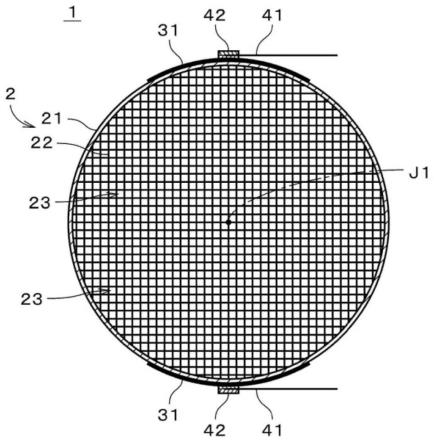
1.本发明涉及碳化硅质多孔体及其制造方法、包含该碳化硅质多孔体而构成的蜂窝结构体、以及具备该蜂窝结构体的电加热催化器。
背景技术:2.以往,为了对从汽车等的发动机中排出的废气中包含的hc、co、nox等有害物质进行净化处理,使用在柱状的蜂窝结构体等担载有催化剂的催化转换器。
3.例如,专利文献1中公开一种蜂窝结构体,其可以作为柴油废气净化用的过滤器(dpf)加以利用。该蜂窝结构体由含有1质量%~35质量%的镍硅化物或锆硅化物及0.5质量%~10质量%的氧化铝(al2o3)的碳化硅质多孔体构成。该碳化硅质多孔体的气孔率为38%~80%,据此,实现了dpf中的高气体透过性能。另外,该碳化硅质多孔体中,作为主成分而含有的β-sic的至少一部分的形状为粒径10μm以上的粒子状。据此,提高了碳化硅质多孔体的强度。专利文献2中公开了一种蜂窝结构体,其中,以氧化硼代替专利文献1的氧化铝,该蜂窝结构体由按氧化硼(b2o3)换算含有0.1质量%~10质量%的硼(b)的碳化硅质多孔体构成。
4.上述的催化转换器中,在废气的净化处理时,催化剂需要升温至活性温度,但是,在发动机刚启动后等,催化转换器的温度较低,因此,废气的净化性能有可能降低。特别是,在插电式混合动力汽车(phev)、混合动力汽车(hv)中,仅利用马达进行行驶,由此催化剂的温度容易降低。因此,利用了电加热催化器(ehc:electrically heated catalyst),其在导电性的催化转换器连接一对电极,通过通电而使催化转换器自身发热,由此将催化剂预热。
5.例如,专利文献3中提出如下方案,即,作为可用于电加热催化器的蜂窝结构体,含有作为骨料的碳化硅粒子和作为使该碳化硅粒子粘结的粘结材料的硅,体积电阻(即、体积电阻率)为1ω
·
cm~400ω
·
cm。
6.现有技术文献
7.专利文献
8.专利文献1:日本特许第5193804号公报
9.专利文献2:日本特许第5053981号公报
10.专利文献3:日本特许第5735428号公报
技术实现要素:11.但是,在专利文献1及专利文献2的蜂窝结构体中,由于sic粒子的粒径不够大,所以,成为导电通路的sic粒子彼此的粘结部分有可能变细。另外,该蜂窝结构体中,除了sic粒子彼此的粘结以外,几乎不包含形成导电通路的构成。因此,蜂窝结构体暴露于高温氧化气氛的情况下,sic粒子彼此的较细的粘结部分被氧化而导致导电通路被切断,体积电阻率有可能大幅增大。因此,该蜂窝结构体很难转用于电加热催化器。另外,近年来,专利文献3
的蜂窝结构体这样的用于电加热催化器的蜂窝结构体中,要求体积电阻率进一步降低。
12.本发明是鉴于上述课题而完成的,其目的在于,提供具有高耐氧化性的碳化硅质多孔体。
13.本发明的优选的一个方案所涉及的碳化硅质多孔体包含:β-sic粒子、si粒子、以及金属硅化物粒子。所述β-sic粒子的最大粒径为15μm以上。所述si粒子的含有率为10质量%以上。所述si粒子的最大粒径为40μm以下。在所述si粒子的表面设置有厚度0.01μm以上且5μm以下的氧化物被膜。
14.优选为,所述金属硅化物粒子的含有率为5质量%以上,所述金属硅化物粒子的最大粒径为20μm以下。
15.优选为,所述碳化硅质多孔体还包含al及b中的1种以上。
16.优选为,所述金属硅化物粒子为镍硅化物。
17.优选为,于室温的体积电阻率为0.01ω
·
cm以上且小于1.0ω
·
cm。
18.优选为,在950℃的大气中暴露50小时后的体积电阻率的变化率为100%以下。
19.本发明还涉及蜂窝结构体。本发明的优选的一个方案所涉及的蜂窝结构体具备:筒状外壁;以及格子状的隔壁,该隔壁将所述筒状外壁的内部分隔为多个隔室。所述筒状外壁及所述隔壁是包含上述的碳化硅质多孔体而构成的。
20.本发明还涉及进行从发动机中排出的废气的净化处理的电加热催化器。本发明的优选的一个方案所涉及的电加热催化器具备:上述的蜂窝结构体;以及一对电极部,该一对电极部固定于所述蜂窝结构体的外侧面而对所述蜂窝结构体赋予电流。
21.本发明还涉及碳化硅质多孔体的制造方法。本发明的优选的一个方案所涉及的碳化硅质多孔体的制造方法包括:将包含si、c、及金属硅化物的原料金属的原料粉末成型并进行烧成而得到烧成体的工序、以及对所述烧成体实施氧化处理而得到碳化硅质多孔体的工序。所述碳化硅质多孔体包含:β-sic粒子、si粒子、以及金属硅化物粒子。所述β-sic粒子的最大粒径为15μm以上。所述si粒子的含有率为10质量%以上。所述si粒子的最大粒径为40μm以下。在所述si粒子的表面设置有厚度0.01μm以上且5μm以下的氧化物被膜。
22.优选为,所述原料金属为ni,所述原料金属的平均粒径为5μm以下。
23.发明效果
24.本发明中,能够提供具有高耐氧化性的碳化硅质多孔体。
附图说明
25.图1是一个实施方式所涉及的电加热催化器的截面图。
26.图2是表示蜂窝结构体的制造流程的图。
27.图3是实施例的蜂窝结构体的sem图像。
28.图4是比较例的蜂窝结构体的sem图像。
29.图5是比较例的蜂窝结构体的sem图像。
30.符号说明
[0031]1…
电加热催化器、2
…
蜂窝结构体、21
…
筒状外壁、22
…
隔壁、41
…
电极部、s11~s13
…
步骤。
具体实施方式
[0032]
图1是表示本发明的一个实施方式所涉及的电加热催化器1(ehc:electrically heated catalyst)的截面图。电加热催化器1为在一个方向上较长的柱状部件,图1中示出与电加热催化器1的长度方向垂直的截面。电加热催化器1进行从汽车等的发动机中排出的废气的净化处理。
