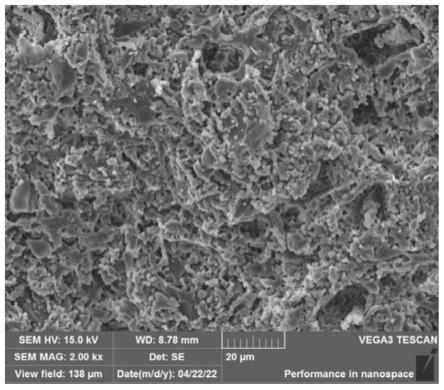
1.本发明涉及发泡陶瓷技术领域,尤其涉及一种氧化铝泡沫陶瓷及其制备方法。
背景技术:2.在铸造生产过程中,泡沫陶瓷可有效地减少或消除液态金属中的夹杂物,显著改善铸件品质和成品率,提高铸造产品的经济效益。其中,氧化铝泡沫陶瓷具有低密度、高强度、高温稳定性及耐腐蚀的特性,被广泛应用于铝及铝合金熔体的过滤,其使用温度约为700~800℃,备受铸造行业的青睐。
3.泡沫陶瓷的制备方法有造孔法、发泡法、有机前驱体浸渍法等,目前多采用有机前驱体浸渍法,即利用有机泡沫作为前驱体模板,通过浸渍、辊压使陶瓷浆料附着于海绵体上,经过干燥、高温烧结而形成具有高通孔率的泡沫陶瓷。由于磷酸二氢铝制备简单、成本低廉,可在相对低的烧成温度(1400℃)获得满足铸造的工况要求、具有良好力学性能的氧化铝泡沫陶瓷,因此常引入磷酸二氢铝作为氧化铝泡沫陶瓷添加剂。然而,磷酸二氢铝导致氧化铝陶瓷浆料的ph值低于5,酸性条件可对生产设备与场地造成明显的腐蚀作用,伴随产生的废水废气会影响周围环境,并且适用于酸性条件下的添加剂种类相对较少,较难通过添加剂调节氧化铝陶瓷浆料的性能,容易造成浆料涂覆不均匀、堵孔等缺陷。
技术实现要素:4.本发明所要解决的技术问题在于,提供一种氧化铝泡沫陶瓷的制备方法,其能够实现在低温条件下烧结得到高通孔率及高力学性能的氧化铝泡沫陶瓷,且工艺简单、节能降耗、环境友好。
5.本发明所要解决的技术问题还在于,提供一种氧化铝泡沫陶瓷,其具有较高通孔率及较高的力学性能。
6.为了解决上述技术问题,本发明提供了一种氧化铝泡沫陶瓷的制备方法,包括以下步骤:
7.以重量份计,将60份~75份α-al2o3粉、10份~12份高岭土粉,5份~8份堇青石粉,1份~6份硅微粉,3份~4份水玻璃,6份~10份pva溶液混合并研磨,得到陶瓷浆料;
8.对聚氨酯海绵体进行预处理,然后对所述聚氨酯海绵体进行挂浆处理,以使所述陶瓷浆料覆盖在所述聚氨酯海绵体上并得到氧化铝泡沫陶瓷坯体;
9.所述氧化铝泡沫陶瓷坯体经干燥处理后进行烧结,得到成品。
10.在一种实施方式中,所述α-al2o3粉的粒径≤2μm;
11.所述高岭土粉的粒径≤65μm;
12.所述堇青石粉的粒径≤1.5μm;
13.所述硅微粉的粒径≤0.5μm;
14.所述水玻璃的模数为2~3;
15.所述pva溶液的聚合度为5000~7000;所述pva溶液的浓度为10%~15%。
16.优选地,所述α-al2o3粉的粒径为0.4μm~0.6μm;
17.所述高岭土粉的粒径58μm~62μm;
18.所述堇青石粉的粒径0.4μm~0.6μm;
19.所述硅微粉的粒径0.1μm~0.3μm。
20.在一种实施方式中,所述研磨包括:采用球磨方式研磨,球磨的球料比为5:1~10:1,混料时间为5h~10h;
21.所述陶瓷浆料的粘度为4200mpa
·
s~4800mpa
·
s。
22.在一种实施方式中,所述对聚氨酯海绵体进行预处理包括以下步骤:
23.采用浓度为0.5%~1%的naoh溶液浸泡所述聚氨酯海绵体,浸泡时间为8h~10h。
24.在一种实施方式中,所述挂浆处理包括以下步骤:
25.将预处理后的所述聚氨酯海绵体浸渍在所述陶瓷浆料中,辊压后形成第一坯体;
