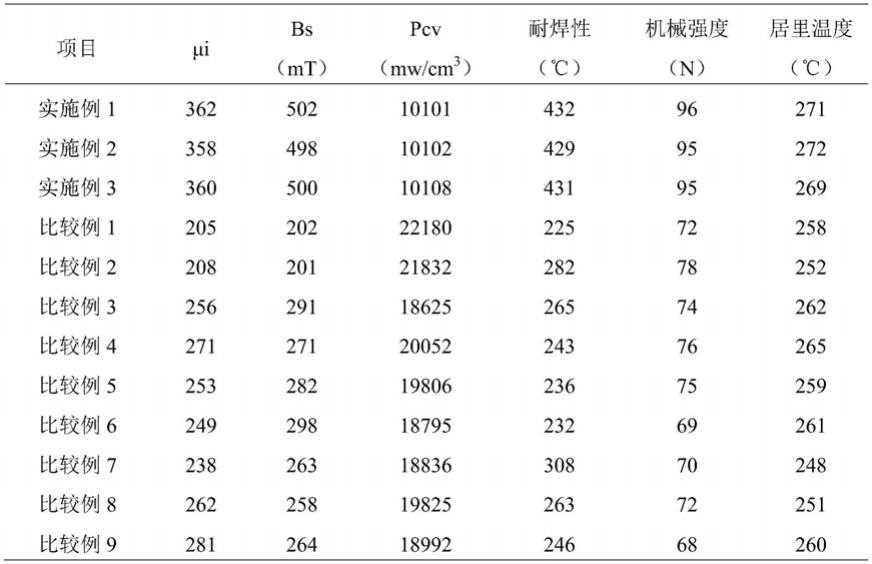
[0001]
本发明属于软磁铁氧体技术领域,具体涉及一种功率型铁氧体材料及其制备方法。
背景技术:[0002]
功率铁氧体是一种高饱和磁感应强度和磁导率、低功耗材料。在外加高磁场强度、高频的情况下仍然能够保持很低的功率损耗,并且功耗会维持在一个固定值附近,不会随温度的提升而急剧增大,从而使磁心处于一种良性循环。
[0003]
相比较于mnzn功率铁氧体,nizn铁氧体具有高电阻率、使用频率高等的特点,在很多领域有着广泛的应用,比如工业、农业、军品和民品,并且还能够大规模量产,特别适合制作成各种表面贴装用的电磁元器件和表面安装的功率电感器,这为传输较大功率的dc-dc电源模块的小型化和轻薄化奠定了一定的理论基础和应用前景,所以说nizn功率铁氧体是当代电子设备的不可或缺的重要组成部分。
[0004]
目前nizn功率铁氧体材料存在的问题主要包括以下的方面:
[0005]
(1)材料磁导率升高引起饱和磁感应强度显著下降,居里温度较低,满足不了大电流和高密度安装的应用场合需求;
[0006]
(2)若将饱和磁感应强度提高,则材料的磁导率又偏低,满足不了电子设备小型化的要求;
[0007]
(3)耐热冲击、机械强度等仍然较弱,焊接温度较高,如何提高器件耐热冲击性能和铁氧体的强度成为了主要的技术难题。
技术实现要素:[0008]
本发明目的在于克服现有技术的不足,提供一种功率型铁氧体材料。
[0009]
为达到上述目的,本发明采用的技术方案如下:
[0010]
一种功率型铁氧体材料,所述功率型铁氧体材料由主料和辅料制成,所述主料以摩尔百分比计包括以下组分:52.6~54.2mol%fe2o3,12.5~21.5mol%nio和余量的zno;所述辅料的组分包括:geo2、hfo2、oso4、tl2o、tl2o3和teo2。
[0011]
优选地,以所述功率型铁氧体材料的重量作为基准,所述辅料的组分包括:0.05~0.15wt%geo2、0.03~0.05wt%hfo2、0.01~0.03wt%oso4、0.02~0.04wt%tl2o、0.01~0.06wt%tl2o3和0.05~0.1wt%teo2。
[0012]
较佳地,所述功率型铁氧体材料由主料和辅料制成,所述主料以摩尔百分比计包括以下组分:53.4mol%fe2o3,17.2mol%nio和余量的zno;以所述功率型铁氧体材料的重量作为基准,所述辅料的组分包括:0.09wt%geo2、0.04wt%hfo2、0.02wt%oso4、0.03wt%tl2o、0.03wt%tl2o3和0.08wt%teo2。
[0013]
基于一个总的发明构思,本发明的另一个目的在于提供上述功率型铁氧体材料的制备方法,包括如下步骤:
[0014]
s1.混合,将主料按比例分别放入振磨机中进行干式混合;
[0015]
s2.湿磨,将步骤s1混合之后的主料装入球磨罐中,并加入氧化锆球和去离子水,进行湿法混合球磨;
[0016]
s3.预烧,将步骤s2湿磨之后的混合料放入烧结炉内,在氧化性气氛中进行预烧,预烧温度812~936℃,保温时间1.4~2.6小时;
[0017]
s4.掺杂,将步骤s3的预烧料放入砂磨机中,并分别加入按比例称取的辅料和去离子水,进行砂磨,控制浆料的粒度在1.0~1.5μm;
[0018]
s5.压制成型:进行喷雾造粒,然后成型,压制成标环;