[0033]
电加热催化器1具备:蜂窝结构体2、一对电极层31、以及一对电极部41。蜂窝结构体2、一对电极层31及一对电极部41具有导电性。蜂窝结构体2为具有蜂窝结构的大致圆柱状的部件,且是电加热催化器1中供催化剂担载的载体。一对电极层31固定于蜂窝结构体2的外侧面。一对电极层31为配置成夹着沿着蜂窝结构体2的长度方向延伸的中心轴j1而对置的箔状或板状的部件。各电极层31沿着蜂窝结构体2的外侧面而设置。
[0034]
一对电极部41借助接合部42而固定于一对电极层31的表面。换言之,一对电极部41隔着一对电极层31而间接地固定于蜂窝结构体2的外侧面。电极部41为例如大致带状的部件。电极部41为向蜂窝结构体2供电的电极端子的一部分。电极部41与省略图示的电源连接。如果从该电源经由电极部41而向一对电极层31之间施加电压,则电流流通于蜂窝结构体2,蜂窝结构体2利用焦耳热而发热。据此,担载于蜂窝结构体2的催化剂被预热。向电加热催化器1施加的电压为例如12v~900v,优选为64v~600v。应予说明,该电压可以适当变更。
[0035]
蜂窝结构体2为内部被分隔为多个隔室23的隔室结构体。蜂窝结构体2具备筒状外壁21和隔壁22。筒状外壁21为沿着长度方向(即、与图1中的纸面垂直的方向)延伸的筒状的部位。与长度方向垂直的筒状外壁21的截面形状为大致圆形。该截面形状可以为椭圆形、多边形等其他形状。
[0036]
隔壁22为设置于筒状外壁21的内部并将该内部分隔为多个隔室23的格子状的部件。多个隔室23分别为在蜂窝结构体2的大致全长沿着长度方向延伸的空间。各隔室23为供废气流动的流路,废气的净化处理用的催化剂担载于隔壁22。与长度方向垂直的各隔室23的截面形状为例如大致矩形。该截面形状可以为多边形或圆形等其他形状。从降低废气在隔室23内流动时的压力损失的观点出发,该截面形状优选为四边形或六边形。另外,从提高蜂窝结构体2的结构强度、及加热均匀性的观点出发,该截面形状优选为长方形。多个隔室23原则上具有相同的截面形状。在多个隔室23中可以包含不同截面形状的隔室23。
[0037]
筒状外壁21的长度方向上的长度为例如30mm~200mm。筒状外壁21的外径为例如25mm~120mm。从提高蜂窝结构体2的耐热性的观点出发,蜂窝结构体2的底面的面积(即、蜂窝结构体2的底面中由筒状外壁21包围的区域的面积)优选为2000mm2~20000mm2,更优选为5000mm2~15000mm2。从防止流通于隔室23的流体流出、提高蜂窝结构体2的强度、及筒状外壁21与隔壁22之间的强度平衡的观点出发,筒状外壁21的厚度为例如0.1mm~1.0mm,优选为0.15mm~0.7mm,更优选为0.2mm~0.5mm。
[0038]
隔壁22的长度方向上的长度与筒状外壁21大致相同。从提高蜂窝结构体2的强度、及降低废气在隔室23内流动时的压力损失的观点出发,隔壁22的厚度为例如0.1mm~0.3mm,优选为0.15mm~0.25mm。
[0039]
从增大隔壁22的催化剂担载面积、及降低废气在隔室23内流动时的压力损失的观点出发,蜂窝结构体2的隔室密度(即、与长度方向垂直的截面中的每单位面积的隔室23的数量)为例如40隔室/cm2~150隔室/cm2,优选为70隔室/cm2~100隔室/cm2。该隔室密度如
下求解,即,蜂窝结构体2的全部隔室数除以蜂窝结构体2的底面中的比筒状外壁21的内周缘更靠内侧的区域的面积,由此求出隔室密度。隔室23的大小、数量、隔室密度等可以进行各种变更。
[0040]
蜂窝结构体2的筒状外壁21及隔壁22是包含以下说明的碳化硅质多孔体而构成的。本实施方式中,筒状外壁21及隔壁22实质上仅由该碳化硅质多孔体构成。
[0041]
该碳化硅质多孔体是主成分为碳化硅(sic)的多孔质陶瓷。碳化硅质多孔体为包含β-sic粒子、si粒子(即、硅粒子)、以及金属硅化物粒子的复合烧结体。β-sic粒子为碳化硅质多孔体的骨料。si粒子为使β-sic粒子粘结的粘结材料(即、基质)。碳化硅质多孔体中,优选多个β-sic粒子以在β-sic粒子间形成细孔的方式通过si粒子而粘结。
[0042]
碳化硅质多孔体中的β-sic粒子的含有率为例如30质量%以上,优选为50质量%以上。另外,β-sic粒子的含有率为例如90质量%以下,优选为70质量%以下。
[0043]
碳化硅质多孔体中的β-sic粒子的最大粒径为15μm以上,优选为20μm以上。像这样,通过使β-sic粒子的最大粒径变大(即、使β-sic粒子粗大化),使得形成导电通路的β-sic粒子彼此的粘结部变粗。因此,碳化硅质多孔体的体积电阻率降低。另外,即便β-sic粒子彼此的粘结部被氧化的情况下,导电通路也不易被切断。因此,即便碳化硅质多孔体暴露于高温氧化气氛的情况下,碳化硅质多孔体的体积电阻率变化也得以抑制。即,碳化硅质多孔体的耐氧化性得到提高。应予说明,β-sic粒子的最大粒径的上限没有特别限定,作为现实的范围,例如为120μm以下。
[0044]
β-sic粒子的最大粒径为利用以下方法求出的值。首先,利用电子显微镜,以任意倍率(例如、500倍)观察碳化硅质多孔体的任意截面,选出视野内的最大粒子(即、在视野内具有最大面积的粒子)。接下来,求出该最大粒子的长径及短径。具体而言,求出将该最大粒子的外周的2点连结且从重心通过的最大径作为长径。另外,求出将该最大粒子的外周的2点连结且从重心通过的最小径作为短径。长径及短径的测定可以采用例如media cybernetics公司制的图像解析软件“image pro 9”。然后,将长径和短径的算术平均设为该最大粒子的粒径。接下来,在碳化硅质多孔体的上述截面中变更视野的位置,与上述同样地求出最大粒子的粒径。然后,在碳化硅质多孔体的上述截面中的规定数量(2以上、例如20)的视野中分别取得最大粒子的粒径,将该规定数量的最大粒子的粒径的算术平均设为β-sic粒子的最大粒径。
