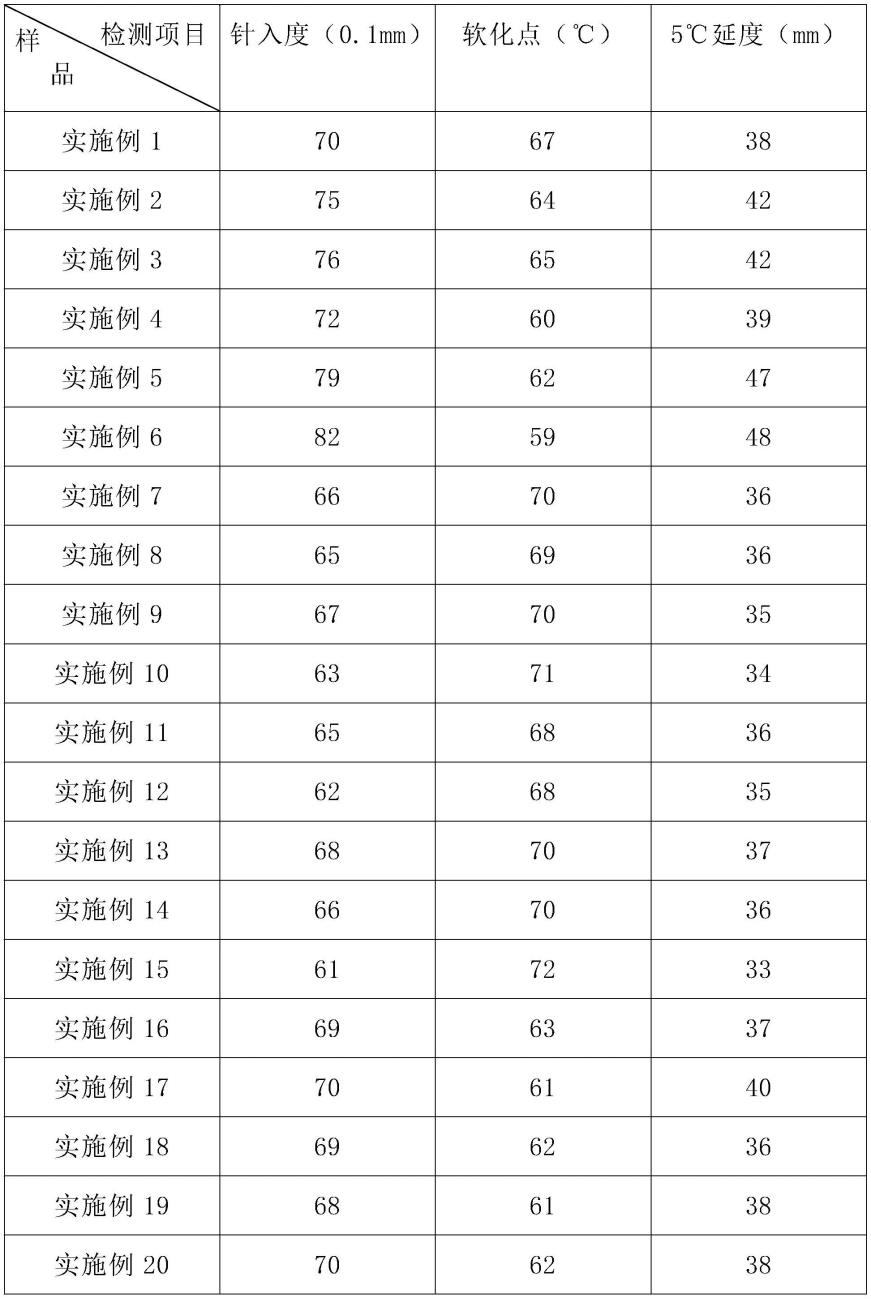
1.本技术涉及沥青技术领域,更具体地说,它涉及一种基于沥青路面旧料热再生的沥青 的生产工艺。
背景技术:2.沥青是由不同分子量的碳氢化合物及其非金属衍生物组成的黑褐色复杂混合物,是一 种防水防潮和防腐的有机胶凝材料。沥青主要可以分为煤焦沥青、石油沥青和天然沥青三种, 且沥青主要用于涂料、塑料、橡胶以及铺筑路面等。其中铺设路面的沥青因长期暴露在室外 等自然条件下,并在车辆的反复碾压下,沥青容易发生老化、破损等情况,导致沥青的使用 寿命受限,从而需要更换新的沥青维持路面的平整度和强度。
3.但是被替换的路面沥青旧料的处理是目前较大的难点,其中较为常用的处理方式是通 过再生工艺实现路面沥青旧料的再生,再生后的路面沥青旧料可以重新应用在道路铺设中; 不仅较为合理的处理了路面沥青旧料,而且也节约了沥青铺设道路的维护成本。
4.路面沥青旧料是由旧沥青和旧集料组成,对路面沥青旧料进行再生的过程中,通常需 要添加再生剂活化旧沥青,并通过新沥青与旧沥青融合,从而改善旧沥青软化点和粘度上升 而针入度和延度下降的情况。但是路面沥青旧料中的旧沥青较为牢固地包裹在旧集料上或渗 透在旧集料的空隙中,从而是的旧沥青与再生剂、新沥青的接触面积受限,进而容易影响路 面沥青旧料的再生效果。
技术实现要素:5.为了使得路面沥青旧料上的沥青料和再生剂、新沥青发生充分接触,从而提高沥青旧 料与新沥青的融合效果和路面沥青旧料的再生效果,本技术提供一种基于沥青路面旧料热再 生的沥青的生产工艺。
6.第一方面,本技术提供一种基于沥青路面旧料热再生的沥青的生产工艺,采用如下的 技术方案:一种基于沥青路面旧料热再生的沥青的生产工艺,包括以下步骤:s1:粉碎筛分沥青路面旧料,得到粉碎后的沥青路面旧料;s2:将粉碎后的沥青路面旧料浸泡在质量浓度为5%~10%的硫酸溶液中,过滤后将滤渣洗涤 烘干,得到酸化沥青路面旧料;s3:加热熔融酸化沥青路面旧料,加入再生剂搅拌,得到沥青路面热旧料;s4:在沥青路面热旧料中加入新集料、粉料、新沥青,搅拌后得到热再生沥青。
7.通过采用上述技术方案,粉碎筛分沥青路面旧料,即细化沥青路面旧料的粒径,为后 续处理工艺作准备工作。然后通过规定质量浓度的硫酸溶液浸泡处理,由于旧沥青和旧集料 之间的粘结强度在酸性的影响下会呈逐渐衰弱趋势,使得旧沥青能够在一定程度上脱离旧集 料或者与旧集料接触面积逐渐变小,为后续再生剂和新沥青活化旧沥青提供较高的接触率和 较大的接触面积,有助于提高沥青旧料与新沥青的融合效果和路面沥青旧
料的再生效果。并 且后续通过加入新集料、粉料和新沥青得到的再生沥青各方面性能符合用于铺设道路的标准。
8.本技术的生产工艺对沥青路面旧料的再生效果较好,具体是通过提高旧沥青与再生剂、 新沥青的接触率和接触面积,从而提高旧沥青的再生效果。并且本技术的生产工艺整体较为 简单,操作难度较低,在实现废弃资源再次利用的同时成本较低。
9.作为优选,所述s1步骤中,粉碎后的沥青路面旧料的粒径为10mm~20mm。