[0019]
s6.烧结:将标环进行烧结,得到功率型铁氧体。
[0020]
优选地,步骤s2,主料∶氧化锆球∶去离子水的质量比1∶2~4∶0.5~1.5,球磨时间2~6h。
[0021]
优选地,步骤s3,氧化性气氛为空气气氛,所述预烧具体包括:从室温以1.1℃/min速率升温至532~568℃,532~568℃保温0.6~1h,再以1.6℃/min速率升温至812~936℃,812~936℃保温1~1.8h之后,随炉冷却。
[0022]
优选地,步骤s4,预烧料和辅料∶去离子水的质量比1∶1~2,砂磨时间4~8h。
[0023]
优选地,步骤s5,将喷雾料在10mpa下加压成25*15*8的标环。
[0024]
优选地,步骤s6,标环烧结前,在露天放置24~72小时,使标环在空气中膨胀,释放其内部应力,并使标环内部的颗粒自由舒展。
[0025]
优选地,步骤s6,所述烧结具体包括:从室温以1.2℃/min速率升温至520~580℃,520~580℃保温1~1.5h,再以1.8℃/min速率升温至820~960℃,820~960℃保温1.5~2h之后,再以3.2℃/min速率升温至1080~1120℃,1080~1120℃保温2.5~4h之后,随炉冷却。
[0026]
与现有技术相比,本发明对镍锌铁氧体材料的具体成分和配比进行了优化地调整,通过将作为主要成分的氧化铁、氧化镍、氧化锌的含量限定在规定范围内,并对辅助成分的组分进行非显而易见的组合和含量限定,在特定的工艺条件下,既能够保证得到高磁导率、高饱和磁感应强度、低功率损耗,又能够提高耐高温焊锡温度、机械强度,增强韧性,拓宽镍锌铁氧体材料的应用范围,满足大电流和高密度安装应用场合的需求,更好地满足制作而成的器件小型化的要求。
具体实施方式
[0027]
为使本发明的目的、技术方案和优点更加明白清楚,结合具体实施方式,对本发明做进一步描述,但是本发明并不限于这些实施例。需要说明的是,在不相冲突的前提下,以下描述的各实施例之间或各技术特征之间可以任意组合形成新的实施例。在本发明中,若非特指,所有的份、百分比均为质量单位,所采用的设备和原料等均可从市场购得或是本领域常用的。下述实施例中的方法,如没有特别说明,均为本领域的常规方法。
[0028]
实施例1
[0029]
一种功率型铁氧体材料,所述功率型铁氧体材料由主料和辅料制成,所述主料以摩尔百分比计包括以下组分:53.4mol%fe2o3,17.2mol%nio和余量的zno;以所述功率型铁氧体材料的重量作为基准,所述辅料的组分包括:0.09wt%geo2、0.04wt%hfo2、0.02wt%
oso4、0.03wt%tl2o、0.03wt%tl2o3和0.08wt%teo2。
[0030]
上述功率型铁氧体材料的制备方法,包括如下步骤:
[0031]
s1.混合,将主料按比例分别放入振磨机中进行干式混合;
[0032]
s2.湿磨,将步骤s1混合之后的主料装入球磨罐中,并加入氧化锆球和去离子水,进行湿法混合球磨;
[0033]
其中,主料∶氧化锆球∶去离子水的质量比1∶3∶1,球磨时间4h;
[0034]
s3.预烧,将步骤s2湿磨之后的混合料放入烧结炉内,在空气气氛中进行预烧,所述预烧具体包括:从室温以1.1℃/min速率升温至550℃,550℃保温0.8h,再以1.6℃/min速率升温至875℃,875℃保温1.4h之后,随炉冷却;
[0035]