26.将所述第一坯体再次浸渍在所述陶瓷浆料中,辊压后形成第二坯体;
27.所述第二坯体干燥后,在所述第二坯体表面喷涂所述陶瓷浆料,得到所述氧化铝泡沫陶瓷坯体。
28.在一种实施方式中,所述干燥处理的工艺参数为:干燥温度为40℃~45℃,干燥时间为10h~12h。
29.在一种实施方式中,所述烧结条件为:
30.先以0.3℃/min~0.5℃/min的升温速率升至530℃~570℃并保温1h~2h;
31.再以0.5℃/min~1.5℃/min的升温速率升至1250℃~1350℃并保温4h~6h;
32.烧结气氛为空气。
33.在一种实施方式中,所述氧化铝泡沫陶瓷的通孔率>85%,常温抗压强度>3.5mpa,800℃一次空气热震后残余强度>3mpa。
34.为解决上述问题,本发明提供了一种氧化铝泡沫陶瓷,所述氧化铝泡沫陶瓷由上述的氧化铝泡沫陶瓷的制备方法制得。
35.实施本发明,具有如下有益效果:
36.本发明选用特定比例的α-al2o3粉、高岭土粉、堇青石粉和硅微粉,四者协同作用下可显著降低氧化铝泡沫陶瓷的烧结温度、增强力学强度和抗热震性能。并采用pva溶液作为粘结剂,可有效地使陶瓷浆料附着在聚氨酯海绵体上,提高上浆量与挂浆均匀度。同时采用水玻璃作为高温固化剂,可有效使氧化铝泡沫陶瓷在1250~1350℃烧成后具有较高的强度,实现了节能降耗与性能优异的统一,同时水玻璃在陶瓷浆料中形成弱碱性环境,能够有效降低浆料对设备的腐蚀,生产过程中产生的废气废水更易于处理。
37.本发明在低温烧结条件下得到高通孔率、高力学强度的氧化铝泡沫陶瓷,具有良好的室温强度及热震残余强度,即通孔率>85%,常温抗压强度>3.5mpa,800℃一次空气热震后残余强度>3mpa,满足浇注要求。
附图说明
38.图1为本发明实施例1中预处理后的聚氨酯海绵体的扫描电镜图片;
39.图2为本发明实施例1中得到的氧化铝泡沫陶瓷的扫描电镜图。
具体实施方式
40.为使本发明的目的、技术方案和优点更加清楚,下面对本发明作进一步地详细描述。
41.术语
42.除非另外说明或存在矛盾之处,本文中使用的术语或短语具有以下含义:
43.本发明中,所使用的“其组合”、“其任意组合”、“其任意组合方式”等中包括所列项目中任两个或任两个以上项目的所有合适的组合方式。
44.本发明中,“优选”仅为描述效果更好的实施方式或实施例,应当理解,并不构成对本发明保护范围的限制。
45.本发明中,以开放式描述的技术特征中,包括所列举特征组成的封闭式技术方案,也包括包含所列举特征的开放式技术方案。
46.本发明中,涉及到数值区间,如无特别说明,则包括数值区间的两个端点。
47.本发明提供了一种氧化铝泡沫陶瓷的制备方法,包括以下步骤:
48.s1、以重量份计,将60份~75份α-al2o3粉、10份~12份高岭土粉,5份~8份堇青石粉,1份~6份硅微粉,3份~4份水玻璃,6份~10份pva溶液混合并研磨,得到陶瓷浆料;
49.具体地,α-al2o3粉,俗称刚玉,是所有氧化铝中最稳定的物相,是氧化铝泡沫陶瓷的主要原料,氧化铝陶瓷的烧结温度主要由其化学组成中的含量来决定,含量越高,瓷料的烧结温度越高。为了实现低温烧成氧化铝泡沫陶瓷,应适当减少氧化铝含量,但是氧化铝含量过低会影响成品强度。优选地,所述α-al2o3粉的重量份为65-70份。示例性的α-al2o3粉的重量份为66份、67份、68份、69份,但不限于此。另外,所述α-al2o3粉的粒径过大将影响成品的力学强度,优选地,所述α-al2o3粉的粒径≤2μm,更佳地,所述α-al2o3粉的粒径为0.4μm~0.6μm。
