出,实现板材的连续化生产。
[0013]
上述步骤(1)中,研磨矿渣至粒径为小于15微米(相当于800目粒径)的菱镁尾矿粉,优选为1250目粒径的菱镁尾矿粉。
[0014]
上述步骤(2)中,控制挤出温度为165℃-180℃。
[0015]
本发明提到的增韧剂、稳定剂、偶联剂、润滑剂、发泡剂,习惯性被统称为加工助剂,对改善材料的加工性能和强度、韧性、稳定性等五里河化学指标,有很好的调节作用,除此之外,实践过程中,还经常添加着色剂(调节材料的颜色)、抗氧化剂、增强剂、增熔剂,或其他有利于提高材料性能、美观效果的两种或多种复合助剂。
[0016]
本发明提到的增韧剂优选cpe增韧剂,稳定剂优选无毒金属皂类(ca—zn复合稳定剂),偶联剂优选硅烷偶联剂,润滑剂优选pe蜡,发泡剂优选黄发泡剂、白发泡剂和双甲基发泡调节剂等。
[0017]
上述步骤(4)熔体挤出过程中,通过调节挤出机螺杆转速和电加热控制挤出机区块温度一区为135~150℃、二区为150~168℃、三区168~178℃,四区及以后各区温度小于185℃;加热模具温度达到160℃~170℃。
[0018]
所制备的复合板材中,pvc与菱镁尾矿粉的重量比例为100:(70~140)。
[0019]
本发明设计机理和有益效果如下:
[0020]
1、本发明通过调控菱镁尾矿粉粒径、以及在制备预塑化粉和混合原料粉过程中选用合适的加工助剂,实现提高复合板材中菱镁尾矿粉掺混量,从而降低原材料成本。
[0021]
2、由于无机粉体与高分子材料表面极性不同,两者很难融合形成刚柔共济的“锚固”结构,通过限定量的偶联剂对无机粉体表面浸润改性,使掺混的无机粉体在混料过程中能够较好的分散到高分子粉体中,形成相对稳定的“刚柔锚固”结合体。而常规工艺过程,大比例掺混无机粉体会导致的无机粉体结块、不均匀分散问题,严重影响两种材料之间的结合性能与强度。
[0022]
3、本发明通过预塑化过程,实现了菱镁尾矿无机粉体的大比例掺混,同时预塑化挤出过程进一步强化了无机粉体与pvc塑料之间分散性和两者熔融结合,确保了菱镁尾矿粉体在pvc高分子复合材料中大比例掺混量的同时提高材料复合成型后的内部结构稳定性和强度。
[0023]
4、采用本发明制作的板材,复合材料中pvc含量与菱镁尾矿粉的固废掺混量配比达到100:(70~140)的份额,菱镁尾矿粉掺混量可高达140%份额,在确保材料的强度和韧性达到满意效果的前提下,由于低成本固废掺混量增加,单位重量的复合板材原材料成本获得较大幅度的降低。
[0024]
5、采用本发明工艺,板材发泡性能较好,强度高,具有较好的材料韧性,能更好的
满足轻便高强度性能要求。
附图说明
[0025]
图1为本发明实施例1所加工的板型实物图。
[0026]
图2为本发明实施例2所加工的板型实物图。
[0027]
图3为本发明实施例3所加工的板型实物图。
具体实施方式
[0028]
下面结合附图对本发明做进一步说明。
[0029]
以下实施例中涉及到的含量或配方均为重量百分比或重量份。以下实施例中,增韧剂为cpe增韧剂,稳定剂为ca-zn复合稳定剂,润滑剂为pe蜡,发泡剂为黄发泡剂。
[0030]
实施例1:
[0031]
本实施例为装饰墙板的制作,为板宽600mm、板厚8.5mm的单层孔整体成型装饰墙板,板长根据工程需要裁剪。具体制备过程如下:
[0032]
1、原料为取加工好的菱镁尾矿粉体材料,主要组分为:sio2含量55.75%,mgo含量为24.96%,al2o3含量为6.65%和其他少量无机组分。