s4.掺杂,将步骤s3的预烧料放入砂磨机中,并分别加入按比例称取的辅料和去离子水,进行砂磨,控制浆料的粒度在1.2μm;
[0036]
其中,预烧料和辅料∶去离子水的质量比1∶1.5,砂磨时间6h;
[0037]
s5.压制成型:进行喷雾造粒,将喷雾料在10mpa下加压成25*15*8的标环;
[0038]
s6.烧结:标环烧结前,在露天放置36小时,使标环在空气中膨胀,释放其内部应力,并使标环内部的颗粒自由舒展,再将标环进行烧结,所述烧结具体包括:从室温以1.2℃/min速率升温至550℃,550℃保温1~1.5h,再以1.8℃/min速率升温至890℃,890℃保温1.8h之后,再以3.2℃/min速率升温至1100℃,1100℃保温3.2h之后,随炉冷却,得到功率型铁氧体。
[0039]
实施例2
[0040]
一种功率型铁氧体材料,所述功率型铁氧体材料由主料和辅料制成,所述主料以摩尔百分比计包括以下组分:54.2mol%fe2o3,12.5mol%nio和余量的zno;以所述功率型铁氧体材料的重量作为基准,所述辅料的组分包括:0.15wt%geo2、0.03~0.05wt%hfo2、0.01wt%oso4、0.04wt%tl2o、0.01wt%tl2o3和0.1wt%teo2。
[0041]
上述功率型铁氧体材料的制备方法,包括如下步骤:
[0042]
s1.混合,将主料按比例分别放入振磨机中进行干式混合;
[0043]
s2.湿磨,将步骤s1混合之后的主料装入球磨罐中,并加入氧化锆球和去离子水,进行湿法混合球磨;
[0044]
其中,主料∶氧化锆球∶去离子水的质量比1∶4∶0.5,球磨时间6h;
[0045]
s3.预烧,将步骤s2湿磨之后的混合料放入烧结炉内,在空气气氛中进行预烧,所述预烧具体包括:从室温以1.1℃/min速率升温至568℃,568℃保温0.6h,再以1.6℃/min速率升温至936℃,936℃保温1h之后,随炉冷却;
[0046]
s4.掺杂,将步骤s3的预烧料放入砂磨机中,并分别加入按比例称取的辅料和去离子水,进行砂磨,控制浆料的粒度在1.5μm;
[0047]
其中,预烧料和辅料∶去离子水的质量比1∶2,砂磨时间4h;
[0048]
s5.压制成型:进行喷雾造粒,将喷雾料在10mpa下加压成25*15*8的标环;
[0049]
s6.烧结:标环烧结前,在露天放置72小时,使标环在空气中膨胀,释放其内部应力,并使标环内部的颗粒自由舒展,再将标环进行烧结,所述烧结具体包括:从室温以1.2℃/min速率升温至580℃,580℃保温1h,再以1.8℃/min速率升温至960℃,960℃保温1.5h之后,再以3.2℃/min速率升温至1120℃,1120℃保温2.5h之后,随炉冷却,得到功率型铁氧
体。
[0050]
实施例3
[0051]
一种功率型铁氧体材料,所述功率型铁氧体材料由主料和辅料制成,所述主料以摩尔百分比计包括以下组分:52.6mol%fe2o3,21.5mol%nio和余量的zno;以所述功率型铁氧体材料的重量作为基准,所述辅料的组分包括:0.05wt%geo2、0.05wt%hfo2、0.01wt%oso4、0.04wt%tl2o、0.01wt%tl2o3和0.1wt%teo2。
[0052]
上述功率型铁氧体材料的制备方法,包括如下步骤:
[0053]
s1.混合,将主料按比例分别放入振磨机中进行干式混合;
[0054]
