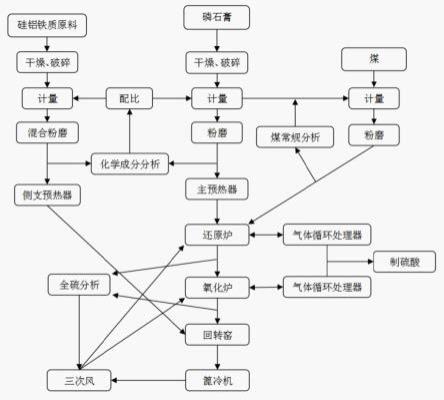
1.本发明属于建筑材料技术领域,具体涉及一种磷石膏分解联产水泥工艺。
背景技术:2.磷石膏是湿法磷酸工艺中产生的固体废弃物,磷石膏的组成比较复杂,除水合硫酸钙以外,还有未完全分解的磷矿、残余的磷酸、氟化物、酸不溶物、有机质等,其中氟和有机质的存在对磷石膏的资源化利用影响最大,堆放会占用大量土地,并会对水资源和土地资源造成污染。据中国磷肥工业协会统计,2020年磷石膏年排放总量约7500-8000万吨,虽有很多行业尝试使用磷石膏,但利用率低,国内堆存量已达6亿多吨,世界达60亿多吨,磷石膏的资源化利用是世界性难题。
3.水泥行业是世界上最大的二氧化碳排放源之一,占全球排放量的5-8%,其中,60%来源于石灰石的煅烧。磷石膏代替石灰石作为cao源生产水泥熟料是解决磷石膏资源化利用的一个具有挑战和意义的方向,可以使磷石膏的利用率达到90%以上,并且可以避免石灰石在水泥生产中的二氧化碳排放问题。
4.caso4相对于caco3而言,需要在更高的温度下才能分解,为了让磷石膏适应水泥生产的要求,降低在工艺上的操作难度和能源损耗,磷石膏需要在较低的温度下完成分解并脱硫。已有较多文献报道采用碳质原料、一氧化碳气氛、单质硫等对磷石膏进行分解的研究,虽然在1000-1100℃的低温环境下磷石膏分解率可以达到99%以上,但要使脱硫率达到95%以上则较难实现,需要对气氛进行稳定、精准调控,这无疑会增加实际生产过程中的难度,若脱硫率达不到此要求,则在熟料烧成阶段硫会以caso4、cas或固溶物的形式存在,对于以磷石膏为主要cao源生产水泥熟料的体系而言,一方面使得cao不足,另一方面caso4、cas等含硫物质高温时脱硫会产生较多的so3影响窑内气氛,最终严重影响c3s的形成,还会对熟料的生产和应用带来诸多不利影响。
5.目前我国建成投产的磷石膏制硫酸联产水泥工厂,主要方法为磷石膏经干燥脱水,与焦炭、粘土、砂页岩等按熟料进行配比,在中空回转窑内煅烧制得熟料,窑气中的so2经转化、吸收后制得硫酸,采用此方法的能耗高、成本高,磷石膏的分解脱硫以及熟料的煅烧均在窑内进行。因为caso4在900-1100℃的低温还原气氛下更容易被还原分解为cas,因而caso4难以一次性实现高分解率和高脱硫率,本领域技术人员为了保证磷石膏的高分解率会导致其在窑尾的低温还原气氛段的脱硫率进一步降低,难以达到90%,从而让剩余的大部分caso4、cas在窑中间的高温段发生一系列反应而脱硫,最终制得的熟料中c3s含量达不到30%,使熟料的颜色偏浅且强度偏低,还因cas在熟料高温烧成时脱硫以及少量存在于熟料中而使制得的熟料释放出h2s的臭鸡蛋有毒气体,危害人体健康,因此难以得到推广和应用。
技术实现要素:6.本发明目的在于提供一种磷石膏分解联产水泥工艺,对磷石膏分两步完全脱硫处
理,应用于水泥熟料的制备中利用率达到90%以上。
7.为达到上述目的,采用技术方案如下:
8.一种磷石膏分解联产水泥工艺,包括以下步骤:
9.(1)获取磷石膏,经干燥、破碎、粉磨后经预热器进入还原炉进行caso4的分解;
10.(2)经过还原分解的粉料进入氧化炉将剩余的cas氧化;
11.(3)按照硅酸盐水泥熟料进行配比计量的硅铝铁质原料经过混合粉磨后进入侧支预热器,与磷石膏的分解产物一起进入回转窑进行熟料的煅烧。
12.按上述方案,步骤3中所述硅铝铁质原料为砂页岩、煤矸石、粘土、粉煤灰中的一种或多种;所述磷石膏化学成分中的so3算入自身的烧失量中,剩余化学成分对应于以cao为主的物质进行计量。