[0045]
碳化硅质多孔体中的si粒子的含有率为10质量%以上,优选为12质量%以上。另外,si粒子的含有率为例如70质量%以下,优选为50质量%以下。碳化硅质多孔体中的si粒子的最大粒径为例如5μm以上,优选为10μm以上。另外,si粒子的最大粒径为40μm以下,优选为20μm以下。si粒子的最大粒径利用与上述的β-sic粒子的最大粒径同样的方法进行求解。
[0046]
si粒子的含有率设为10质量%以上,si粒子的最大粒径设为40μm以下,由此,碳化硅质多孔体中,si粒子的分布均匀性得到提高,形成利用大致均等分布的si粒子而将β-sic粒子彼此连结的导电通路。据此,碳化硅质多孔体的体积电阻率进一步降低。另外,即便碳化硅质多孔体暴露于高温氧化气氛的情况下,由氧化所导致的导电通路切断也得以抑制,碳化硅质多孔体的体积电阻率变化得到进一步的抑制。即,碳化硅质多孔体的耐氧化性进一步提高。
[0047]
碳化硅质多孔体中,在si粒子的表面设置有氧化物被膜。该氧化物被膜的厚度为
0.01μm以上且5μm以下。据此,即便碳化硅质多孔体暴露于高温氧化气氛的情况下,si粒子的氧化也得以抑制,碳化硅质多孔体的体积电阻率变化得到更进一步的抑制。即,碳化硅质多孔体的耐氧化性更进一步提高。上述氧化物被膜的厚度优选为0.05μm以上。另外,氧化物被膜的厚度优选为1.0μm以下。
[0048]
氧化物被膜的厚度为利用以下方法求出的值。首先,利用电子显微镜,以任意倍率(例如、10000倍)观察碳化硅质多孔体的包含氧化物被膜的任意截面,求出视野内的氧化物被膜的最大厚度。接下来,在碳化硅质多孔体的上述截面中变更视野的位置,与上述同样地求出氧化物被膜的最大膜厚。然后,在碳化硅质多孔体的上述截面中的规定数量(2以上、例如20)的视野中分别取得氧化物被膜的最大膜厚,将该规定数量的最大膜厚的算术平均设为氧化物被膜的厚度。
[0049]
上述氧化物被膜将si粒子部分地或整体地被覆。氧化物被膜包含例如二氧化硅(sio2)。该sio2是后述的碳化硅质多孔体制造时si粒子的表面被氧化而生成的。该氧化物被膜可以包含除了sio2以外的氧化物。另外,该氧化物被膜可以不含sio2,而由除了sio2以外的氧化物构成。
[0050]
碳化硅质多孔体中的金属硅化物粒子的含有率为例如5质量%以上,优选为10质量%以上。另外,金属硅化物粒子的含有率为例如30质量%以下,优选为20质量%以下。碳化硅质多孔体中的金属硅化物粒子的最大粒径为例如5μm以上,优选为10μm以上。另外,金属硅化物粒子的最大粒径为例如20μm以下,优选为15μm以下。金属硅化物粒子的最大粒径利用与上述的β-sic粒子的最大粒径同样的方法进行求解。
[0051]
金属硅化物粒子的含有率设为5质量%以上,金属硅化物粒子的最大粒径设为20μm以下,由此,在碳化硅质多孔体中,金属硅化物粒子的分布均匀性得到提高。如后所述,在利用反应烧结来制造碳化硅质多孔体时,金属硅化物(metal silicide)大致均等地分布,由此,在碳化硅质多孔体的大致整体中,β-sic粒子的粒生长(即、粗大化)得到促进。据此,形成导电通路的β-sic粒子彼此的粘结部进一步变粗,碳化硅质多孔体的体积电阻率进一步降低。另外,即便碳化硅质多孔体暴露于高温氧化气氛的情况下,导电通路也进一步不易切断,碳化硅质多孔体的体积电阻率变化得到进一步的抑制。即,碳化硅质多孔体的耐氧化性进一步提高。
[0052]
碳化硅质多孔体中,通过包含金属硅化物粒子,使得热传导率也有所增大。另外,金属硅化物粒子的含有率设为20质量%以下,由此,碳化硅质多孔体的热膨胀率降低,耐热冲击性得到提高。应予说明,上述的氧化物被膜也可以设置于金属硅化物粒子的表面。据此,即便碳化硅质多孔体暴露于高温氧化气氛的情况下,金属硅化物粒子的氧化也得以抑制。
[0053]
上述金属硅化物粒子优选为镍硅化物。在后述的碳化硅质多孔体制造时,通过原料中包含镍(ni),使得si的熔点降低,β-sic粒子的粒生长(即、粗大化)得到进一步的促进。据此,形成导电通路的β-sic粒子彼此的粘结部更进一步变粗,碳化硅质多孔体的体积电阻率更进一步降低。另外,即便碳化硅质多孔体暴露于高温氧化气氛的情况下,导电通路也更进一步不易切断,碳化硅质多孔体的体积电阻率变化得到更进一步的抑制。即,碳化硅质多孔体的耐氧化性更进一步提高。
[0054]
本实施方式中,上述金属硅化物粒子为二硅化镍(nisi2)。据此,碳化硅质多孔体
的耐热性得到提高。应予说明,金属硅化物粒子可以除了包含nisi2以外,还包含除了nisi2以外的镍硅化物(例如、ni3si、ni5si2、ni2si、nisi)。或者,金属硅化物粒子可以不含nisi2,而是包含除了nisi2以外的镍硅化物。金属硅化物粒子可以除了包含镍硅化物以外,还包含除了镍硅化物以外的金属硅化物(例如、锆硅化物、铁硅化物、钛硅化物、钨硅化物等)。或者,金属硅化物粒子可以不含镍硅化物,而是包含除了镍硅化物以外的金属硅化物。
[0055]
碳化硅质多孔体可以包含铝(al)及硼(b)中的1种以上。al和/或b在后述的碳化硅质多孔体制造时作为助剂进行添加。在碳化硅质多孔体制造时,通过原料中包含al和/或b,使得β-sic粒子的粒生长(即、粗大化)得到促进。据此,形成导电通路的β-sic粒子彼此的粘结部变粗,碳化硅质多孔体的体积电阻率降低。另外,即便碳化硅质多孔体暴露于高温氧化气氛的情况下,导电通路也不易切断,碳化硅质多孔体的体积电阻率变化得到抑制。即,碳化硅质多孔体的耐氧化性提高。
