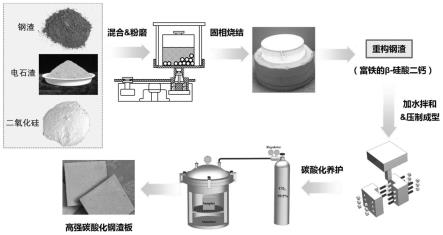
1.本发明涉及建筑材料技术领域,特别涉及高强碳酸化钢渣板的制备方法。
背景技术:2.炼钢过程会产生大量冶金渣,而综合资源化利用率只有30%左右。钢渣的综合利用率不足已经成为限制钢铁行业健康发展的关键问题。钢渣含有多种碱性矿物及重金属元素,其大量堆存会造成地下水污染。当以钢渣为原料制备建筑材料时,其含有会引起安定性不良的膨胀组分(游离氧化钙/氧化镁,f-cao/f-mgo),直接利用会引发混凝土的严重质量问题。钢渣是一种弱胶凝活性材料,早期强度低,凝结时间长。钢渣利用的关键是改善其安定性,提高反应活性及环境友好性。
3.矿物碳酸化是解决钢渣资源化利用的有效方法。利用碳酸化可有效提高钢渣安定性;碳酸化养护2h之后,游离cao和mgo的含量分别从4.21%、1.12%降低到0.60%、0.36%。降低钢渣渗滤液ph并限制一些微量元素浸出,改善其对环境质量的不利影响;数小时内显著提升制品强度;按年产钢渣1.25亿吨,1kg 钢渣可固定178g co2(72h养护,前期实验结果)计算,每年通过矿物碳酸化处理钢渣可固定0.22亿吨co2。因此,矿物碳酸化制备建材制品具有巨大的固碳潜力,在co2高效固定、固体废弃物资源化利用等方面具有诸多显著经济环境效益。
4.现有的钢渣碳酸化技术中,钢渣碳酸化增重率(即固定co2的能力)约为 9.48%,远低于钢渣碳酸化增重率的理论值37%。钢渣碳酸化制品抗压强度约为 20-40mpa,而其抗压强度取决于钢渣的矿物组成以及碳酸化工艺。因此如何进一步提升钢渣的碳酸化增重率与固碳能力,提升钢渣碳酸化制品的强度使其适用于更广泛的领域是本领域人员研究的热点。此外,将碳酸化后的钢渣用于制备碳化砖等建筑材料,例如中国授权专利cn111875332b提供的一种湿磨电石渣制备碳化砖的方法,该方法使用电石渣、石膏、矿渣和细骨料加水搅拌成砂浆,在压制成型,最后放入碳化室中,co2环境中恒温恒湿碳化养护,然而这种以矿渣或钢渣为原料的碳化砖,对co2的吸附固定能力有限,制备的碳化砖的力学强度也亟待进一步提高。
技术实现要素:5.针对以上现有技术的不足,本发明提供了高强碳酸化钢渣板的制备方法,具体通过以下技术实现。
6.一种高强碳酸化钢渣板的制备方法,其特征在于,包括以下步骤:
7.s1、取钢渣、硅补充剂、钙补充剂、晶型控制剂粉磨,搅拌均匀后加水混合,压制成第一胚体,加水量以压制成第一胚体为基准;
8.或者取钢渣、硅补充剂、钙补充剂、晶型控制剂加水粉磨,混合均匀,再经过干燥并压制成第一胚体,干燥程度以压制成第一胚体为基准;
9.所述钙补充剂为电石渣、石灰、石灰岩、大理石、大理石渣中的至少一种,所述硅补
充剂为二氧化硅、石英砂、硅胶、硅灰中的至少一种;
10.硅补充剂和钙补充剂的用量,以所述第一胚体中cao和mgo二者的总物质的量与sio2、fe2o3和al2o3三者的总物质的量的比例为2:1,以及所述第一胚体中的fe2o3和sio2的物质的量的比例为(0.01-0.3):1为基准;晶型控制剂的加入量为钢渣、硅补充剂、钙补充剂的总重量的0.5%;
11.s2、将步骤s1获得的第一胚体在1300-1450℃下重构反应,保温4-5h,降温冷却待用;
12.s3、将步骤s2制备的产物进行粉磨,过80-200目筛;再加水拌和,压制成第二胚体;将所述第二胚体进行碳酸化养护,制成高强碳酸化钢渣板成品。
13.本发明提供的上述高强碳酸化钢渣板的制备方法中,由于重构反应属于固态物料之间的化学反应,因此,各物料的接触面积越大,反应效率越高。只有将各物料制成固定形状,才能保证各物料最大限度地相互接触。如果仅仅是将各物料的粉末简单混合堆放后重构反应,则反应效率十分有限。因此,步骤s1中,在对原料进行重构反应之前,需要先将钢渣、硅补充剂、钙补充剂、晶型控制剂粉磨成粉料,然后混合均匀,再制备成固定形状的第一胚体。