13.按上述方案,步骤1中还原炉通过加入煤质原料以及通入三次风创造还原气氛,控制还原炉内co的体积浓度为2%-6%;温度保持在900-1000℃。
14.按上述方案,所述煤质原料为水泥生产普通用煤或高硫煤,其中c与磷石膏中so3的摩尔比为0.6-1.0。
15.按上述方案,所述三次风的通入速度和气体量通过还原炉出口处粉料的全硫分析检测结果进行调整,以全硫含量越小越好。
16.按上述方案,步骤2中氧化炉通过通入三次风创造氧化气氛,控制氧化炉内o2的体积浓度为2%-10%;温度保持在1000-1100℃。
17.按上述方案,所述三次风的通入速度和气体量通过氧化炉出口处粉料的全硫分析检测结果进行调整,以全硫含量越小越好。
18.按上述方案,所得熟料矿物组成中c3s为25%-65%,c2s为10%-50%,c3a为2%-10%,c4af为5%-15%。
19.相对于现有技术,本发明有益效果如下:
20.采用本发明的方法,将磷石膏的分解和脱硫分别放入还原炉和氧化炉中进行,使得磷石膏在还原炉中达到较高的分解率,然后在氧化炉中将剩余的cas在弱氧化气氛中朝着cao的方向转化而非caso4,两步之后脱硫更彻底,避免了cas、caso4对后端回转窑内熟料煅烧的不利影响,且通过使用三次风的气体循环系统控制了气氛条件并节约了能源。还原炉中的还原气氛通过三次风热空气与煤质原料控制,氧化炉中的弱氧化气氛通过三次风热空气与窑内燃烧后送入氧化炉的无氧气体控制。
21.可以有效利用磷石膏,使其利用率达到90%以上,无需使用天然石灰石,按照日产5000吨熟料的水泥生产线计算,每年可处理400万吨磷石膏,并可每年减少碳排放100万吨。
附图说明
22.图1:本发明磷石膏分解联产水泥工艺的流程图。
23.图2:实施例1、2、3、4制得熟料的xrd图谱。
具体实施方式
24.以下实施例进一步阐释本发明的技术方案,但不作为对本发明保护范围的限制。
25.具体实施方式中提供了一种磷石膏分解联产水泥工艺,参照附图1所示:
26.(1)获取磷石膏,经干燥、破碎、粉磨后经预热器进入还原炉进行caso4的分解;还原炉通过加入煤质原料以及通入三次风创造还原气氛;温度保持在900-1000℃;所述煤质原料为水泥生产普通用煤或高硫煤,其中c与磷石膏中so3的摩尔比为0.6-1.0;所述三次风的通入速度和气体量通过还原炉出口处粉料的全硫分析检测结果进行调整,以全硫含量越小越好,控制还原炉内co的体积浓度为2%-6%。
27.(2)经过还原分解的粉料进入氧化炉将剩余的cas氧化;氧化炉通过通入三次风创造氧化气氛;温度保持在1000-1100℃;所述三次风的通入速度和气体量通过氧化炉出口处粉料的全硫分析检测结果进行调整,以全硫含量越小越好,控制氧化炉内o2的体积浓度为2%-10%。
28.(3)按照硅酸盐水泥熟料进行配比计量的硅铝铁质原料经过混合粉磨后进入侧支预热器,与磷石膏的分解产物一起进入回转窑进行熟料的煅烧;所得的熟料矿物组成中c3s为25%-65%,c2s为10%-50%,c3a为2%-10%,c4af为5%-15%。
29.具体实施方式中,所述硅铝铁质原料为砂页岩、煤矸石、粘土、粉煤灰等常用原料中的一种或多种;所述磷石膏化学成分中的so3算入自身的烧失量中,剩余化学成分对应于以cao为主的物质进行计量。获取磷石膏和硅铝铁质辅料,经干燥、破碎、粉磨后进行化学成分分析,具体实施方式中磷石膏、铁矿土、粉煤灰、煤矸石的化学成分如表1所示:
30.表1化学成分分析
31.名称烧失量sio2al2o3fe2o3caomgoso3k2ona2o磷石膏20.046.040.300.2829.750.0242.280.220.12铁矿土3.2748.915.5515.97.564.410.010.782.79粉煤灰5.3343.4132.886.446.720.71.20.810.47煤矸石4.6376.36.624.641.912.350.481.340.55
32.实施例1
33.1、配比设计
34.将磷石膏化学成分中的so3算入自身的烧失量中,按照烧失量20.04%+42.28%=62.32%,剩余化学成分对应于以cao为主的物质进行计量,类似于石灰石使用,然后与铁矿土按照硅酸盐水泥熟料进行设计配比,配比如表2所示,采用重量比磷石膏:铁矿土为91:9,理论矿物组成如表3所示:
35.表2配比
36.名称烧失量sio2al2o3fe2o3caomgoso3k2ona2o配比磷石膏62.326.040.300.2829.750.0200.220.1291铁矿土3.2748.915.5515.97.564.410.010.782.799
37.表3理论矿物组成
38.khsmimc3sc2sc3ac4af0.882.951.0052.4522.093.4211.14
39.2、磷石膏的还原分解与氧化
40.将配比计量的磷石膏粉料经预热器进入还原炉进行caso4的分解,还原炉通过加入煤质原料以及通入三次风创造还原气氛,此处加入高硫煤,其常规分析结果如表4所示:
41.表4高硫煤常规分析
42.名称水分灰分挥发分固定碳含量全硫qnet,adqnet,d高硫煤1.4223.4810.2564.852.9925.2526.33
43.此处设计固定碳含量与磷石膏中so3的摩尔比为0.8,那么配比中重量为91的磷石膏所需加入高硫煤的重量为(91*0.4228/80)*0.8*12/0.6485=7.12。
44.还原炉温度设定为950℃,出口处粉料的全硫分析测得so3含量为7.7%。然后将经过还原分解的粉料进入氧化炉将剩余的cas氧化,氧化炉通过通入三次风创造氧化气氛,氧化炉温度设定为1050℃,出口处粉料的全硫分析测得so3含量为2.5%。
45.这里需要说明的是,还原炉和氧化炉中通入三次风的速度或气体量,其受到工艺和设备的共同影响,要使其达到适宜的气氛条件,需要通过炉出口处粉料的全硫分析检测结果进行评价和调整,以全硫含量越小越好,本例中控制还原炉内co的体积浓度为4%,控制氧化炉内o2的体积浓度为5%。
46.3、熟料煅烧
47.经过还原分解和氧化后的磷石膏直接由窑尾进入回转窑,同时,铁矿土单独从另一支向也由窑尾进入回转窑,此时经过还原分解和氧化后的磷石膏和铁矿土在回转窑中制得熟料。
48.实施例2
49.1、配比设计
50.将磷石膏化学成分中的so3算入自身的烧失量中,按照烧失量20.04%+42.28%=62.32%,剩余化学成分对应于以cao为主的物质进行计量,类似于石灰石使用,然后与粉煤灰和铁矿土按照硅酸盐水泥熟料进行设计配比,配比如表5所示,采用重量比磷石膏:粉煤灰:铁矿土为92:3:5,理论矿物组成如表6所示:
51.表5配比
52.名称烧失量sio2al2o3fe2o3caomgoso3k2ona2o配比磷石膏62.326.040.300.2829.750.0200.220.1292粉煤灰5.3343.4132.886.446.720.71.20.810.473铁矿土3.2748.915.5515.97.564.410.010.782.795