10.通过采用上述技术方案,将沥青路面旧料粉碎至粒径为10mm~20mm,便于后续硫酸 溶液浸泡,并且符合再生沥青所需骨料规格。
11.作为优选,所述s2步骤中,在硫酸溶液中加入占粉碎后沥青路面旧料0.1%~0.5%的 正庚烷,并密闭浸泡,过滤后将滤渣洗涤烘干,得到酸化沥青路面旧料。
12.通过采用上述技术方案,正庚烷有助于促进旧沥青中沥青质与其他组分相分离,便于 后续再生剂的活化处理和新沥青的融合。考虑到正庚烷具有一定的挥发性,为了保障正庚烷 对旧沥青的处理效果,浸泡环境为密闭环境,有助于提高路面沥青旧料的处理效果。
13.作为优选,所述s3步骤中,再生剂为废机油和废润滑油按照质量比1:(1~4)组成 的混合物。
14.通过采用上述技术方案,以废机油和废润滑油作为再生剂,在满足对旧沥青再生处理 的同时,由于废机油和废润滑油中含有较多的金属离子,可以与旧沥青中的活性基团发生相 互作用,从而可以有效提高活化后的旧沥青与新集料、旧集料之间的粘附效果。
15.并且废机油和废润滑油所富含的金属离子还可以有效改善沥青混合料的分散性,从而 有助于减少再生沥青铺设的道路出现裂纹的情况,并且有助于提高路面压缩、弯曲和抗疲劳 强度,进而延长沥青道路的使用寿命。
16.另外,废机油和废润滑油均为废弃资源,应用至沥青路面旧料的再生工艺中,契合废 物利用的绿色环保理念。
17.作为优选,所述s3步骤中,在加热熔融酸化沥青路面旧料之前,先将酸化沥青路面 旧料浸泡在含铬外加剂中,过滤后将滤渣洗涤烘干,得到改性沥青路面旧料。
18.通过采用上述技术方案,由于酸化沥青路面旧料中的旧集料与旧沥青、新沥青的粘附 效果会因酸性处理有一定程度的下降趋势,而利用含铬外加剂处理酸化沥青路面旧料,改变 旧集料的表面,使得旧集料与新沥青、旧沥青的界面粘结状态趋向于更为稳定的状态,能够 较好地克服上述缺陷,使得后续旧集料与旧沥青、新沥青的粘附性能得到改善。
19.作为优选,所述s4步骤中,粉料为碱渣和碱性高炉矿渣的按照质量比(3~6):1组 成的混合物。
20.通过采用上述技术方案,添加粉料可以改善再生沥青的强度及用于铺设路面后的平整 度。同时碱渣和碱性高炉矿渣均能够提供一定的碱性环境,在与沥青路面热旧料共混的过程 中,对体系的酸性具有一定的中和效果,从而可以减弱因前期酸化处理所引起的旧集料与旧 沥青、新沥青粘附性变差的情况,即有助于提高旧集料与新沥青、旧沥青的粘附效果。
21.另外,碱渣和碱性高炉矿渣均属于工业废料,与本技术中废物利用的理念相契合。
22.作为优选,所述碱渣和碱性高炉矿渣的粒径为1~5mm。
23.作为优选,所述s4步骤中,在沥青路面热旧料中加入新集料、粉料、新沥青和温拌 剂,搅拌后得到热再生沥青。
24.通过采用上述技术方案,温拌剂的加入可以有效降低再生沥青在铺设及碾压时的温度, 从而可以减少因温度较高而导致再生沥青老化速率变快的情况,并且节约能源的同时还可以 减少高温下有害气体的析出。
25.作为优选,所述温拌剂为xt-w1、xt-w2和xt-w3按照质量比1:(2~4):1组成的 混合物。