50.高岭土的主要成分为二氧化硅和氧化铝。其中,二氧化硅属于液相的烧结助剂。由于液相的生成温度低,因而大大地降低了氧化铝陶瓷的烧结温度。以实现在较低的烧结温度条件下制得高强度的氧化铝泡沫陶瓷。优选地,所述高岭土粉的重量份为10.5-11.5份。示例性的高岭土粉的重量份为11份,但不限于此。另外,所述高岭土粉的粒径过大将影响高岭土粉与其它物料的结合强度,优选地,所述高岭土粉的粒径≤65μm。更佳地,所述高岭土粉的粒径58μm~62μm。
51.原料中包含硅微粉,所述硅微粉是指石英粉,硅微粉的加入一方面能够降低烧结温度,另一方面能够与镁、铝协同形成堇青石,有利于增强材料的抗热震性,从而形成高强度的氧化铝泡沫陶瓷。优选地,所述硅微粉的重量份为2-5份。另外,所述硅微粉的粒径过大将影响硅微粉与其它物料的结合强度,优选地,所述硅微粉的粒径≤0.5μm。更佳地,所述硅微粉的粒径0.1μm~0.3μm。
52.堇青石粉,具有较低的热膨胀系数,其化学式为2mgo
·
2al2o3·
5sio2。堇青石含量的提高使得在烧结时能产生更多的液相,有利于提高烧结相对密度,同时液相会产生流淌起泡现象,提高成品的气孔率,有利于提升抗热震性能。但是堇青石含量过高将导致烧结无法顺利进行,而且会降低成品的烧结密度。优选地,所述硅微粉的重量份为6-7份。另外,所述堇青石粉的粒径≤1.5μm;更佳地,所述堇青石粉的粒径0.4μm~0.6μm。
53.综上,本发明选用特定比例的α-al2o3粉、高岭土粉、堇青石粉和硅微粉,四者协同
作用下可显著降低氧化铝泡沫陶瓷的烧结温度、增强力学强度和抗热震性能。其中,堇青石分解熔化所产生的液相能够与氧化铝晶体发生反应析出莫来石,且随着堇青石和氧化铝晶体的长大与结合,会形成网状结构。而高岭土和硅微粉反应也能生成莫来石,堇青石晶体和莫来石晶体相互交错,无序分布,从而能够较好地抵抗由于热震所引起的裂纹扩展,使裂纹扩展所需的能量提高,在宏观上表现出力学强度更高的特点,而且抗热震性也有所提高。
54.另外,由于堇青石的引入,导致在烧结过程中会产生玻璃相,玻璃相是陶瓷结构中最为脆弱的部分,玻璃相含量的增加,不利于陶瓷的力学性能和抗热震性能。本发明向配方体系中引入高岭土粉,可以降低堇青石形成玻璃相的倾向,使得玻璃相含量减少。同时高岭土粉的加入可以改善堇青石玻璃相的结构,对提高玻璃相强度具有重要作用,减少其对成品的力学性能和抗热震性能的不利影响。
55.另外,本技术采用pva溶液作为粘结剂,可有效地使陶瓷浆料附着在聚氨酯海绵体上,提高上浆量与挂浆均匀度。优选地,所述pva溶液的聚合度为5000~7000;所述pva溶液的浓度为10%~15%。
56.同时,本发明采用水玻璃作为高温固化剂,可有效使氧化铝泡沫陶瓷在1250~1350℃烧成后具有较高的强度,实现了节能降耗与性能优异的统一,而且水玻璃在陶瓷浆料中形成弱碱性环境,能够有效降低浆料对设备的腐蚀,生产过程中产生的废气废水更易于处理。优选地,所述水玻璃的模数为2~3。