53.表6理论矿物组成
54.khsmimc3sc2sc3ac4af0.9262.8321.63760.5813.057.258.34
55.2、磷石膏的还原分解与氧化
56.将配比计量的磷石膏粉料经预热器进入还原炉进行caso4的分解,还原炉通过加入煤质原料以及通入三次风创造还原气氛,此处加入高硫煤,其常规分析结果如表7所示:
57.表7高硫煤常规分析
58.名称水分灰分挥发分固定碳含量全硫qnet,adqnet,d高硫煤1.4223.4810.2564.852.9925.2526.33
59.此处设计固定碳含量与磷石膏中so3的摩尔比为0.8,那么配比中重量为92的磷石膏所需加入高硫煤的重量为(92*0.4228/80)*0.8*12/0.6485=7.20。
60.还原炉温度设定为960℃,出口处粉料的全硫分析测得so3含量为8.3%。然后将经过还原分解的粉料进入氧化炉将剩余的cas氧化,氧化炉通过通入三次风创造氧化气氛,氧化炉温度设定为1060℃,出口处粉料的全硫分析测得so3含量为3.2%。
61.这里需要说明的是,还原炉和氧化炉中通入三次风的速度或气体量,其受到工艺和设备的共同影响,要使其达到适宜的气氛条件,需要通过炉出口处粉料的全硫分析检测结果进行评价和调整,以全硫含量越小越好,本例中控制还原炉内co的体积浓度为6%,控制氧化炉内o2的体积浓度为5%。
62.3、熟料煅烧
63.经过还原分解和氧化后的磷石膏直接由窑尾进入回转窑,同时,粉煤灰和铁矿土单独从另一支向也由窑尾进入回转窑,此时经过还原分解和氧化后的磷石膏与粉煤灰和铁矿土在回转窑中制得熟料。
64.实施例3
65.1、配比设计
66.将磷石膏化学成分中的so3算入自身的烧失量中,按照烧失量20.04%+42.28%=62.32%,剩余化学成分对应于以cao为主的物质进行计量,类似于石灰石使用,然后与粉煤灰和铁矿土按照硅酸盐水泥熟料进行设计配比,配比如表8所示,采用重量比磷石膏:粉煤灰:铁矿土为91:4:5,理论矿物组成如表9所示:
67.表8配比
68.名称烧失量sio2al2o3fe2o3caomgoso3k2ona2o配比磷石膏62.326.040.300.2829.750.0200.220.1291粉煤灰5.3343.4132.886.446.720.71.20.810.474铁矿土3.2748.915.5515.97.564.410.010.782.795
69.表9理论矿物组成
70.khsmimc3sc2sc3ac4af0.8612.6351.80946.6225.238.828.65
71.2、磷石膏的还原分解与氧化
72.将配比计量的磷石膏粉料经预热器进入还原炉进行caso4的分解,还原炉通过加入煤质原料以及通入三次风创造还原气氛,此处加入高硫煤,其常规分析结果如表10所示:
73.表10高硫煤常规分析
[0074][0075]
此处设计固定碳含量与磷石膏中so3的摩尔比为0.7,那么配比中重量为91的磷石膏所需加入高硫煤的重量为(91*0.4228/80)*0.7*12/0.6485=6.23。
[0076]
还原炉温度设定为950℃,出口处粉料的全硫分析测得so3含量为6.8%。然后将经过还原分解的粉料进入氧化炉将剩余的cas氧化,氧化炉通过通入三次风创造氧化气氛。氧化炉温度设定为1060℃,出口处粉料的全硫分析测得so3含量为2.4%。