14.制备第一胚体的方法有两种:第一种方法是干法混合制胚,即将各原料(钢渣、硅补充剂、钙补充剂、晶型控制剂)干法混合均匀后,加水拌和成泥状,然后压制成第一胚体,加水的量不能太多,只要能保证制成的第一胚体能保持固定的形状即可;第二种方法是湿法混合制胚,即将各原料加水搅拌,这样能尽可能使所有物料混合均匀,此时的浆料流动性非常高,无法制成第一胚体,因此需要在烘箱/干燥箱中干燥至一定程度,蒸发去除部分水,直至物料中的含水量适中,适合压制成第一胚体,例如可以100℃左右干燥24-48h。第一胚体的形状只要求保持原料不坍落流动即可,常用的可以用圆柱或长方体形状,圆柱形的尺寸为直径为100mm左右,高为10-30mm胚体,最佳为15mm。
15.一般而言,钢渣中含有氧化钙、氧化铁、二氧化硅、氧化镁、氧化铝等化合物,钙补充剂(以电石渣为例)中一般含有氧化钙、氧化铝等化合物,硅补充剂的主要成分为二氧化硅,不同来源的钢渣、钙补充剂和硅补充剂的化合物成分含量无法确定。因此,本发明提供的制备方法中,钢渣、硅补充剂和钙补充剂的具体用量,主要以最终第一胚体中的各种化合物的物质的量比例为准,保证第一胚体中cao和mgo二者的总物质的量与sio2、fe2o3和al2o3三者的总物质的量的比例为2:1,同时还保证fe2o3和sio2的物质的量的比例为(0.01-0.3):1。步骤 s2中,重构反应的温度受到fe2o3的影响;fe2o3含量高,则烧制温度需要相对略微下降;如果fe2o3含量低,则烧制温度可以相对提高,但是,在1300-1450℃重构温度下,最终制备的钢渣板的各项性能效果最好。重构结束后,需要对第一胚体快速冷却降温,理论上降温速度越快越好,但在试验或实际生产中,不可能无限提高降温速度,因此一般可以针对实际生产情况,将降温速度控制在相对合理的范围内。对于重构产物,需要(在行星式球磨机中)重新粉磨,并过筛,再加水拌和,并在模具中压制成第二胚体,最终采用一般的碳酸化养护方法制成钢渣板成品。模具的尺寸可以根据实际应用需求进行选择,例如可以选用(90-120) mm
×
(90-120)mm
×
(10-30)mm,进一步可以最优选为100mm
×
100mm
×
10mm。
16.本发明为了进一步提升钢渣碳酸化制品的各项性能,先对钢渣原料中所含的各种化合物的比例进行调整,向钢渣原材料中补充钙和硅,调控钢渣中铁的含量;再对钢渣的矿
物组成进行高温重构处理,最终显著提升了重构后的混合料中富铁β-硅酸二钙的比例及反应活性。重构的混合物中,富铁β-硅酸二钙(2cao
·
sio2,β-c2s)和铁酸二钙(2cao
·
fe2o3,c2f)为主要成分,还含有少量的含镁硅酸盐相及铝酸钙相杂质。
17.与未重构钢渣碳酸化后生成的碳酸钙相比,本发明提供的钢渣板的制备方法中,本发明利用工业废弃物电石渣提供钙源,对钢渣中的惰性富铁相(ro相及磁铁矿)进行重构,显著提高了活性相β-c2s的含量,利用铁相掺杂对β-c2s晶体结构的影响及固溶作用,改变生成碳酸钙的微观形貌特性。最终制备的钢渣混合物中,所生成的caco3晶体颗粒间搭接更加紧密,呈现明显的咬合现象;晶体颗粒尺寸更大,晶界较清晰,结晶程度更高,从而形成致密的微观结构,显著提升宏观力学性能。
18.采用本发明制备方法制备的碳酸化钢渣板,抗压强度最高可达134mpa,与未重构钢渣相比强度提升166%,远超现有碳酸化制品强度;重构材料的co2固定能力最高达196g/kg,是一种利用工业固废制备高强碳酸化制品的有效方法。
19.优选地,步骤s1中,当取钢渣、硅补充剂、钙补充剂和晶型控制剂加水粉磨时,加水量为2.5-5l/kg。使用湿法混合制胚时,加入相对大量的水能够促进钢渣、硅补充剂、钙补充剂和晶型控制剂混合均匀,提升后续操作重构时的反应效率和程度。
20.优选地,步骤s1中,所述第一胚体中的fe2o3和sio2的物质的量的比例为 0.15:1;步骤s2中,重构反应条件为1350℃下保温4.5h。