[0056]
碳化硅质多孔体中包含al的情况下,al以元素的形式包含在其中即可,al可以以任意状态包含在碳化硅质多孔体中。例如,al可以以氧化铝(al2o3)的形式包含在碳化硅质多孔体中。同样地,碳化硅质多孔体中包含b的情况下,b以元素的形式包含在其中即可,b可以以任意状态包含在碳化硅质多孔体中。例如,b可以以氧化硼(b2o3)的形式包含在碳化硅质多孔体中。
[0057]
关于碳化硅质多孔体中的β-sic相、si相及金属硅化物相的鉴定及定量,采用粉末x射线衍射法(xrd)的结果,利用wppd(whole-powder-pattern decomposition)法,进行图案拟合来进行鉴定及定量。这些解析可以采用例如bruker公司制“topas”等软件。
[0058]
于室温的碳化硅质多孔体的体积电阻率为0.01ω
·
cm以上且小于1.0ω
·
cm。本说明书中,“室温”是指20℃,只要没有特别说明,“体积电阻率”是指于室温的体积电阻率。碳化硅质多孔体的体积电阻率设为小于1.0ω
·
cm,由此,电加热催化器1的通电性提高,实现了电加热催化器1的迅速升温。另外,碳化硅质多孔体的体积电阻率设为0.01ω
·
cm以上,由此,即便对碳化硅质多孔体赋予了比较高的电压的情况下,也能够防止电流过大而导致电路受损。碳化硅质多孔体的体积电阻率优选为0.5ω
·
cm以下。另外,碳化硅质多孔体的体积电阻率优选为0.1ω
·
cm以上。可以利用四端子法(jis c2525)来测定该体积电阻率。
[0059]
将碳化硅质多孔体在作为高温氧化气氛的950℃的大气中暴露50小时后的体积电阻率的变化率(以下也称为“电阻变化率”。)优选为100%以下。该变化率为如下值,即,将碳化硅质多孔体在950℃的大气中暴露50小时后的体积电阻率除以进行该暴露之前的碳化硅质多孔体的体积电阻率(以下也称为“初始电阻率”。)得到的值减去1的结果以百分率表示得到的值。本说明书中,只要没有特别说明,“电阻变化率”是指:在950℃的大气中暴露50小时后的碳化硅质多孔体的体积电阻率的变化率。
[0060]
碳化硅质多孔体的电阻变化率设为100%以下,由此,即便在碳化硅质多孔体暴露于高温氧化气氛的情况下,碳化硅质多孔体的体积电阻率变动也得到很好的抑制。据此,电加热催化器1的通电性能等各性能被维持在期望的范围内。碳化硅质多孔体的电阻变化率更优选为50%以下。应予说明,碳化硅质多孔体的体积电阻率有可能因β-sic粒子、si粒子中包含的杂质等的影响而降低。这种情况下,电阻变化率优选为-50%以上,更优选为-10%以上。由于希望碳化硅质多孔体的体积电阻率没有变动,所以电阻变化率优选接近于0%。
[0061]
碳化硅质多孔体的气孔率为例如30%以上,优选为40%以上。另外,该气孔率为例如70%以下,优选为65%以下。通过使该气孔率为30%以上,能够降低碳化硅质多孔体的杨氏模量,使耐热冲击性提高。另外,通过使该气孔率为70%以下,使得碳化硅质多孔体的致密性得到提高。结果,碳化硅质多孔体的体积电阻率降低,并且,碳化硅质多孔体的耐氧化性及强度提高。例如,可以采用水银孔度计等,利用水银压入法(jis r1655),测定该气孔率。
[0062]
碳化硅质多孔体的气孔径为例如1μm以上,优选为2μm以上。另外,该气孔径为例如15μm以下,优选为10μm以下。通过使该气孔径为1μm以上,能够抑制碳化硅质多孔体的比表面积过大而导致耐氧化性降低。另外,通过使该气孔径为15μm以下,使得碳化硅质多孔体的致密性得到提高。结果,碳化硅质多孔体的体积电阻率降低,并且,碳化硅质多孔体的耐氧化性及强度提高。本说明书中,“气孔径”是指:碳化硅质多孔体的平均细孔径。例如,可以采用水银孔度计等,利用水银压入法(jis r1655),测定该气孔径。
[0063]
碳化硅质多孔体的体积密度为例如1.0g/cm3以上,优选为1.1g/cm3以上。另外,该体积密度为例如1.5g/cm3以下,优选为1.3g/cm3以下。通过使该体积密度为1.0g/cm3以上,使得碳化硅质多孔体的体积电阻率降低,并且,碳化硅质多孔体的耐氧化性及强度提高。另外,通过使该体积密度为1.5g/cm3以下,使得碳化硅质多孔体的热容量降低,容易升温。例如,可以采用水银孔度计等,利用水银压入法(jis r1655),测定该体积密度。
[0064]
电极层31沿着蜂窝结构体2的外侧面而在长度方向上延伸,并且,在以中心轴j1为中心的周向(以下简称为“周向”。)上扩展。电极层31使来自电极部41的电流在长度方向及周向上扩展,使得蜂窝结构体2的发热均匀性提高。电极层31的长度方向上的长度为例如蜂窝结构体2的长度方向上的长度的80%以上,优选为90%以上。更优选为,电极层31在蜂窝结构体2的全长上延伸。
[0065]
电极层31的周向上的角度(即,图1中,从电极层31的周向两端向中心轴j1延伸的2条线段所成的角度)为例如30
°
以上,优选为40
°
以上,更优选为60
°
以上。另一方面,从抑制一对电极层31过于接近而导致在蜂窝结构体2内部流通的电流减少的观点出发,电极层31的周向上的角度为例如140
°
以下,优选为130
°
以下,更优选为120
°
以下。
[0066]
在图1所示的例子中,一对电极层31的中心间的周向上的角度(即、图1中,从2个电极层31的周向中心向中心轴j1延伸的2条线段所成的180
°
以下的角度)为180
°
,不过,该角度可以适当变更。例如,该角度为150
°
以上,优选为160
°
以上,更优选为170
°
以上。
[0067]
从防止电阻过大,并且,防止将蜂窝结构体2收纳于容器内时的(即、装罐时的)破损的观点出发,电极层31的厚度(即、径向上的厚度)为例如0.01mm~5mm,优选为0.01mm~3mm。
