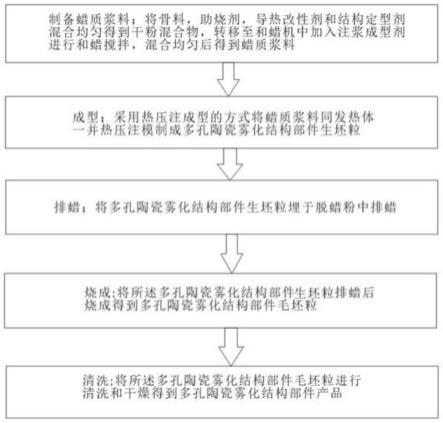
1.本发明涉及雾化器技术领域,尤其涉及一种多孔陶瓷雾化结构部件及其制备方法。
背景技术:2.目前,多孔陶瓷雾化结构部件在电子烟用各类相关部件中占据着举足轻重的核心地位,并吸引了大批从业者对该核心部件进行不断地改良和优化,促进了电子烟行业的健康稳定发展。市场主流的多孔陶瓷雾化结构部件按发热体附着形式主要有内嵌型、表面镶嵌型和表面覆膜型等三种,按部件形状分类常见的主要有圆柱形、杯形和方形等三种。
3.尽管如此,市面上流行的多孔陶瓷雾化结构部件仍然是参差不齐,其品吸口感性能也是良莠不齐。引发这种差异性的原因是多数开发者未能准确匹配到影响多孔陶瓷雾化结构部件品吸口感性能优良的关键性指标。产品制备时多停留在对陶瓷基体的孔隙率、孔径大小、孔分布等多孔陶瓷制备的一般性指标做过度分析,一味局限地追求高孔隙率的多孔陶瓷材料,不仅错失了大量可做进一步分析的多孔陶瓷基材,而且最重要的一点是未能准确地将每一种多孔陶瓷材料的雾化表现提升到极致,无法精确定制雾化领域可用的多孔陶瓷佳品。此外,大多数该类产品的烧结温度范围窄,不易控制产品的尺寸收缩,使其对烧结设备的控温要求严格,而控温精度高的烧结设备价格较为昂贵,这致使从业者要么提升产品品质而增加生产成本,要么降低产品品质而降低生产成本,从而也导致市面上的产品性能千差万别。
4.对于表面镶嵌的多孔陶瓷雾化结构部件,通过采用外添加导热拟合剂的方式能够最大限度地拟合多孔陶瓷基体与发热体相互工作时的最佳协同雾化能力,而结构定型剂的引入不仅能够极大地拓宽了多孔陶瓷基体的烧结温度范围,也能够广泛适配更多的常用烧结设备。通过上述两种方式的加持,可以精确定制得到尺寸稳定可控、发热集中、雾化均匀的多孔陶瓷雾化结构部件,其关键难点在于导热拟合剂、结构定型剂的种类选择及加入量的精确控制。
技术实现要素:5.针对上述技术中存在的不足之处,本发明提供一种多孔陶瓷雾化结构部件及其制备方法,旨在解决现有技术开发成效低、产品差异大、生产成本高的问题。
6.为实现上述目的,本发明提供一种多孔陶瓷雾化结构部件的制备方法,包括以下步骤:
7.s1:制备蜡质浆料;将骨料,助烧剂,导热改性剂和结构定型剂混合均匀得到干粉混合物,转移至和蜡机中加入注浆成型剂进行和蜡搅拌,混合均匀后得到蜡质浆料;
8.s2:成型;采用热压注成型的方式将蜡质浆料同发热体一并热压注模制成多孔陶瓷雾化结构部件生坯粒;
9.s3:排蜡;将多孔陶瓷雾化结构部件生坯粒埋于脱蜡粉中排蜡;
10.s4:烧成;将所述多孔陶瓷雾化结构部件生坯粒排蜡后烧成得到多孔陶瓷雾化结构部件毛坯粒;
11.s5:清洗;将所述多孔陶瓷雾化结构部件毛坯粒进行清洗和干燥得到多孔陶瓷雾化结构部件产品。
12.作为优选,在步骤s1中,按照质量百分比,各个组分的含量为:
13.骨料:30%-70%;
14.助烧剂:15%-40%;
15.导热改性剂:0.5%-15%;
16.结构定型剂:5%-20%;
17.且注浆成型剂的添加量为干粉混合物总质量的40%-60%。
18.作为优选,在步骤s1中,骨料为石英粉,刚玉粉中的一种或两种混合;助烧剂为玻璃粉、玻璃微珠中的一种或两种混合,造孔剂为淀粉、稻壳粉和草灰中的一种或多种混合,导热改性剂为硅藻土、绿沸石、漂珠、海泡石中一种或多种混合,结构定型剂为氧化锆空心球、粉煤灰空心球、硅藻土、海泡石中的一种或多种混合,注浆成型剂为石蜡、蜂蜡、油酸与硬脂酸中的一种或多种混合。