57.上述原料混合并研磨后得到陶瓷浆料,在一种实施方式中,所述研磨包括:采用球磨方式研磨,球磨的球料比为5:1~10:1,混料时间为5h~10h;所述陶瓷浆料的粘度为4200mpa
·
s~4800mpa
·
s。优选地,所述研磨包括:采用球磨方式研磨,球磨的球料比为6:1~9:1,混料时间为6h~8h;所述陶瓷浆料的粘度为4300mpa
·
s~4700mpa
·
s。
58.s2、对聚氨酯海绵体进行预处理,然后对所述聚氨酯海绵体进行挂浆处理,以使所述陶瓷浆料覆盖在所述聚氨酯海绵体上并得到氧化铝泡沫陶瓷坯体;
59.优选地,所述聚氨酯海绵体的直径为30~100mm,厚度为10~30mm,孔密度为10~30ppi。在一种实施方式中,所述对聚氨酯海绵体进行预处理包括以下步骤:采用浓度为0.5%~1%的naoh溶液浸泡所述聚氨酯海绵体,浸泡时间为8h~10h。
60.需要说明的是,预处理过程中,naoh溶液的浓度过低或浸泡时间过短,无法在聚氨酯海绵体表面产生足够多的腐蚀坑,从而无法提高挂浆量;反之,所述naoh溶液的浓度过高或浸泡时间过长,将导致聚氨酯海绵体的结构遭到破坏,无法满足后续的生产。因此,需要将naoh溶液的浓度控制在0.5%~1%,浸泡时间控制在8h~10h,这样经预处理处理后的聚氨酯海绵体表面具有合适数量的腐蚀坑,同时具有满足后续生产条件的力学强度。
61.在一种实施方式中,所述挂浆处理包括以下步骤:
62.将预处理后的所述聚氨酯海绵体浸渍在所述陶瓷浆料中,辊压后形成第一坯体;
63.将所述第一坯体再次浸渍在所述陶瓷浆料中,辊压后形成第二坯体;
64.所述第二坯体干燥后,在所述第二坯体表面喷涂所述陶瓷浆料,得到所述氧化铝泡沫陶瓷坯体。
65.优选地,所述第一坯体的上浆量为15~20wt%;所述第二坯体的上浆量为80~70wt%;所述在所述第二坯体表面喷涂的上浆量为5~10wt%。
66.本发明采用三次上浆的方式,分别形成三层浆层,第一次上浆在于改善海绵体的
疏水表面,形成有利于浆料附着的过渡层;第二次上浆在过渡层的基础上大量上浆,形成氧化铝泡沫陶瓷主体;第三次上浆在于对泡沫陶瓷表面进行修饰,使其线条更加圆润粗壮。
67.s3、所述氧化铝泡沫陶瓷坯体经干燥处理后进行烧结,得到成品。
68.在一种实施方式中,所述干燥处理的工艺参数为:干燥温度为40℃~45℃,干燥时间为10h~12h。优选地,所述干燥处理后含水量不高于3wt%。
69.在一种实施方式中,所述烧结条件为:
70.先以0.3℃/min~0.5℃/min的升温速率升至530℃~570℃并保温1h~2h;
71.再以0.5℃/min~1.5℃/min的升温速率升至1250℃~1350℃并保温4h~6h;
72.烧结气氛为空气。
73.优选地,所述烧结条件为:采用电炉进行无压烧结,升温速率为0.3℃/min,烧结温度至550℃进行保温处理,保温时间为2h;升温速率为1.0℃/min,烧结温度至1300℃进行保温处理,保温时间为5h,烧结气氛为空气,得到氧化铝泡沫陶瓷。
74.本发明先以较慢的升温速度升至530℃~570℃并保温1h~2h,再以较快的的升温速度升至1250℃~1350℃并烧结4h~6h,有利于减少玻璃相的析出,并且最大程度上提高晶相中的莫来石含量和保留一部分的堇青石晶体,从而实现增强成品的力学强度和抗热震性能。相应地,本发明提供了一种氧化铝泡沫陶瓷,所述氧化铝泡沫陶瓷由上述的氧化铝泡沫陶瓷的制备方法制得。在一种实施方式中,所述氧化铝泡沫陶瓷的通孔率>85%,常温抗压强度>3.5mpa,800℃一次空气热震后残余强度>3mpa。