21.钢渣在炼钢过程中通常要经历1600℃以上的高温煅烧环境。过高的温度使钢渣中原先含有的活性矿物(如β-c2s、c4af)处于过烧状态,导致活性矿物反应活性显著低于普通硅酸盐水泥中矿物。钢渣中含有的ro相(由feo、mgo,以及mno等其他二价金属氧化物形成的固溶体)通常不具有反应活性。钢渣中还含有导致安定性不良的游离氧化钙和氧化镁,在热闷等处理工艺中,会使β-c2s、c4af等活性矿物发生水化反应,产生水化产物氢氧化钙及水化硅酸钙,而水化产物虽然具有较高的碳酸化反应活性,但对最终钢渣板成品的力学强度贡献很小。水化硅酸钙碳酸化反应后发生体积收缩,甚至导致碳酸化制品在co2养护过程中开裂,严重影响钢渣制品的各项性能,制约了钢渣制品的广泛应用。
22.本发明的钢渣的重构后矿物组成以β-c2s和c2f为主,原本含有的水化产物氢氧化钙及水化硅酸钙重新转变为β-c2s,而原本反应活性较低的β-c2s在重构过程中得到活化作用,游离氧化钙和氧化镁转变为更稳定的硅酸盐相。钢渣自身含有的铁相,将惰性ro相及磁铁矿等转变为具有碳酸化反应活性的c2f。因此,钢渣的重构可以从根本上解决钢渣安定性不良及活性低的问题。
23.第一胚体中的fe2o3和sio2的物质的量比例,在不影响重构产物的碳酸化反应程度及对co2的固定能力的前提下,还可以显著增强碳酸化钢渣制品的抗压强度。
24.优选地,步骤s2中,重构反应后的降温冷却的平均速度为50℃/min。
25.优选地,步骤s3中,加水拌和的液固比为(1-1.5):10。
26.更优选地,步骤s3中,加水拌和的液固比为1.2:10。
27.优选地,步骤s3中,当以通入纯度为99%的co2为基准时,碳酸化养护的具体方法为:co2分压为0.1-0.3mpa,20-30℃养护2-168h。经过大量的试验发现,当养护2h后,其抗压强度就可以达到较高的水平。随养护时间不断延长,碳酸化钢渣板的抗压强度随之提高,可根据产品用途及参数调整养护时间。当养护3天(72h)后,随着养护时间继续延长,碳酸化钢
渣板的抗压强度虽然可以继续上升,但上升幅度已经大幅下降。当养护7天(168h)后,碳酸化钢渣板的抗压强度已经基本不再变化。
28.优选地,步骤s3中,压制第二胚体的压力为6-9mpa,速度为1-2mm/min,持荷0.5-1min。
29.优选地,所述晶型控制剂为b2o5、v2o5、cr2o3、tio2、mno2中的任意一种。
30.与现有技术相比,本发明的有益之处在于:本发明针对钢渣在制备碳酸化钢渣板上存在的应用问题,通过将钢渣、硅补充剂、钙补充剂、晶型控制剂混合,并调节cao和mgo总量与sio2、fe2o3和al2o3总量的比例,以及fe2o3和sio2的用量比例,与高温重构协同配合,再进行碳酸化养护,显著提升了重构产物中β-c2s的含量,最终显著提升了对co2的固定能力,以及碳酸化钢渣板的力学强度。
附图说明
31.图1为本发明的高强钢渣板的工艺流程;
32.图2为本发明试验例1中钢渣的xrd定量分析效果图;
33.图3为试验例1中重构钢渣的xrd图谱及bse图谱;bse图谱中, n(fe2o3):n(sio2)=0.3;
34.图4为试验例1中钢渣试块的抗压强度及固碳能力的检测结果;
35.图5为试验例1的钢渣试块的微观结构及产物形貌测试结果, n(fe2o3):n(sio2)=0.3;
36.图6为n(fe2o3)/n(sio2)比为0.15条件下,碳酸化养护不同时间得到第二胚体的强度变化规律。
具体实施方式
37.下面将对本发明的技术方案进行清楚、完整地描述,显然,所描述的实施例仅仅是本发明一部分实施例,而不是全部的实施例。基于本发明中的实施例,本领域普通技术人员在没有做出创造性劳动条件下所获得的所有其它实施例,都属于本发明保护的范围。
38.以下实施例和对比例中,所使用的钢渣微粉为采购自本溪钢铁集团的快速水冷处理的转炉钢渣,其化学组成和矿物组成如下表1和附图2所示;所使用的钙补充剂为电石渣,采购自中盐安徽红四方股份公司,主要成分氢氧化钙,其化学组成如下表2所示;所使用的硅补充剂为二氧化硅(分析纯,纯度99.9%);所使用的晶型控制剂为b2o5。