19.作为优选,热压注成型的气压为0.4-0.9mpa,浆桶温度为60-80℃,注浆口温度为55-75℃;排蜡的条件为排蜡速率为0.1-1℃/min,排蜡温度为350-380℃,保温时间为1-4h;所述烧成的条件为烧结速率为1.5-10℃/min,烧结温度为500-800℃,保温时间为0.5-3h。
20.作为优选,烧成过程中的控制条件为烧成线收缩小于4%,孔隙率为40%-65%,孔径中位值为5-60μm,抗折力大于15n,导热系数0.15-0.6w/(m
·
k)。
21.本发明还公开了一种多孔陶瓷雾化结构部件,所述多孔陶瓷雾化结构部件采用上文所述的制备方法制得。
22.本发明的有益效果是:与现有技术相比,本发明提供一种多孔陶瓷雾化结构部件及其制备方法,精细化了电子烟用多孔陶瓷雾化结构部件的开发思路,更加精准地把握住了产品的开发方向,恰如其分地发挥了每一种原料的实际效用;通过导热拟合剂的引入精准预知多孔陶瓷基体与发热体的匹配程度,不仅可缩短产品开发时间,还能提升原料的可利用率,为进一步提升多孔陶瓷雾化结构部件的综合雾化能力提供保障;而且制备方法中结构定型剂的引入也降低了生产过程中对设备的严格要求,减少了高精度设备的需求,从而有利于降低生产制造成本,可以最终实现低成本投入下也能制备出来产品尺寸特征高度一致性的多孔陶瓷雾化结构部件。
附图说明
23.图1为本发明的步骤流程图;
具体实施方式
24.为了更清楚地表述本发明,下面结合附图和实施例对本发明作进一步地描述,当然本发明的保护范围不仅于此,在不付出创造性劳动的前提下,本领域技术人员能思之变化都属于本技术的保护范围。
25.请参阅图1,本发明公开了一种多孔陶瓷雾化结构部件的制备方法,包括以下步
骤:
26.s1:制备蜡质浆料;将骨料,助烧剂,导热改性剂和结构定型剂混合均匀得到干粉混合物,转移至和蜡机中加入注浆成型剂进行和蜡搅拌,混合均匀后得到蜡质浆料;s2:成型;采用热压注成型的方式将蜡质浆料同发热体一并热压注模制成多孔陶瓷雾化结构部件生坯粒;s3:排蜡;将多孔陶瓷雾化结构部件生坯粒埋于脱蜡粉中排蜡;s4:烧成;将所述多孔陶瓷雾化结构部件生坯粒排蜡后烧成得到多孔陶瓷雾化结构部件毛坯粒;s5:清洗;将多孔陶瓷雾化结构部件毛坯粒进行清洗和干燥得到多孔陶瓷雾化结构部件产品。在具体实施过程中,首先将骨料和造孔剂等成分预先混合均匀后再与注浆成型剂进行混合,从而得到物料分散更加均匀的蜡纸浆料,再经过成型,先排蜡处理以减少注浆成型剂在烧成步骤中的影响,待烧成后进行清洗则得到所需要的产品。
27.为了实现上述目的,在步骤s1中,按照质量百分比,各个组分的含量为:骨料:30%-70%;助烧剂:15%-40%;导热改性剂:0.5%-15%;结构定型剂:5%-20%;且注浆成型剂的添加量为干粉混合物总质量的40%-60%。在步骤s1中,骨料为石英粉,刚玉粉中的一种或两种混合;助烧剂为玻璃粉、玻璃微珠中的一种或两种混合,造孔剂为淀粉、稻壳粉和草灰中的一种或多种混合,导热改性剂为硅藻土、绿沸石、漂珠、海泡石中一种或多种混合,结构定型剂为氧化锆空心球、粉煤灰空心球、硅藻土、海泡石中的一种或多种混合,注浆成型剂为石蜡、蜂蜡、油酸与硬脂酸中的一种或多种混合。热压注成型的气压为0.4-0.9mpa,浆桶温度为60-80℃,注浆口温度为55-75℃;排蜡的条件为排蜡速率为0.1-1℃/min,排蜡温度为350-380℃,保温时间为1-4h;烧成的条件为烧结速率为1.5-10℃/min,烧结温度为500-800℃,保温时间为0.5-3h。烧成过程中的控制条件为烧成线收缩小于4%,孔隙率为40%-65%,孔径中位值为5-60μm,抗折力大于15n,导热系数0.15-0.6w/(m