26.通过采用上述技术方案,xt-w1是一种液体温拌剂,t-w2是一种固体温拌剂,xt-w3 是一种含结晶水的粉状固体,三种不同形态的温拌剂相配合,对体系的适应性更好。同时 xt-w1和xt-w3均属于表面活性型温拌剂,对再生沥青的稳定性有较好的改善效果,而 xt-w2对再生沥青的针入度、软化点和黏度具有较为明显的改善效果,因此xt-w1、xt-w2 和xt-w3按照上述质量比复配使用,在降低再生沥青使用过程中温度的同时对再生沥青其他 性能具有良好的改善效果。
27.第二方面,本技术提供一种基于沥青路面旧料热再生的沥青,采用如下的技术方案: 一种基于沥青路面旧料热再生的沥青,由上述生产工艺制得。
28.综上所述,本技术具有以下有益效果:1、本技术通过对沥青路面旧料进行酸化处理,促进沥青路面旧料中的旧集料与旧沥青相脱离 或缩小旧集料与旧沥青的接触面积,从而提高后续再生剂、新沥青与旧沥青的接触率和接触 面积,进而有助于提高再生剂对旧沥青的再生效果以及新沥青的融合效果。
29.2、本技术通过正庚烷对酸化处理后的沥青路面旧料进一步处理,有助于促进旧沥青中 的沥青质与其他组分相分离,便于后续再生剂的活化处理和新沥青的融合。
30.3、本技术以废机油和废润滑油作为再生剂,在满足再生效果的同时,两者所含有的金 属离子可以有效改善活化后的旧沥青与新集料、旧集料之间的粘附效果;并且废机油和废润 滑油均属于废弃资源,契合本技术废物利用的绿色环保理念。
31.4、本技术进一步选用碱渣和碱性高炉矿渣作为粉料,在填充和细集料作用的基础上, 其具备的碱性特性可以有效中和因酸处理而存在的酸性,有助于减少旧集料与旧沥青、新沥 青之间粘附性能下降的情况。
具体实施方式
32.以下结合实施例和对比例对本技术作进一步详细说明,本技术涉及的原料均可通过市 售获得;其中xt-w1、xt-w2和xt-w3均产自常州信拓路面改性材料有限公司。实施例
33.实施例1一种基于沥青路面旧料热再生的沥青的生产工艺,包括以下步骤:s1:粉碎筛分沥青路面旧料,控制其粒径为10mm~20mm,得到粉碎后的沥青路面旧料;s2:将100kg粉碎后的沥青路面旧料浸泡在质量浓度为5%的硫酸溶液中,硫酸溶液没过粉碎 后的沥青路面旧料,浸泡时间为1h,过滤后用清水反复洗涤滤渣3次,在70℃的
温度下烘干 滤渣,得到酸化沥青路面旧料;s3:150℃的温度下加热熔融酸化沥青路面旧料5min,待其冷却至100℃后加入0.5kg再生剂 搅拌,得到沥青路面热旧料;s4:在沥青路面热旧料中加入70kg新集料、10kg粉料、10kg新沥青,搅拌1min后得到热再 生沥青;其中再生剂为废机油和废润滑油按照质量比1:3组成的混合物;新集料为石料,且粒径为20~30mm;粉料为碱渣和碱性高炉矿渣按照质量比4:1组成的混合物,且粒径为1~5mm。