75.下面以具体实施例进一步说明本发明:
76.实施例1
77.本实施例提供一种氧化铝泡沫陶瓷的制备方法,包括以下步骤:
78.s1、以重量份计,将60份粒径为0.5μm的α-al2o3粉、12份粒径为60μm的高岭土粉,8份粒径为0.5μm的堇青石粉,6份粒径为0.2μm的硅微粉,4份模数为2.5的水玻璃,10份浓度为10%的pva溶液混合,通过球磨法研磨,球料比为10:1,混料时间为5h,得到陶瓷浆料,所述陶瓷浆料的粘度为4200mpa
·
s。
79.s2、对聚氨酯海绵体进行预处理,然后对所述聚氨酯海绵体进行挂浆处理,以使所述陶瓷浆料覆盖在所述聚氨酯海绵体上并得到氧化铝泡沫陶瓷坯体;
80.选取规格为直径为100mm,厚度为30mm,30ppi的聚氨酯海绵块作为上浆模板,采用浓度为1%的naoh溶液浸泡10h处理聚氨酯海绵体。图1为实施例1中预处理后的聚氨酯海绵体的扫描电镜图片,由图1可知,预处理后,聚氨酯海绵体表面增加腐蚀坑,有利于比表面积增大,提高挂浆量。
81.随后,采用纯净水清洗后并对其进行浸渍陶瓷浆料,自动辊压后形成第一坯体,所述第一坯体的上浆量为15wt%;将所述第一坯体再次浸渍在陶瓷浆料中,自动辊压后形成第二坯体,所述第二坯体的上浆量为80wt%;待所述第二坯体干燥后,在所述第二坯体表面喷涂所述陶瓷浆料,喷涂的上浆量为5wt%,得到氧化铝泡沫陶瓷坯体;
82.s3、所述氧化铝泡沫陶瓷坯体经干燥处理后进行烧结,得到成品。
83.具体地,利用45℃干燥室将得到氧化铝泡沫陶瓷坯体进行12h干燥处理,所述的干燥后的氧化铝泡沫陶瓷含水量低于3wt%。再采用电炉进行无压烧结,升温速率为0.3℃/min,烧结温度至550℃进行保温处理,保温时间为2h;升温速率为0.5℃/min,烧结温度至
1250℃进行保温处理,保温时间为6h,烧结气氛为空气,得到氧化铝泡沫陶瓷,图2为实施例1得到的氧化铝泡沫陶瓷的扫描电镜图。
84.实施例2
85.本实施例提供一种氧化铝泡沫陶瓷的制备方法,包括以下步骤:
86.s1、以重量份计,将75份粒径为2μm的α-al2o3粉、8份粒径为50μm的高岭土粉,5份粒径为1.5μm的堇青石粉,3份粒径为0.5μm的硅微粉,3份模数为2.5的水玻璃,6份浓度为15%的pva溶液混合,通过球磨法研磨,球料比为10:1,混料时间为5h,得到陶瓷浆料,所述陶瓷浆料的粘度为4800mpa
·
s。
87.s2、对聚氨酯海绵体进行预处理,然后对所述聚氨酯海绵体进行挂浆处理,以使所述陶瓷浆料覆盖在所述聚氨酯海绵体上并得到氧化铝泡沫陶瓷坯体;
88.选取规格为直径为30mm,厚度为10mm,10ppi的聚氨酯海绵块作为上浆模板,采用浓度为0.5%的naoh溶液浸泡8h处理聚氨酯海绵体。采用纯净水清洗后并对其进行浸渍陶瓷浆料,自动辊压后形成第一坯体,所述第一坯体的上浆量为20wt%;将所述第一坯体再次浸渍在陶瓷浆料中,自动辊压后形成第二坯体,所述第二坯体的上浆量为70wt%;待所述第二坯体干燥后,在所述第二坯体表面喷涂所述陶瓷浆料,喷涂的上浆量为10wt%,得到氧化铝泡沫陶瓷坯体;