s2.湿磨,将步骤s1混合之后的主料装入球磨罐中,并加入氧化锆球和去离子水,进行湿法混合球磨;
[0055]
其中,主料∶氧化锆球∶去离子水的质量比1∶2∶1.5,球磨时间2h;
[0056]
s3.预烧,将步骤s2湿磨之后的混合料放入烧结炉内,在空气气氛中进行预烧,所述预烧具体包括:从室温以1.1℃/min速率升温至532℃,532℃保温1h,再以1.6℃/min速率升温至812℃,812℃保温1.8h之后,随炉冷却;
[0057]
s4.掺杂,将步骤s3的预烧料放入砂磨机中,并分别加入按比例称取的辅料和去离子水,进行砂磨,控制浆料的粒度在1.0μm;
[0058]
其中,预烧料和辅料∶去离子水的质量比1∶1,砂磨时间8h;
[0059]
s5.压制成型:进行喷雾造粒,将喷雾料在10mpa下加压成25*15*8的标环;
[0060]
s6.烧结:标环烧结前,在露天放置24小时,使标环在空气中膨胀,释放其内部应力,并使标环内部的颗粒自由舒展,再将标环进行烧结,所述烧结具体包括:从室温以1.2℃/min速率升温至520℃,520℃保温1.5h,再以1.8℃/min速率升温至820℃,820℃保温2h之后,再以3.2℃/min速率升温至1080℃,1080℃保温4h之后,随炉冷却,得到功率型铁氧体。
[0061]
比较例1
[0062]
一种功率型铁氧体材料,所述功率型铁氧体材料由主料制成,所述主料以摩尔百分比计包括以下组分:53.4mol%fe2o3,17.2mol%nio和余量的zno。
[0063]
上述功率型铁氧体材料的制备方法,包括如下步骤:
[0064]
s1.混合,将主料按比例分别放入振磨机中进行干式混合;
[0065]
s2.湿磨,将步骤s1混合之后的主料装入球磨罐中,并加入氧化锆球和去离子水,进行湿法混合球磨;
[0066]
其中,主料∶氧化锆球∶去离子水的质量比1∶3∶1,球磨时间4h;
[0067]
s3.预烧,将步骤s2湿磨之后的混合料放入烧结炉内,在空气气氛中进行预烧,所述预烧具体包括:从室温以1.1℃/min速率升温至550℃,550℃保温0.8h,再以1.6℃/min速率升温至875℃,875℃保温1.4h之后,随炉冷却;
[0068]
s4.砂磨,将步骤s3的预烧料放入砂磨机中,并加入按比例称取去离子水,进行砂磨,控制浆料的粒度在1.2μm;
[0069]
其中,预烧料∶去离子水的质量比1∶1.5,砂磨时间6h;
[0070]
s5.压制成型:进行喷雾造粒,将喷雾料在10mpa下加压成25*15*8的标环;
[0071]
s6.烧结:标环烧结前,在露天放置36小时,使标环在空气中膨胀,释放其内部应
力,并使标环内部的颗粒自由舒展,再将标环进行烧结,所述烧结具体包括:从室温以1.2℃/min速率升温至550℃,550℃保温1~1.5h,再以1.8℃/min速率升温至890℃,890℃保温1.8h之后,再以3.2℃/min速率升温至1100℃,1100℃保温3.2h之后,随炉冷却,得到功率型铁氧体。
[0072]
比较例2
[0073]
一种功率型铁氧体材料,所述功率型铁氧体材料由主料制成,所述主料以摩尔百分比计包括以下组分:50.5mol%fe2o3,19.5mol%nio、23.8mol%zno和6.2mol%cuo;制备方法与比较例1相同。
[0074]
比较例3
[0075]
将主料成分fe2o3的添加量调整至52.5mol%,其他成分和制备方法与实施例1相同。