[0068]
电极层31的体积电阻率优选低于蜂窝结构体2的体积电阻率。据此,与蜂窝结构体2相比,电流容易流通于电极层31,电流容易在蜂窝结构体2的长度方向及周向上扩展。
[0069]
电极层31由例如导电性陶瓷、金属、或导电性陶瓷与金属的复合材料形成。该导电性陶瓷为例如碳化硅(sic)、或硅化钽(tasi2)、硅化铬(crsi2)等金属硅化物。该金属为例如铬(cr)、铁(fe)、钴(co)、镍(ni)、si或钛(ti)。从降低热膨胀率的观点出发,电极层31的材质可以为在1种或2种以上的金属中添加氧化铝、多铝红柱石、氧化锆、堇青石、氮化硅及氮化铝等得到的复合材料。
[0070]
电极层31的材质优选能够与蜂窝结构体2同时烧成。从兼具有耐热性和导电性的观点出发,电极层31的材质优选为以sic或硅-碳化硅(si-sic)复合材料为主成分(具体而言,含量为90质量%以上)的陶瓷,更优选为sic或si-sic复合材料。si-sic复合材料优选含有作为骨料的sic粒子及作为使sic粒子粘结的粘结材料的si,多个sic粒子以在sic粒子间形成细孔的方式通过si而粘结。
[0071]
电极部41由例如金属单质或合金形成。从具有高耐腐蚀性和适当的体积电阻率及热膨胀率的观点出发,电极部41的材质优选为包含cr、fe、co、ni、ti及铝(al)中的至少1种的合金。电极部41优选为不锈钢,更优选包含al。另外,电极部41可以由金属-陶瓷混合材料形成。该金属-陶瓷混合材料中包含的金属为例如cr、fe、co、ni、si或ti的金属单质、或者含有选自由这些金属构成的组中的至少一种金属的合金。该金属-陶瓷混合材料中包含的陶瓷为例如碳化硅(sic)、或金属硅化物(例如、硅化钽(tasi2)、硅化铬(crsi2))等金属化合物。作为该陶瓷,可以采用金属陶瓷(即、陶瓷与金属的复合材料)。该金属陶瓷为例如金属硅与碳化硅的复合材料、金属硅化物与金属硅、碳化硅的复合材料、或在上述的1种以上的金属中添加氧化铝、多铝红柱石、氧化锆、堇青石、氮化硅及氮化铝等绝缘性陶瓷中的1种以上得到的复合材料。
[0072]
接合部42分别由例如包含金属及氧化物的复合材料形成。该金属为例如不锈钢、ni-fe系合金及si中的1种以上。该氧化物为堇青石系玻璃、二氧化硅(sio2)、氧化铝(al2o3)、氧化镁(mgo)及它们的复合氧化物中的1种以上。
[0073]
接合部42中,可以包含除了金属以外的导电性物质来代替上述金属,或者可以除了包含上述金属以外,还包含除了金属以外的导电性物质。该导电性物质为例如硼化锌及硼化钽等硼化物、氮化钛及氮化锆等氮化物、以及碳化硅及碳化钨等碳化物中的1种以上。
[0074]
接下来,参照图2,对蜂窝结构体2的制造流程的一例进行说明。首先,按规定的组成,称量包含si、碳(c)、及金属硅化物的原料金属(本实施方式中为ni)的原料粉末、以及粘合剂、造孔剂等,利用干式混合器进行干式混合,由此得到混合粉末。应予说明,也可以利用采用了溶剂(例如、离子交换水或有机溶剂等)的湿式混合进行该原料粉末及粘合剂等的混合。上述原料粉末中,可以除了作为主原料的si、c及ni以外,还添加有助剂。该助剂为例如al和/或b。
[0075]
作为粘合剂,例如可以利用甲基纤维素、羟丙氧基纤维素、羟乙基纤维素、羧甲基纤维素、聚乙烯醇等。作为造孔剂,可以利用石墨、小麦粉、淀粉、酚醛树脂、聚甲基丙烯酸甲酯、聚乙烯、聚对苯二甲酸乙二醇酯、发泡树脂(丙烯腈系塑料微球)、吸水性树脂等。
[0076]
接下来,将上述的混合粉末和适量的水等,利用捏合机进行混炼,通过练泥机由得到的混炼物制作坯料。然后,将该坯料挤出成型,由此制作具有蜂窝结构的成型体(以下也称为“蜂窝成型体”。)(步骤s11)。接下来,对蜂窝成型体进行微波干燥,然后,于100℃进行热风干燥。进而,在大气气氛下,于200℃~1000℃对干燥后的蜂窝成型体进行1小时~10小时的脱脂。
[0077]
将脱脂后的蜂窝成型体在氩(ar)气氛等不活泼性气体气氛下于1250℃~1800℃(优选为1300℃~1750℃)进行0.5小时~5小时烧成。据此,制作具有蜂窝结构的烧成体(以下也称为“蜂窝烧成体”。)(步骤s12)。
[0078]
然后,进行蜂窝烧成体的氧化处理,由此制作上述的蜂窝结构体2(步骤s13)。步骤
s13的氧化处理为在蜂窝结构体2使用时暴露于氧化气氛之前进行的预备的氧化处理,以下也称为“预氧化处理”。例如,在大气气氛下,将蜂窝烧成体于900℃~1300℃进行0.5小时~20小时加热,由此进行该预氧化处理。该预氧化处理也称为氧化老化。通过对蜂窝烧成体进行预氧化处理,使得在si粒子的表面生成sio2等氧化物被膜,si粒子的表面由该氧化物被膜被覆。应予说明,预氧化处理时的温度、时间及气氛等可以进行各种变更。另外,上述的蜂窝成型体的干燥、脱脂及烧成时的温度、时间及气氛等也可以进行各种变更。
[0079]
蜂窝结构体2制造中,上述的原料粉末中的ni的平均粒径优选为5μm以下。据此,后述的蜂窝成型体中,ni的分布均匀性得到提高。因此,蜂窝成型体烧成时,蜂窝成型体的大致整体中,β-sic粒子的粒生长(即、粗大化)得到促进。结果,碳化硅质多孔体的体积电阻率进一步降低,并且,碳化硅质多孔体的耐氧化性进一步提高。本说明书中,只要没有特别说明,原料粉末的“平均粒径”为利用激光衍射散射法(jis r1629)进行粒度分布测定得到的值,且是体积基准下的平均粒径。
[0080]
上述的原料粉末中的si的平均粒径为例如1μm~100μm,优选为2μm~80μm。另外,原料粉末中的c的平均粒径为例如5nm~50μm,优选为10nm~30μm。原料粉末中的al的平均粒径为例如1μm~100μm,优选为3μm~50μm。