39.表1钢渣的化学组成和矿物组成,单位:wt%
[0040][0041]
表2电石渣的化学组成单位:wt%
[0042]
化学组成caoal2o3sio2na2omgofe2o3k2oso3烧失量(%)质量分数48.511.973.750.7210.1790.2550.0290.28444.30
[0043]
从上表1、2可以看到,钢渣中含有cao为47.61%,sio2为14.76%,fe2o3为21.69%,mgo为6.59%,al2o3为3.44%;电石渣中含有cao为48.51%,sio2为3.75%,al2o3为1.97%;二氧化硅按sio2含量100%计算。
[0044]
以下试验例中,如果未作特殊说明,钢渣、二氧化硅(硅补充剂)、电石渣 (钙补充剂)、b2o5(晶型控制剂)的用量,均采用以下方法换算后获得。
[0045]
钢渣及电石渣中的mgo在配料中考虑取代cao;钢渣及电石渣中的al2o3在配料中考虑取代fe2o3,因为al2o3可与2cao
·
fe2o3结合形成 4cao
·
al2o3·
fe2o3(c4af)。其他微量物质在计算中忽略;
[0046]
下面以第一胚体中cao和mgo二者的总物质的量与sio2、fe2o3和al2o3三者的总物质的量的比例,即n(cao+mgo):n(sio2+fe2o3+al2o3)=2:1,以及第一胚体中的fe2o3和sio2的物质的量的比例,即n(fe2o3):n(sio2)=0.01为例,计算钢渣、电石渣和二氧化硅的重量比:
[0047]
cao的物质的量n(cao)=(47.61m1+48.51m2)/56;
[0048]
mgo的物质的量n(mgo)=6.59m1/40;
[0049]
sio2的物质的量n(sio2)=(14.76m1+3.75m2+100m3)/60;
[0050]
fe2o3的物质的量n(fe2o3)=21.69m1/160;
[0051]
al2o3的物质的量n(al2o3)=(3.44m1+1.97m2)/102;
[0052]
其中,m1为钢渣的重量,m2为电石渣的重量,m3为二氧化硅的重量;
[0053]
基于上述计算公式,倒推整理得到钢渣、电石渣、二氧化硅的重量比 m1:m2:m3=1:6.85:7.75。当改变fe2o3和sio2的物质的量的比例时,所使用的钢渣、电石渣、二氧化硅的用量也会产生相应的变化。
[0054]
以下试验例中,如果未作特殊说明,高强碳酸化钢渣板均按以下方法制备而成:
[0055]
s1、取钢渣、二氧化硅(硅补充剂)、电石渣(钙补充剂)、b2o5(晶型控制剂)采用湿法
球磨的方法加水粉磨,混合均匀,加水量为3l/kg;再将混合浆料置于100℃干燥箱中干燥脱水,持续30h;将适度脱水的混合料压制成直径高为15mm的第一胚体;
[0056]
硅补充剂和钙补充剂的用量,以所述第一胚体中cao和mgo二者的总物质的量(即n(cao+mgo))与sio2、fe2o3和al2o3三者的总物质的量(即 n(sio2+fe2o3+al2o3))的比例为2:1,以及所述第一胚体中的fe2o3和sio2的物质的量的特定比例(视具体试验例情况而定)为基准;晶型控制剂的加入量为钢渣、硅补充剂、钙补充剂的总重量的0.5%;
[0057]
s2、将步骤s1获得的第一胚体在特定条件下进行高温重构反应,保温4.5h,降温冷却待用;
[0058]
s3、将步骤s2制备的产物放入行星式球磨机中进行粉磨,过100目筛(得到的粉末的平均粒径范围为43-60μm);再参考gb/t 17671-2021《水泥胶砂强度检验方法(iso法)》中的标准搅拌方法,加水拌和,液固比为1.2:10,将混合料倒入模具中,按8mpa压力,速度2mm/min,并保持压力30s,压制成第二胚体;所使用的模具尺寸为20mm
×
20mm
×
20mm;
[0059]
最后将所述第二胚体放入碳化釜中,通入99%的co2,co2分压为0.2mpa, 25℃下养护2-168h进行碳酸化养护,制成高强碳酸化钢渣板成品。