[0033]
2、取用7型或8型pvc材料80份,选用1250目菱镁尾矿粉80份,80目木粉10份,硅烷偶联剂kh-560偶联剂2份,钙锌复合稳定剂4份,可加入其他如润滑剂5份、增韧剂5份,加入混料机,经过高速混料机混料温度达到115℃后,待混合物料缓慢冷却到40℃,转入挤出机,挤出预塑化复合颗粒材料制成预塑化粉;
[0034]
3、然后取同样的pvc材料20份、预塑化粉100粉、菱镁尾矿粉25份,偶联剂1.5份,发泡剂3份;按该比例配料并加入混料机,经过高速混料机混料温度达到115℃后,低温混料冷却到40℃待用;
[0035]
4、板材挤出成型:将步骤(3)所得物料借用现有墙体装饰板材模具和jhz80双螺杆加工挤出设备挤出熔体达到预期效果并成型稳定后,将模具物料出口与定型台对接,借助10~25℃冷却水降低挤出成型板材的温度,利用牵引机将板材引出;熔体挤出过程中,通过调节挤出机螺杆转速和电加热控制挤出机区块温度一区为135~150℃、二区为150~168℃、三区168~178℃,四区及以后各区温度在160℃-185℃合理范围内(根据挤出过程出料成型情况和色泽调整挤出稳定);加热模具温度达到160℃~170℃;最终获得如图1所示的装饰板材。
[0036]
相比pvc的量100份,本实施例无机矿粉总添加量达到105份,经检测,获得的发泡复合板材指标,经过测试板材各项指标均表现良好:板材成型完整不破碎、外围结构尺寸计算的材料体积密度约0.9g/cm3,导热系数约0.14w/(m
·
k),吸水率3.6%,阻燃氧指数达到36,弯曲强度10.5mpa,拉伸强度8mpa,jc-300落锤冲击试验显示材料没有破碎。
[0037]
实施例2:
[0038]
本实施例为墙体板材的制作:板宽280mm、板厚80mm的三层多孔型整体成型板材,板长根据工程需要裁剪。制作过程如下:
[0039]
原料为取加工好的菱镁尾矿粉体材料,主要组分为:sio2含量55.75%,mgo含量为24.96%,al2o3含量为6.65%和其他少量无机组分。
[0040]
取用7-8型pvc材料80份,选用1250目菱镁尾矿粉90份,80目木粉少许10份,硅烷偶联剂kh-560偶联剂2份,钙锌复合稳定剂4份,润滑剂5份、增韧剂4份,完成预塑化粉加工;加入混料机,经过高速混料机混料温度达到105℃-120℃后,待混合物料缓慢冷却到40℃,转入挤出机,挤出预塑化复合颗粒材料制成预塑化粉;
[0041]
然后取同样的pvc材料20份、塑化粉100粉、菱镁尾矿粉30份、偶联剂1.2份、发泡剂2份;按该比例配料并加入混料机,经过高速混料机混料温度达到105℃-120℃后,低温混料冷却到40℃待用;
[0042]
将混料后的物料借用现有墙体装饰板材模具和jhz80双螺杆加工挤出设备挤出熔体达到预期效果并成型稳定后,将模具物料出口与定型台对接,借助10~25℃冷却水降低挤出成型板材的温度,利用牵引机将板材引出;熔体挤出过程中,通过调节挤出机螺杆转速和电加热控制挤出机区块温度一区为135~150℃、二区为150~168℃、三区168~178℃,四区及以后各区温度在160℃-185℃合理范围内(根据挤出过程出料成型情况和色泽调整挤出稳定);加热模具温度达到160℃~170℃;最终获得如图2所示的装饰板材。
[0043]