[0081]
电加热催化器1是通过在如上所述制造的蜂窝结构体2固定一对电极层31及一对电极部41而制造的。电加热催化器1中,在蜂窝结构体2的多个隔室23的内侧面(即、隔壁22的侧面)担载有催化剂。应予说明,对作为蜂窝结构体2的前驱体的蜂窝成型体赋予作为电极层31的原料的电极层糊料,将蜂窝成型体及电极层糊料一同进行烧成,由此可以同时形成一对电极层31和蜂窝结构体2。
[0082]
接下来,参照表1~表3,对本发明所涉及的蜂窝结构体2的实施例及用于与蜂窝结构体2进行比较的比较例进行说明。表1示出实施例的蜂窝结构体2及比较例的蜂窝结构体的原料组成,表2~表3示出实施例的蜂窝结构体2及比较例的蜂窝结构体的组成及特性。
[0083]
表1
[0084][0085]
表2
[0086][0087]
表3
[0088][0089]
如表1所示,实施例1~7及比较例1~4中,变更了作为主原料的si、c、ni的组成、ni的平均粒径、以及助剂的有无、种类及添加量。实施例1~7的蜂窝结构体2利用上述的步骤s11~s13进行制造。步骤s12中的蜂窝成型体的烧成温度及烧成时间为1430℃及2小时。比较例1的蜂窝结构体也是同样的。
[0090]
表2中的β-sic、si及nisi2的含有率利用上述的粉末x射线衍射法进行测定。作为x射线衍射装置,使用封入管式x射线衍射装置(bruker
·
axs株式会社制d8-advance)。测定条件为cukα、40kv、40ma、2θ=10~70
°
,测定的步幅设为0.002
°
。另外,β-sic、si及nisi2的最大粒径利用上述的方法求解。sio2的膜厚利用上述的氧化物被膜的厚度的求法求解。
[0091]
表3中的初始电阻率为利用四端子法(jis c2525)测定得到的体积电阻率。电阻变化率利用上述的方法求解。具体而言,将从蜂窝结构体2的隔壁22切出的试验片在950℃的大气中暴露50小时后,利用四端子法来测定该试验片的体积电阻率(以下也称为“暴露后电阻率”。)。然后,将暴露后电阻率除以初始电阻率得到的值减去1的结果以百分率表示的值设为电阻变化率。对蜂窝结构体的体积电阻率进行测定时的截面积采用开口率进行校正。
[0092]
实施例1中,作为蜂窝结构体2的主原料的si、c、ni的含有率分别为70.9质量%、21.7质量%及7.4质量%,ni的平均粒径为0.5μm。另外,相对于主原料(即、si、c及ni)100质
量份,添加粘合剂10质量份、造孔剂2质量份。应予说明,未添加作为助剂的al及b。
[0093]
实施例1的蜂窝结构体2的构成为β-sic、si、nisi2、及作为氧化物被膜的sio2。sio2的膜厚为0.5μm。si的含有率及最大粒径分别为13质量%及10μm。β-sic的含有率及最大粒径分别为72质量%及22μm。nisi2的含有率及最大粒径分别为13质量%及11μm。
[0094]
图3是表示实施例1的蜂窝结构体2的研磨截面的sem(扫描型电子显微镜)图像。图3中的白色部81为nisi2,黑色部84为气孔。另外,较深的灰色部82为β-sic,较淡的灰色部83为si。图3中,将表示β-sic的灰色部82的一部分用虚线包围,将与si相对应的灰色部83用双点划线包围。后述的图4及图5也是同样的。
[0095]
实施例1中,原料粉末中的si在β-sic及nisi2的生成中没有耗尽,蜂窝结构体2中残留10质量%以上,因此,如上所述,蜂窝结构体2的体积电阻率降低,并且,耐氧化性提高。另外,由于β-sic粒子的最大粒径为15μm以上,所以形成导电通路的β-sic粒子彼此的粘结部变粗,蜂窝结构体2的体积电阻率进一步降低,并且,耐氧化性进一步提高。此外,si粒子的含有率及最大粒径分别为10质量%以上及40μm以下,因此,si粒子的分布均匀性提高,形成利用大致均等地分布的si粒子而将β-sic粒子彼此连结的导电通路。据此,蜂窝结构体2的体积电阻率进一步降低,并且,耐氧化性进一步提高。进而,在si粒子的表面预先设置有厚度0.01μm以上且5μm以下的氧化物被膜(即、sio2的被膜),因此,蜂窝结构体2的耐氧化性更进一步提高。具体而言,实施例1中,蜂窝结构体2的初始电阻率低至0.10ω
·
cm,电阻变化率低至10%。
[0096]
实施例2中,相对于主原料(即、si、c及ni)100质量份,添加了1质量份的作为助剂的al,除此以外,蜂窝结构体2的制作条件与实施例1相同。关于蜂窝结构体2的构成,虽然表中没有示出,但是,在与实施例1相同的构成(即、β-sic、si、nisi2、及作为氧化物被膜的sio2)中加入了al2o3。sio2的膜厚为0.4μm。si的含有率及最大粒径分别为13质量%及35μm。β-sic的含有率及最大粒径分别为70质量%及26μm。nisi2的含有率及最大粒径分别为14质量%及15μm。实施例2中,蜂窝结构体2的初始电阻率低至0.15ω
·
cm,电阻变化率低至20%。
[0097]
实施例3中,将作为助剂的al的添加量变更为2质量份,除此以外,蜂窝结构体2的制作条件与实施例2相同。蜂窝结构体2的构成与实施例2相同。sio2的膜厚为0.3μm。si的含有率及最大粒径分别为13质量%及32μm。β-sic的含有率及最大粒径分别为70质量%及28μm。nisi2的含有率及最大粒径分别为14质量%及12μm。实施例3中,蜂窝结构体2的初始电阻率低至0.12ω
·
cm,电阻变化率低至20%。
[0098]