·
k)。在本实施例中,导热系数大小取决于导热改性剂的种类以及加入量的精确控制,添加有不同种类的导热改性剂,添加有不同的量的导热改性剂都会对整个体系的导热系数造成影响,且随着导热改性剂加入量的增多,导热系数会逐渐降低;此外烧结温度范围取决于结构定性剂的种类选择以及加入量的精确控制;在具体的实施过程中,为了使得整个结构能够产生更多的气孔,可以额外添加质量分数为5%-30%的造孔剂,可以采用淀粉、稻壳粉和草灰中的一种或多种混合,从而使得最终得到的多孔雾化结构部件的气孔率和孔径满足使用需求。
28.下面通过具体实施例来阐述本技术
29.实施例1:
30.按照质量分数,称取石英粉60%,玻璃粉20%,粉煤灰空心球20%,淀粉20%,石蜡52.5%,油酸0.4%,首先将石英粉,玻璃粉,粉煤灰空心球与淀粉进行混合,待混合均匀后与石蜡和油酸进行再混合,在热压注成型的气压为0.4mpa,浆桶温度为60℃,注浆口温度为55℃;排蜡的条件为排蜡速率为0.1℃/min,排蜡温度为350℃,保温时间为1h;烧成的条件为烧结速率为1℃/min,烧结温度为500℃,保温时间为0.5h;
31.实施例2:
32.按照质量分数,称取石英粉45%,玻璃粉30%,粉煤灰空心球25%,淀粉10%,石蜡52.5%,油酸0.4%,首先将石英粉,玻璃粉,粉煤灰空心球与淀粉进行混合,待混合均匀后与石蜡和油酸进行再混合,在热压注成型的气压为0.4mpa,浆桶温度为60℃,注浆口温度为
55℃;排蜡的条件为排蜡速率为0.1℃/min,排蜡温度为350℃,保温时间为1h;烧成的条件为烧结速率为1℃/min,烧结温度为500℃,保温时间为0.5h。
33.实施例3:
34.称取石英粉35%,玻璃粉30%,粉煤灰空心球30%,淀粉10%,石蜡52.5%,油酸0.4%,首先将石英粉,玻璃粉,粉煤灰空心球与淀粉进行混合,待混合均匀后与石蜡和油酸进行再混合,在热压注成型的气压为0.4mpa,浆桶温度为60℃,注浆口温度为55℃;排蜡的条件为排蜡速率为0.1℃/min,排蜡温度为350℃,保温时间为1h;烧成的条件为烧结速率为1℃/min,烧结温度为500℃,保温时间为0.5h。
35.实施例4:
36.称取石英粉25%,玻璃粉30%,粉煤灰空心球45%,淀粉10%,石蜡45%,油酸0.4%,首先将石英粉,玻璃粉,粉煤灰空心球与淀粉进行混合,待混合均匀后与石蜡和油酸进行再混合,在热压注成型的气压为0.4mpa,浆桶温度为60℃,注浆口温度为55℃;排蜡的条件为排蜡速率为0.1℃/min,排蜡温度为350℃,保温时间为1h;烧成的条件为烧结速率为1℃/min,烧结温度为500℃,保温时间为0.5h。
37.实施例5:
38.称取石英粉30%,玻璃粉30%,硅藻土45%,石蜡57.5%,油酸0.4%,首先将石英粉,玻璃粉,硅藻土进行混合,待混合均匀后与石蜡和油酸进行再混合,热压注成型的气压为0.9mpa,浆桶温度为80℃,注浆口温度为75℃;排蜡的条件为排蜡速率为1℃/min,排蜡温度为380℃,保温时间为4h;烧成的条件为烧结速率为10℃/min,烧结温度为800℃,保温时间为3h。