相比pvc的量100份,本实施例无机矿粉添加量达到120份,经检测,获得的发泡复合板材指标,经过测试板材各项指标均表现良好:板材成型完整不破碎、外围体积密度约0.95g/cm3,利用热流法导热系数测量仪测量环境温度25℃型材整体导热系数约0.08w/(m
·
k),吸水率1.5%,阻燃氧指数达到39,板型弯曲强度35.8mpa,拉伸强度为14.85mpa,jc-300落锤冲击试验显示材料没有破碎。
[0044]
实施例3:
[0045]
本实施例为墙体板材的制作:板宽280mm、板厚80mm的三层多孔型整体成型板材,板长根据工程需要裁剪。制作过程如下:
[0046]
原料为取加工好的菱镁尾矿粉体材料,主要组分为:sio2含量55.75%,mgo含量为24.96%,al2o3含量为6.65%和其他少量无机组分。
[0047]
取用7-8型pvc材料80份,选用1250目菱镁尾矿粉100份,80目木粉少许15份,硅烷偶联剂kh-560偶联剂2份,钙锌复合稳定剂4份、润滑剂5份、增韧剂6份,加入混料机,经过高速混料机混料温度达到105℃-120℃后,待混合物料缓慢冷却到40℃,转入挤出机,挤出预塑化复合颗粒材料制成预塑化粉;;
[0048]
然后取同样的pvc材料20份、塑化粉100粉、菱镁尾矿粉40份,偶联剂1.5份,发泡剂2.5份,还可再加入内外润滑剂、着色剂若干。按该比例配料并加入混料机,经过高速混料机混料温度达到105℃-120℃后,低温混料冷却到40℃待用;
[0049]
将混合后的物料借用现有墙体装饰板材模具和jhz80双螺杆加工挤出设备挤出熔体达到预期效果并成型稳定后,将模具物料出口与定型台对接,借助10~25℃冷却水降低挤出成型板材的温度,利用牵引机将板材引出;熔体挤出过程中,通过调节挤出机螺杆转速和电加热控制挤出机区块温度一区为135~150℃、二区为150~168℃、三区168~178℃,四区及以后各区温度在160℃-185℃合理范围内(根据挤出过程出料成型情况和色泽调整挤出稳定);加热模具温度达到160℃~170℃;最终获得如图3所示的装饰板材。
[0050]
相比pvc的量,本实施例无机矿粉添加量达到140份,经检测,获得的发泡复合板材指标,经过测试板材各项指标均表现良好:板材成型完整不破碎、体积密度约1.15g/cm3,利用热流法导热系数测量仪测量环境温度25℃型材整体导热系数约0.10w/(m
·
k),吸水率
0.9%,阻燃氧指数达到42,弯曲强度46.8mpa,拉伸强度为11.92mpa,,jc-300落锤冲击试验显示材料没有破碎。
[0051]
对比例1:
[0052]
与实施例1不同之处在于:该对比例无预塑化粉过程,
[0053]
对比产品掺混量,性能如下:
[0054]
利用pvc与500目粒径caco3材料添加量达到35%时一次性发泡挤出制备高分子复合材料,板厚15mm、密度为0.528g/cm3的实心光面板,经检测材料的弯曲强度为24.8mpa,而拉伸强度则只有8.8mpa,远低于通过预塑化粉过程实现的菱镁尾矿无机粉体的掺混量高达100%所获得的性能指标。
[0055]
对比例2:
[0056]
选择其他粒径的菱镁尾矿粉,对比掺混量,性能。
[0057]
王贵斌等编写的《硬质聚氯乙烯制品及工艺》中图4-92显示不同粒径无机粉体填充量与pvc材料复合挤出成型后对产品性能影响,对于微米级caco3在20%填充量时材料拉伸强度达到最大值,进一步提高无机粉体填充量,材料性能指标呈现快速下降趋势。现有技术显示,在pvc复合材料中,无机粉体的填充量均控制在35%以下。