34.实施例2一种基于沥青路面旧料热再生的沥青的生产工艺,包括以下步骤:s1:粉碎筛分沥青路面旧料,控制其粒径为10mm~20mm,得到粉碎后的沥青路面旧料;s2:将100kg粉碎后的沥青路面旧料浸泡在质量浓度为5%的硫酸溶液中,硫酸溶液没过粉碎 后的沥青路面旧料,并在硫酸溶液中加入0.2kg正庚烷,密闭浸泡1h,过滤后用清水反复洗 涤滤渣3次,在70℃的温度下烘干滤渣,得到酸化沥青路面旧料;s3:150℃的温度下加热熔融酸化沥青路面旧料5min,待其冷却至100℃后加入0.5kg再生剂 搅拌,得到沥青路面热旧料;s4:在沥青路面热旧料中加入70kg新集料、10kg粉料、10kg新沥青,搅拌1min后得到热再 生沥青;其中再生剂为废机油和废润滑油按照质量比1:3组成的混合物;新集料为石料,且粒径为20~30mm;粉料为碱渣和碱性高炉矿渣按照质量比4:1组成的混合物,且粒径为1~5mm。
35.实施例3一种基于沥青路面旧料热再生的沥青的生产工艺,包括以下步骤:s1:粉碎筛分沥青路面旧料,控制其粒径为10mm~20mm,得到粉碎后的沥青路面旧料;s2:将100kg粉碎后的沥青路面旧料浸泡在质量浓度为5%的硫酸溶液中,硫酸溶液没过粉碎 后的沥青路面旧料,浸泡时间为1h,过滤后用清水反复洗涤滤渣3次,在70℃的温度下烘干 滤渣,得到酸化沥青路面旧料;s3:先将酸化沥青路面旧料浸泡在含铬外加剂中,过滤后用清水反复洗涤3次,在70℃的温 度下烘干滤渣,得到改性沥青路面旧料;150℃的温度下加热熔融改性沥青路面旧料5min, 待其冷却至100℃后加入0.5kg再生剂搅拌,得到沥青路面热旧料;s4:在沥青路面热旧料中加入70kg新集料、10kg粉料、10kg新沥青,搅拌1min后得到热再 生沥青;其中再生剂为废机油和废润滑油按照质量比1:3组成的混合物;新集料为石料,且粒径为20~30mm;粉料为碱渣和碱性高炉矿渣按照质量比4:1组成的混合物,且粒径为1~5mm;含铬外加剂的铬浓度为46mg/l,且可选用电镀废水作为含铬外加剂。
36.实施例4
一种基于沥青路面旧料热再生的沥青的生产工艺,包括以下步骤:s1:粉碎筛分沥青路面旧料,控制其粒径为10mm~20mm,得到粉碎后的沥青路面旧料;s2:将100kg粉碎后的沥青路面旧料浸泡在质量浓度为5%的硫酸溶液中,硫酸溶液没过粉碎 后的沥青路面旧料,浸泡时间为1h,过滤后用清水反复洗涤滤渣3次,在70℃的温度下烘干 滤渣,得到酸化沥青路面旧料;s3:150℃的温度下加热熔融酸化沥青路面旧料5min,待其冷却至100℃后加入0.5kg再生剂 搅拌,得到沥青路面热旧料;s4:在沥青路面热旧料中加入70kg新集料、10kg粉料、10kg新沥青、温拌剂1kg,搅拌1min 后得到热再生沥青;其中再生剂为废机油和废润滑油按照质量比1:3组成的混合物;新集料为石料,且粒径为20~30mm;粉料为碱渣和碱性高炉矿渣按照质量比4:1组成的混合物,且粒径为1~5mm;温拌剂为xt-w1、xt-w2和xt-w3按照质量比1:2:1组成的混合物。