[0076]
比较例4
[0077]
将主料成分fe2o3的添加量调整至54.5mol%,其他成分和制备方法与实施例1相同。
[0078]
比较例5
[0079]
将主料成分nio的添加量调整至12.3mol%,其他成分和制备方法与实施例1相同。
[0080]
比较例6
[0081]
将主料成分nio的添加量调整至22.0mol%,其他成分和制备方法与实施例1相同。
[0082]
比较例7
[0083]
不添加辅料成分geo2,其他成分和制备方法与实施例1相同。
[0084]
比较例8
[0085]
不添加辅料成分hfo2,其他成分和制备方法与实施例1相同。
[0086]
比较例9
[0087]
不添加辅料成分oso4,其他成分和制备方法与实施例1相同。
[0088]
比较例10
[0089]
不添加辅料成分tl2o,其他成分和制备方法与实施例1相同。
[0090]
比较例11
[0091]
不添加辅料成分tl2o3,其他成分和制备方法与实施例1相同。
[0092]
比较例12
[0093]
不添加辅料成分teo2,其他成分和制备方法与实施例1相同。
[0094]
比较例13
[0095]
将预烧温度调整至810℃,烧结温度1070℃,其他成分和制备方法与实施例1相同。
[0096]
比较例14
[0097]
将预烧温度调整至940℃,烧结温度1130℃,其他成分和制备方法与实施例1相同。
[0098]
测试例1
[0099]
将上述各实施例中烧结后得到的标环进行测试和评价。在匝数n=20ts条件下,用e4980a型lcr测试仪测试磁环样品的起始磁导率μi;用sy-8258型b-h分析仪测试样品25℃时的饱和磁感应强度bs(1khz/1200a/m),用sy-8218型b-h分析仪测试样品的功率损耗pcv(700khz/100mt),得到的测试和评价结果如下表1所示。
[0100]
表1实施例1~3、比较例1~14中标环样品性能测试结果
[0101][0102][0103]
综合实施例1~3与比较例1~2可看出,没有添加辅料所制成的铁氧体材料,磁导率和磁感应强度均明显低,综合功率损耗也十分高;由实施例1~3与比较例3~6可看出,作为主要成分的氧化铁、氧化镍、氧化锌的含量没有在限定范围内,材料的磁导率、饱和磁感应强度、功率损耗、耐高温焊锡温度和机械强度均受到预料不到的负面影响;由实施例1~3与比较例7~12可看出,没有协同掺杂辅料成分geo2、hfo2、oso4、tl2o、tl2o3和teo2制成的磁性能(磁导率、磁感应强度)和机械强度均严重下降,并且功率损耗pcv明显升高,通过实施例1~3与对比例13~14的比较可以看出,比较例13~14由于烧结温度没有在特定的范围内,导致烧结不致密,有大量的气孔存在,从而影响了磁性能。
[0104]
本发明通过将作为主要成分的氧化铁、氧化镍、氧化锌的含量限定在规定范围内,并对辅助成分的组分进行非显而易见的协同组合和含量限定,并且在特定的工艺条件下,得到的功率型铁氧体材料既具有高磁导率、高饱和磁感应强度、低功率损耗,又能够提高耐高温焊锡温度、机械强度,增强韧性,拓宽了铁氧体材料的应用范围,满足大电流和高密度安装应用场合的需求,更好地满足了制作而成的器件小型化的要求。
[0105]
上述实施例仅是本发明的较优实施方式,凡是依据本发明的技术实质对以上实施例所做的任何简单修饰、修改及替代变化,均属于本发明技术方案的范围内。