[0077]
这里需要说明的是,还原炉和氧化炉中通入三次风的速度或气体量,其受到工艺和设备的共同影响,要使其达到适宜的气氛条件,需要通过炉出口处粉料的全硫分析检测结果进行评价和调整,以全硫含量越小越好,本例中控制还原炉内co的体积浓度为3%,控制氧化炉内o2的体积浓度为6%。
[0078]
3、熟料煅烧
[0079]
经过还原分解和氧化后的磷石膏直接由窑尾进入回转窑,同时,粉煤灰和铁矿土单独从另一支向也由窑尾进入回转窑,此时经过还原分解和氧化后的磷石膏与粉煤灰和铁矿土在回转窑中制得熟料。
[0080]
实施例4
[0081]
1、配比设计
[0082]
将磷石膏化学成分中的so3算入自身的烧失量中,按照烧失量20.04%+42.28%=62.32%,剩余化学成分对应于以cao为主的物质进行计量,类似于石灰石使用,然后与铁矿土和煤矸石按照低热硅酸盐水泥熟料进行设计配比,配比如表11所示,采用重量比磷石膏:铁矿土:煤矸石为90:8:2,理论矿物组成如表12所示:
[0083]
表11配比
[0084]
名称烧失量sio2al2o3fe2o3caomgoso3k2ona2o配比磷石膏62.326.040.300.2829.750.0200.220.1290铁矿土3.2748.915.5515.97.564.410.010.782.798煤矸石4.6376.36.624.641.912.350.481.340.552
[0085]
表12理论矿物组成
[0086]
khsmimc3sc2sc3ac4af0.7923.3321.01833.5041.703.4810.56
[0087]
2、磷石膏的还原分解与氧化
[0088]
将配比计量的磷石膏粉料经预热器进入还原炉进行caso4的分解,还原炉通过加入煤质原料以及通入三次风创造还原气氛,此处加入煤粉,其常规分析结果如表13所示:
[0089]
表13煤粉常规分析
[0090]
名称水分灰分挥发分固定碳含量全硫qnet,adqnet,d煤粉3.2315.1432.3049.330.9725.5127.43
[0091]
此处设计固定碳含量与磷石膏中so3的摩尔比为0.6,那么配比中重量为90的磷石膏所需加入煤粉的重量为(90*0.4228/80)*0.6*12/0.4933=6.94。
[0092]
还原炉温度设定为960℃,出口处粉料的全硫分析测得so3含量为7.5%。然后将经过还原分解的粉料进入氧化炉将剩余的cas氧化,氧化炉通过通入三次风创造氧化气氛,氧化炉温度设定为1040℃,出口处粉料的全硫分析测得so3含量为2.3%。
[0093]
这里需要说明的是,还原炉和氧化炉中通入三次风的速度或气体量,其受到工艺和设备的共同影响,要使其达到适宜的气氛条件,需要通过炉出口处粉料的全硫分析检测结果进行评价和调整,以全硫含量越小越好,本例中控制还原炉内co的体积浓度为3%,控制氧化炉内o2的体积浓度为8%。
[0094]
3、熟料煅烧
[0095]
经过还原分解和氧化后的磷石膏直接由窑尾进入回转窑,同时,铁矿土和煤矸石单独从另一支向也由窑尾进入回转窑,此时经过还原分解和氧化后的磷石膏与铁矿土和煤矸石在回转窑中制得熟料。
[0096]
实施例1、2、3、4制得熟料的xrd图谱如图所示,各熟料矿物均形成良好。
[0097]
上述实施方式仅为本发明的优选实施方式,不能以此来限定本发明保护的范围,本领域的技术人员在本发明的基础上所做的任何非实质性的变化及替换均属于本发明所要求保护的范围。