37.实施例5一种基于沥青路面旧料热再生的沥青的生产工艺,包括以下步骤:s1:粉碎筛分沥青路面旧料,控制其粒径为10mm~20mm,得到粉碎后的沥青路面旧料;s2:将100kg粉碎后的沥青路面旧料浸泡在质量浓度为5%的硫酸溶液中,硫酸溶液没过粉碎 后的沥青路面旧料,并在硫酸溶液中加入0.2kg正庚烷,密闭浸泡1h,过滤后用清水反复洗 涤滤渣3次,在70℃的温度下烘干滤渣,得到酸化沥青路面旧料;s3:先将酸化沥青路面旧料浸泡在含铬外加剂中,过滤后用清水反复洗涤3次,在70℃的温 度下烘干滤渣,得到改性沥青路面旧料;150℃的温度下加热熔融改性沥青路面旧料5min, 待其冷却至100℃后加入0.5kg再生剂搅拌,得到沥青路面热旧料;s4:在沥青路面热旧料中加入70kg新集料、10kg粉料、10kg新沥青,搅拌1min后得到热再 生沥青;其中再生剂为废机油和废润滑油按照质量比1:3组成的混合物;新集料为石料,且粒径为20~30mm;粉料为碱渣和碱性高炉矿渣按照质量比4:1组成的混合物,且粒径为1~5mm;含铬外加剂的铬浓度为46mg/l,且可选用电镀废水作为含铬外加剂。
38.实施例6一种基于沥青路面旧料热再生的沥青的生产工艺,包括以下步骤:s1:粉碎筛分沥青路面旧料,控制其粒径为10mm~20mm,得到粉碎后的沥青路面旧料;s2:将100kg粉碎后的沥青路面旧料浸泡在质量浓度为5%的硫酸溶液中,硫酸溶液没过粉碎 后的沥青路面旧料,并在硫酸溶液中加入0.2kg正庚烷,密闭浸泡1h,过滤后用清水反复洗 涤滤渣3次,在70℃的温度下烘干滤渣,得到酸化沥青路面旧料;s3:先将酸化沥青路面旧料浸泡在含铬外加剂中,过滤后用清水反复洗涤3次,在70℃的温 度下烘干滤渣,得到改性沥青路面旧料;150℃的温度下加热熔融改性沥青路面
旧料5min, 待其冷却至100℃后加入0.5kg再生剂搅拌,得到沥青路面热旧料;s4:在沥青路面热旧料中加入70kg新集料、10kg粉料、10kg新沥青、温拌剂1kg,搅拌1min 后得到热再生沥青;其中再生剂为废机油和废润滑油按照质量比1:3组成的混合物;新集料为石料,且粒径为20~30mm;粉料为碱渣和碱性高炉矿渣按照质量比4:1组成的混合物,且粒径为1~5mm;含铬外加剂的铬浓度为46mg/l,且可选用电镀废水作为含铬外加剂;温拌剂为xt-w1、xt-w2和xt-w3按照质量比1:2:1组成的混合物。
39.实施例7本实施例与实施例1的区别之处在于,沥青路面旧料粉碎后的粒径为30~50mm。
40.实施例8本实施例与实施例1的区别之处在于,再生剂为废机油和废润滑油按照质量比1:1组成的混 合物。
41.实施例9本实施例与实施例1的区别之处在于,再生剂为废机油和废润滑油按照质量比4:1组成的混 合物。
42.实施例10本实施例与实施例1的区别之处在于,再生剂为废机油。
43.实施例11本实施例与实施例1的区别之处在于,再生剂为废润滑油。
44.实施例12本实施例与实施例1的区别之处在于,再生剂为厨余废弃油。
45.实施例13本实施例与实施例1的区别之处在于,粉料为碱渣。
46.实施例14本实施例与实施例1的区别之处在于,粉料为碱性高炉矿渣。
47.实施例15本实施例与实施例1的区别之处在于,粉料为石粉。
48.实施例16本实施例与实施例4的区别之处在于,温拌剂为xt-w1。