实施例4中,将作为助剂的al的添加量变更为5质量份,除此以外,蜂窝结构体2的制作条件与实施例2相同。蜂窝结构体2的构成与实施例2相同。sio2的膜厚为0.1μm。si的含有率及最大粒径分别为12质量%及30μm。β-sic的含有率及最大粒径分别为68质量%及33μm。nisi2的含有率及最大粒径分别为14质量%及9μm。实施例4中,蜂窝结构体2的初始电阻率低至0.20ω
·
cm,电阻变化率低至30%。
[0099]
实施例5中,将作为主原料的si、c、ni的含有率分别变更为74.5质量%、17.7质量%及7.8质量%,除此以外,蜂窝结构体2的制作条件与实施例4相同。蜂窝结构体2的构成与实施例4相同。sio2的膜厚为0.05μm。si的含有率及最大粒径分别为24质量%及38μm。β-sic的含有率及最大粒径分别为56质量%及30μm。nisi2的含有率及最大粒径分别为14质
量%及15μm。实施例5中,蜂窝结构体2的初始电阻率低至0.08ω
·
cm,电阻变化率低至50%。
[0100]
实施例6中,未添加助剂,除此以外,蜂窝结构体2的制作条件与实施例5相同。蜂窝结构体2的构成与实施例5相同。sio2的膜厚为0.3μm。si的含有率及最大粒径分别为26质量%及15μm。β-sic的含有率及最大粒径分别为56质量%及17μm。nisi2的含有率及最大粒径分别为16质量%及10μm。实施例6中,蜂窝结构体2的初始电阻率低至0.12ω
·
cm,电阻变化率低至50%。
[0101]
实施例7中,相对于主原料(即、si、c及ni)100质量份,添加了0.5质量份的作为助剂的b,除此以外,蜂窝结构体2的制作条件与实施例1相同。关于蜂窝结构体2的构成,虽然表中没有示出,但是,在与实施例1相同的构成(即、β-sic、si、nisi2、及作为氧化物被膜的sio2)中加入了b2o3。sio2的膜厚为1.0μm。si的含有率及最大粒径分别为12质量%及35μm。β-sic的含有率及最大粒径分别为71质量%及25μm。nisi2的含有率及最大粒径分别为14质量%及15μm。实施例7中,蜂窝结构体2的初始电阻率低至0.52ω
·
cm,电阻变化率低至80%。
[0102]
比较例1中,将ni的平均粒径设为35μm,除此以外,蜂窝结构体的制作条件与实施例1相同。蜂窝结构体的构成与实施例1相同。sio2的膜厚为0.5μm。si的含有率为13质量%。si的最大粒径高达50μm(即、大于40μm)。β-sic的含有率为72质量%。β-sic的最大粒径低至10μm(即、小于15μm)。nisi2的含有率为13质量%。nisi2的最大粒径高达22μm(即、大于20μm)。
[0103]
图4是表示比较例1的蜂窝结构体的研磨截面的sem图像。比较例1中,因最大粒径大于40μm的si粒子偏在,阻碍了β-sic粒子彼此的粘结。另外,β-sic粒子的最大粒径也较小,低于15μm,因此,β-sic粒子的粘结部处的导电通路较细。因此,如果高温氧化气氛中,该si粒子及β-sic粒子的粘结部被氧化,则导电通路被切断而使得体积电阻率大幅增大。因此,蜂窝结构体的耐氧化性降低。此外,比较例1中,最大粒径大于20μm的nisi2粒子偏在,认为存在许多无法利用ni促进β-sic粒子的粒生长的部位。因此,蜂窝结构体的耐氧化性进一步降低。具体而言,比较例1中,蜂窝结构体的初始电阻率为0.15ω
·
cm,电阻变化率高达150%(即、大于100%)。
[0104]
比较例2中,将作为主原料的si、c、ni的含有率分别变更为68.5质量%、24.4质量%及7.2质量%,将ni的平均粒径变更为0.5μm,除此以外,蜂窝结构体的制作条件与实施例1相同。蜂窝结构体的构成与实施例1相同。sio2的膜厚为0.5μm。si的含有率低至5质量%(即、小于10质量%)。si的最大粒径为5μm。β-sic的含有率为87质量%。β-sic的最大粒径低至5μm(即、小于15μm)。nisi2的含有率及最大粒径分别为7质量%及5μm。
[0105]
图5是表示比较例2的蜂窝结构体的研磨截面的sem图像。比较例2中,si粒子的含有率较小,小于10质量%,因此,由将β-sic粒子彼此连结的si粒子形成的导电通路较少,或者实质上不存在。另外,β-sic粒子的最大粒径也较小,小于15μm,因此,β-sic粒子的粘结部处的导电通路较细。因此,蜂窝结构体的体积电阻率比较大,耐氧化性显著降低。具体而言,比较例2中,蜂窝结构体的初始电阻率为0.64ω
·
cm,电阻变化率高达440%(即、大于100%)。
[0106]
比较例3中,将ni的平均粒径设为35μm,除此以外,蜂窝结构体的制作条件与实施
例2相同。蜂窝结构体的构成与实施例2相同。sio2的膜厚为0.5μm。si的含有率及最大粒径分别为12质量%及35μm。β-sic的含有率为71质量%。β-sic的最大粒径低至10μm(即、小于15μm)。nisi2的含有率为14质量%。nisi2的最大粒径高达25μm(即、大于20μm)。比较例3中,最大粒径大于20μm的nisi2粒子偏在,认为存在许多无法利用ni促进β-sic粒子的粒生长的部位。因此,蜂窝结构体的耐氧化性降低。具体而言,比较例3中,蜂窝结构体的初始电阻率为0.05ω
·
cm,电阻变化率高达150%(即、大于100%)。
[0107]
比较例4中,省略了上述的步骤s13中的预氧化处理,除此以外,蜂窝结构体的制作条件与实施例4相同。关于蜂窝结构体的构成,没有在si粒子的表面形成氧化物被膜,除此以外,与实施例4相同。比较例4中,si的含有率及最大粒径分别为12质量%及30μm。β-sic的含有率及最大粒径分别为68质量%及33μm。nisi2的含有率及最大粒径分别为14质量%及10μm。比较例4中,蜂窝结构体的初始电阻率为0.15ω
·