89.s3、所述氧化铝泡沫陶瓷坯体经干燥处理后进行烧结,得到成品。
90.具体地,利用40℃干燥室将得到氧化铝泡沫陶瓷坯体进行10h干燥处理,所述的干燥后的氧化铝泡沫陶瓷含水量低于3wt%。再采用电炉进行无压烧结,升温速率为0.5℃/min,烧结温度至550℃进行保温处理,保温时间为1h;升温速率为1.5℃/min,烧结温度至1350℃进行保温处理,保温时间为4h,烧结气氛为空气,得到氧化铝泡沫陶瓷。
91.实施例3
92.本实施例提供一种氧化铝泡沫陶瓷的制备方法,包括以下步骤:
93.s1、以重量份计,将68份粒径为1μm的α-al2o3粉、10份粒径为50μm的高岭土粉,6份粒径为1.5μm的堇青石粉,4份粒径为0.2μm的硅微粉,4份模数为2.5的水玻璃,8份浓度为12%的pva溶液混合,通过球磨法研磨,球料比为7:1,混料时间为8h,得到陶瓷浆料,所述陶瓷浆料的粘度为4500mpa
·
s。
94.s2、对聚氨酯海绵体进行预处理,然后对所述聚氨酯海绵体进行挂浆处理,以使所述陶瓷浆料覆盖在所述聚氨酯海绵体上并得到氧化铝泡沫陶瓷坯体;
95.选取规格为直径为60mm,厚度为20mm,20ppi的聚氨酯海绵块作为上浆模板,采用浓度为1%的naoh溶液浸泡10h处理聚氨酯海绵体。采用纯净水清洗后并对其进行浸渍陶瓷浆料,自动辊压后形成第一坯体,所述第一坯体的上浆量为15wt%;将所述第一坯体再次浸渍在陶瓷浆料中,自动辊压后形成第二坯体,所述第二坯体的上浆量为75wt%;待所述第二坯体干燥后,在所述第二坯体表面喷涂所述陶瓷浆料,喷涂的上浆量为10wt%,得到氧化铝泡沫陶瓷坯体;
96.s3、所述氧化铝泡沫陶瓷坯体经干燥处理后进行烧结,得到成品。
97.具体地,利用45℃干燥室将得到氧化铝泡沫陶瓷坯体进行12h干燥处理,所述的干燥后的氧化铝泡沫陶瓷含水量低于3wt%。再采用电炉进行无压烧结,升温速率为0.3℃/min,烧结温度至550℃进行保温处理,保温时间为2h;升温速率为1℃/min,烧结温度至1300
℃进行保温处理,保温时间为5h,烧结气氛为空气,得到氧化铝泡沫陶瓷。
98.对比例1
99.本实施例提供一种氧化铝泡沫陶瓷的制备方法,与实施例1不同之处在于步骤s1,对比例1的步骤s1中不含有堇青石粉,其余均与实施例1相同。
100.对比例2
101.本实施例提供一种氧化铝泡沫陶瓷的制备方法,与实施例1不同之处在于步骤s1,对比例1的步骤s1中不含有高岭土粉,其余均与实施例1相同。
102.对比例3
103.本实施例提供一种氧化铝泡沫陶瓷的制备方法,与实施例1不同之处在于步骤s1,对比例1的步骤s1中不含有硅微粉,其余均与实施例1相同。
104.对实施例1~3和对比例1~3制得的氧化铝泡沫陶瓷进行性能测试,测试结果如表1所示。由表1数据可知,本发明在低温烧结条件下得到高通孔率、高力学强度的氧化铝泡沫陶瓷,具有良好的室温强度及热震残余强度,即通孔率>85%,常温抗压强度>3.5mpa,800℃一次空气热震后残余强度>3mpa,满足浇注要求。
105.表1为实施例1~3和对比例1~3制得的氧化铝泡沫陶瓷进行性能测试结果
[0106][0107]
以上所述是发明的优选实施方式,应当指出,对于本技术领域的普通技术人员来说,在不脱离本发明原理的前提下,还可以做出若干改进和润饰,这些改进和润饰也视为本发明的保护范围。