39.实施例6:
40.称取石英粉55%,玻璃粉20%,绿沸石40%,石蜡57.5%,硬脂酸4%,首先将石英粉,玻璃粉,绿沸石进行混合,待混合均匀后与石蜡和硬脂酸进行再混合,热压注成型的气压为0.9mpa,浆桶温度为80℃,注浆口温度为75℃;排蜡的条件为排蜡速率为1℃/min,排蜡温度为380℃,保温时间为4h;烧成的条件为烧结速率为10℃/min,烧结温度为800℃,保温时间为3h。
41.实施例7:
42.称取石英粉25%,玻璃粉35%,海泡石40%,石蜡57.5%,油酸0.4%,首先将石英粉,玻璃粉,海泡石进行混合,待混合均匀后与石蜡和油酸进行再混合,热压注成型的气压为0.9mpa,浆桶温度为80℃,注浆口温度为75℃;排蜡的条件为排蜡速率为1℃/min,排蜡温度为380℃,保温时间为4h;烧成的条件为烧结速率为10℃/min,烧结温度为800℃,保温时间为3h。
43.实施例8:
44.称取玻璃粉20%,玻璃微珠40%,硅藻土40%,石蜡57.5%,硬脂酸4%,首先将玻璃粉,玻璃微珠和硅藻土进行混合,待混合均匀后与石蜡和硬脂酸进行再混合,热压注成型的气压为0.9mpa,浆桶温度为80℃,注浆口温度为75℃;排蜡的条件为排蜡速率为1℃/min,排蜡温度为380℃,保温时间为4h;烧成的条件为烧结速率为10℃/min,烧结温度为800℃,保温时间为3h。
45.实施例9:
46.称取刚玉粉20%,玻璃粉20%,玻璃微珠20%,硅藻土40%,石蜡57.5%,油酸0.4%,首先将刚玉粉、玻璃粉,玻璃微珠和硅藻土进行混合,待混合均匀后与石蜡和油酸进行再混合,热压注成型的气压为0.9mpa,浆桶温度为80℃,注浆口温度为75℃;排蜡的条件为排蜡速率为1℃/min,排蜡温度为380℃,保温时间为4h;烧成的条件为烧结速率为10℃/min,烧结温度为800℃,保温时间为3h。
47.对比例1:
48.称取石英粉80%,玻璃粉20%,淀粉10%,石蜡40%,油酸0.4%,首先将石英粉,玻璃粉,淀粉进行混合,待混合均匀后与石蜡和油酸进行再混合,热压注成型的气压为0.9mpa,浆桶温度为80℃,注浆口温度为75℃;排蜡的条件为排蜡速率为1℃/min,排蜡温度为380℃,保温时间为4h;烧成的条件为烧结速率为10℃/min,烧结温度为800℃,保温时间为3h。
49.对比例2:
50.称取刚玉粉80%,玻璃粉20%,淀粉20%,石蜡40%,油酸0.5%,首先将石刚玉粉,玻璃粉,淀粉进行混合,待混合均匀后与石蜡和油酸进行再混合,热压注成型的气压为0.9mpa,浆桶温度为80℃,注浆口温度为75℃;排蜡的条件为排蜡速率为1℃/min,排蜡温度为380℃,保温时间为4h;烧成的条件为烧结速率为10℃/min,烧结温度为800℃,保温时间为3h。
51.分别对上述实施例和对比例所得到的陶瓷雾化结构部件进行测试,进行外观、线收缩、电阻、强度、孔隙率、导热系数等进行检测,测试结果如下:
[0052][0053]
本发明还公开了一种多孔陶瓷雾化结构部件,多孔陶瓷雾化结构部件采用上文所述的制备方法制得。
[0054]
以上公开的仅为本发明的几个具体实施例,但是本发明并非局限于此,任何本领域的技术人员能思之的变化都应落入本发明的保护范围。