cm。另外,蜂窝结构体的电阻变化率因未设置氧化物被膜而高达220%(即、大于100%)。
[0108]
如以上所说明,碳化硅质多孔体包含β-sic粒子、si粒子以及金属硅化物粒子。β-sic粒子的最大粒径为15μm以上。si粒子的含有率为10质量%以上。si粒子的最大粒径为40μm以下。另外,在si粒子的表面设置有厚度0.01μm以上且5μm以下的氧化物被膜。
[0109]
该碳化硅质多孔体中,si粒子的最大粒径粗大化为15μm以上,由此,形成导电通路的β-sic粒子彼此的粘结部变粗。另外,原料粉末中的si没有耗尽,作为si粒子,残留10质量%以上,因此,很好地形成将β-sic粒子彼此连结的si粒子的导电通路。此外,si粒子的含有率及最大粒径分别设为10质量%以上及40μm以下,由此,si粒子的分布均匀性提高,将β-sic粒子彼此连结的si粒子的导电通路大致均等地分布。据此,蜂窝结构体2的体积电阻率降低,耐氧化性提高。并且,在si粒子的表面设置有厚度0.01μm以上且5μm以下的氧化物被膜(上述例中,sio2的被膜),由此,蜂窝结构体2的耐氧化性进一步提高。因此,可以提供具有高耐氧化性的(即、在高温氧化气氛下暴露后的电阻变化率较小的)碳化硅质多孔体。
[0110]
如上所述,碳化硅质多孔体中,优选为,金属硅化物粒子的含有率为5质量%以上,该金属硅化物粒子的最大粒径为20μm以下。据此,碳化硅质多孔体中的金属硅化物粒子的分布均匀性提高。即,在制造碳化硅质多孔体时,利用构成金属硅化物粒子的金属在碳化硅质多孔体的大致整体中促进β-sic粒子的粒生长(即、粗大化)。结果,能够进一步降低碳化硅质多孔体的体积电阻率,并且,能够进一步提高碳化硅质多孔体的耐氧化性。
[0111]
如上所述,碳化硅质多孔体优选还包含al及b中的1种以上。像这样,在碳化硅质多孔体制造时,添加al及b中的1种以上作为助剂,由此能够进一步促进β-sic粒子的粒生长。
[0112]
如上所述,金属硅化物粒子优选为镍硅化物。据此,能够更好地促进碳化硅质多孔体制造时的β-sic粒子的粒生长。
[0113]
如上所述,碳化硅质多孔体的于室温的体积电阻率优选为0.01ω
·
cm以上且小于1.0ω
·
cm。像这样,碳化硅质多孔体中,能够实现非常低的体积电阻率。
[0114]
如上所述,碳化硅质多孔体中,在950℃的大气中暴露50小时后的体积电阻率的变化率优选为100%以下。据此,能够提供具有更高耐氧化性的碳化硅质多孔体。
[0115]
上述的蜂窝结构体2具备筒状外壁21和格子状的隔壁22。隔壁22将筒状外壁21的内部分隔为多个隔室23。筒状外壁21及隔壁22是包含上述的碳化硅质多孔体而构成的。据此,能够实现具有高耐氧化性的蜂窝结构体2。
[0116]
上述的电加热催化器1进行从发动机中排出的废气的净化处理。电加热催化器1具备上述的蜂窝结构体2和一对电极部41,该一对电极部41固定于蜂窝结构体2的外侧面而对蜂窝结构体2赋予电流。如上所述,蜂窝结构体2具有高耐氧化性,因此,能够利用电加热催化器1效率良好地长期进行废气的净化处理。
[0117]
上述的碳化硅质多孔体的制造方法包括:将包含si、c、及金属硅化物的原料金属的原料粉末成型并烧成而得到烧成体的工序(步骤s11~s12)、以及对该烧成体实施氧化处理而得到碳化硅质多孔体的工序(步骤s13)。该碳化硅质多孔体包含β-sic粒子、si粒子以及金属硅化物粒子。β-sic粒子的最大粒径为15μm以上。si粒子的含有率为10质量%以上。si粒子的最大粒径为40μm以下。另外,在si粒子的表面设置有厚度0.01μm以上且5μm以下的氧化物被膜。据此,如上所述,能够提供具有高耐氧化性的碳化硅质多孔体。
[0118]
如上所述,该碳化硅质多孔体的制造方法中,优选为,上述原料金属为ni,原料金属的平均粒径为5μm以下。据此,在制造碳化硅质多孔体时,该原料金属的分散均匀性提高,在碳化硅质多孔体的大致整体中,利用该原料金属来促进β-sic粒子的粒生长(即、粗大化)。结果,能够进一步降低碳化硅质多孔体的体积电阻率,并且,能够进一步提高碳化硅质多孔体的耐氧化性。
[0119]
上述的碳化硅质多孔体、蜂窝结构体2及电加热催化器1中,可以进行各种变更。
[0120]
例如,碳化硅质多孔体中的金属硅化物粒子的含有率可以小于5质量%,金属硅化物粒子的最大粒径可以大于20μm。
[0121]
另外,碳化硅质多孔体可以包含al及b这两者,也可以不含al及b。
[0122]
碳化硅质多孔体的于室温的体积电阻率可以小于0.01ω
·
cm,也可以大于1.0ω
·
cm。另外,电阻变化率(即、在950℃的大气中暴露50小时后的体积电阻率的变化率)可以大于100%,也可以小于-50%。
[0123]
上述的碳化硅质多孔体的制造方法中,作为金属硅化物的原料金属的ni的平均粒径可以大于5μm。另外,如上所述,该原料金属不限定于ni,可以为锆(zr)、铁(fe)、钛(ti)或钨(w)等。
[0124]
电加热催化器1中,蜂窝结构体2的外形不限定于大致圆柱状,可以进行各种变更。另外,电极层31及电极部41的数量及配置也可以进行各种变更。应予说明,电加热催化器1中,可以省略电极层31,将电极部41直接固定于蜂窝结构体2。
[0125]
蜂窝结构体2可以用于除了电加热催化器以外的用途(例如、陶瓷加热器)。
[0126]
上述的碳化硅质多孔体可以利用于除了蜂窝结构体2以外的结构体。例如,大致圆筒状或大致平板状等各种形状的结构体可以构成为包括该碳化硅质多孔体。
[0127]
上述实施方式及各变形例中的构成只要不相互矛盾,就可以适当组合。
[0128]
产业上的可利用性
[0129]
本发明可以利用于来自汽车等的发动机的废气的净化处理用的电加热催化器等。