49.实施例17本实施例与实施例4的区别之处在于,温拌剂为xt-w2。
50.实施例18本实施例与实施例4的区别之处在于,温拌剂为xt-w3。
51.实施例19本实施例与实施例4的区别之处在于,温拌剂为xt-w1和xt-w3按照质量比1:1组成的混 合物。
52.实施例20本实施例与实施例4的区别之处在于,温拌剂为xt-w1、xt-w2和xt-w3按照质量比
2:1:2 组成的混合物。
53.对比例对比例1一种再生沥青的生产工艺,包括以下步骤:a1:将收集的旧沥青路面料粉碎、筛分,控制粒径为10mm以下;a2:140℃的温度下加热熔融粉碎后的旧沥青路面料50kg,5min后得到熔融旧沥青;a3:向熔融后的旧沥青中再生剂0.05kg,搅拌后加入粒径为10~20mm的新石料50kg、新 沥青3kg、新石粉2.5kg,继续搅拌30s得沥青热再生成品料;其中再生剂为石油重油和厨余废弃油按照质量比1:1组成的混合物。
54.性能检测试验方法 针入度:参照gb/t4509-2010《沥青针入度测定法》测定实施例1~20和对比例1中的热再 生沥青的针入度。
55.软化点:参照gb/t4507-2014《沥青软化点测定法》测定实施例1~20和对比例1中 的热再生沥青的软化点。
56.延度:参照gb/t4508-2010《沥青延度测定法》测定实施例1~20和对比例1中的热 再生沥青的延度。
57.表1检测数据表
通过表1的检测数据,并结合实施例1和对比例1的检测结果来看,利用硫酸溶液对
粉碎后 的沥青路面旧料进行酸化处理,促进旧沥青和旧集料相分离,可以使得旧沥青与再生剂、新 沥青的接触率更高,接触面积更大,从而有助于提高热再生沥青的性能。
58.结合实施例1和实施例2的检测结果来看,在实施例1的基础上进一步利用正庚烷处 理沥青路面旧料,有助于促进沥青质与其他组分分离,更有利于沥青路面旧料的再生效果。
59.结合实施例1和实施例3的检测结果来看,在实施例1的基础上进一步利用含铬外加 剂处理沥青路面旧料,对由于酸化沥青路面旧料中的旧集料与旧沥青、新沥青的粘附效果因 酸性处理有一定程度的下降趋势的情况有所改善。
60.结合实施例1和实施例4的检测结果来看,在实施例1的基础上加入温拌剂可以降低 热再生沥青的软化点,从而可以减少因热再生沥青加热温度较高而导致加速老化和有害气体 的析出,并且温拌剂对热再生沥青的针入度和延度也有一定程度的改善效果。
61.结合实施例1和实施例5~6的检测结果来看,正庚烷处理、含铬外加剂处理和添加 温拌剂的进一步优化措施之间可以同时进行,即各优化措施之间无明显排斥现象,且组合使 用的效果更好。
62.结合实施例1和实施例15的检测结果来看,碱渣和碱性高炉矿渣具有的碱性对沥青 路面旧料酸化后所具有的酸性具有较好的中和效果,且对提高热再生沥青的综合性能具有积 极意义。
63.本具体实施例仅仅是对本技术的解释,其并不是对本技术的限制,本领域技术人员在 阅读完本说明书后可以根据需要对本实施例做出没有创造性贡献的修改,但只要在本技术的 权利要求范围内都受到专利法的保护。