[0060]
试验例1:第一胚体中的fe2o3和sio2的物质的量的比例对高强碳酸化钢渣板的性能的影响
[0061]
1、试验过程
[0062]
本试验例提供的高强碳酸化钢渣板的制备方法中,分别调整第一胚体中的 fe2o3和sio2的物质的量的比例为0.01:1、0.05:1、0.1:1、0.15:1、0.2:1、0.25:1、 0.3:1、0.4:1,并通过相应的换算后确定钢渣、电石渣和二氧化硅的用量;晶型控制剂b2o5的用量为钢渣、电石渣、二氧化硅、b2o5总重量的0.5%;
[0063]
针对上述fe2o3和sio2的物质的量,选择相应的重构温度分别为1450℃、 1425℃、1400℃、1350℃、1325℃、1300℃、1300℃下重构反应,保温4.5h,按照50℃/min的速率降温冷却待用;
[0064]
将高温重构后样品破碎后,在球磨机中粉磨直至全部过100目筛,不同 n(fe2o3)/n(sio2)比条件下,得到的改性钢渣的粒径分布如下表3所示。各组平均粒径变化范围为43-60μm,较未接近。
[0065]
表3重构钢渣粉体的粒径分布结果
[0066]
[0067]
因此,后续分析可忽略由于粒径变化对反应速率及程度的影响。压制成型的第二胚体在碳化釜中碳酸化养护168h,得到钢渣试块。
[0068]
此外,以未进行重构处理,直接将第一胚体进行碳酸化养护制成钢渣试块,作为比较例。
[0069]
2、测试钢渣试块的碳酸化程度、co2固定能力、物理性能和抗压强度等参数
[0070]
按照上述方法测试制备的钢渣制品的co2固定能力、碳酸化程度及产物碳酸钙的含量。抗压实验使用ye-30型液压式压力实验机:计算三个试块抗压强度的平均值,精确至0.01mpa,如果所测得的三个值与它们平均值的差不大于 15%,则用该平均值作为抗压强度,如果有某个值与平均值之差大于15%,应将此值舍去,以其余的值计算平均值;如果有二个以上的值与平均值之差大于15%,应重做实验。通过热重-差式扫描量热仪(tg-dsc)对物相的矿物成分,碳酸化程度及碳酸钙的分解温度进行测定。测试温度为50-1000℃,升温速度10℃/min。碳酸化程度、二氧化碳固定能力、碳酸钙含量、物理性能的测试及计算方法如下。
[0071]
(1)二氧化碳固定能力
[0072]
二氧化碳固定能力(co2sequestration capacity,g/kg)表示每kg原材料可以固定的co2质量(g),由以下公式计算:
[0073][0074]
式中co2(wt%)由碳酸钙对应分解温度范围的脱碳量得到。
[0075]
(2)碳酸化程度
[0076]
按以下公式计算:
[0077][0078]
其中,代表在加热过程中的脱碳量;和mw
co2
分别表示和co2的摩尔质量。
[0079]
(3)物理性能测试
[0080]
利用材料现代科学分析测试技术,对试样进行sem,bse-eds,xrd-qxrd, dta-tg及mip等物相分析。对铁相含量变化对钢渣碳酸化制品强度及碳酸化程度的影响机理进行了探讨。重构后钢渣中主要发生的碳酸化反应方程如下:
[0081]
1/2[ca2sio
4(s)
]+co
2(g)
→
caco
3(s)
+1/2sio
2(s)
,δhm<-113.4kj/mol
[0082]
(4)钢渣试块的性能测试结果
[0083]
钢渣试块的性能测试结果如下表4和附图3、4所示。
[0084]
表4钢渣试块的性能测试结果
[0085]
编号重构温度,℃n(fe2o3)/n(sio2)co2固定能力,g/kg抗压强度,mpa比较例-0.55:117250.4实施例114500.01:116864.5实施例214250.05:1197107.9实施例314000.1:1189105.9实施例413500.15:1196134.3
实施例513250.2:1192130.7实施例613000.25:1188120.7实施例713000.3:1166120.4
[0086]
从上表3可以看到,比较例的钢渣碳酸化样品的co2固定能力及抗压强度分别为172g co2/kg钢渣、50.4mpa。高温重构试样与空白样对比得到,在 n(fe2o3)/n(sio2)重=0.05-0.25范围内均可提升材料的co2固定能力,在 n(fe2o3)/n(sio2)重=0.01-0.3范围内均可显著提升碳酸化制品的抗压强度。最佳方案为n(fe2o3)/n(sio2)=0.15,重构温度与硅酸盐水泥的1500℃相比,降低 50-200℃,由此可节省大量能源并减少co2排放。
[0087]
从附图3可以发现,c2f包裹在β-c2s颗粒间隙,c2f自身也具有碳酸化反应活性,但反应活性低于β-c2s。随着n(fe2o3)/n(sio2)比例增加,生成的β-c2s 量逐渐降低,α
’‑
c2s含量逐渐增加,c2f含量逐渐增加,伴随c2f包裹β-c2s的厚度逐渐增加。适量的c2f可提升材料总体的碳酸化程度,但过高的c2f包裹层厚度对总碳酸化程度及固碳量不利,最佳n(fe2o3)/n(sio2)比为0.15,此时重构材料的co2固定能力最高,达到196g co2/kg,抗压强度达到134mpa,与未重构钢渣相比强度提升166%。
[0088]
总体而言,c2f的含量的变化对材料总体碳酸化程度的影响较小,但可显著提升制品的抗压强度,即使n(fe2o3)/n(sio2)比仅为0.05,抗压强度也已经达到 108mpa,与未重构钢渣相比强度提升114%,而co2固定能力仅提升15%,可见强度提升的主要原因并不在于产物碳酸钙含量增加,而是铁掺杂对碳酸钙微观结构的影响。
[0089]
从附图4可以看到,富铁的β-c2s碳酸化后产物具有更高的强度贡献能力。 n(fe2o3)/n(sio2)设计比例的变化并未显著影响重构材料的碳酸化反应程度及co2固定能力,但即使少量的铁即可显著增强碳酸化制品的抗压强度。
[0090]
从附图5可以看到,铁掺杂后生成的碳酸钙结晶程度更高,颗粒间堆积更加紧密,且颗粒间呈现出明显的机械咬合作用,使得碳酸化制品微观结构更加致密,孔隙以封闭的微孔为主,可引起结构缺陷的大孔较少。
[0091]
试验例2:碳酸化养护时间对碳酸化钢渣板的性能影响
[0092]
本试验例用于测试的高强碳酸化钢渣板的制备方法中,第一胚体中的fe2o3和sio2的物质的量的比例为0.15:1,重构条件为1350℃保温4.5h。压制成型的第二胚体在碳化釜中分别碳酸化养护2min、5min、30min、2h、和168h(7天),得到相应的钢渣试块,对其进行抗压强度测试,结果如附图6所示。
[0093]
从图6可以看到,当将第一胚体中的fe2o3和sio2的物质的量的比例控制约为0.15:1时,随着碳酸化养护时间的延长,碳酸化钢渣板的抗压强度显著提升。
[0094]
试验例3:重构温度对重构后的第二胚体中活性矿物成分含量的影响
[0095]
本实验在钢渣矿物成分过程中,尝试在给定n(fe2o3)/n(sio2)比条件下,重构温度对第二胚体中主要活性成分含量的影响,并依次确定不同n(fe2o3)/n(sio2) 比条件下的最佳重构温度。
[0096]
以第一胚体中的fe2o3和sio2的物质的量的比例为0.15:1为例,给出不同重构温度的影响结果,如下表5所示。其中1400℃温度过高导致胚体溶化难以收集样品。在1350℃条件下,主要活性成分β-c2s含量最高,且伴随7.6wt.%的α
’‑
c2s生成。α
’‑
c2s是一种活性更高的c2s相,其生成会提高重构钢渣碳酸化反应速率,对最终制品强度有益。因此选定改组最
佳重构温度为1350℃。
[0097]
表5温度对重构钢渣有效活性成分含量的影响
[0098][0099]
以上具体实施方式详细描述了本发明的实施,但是,本发明并不限于上述实施方式中的具体细节。在本发明的权利要求书和技术构思范围内,可以对本发明的技术方案进行多种简单改型和改变,这些简单变型均属于本发明的保护范围。